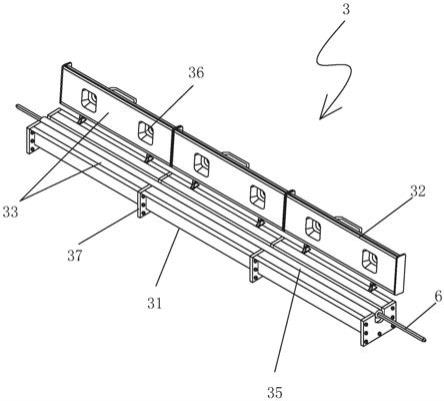
[0001]
本实用新型涉及铜导体退火的技术领域,特别涉及一种利用火焰燃烧法进行铜绞线导体退火的装置及系统。
背景技术:[0002]
通常,国内线缆行业中,铜绞线导体的生产过程,基本都是先进行单线拉丝生产,拉丝工序同时也进行单线的退火处理,使铜单线满足国标gb/t 3953中tr的要求,再进行导体绞制。在绞制过程中由于单线受到挤压、扭转、拉伸等作用产生变形造成铜材电阻率的变大。这样就导致同等导体电阻值要求条件下导体截面的增加,造成铜材浪费,同时还浪费了单线退火所消耗的能源。这就是现有的绞前单线退火导体绞制工艺所存在的问题。而目前国内同行中也有使用绞后罐式退火的处理工艺,其工艺方案为在密封容器内充入保护气体再对导体进行加热退火处理,此类方案最大缺点是容易发生退火不均问题。
[0003]
为了减少同等导体电阻值要求条件下铜材的浪费,降低绞后导体的电阻值,节约资源,同时解决退火不均问题,确保导体退火均匀稳定,本发明人研究开发了火焰燃烧法导体退火技术,遂有本案产生。
技术实现要素:[0004]
本实用新型的目的在于提供一种火焰燃烧法导体退火装置及系统,以降低绞后导体的电阻值,节约资源,提高效益。
[0005]
为了实现上述目的,本实用新型的解决方案是:
[0006]
一种火焰燃烧法导体退火装置,由下槽体和上盖扣合而成,下槽体和上盖的内侧铺设耐火材料层,下槽体和上盖之间形成容纳室,容纳室中布置有供待退火导体穿过的退火管道,上盖装有若干燃气燃烧喷嘴正对退火管道。
[0007]
所述下槽体和上盖均由二段以上拼接而成,每一段下槽体和上盖的端部都设有法兰,相邻的二段之间下槽体和上盖之间借助法兰连接在一起,可依据不同绞合导体需要的退火时间等,选择适当段数进行拼接。
[0008]
所述容纳室是在下槽体的耐火材料层上形成的u型槽,退火管道布置在u型槽中,上盖的耐火材料层上设有喇叭口形状的燃气燃烧喷嘴,燃气燃烧喷嘴的喇叭口下方正对u型槽的上开口。
[0009]
一种火焰燃烧法导体退火系统,由退火放线装置、退火冷却腔室、退火装置、水冷却装置、气冷却装置和退火收线装置组成;退火放线装置和退火收线装置之间安装退火冷却腔室,退火冷却腔室中由前至后依次安装退火装置、水冷却装置和气冷却装置;退火装置由下槽体和上盖扣合而成,下槽体和上盖的内侧铺设耐火材料层,下槽体和上盖之间形成容纳室,容纳室中布置有供待退火导体穿过的退火管道,上盖装有若干燃气燃烧喷嘴正对退火管道;水冷却装置由冷却水管道和喷水头组成,若干喷水头安装在冷却水管道上,且喷水头正对由退火装置中出来的绞合导体运行路径;气冷却装置由冷却气管道和喷气头组
成,若干喷气头安装在冷却气管道上,且喷气头正对由退火装置中出来的绞合导体运行路径;绞合导体由退火放线装置的线盘放出,穿入退火冷却腔室中,依次经过退火装置、水冷却装置和气冷却装置,从退火冷却腔室中穿出,再由退火收线装置的线盘收线。
[0010]
采用上述方案后,本实用新型是通过火焰燃烧法导体退火的装置和系统设计,实现绞后导体的电阻率的降低,以实现在同等电阻要求值的前提下降低铜材消耗的目标。本实用新型同现有的绞前单线退火导体绞制工艺相比,铜材消耗降低1%左右,经济效益提高;同现有的绞后罐式退火的处理工艺相比,退火装置简单,退火效果均匀稳定,速度快,成本低,生产效率明显提高。
[0011]
下面结合实施例对本实用新型做进一步详细说明。
附图说明
[0012]
图1是本实用新型的退火系统结构示意图;
[0013]
图2是本实用新型的退火装置结构示意图;
[0014]
图3是本实用新型的退火装置结构剖视图。
[0015]
标号说明
[0016]
退火放线装置1,退火冷却腔室2,退火装置3,下槽体31,上盖32,耐火材料层33,容纳室34,退火管道35,燃气燃烧喷嘴36,法兰37,水冷却装置4,冷却水管道41,喷水头42,气冷却装置5,冷却气管道51,喷气头52,绞合导体6,退火收线装置7。
具体实施方式
[0017]
如图2至图3所示,本实用新型揭示的一种火焰燃烧法导体退火装置3,由下槽体31和上盖32扣合而成,下槽体31和上盖32的内侧都铺设耐火材料层33(如耐火泥或耐火砖),下槽体31和上盖32之间形成容纳室34,容纳室34中布置有退火管道35供待退火的绞合导体6穿过,上盖32还设有若干燃气燃烧喷嘴36,燃气燃烧喷嘴36正对退火管道35。
[0018]
其中,所述下槽体31和上盖32可以只有一段,也可以如图所示均由二段以上拼接而成,每一段下槽体31和上盖32的端部都设有法兰37,相邻的二段之间下槽体31和上盖32之间借助法兰37连接在一起,这样,可以依据不同绞合导体6需要的退火工艺条件如退火时间等等,选择适当段数进行拼接。
[0019]
本实用新型所述容纳室34的较佳设计是:在下槽体31的耐火材料层33上形成的u型槽,退火管道35布置在u型槽中,上盖32的耐火材料层33上形成喇叭口形状的燃气燃烧喷嘴36,燃气燃烧喷嘴36的喇叭口下方正对u型槽的上开口。
[0020]
如图1所示,本实用新型揭示的一种火焰燃烧法导体退火系统,是图2和图3所示退火装置3的具体运用,由退火放线装置1、退火冷却腔室2、退火装置3、水冷却装置4、气冷却装置5和退火收线装置7组成。退火放线装置1和退火收线装置7之间安装退火冷却腔室2,退火冷却腔室2中按绞合导体6运行路径由前至后依次安装退火装置3、水冷却装置4和气冷却装置5。退火装置3是本实用新型的设计要点,如前所述,由下槽体31和上盖32扣合而成,下槽体31和上盖32的内侧都铺设耐火材料层33(如耐火泥或耐火砖),下槽体31和上盖32之间形成容纳室34,容纳室34中布置有退火管道35供待退火的绞合导体6穿过,上盖32还装有若干燃气燃烧喷嘴36,燃气燃烧喷嘴36正对退火管道35。水冷却装置4由冷却水管道41和喷水
头42组成,若干喷水头42安装在冷却水管道41上,且喷水头42正对由退火装置3中出来的绞合导体6运行路径。气冷却装置5由冷却气管道51和喷气头52组成,若干喷气头52安装在冷却气管道51上,且喷气头52正对由退火装置3中出来的绞合导体6运行路径。燃气燃烧喷嘴36、喷水头42和喷气头52的个数可以根据需要设定。绞合导体6由退火放线装置1的线盘放出,穿入退火冷却腔室2中,依次经过退火装置3、水冷却装置4和气冷却装置5,从退火冷却腔室2中穿出,再由退火收线装置7的线盘收线。其中,所述退火冷却腔室2可以如图所示是直线式但不限于图示结构,退火冷却腔室2的入线口正对退火装置3的入线口,退火装置3的出线口正对退火冷却腔室2的出线口。
[0021]
本实用新型实际应用火焰燃烧法进行导体退火工艺,具体步骤是:
[0022]
第一步,先将拉丝工序生产的铜单线,经过绞线工序绞制成所需截面的绞合导体6。其中,拉丝工序生产的铜单线可以为不经退火或经退火的铜单线;铜单线可以是符合国标gb/t 3953的圆铜线,也可以是拉拔成型的瓦形单线或梯形单线;绞合导体6可以不经紧压成型也可以经过拉拔成型或辊轧成型。
[0023]
第二步,再将绞合导体6穿入退火冷却腔室2并穿过退火装置3的退火管道35,利用燃气燃烧喷嘴36喷出的火焰燃烧退火管道35,将退火管道35升温,再通过热辐射使退火管道35内的绞合导体6升温至铜材退火温度(大约400℃左右),并且持续相应时间,绞合导体6退火,使导体电阻率降低,从而降低导体电阻值至满足国家标准要求。
[0024]
第三步,利用水冷却装置4,采用添加了适量(1wt%~3wt%)抗氧化助剂的水溶液作为冷却水,通过喷水头42,对从第二步退火装置3出来的绞合导体6进行喷淋,水冷却;其中,抗氧化助剂本案优选特例为异丙醇。
[0025]
第四步,利用气冷却装置5,通过喷气头52,用惰性气体(如氮气)喷吹第三步水冷却后的绞合导体6,补充冷却保护。第三步和第四步,起到防止铜导体表面被氧化的功效。
[0026]
第五步,将退火冷却后的绞合导体6收线,完成整个工序操作。整个退火过程中,绞合导体6是处于连续不断地在线牵引运行中。
[0027]
以标称截面为185mm2的圆紧压绞合导体6为例,在退火工序,先点燃退火装置3的燃气燃烧喷嘴36,加热退火管道35至预定温度,再将绞合后绞合导体6牵引至退火装置3内穿过退火管道35,通过管道热辐射,使绞合导体6温度迅速升高至400℃左右,达到预定退火温度;待绞合导体6被牵引出退火管道35时,立即通过水冷却装置4用添加了1%~3%的抗氧化助剂的冷却水进行快速喷淋冷却,然后利用气冷却装置5用氮气喷吹进行补充冷却保护,同时吹干铜导体表面和缝隙间残留的冷却水,使绞合导体6温度快速降低至50℃以下后,再牵引收卷至线盘上。整个退火过程的牵引速度为16m/min。经测试,退火后的185mm2的圆紧压绞合导体6其20℃导体直流电阻平均值为0.0958ω/km,而退火前测试其20℃导体直流电阻平均值为0.0972ω/km,电阻值降低率约1.44%。
[0028]
按同样步骤对标称截面为70mm2和300mm2圆紧压绞合导体进行退火操作,得到相关数据如下:
[0029][0030]
本实用新型由于能有效降低绞后铜导体的电阻值1%左右,换而言之,在同等电阻要求值的前提条件下所需消耗的铜材可减少1%左右,因而达到了节约资源、提高效益的效果。同时,本实用新型的整个退火过程与现有绞后罐式退火工艺相比,时间明显缩短,以长度为1000米的标称截面300平方的导体为例,采用绞后罐式退火工艺完成整个退火过程时间需要4小时,而采用本方案所需时间为1小时10分钟,有效的提升了生产效率。而且采用绞后罐式退火工艺,导体尤其是大截面导体长度受限于罐式退火炉的结构尺寸(例如标称截面300平方的导体长度限于1500米以下),采用本方案则无此限制(标称截面300平方的导体长度可达3700米),这为生产大规格大长度绞后退火导体提供了相当的便利。
[0031]
以下给出本实用新型的一些过程控制参数实例数据:
[0032][0033]
本实用新型在退火过程的整个阶段,退火温度根据导体截面的不同基本控制在300~650℃的范围,截面越大退火温度越高;而绞合导体6截面与牵引速度之间的匹配,成为稳定控制退火温度的最关键因素,应当以绞合导体6的截面为基准,控制牵引速度,使导体温升和温升持续时长均达到工艺控制指标要求范围,才可实现本案目标。
[0034]
以上所述仅为本实用新型的实施个例,并非对本实用新型的限制。应当指出,本领域的技术人员在阅读完本说明书后可以根据需要做出没有创造性贡献的修改,但只要在本实用新型的权利要求范围内都受到专利法的保护。