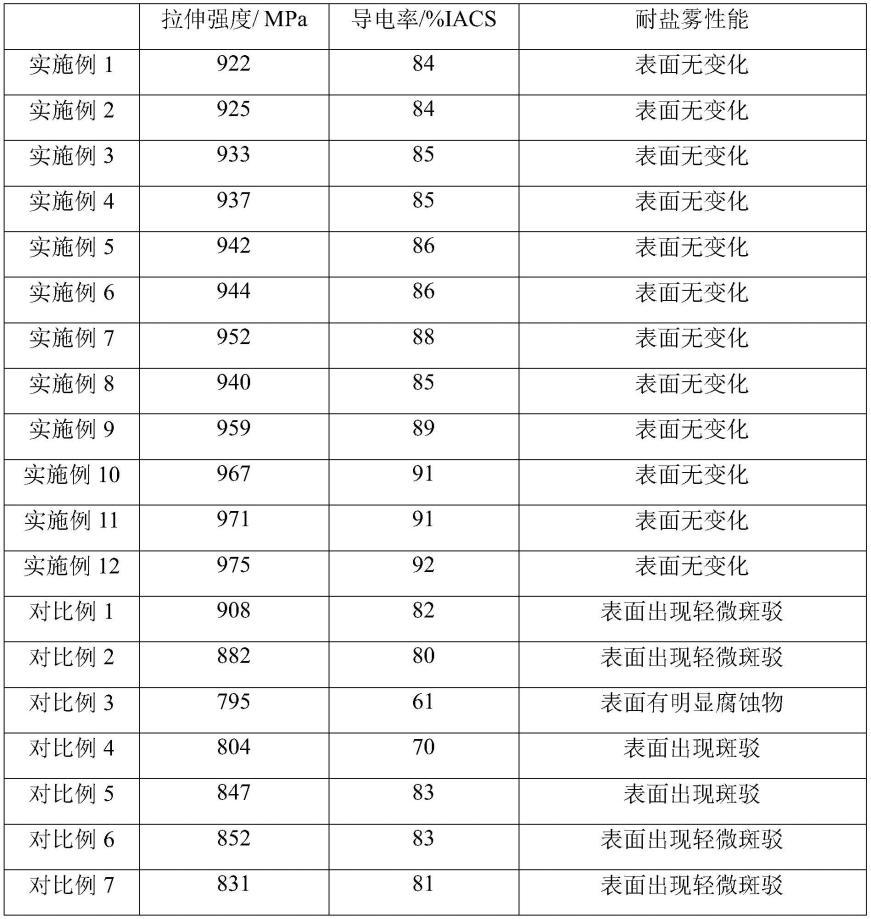
1.本技术涉及铜合金领域,更具体地说,它涉及一种高强高导铜合金的制备工艺及制得的铜合金。
背景技术:2.铜合金一般指以纯铜为基体加入一种或几种其他元素所构成的合金。铜合金在生活中的应用非常广泛,涉及电力输送、通讯电缆、电气线路、印刷电路、船舶、汽车等各行各业。
3.目前,在电力输送过程中,会大批量的使用电缆接头,电缆铺设好后,为了使其成为一个连续的线路,各段线必须连接为一个整体,这些连接点就称为电缆接头;而高压电缆接头用铜外壳是一种高压电缆连接用的接头,若采用一般的铜合金铸造高压电缆接头用铜外壳,发明人发现其无法同时满足高压电缆接头使用时所需的高强度和高导电性,同时由于高压电缆接头需长期暴露使用,使用一段时间后,表面便被腐蚀氧化,使用寿命明显短,因此研发一种高强高导铜合金,同时兼具良好的耐腐蚀性,将其应用在高压电缆接头方面十分必要。
技术实现要素:4.为了有效改善铜合金的强度和导电性,同时改善铜合金的耐腐蚀性,本技术提供一种高强高导铜合金的制备工艺及制得的铜合金。
5.第一方面,本技术提供的一种高强高导铜合金的制备工艺采用如下的技术方案:一种高强高导铜合金的制备工艺,包括以下步骤:步骤一,将原料铜进行熔融并加入复合金属粉料,并在复合气体吹扫下保温1-2h,冷却至常温后制得半成品铜合金,复合气体由有机气体和无机惰性气体组成,半成品铜合金由以下质量百分比的原料制成:锌21-29%,铝5-11%,锡0.01-0.08%,铁1-3%,镍2.5-4%,余量为铜以及不可避免的杂质;步骤二,将半成品铜合金进行气流磨,并加入复合剂混合均匀,随后压制成型,获得一次压坯,将一次压坯在温度为950-1050℃的温度下进行真空烧结,烧结时间为1-2.5h,然后冷却至室温获得烧坯,所述复合剂包括聚酰亚胺纤维,硅粉,碳纤维和二氧化钛;所述复合剂通过以下步骤制得:步骤1,将碳纤维和二氧化钛均匀分散在乙醇溶液中,超声处理,将乙醇蒸干后制得固体产物;步骤2,将聚酰亚胺纤维和硅粉均研磨成微粉,然后加入固体产物和粘结剂进行喷雾造粒制得0.1mm以下的颗粒;步骤三,将烧坯进行破碎磨粉制成5μm以下的微粉,加入稀土金属搅拌混合均匀后制得混料,将混料再次压制成型获得二次压坯,将二次压坯进行真空细化工艺,制得细化压坯;
步骤四,将细化压坯在无机惰性气体的保护下将温度升至800-850℃后保温1-2h,在保温期间采用有机气体进行渗碳处理,保温结束后进行二次烧结,然后冷却至室温获得成型铜合金;步骤五,将成型铜合金在密闭条件下升温至500-620℃,并在无机惰性气体的氛围下退火2-3h,随后迅速淬入油中冷却,制得铜合金产品。
6.通过采用上述技术方案,在制备半成品铜合金阶段严格控制其原料组分,采用锌、铝、锡、铁、镍和铜几种组分形成半成品铜合金,铝元素的加入可与后续工序协同进一步细化晶粒,在熔融过程中,一并采用复合气体进行吹扫,一方面可以将原料在熔融保温过程中产生的气相杂质或低熔点杂物形成的气泡进行吹扫除杂,降低半成品铜合金中杂质残留的几率,在产品初期保证其相应的强度和电导性,另一方面可以减少产品的熔融阶段被氧化,以及在有机气体的吹扫下,进行碳元素的捕捉与吸纳,增强产品内部的弥散强化作用,改善产品的强度。
7.在复合剂的制备中,先将碳纤维和二氧化钛加入乙醇溶液中进行表面处理,同时并进行超声处理,提高各组分的均匀分散性,蒸干乙醇的过程中,激发碳纤维和二氧化钛的表面活性,同时形成复合团聚固体产物,与磨成微粉的聚酰亚胺纤维和硅粉在粘结剂的作用下进行喷雾造粒,形成均匀且致密的颗粒。在磨粉后的半成品铜合金中加入复合剂再进行烧结,复合剂不仅能够有效改善产品的强度和导电性,还能有效改善产品的耐腐蚀性能。
8.其中聚酰亚胺纤维在真空烧结过程中进行真空热解,最终生成具有高导电率的更为扩展的网络芳族石墨结构,磨成微粉的硅粉具有优良的表面活性,与碳纤维和二氧化钛复配形成的颗粒复合剂,与真空烧结工艺配合,使得产品具有高导电性、优异的强度和耐腐蚀性。进行真空烧结,可有效提高产品的致密度,改善产品内部结构,不仅能提高产品的强度,还能提高产品的耐腐蚀性,延长产品的使用寿命。
9.将加入稀土金属的二次压坯进行真空细化工艺,以改变各组分之间的作用力和各向异性,提高各原料组分的效用发挥,渗碳处理工艺以有机气体进行渗碳处理,复合剂中含有钛元素,两者结合后以均匀细小的颗粒弥散分布在体系内,能进一步起到弥散强化作用,有效提高产品的强度和硬度。采用真空细化工艺、渗碳处理和二次烧结工艺三者协同,能够有效防止产品内部出现粗大颗粒物,显著改善产品内部结构和组织,提高产品的致密性,改善产品的强度和耐腐蚀情况。
10.优选的,步骤二中,以半成品铜合金为基准,按照3-6wt%的比例添加复合剂。
11.通过采用上述技术方案,优化复合剂的添加比例,避免复合剂添加过多或过少带来的不利影响,进一步改善产品的强度和导电性,同时提高产品的耐腐蚀性。
12.优选的,所述聚酰亚胺纤维、硅粉,碳纤维和二氧化钛的质量比为(1-2):(2-3.5):(0.7-1.2):(0.5-1)。
13.通过采用上述技术方案,优化聚酰亚胺纤维、硅粉、碳纤维和二氧化钛的质量比,以利于复合剂在产品中的效用发挥,从而与真空烧结工艺配合,协同改善产品的强度和导电性,同时改善产品的耐腐蚀性能。
14.优选的,粘结剂为聚乙烯醇或糊精中的一种。
15.通过采用上述技术方案,选择特定类型的粘结剂,有利于改善复合剂中各原料组分的粘结性能,以利于复合剂在体系中的效用发挥。
16.优选的,所述步骤三中,以烧坯破碎磨粉后的微粉为基准,按照0.01-0.03wt%的比例添加稀土金属。
17.通过采用上述技术方案,优化稀土金属添加的量,进一步改善铜合金的原料组成和内部结构,以利于改善产品的导电性和强度性能。
18.优选的,所述稀土金属为镧、铈或镨中的至少一种。
19.通过采用上述技术方案,优化稀土金属的选择,进一步改善产品的导电性和强度性能。
20.优选的,所述步骤三中的真空细化工艺步骤包括:s1预冷:预冷温度为-20℃至-5℃,保温0.5-1h;s2分段升温至100℃,且分段升温过程中真空度设置为15pa
±
10pa;其中所述分段升温包括:第一段,-20℃至-10℃,保持10-25min;第二段:-10℃至0℃,保持10-20min;第三段:0℃-50℃,保持20-30min;第四段:50℃-100℃,保持15-25min。
21.通过采用上述技术方案,将二次压坯进行预冷、再进行分段升温,能够有效改善产品内原料组分的各向异性,从而改善产品的内部组织结构,提高产品的强度和导电性。
22.优选的,所述步骤一和步骤四中的有机气体均为天然气,天然气的流量为0.2-0.5m3/h。
23.优选的,步骤一、步骤四和步骤五中的无机惰性气体均为氮气,氮气的流量为2.0-3.0m3/h。
24.通过采用上述技术方案,步骤一种采用的天然气和氮气配合保证安全生产的同时,也能防止产品表面被氧化和改善其耐腐蚀情况,又能加快气相杂质的澄清,从而在一定程度上改善产品的质量。步骤四中氮气作为保护气体,天然气对细化压坯进行渗碳处理,控制天然气的流量,以控制渗碳量,进一步改善产品的性能。
25.第二方面,本技术提供一种高强高导铜合金,采用如下的技术方案:一种高强高导铜合金,通过上述高强高导铜合金的制备工艺制得。
26.通过采用上述技术方案,通过上述制备工艺制得的铜合金强度高,耐腐蚀性能佳且导电性优异。
27.综上所述,本技术具有以下有益效果:1.在制备半成品铜合金阶段严格控制其原料组分,并采用复合气体进行吹扫,一方面可以将原料在熔融保温过程中产生的气相杂质或低熔点杂物形成的气泡进行吹扫除杂,降低半成品铜合金中杂质残留的几率,在产品初期保证其相应的强度和电导性。
28.2.在磨粉后的半成品铜合金中加入复合剂再进行烧结,复合剂不仅能够有效改善产品的强度和导电性,还能有效改善产品的耐腐蚀性能。其中聚酰亚胺纤维在真空烧结过程中进行真空热解,最终生成具有高导电率的更为扩展的网络芳族石墨结构,磨成微粉的硅粉具有优良的表面活性,与碳纤维和二氧化钛复配形成的颗粒复合剂,与真空烧结工艺配合,使得产品具有高导电性、优异的强度和耐腐蚀性。进行真空烧结,可有效提高产品的致密度,改善产品内部结构,不仅能提高产品的强度,还能提高产品的耐腐蚀性,延长产品的使用寿命。
29.3.采用真空细化工艺、渗碳处理和二次烧结工艺三者协同,能够有效防止产品内部出现粗大颗粒物,显著改善产品内部结构和组织,提高产品的致密性,改善产品的强度和
耐腐蚀情况。
具体实施方式
30.以下结合实施例对本技术作进一步详细说明。
31.本技术所用原料均为普通市售原料,其中碳纤维直径为0.5mm以下,二氧化钛的粒径为50μm以下,乙醇溶液的质量浓度为80%。
32.制备例制备例1复合剂通过以下步骤制得:步骤1,将碳纤维0.7kg和二氧化钛0.5kg均匀分散在乙醇溶液中,超声处理,将乙醇蒸干后制得固体产物;步骤2,将聚酰亚胺纤维1kg和硅粉2kg均研磨成10μm以下的微粉,然后加入固体产物和糊精0.15kg进行喷雾造粒制得0.1mm以下的颗粒。
33.制备例2复合剂通过以下步骤制得:步骤1,将碳纤维1.2kg和二氧化钛1kg均匀分散在乙醇溶液中,超声处理,将乙醇蒸干后制得固体产物;步骤2,将聚酰亚胺纤维2kg和硅粉3.5kg均研磨成10μm以下的微粉,然后加入固体产物和聚乙烯醇0.22kg进行喷雾造粒制得0.1mm以下的颗粒。
34.制备例3复合剂通过以下步骤制得:步骤1,将碳纤维1kg和二氧化钛0.8kg均匀分散在乙醇溶液中,超声处理,将乙醇蒸干后制得固体产物;步骤2,将聚酰亚胺纤维1.5kg和硅粉2.7kg均研磨成10μm以下的微粉,然后加入固体产物和聚乙烯醇0.2kg进行喷雾造粒制得0.1mm以下的颗粒。
35.制备例4复合剂通过以下步骤制得:步骤1,将碳纤维0.4kg和二氧化钛1.8kg均匀分散在乙醇溶液中,超声处理,将乙醇蒸干后制得固体产物;步骤2,将聚酰亚胺纤维2.8kg和硅粉1kg均研磨成10μm以下的微粉,然后加入固体产物和聚乙烯醇0.2kg进行喷雾造粒制得0.1mm以下的颗粒。实施例
36.实施例1高强高导铜合金的制备工艺包括以下步骤:步骤一,将原料铜进行熔融并加入复合金属粉料,并在复合气体吹扫下保温1h,冷却至常温后制得半成品铜合金,复合气体由氮气和天然气组成,氮气从原料铜开始升温前便通入,保温结束后停止,氮气的流量为3.0m3/h,天然气的流量为0.5m3/h,半成品铜合金由以下质量百分比的原料制成:锌21%,铝11%,锡0.01%,铁1%,镍4%,余量为铜以及不可避免的杂质;
步骤二,将半成品铜合金进行气流磨,研磨粒径至0.2mm以下,以半成品铜合金为基准,按照3wt%的比例添加制备例1制得的复合剂混合均匀,随后压制成型,获得一次压坯,将一次压坯在温度为950℃的温度下进行真空烧结,烧结时间为2.5h,然后冷却至室温获得烧坯;步骤三,将烧坯进行破碎磨粉制成5μm以下的微粉,以烧坯破碎磨粉后的微粉为基准,按照0.01wt%的比例添加稀土金属铈搅拌混合均匀后制得混料,将混料再次压制成型获得二次压坯,将二次压坯进行真空细化工艺,制得细化压坯;真空细化工艺步骤包括:s1预冷:预冷温度为-20℃,保温0.5h;s2分段升温至100℃,且分段升温过程中真空度设置为10pa;其中所述分段升温包括:第一段,-15℃,保持10min;第二段:-10℃,保持20min;第三段:20℃,保持20min;第四段:50℃,保持25min;步骤四,将细化压坯在氮气的保护下将温度升至800℃后保温2h,在保温期间采用天然气进行渗碳处理,天然气的流量为0.4m3/h,保温结束后在温度为900℃的条件下进行二次烧结,烧结时间为1.5h,然后冷却至室温获得成型铜合金;步骤五,将成型铜合金在密闭条件下升温至620℃,并在氮气的氛围下退火2h,氮气流量为2.0m3/h,随后迅速淬入油中冷却,制得铜合金产品。
37.实施例2高强高导铜合金的制备工艺包括以下步骤:步骤一,将原料铜进行熔融并加入复合金属粉料,并在复合气体吹扫下保温1h,冷却至常温后制得半成品铜合金,复合气体由氮气和天然气组成,氮气从原料铜开始升温前便通入,保温结束后停止,氮气的流量为2.0m3/h,天然气的流量为0.5m3/h,半成品铜合金由以下质量百分比的原料制成:锌29%,铝5%,锡0.08%,铁3%,镍2.5%,余量为铜以及不可避免的杂质;步骤二,将半成品铜合金进行气流磨,研磨粒径至0.2mm以下,以半成品铜合金为基准,按照6wt%的比例添加制备例1制得的复合剂混合均匀,随后压制成型,获得一次压坯,将一次压坯在温度为1050℃的温度下进行真空烧结,烧结时间为1h,然后冷却至室温获得烧坯;步骤三,将烧坯进行破碎磨粉制成5μm以下的微粉,以烧坯破碎磨粉后的微粉为基准,按照0.03wt%的比例添加稀土金属镨搅拌混合均匀后制得混料,将混料再次压制成型获得二次压坯,将二次压坯进行真空细化工艺,制得细化压坯;真空细化工艺步骤包括:s1预冷:预冷温度为-20℃,保温0.5h;s2分段升温至100℃,且分段升温过程中真空度设置为25pa;其中所述分段升温包括:第一段,-10℃,保持25min;第二段:0℃,保持10min;第三段:50℃,保持30min;第四段:100℃,保持15min;步骤四,将细化压坯在氮气的保护下将温度升至800℃后保温2h,在保温期间采用天然气进行渗碳处理,天然气的流量为0.4m3/h,保温结束后在温度为900℃的条件下进行二次烧结,烧结时间为1.5h,然后冷却至室温获得成型铜合金;步骤五,将成型铜合金在密闭条件下升温至500℃,并在氮气的氛围下退火3h,氮气流量为3.0m3/h,随后迅速淬入油中冷却,制得铜合金产品。
38.实施例3与实施例2的区别在于,步骤一中,半成品铜合金由以下质量百分比的原料制成:锌25.9%,铝8.1%,锡0.03%,铁1.6%,镍3%,余量为铜以及不可避免的杂质;其余均与实施例2相同。
39.实施例4与实施例3的区别在于,步骤二中,烧结温度为1000℃,烧结时间为1.8h,其余均与实施例3相同。
40.实施例5与实施例4的区别在于,步骤二中,以半成品铜合金为基准,按照4.3wt%的比例添加复合剂,其余均与实施例4相同。
41.实施例6与实施例5的区别在于,步骤二中,选用制备例2制得的复合剂,其余均与实施例5相同。
42.实施例7与实施例5的区别在于,步骤二中,选用制备例3制得的复合剂,其余均与实施例5相同。
43.实施例8与实施例5的区别在于,步骤二中,选用制备例4制得的复合剂,其余均与实施例5相同。
44.实施例9与实施例7的区别在于,步骤三中,以烧坯破碎磨粉后的微粉为基准,按照0.05wt%的比例添加稀土金属镧,其余均与实施例7相同。
45.实施例10与实施例9的区别在于,步骤三中,真空细化工艺步骤包括:s1预冷:预冷温度为-15℃,保温0.8h;s2分段升温至100℃,且分段升温过程中真空度设置为20pa;其中所述分段升温包括:第一段,-12℃,保持20min;第二段:0℃,保持16min;第三段:35℃,保持30min;第四段:85℃,保持20min;其余均与实施例9相同。
46.实施例11与实施例10的区别在于,步骤四中,将细化压坯在氮气的保护下将温度升至820℃后保温1.4h,在保温期间采用天然气进行渗碳处理,天然气的流量为0.3m3/h;其余均与实施例10相同。
47.实施例12与实施例11的区别在于,步骤五中,将成型铜合金在密闭条件下升温至580℃,并在氮气的氛围下退火2.2h,氮气流量为3.0m3/h,随后迅速淬入油中冷却,制得铜合金产品;其余均与实施例11相同。
48.对比例对比例1与实施例12的区别在于,步骤一中省略采用复合气体进行吹扫,其余均与实施例
12相同。
49.对比例2与实施例12的区别在于,步骤一中,半成品铜合金由以下质量百分比的原料制成:锌25.9%,锡0.03%,铁1.6%,镍3%,余量为铜以及不可避免的杂质;其余均与实施例12相同。
50.对比例3与实施例12的区别在于,不加入复合剂,其余均与实施例12相同。
51.对比例4与实施例12的区别在于,不加入聚酰亚胺纤维,其余均与实施例12相同。
52.对比例5与实施例12的区别在于,不加入二氧化钛,其余均与实施例12相同。
53.对比例6与实施例12的区别在于,复合剂通过以下步骤制得:将碳纤维1kg和二氧化钛0.8kg和聚酰亚胺纤维1.5kg和硅粉2.7kg混合均匀;其余均与实施例12相同。
54.对比例7与实施例12的区别在于,步骤三中,省略真空细化工艺,其余均与实施例12相同。
55.对比例8与实施例12的区别在于,步骤四中,不进行渗碳处理,直接将细化压坯进行二次烧结;其余均与实施例12相同。
56.性能检测试验将实施例1-12和对比例1-8制得的铜合金进行根据gb/t 228-2010《金属材料室温拉伸试验方法》进行拉伸强度试验,按照ys/t 478-2019《铜及铜合金导电率涡流检测方法》进行导电率试验,结果记录在表1。
57.将实施例1-12和对比例1-8制得的铜合金进行耐盐雾试验,试验温度为35
±
2℃,喷雾压力0.1mpa,盐雾沉降量1-2ml/h,盐雾时间140h,观察铜合金表面是否出现腐蚀现象,结果记录在表1。
58.表1试验结果
通过实施例1-12并结合表1可以看到,通过本技术制得的铜合金具有高强导性,抗拉强度最高可达970mpa,导电率最高可超90%iacs,同时兼具优异的耐腐蚀性能,耐盐雾时间高达140h以上。通过逐步优化铜合金制备步骤中的各工艺条件和参数,产品的质量得到进一步改善和提高;其中实施例8选用制备例4制得的复合剂,其中聚酰亚胺纤维、硅粉,碳纤维和二氧化钛之间的用量比欠佳,以使得制得的产品在抗拉强度、导电性方面均比实施例7的性能略微下降。
59.通过实施例12和对比例1-2可以看到,对比例1中缺少复合气体的协同处理,产品初期内部的杂质增多,在熔融阶段存在被氧化的可能,内部结构欠佳,导致产品的强度和导电性均下降,同时表面出现轻微斑驳现象,有被轻微腐蚀,耐腐蚀性能下降。对比例2则在半成品铜合金阶段缺少铝元素,而铝元素的加入可与后续工艺协同起到细化晶粒的作用,从而改善产品的强度,影响产品的导电性。
60.通过实施例12和对比例3-6并结合表1可以看到,对比例3中不加入复合剂,其制得
的铜合金的强度和导电性均显著下降,同时在耐盐雾试验中出现明显的腐蚀物,产品的耐腐蚀性能也明显下降。而对比例4和对比例5均缺少组分,对比例6则直接将各原料组分混合使用,对比例4-6制得的铜合金的抗拉强度和导电性均明显下降,且耐腐蚀性也不佳,这是由于在复合剂的制备中,先将碳纤维和二氧化钛加入乙醇溶液中进行表面处理,同时并进行超声处理,提高各组分的均匀分散性,蒸干乙醇的过程中,激发碳纤维和二氧化钛的表面活性,同时形成复合团聚固体产物,与磨成微粉的聚酰亚胺纤维和硅粉在粘结剂的作用下进行喷雾造粒,形成均匀且致密的颗粒。聚酰亚胺纤维在真空烧结过程中进行真空热解,最终生成具有高导电率的更为扩展的网络芳族石墨结构,磨成微粉的硅粉具有优良的表面活性,与碳纤维和二氧化钛复配形成的颗粒复合剂,与真空烧结工艺配合,使得产品具有高导电性、优异的强度和耐腐蚀性。
61.通过实施例12和对比例7-8并结合表1可以看到,不论是缺少步骤三的真空细化工艺步骤还是缺少步骤四的渗碳处理步骤,制得的产品各性能均下降,这是由于真空细化工艺,可以改变各组分之间的作用力和各向异性,提高各原料组分的效用发挥,渗碳处理工艺以有机气体进行渗碳处理,复合剂中含有钛元素,两者结合后以均匀细小的颗粒弥散分布在体系内,能进一步起到弥散强化作用,有效提高产品的强度和硬度。同时真空细化工艺、渗碳处理和二次烧结工艺三者协同,能够有效防止产品内部出现粗大颗粒物,显著改善产品内部结构和组织,提高产品的致密性,改善产品的强度和耐腐蚀情况。
62.本具体实施例仅仅是对本技术的解释,其并不是对本技术的限制,本领域技术人员在阅读完本说明书后可以根据需要对本实施例做出没有创造性贡献的修改,但只要在本技术的权利要求范围内都受到专利法的保护。