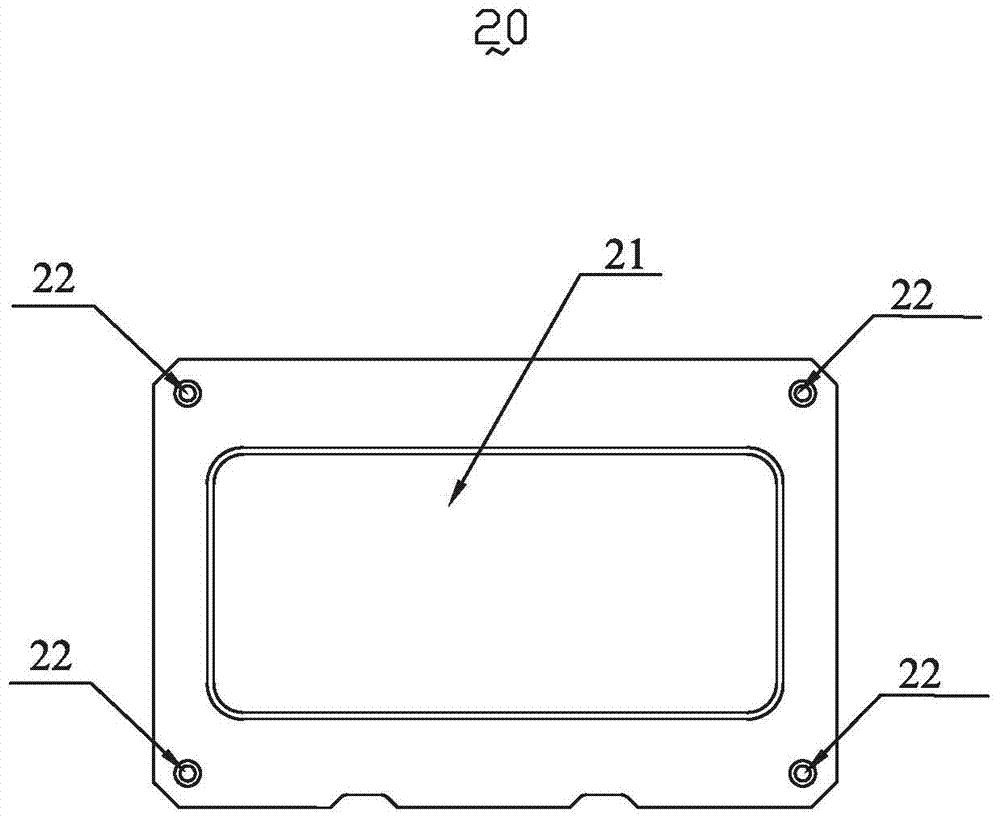
玻璃盖板热弯模具、玻璃盖板热弯制备系统及其工艺【技术领域】本发明涉及玻璃盖板制备领域,尤其涉及一种玻璃盖板热弯模具、玻璃盖板热弯制备系统及其工艺。
背景技术:玻璃盖板即保护玻璃,随着产品要求的升级,市场对于玻璃屏幕的要求也越来越高。目前,市场一般将玻璃干板分为平面玻璃盖板与非平面玻璃盖板,其中,非平面玻璃盖板指的其中间区域可为一平面或弧面,且在玻璃盖板的边缘部分采用弧面过渡。非平面玻璃盖板的优点在于极大提升了手机的外形美观程度以及提升了用户在使用屏幕触屏操作时的体验,因此得到了越来越广泛的应用,同样也对玻璃盖板的加工工艺提出的更高的要求。现有的非平面玻璃盖板制备一般采用冷加工方式,对平面玻璃的边缘进行研磨抛光而获得弧面边缘,采用冷加工制备方式易使加工获得非平面玻璃盖板上出现细小的裂纹,极大地影响了玻璃盖板制备的良品率。因此,亟待对玻璃盖板的制备工艺进行改进。
技术实现要素:为克服目前非平面玻璃盖板制备的缺陷,本发明提供一种操作简便、成品品质稳定性高的玻璃盖板热弯模具、玻璃盖板热弯制备系统及其工艺。本发明为解决上述技术问题提出一技术方案:一种玻璃盖板热弯模具,提供待加工玻璃盖板,所述玻璃盖板热弯模具包括一下模、一型腔及至少四个玻璃球及一定位板,所述型腔设置在所述下模之内,四个所述玻璃球均匀分在所述型腔与所述下模之间,所述待加工玻璃盖板设在所述型腔之上,所述定位板包括一具有开口的平板及设置在所述开口内侧的可变形条状结构,所述定位板的开口内侧与所述待加工玻璃盖板的尺寸相匹配,用于固定放置在所述型腔上的玻璃盖板,当对所述玻璃盖板热弯模具进行加热至接近且低于所述待加工玻璃盖板的最低软化温度,所述待加工玻璃盖板与所述玻璃球软化并在受压后变形。优选地,所述型腔的下表面与所述下模的上表面相对设置,所述型腔的下表面包括至少四个第一圆形凹槽,所述下模的上表面包括至少四个第二圆形凹槽,所述第一圆形凹槽与所述第二圆形凹槽相匹配设置,所述玻璃球直径为6-12mm,容置于所述第一圆形凹槽和第二圆形凹槽之间,且所述第一圆形凹槽深度与所述第二圆形凹槽深度之和小于所述玻璃球的直径。优选地,所述玻璃盖板热弯模具进一步包括一上模,所述上模包括一凸台,所述凸台的下表面与所述型腔的上表面相对设置,所述凸台与所述待加工玻璃盖板尺寸相当。优选地,所述凸台的下表面与所述型腔的上表面为平面或弧面。优选地,所述凸台包括四个弧面边,所述下模包括一内凹平台,所述内凹平台的内侧上部包括至少一弧形凹槽,所述弧面边与所述弧形凹槽匹配设置,所述待加工玻璃盖板边缘与所述弧形凹槽接触。优选地,所述弧形凹槽形状为矩形框、C型框;或所述弧形凹槽为平行设置于相对两侧。本发明为解决上述技术问题提出另一技术方案:一种玻璃盖板热弯制备系统,所述玻璃盖板热弯制备系统包括如上所述玻璃盖板热弯模具,所述玻璃盖板热弯制备系统进一步包括至少一加热工段、一成型工段、一冷却工段及一传送装置,所述玻璃盖板热弯模具由所述传送装置带动并依次进入所述加热工段、所述成型工段及所述冷却工段进行加热、施压及冷却操作。优选地,所述加热工段包括至少三个第一加热工位,至少三个所述第一加热工位的加热温度上限依次增高。优选地,进一步包括温度调整工段,所述温度调整工段位于所述成型工段和冷却工段之间。本发明为解决上述技术问题提出又一技术方案:一种玻璃盖板热弯制备工艺,提供一待加工玻璃盖板,提供一下模、一型腔及至少四个玻璃球及一定位板,所述定位板包括一具有开口的平板及设置在所述开口内侧的可变形条状结构,所述定位板的开口内侧与所述待加工玻璃盖板的尺寸相匹配,所述玻璃盖板热弯制备工艺至少包括如下步骤:步骤1,在所述下模的上表面置放至少四个所述玻璃球;步骤2,将所述型腔放置在所述玻璃球上,所述型腔下表面与所述下模的上表面平行;步骤3,在所述型腔上表面置放所述待加工玻璃盖板,所述定位板用于固定放置在所述型腔上的玻璃盖板;及步骤4,对所述待加工玻璃盖板加热后施加压力,所述待加工玻璃盖板与所述玻璃球软化并在受压后变形。与相对于现有技术,本发明所提供所述玻璃盖板热弯模具、所述玻璃盖板热弯制备系统及所述玻璃盖板热弯制备工艺可用于非平面玻璃盖板的制备(如2.5D玻璃盖板及3D玻璃盖板),通过所述待加工玻璃盖板之下设置至少四个玻璃球(如可为六个),并使所述待加工玻璃盖板与所述玻璃球共同受热软化的状态下,受压后变形,由于所述玻璃球的设置,可使原施加在所述待加工玻璃盖板上的力作用(如应力)均匀分散,从而减少所述待加工玻璃盖板的局部受到过大的压力而出现不均或应力集中的问题。【附图说明】图1是本发明第一实施例玻璃盖板热弯模具的结构示意图。图2是图1中所示玻璃盖板热弯模具的上模的俯视图。图3是图1中所示玻璃盖板热弯模具的下模的仰视图。图4A是图1中所示玻璃盖板热弯模具的下模的俯视图。图4B是图4A中所示下模沿A-A方向的剖面示意图。图5A是图4B中所示C处的放大示意图。图5B是图1中所示B处的放大示意图。图6是图4A中所示下模的一变形实施例的俯视图。图7是图1中所示玻璃盖板热弯模具的定位装置的俯视图。图8是图1中所示D处的放大示意图。图9是本发明第二实施例玻璃盖板热弯制备系统的结构示意图。图10A-图10C是采用本发明提供的玻璃盖板热弯模具对玻璃盖板热弯加工的状态示意图。【具体实施方式】为了使本发明的目的,技术方案及优点更加清楚明白,以下结合附图及实施实例,对本发明进行进一步详细说明。应当理解,此处所描述的具体实施例仅仅用以解释本发明,并不用于限定本发明。需要特别说明的是,在本实用新型中,当元件被称为“设置于”或“设于”另一元件,它可以直接在另一个元件上或者也可以存在居中元件。本文所使用的术语“垂直”、“水平”、“上”及“下”以及类似的表述只是为了说明的目的,不是旨在限制本实用新型。请参阅图1及图2,本发明第一实施例提供一玻璃盖板热弯模具10,所述玻璃盖板热弯模具10可用于将平面玻璃盖板(图未示)通过热弯工艺制备获得边缘具有一定非平面玻璃盖板。所述玻璃盖板热弯模具10包括一上模20、一型腔30、一下模40、一定位装置50及一缓冲装置60,其中,所述上模20设置在所述型腔30之上,所述型腔30可收容于所述下模40之内,所述定位装置50设置在所述上模20与所述型腔30之间。所述上模20为一具有一凸台21的平板,在所述上模20包括至少四个上通孔22,在本实施例中,所述上通孔22为四个,所述上通孔22分别设置在所述上模20表面的四个角落处。所述凸台21的下表面四个角落各设有一弧面边211。所述凸台21的下表面为抛光面,所述凸台21的下表面与所述玻璃盖板接触。在本发明中,所述凸台21的下表面可为平面或弧面。请参阅图3,所述型腔30为一尺寸略小于待加工玻璃盖板尺寸的平板,所述型腔30包括上下主表面(未标号),所述型腔30的上表面为抛光面,所述型腔30的上表面与所述玻璃盖板接触。所述型腔30的厚度为8-30mm,所述型腔30的厚度较优地为8-20mm。所述型腔30的下表面向所述型腔30内部凹陷形成至少四个第一圆形凹槽31,所述第一圆形凹槽31的高度可为2-7mm,在本实施例中,所述第一圆形凹槽31的数量为六个。在本发明中,所述型腔30的上表面为平面或弧面。请参阅图4A,所述下模40为一凹型结构,所述下模40包括一内凹平台401及一边框402,所述内凹平台401设置在所述边框402之内,所述内凹平台401进一步包括两个固定通孔43及至少六个第二圆形凹槽42,所述第二圆形凹槽42分别均匀设置在所述内凹平台401的相对应的两侧,在一些较优的实施例中,所述第二圆形凹槽42设置在所述内凹平台401较长的两侧边上,所述第二圆形凹槽42的高度约为2-7mm。所述边框402的四个边角进一步包括四个下通孔41,所述下通孔41与所述上通孔22相匹配,通过在所述下通孔41与所述上通孔22之间插入插销或螺丝等,可使所述上模20与所述下模40之间对齐并连接。在本实施例中,所述下模40的进一步包括一设置在所述边框402内侧上部的第一弧形凹槽44,所述第一弧形凹槽44为一矩形环状结构。请参阅图4B及图5A,系第一弧形凹槽44的剖面示意图,所述第一弧形凹槽44的弧面结构为朝向所述下模40内部的一端的高度略低于另一端的高度,所述第一弧形凹槽44的弧面角度表示为a1。所述第一弧面凹槽44的形状为矩形框。采用所述第一弧面凹槽44制备获得的非平面玻璃盖板的四个边缘均为弧面。如图5B中所示,系所述上模20的所述凸台21的弧面边211,所述弧面边211的弧面角度为a2。在一些较优的实施例中,所述第一弧面凹槽44与所述弧面边211相匹配。所述弧面角度a1与所述弧面角度a2的选择与所述待加工玻璃盖板的边缘弧面有关,由于所述第一弧面凹槽44与所述弧面边211分别对应于所述待加工玻璃盖板的外表面与内表面(所述玻璃盖板的内表面即为朝向显示模组的一面,所述玻璃盖板的外表面即为所述玻璃盖板朝向用户的一面。)如图6中所示,为本发明所述下模40的一个变形实施例,在该变形实施例中,所述下模40’与上述下模40的区别在于:所述下模40’包括两对称设置的所述第一固定结构401’及两对称设置的所述第二固定结构402’,所述第一固定结构401’与所述第二固定结构402’之间分离设置。所述下模40’包括两设置在所述第一固定结构401’内侧上部的第二弧面凹槽44’,所述弧面凹槽44’的形状特点为平行设置于相对两侧,所述第二弧面凹槽44’的弧面结构特点与所述第一弧面凹槽44相同。采用所述第二弧面凹槽44’制备获得的非平面玻璃盖板的相对两侧的边缘均为弧面。在本发明一些实施例中,所述第一弧形凹槽44还可为C型框等,在此不受限制。所述定位装置50用于固定放置在所述型腔30上的玻璃盖板,所述定位装置50可直接设置在所述型腔30上,如为与所述玻璃盖板上按键孔、TV孔位置相对应的凸柱。如图7中所示,若待加工玻璃盖板上无孔洞,则可采用定位板501对所述玻璃盖板进行固定,所述定位板501上包括四个定位通孔51、一具有开口的平板52及设置在所述开口(未标号)内侧的可变形条状结构53,所述定位通孔51位于所述具有开口的平板52的四个角落。所述开口内侧与所述待加工玻璃盖板的尺寸相匹配,当所述定位板501与所述待加工玻璃盖板进行配合时,所述可变形条状结构53发生形变,从而使所述待加工玻璃盖板可与所述定位板501更为紧密的结合。在一些实施例中,所述定位通孔51与所述上通孔22、所述下通孔41相匹配设置并可通过插入插销或螺丝等进行连接。请参阅图8,所述缓冲装置60包括至少四个玻璃球601,所述玻璃球601设置在所述型腔30的第一圆形凹槽31与所述下模40的第二圆形凹槽42相互配合形成的腔体中,所述玻璃球601放置在所述第一圆形凹槽31与所述第二圆形凹槽42中后,所述型腔30与所述下模40之间仍具有一定的空隙d1。在本发明中,所述第一圆形凹槽31的高度与所述第二圆形凹槽42的高度之和小于所述玻璃球601的直径。所述玻璃球601的直径为6mm-12mm,所述玻璃球601的直径较佳地为7mm-10mm,在本实施例中,所述玻璃球601的直径为8mm。所述玻璃球601的数量较佳地为六个、八个、十个等,在本实施例中,所述玻璃球601的数量选择为六个,所述第一圆形凹槽31、所述第二圆形凹槽42的数量与位置与所述玻璃球601相匹配。所述玻璃球601均匀分布可使所述待加工玻璃盖板受压后力传递更为均匀。在本发明一些实施例中,所述玻璃球601的材质可为钙钠玻璃、含铅玻璃、颜色玻璃等。请参阅图9,本发明的第二实施例提供一玻璃盖板热弯制备系统90,所述玻璃盖板热弯制备系统90包括多个所述玻璃盖板热弯模具10,所述玻璃盖板热弯制备系统90用于对所述待加工玻璃盖板进行加热、施压及冷却操作。所述玻璃盖板热弯制备系统90包括依次设置的一加热工段91、一成型工段91、一温度调整工段93、一第一冷却工段94及一第二冷却工段95。所述玻璃盖板热弯制备系统90进一步包括一传动装置,所述传动装置可带动所述玻璃盖板热弯模具10依次经过所述加热工段91、所述成型工段91、所述温度调整工段93、所述第一冷却工段94及所述第二冷却工段95。其中,所述加热工段91包括至少三个第一加热工位911,至少三个所述第一加热工位911的加热温度上限依次增高,在本实施例中,所述第一加热工位911的数量选择为四个,四个所述第一加热工位911的加热温度上限依次为600℃、650℃、730℃及750℃。在本发明中,所述加热工段91的加热温度上限可根据所述待加工玻璃盖板的材质进行调整,如当所述待加工玻璃盖板为钠钙玻璃时,四个所述第一加热工位911加热温度上限为600℃,而当所述待加工玻璃盖板为高铝玻璃时,所述四个所述第一加热工位911加热温度上限则约为700℃。所述加热工段91中,多个所述第一加热工位911的加热温度上限不易超过所述待加工玻璃盖板的最低软化。温度过高易使所述待加工玻璃盖板的表面形成麻点,使整个热弯成型后的玻璃盖板成品的品质变差。在本发明一些较优的实施例中,所述第一加热工位911进一步包括一上加热部件912及一下加热部件913,所述上加热部件912与所述下加热部件913均为由至少三个加热棒(图未示)组成,如在本实施例中,所述上加热部件912与所述下加热部件913的加热棒的数量均为5个,所述加热棒的温度由中部向两侧增高,如可为1000℃、900℃、750℃、900℃及1000℃。四个所述第一加热工位911温度的分布方式有利于进入所述加热工段91的所述玻璃盖板热弯模具10受到均匀且稳定的加热。所述成型工段92可分为第一成型工位921及第二成型工位922,所述第一成型工位921与所述第二成型工位922分别有一气缸(图未示)带动,实现对所述上模20的按压,如图中所示,所述第一成型工位921包括一下压部件923,所述下压部件923由所述气缸驱动,逐步向下压,所述下压部件923与所述上模20的上表面接触,并逐步下压所述上模20,使温度接近于且低于所述待加工玻璃盖板的最低软化温度时,所述待加工玻璃盖板受压后变形。所述第二成型工位921的结构与运作原理与所述第一成型工位922相同,在此不再赘述。所述玻璃盖板热弯模具10在所述第一成型工位921与所述第二成型工位922中进行按压的时间可根据所述待加工玻璃盖板的材质与厚度进行调整,一般可为30s-200s。所述温度调整工段93与所述加热工段91的结构及其原理的区别在于,所述温度调整工段93的加热温度低于所述加热工段91的加热温度。在本发明的所述加热工段91中温度逐步提升,使置放于所述玻璃盖板热弯模具10中的所述待加工玻璃盖板逐步升温并达到接近于且低于其最低软化温度。所述待加工玻璃盖板在完成热弯及受压变形后,进入本发明的所述温度调整工段93中温度逐步下降,使所述待加工玻璃盖板逐步降温并硬化成型。所述第一冷却工段94及所述第二冷却工段95用于进一步对所述玻璃盖板热弯模具10进行降温,在本实施例中,所述第一冷却工段94及所述第二冷却工段95采用水冷却方式,使所述玻璃盖板热弯模具10及其内置放的所述热弯玻璃盖板进一步冷却成型。其中,所述第一冷却工段94与所述第二冷却工段95的区别在于:所述第一冷却工段94与所述温度调整工段93连接,所述第一冷却工段94的冷却温度受到所述温度调整工段93的影响,因此,所述第一冷却工段94的冷却温度高于所述第二冷却工段95的冷却温度。在本实施例中,从所述温度调整工段93、第一冷却工段94至所述第二冷却工段95,温度逐渐下降,以使所述玻璃盖板热弯模具10及其内置放的所述热弯玻璃盖板逐步降温,从而避免由于急速冷却而出现裂纹或使热弯成型的玻璃盖板出现应力集中等问题,而影响热弯玻璃盖板成品的品质。在本发明中,为了使所述玻璃盖板热弯模具10获得更优的玻璃热弯效果,在本发明中,所述玻璃盖板热弯制备系统90进一步包括一控制模块(图未示)及一驱动模块(图未示),所述控制模块用于控制所述驱动模块,所述驱动模块用于驱动所述加热工段91、所述成型工段91、所述温度调整工段93、所述第一冷却工段94及所述第二冷却工段95的开启、闭合。在本发明一些较优的实施例中,所述上模20与所述下模40之间的上下移动与配合可实现自动化操作,如采用气动装置(图未示)进行驱动,从而使所述下模20与所述下模40之间可更精准的压合,提高所述非平面玻璃盖板制备的良品率。采用本发明所述玻璃盖板热弯模具10进行非平面玻璃盖板的制备过程如下:步骤1,将所述下模40放置一支撑平台(图未示)上,所述支撑平台的中心位置设置有两圆柱体,所述圆柱体可穿过下模40的两所述固定通孔43。继续往所述下模40的的第二圆形凹槽42内逐个放置所述玻璃球601后,将所述型腔30放置在所述下模40的所述内凹平台401后,将所述下模40与所述内凹平台401从所述支撑平台取出。步骤2,将待加工玻璃盖板放置在所述型腔30之上,并采用所述定位装置50进行定位,如所述定位装置50可为所述定位板501或设置在所述型腔30上表面的凸柱。此时,所述待加工玻璃盖板的下表面与所述型腔30的上表面接触,所述待加工玻璃盖板的下表面略大于所述型腔30,所述待加工玻璃盖板的下表面边缘处延伸至所述下模40的第一弧形凹槽44处;使用插销或螺丝将所述下模20与所述下模40连接固定后,将所述玻璃盖板热弯模具置入所述玻璃盖板热弯制备系统90中。步骤3,所述玻璃盖板热弯模具10由所述玻璃盖板热弯制备系统90的传送装置96带动,依次经过所述加热工段91、所述成型工段91、所述温度调整工段93、所述第一冷却工段94及所述第二冷却工段95后,完成玻璃热弯工艺操作。在所述第一加工工段91与所述温度调整工段93中,均包括设置在所述玻璃盖板热弯模具10上下多个加热板,所述加热棒的温度变化与本发明第二实施例中所述,在此不再赘述。在所述成型工段91中,所述玻璃盖板热弯制备系统90向所述玻璃盖板热弯模具10施加压力,从而使所述上模20向下移动。此时,由于所述玻璃盖板热弯模具10经过所述加热工段91与所述温度调整工段92,所述玻璃盖板热弯模具10已逐渐升温至接近且低于所述待加工玻璃盖板的指定温度(如为所述待加工玻璃盖板的最低软化温度)而逐步软化,设置在所述型腔30所述下模40之间的所述玻璃球601由于温度变高,也逐步变软。由于所述上模20的所述弧面边211与所述下模40的所述第一弧面凹槽44相匹配,所述待加工玻璃盖板边缘处受到加压变形,并与所述第一弧面凹槽44的内弧面相匹配。在所述待加工的盖板玻璃被加压的同时,所述玻璃球601由于受到来自所述型腔30的下压力,所述玻璃球601也逐步变形,并将原施加在所述待加工的盖板玻璃上的应力分散。步骤4,完成上述步骤3后,将所述玻璃盖板热弯模具10从所述玻璃盖板热弯制备系统90中取出,将固定所述玻璃盖板热弯模具10的所述上模20与所述下模40的插销或螺丝取出,并将所述上模20取出,将所述下模40、所述型腔30放置在所述支撑平台上,所述支撑平台的圆柱体将所述型腔30顶起,热弯成型的非平面玻璃盖板边缘处与所述下模40的第一弧形凹槽44分离,以便于所述热弯成型的非平面玻璃盖板取出。完成所述热弯成型的非平面玻璃盖板取出后,将所述型腔30从所述下模40中取出后,进一步将受压变形后的所述玻璃球601从所述下模40的第二圆形凹槽42中移除,以完成一次玻璃盖板的热弯成型操作。在实际操作中,所述步骤3与所述步骤4可连续进行,所述加热工段91与所述温度调整工段92的温度保持恒定,所述玻璃盖板热弯制备系统90可同时置入10个所述玻璃盖板热弯模具10,可保证玻璃热弯产品工艺品质稳定性及提高生产效率。在上述步骤1中,在所述玻璃盖板热弯模具10中置入所述玻璃球601的具体步骤如下:将所述型腔40的六个所述第二圆形凹槽42内逐一放置所述玻璃球601后,将所述型腔30连同所述待加工玻璃盖板置入所述型腔40的内凹平台401内,此时,所述玻璃球601的下曲面与所述第二圆形凹槽42接触,所述玻璃球601的上曲面与所述第一圆形凹槽31接触,所述型腔30的上表面与所述型腔40的上表面基本齐平。在上述步骤3中,如采用第一弧面凹槽44,所述待加工玻璃盖板四周边缘均可由平面变形为非平面,如采用所述第二弧面凹槽44’,则所述待加工玻璃盖板的两侧边缘由平面变形为非平面。在本发明另外的一些实施例中,所述第一弧面凹槽44及所述第二弧面凹槽44’还可为其它形状,在此不做限制。更进一步地,如图10A中所示,所述待加工玻璃盖板101a放置在所述上模20与所述型腔30之间,此时,所述待加工玻璃盖板101a为平面状态,此时,所述玻璃球601为初始状态。如图10B中所示,所述上模20的凸台21的下表面及所述型腔30的上表面均为平面结构,所述待加工玻璃盖板101b受到压力后变形,所述待加工玻璃盖板101b的中间区域为平面,所述待加工玻璃盖板101b的边缘变形为弧面,所述待加工玻璃盖板101b成型后形成2.5D玻璃盖板。如图10C中所示,所述上模20的凸台21的下表面及所述型腔30的上表面均为弧面结构,所述待加工玻璃盖板101c受到压力后变形,所述待加工玻璃盖板101c的中间区域为第一弧面(未标号),所述第一弧面的弧度与所述凸台21的下表面、所述型腔30的上表面的弧面结构的弧度均相匹配,所述待加工玻璃盖板101c的边缘变形为第二弧面(未标号),所述待加工玻璃盖板101b成型后形成3D玻璃盖板。采用本发明所提供的玻璃盖板热弯模具10与所述玻璃盖板热弯制备系统90对所述待加工玻璃盖板进行热弯加工后所获得的热弯成型玻璃盖板的表面应力及成品品质均由于采用冷加工制备方法或现有热弯加工工艺方法。在本发明中采用玻璃表面应力仪测量所述热弯成型的玻璃盖板的表面应力,以采用本发明所述玻璃盖板热弯模具10与所述玻璃盖板热弯制备系统90制备获得的所述热弯成型玻璃盖板为实验组1,将采用现有热弯工艺制备的热弯成型玻璃盖板为对照组1,将采用冷加工方式制备的非平面玻璃盖板为对照组2,通过对上述三组非平面玻璃盖板的钢化性能(如应力、抗冲击强度)及外观进行测试,采用本发明所述玻璃盖板热弯模具10与所述玻璃盖板热弯制备系统90制备获得的热弯成型玻璃盖板的各项性能均优于上述的对照组1与对照组2的性能。本发明第三实施例提供一种玻璃盖板热弯制备工艺,提供一待加工玻璃盖板,提供一下模、一型腔及至少四个玻璃球及一定位板,所述定位板包括一具有开口的平板及设置在所述开口内侧的可变形条状结构,所述定位板的开口内侧与所述待加工玻璃盖板的尺寸相匹配,所述玻璃盖板热弯制备工艺至少包括如下步骤:步骤1,在所述下模的上表面置放至少四个所述玻璃球;步骤2,将所述型腔放置在所述玻璃球上,所述型腔下表面与所述下模的上表面平行;步骤3,在所述型腔上表面置放所述待加工玻璃盖板,所述定位板用于固定放置在所述型腔上的玻璃盖板;步骤4,对所述待加工玻璃盖板加热后施加压力,所述待加工玻璃盖板与所述玻璃球软化并在受压后变形。与现有技术相比,本发明所提供的玻璃盖板热弯模具10与所述玻璃盖板热弯制备系统90具有如下的优点:1、本发明所提供的玻璃盖板热弯模具10、所述玻璃盖板热弯制备系统90与所述玻璃盖板热弯制备工艺中,通过所述待加工玻璃盖板之下设置至少四个玻璃球601,并使所述待加工玻璃盖板与所述玻璃球601共同受热软化的状态下,受压后变形,由于所述玻璃球601的设置,可使原施加在所述待加工玻璃盖板上的力作用(如应力)均匀分散,从而减少所述待加工玻璃盖板的局部受到过大的压力而出现不均或应力集中的问题。2、本发明所提供的玻璃盖板热弯模具10与所述玻璃盖板热弯制备系统90中所述型腔30的下表面与所述下模40的上表面上分别设置有数量与位置相匹配的所述第一圆形凹槽31与所述第二圆形凹槽42,所述玻璃球601的上曲面与下曲面分别与所述第一圆形凹槽31与所述第二圆形凹槽42接触,此时,所述型腔30与所述下模40不接触却具有间隙,所述间隙的设置为所述玻璃球在受热变形后可具有一定的变形挤压空间,可利于所述玻璃球601的自由形变。3、所述玻璃球601直径选为6-12mm,采用上述直径大小的所述玻璃球601可获得最优的形变挤压效果。4、本发明所提供的玻璃盖板热弯模具10与所述玻璃盖板热弯制备系统90中所述凸台21的下表面与所述型腔30的上表面相对设置,所述凸台21与所述待加工玻璃盖板尺寸相当,从而在下压时,可获得较佳的压合作用。5、所述弧面边211与所述弧形凹槽44的匹配设置,从而可使所述待加工玻璃盖板的内表面与外表面可同时受到力的作用,使所述待加工玻璃盖板内外表面力平衡且成型程度相当,因此,可获得更优的玻璃盖板热弯成型效果。6、本发明所提供的所述玻璃盖板热弯制备系统90中可进一步包括至少一加热工段(如加热工段91与温度调整工段93)、一成型工段92、一冷却工段(如第一冷却工段94与第二冷却工段95)及一传送装置,所述玻璃盖板热弯模具10由所述传送装置带动并依次进入所述加热工段、所述成型工段92及所述冷却工段进行加热、施压及冷却操作,从而实现玻璃盖板热弯制备的自动化操作。与现有使用单一腔室进行玻璃盖板热弯制备系统相比,采用本发明可实现在玻璃盖板热弯制备自动化,且玻璃盖板热弯制备的温度与按压力可调且可保持为恒定值,而无需对反应腔体内部不断进行升降温操作,具有更高的生产效率且节省能耗。7、采用本发明中所述玻璃盖板热弯模具10制备获得的非平面玻璃盖板与采用冷加工、现有热弯成型工艺的制备或的非平面玻璃盖板相比,具有更优品质且不易形成细小的裂缝,与现有技术相比,本发明所提供的所述玻璃盖板热弯模具10、所述玻璃盖板热弯制备系统90与所述玻璃盖板热弯制备工艺适用性强且操作简便,良品率高。以上所述仅为本发明的较佳实施例而已,并不用以限制本发明,凡在本发明的原则之内所作的任何修改,等同替换和改进等均应包含本发明的保护范围之内。