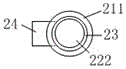
本发明涉及材料加工领域,具体涉及一种连续研磨挤出制备石墨烯复合材料的设备及其方法。
背景技术:
:2004年石墨烯材料被成功制备,自此引发了新一波碳素材料研究的热潮。石墨烯是由一层碳原子组成的平面碳纳米材料,是目前已知最薄的二维材料,其厚度仅为0.335nm,它由六方的晶格组成。石墨烯中的碳原子之间由σ键连接,赋予了石墨烯极其优异的力学性质和结构刚性。而且,在石墨烯中,每个碳原子都有一个未成键的p电子,这些p电子可以在晶体中自由移动,且运动速度高达光速的1/300,赋予了石墨烯良好的导电性。在光学方面,石墨烯几乎是完全透明的,只吸收2.3%的光。石墨烯具有奇特的力学、光学和电学性质,石墨烯拥有十分广阔的发展前景。机械剥离法制备石墨烯方法简单,制备过程环保无污染,生产成本较为低廉,在工业生产中备受青睐。螺杆挤出机是一种连续化高剪切设备,主要是利用螺杆机的啮合剪切,借助研磨、分散物料实现剪切剥离。特点是剪切功能强大、可连续化、适应性较广。利用螺杆剥离制备石墨烯,不但对石墨层的冲击压力极小,而且通过改进剪切螺纹块,以平行于石墨层面的方向被剪切剥离。但用于剥离石墨烯时存在剥离强度低、剥离层数厚等缺陷。为了克服普通螺杆机在制备石墨烯过程中存在的上述缺陷,中国发明专利申请号CN201510815664公开了一种利用螺杆机剪切连续制备石墨烯材料的方法,利用连续旋转的同向啮合螺杆机,将石墨预混物沿螺杆旋转方向均匀分散开,形成片形的取向,通过啮合螺纹元件定向的方向剪切剥离,在螺杆同向旋转过程中螺杆啮合螺纹元件间界面产生高剪切应力,从而形成了大尺寸面积的石墨烯。该方案提供的螺杆机需要分段设计各种不同类型的螺杆啮合螺纹元件来实现碳原料的连续碳化、还原和剪切剥离,螺杆的机械结构较为复杂,易损耗,并且在同一螺杆机上靠零部件的替换无法进一步提高剪切强度,降低剥离石墨烯层数。中国发明专利申请号CN201510965633公开了一种利用石墨烯量子点机械剥离制备石墨烯的方法,采用石墨烯量子点作为剥离剂,超临界氨气作为输运载体,置于高压釜内,通入氨气,降低温度使处于超临界状态下的氨气固化,用螺杆挤出机机械剥离所述低温固态复合碳素材料,获得所述固态复合碳素材料的挤出物,降压升温至常压常温,所述挤出物膨化,获得膨化产物并进行超声分离,获得石墨烯粉。该方案采用石墨烯量子点和超临界氨气作为剥离介质,虽然能够有效制备出质量较高的石墨烯产品,但整个工艺过程不易控制,并且制备成本较高,不利于大规模工业化生产。中国发明专利申请号CN201510893731公开了一种利用晶型诱导在螺杆挤出机中制备石墨烯的方法,通过螺杆挤出机对碳源的剪切切片,利用晶型诱导剂在一定温度下对碳源进行诱导,使碳源形成晶体并沿层生长,获得层结构明显的石墨,接着利用螺杆挤出机挤出获得石墨烯,该方案能够获得厚度小于10nm,结构完整的大尺寸二维面积石墨烯,但该方案采用晶型诱导需要对反应温度、压力、以及反应物在螺杆中停留反应的时间进行精确控制,对生产工艺条件有较高要求。由此可知,为了提高螺杆机剥离石墨烯的效率,降低剥离石墨烯层数,现有技术中通过改进螺杆机械机构的方式能够一定程度提高螺杆机的机械剥离强度,获得较薄的石墨烯产品,但是螺杆的机械结构较为复杂,进一步提高机械剥离强度较为困难。再者,在利用螺杆机进行机械剥离之前,采用超临界气体以及晶型诱导剂等方案对剥离原材料进行加工,接着利用螺杆挤出机机械剥离处理后的原材料,虽然能够提高螺杆机机械剥离效率,获得厚度较薄的石墨烯产品,但整个工艺过程较为复杂,不易控制,需要精确掌握工艺参数,过程连续化程度也不及单纯机械剥离的高,进而导致生产周期及成本增加等问题。技术实现要素:针对现有技术中利用螺杆剥离制备石墨烯剥离强度低、剥离层数厚等缺陷,现有技术中的方案存在螺杆机械结构较为复杂、制备工艺过程不易控制等缺陷,本发明提出一种连续研磨挤出制备石墨烯复合材料的设备及其方法,在提高剪切强度的同时实现了连续生产,进一步,获得了剥离厚度薄的石墨烯复合产品,防止石墨烯团聚,便于储存,推动了石墨烯的量产化生产。为解决上述问题,本发明采用以下技术方案:一方面提供一种连续研磨挤出制备石墨烯复合材料的设备,包括:进料机构,由同向啮合螺杆组或反向啮合螺杆组构成;剥离机构,与所述进料机构相连通;驱动机构,包括一电机设备,与所述进料机构和所述剥离机构连接导通,用于驱动所述进料机构以及所述剥离机构;收集机构,用于收集石墨烯复合材料;其中,所述剥离机构包括配合的内、外磨盘,将石墨原料和塑性剥离剂通过所述进料机构进行初级剥离同时将初级剥离产物输送到所述剥离机构,通过所述剥离机构对所述初级剥离产物再次剪切剥离,通过所述收集机构收集获得石墨烯复合材料。优选的,所述进料机构上开设至少一个喂料口。优选的,所述同向啮合螺杆组是同向啮合双螺杆组、同向啮合三螺杆组、同向啮合四螺杆组或同向啮合四螺杆以上的螺杆组中的一种;所述反向啮合螺杆组是反向啮合双螺杆组、反向啮合三螺杆组、反向啮合四螺杆组或者反向啮合四螺杆以上的螺杆组中的一种;所述同向啮合螺杆组或反向啮合螺杆组长径比大于5/1、螺杆直径为20-150mm。所述同向啮合螺杆组或反向啮合螺杆组是由螺纹元件在芯轴上组合而成,通过螺纹元件,使石墨和塑性剥离剂在螺杆旋转时沿纵向和横向方向进行初级剥离同时将初级剥离产物输送到所述剥离机构。优选的,所述螺纹元件由两组56/56输送螺纹元件、四组斜角为30°的啮合螺纹元件、四组斜角为45°的啮合螺纹元件、六组斜角为60°的啮合螺纹元件组成。优选的,所述外磨盘套置在所述内磨盘外表面,所述内、外磨盘之间形成一环状空间,所述外磨盘侧壁设有至少一个上进料口,将所述进料机构和所述环状空间进行连通;所述环状空间的内外径之差为1-5mm;所述外磨盘第一端面被密封,形成的密封面上设有一进液口,与一高压进液管紧密连接;所述外磨盘第二端面与所述收集机构相连通;所述外磨盘内侧面设有凹槽,所述凹槽的深度为0.5-5mm;通过驱动机构对所述内磨盘进行驱动,为内、外磨盘之间提供剪切力,使所述初级剥离产物再次剪切剥离后,通过控制所述高压进液管中液体压强0.1-10MPa,将剥离产物冲入所述收集机构。优选的,所述内磨盘的侧面设有毛毡或磨砂部;所述内、外磨盘为耐磨陶瓷或耐磨塑料;或所述内、外磨盘在两者相互靠近的两侧面覆盖耐磨陶瓷层或耐磨塑料层。另一方面,提供一种利用连续研磨挤出制备石墨烯复合材料的方法,向设备的喂料口加入质量比为1:0.1-1的石墨原料和塑性剥离剂,接通驱动机构,调节所述进料机构转速为50-350rpm,进行初级剥离同时将初级剥离产物输送到剥离机构,设置剥离机构转速为500-1500rpm,通过所述剥离机构对所述初级剥离产物再次剪切剥离,物料在被剥离的同时,被输送到达所述收集机构,所述收集机构收集获得石墨烯复合材料;优选的,所述塑性剥离剂为PE高分子蜡、阳离子淀粉、巴西棕榈蜡和氧化聚乙烯蜡中的至少一种。现有方案提供的螺杆机需要分段设计各种不同类型的螺杆啮合螺纹元件来实现增加螺杆机剥离强度,尽管产生剪切获得了石墨烯,但螺杆螺纹元件较为复杂,易变形损耗。并且采用超临界气体以及晶型诱导剂等方案对原材料进行加工,接着利用螺杆挤出机剥离处理后的原材料,虽然能够提高螺杆机机械剥离效率,获得厚度较薄的石墨烯产品,但整个过程较为复杂,不易控制。鉴于此,本发明提出一种连续研磨挤出制备石墨烯复合材料的设备及其方法,将石墨和塑性剥离剂通过由螺杆组构成的进料机构对原料进行取向剪切,获得初级剥离产物,同时将初级剥离产物输送到磨盘组构成的剥离机构,通过内、外磨盘的相对转动,对初级剥离产物再次剪切剥离,获得石墨烯复合材料。装置结构简单,在提高剪切强度的同时实现了连续生产,进一步,获得了剥离厚度薄的石墨烯复合产品,避免了石墨烯团聚,提高了石墨烯的质量,便于储存,推动了石墨烯的量产化生产。将本发明所制备石墨烯性能与改进螺杆机械结构的挤出机制备的石墨烯、添加量子点以氨气为载体制备石墨烯以及晶型诱导制备石墨烯相比,在石墨烯质量、产量、成本等方面具有的优势如表1所示。表1:本发明一种连续研磨挤出制备石墨烯复合材料的设备及其方法,与现有技术相比,其突出的特点和优异的效果在于:1、本发明采用连续研磨挤出剥离石墨的方法,第一级采用螺杆机初级剥离,降低石墨尺寸,再通过内外盘提供的机械剪切力,对石墨精细剥离,增加剥离强度,获得厚度较薄的石墨烯产品。2、本发明制备的石墨烯复合材料,有效防止了石墨烯的团聚,增加了石墨烯的分散性,便于存储。3、本发明所涉及到石墨烯复合材料的制备工艺采用液体取样,避免了制备的石墨烯片层结构的破坏,制得晶体结构完整,导电性较好的石墨烯。4、本发明制备石墨烯复合材料的设备及方法,剥离效率高,连续制备产量大,制备周期较短,提高了石墨烯的生产效率,可以适用于规模化工业生产。附图说明为进一步明本发明中连续研磨挤出制备石墨烯复合材料的设备及其方法,通过附图进行说明。附图1:本发明中一种连续研磨挤出制备石墨烯复合材料的设备的结构示意图;附图2:本发明中一种连续研磨挤出制备石墨烯复合材料设备中剥离机构的俯视图;附图3:本发明中一种连续研磨挤出制备石墨烯复合材料设备中剥离机构内、外磨盘的结构示意图。具体实施方式以下通过具体实施方式对本发明作进一步的详细说明,但不应将此理解为本发明的范围仅限于以下的实例。在不脱离本发明上述方法思想的情况下,根据本领域普通技术知识和惯用手段做出的各种替换或变更,均应包含在本发明的范围内。实施例1如图1所示,本发明中的一种连续研磨挤出制备石墨烯复合材料的设备,沿工艺顺序依次包括进料机构10、与进料机构10相连通的剥离机构20、用于收集石墨烯复合材料收集机构30,以及驱动机构40,包括一电机设备,与进料机构10和剥离机构20连接导通,用于单独或同时驱动进料机构10以及剥离机构20。进料机构10上开设一个喂料口13。进料机构10由同向啮合螺杆组11构成,在实施过程中,同向啮合螺杆组11可以为同向啮合双螺杆组、同向啮合三螺杆组、同向啮合四螺杆组或同向啮合四螺杆以上的螺杆组中的一种,在本实施例中以同向啮合双螺杆组为例进行说明,同向啮合螺杆组长径比为10/1、螺杆直径为20mm。同向啮合螺杆组是由螺纹元件在芯轴上组合而成,通过两组56/56输送螺纹元件、四组斜角为30°的啮合螺纹元件、四组斜角为45°的啮合螺纹元件、六组斜角为60°的啮合螺纹元件,使石墨原料和塑性剥离剂在螺杆旋转时,沿纵向和横向方向提供剪切力,将石墨原料剪切剥离,并不断分散将物料混合均匀。结合如图2所示,剥离机构20包括配合的内、外磨盘21,所述外磨盘套置在所述内磨盘外表面,所述内、外磨盘之间形成一环状空间23,所述外磨盘侧壁设有至少一个上进料口24,将进料机构20和环状空间23进行连通。环状空间的内外径之差为1mm,外磨盘211第一端面被密封,形成的密封面上设有一进液口,与一高压进液管25密封连接;外磨盘211第二端面与收集机构30相连通,外磨盘211内侧面设有凹槽212,所述凹槽的深度为0.5mm;内磨盘222的侧面设有毛毡223,如图3所示;内、外磨盘21的材质为耐磨陶瓷或耐磨塑料。通过驱动机构对所述内磨盘进行驱动,为内、外磨盘21之间提供剪切力,对石墨精细剥离,增加剥离强度,获得厚度较薄的石墨烯,通过高压进液管25对环状空间充入水,控制水压为0.1Mpa,将层片厚度小于5nm的剥离产物冲入收集机构30,进而避免了收集过程中对石墨烯复合材料的结构的破坏。利用实施例1中的装置制备石墨烯复合材料的方法如下:在实施过程中,石墨原料可以是鳞片石墨、膨胀石墨、高取向石墨、热裂解石墨、氧化石墨的粉体中的至少一种,塑性剥离剂为PE高分子蜡、阳离子淀粉、巴西棕榈蜡和氧化聚乙烯蜡中的至少一种,在本实施例中以鳞片石墨粉和阳离子淀粉为例进行说明,本领域技术人员可以根据需要进行选择。向喂料口13加入质量比为1:0.2的鳞片石墨粉和阳离子淀粉混合物,接通驱动机构40,调节进料机构10转速为50rpm,经过同向啮合双螺杆组混合、剥离、输运后,将初级剥离产物输送到剥离机构20。设置剥离机构20转速为500rpm,通过剥离机构30对初级剥离产物再次剪切剥离,同时被输送到达所述收集机构30,所述收集机构30收集获得石墨烯复合材料,经过蒸发干燥获得石墨烯复合材料。对实施例1中制备获得的石墨烯复合材料进行性能测试后,获得数据如表2所示。实施例2如图1所示,本发明中的一种连续研磨挤出制备石墨烯复合材料的设备,沿工艺顺序依次包括进料机构10、与进料机构10相连通的剥离机构20、用于收集石墨烯复合材料收集机构30,以及驱动机构40,包括一电机设备,与进料机构10和剥离机构20连接导通,用于驱动进料机构10以及剥离机构20。其中,进料机构10由同向啮合螺杆组11构成,进料机构10上开设至少一个喂料口13。在实施过程中,同向啮合螺杆组11可以为同向啮合双螺杆组、同向啮合三螺杆组、同向啮合四螺杆组或同向啮合四螺杆以上的螺杆组中的一种,在本实施例中以同向啮合双螺杆组为例进行说明,同向啮合螺杆组长径比为10/1、螺杆直径为30mm。同向啮合螺杆组是由螺纹元件在芯轴上组合而成,通过两组56/56输送螺纹元件、四组斜角为30°的啮合螺纹元件、四组斜角为45°的啮合螺纹元件、六组斜角为60°的啮合螺纹元件,使石墨原料和塑性剥离剂在螺杆旋转时,沿纵向和横向方向提供剪切力,将石墨原料剪切剥离,并不断分散将物料混合均匀。结合如图2所示,剥离机构20包括配合的内、外磨盘21,所述外磨盘套置在所述内磨盘外表面,所述内、外磨盘之间形成一环状空间23,所述外磨盘侧壁设有至少一个上进料口24,将进料机构20和环状空间23进行连通。环状空间的内外径之差为1mm,外磨盘211第一端面被密封,形成的密封面上设有一进液口,与一高压进液管25密封连接;外磨盘211第二端面与收集机构30相连通,外磨盘211内侧面设有凹槽212,所述凹槽的深度为0.5mm;内磨盘222的侧面设有毛毡223,如图3所示;内、外磨盘21的材质为耐磨陶瓷或耐磨塑料。通过驱动机构对所述内磨盘进行驱动,为内、外磨盘21之间提供剪切力,对石墨精细剥离,增加剥离强度,获得厚度较薄的石墨烯,通过高压进液管25对环状空间充入水,控制水压为0.5Mpa,将层片厚度小于5nm的剥离产物冲入收集机构30,进而避免了收集过程中对石墨烯复合材料的结构的破坏。利用实施例2中的装置制备石墨烯复合材料的方法如下:在实施过程中,石墨原料可以是鳞片石墨、膨胀石墨、高取向石墨、热裂解石墨、氧化石墨的粉体中的至少一种,塑性剥离剂为PE高分子蜡、阳离子淀粉、巴西棕榈蜡和氧化聚乙烯蜡中的至少一种,在本实施例中以膨胀石墨粉和PE高分子蜡为例进行说明,本领域技术人员可以根据需要进行选择。向喂料口13加入质量比为1:0.5的膨胀石墨粉和PE高分子蜡混合物,接通驱动机构40,调节进料机构10转速为150rpm,经过同向啮合双螺杆组混合、剥离、输运后,将初级剥离产物输送到剥离机构20。设置剥离机构20转速为800rpm,通过剥离机构30对初级剥离产物再次剪切剥离,同时被输送到达所述收集机构30,所述收集机构30收集获得石墨烯复合材料,经过蒸发干燥获得石墨烯复合材料。对实施例2中制备获得的石墨烯复合材料进行性能测试后,获得数据如表2所示。实施例3如图1所示,本发明中的一种连续研磨挤出制备石墨烯复合材料的设备,沿工艺顺序依次包括进料机构10、与进料机构10相连通的剥离机构20、用于收集石墨烯复合材料收集机构30,以及驱动机构40,包括一电机设备,与进料机构10和剥离机构20连接导通,用于驱动进料机构10以及剥离机构20。其中,进料机构10由同向啮合螺杆组11构成,进料机构10上开设至少一个喂料口13。在实施过程中,同向啮合螺杆组11可以为同向啮合双螺杆组、同向啮合三螺杆组、同向啮合四螺杆组或同向啮合四螺杆以上的螺杆组中的一种,在本实施例中以同向啮合双螺杆组为例进行说明,同向啮合螺杆组长径比为10/1、螺杆直径为30mm。同向啮合螺杆组是由螺纹元件在芯轴上组合而成,通过两组56/56输送螺纹元件、四组斜角为30°的啮合螺纹元件、四组斜角为45°的啮合螺纹元件、六组斜角为60°的啮合螺纹元件,使石墨原料和塑性剥离剂在螺杆旋转时,沿纵向和横向方向提供剪切力,将石墨原料剪切剥离,并不断分散将物料混合均匀。结合如图2所示,剥离机构20包括配合的内、外磨盘21,所述外磨盘套置在所述内磨盘外表面,所述内、外磨盘之间形成一环状空间23,所述外磨盘侧壁设有至少一个上进料口24,将进料机构20和环状空间23进行连通。环状空间的内外径之差为1mm,外磨盘211第一端面被密封,形成的密封面上设有一进液口,与一高压进液管25密封连接;外磨盘211第二端面与收集机构30相连通,外磨盘211内侧面设有凹槽212,所述凹槽的深度为0.5mm;内磨盘222的侧面设有毛毡223,如图3所示;内、外磨盘21的材质为耐磨陶瓷或耐磨塑料。通过驱动机构对所述内磨盘进行驱动,为内、外磨盘21之间提供剪切力,对石墨精细剥离,增加剥离强度,获得厚度较薄的石墨烯,通过高压进液管25对环状空间充入植物油,控制油压为3.5Mpa,将层片厚度小于5nm的剥离产物冲入收集机构30,进而避免了收集过程中对石墨烯复合材料的结构的破坏。利用实施例3中的装置制备石墨烯复合材料的方法如下:在实施过程中,石墨原料可以是鳞片石墨、膨胀石墨、高取向石墨、热裂解石墨、氧化石墨的粉体中的至少一种,塑性剥离剂为PE高分子蜡、阳离子淀粉、巴西棕榈蜡和氧化聚乙烯蜡中的至少一种,在本实施例中以膨胀石墨粉和阳离子淀粉为例进行说明,本领域技术人员可以根据需要进行选择。向喂料口13加入质量比为1:0.8的膨胀石墨粉和阳离子淀粉混合物,接通驱动机构40,调节进料机构10转速为200rpm,经过同向啮合双螺杆组混合、剥离、输运后,将初级剥离产物输送到剥离机构20。设置剥离机构20转速为1200rpm,通过剥离机构30对初级剥离产物再次剪切剥离,同时被输送到达所述收集机构30,所述收集机构30收集获得石墨烯复合材料,经过蒸发干燥获得石墨烯复合材料。对实施例3中制备获得的石墨烯复合材料进行性能测试后,获得数据如表2所示。实施例4如图1所示,本发明中的一种连续研磨挤出制备石墨烯复合材料的设备,沿工艺顺序依次包括进料机构10、与进料机构10相连通的剥离机构20、用于收集石墨烯复合材料收集机构30,以及驱动机构40,包括一电机设备,与进料机构10和剥离机构20连接导通,用于驱动进料机构10以及剥离机构20。其中,进料机构10由同向啮合螺杆组11构成,进料机构10上开设至少一个喂料口13。在实施过程中,同向啮合螺杆组11可以为同向啮合双螺杆组、同向啮合三螺杆组、同向啮合四螺杆组或同向啮合四螺杆以上的螺杆组中的一种,在本实施例中以同向啮合双螺杆组为例进行说明,同向啮合螺杆组长径比为10/1、螺杆直径为50mm。同向啮合螺杆组是由螺纹元件在芯轴上组合而成,通过两组56/56输送螺纹元件、四组斜角为30°的啮合螺纹元件、四组斜角为45°的啮合螺纹元件、六组斜角为60°的啮合螺纹元件,使石墨原料和塑性剥离剂在螺杆旋转时,沿纵向和横向方向提供剪切力,将石墨原料剪切剥离,并不断分散将物料混合均匀。结合如图2所示,剥离机构20包括配合的内、外磨盘21,所述外磨盘套置在所述内磨盘外表面,所述内、外磨盘之间形成一环状空间23,所述外磨盘侧壁设有至少一个上进料口24,将进料机构20和环状空间23进行连通。环状空间的内外径之差为5mm,外磨盘211第一端面被密封,形成的密封面上设有一进液口,与一高压进液管25密封连接;外磨盘211第二端面与收集机构30相连通,外磨盘211内侧面设有凹槽212,所述凹槽的深度为0.5mm;内磨盘222的侧面设有毛毡223,如图3所示;内、外磨盘21的材质为耐磨陶瓷或耐磨塑料。通过驱动机构对所述内磨盘进行驱动,为内、外磨盘21之间提供剪切力,对石墨精细剥离,增加剥离强度,获得厚度较薄的石墨烯,通过高压进液管25对环状空间充入异丙醇,控制液压为5Mpa,将层片厚度小于5nm的剥离产物冲入收集机构30,进而避免了收集过程中对石墨烯复合材料的结构的破坏。利用实施例4中的装置制备石墨烯复合材料的方法如下:在实施过程中,石墨原料可以是鳞片石墨、膨胀石墨、高取向石墨、热裂解石墨、氧化石墨的粉体中的至少一种,塑性剥离剂为PE高分子蜡、阳离子淀粉、巴西棕榈蜡和氧化聚乙烯蜡中的至少一种,在本实施例中以热裂解石墨粉和巴西棕榈蜡为例进行说明,本领域技术人员可以根据需要进行选择。向喂料口13加入质量比为1:0.9的热裂解石墨粉和巴西棕榈蜡混合物,接通驱动机构40,调节进料机构10转速为250rpm,经过同向啮合双螺杆组混合、剥离、输运后,将初级剥离产物输送到剥离机构20。设置剥离机构20转速为1200rpm,通过剥离机构30对初级剥离产物再次剪切剥离,同时被输送到达所述收集机构30,所述收集机构30收集获得石墨烯复合材料,经过蒸发干燥获得石墨烯复合材料。对实施例4中制备获得的石墨烯复合材料进行性能测试后,获得数据如表2所示。实施例5如图1所示,本发明中的一种连续研磨挤出制备石墨烯复合材料的设备,沿工艺顺序依次包括进料机构10、与进料机构10相连通的剥离机构20、用于收集石墨烯复合材料收集机构30,以及驱动机构40,包括一电机设备,与进料机构10和剥离机构20连接导通,用于驱动进料机构10以及剥离机构20。其中,进料机构10由同向啮合螺杆组11构成,进料机构10上开设至少一个喂料口13。在实施过程中,同向啮合螺杆组11可以为同向啮合双螺杆组、同向啮合三螺杆组、同向啮合四螺杆组或同向啮合四螺杆以上的螺杆组中的一种,在本实施例中以同向啮合双螺杆组为例进行说明,同向啮合螺杆组长径比为10/1、螺杆直径为150mm。同向啮合螺杆组是由螺纹元件在芯轴上组合而成,通过两组56/56输送螺纹元件、四组斜角为30°的啮合螺纹元件、四组斜角为45°的啮合螺纹元件、六组斜角为60°的啮合螺纹元件,使石墨原料和塑性剥离剂在螺杆旋转时,沿纵向和横向方向提供剪切力,将石墨原料剪切剥离,并不断分散将物料混合均匀。结合如图2所示,剥离机构20包括配合的内、外磨盘21,所述外磨盘套置在所述内磨盘外表面,所述内、外磨盘之间形成一环状空间23,所述外磨盘侧壁设有至少一个上进料口24,将进料机构20和环状空间23进行连通。环状空间的内外径之差为3mm,外磨盘211第一端面被密封,形成的密封面上设有一进液口,与一高压进液管25密封连接;外磨盘211第二端面与收集机构30相连通,外磨盘211内侧面设有凹槽212,所述凹槽的深度为0.5mm;内磨盘222的侧面设有毛毡223,如图3所示;内、外磨盘21的材质为耐磨陶瓷或耐磨塑料。通过驱动机构对所述内磨盘进行驱动,为内、外磨盘21之间提供剪切力,对石墨精细剥离,增加剥离强度,获得厚度较薄的石墨烯,通过高压进液管25对环状空间充入异丁醇,控制液压为10Mpa,将层片厚度小于5nm的剥离产物冲入收集机构30,进而避免了收集过程中对石墨烯复合材料的结构的破坏。利用实施例5中的装置制备石墨烯复合材料的方法如下:在实施过程中,石墨原料可以是鳞片石墨、膨胀石墨、高取向石墨、热裂解石墨、氧化石墨的粉体中的至少一种,塑性剥离剂为PE高分子蜡、阳离子淀粉、巴西棕榈蜡和氧化聚乙烯蜡中的至少一种,在本实施例中以高取向石墨粉和氧化聚乙烯蜡为例进行说明,本领域技术人员可以根据需要进行选择。向喂料口13加入质量比为1:1的高取向石墨粉和氧化聚乙烯蜡混合物,接通驱动机构40,调节进料机构10转速为100rpm,经过同向啮合双螺杆组混合、剥离、输运后,将初级剥离产物输送到剥离机构20。设置剥离机构20转速为1500rpm,通过剥离机构30对初级剥离产物再次剪切剥离,同时被输送到达所述收集机构30,所述收集机构30收集获得石墨烯复合材料,经过蒸发干燥获得石墨烯复合材料。对实施例5中制备获得的石墨烯复合材料进行性能测试后,获得数据如表2所示。表2性能指标90%石墨烯片径向大小90%石墨烯厚度剥离效率实施例一50-60μm0.3-1.2nm25.1%实施例二50-70μm0.7-2.3nm29.4%实施例三60-70μm1.3-2.0nm30.8%实施例四70-100μm3.3-4.2nm29.1%实施例五80-100μm3.3-5.0nm38.3%当前第1页1 2 3