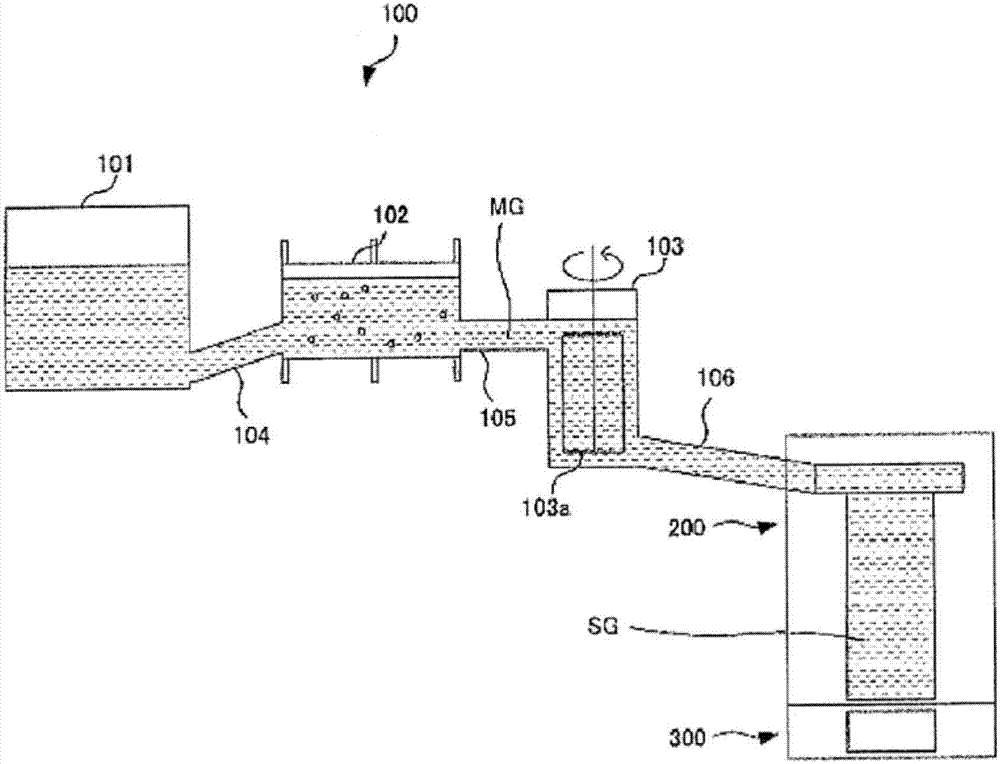
本发明涉及一种玻璃衬底的制造方法、及玻璃衬底的制造装置。
背景技术:
:有时为制造用于液晶显示器或等离子体显示器等平板显示器的玻璃衬底(以下,称为「显示器用玻璃衬底」),而使用溢流下拉法。溢流下拉法包括如下步骤:通过在成形炉中使熔融玻璃自成形体的上部溢出(overflow)而在成形体的下方成形板状的平板玻璃、及使平板玻璃在缓冷炉中缓冷的冷却步骤。在缓冷炉中,将平板玻璃引入成对的辊间,利用辊将平板玻璃一面搬运至下方一边拉拔成所需的厚度后,将平板玻璃进行缓冷。此后,通过将平板玻璃截断为特定的尺寸而形成玻璃板。沿着成形体的侧面向下流动的熔融玻璃在离开成形体的同时,因表面张力而在平板玻璃的宽度方向上收缩。专利文献1中,公开有如下方法,即,在成形体与成形体下方的张力辊之间,在平板玻璃的宽度方向的缘部附近,使用与平板玻璃相隔地设置的冷却单元,调整平板玻璃的缘部的温度,抑制平板玻璃的收缩。此后,收缩被抑制的平板玻璃穿过缓冷空间而成形。在该缓冷空间中,环境温度以成为所需的温度轮廓(玻璃板中不产生应变的温度分布)的方式得到控制,从而抑制玻璃板的板厚偏差、翘曲、应变。[
背景技术:
文献][专利文献][专利文献1]日本专利特开平5-124827号公报技术实现要素:[发明要解决的问题]近年来,在液晶显示装置用玻璃衬底中,对规格(品质)的要求日益严格。对玻璃衬底的表面要求较高的平坦性,为满足要求规格,尤其必须抑制陡峭的凹或凸导致产生条纹(striae)或局部的板厚偏差。该条纹是在特定的宽度中平板玻璃的厚度(高度)变动所致的凹凸,且因离开成形体的同时,因表面张力而在平板玻璃的宽度方向上收缩所致,且在平板玻璃的搬运方向上纹路状连续地产生。因此,本发明的目的在于提供一种可抑制包含平板玻璃上产生的条纹的局部的板厚偏差的玻璃衬底的制造方法、及玻璃衬底的制造装置。[解决问题的技术手段]本发明的一形态是一种将熔融玻璃自玻璃供给管供给至具有供给槽的成形体,使用所述成形体通过溢流下拉法成形平板玻璃的玻璃衬底的制造方法。在该制造方法中,所述供给槽具有供给至所述供给槽的熔融玻璃自所述供给槽溢出的量在所述供给槽的延伸方向及与所述延伸方向正交的宽度方向上达到均一的底面形状,所述玻璃衬底的制造方法具有:成形步骤,将自所述玻璃供给管供给至所述供给槽的熔融玻璃的最大温度差为30℃以下且熔融玻璃的粘度为22000dpa·s以上38000dpa·s以下的熔融玻璃供给至所述供给槽,且在所述成形体的下端使所述熔融玻璃汇流,成形平板玻璃;及端部冷却步骤,以抑制在所述成形步骤中成形所得的所述平板玻璃中局部产生的板厚偏差的方式,将平板玻璃的宽度方向的两端部冷却。在所述端部冷却步骤中,优选将所述成形体在所述平板玻璃的宽度方向上未变形时施加的且所述平板玻璃的剖面形状成为目标形状的张力设为基准张力,在所述成形体未变形时,以通过将所述平板玻璃的宽度方向的两端部冷却而达到所述基准张力的方式进行控制,且在所述成形体产生变形时,对于所述平板玻璃施加根据所述成形体的变形而与所述基准张力相加的张力。此时,优选所述成形体的变形是随着所述成形体的使用而经时变化的蠕变变形,且对所述基准张力加上与所述蠕变变形造成的所述成形体的特定位置的位移量相应的张力。而且,优选随着所述变形变大,而增强所述两端部的冷却。优选所述板厚偏差为10μm以下。在所述成形步骤中,优选以在所述成形体中向下流动的熔融玻璃的温度比所述熔融玻璃的液相温度增高10℃~150℃的方式,加热所述熔融玻璃。本发明的其他一形态是一种将熔融玻璃自玻璃供给管供给至具有供给槽的成形体,使用所述成形体通过溢流下拉法成形平板玻璃的玻璃衬底的制造装置。所述成形体具有接收最大温度差为30℃以下且粘度为22000dpa·s以上38000dpa·s以下的熔融玻璃供给的供给槽、及用以在所述成形体的下端使所述熔融玻璃汇流而成形平板玻璃的壁面。所述供给槽具有供给至所述供给槽的熔融玻璃自所述供给槽溢出的量在所述供给槽的延伸方向及与所述延伸方向正交的宽度方向上达到均一的底面形状。所述制造装置更具备以抑制利用所述成形体成形所得的所述平板玻璃中局部产生的板厚偏差的方式冷却平板玻璃的宽度方向的两端部的端部冷却装置。[发明的效果]根据所述形态的玻璃衬底的制造方法及玻璃衬底的制造装置,可抑制平板玻璃中产生的局部性板厚偏差。附图说明图1是表示本实施方式的制造方法的流程的图。图2是玻璃衬底的制造装置的概略图。图3是表示可在本实施方式的制造方法中使用的成形体的一例的立体图。图4是说明使用图3所示的装置的本发明的制造方法的一例的图。图5是表示与成形体的供给槽连接的玻璃供给管的剖面的图。图6是表示本实施方式中使用的玻璃供给管的长边方向上的在玻璃供给管之中流动的熔融玻璃的温度变化的图表。图7是说明利用获取部所获取的成形体的形状变化之例的图。图8是表示利用已蠕变变形的成形体所成形的玻璃带的剖面的一例的图。图9是表示成形体的位移量与对玻璃带施加的张力t的关系的图。图10(a)是将沿着图4所示的a-a线的平板玻璃的剖面的一例放大所得的图,(b)是将沿着图4所示的b-b线的平板玻璃的剖面的一例放大所得的图。具体实施方式以下,对本实施方式的玻璃衬底的制造方法进行说明。(玻璃衬底的制造方法的整体概要)图1是表示本实施方式的玻璃衬底的制造方法的步骤的一例的图。玻璃衬底的制造方法主要具有:熔解步骤(st1)、清澄步骤(st2)、均质化步骤(st3)、供给步骤(st4)、成形步骤(st5)、缓冷步骤(st6)、及截断步骤(st7)。其他也可具有研削步骤、研磨步骤、清洗步骤、检查步骤、包装步骤等。制造所得的玻璃衬底视需要在包装步骤中积层后,搬运到订货方的业者。熔解步骤(st1)是通过将玻璃原料加热而制成熔融玻璃。清澄步骤(st2)是通过使熔融玻璃升温,而产生包含熔融玻璃中所含的氧、co2或so2的泡。该泡是吸收因熔融玻璃中所含的澄清剂(氧化锡等)的还原反应而产生的氧进行成长,且漂浮到熔融玻璃的液面而释放。此后,在清澄步骤中,因使熔融玻璃的温度下降,故利用澄清剂的还原反应所得的还原物质进行氧化反应。由此,熔融玻璃中残存的泡中的氧等气体成分被再次吸收到熔融玻璃中,从而泡破灭。澄清剂所进行的氧化反应及还原反应是通过控制熔融玻璃的温度而进行。另外,清澄步骤也可以采用使存在于熔融玻璃中的泡在减压环境下成长后消泡的减压消泡方式。减压消泡方式在不使用澄清剂方面较为有效。然而,减压消泡方式导致装置复杂化及大型化。因此,优选采用使用澄清剂使熔融玻璃温度上升的清澄方法。均质化步骤(st3)是通过使用搅拌器搅拌熔融玻璃,而进行玻璃成分的均质化。由此,可减少作为条纹等原因的玻璃的组成不均。均质化步骤是在下述的搅拌槽中进行。供给步骤(st4)是将搅拌所得的熔融玻璃供给至成形装置。成形步骤(st5)及缓冷步骤(st6)是在成形装置中进行。成形步骤(st5)是将熔融玻璃成形为平板玻璃,制成平板玻璃流。成形中,采用溢流下拉法。缓冷步骤(st6)是将成形后流动的平板玻璃以达到所需的厚度,且不产生内部应变的方式,进而不产生翘曲的方式进行冷却。截断步骤(st7)是通过将缓冷后的平板玻璃截断为特定的长度,而获得板状的玻璃衬底。截断所得的玻璃衬底进而被截断为特定的尺寸,制成目标尺寸的玻璃衬底。图2是进行本实施方式中的熔解步骤(st1)~截断步骤(st8)的玻璃衬底的制造装置的概略图。玻璃衬底的制造装置如图2所示主要具有熔解装置100、成形装置200、及截断装置300。熔解装置100具有熔解槽101、清澄管102、搅拌槽103、输送管104、105、及玻璃供给管106。在图2所示的熔解槽101中,设置有未图示的燃烧器等加热机构。对熔解槽投入已添加澄清剂的玻璃原料,进行熔解步骤(st1)。熔解槽101中已熔融的熔融玻璃是经由输送管104供给至清澄管102。在清澄管102中,调整熔融玻璃mg的温度,利用澄清剂的氧化还原反应进行熔融玻璃的清澄步骤(st2)。具体而言,通过使清澄管102内的熔融玻璃升温,含有熔融玻璃中所含的氧、co2或so2的泡吸收因澄清剂的还原反应而产生的氧而成长,且漂浮至熔融玻璃的液面后释放到气相空间。此后,通过使熔融玻璃的温度下降,因澄清剂的还原反应所得的还原物质进行氧化反应。由此,熔融玻璃中残存的泡中的氧等气体成分被再次吸收到熔融玻璃中,从而泡破灭。清澄后的熔融玻璃是经由输送管105供给至搅拌槽103。在搅拌槽103中,利用搅拌棒103a搅拌熔融玻璃进行均质化步骤(st3)。搅拌槽103中得以均质化的熔融玻璃是经由玻璃供给管106供给至成形装置200(供给步骤st4)。在成形装置200中,利用溢流下拉法,自熔融玻璃成形平板玻璃sg(成形步骤st5),且进行缓冷(缓冷步骤st6)。在截断装置300中,形成自平板玻璃sg切取所得的板状的玻璃衬底(截断步骤st7)。供给步骤s4是控制在玻璃供给管106之中流动的熔融玻璃的温度。具体而言,将玻璃供给管106通电加热,从而将在玻璃供给管106之中流动的熔融玻璃加热,且利用耐火材料将玻璃供给管106包围,由此,抑制在玻璃供给管106之中流动的熔融玻璃的散热。在供给步骤s4中,以在玻璃供给管106之中流动的熔融玻璃的温度自上游侧朝向下游侧逐渐降低的方式,控制熔融玻璃的温度。玻璃供给管106被区分为多个区,熔融玻璃的温度按区进行控制。加热玻璃供给管106的通电加热装置是基于测定装置的测定数据,以熔融玻璃的温度呈现变化的方式,控制流入玻璃供给管106的各区的电流及电压。可通过在玻璃供给管106中控制电流及电压,而将供给至成形装置200的熔融玻璃的温度适当地变更。此处,在玻璃供给管106的下游侧的端部,管温度及熔融玻璃的中心温度优选为1235℃~1265℃,更优选为1240℃~1260℃。(成形体的构成)接着,参照图3及图4,对成形装置200所具备的成形体1的构成进行说明。在图3中,表示可用于本实施方式的制造方法的成形体1的一例,在图4中,表示使用图3所示的成形体1的本实施方式的制造方法中的成形步骤的一例。成形体1具备:上表面3,形成有供给熔融玻璃的供给槽2;一对壁面5(图3、4中仅图示了一壁面),引导自供给槽2的两侧溢出后自上表面3中的供给槽2所延伸的方向的两端部3a、3b之间向下流动的熔融玻璃,在成形体1的下端4汇合成为平板玻璃sg;及一对导件6a、6b,形成在壁面5的宽度方向上的两端部5a、5b的位置处。导件6a、6b分别以在端部5a、5b的位置处自壁面5突出的方式相互对向地形成。自供给槽2溢出的熔融玻璃是在一对壁面5各自之上向下流动。壁面5具有自供给槽2溢出的熔融玻璃在铅垂方向上向下流动的垂直壁面、及将在垂直壁面向下流动的熔融玻璃导向成形体1的下端4且与垂直壁面连接的倾斜壁面。在壁面5向下流动的熔融玻璃的一对流体在成形体1的下端4汇流,从而相互地交汇。此时,利用导件6a、6b,限制沿着壁面5向下流动的熔融玻璃的宽度,从而连续地形成例如宽度方向的厚度均一性较高的平板玻璃sg。成形体1的下端4形成一对壁面5彼此(倾斜壁面彼此)连接的直线状棱线。图3、4所示的符号2a是供给槽2的底面2a,图3所示的符号7是供给至供给槽2的熔融玻璃的液面7。此处,成形体1的供给槽2具有如下的底面2a的形状,即,供给至供给槽2的熔融玻璃自供给槽2溢出的量在供给槽2的延伸方向(熔融玻璃的流动方向)、及与该延伸方向正交的供给槽2的宽度方向上达到均一。在供给槽2中流动的熔融玻璃的流量是根据基于熔融玻璃的粘度、熔融玻璃的密度、供给槽2中流动的熔融玻璃的液面至底面2a为止的深度、及底面2a的宽度的算式运算。通过对该算式,添加熔融玻璃的流量的线密度在自连接有玻璃供给管106的槽始点侧至槽终点侧为止的流动方向上成为固定、即溢出量达到均一的条件,而求出供给槽2的底面2a的形状。而且,成形体1的两端部3a、3b的位置处的供给槽2具有自熔融玻璃溢出至供给槽2的两侧且自上表面3的两端部3a、3b的位置起与其他部分相同地均一溢出的底面2a至上表面3为止的高度。当熔融玻璃自上表面3的两端部3a、3b溢出时,熔融玻璃具有自上表面3至熔融玻璃的液面为止的高度。包含将自溢出时的底面2a至熔融玻璃的液面为止的高度减去自上表面3至熔融玻璃的液面为止的高度所得的底面2a的形状的槽曲线与上表面3的交点成为供给槽2的槽终点。由此,求出连接有玻璃供给管106的供给槽2的自槽始点至槽终点为止的距离,从而决定成形体1的形状。冷却辊8是对平板玻璃sg的宽度方向两端部进行热处理的单元。冷却辊8相较成形体1的下端4配置在更下游侧。而且,冷却辊8配置在平板玻璃sg的厚度方向两侧,且平板玻璃sg的宽度方向两侧。即,冷却辊8在成形体1的正下方对离开成形体1的平板玻璃sg进行热处理。配置在平板玻璃sg的厚度方向两侧的冷却辊8是以对进行动作。因此,平板玻璃sg的宽度方向两端部被二对冷却辊8夹住。冷却辊8是利用通向内部的空气冷却管进行空气冷却。冷却辊8接触于平板玻璃sg的端部sga,利用热传导将平板玻璃sg的端部sga进行淬火(端部冷却步骤)。冷却辊8是以平板玻璃sg的端部sga的粘度达到109.0dpa·s以上的方式,将平板玻璃sg的端部sga进行淬火。另外,冷却辊8优选以平板玻璃sg的端部sga的粘度成为109.0~1014.5dpa·s的范围内的方式,将平板玻璃sg的端部sga进行淬火。在导件6a、6b各自的附近,以自成形体1的上表面3侧延伸至下端4侧的方式配置有加热器,利用该加热器将在一对壁面5上向下流动的熔融玻璃中的导件6a、6b附近的部分、及在壁面5上向下流动的熔融玻璃进行加热。该加热是以在壁面5上向下流动的熔融玻璃中的导件6a、6b附近的部分的粘度自成形体1的上表面3至下端4为止(熔融玻璃的该部分自成形体1的上表面3向下流动至下端4为止),小于构成该熔融玻璃的玻璃组合物的液相粘度(以下,也简称为「液相粘度」)的方式,沿着导件6a、6b进行。在使用具备导件的成形体1的溢流下拉法所进行的平板玻璃sg的成形(及将该平板玻璃sg冷却所得的玻璃衬底的制造)中,容易在导件附近、即成形的平板玻璃sg的端部产生失透。该情况被认为因以下原因造成,即,由于以收容成形体1的成形炉在成形体1的下端将熔融玻璃设为适于成形的粘度为目的,而通常设定为不仅以平板玻璃sg成形为目的而且也以熔融玻璃冷却为目的的温度、即低于熔融玻璃的温度,故而,熔融玻璃的热自导件6a、6b中被夺取,导致导件6a、6b附近的熔融玻璃的温度容易低于熔融玻璃中的其他部分的温度;以及,因如此的温度下降及与导件6a、6b的接触导致的物理性阻力,导件6a、6b附近的熔融玻璃的向下流动速度容易低于熔融玻璃中的其他部分,从而自与导件6a、6b相接触起直至离开成形体1为止需要长时间等。根据日本专利特开2010-215428号公报,存在可抑制在导件的下端产生的失透的可能性。然而,在该文献的技术中,难以抑制相较导件的下端更上游的区域、尤其熔融玻璃与导件接触开始冷却的初期中产生的失透,从而也无法通过导件下端的加热将一次产生的失透消除。而且,在成形包含适于用于平板显示器的玻璃衬底的无碱玻璃及含微量碱玻璃等液相温度较高且液相粘度较小的玻璃组合物、例如本实施方式的制造方法中使用的液相粘度为80000dpa·s以上100000dpa·s以下且液相温度为1200℃~1220℃的范围的玻璃组合物的平板玻璃的情形时,尤其容易产生如此的失透。在本实施方式的制造方法中,以在成形体1的壁面5上向下流动的熔融玻璃中的导件6a、6b附近的部分的粘度自成形体1的上表面3至下端4为止保持小于液相粘度的方式(以该部分的温度自成形体1的上表面3至下端4为止成为液相温度以上的方式),沿着导件6a、6b加热熔融玻璃中的该部分。由此,获得抑制熔融玻璃的导件附近的部分(熔融玻璃的端部)中的失透的较高效果,从而即便构成熔融玻璃的玻璃组合物具有80000dpa·s以上100000dpa·s以下的较小的液相粘度,且具有1200℃~1220℃的范围的液相温度的情形时,也可以抑制该端部中产生失透。在本说明书中,所谓液相温度是指熔融体与结晶的初相之间的平衡温度,且若超过该温度则不存在结晶的温度,所谓液相粘度是指玻璃成为所述液相温度的粘度。图5是表示与成形体1的供给槽2连接的玻璃供给管106的剖面的图。在玻璃供给管106内,若将在玻璃供给管106的中心区域106a流动的熔融玻璃的温度与在周边区域106b流动的熔融玻璃的温度进行比较,则在中心区域106a流动的熔融玻璃的温度升高。若在存在中心区域106a与周边区域106b的温度差(粘度差)的状态下,对成形体1的供给槽2供给熔融玻璃,则在设置有成形体1的空间内,熔融玻璃即便被加热,自玻璃供给管106至成形体1的上表面3为止,熔融玻璃的温度差也未被改善,而在残存熔融玻璃的温度差的状态下自成形体1的上表面3朝向下端4溢出。若在成形体1的上表面3上溢出的时间点,熔融玻璃中存在温度差,则熔融玻璃的流动局部地产生变化(停滞),故熔融玻璃未均一地溢出,在成形体1的壁面5上向下流动的熔融玻璃的厚度(量)产生变化,在下端4进行成形的平板玻璃sg的厚度局部地产生差异。由此,在平板玻璃sg中,产生包含条纹的局部性板厚偏差。因平板玻璃的两端部sga被冷却辊8冷却,且对平板玻璃sg施加朝向两端部sga方向的张力,因此,平板玻璃sg中产生的板厚偏差减少。为了利用如此的原理将所产生的平板玻璃sg的板厚偏差抑制为10μm以下,对成形体1的供给槽2供给时的玻璃供给管106内的熔融玻璃的最大温度差、及熔融玻璃的粘度变得较为重要。在本实施方式的制造方法中,自玻璃供给管106对成形装置200(成形体1的供给槽2)供给时的熔融玻璃的最大温度差(玻璃供给管106的中心区域106a与周边区域106b的温度差)优选设为30℃以下,更优选设为20℃以下,且更优选设为10℃以下。而且,将熔融玻璃的最大粘度差(玻璃供给管106的中心区域106a与周边区域106b的粘度差)优选设为19000dpa·s以下,更优选设为12500dpa·s以下,且更优选设为6200dpa·s以下。因将供给至供给槽2的熔融玻璃在设置有成形体1的空间内进行加热,因此,自成形体1的供给槽2至上表面3为止,熔融玻璃的温度差变得进一步小于供给槽2的供给时的温度差,例如成为10℃以下。在如此的温度差的状态下,若使熔融玻璃自上表面3溢出,则熔融玻璃均一地溢出,从而在壁面5上向下流动的熔融玻璃的厚度(量)达到均一。在下端4汇流而成的熔融玻璃被成形为平板玻璃sg。下端4中的平板玻璃sg的板厚偏差大于10μm,但通过以朝向平板玻璃的两端部sga施加张力的方式,利用冷却辊8将平板玻璃的两端部sga冷却,平板玻璃sg中产生的局部的板厚偏差成为10μm以下。可通过冷却平板玻璃的两端部sga而减少的板厚偏差的量对熔融玻璃的粘度产生影响。在本实施方式的制造方法中,经由玻璃供给管106将熔融玻璃供给至成形装置200(成形体1的供给槽2)时的熔融玻璃的粘度优选为22000dpa·s以上38000dpa·s以下,更优选为25000dpa·s以上38000dpa·s以下,且更优选为25000dpa·s以上35000dpa·s以下。若降低对成形体1的供给槽2供给的熔融玻璃的粘度,即,若升高熔融玻璃的温度,则成形体1的蠕变现象变得显著,从而也产生随着自成形开始起时间的经过,平板玻璃的中央部下垂等问题。另一方面,若提升对成形体1的供给槽2供给的熔融玻璃的粘度,即,若降低熔融玻璃的温度,则平板玻璃中容易产生板厚偏差,而且,容易产生失透。因此,必须将可一面防止板厚偏差及失透的产生一面抑制成形体1的蠕变现象的熔融玻璃供给至成形体1。对成形装置200供给时的熔融玻璃的粘度优选为22000dpa·s以上38000dpa·s以下。所述粘度是因熔融玻璃的平均粘度进而由玻璃组成决定的粘度。以下,将该粘度称为基于平均粘度的粘度。在构成熔融玻璃的玻璃组合物的液相粘度为80000dpa·s以上100000dpa·s以下的情形时,为了在利用成形体1成形的熔融玻璃的粘度变为最高的成形体1的下端防止失透,而以熔融玻璃的粘度变得小于80000dpa·s的方式,控制熔融玻璃的粘度。为抑制成形体1的蠕变现象,而以提升对成形体1的供给槽2供给的熔融玻璃的粘度,同时在成形体1的下端,熔融玻璃的粘度变得小于80000dpa·s的方式,将熔融玻璃供给至成形体1的供给槽2。在本实施方式的制造方法中,对成形体1的供给槽2供给的熔融玻璃的粘度(基于平均粘度的粘度)是下限为自22000dpa·s至25000dpa·s,且上限为自35000dpa·s至38000dpa·s。因供给至供给槽2中的熔融玻璃的粘度变小,故自熔融玻璃供给至供给槽2起至自上表面3溢出为止的时间变短。因此,在该时间之期间,熔融玻璃受到的热量减少。熔融玻璃是以供给槽2内,温度差变小的方式进行加热,但若自供给至溢出为止的时间较短,则无法消除温度差,从而在存在温度差的状态下溢出。如此一来,产生向下流动的速度局部出现变化的部位,从而成为板厚偏差的原因。通过将对成形体1的供给槽2供给的熔融玻璃的粘度(基于平均粘度的粘度)设为22000dpa·s至38000dpa·s,在成形体1的下端4汇流而成形的平板玻璃sg成为低粘度,容易受到冷却辊8的冷却效应,而被拉拔至宽度方向的端部侧,从而平板玻璃sg的板厚偏差的抑制效果变大。另一方面,若熔融玻璃成为低粘度,则至溢出为止的时间变短,故若存在熔融玻璃的温度差(粘性差),则因该温度差(粘性差)而产生板厚偏差。因此,将供给至供给槽2的熔融玻璃的最大温度差设为30℃以下。可通过将满足该等2个条件的熔融玻璃供给至供给槽2,而使平板玻璃sg的板厚偏差成为10μm以下。为了将供给至供给槽2的熔融玻璃的最大温度差设为30℃以下,重要的是玻璃供给管106中流动的熔融玻璃的温度管理,且在玻璃供给管106的管的长边方向上,如图6所示地划分为多个区sc1~sc9及多个管区段pp1~pp3,进行温度调整。图6是表示玻璃供给管106的管的长边方向上的在玻璃供给管106之中流动的熔融玻璃的温度变化的图表。在图6中,实线l1表示作为与玻璃供给管106的内周面接触的熔融玻璃的温度、即玻璃供给管106的温度的“管温度”的变化,虚线l2表示作为玻璃供给管106的剖面中心的熔融玻璃的温度的“中心温度”的变化。在图6中,点划线l3表示以每一单位剖面面积中的熔融玻璃的质量流量进行加权平均所得的玻璃平均温度。使用该平均温度,求出熔融玻璃的基于平均温度的粘度。对于图6所示的熔融玻璃的温度变化进行说明,流入玻璃供给管106中的熔融玻璃是均质化步骤st3中均质化所得的熔融玻璃,因此,流入第1管区段pp1(区sc1~sc5)中的熔融玻璃的管温度与中心温度之差为零。第1管区段pp1是用以将熔融玻璃冷却到不低于玻璃的失透温度的程度的区域。在第1管区段pp1中,存在管温度及中心温度逐渐地下降,且因来自玻璃供给管106的散热,管温度与中心温度之差逐渐地增加的倾向。在第1管区段pp1与第2管区段pp2的交界处,管温度与中心温度之差优选为100℃以下。在图6中,在第1管区段pp1中,玻璃平均温度自1470℃下降到1260℃。在第2管区段pp2中,管温度的下降得到抑制。第2管区段pp2中流动的电流高于第1管区段pp1中流动的电流。因此,利用通电加热赋予给第2管区段pp2的热量大于利用通电加热赋予给第1管区段pp1的热量。因此,在第2管区段pp2中,来自玻璃供给管106的散热得到抑制,玻璃供给管106的温度维持大致固定。此时,在第2管区段pp2内,热自玻璃供给管106的剖面中心的熔融玻璃朝向与玻璃供给管106的内周面接触的熔融玻璃移动,故中心温度逐渐地下降。其结果,在第2管区段pp2中,存在管温度与中心温度之差逐渐地减少的倾向。在第2管区段pp2与第3管区段pp3的交界处,管温度与中心温度之差优选为50℃以下。在图6中,在第2管区段pp2中,玻璃平均温度自1260℃下降到1250℃。另外,在第2管区段pp2的第7区sc7中,玻璃供给管106的内径减少。因此,在第2管区段pp2中,玻璃供给管106的外周面的面积逐渐地减少,因此,经由玻璃供给管106的熔融玻璃的散热被抑制。即,在第2管区段pp2中,因高电流的赋予与内径减少这2个主要因素,管温度与中心温度之差逐渐地减少。在第3管区段pp3中,熔融玻璃的管温度与中心温度之最大温度差达到30℃以下。将第3管区段pp3包围的耐火材料的隔热性能优于将第1管区段pp1及第2管区段pp2包围的耐火材料106。因此,在第3管区段pp3中,与第1管区段pp1及第2管区段pp2相比,经由玻璃供给管106的熔融玻璃的散热进一步被抑制。而且,第3管区段pp3中流动的电流低于第2管区段pp2中流动的电流,且利用通电加热赋予给第3管区段pp3的热量小于利用通电加热赋予给第2管区段pp2的热量。因此,第3管区段pp3之中流动的熔融玻璃的温度上升得到抑制。由此,在第3管区段pp3中,在玻璃平均温度成为大致固定的状态下,因熔融玻璃内的热传递,管温度与中心温度之差进而减少。在图6中,在第3管区段pp3中,玻璃平均温度维持1250℃。另外,通过玻璃供给管106的熔融玻璃的温度的优选范围如下所述。在玻璃供给管106的上流侧的端部,优选管温度及中心温度为1420℃~1470℃。在第1管区段pp1与第2管区段pp2的交界处,优选管温度为1210℃~1260℃,且中心温度为1300℃~1350℃。在第2管区段pp2与第3管区段pp3的交界处,优选管温度为1210℃~1260℃,且中心温度为1250℃~1300℃。在玻璃供给管106的下流侧的端部,优选管温度及中心温度为1235℃~12665℃。通过利用如此的玻璃供给管106进行熔融玻璃的温度调整,而将供给至供给槽2的熔融玻璃的最大温度差设为30℃以下。另外,熔融玻璃的中心温度的测定因存在难以使用温度计的情形,故在该情形时,可使用自玻璃供给管106起的单位时间、单位面积的散热量的信息、玻璃供给管106的单位时间、单位面积的加热量的信息、流入至玻璃供给管106时的熔融玻璃的温度及流量的信息,根据玻璃供给管106的管温度的测定结果,通过计算机模拟而求出。另外,所述管温度是利用安装在玻璃供给管106的各位置处的温度计(未图示)进行测定。粘度是通过安装在玻璃供给管106与成形体1的供给槽2连接的部分的粘度计(未图示)进行测定。粘度计是使用例如细管式粘度计或旋转式粘度计。细管式粘度计是使测定对象的熔融玻璃通过细管,根据熔融玻璃通过细管的时间(流量)及细管的两端的压力差,测定熔融玻璃的粘度。旋转式粘度计是通过根据旋转体的转矩等读取熔融玻璃自旋转体受到的阻力即粘性阻力,而测定熔融玻璃的粘度。在本实施方式的制造方法中,优选以在成形体1的壁面5上向下流动的熔融玻璃中的导件6a、6b附近的部分的温度成为自成形体1的上表面3至下端4为止比液相温度高10℃以上的温度的方式,加热该部分,更优选以成为比液相温度高15℃以上的温度的方式加热该部分。在该等情形时,进行成形的平板玻璃的端部中失透的产生被更确实地抑制。具体的液相温度因玻璃组合物的组成而异。本实施方式的制造方法优选在成形步骤中,以在成形体1的壁面5上向下流动的熔融玻璃中的导件6a、6b附近的部分的温度成为自成形体1的上表面3至下端4为止比液相温度高10℃~150℃的方式(以成为比液相温度高10℃以上,且将液相温度加上150℃所得的温度以下的方式),沿着导件加热该部分。由此,可抑制成形体1的变形、及成形后的平板玻璃sg中的宽度方向的收缩。进而优选以在成形体1的壁面5上向下流动的熔融玻璃中的导件6a、6b附近的部分的温度成为自成形体1的上表面3至下端4为止比液相温度高15℃~100℃的方式,沿着导件加热该部分。通过与熔融玻璃离开成形体1后的端部的淬火(平板玻璃sg的端部sga的淬火)进行组合,平板玻璃sg的板厚偏差达到10μm以下。而且,该端部sga中失透的产生进而被确实地抑制。即便以在成形体1的壁面5上向下流动的熔融玻璃中的导件6a、6b附近的部分的温度自成形体1的上表面3至下端4为止充分地高于液相温度的方式,使在成形体1上向下流动的熔融玻璃整体的温度相较液相温度充分地成为高温,理论上也可抑制失透。然而,在制造液相温度较高的玻璃的情形时,现实中,溢流下拉法中无法适用如此的方法。其原因在于,存在适合溢流下拉法所进行的平板玻璃成形的熔融玻璃的粘度(为避免产生下述平板玻璃的松弛或平板玻璃的宽度收缩的问题,成形体1的下端4中的熔融玻璃的粘度优选为40000dpa·s以上,更优选为70000dpa·s以上)。若以熔融玻璃中的导件附近的部分的温度变得充分地高于液相温度的方式,使在成形体1上向下流动的熔融玻璃整体的温度相较液相温度充分地成为高温,或在成形体1的下端4过度地进行加热,则存在导致成形体1的下端4中的熔融玻璃的粘度变得小于所述适当的范围的可能性。如此一来,产生如下问题,即,离开成形体1后的平板玻璃的粘度未能充分地上升,平板玻璃以配置在成形体1的下游侧的搬运辊的拉伸速度以上的速度落下,导致平板玻璃在该辊上松弛,或平板玻璃的宽度进行收缩。而且,成形体的温度越高,则伴随成形体使用而经时变化的蠕变现象变得越显著,从而也产生平板玻璃的中央部自成形开始起随着时间经过而下垂等问题。若考虑作为玻璃衬底所需的厚度及成形后的缓冷步骤中实施的平板玻璃的温度控制,则搬运辊的拉伸速度增加存在极限(若考虑缓冷步骤中实施的平板玻璃的温度控制,则平板玻璃的搬运速度优选50~500m/小时,优选100~400m/小时,且优选120~300m/小时)。而且,若使熔融玻璃中的导件附近的部分的温度充分地高于液相温度,则进行成形的平板玻璃的宽度收缩,从而无法确保作为玻璃衬底的产品宽度。而且,若使在成形体1上向下流动的熔融玻璃整体的温度相较液相温度充分地成为高温,则产生成形体1的蠕变现象,且若该蠕变现象变得显著,则制造的玻璃衬底的板厚均一性下降。自成形体1中熔融玻璃流动的壁面突出的导件的高度优选低至成形装置的下方的位置。优选成形体1的下端4为两侧的倾斜壁面彼此连接而成的直线状棱线,且一对导件在倾斜的壁面中的高度在该棱线的位置处为0(零)。由此,可进一步抑制平板玻璃的端部(耳部)二叉状打开,从而可更稳定地连续生产玻璃衬底。冷却辊8的冷却量及旋转量是由控制装置(未图示)进行控制。控制装置是主要包括cpu、ram、rom及硬盘等的计算机。控制装置可控制使冷却辊8驱动的驱动电动机,获取及调节夹持平板玻璃sg的宽度方向的端部sga的一对冷却辊8与平板玻璃sg之间的接触负载。控制装置是分别单独地控制各冷却辊8的冷却量。进而,控制装置为了将下述说明的平板玻璃sg的厚度方向的剖面形状成为目标形状作为目的,利用冷却辊8的冷却控制对平板玻璃sg施加的张力,而至少将作为搬运部、获取部、判定部及控制部发挥作用的4个程序存储执行。搬运部是使用设置在成形体1的下方的搬运辊,将利用成形体1成形所得的平板玻璃sg在缓冷空间中以特定的搬运速度搬运至下方。搬运部控制使搬运辊驱动的驱动电动机,调节搬运辊的旋转速度,由此,调节平板玻璃sg的搬运速度。获取部通过利用计算机模拟求出成形体1的形状的时间变化,而获取与成形体1的当前形状相关的形状数据。具体而言,获取部基于蠕变特性参数获取形状数据。蠕变特性参数是用以再现施加至成形体1的应力、成形体1的温度、及因蠕变变形产生的成形体1的应变速度之间的关系的参数。此处,施加至成形体1的应力是沿着成形体1的长边方向(供给槽2的延伸方向)压缩成形体1的力。而且,成形体1的应变速度假设为不随时间变化而固定。最初,获取部测定施加至成形体1的应力固定的条件下成形体1的应变速度对于成形体1的温度依赖性变化。接着,获取部测定成形体1的温度固定的条件下成形体1的应变速度对于施加至成形体1的应力的应力依赖性变化。接着,获取部决定可将成形体1的应变速度的温度依赖性变化及应力依赖性变化的测定值再现的蠕变特性参数。接着,获取部通过计算机模拟,使用所决定的蠕变特性参数,运算特定的温度及应力下的成形体1的应变速度,求出成形体1的形状的时间变化,由此,获取成形体1的形状数据。图7是利用获取部获取的成形体1的形状数据的一例。图7表示沿着与利用成形体1成形所得的平板玻璃sg的表面垂直的方向观察所得的成形体1。图7中,相较实际情况强化地表示成形体1的蠕变变形。在图7中,以虚线表示未使用的成形体1的形状、即蠕变变形之前的成形体1的形状,且以实线表示蠕变变形之后的成形体1的当前形状。获取部是根据成形体1的基于蠕变变形的形状数据,至少获取成形体1的上表面3的铅垂方向的位移量即上表面位移量。在图7中,上表面位移量是蠕变变形前的上表面3与蠕变变形后的上表面3之间的铅垂方向的尺寸。另外,在图7中,表示成形体1的长边方向上的上表面位移量的最大值即最大上表面位移量l。而且,获取部获取通过玻璃衬底形状测定装置(未图示)测定所得的玻璃衬底的厚度数据。厚度数据是例如利用成形装置200制造的玻璃衬底的厚度的宽度方向的轮廓。判定部判定由获取部获取的位移量l是否达到基准量。此处,所谓基准量是指当对平板玻璃sg施加固定的张力(初始的张力),将平板玻璃sg(玻璃衬底)成形为成形预定的厚度(例如0.1mm~0.8mm)时,板厚偏差可满足±10μm的量。在未使施加至平板玻璃sg的张力自初始值变化的情形时,若位移量l超过基准量,则平板玻璃sg的板厚偏差超过±10μm。因此,通过使施加至平板玻璃sg的张力相较初始张力增大,而以平板玻璃sg的板厚偏差成为±10μm以内的方式控制平板玻璃sg的厚度。基准量可因初始张力、平板玻璃sg的成形预定的板厚、及板厚偏差等而任意地变更,例如为3mm~30mm。控制部是将成形体1未沿着成形所得的平板玻璃sg的宽度方向(成形体1的长边方向)移位时所施加且平板玻璃sg的厚度方向的剖面形状成为目标形状的张力设为基准张力(初始张力),且以通过控制冷却辊8的冷却量而将平板玻璃sg的宽度方向的两端部sga冷却,由此施加至平板玻璃sg的张力成为基准张力的方式进行控制。在成形体1未移位的状态下,通过在平板玻璃sg的宽度方向上施加基准张力,平板玻璃sg成为成形预定的板厚,从而板厚偏差满足±10μm。若在成形体1蠕变变形的状态下,施加至平板玻璃sg的张力一直为基准张力,则无法成为目标形状,例如无法成形为成形预定的板厚,而且,板厚偏差无法满足±10μm。因此,控制部不仅施加基准张力,而且对平板玻璃sg施加与成形体1的位移相应的张力。此处,成形体1的位移是例如成形体1的长边方向上的上表面位移。控制部是基于由获取部获取的成形体1的形状数据,以平板玻璃sg的厚度成为成形预定的厚度的方式,而且,以平板玻璃sg的宽度方向的板厚偏差变小的方式,控制冷却辊8的冷却量,由此,控制对平板玻璃sg施加的张力。成形体1的形状数据是例如成形体1的长边方向上的上表面位移量的轮廓即形状轮廓。控制部以根据形状轮廓求得的上表面3的位移量越大,则朝向平板玻璃sg的宽度方向的张力变得越大的方式,控制冷却辊8的冷却量。作为根据形状轮廓求得的上表面3的位移量,例如使用最大上表面位移量l。在成形体1的下端4成形的平板玻璃sg在离开下端4后,因自身的表面张力,中央区域sgb开始朝向宽度方向的中央收缩。因此,冷却辊8将平板玻璃sg的两端部sga冷却使两端部sga的粘度上升,以张力自中央区域sgb朝向两端部sga施加的方式抑制平板玻璃sg在宽度方向上收缩,以使平板玻璃sg的中央区域sgb的厚度达到均一。然而,若成形体1进行蠕变变形,则平板玻璃sg的中央区域sgb附近的熔融玻璃量增多,中央区域sgb的厚度产生变化。即,平板玻璃sg的厚度方向的剖面形状不再为目标形状。图8是表示因成形体1的蠕变变形,中央区域sgb附近的厚度增加的平板玻璃sg的图。若成形体1进行蠕变变形,则自上表面3的端部3a与端部3b之间溢出的熔融玻璃的量增多,故平板玻璃sg的中央区域sgb附近的厚度增加。在图8中,中央区域sgb附近的厚度相比成形预定的厚度最多变厚d1,从而中央区域sgb的厚度成为不均一。因此,控制部根据成形体1的形状数据,使冷却辊8的冷却量变化,以自平板玻璃sg的中央区域sgb朝向两端部sga施加张力的方式抑制平板玻璃sg在宽度方向上收缩,以使平板玻璃sg的中央区域sgb的厚度达到均一。图9是表示成形体1的最大上表面位移量l与施加至平板玻璃sg的张力t的关系的图。在图9中,将最大上表面位移量l记作位移量l。控制部设为在利用判定部判定成形体1的最大上表面位移量l未超过l1的情形时,忽视成形体1的蠕变变形造成的平板玻璃sg的中央区域sgb的厚度变化,不使对平板玻璃sg施加的张力t自初始值t1(位移量l的范围:0以上小于l1)进行变化。若成形体1的位移量l小于l1,则控制部不使冷却辊8的冷却量产生变化,以初始值t1维持张力t,由此,成形的平板玻璃sg的板厚偏差满足±10μm。控制部设为在利用判定部判定成形体1的位移量l超过l1的情形时,如图9所示,以与最大上表面位移量l对应的张力t施加至平板玻璃sg的方式进行控制。若最大上表面位移量l达到l1以上,则如图8所示,平板玻璃sg的中央区域sgb的厚度增加,厚度不再达到均一。因此,控制部以如下方式进行控制:以与位移量l对应的方式,将大于初始值t1的张力t=t1+a×最大上表面位移量l(位移量l的范围:l1以上小于lm,a:系数)自平板玻璃sg的中央区域sgb朝向两端部sga地施加至平板玻璃sg。控制部是随着成形体1的变形变大,而增强两端部sga的冷却。具体而言,使冷却辊8的冷却量增加,从而使两端部sga的粘度上升。若两端部sga的粘度变高,则自中央区域sgb朝向两端部sga的张力t变大,将位于平板玻璃sg的中央区域sgb的熔融玻璃向两端部sga拉伸,从而中央区域sgb的厚度接近于成形预定的厚度,厚度达到均一。控制部以使两端部sga的粘度自例如109.0dpa·s增加至1014.5dpa·s为止,由此张力t变大的方式进行控制。另外,在最大上表面位移量l的范围为l1以上小于lm的情形时,通过将张力t控制为t1至tm,中央区域sgb的厚度向成形预定的厚度靠近,从而厚度达到均一,但在位移量l超过lm进行移位的情形时,仅控制张力t,则难以一面使中央区域sgb的厚度向成形预定的厚度靠近,一面使厚度达到均一,因此,通过判定部判定已到达成形体1的定期更换时期。而且,因成形体1的蠕变变形,平板玻璃sg的局部的板厚偏差(表面凹凸差)也产生变化。平板玻璃sg的体积收缩量随着自平板玻璃sg的端部sga朝向中央区域sgb而变大,因此,在平板玻璃sg的中央区域sgb,拉伸应力进行作用。因中央区域sgb附近的厚度变厚,自两端部sga朝向中央区域sgb的张力变大,故平板玻璃sg的表面凹凸差变大。图10(a)是将图4的a-a线的剖面放大所得的图,图10(b)是将图4的b-b线的剖面放大所得的图。在利用冷却辊8对平板玻璃sg施加张力t之前,平板玻璃sg朝向中央区域sgb收缩,因此,平板玻璃sg的表面凹凸差成为d2,在利用冷却辊8对平板玻璃sg施加张力t之后,平板玻璃sg的表面凹凸差成为小于d2的d3。若成形体1进行蠕变变形,则平板玻璃sg的表面凹凸差d2、d3也变大。因此,通过以对应于最大上表面位移量l的方式,施加自中央区域sgb朝向两端部sga的张力t,而将平板玻璃sg向两端部sga拉伸,故平板玻璃sg的表面凹凸差d3变小。为使中央区域sgb的厚度接近成形预定的厚度,而通过以对应于最大上表面位移量l的方式施加张力t,使得平板玻璃sg的表面凹凸差d3变小,从而平板玻璃sg的中央区域sgb的厚度达到均一。而且,控制部也可以通过对平板玻璃sg施加张力t,而抑制存在产生于平板玻璃sg的搬运方向上的可能性的条纹。条纹是在特定的宽度范围中平板玻璃sg的厚度(高度)变动所致的应变的一种,且在平板玻璃sg的搬运方向上纹路状地连续产生。而且,条纹的主要因素中也包括玻璃的粘度差。若通过控制部控制冷却辊8的冷却量而在平板玻璃sg的宽度方向上施加张力,则平板玻璃sg的表面凹凸的一种且局部地产生的条纹被拉伸至平板玻璃sg的两端侧sga,从而成形表面凹凸差变小且局部的板厚偏差满足±10μm的平板玻璃sg。如以上所说明,可通过在成形体1的下端4,使对平板玻璃sg施加的平板玻璃sg的宽度方向的张力t对应于成形体1的蠕变变形引起的位移量进行变化,而一面使中央区域sgb的厚度接近成形预定的厚度,一面使厚度达到均一。在因成形体1的蠕变变形,成形体1的长边方向的中央部向下方下垂而挠曲的情形时,可通过将冷却辊8的冷却量增大,使对平板玻璃sg施加的平板玻璃sg的宽度方向的张力t变大,而降低平板玻璃sg的宽度方向的板厚偏差。其结果,可降低作为最终产品的玻璃衬底的板厚偏差。而且,在使用液相温度较高的玻璃及应变点较高的玻璃的玻璃衬底的制造步骤中,成形体1的蠕变变形因成形体1的温度容易增高而尤其容易成为问题。而且,近年来,因玻璃衬底不断大型化,成形体的长边方向的尺寸不断变长,因此,存在蠕变变形造成的成形体1的挠曲变得更显著的倾向。在本实施方式中,可通过调节冷却辊8的冷却量,使对平板玻璃sg施加的张力t变化,而有效地降低因成形体1的蠕变变形引起的平板玻璃sg的宽度方向的板厚偏差。根据本实施方式的制造方法,即便在构成熔融玻璃的玻璃组合物的液相温度较高,且液相粘度较小的情形时,例如玻璃组合物为无碱玻璃、含微量碱玻璃等情形时,也可获得抑制成形的平板玻璃的端部中的失透的效果。即,在构成熔融玻璃的玻璃组合物的液相温度较高且液相粘度较小的情形时,通过本实施方式的制造方法获得的优点较大。在本实施方式的制造方法中,构成熔融玻璃的玻璃组合物的液相粘度为10000dpa·s以下。如此的玻璃组合物以往在溢流下拉法的平板玻璃的成形中容易产生端部中的失透问题。然而,在本实施方式的制造方法中,可获得抑制失透的效果。本实施方式的制造方法中所用的熔融玻璃的液相粘度为100000dpa·s以下。液相粘度为100000dpa·s以下的玻璃组合物中,所述失透的问题变得更显著,但本实施方式的制造方法获得了抑制失透的效果。根据可稳定地实施溢流下拉法的平板玻璃的成形的观点,液相粘度优选为80000dpa·s以上。构成本实施方式的制造方法中所用的熔融玻璃的玻璃组合物的液相温度优选为1200℃以上1220℃以下。如此的玻璃组合物以往在溢流下拉法的平板玻璃的成形中容易产生端部中的失透问题。然而,本实施方式的制造方法获得了抑制失透的效果。在本实施方式的制造方法中,熔融玻璃也可以含有氧化锆及/或氧化锡。在含有氧化锆的熔融玻璃中,与不含氧化锆的情形相比,玻璃组合物的液相温度上升。如此的熔融玻璃以往在溢流下拉法的平板玻璃的成形中容易产生端部中的失透问题。然而,本实施方式的制造方法获得了抑制失透的效果。氧化锆即便在作为玻璃组合物的成分原本包含于熔融玻璃的情形以外,也可以通过采用使用高氧化锆系耐火材料所构成的熔解槽及成形装置而在熔融玻璃中熔出。尤其,在使用如此的熔解槽,将玻璃原料电熔解的情形时,存在熔融玻璃中的氧化锆浓度变高的倾向。即,本实施方式的制造方法更适合于采用使用高氧化锆系耐火材料所构成的熔解槽将玻璃原料电熔解的情形。另外,使用高氧化锆系耐火材料所构成的熔解槽与以往广泛使用的氧化铝电铸耐火材料所构成的熔解槽相比,不易被玻璃腐蚀,从而作为熔解槽的使用寿命较长。而且,也可以抑制熔融玻璃发泡。因此,适于形成熔融温度(玻璃组合物的粘度达到102.5泊的温度)较高的玻璃组合物例如无碱玻璃及含微量碱玻璃的熔融玻璃。而且,在利用熔解槽形成的熔融玻璃包含无碱玻璃或含微量碱玻璃的情形时,玻璃组合物的电阻率容易变高,从而存在电流流入高氧化锆耐火材料中而不流入玻璃原料中的倾向。若电流流入该耐火材料中,则氧化锆在利用熔解槽形成的熔融玻璃中熔出。即,本实施方式的制造方法进而适合于采用使用高氧化锆系耐火材料所构成的熔解槽,通过电熔解形成无碱玻璃或含微量碱玻璃的熔融玻璃的情形。液晶显示器、有机el显示器等的fpd(flatpaneldisplay,平板显示器)用玻璃衬底中,优选包含无碱玻璃或含微量碱玻璃的玻璃衬底。其原因在于,若在面板制造步骤中碱成分自玻璃衬底熔出,则存在薄膜晶体管(tft,thin-filmtransistor)等电子元件的特性劣化之虞。即,本实施方式的制造方法尤其适合于采用使用高氧化锆系耐火材料所构成的熔解槽将玻璃原料电熔解,且使用所得的熔融玻璃通过溢流下拉法制造平板显示器用玻璃衬底的情形。另外,所谓无碱玻璃是指实质上不含碱金属氧化物(就含有率而言小于0.05质量%)的玻璃组合物。所谓含微量碱玻璃是指含有0.05~2.0质量%的碱金属氧化物的玻璃组合物。含有氧化锡的熔融玻璃中,容易因氧化锡结晶化而产生失透。而且,在与氧化锆共存的情形时,氧化锡具有使氧化锆结晶化的作用。如此的熔融玻璃在以往利用溢流下拉法成形平板玻璃的过程中尤其容易产生端部中的失透问题。然而,本实施方式的制造方法获得了抑制失透的效果。在本实施方式的制造方法中,构成熔融玻璃的玻璃组合物也可以是无碱玻璃或含微量碱玻璃。与含有超过2.0质量%的碱金属氧化物的碱玻璃相比,如此的无碱玻璃或含微量碱玻璃存在液相温度较高且液相粘度较小的倾向,但本实施方式的制造方法获得了抑制失透的效果。该效果如上所述在采用使用高氧化锆系耐火材料所构成的熔解槽通过电熔解形成无碱玻璃或含微量碱玻璃的熔融玻璃的情形时变得尤其显著。另外,根据防止tft(thinfilmtransistor)等电子元件的特性劣化的观点,无碱玻璃适合平板显示器用玻璃衬底。其中,根据熔解性及清澄性的观点,含微量碱玻璃适合平板显示器用玻璃衬底。通过特意微量地含有碱金属氧化物制成含微量碱玻璃,使得玻璃组合物的熔解性及清澄性提升。清澄性中因碱金属氧化物的存在,而玻璃的碱性度上升,从而有助于价数变动的金属变得容易氧化。而且,即便在使用高氧化锆系耐火材料所构成的熔解槽中通过玻璃原料的电熔解而形成熔融玻璃的情形时,也可以使玻璃的电阻率小于无碱玻璃,能够抑制氧化锆向熔融玻璃的熔出,从而能够抑制熔融玻璃的失透性上升。在本实施方式的制造方法中,就构成熔融玻璃的玻璃组合物而言,呈现102.5泊的粘度的温度(熔融温度)也可以是1500℃~1750℃。如此的玻璃组合物在熔融时需要高温,因此,在通过使用高氧化锆系耐火材料所构成的熔解槽形成熔融玻璃的情形时,氧化锆容易熔出。即便对于如此的玻璃组合物,本实施方式的制造方法也获得了抑制失透的效果。作为利用本实施方式的制造方法制造的玻璃衬底中所含的玻璃成分,例如可列举sio2、al2o3、b2o3、mgo、cao、sro、bao、li2o、na2o、k2o、zro2、tio2、zno、及p2o5。sio2是玻璃的骨架成分,因此是必须成分。若含量变少,则存在应变点降低,热膨胀系数增加的倾向。而且,若sio2含量过少,则难以使玻璃衬底实现低密度化。另一方面,若sio2含量过多,则存在熔融玻璃mg的电阻率上升,熔融温度显著变高从而难以熔解的倾向。若sio2含量过多,则也存在失透温度上升,抗失透性降低的倾向。进而,若sio2含量过多,则刻蚀速率变慢。根据如此的观点,sio2的含量优选为例如60~80mol%的范围。sio2的含量更优选为64~73mol%或65~75mol%,进一步更优选为66~72mol%,进而更优选为67~71mol%的范围。al2o3是提高应变点的必须成分。若al2o3含量过少,则应变点降低。进而,若al2o3含量过少,则存在杨氏模量及氧所进行的刻蚀速率也降低的倾向。另一方面,若al2o3含量过多,则玻璃的失透温度上升,抗失透性下降,故存在成形性恶化的倾向。根据如此的观点,al2o3的含量为8~20mol%的范围。al2o3的含量优选为10~17mol%,更优选为10.5~17mol%,更优选为11~15mol%,进而优选为12~15mol%的范围。b2o3是使玻璃的高温粘性降低,改善熔融性的成分。即,因使熔融温度附近的粘性降低,故改善熔解性。而且,b2o3也是使失透温度降低的成分。若b2o3含量较少,则存在熔解性及抗失透性下降的倾向。若b2o3含量过多,则应变点及杨氏模量下降。而且,因玻璃成形时b2o3的挥发,导致容易产生失透。尤其,应变点较高的玻璃因存在成型温度变高的倾向,故促进所述挥发,从而失透的产生成为显著的问题。而且,因玻璃熔解时b2o3的挥发,玻璃的非均质变得显著,变得容易产生条纹。根据如此的观点,b2o3含量为0~15mol%,优选为0~8mol%,更优选为0~7mol%,进而优选为0.1~6mol%,更加优选为1~5mol%,进一步更优选为1.5~4.5mol%的范围。mgo是使熔解性提升的成分。而且,mgo是碱土类金属之中使密度难以增加的成分,因此,若使该含量相对地增加,则容易实现低密度化。可通过含有mgo,而降低熔融玻璃mg的电阻率及熔融温度。其中,若mgo的含量过多,则玻璃的失透温度急剧上升,故尤其在成形步骤中容易出现失透。根据如此的观点,mgo含量为0~15mol%,优选为1~15mol%,更优选为0~6mol%,进而优选为1~6mol%的范围。或者,mgo含量优选为0~15mol%,更优选为0~6mol%,进而优选为1~6mol%的范围。cao是对于不使玻璃的失透温度急剧地上升且提升玻璃的熔解性有效的成分。而且,cao是碱土类金属氧化物之中使密度难以增加的成分,故若使该含量相对地增加,则容易实现低密度化。若含量过少,则存在产生熔融玻璃mg的电阻率上升及抗失透性下降的倾向。若cao含量过多,则存在热膨胀系数增加,密度上升的倾向。根据如此的观点,cao含量为0~20mol%,优选为1~15mol%,更优选为2~11mol%,进而优选为4~9mol%的范围。sro是能够降低玻璃的失透温度的成分。sro虽非必须,但若含有sro,则抗失透性及熔解性提升。然而,若sro含量过多,则导致密度上升。根据如此的观点,sro含量为0~15mol%,优选为0~8mol%,更优选为0~3mol%,进而优选为0~1mol%,更加优选为0~0.5mol%的范围,进一步更优选实质上不含有。bao是能够使玻璃的失透温度及熔融玻璃mg的电阻率有效地下降的必须成分。若含有bao,则抗失透性及熔解性提升。然而,若bao的含量过多,则导致密度上升。而且,因环境负荷的观点、及存在热膨胀系数增大的倾向,故bao含量为0~15mol%或0.1~15mol%,优选为1~15mol%,更优选为1~10mol%,进而优选为1.5~6mol%的范围。li2o及na2o是存在增大玻璃的热膨胀系数导致热处理时使衬底破损之虞的成分。而且,li2o及na2o也是使应变点降低的成分。另一方面,因可使熔融玻璃mg的电阻率降低,故可通过含有li2o及na2o而抑制熔解槽被侵蚀。根据以上的观点,li2o的含量优选为0~0.5mol%,更优选实质上不含有。na2o的含量优选为0~0.5mol%,更优选为0~0.2mol%。另外,na2o是与li2o相比使应变点更难以降低的成分,故优选为na2o>li2o。另外,根据防止自玻璃衬底熔出导致tft特性劣化的观点,li2o及na2o优选实质上不含有。k2o是提升玻璃的碱性度促进清澄性的成分。而且,k2o是使熔融玻璃mg的电阻率降低的成分。若含有k2o,则熔融玻璃mg的电阻率下降,故可防止电流流入至构成熔解槽的耐火材料,从而可抑制熔解槽被侵蚀。而且,在构成熔解槽的耐火材料含有氧化锆的情形时,可抑制熔解槽被侵蚀,从而氧化锆自熔解槽向熔融玻璃mg熔出,因此,也可以抑制氧化锆引起的失透。而且,因可使熔解温度附近的玻璃粘性降低,故熔解性与清澄性提升。另一方面,若k2o含量过多,则存在热膨胀系数增大及应变点降低的倾向。根据如此的观点,k2o含量优选为0~0.8mol%,更优选为0.01~0.5mol%,进而优选为0.1~0.3mol%的范围。zro2及tio2是使玻璃的应变点提升的成分。然而,若zro2量及tio2量过多,则失透温度显著地上升,故存在抗失透性降低的倾向。尤其,zro2因熔点高导致难熔,而引发原料的一部分沉积在熔解槽的底部之类的问题。若该等未熔解的成分混入至玻璃毛坯,则作为内含物而引起玻璃的品质恶化。而且,tio2是使玻璃着色的成分,故对于显示器用衬底较为欠佳。根据如此的观点,在本实施方式的玻璃衬底中,zro2及tio2的含量优选分别为0~5mol%,更优选为0~2mol%的范围,进而优选实质上不含有。zno是使熔解性提升的成分。但并非必须成分。若zno含量过多,则存在失透温度上升,应变点降低,且密度上升的倾向。根据如此的观点,zno含量优选为0~5mol%,更优选为0~2mol%的范围,进而优选实质上不含有。p2o5是使高温粘性降低,使熔解性提升的成分。但并非必须成分。若p2o5含量过多则应变点降低。而且,因玻璃熔解时p2o5的挥发,而导致玻璃的非均质变得显著,容易产生条纹。根据如此的观点,p2o5含量优选为0~3mol%,更优选为0~1mol%,进而优选为0~0.5mol%的范围,更加优选实质上不含有。适用本实施方式的玻璃衬底包含例如含有以下组成的无碱玻璃。sio2:55-80质量%al2o3:8-20质量%b2o3:0-18质量%ro0~17摩尔%(ro为mgo、cao、sro及bao的总量)r,2o0~2摩尔%(r,2o为li2o、na2o及k2o的总量)。根据减小热收缩率的观点,优选sio2为60~75质量%,进而为63~72质量%。ro之中,优选mgo为0~10质量%,cao为0~10质量%,sro为0~10质量%,bao为0~10质量%。而且,也可以是至少包含sio2、al2o3、b2o3、及ro且摩尔比((2×sio2)+al2o3)/((2×b2o3)+ro)为4.5以上的玻璃。而且,优选包含mgo、cao、sro、及bao的至少任一个,且摩尔比(bao+sro)/ro为0.1以上。而且,优选质量%表示的b2o3的含有率的2倍与质量%表示的ro的含有率的合计为30质量%以下,优选为10~30质量%。进而,熔融玻璃中价数变动的金属的氧化物(氧化锡,氧化鉄)优选合计含有0.05~1.5质量%。优选实质上不含有as2o3、sb2o3、pbo,但也可以任意地含有该等。而且,玻璃中价数变动的金属的氧化物(氧化锡、氧化鉄)合计含有0.05~1.5质量%,且实质上不含有as2o3、sb2o3及pbo的情况为任意而非必须。本实施方式中制造的玻璃衬底适合包含平板显示器用玻璃衬底的显示器用玻璃衬底。本实施方式中制造的玻璃衬底适合使用有igzo(铟、镓、锌、氧)等的氧化物半导体的氧化物半导体显示器用玻璃衬底及使用有ltps(低温多晶硅)半导体的ltps显示器用玻璃衬底。而且,本实施方式中制造的玻璃衬底适合要求碱金属氧化物的含量极少的液晶显示器用玻璃衬底。而且,也适合有机el显示器用玻璃衬底。换言之,本实施方式的玻璃衬底的制造方法适合制造显示器用玻璃衬底,尤其适合制造液晶显示器用玻璃衬底。其他,也可以用作便携式终端设备等的显示器或壳体用的玻璃盖板、触控面板、太阳能电池的玻璃衬底或玻璃盖板。本实施方式中制造的玻璃衬底尤其适合使用多晶硅tft的液晶显示器用玻璃衬底。而且,本实施方式中制造的玻璃衬底也可以适用于玻璃盖板、磁盘用玻璃、太阳能电池用玻璃衬底等。以上,对本实施方式的玻璃衬底的制造方法及玻璃衬底的制造装置详细地进行了说明,但本发明并非限定于所述实施方式,毋庸置疑,在不脱离本发明主旨的范围内,可进行各种改良或变更。(实施例)利用使用高氧化锆系耐火材料的熔解槽,将以具有下述组成的方式调配而成的玻璃原料电熔解,形成熔融玻璃。接着,利用铂合金制的清澄管将所形成的熔融玻璃清澄之后,利用搅拌槽进行搅拌。接着,将熔融玻璃供给至成形装置200(成形体1),利用溢流下拉法成形平板玻璃。将平板玻璃的端部利用冷却辊8以该端部的粘度成为1012.5dpa·s的方式冷却而成形的平板玻璃进行缓冷之后截断,获得厚度为0.4mm且尺寸为2200mm×2500mm的平板显示器用玻璃衬底。另外,该玻璃组合物的液相粘度为50000dpa·s,且应变点为715℃。sio2:61.5质量%,al2o3:20质量%,b2o3:8.4质量%,cao:10质量%,sno2:0.1质量%。使自玻璃供给管106供给至成形体1的供给槽2中的熔融玻璃的最大温度差、熔融玻璃的粘度(基于平均粘度的粘度)进行变化,测定平板玻璃(玻璃衬底)的板厚偏差。其结果示于表1中。[表1]最大温度差(℃)粘度(dpa)板厚偏差(μm)实施例120220002.0实施例220320001.6实施例320380003.5比较例1202200011.2比较例2204000012.8实施例430220007.9实施例530320005.2实施例630380006.3比较例3302000014.0比较例4304000013.1比较例5352200017.8比较例6353200015.9比较例7353800018.4如表1所示,在熔融玻璃的最大温度差为30℃以下且熔融玻璃的粘度(基于平均粘度的粘度)为22000dpa·s以上38000dpa·s以下的实施例1~6中,板厚偏差达到10μm以下,从而可抑制板厚偏差。另一方面,在熔融玻璃的最大温度差超过30℃的情形时、熔融玻璃的粘度(基于平均粘度的粘度)小于22000dpa·s的情形时、及熔融玻璃的粘度超过38000dpa·s的情形时的比较例1~7中,板厚偏差变得大于10μm。由此,可确认为使平板玻璃的板厚偏差成为10μm以下,将供给至成形体1的供给槽2中的熔融玻璃的最大温度差设为30℃以下,且将熔融玻璃的粘度(基于平均粘度的粘度)设为22000dpa·s以上38000dpa·s以下即可。[符号的说明]100溶熔解装置101溶熔解槽102清澄管103搅拌槽103a搅拌棒104、105输送管106玻璃供给管200成形装置300截断装置mg熔融玻璃sg平板玻璃sga(平板玻璃的)端部1成形体2供给槽3上表面3a、3b(上表面的)端部4下端5壁面6a、6b导件7液面8冷却辊当前第1页12