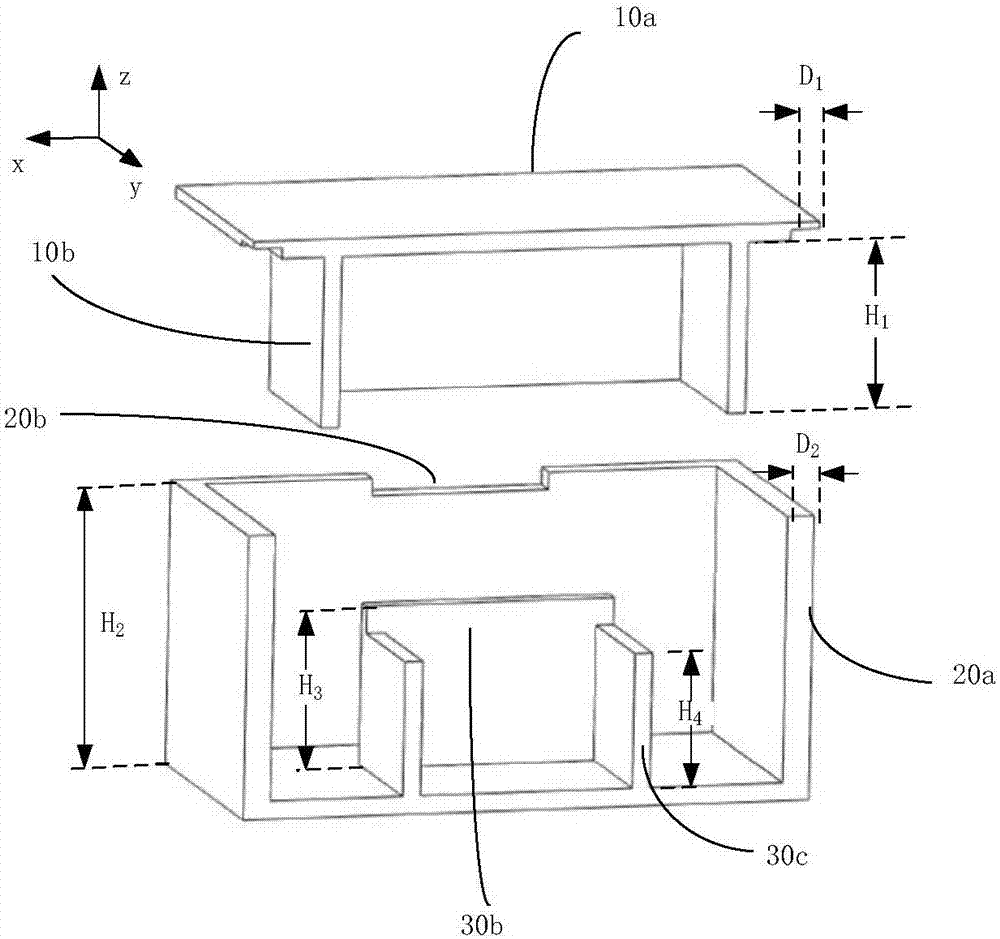
本发明涉及石墨烯材料,尤其涉及一种用于制备石墨烯的匣钵、石墨烯材料及其制备方法。
背景技术:
:由于新能源技术特别是电动汽车技术的发展,对高容量高功率密度的高性能动力电池等提出了巨大需求。作为一种高电导率的二维纳米材料,石墨烯被认为是高性能的动力电池用导电剂的关键材料之一。现有的石墨烯的制备方法为化学氧化还原法、机械剥离法、cvd气相沉积法等。然而,该些方法所制造出的石墨烯均有缺陷。比如,采用化学氧化还原法,虽然石墨烯的厚度较小,单层率高,但是在氧化过程对石墨烯会造成了较大破坏,产生空洞以及引入其他官能团、大量的硫元素、以及铁钴镍锰等金属杂质,而大大影响石墨烯的电导率,导致后续应用于电池时有损电池的性能。采用机械剥离法,虽然石墨烯的电导率高,但是存在石墨烯的厚度较厚、层数较多的缺点,而该方法最大问题是:所采用的原料为鳞片石墨、可膨胀石墨或者膨胀蠕虫石墨,在通过液相或者气相等方法进行物理机械剥离时,该原料的内部带有大量的硫元素,以及残留的铁钴镍锰钾钙等杂质,杂质的含量大大超标,因而会损害电池的性能。采用cvd气相沉积法,虽然得到的石墨烯具有单层或者双层的厚度较薄的特点,电导率极高,但是由于需利用带有大量的金属镍等的基底,该基底需进行溶解剥离,导致石墨烯的产量极低,无法用作大规模的成吨级别的应用。技术实现要素:有鉴于此,确有必要提供一种可用于大规模制备导电性能优异的石墨烯材料的匣钵、制备方法、以及导电性能优异的石墨烯材料。本发明提供一种用于制备石墨烯的匣钵,所述匣钵包括匣钵主体和匣盖,所述匣钵主体的顶部为开口,所述匣盖盖于匣钵主体的顶部,其中,所述匣钵主体包括外匣壁体以及外匣壁体形成的外空腔,所述外匣壁体设有一缺口,使得外空腔与外界相连通;所述匣钵主体中还设有一内匣,所述内匣包括内匣壁体以及内匣壁体形成的内空腔,所述内匣的顶部为开口,所述内空腔与外空腔相连通;所述匣盖包括匣盖顶和匣盖壁体,所述匣盖壁体置于所述匣钵主体的外空腔内,所述匣盖壁体的高度小于所述外匣壁体的高度。优选的,所述内匣壁体由一对第一挡板以及一对第二挡板组成,该第一挡板的高度大于第二挡板的高度。优选的,所述匣盖顶由一顶板以及第一凹部组成,所述第一凹部形成于所述顶板的四周,所述第一凹部在所述顶板的表面上任一方向的最小尺寸均大于所述匣钵主体的外匣壁体的厚度。优选的,在所述第一凹部设至少一第二凹部,所述第二凹部在x方向的长度大于所述匣钵主体的外匣壁体的厚度。优选的,所述匣钵的材料为高密度石墨,所述高密度石墨为将石墨原料经过高温处理得到的石墨,所述高密度石墨的密度为大于等于1.85g/cm3。优选的,将所述石墨原料经过高温处理具体是指将石墨原料在2400摄氏度~3000摄氏度的温度下并被施加1个大气压~3.6个大气压的压力处理。本发明还提供一种利用上述匣钵制备石墨烯材料的方法,其包括以下步骤:(1)提供石墨原料;(2)对石墨原料进行氧化,再将氧化后的石墨置于匣钵中并在惰性气氛中于1000摄氏度~1400摄氏度下进行还原,得到石墨烯材料,其中所述匣钵的材料为高密度石墨。优选的,步骤(2)中所述还原的时间为20分钟~20小时。优选的,在步骤(2)中所述还原的温度为1000摄氏度~1100摄氏度,所述还原的时间为30分钟~12小时。本发明还提供一种采用上述方法制备得到的石墨烯材料,所述石墨烯材料的电导率在105s/m以上,所述石墨烯材料的结构基本无缺陷。与现有技术相比较,所述用于制备石墨烯的匣钵的材料为高密度石墨,因而具有耐高温的优点。所述外匣壁体的缺口的作用在于,使得外空腔与外界连通,在制备石墨烯材料的过程中,可将原料中产生的杂质气体如水、二氧化硫排放至外界。所述内匣、匣盖壁体将所述匣钵主体的内部空间分为三个相互连通的子空间(内空腔、第一子外腔、第二子外腔)。外匣壁体的缺口、内匣、匣盖壁体、外匣壁体的设计形成该特殊的复杂“迷宫”式的结构,有利于形成较长以及蜿蜒的气体通道。当将氧化石墨置于所述内匣的内空腔内时,在高温的作用下,粉状的氧化石墨在发生爆炸式的剥离还原后得到石墨烯材料,石墨烯材料与二氧化硫等气体所形成的气流式混合物一起流动,当遇到起阻隔作用的内匣壁体(即第一挡板、第二挡板)、匣盖壁体以及外匣壁体时,气流式混合物会与之发生碰撞,从而使二氧化硫等气体排出,石墨烯粉体被沉积下来,大大提高石墨烯材料的收得率。该匣钵的结构简单,制备该匣钵的方法简单,原料易得、价格低廉,适合大规模的产业化应用。在使用时,将氧化石墨放入该匣钵中,然后对氧化石墨在高温下进行还原得到石墨烯材料。相对于现有方法中所使用的制备容器或基底而言,由于该匣钵的材料为高密度石墨,因而避免引入其他额外的杂质,同时该匣钵作为制备空间场所,后续无需如cvd方法剥离基底的步骤,大大方便了石墨烯材料的制备。在现有的采用氧化-还原的方法制备石墨烯的过程中,由于还原时采用水合肼进行还原,该得到的石墨烯存在较多的缺陷,并且杂质含量较多;而本申请将氧化石墨置于所述高密度石墨材料制成的匣钵中,通过将该匣钵置于高温环境下,可对氧化石墨进行高温石墨化得到石墨烯材料。该制备方法投入原料及收集产品极其方便,收得率高,可实现大规模的制备,在实际应用中,可实现百吨级别的制备。并且,在该制备过程中,无需加入其它原料,因此不会引入其它杂质;因未使用基底等,也无需剥离。该整个制备过程步骤简单,制备效率高。通过该制备方法得到的石墨烯材料具有以下优点:对氧化石墨仅通过高温还原处理即可得到石墨烯材料,所述石墨烯材料基本无缺陷、厚度较薄、金属杂质含量极低,并且具有高电导率。该得到的石墨烯材料可应用于导电浆料,而进一步用于制备电池。附图说明图1为本发明所述匣钵的结构示意图。图2为图1所述匣钵的分解示意图。图3为图1所述匣钵的匣钵主体的结构示意图。图4为图1所述匣钵的匣盖的结构示意图。图5为本发明实施例(1)得到的石墨烯材料的透射电镜(tem)照片。图6为对比例(1)得到的石墨烯材料的tem照片。图7为本发明实施例(1)得到的石墨烯材料的拉曼光谱图。图8为对比例(1)得到的石墨烯材料的拉曼光谱图。图9为本发明实施例(1)得到的石墨烯材料的x射线衍射(xrd)图。图10为对比例(1)得到的石墨烯材料的xrd图。其中,10表示匣盖,10a表示匣盖顶,10a1表示顶板;10a2表示第一凹部,10a3表示第二凹部,10b表示匣盖壁体,20表示匣钵主体,20a表示外匣壁体,20b表示缺口,20c表示外空腔,30表示内匣,30a表示内空腔,30b表示第一挡板,30c表示第二挡板。如下具体实施例将结合上述附图进一步说明本发明。具体实施方式以下将结合附图对本发明提供的用于制备石墨烯的匣钵、石墨烯材料及其制备方法作进一步说明。本发明提供一种用于制备石墨烯的匣钵。请参阅图1至图4,所述匣钵包括匣盖10和匣钵主体20。所述匣钵主体20的顶部为开口,所述匣盖10盖于匣钵主体20的顶部。所述匣钵主体20与匣盖10为相互独立,所述匣盖10并未紧密固定于所述匣钵主体20即二者并非结合成一体。所述匣盖10仅仅盖于所述匣钵主体20的顶部而同时使用。这是因为,该石墨烯制备过程中,由于匣钵的特定设计,匣钵内的石墨原料等粉状物质基本在匣钵内,而并不会大量飞至外界,仅极少量逸出,在此可忽略。因此,匣盖10无需固定于匣钵主体20,这也降低了匣钵制备的复杂性,匣钵的使用也更为简单。请参阅图3,所述匣钵主体20包括外匣壁体20a以及外匣壁体20a形成的外空腔20c。所述外匣壁体20a设有一缺口20b,使得外空腔20c与外界相连通。当将氧化石墨粉末置于所述匣钵主体20内进行高温还原时,产生的水、二氧化硫等会经由所述外匣壁体20a上的缺口20b而逸出。在水、二氧化硫等逸出的同时也会产生使还原得到的石墨烯与内匣壁体及外匣壁体20a碰撞而落下沉积的效果,而提升石墨烯的收得率。所述匣钵主体20的形状不限,只要有一外空腔20c即可。所述外匣壁体20a为一板状结构,可为平面的板,也可为曲面的板。所述缺口20b的大小以及形状不做限定,只要可将所述外空腔20c与外界连通即可。所述匣钵主体20中还设有一内匣30。所述内匣30与所述匣钵主体20为一体成型。所述内匣30包括内匣壁体以及内匣壁体形成的内空腔30a。所述内匣30的顶部为开口。所述内空腔30a与外空腔20c相连通。所述内匣30的形状可与所述匣钵主体20的形状相同,也可不相同。所述内匣30的形状可为圆柱体、立方体等。所述内匣壁体可为平面的板材结构,也可为曲面的板材结构。当所述内匣壁体为平面的板材结构,请参阅图2以及图3,所述匣钵主体20及内匣30的形状均为长方体,所述内匣壁体可由一对第一挡板30b以及一对第二挡板30c组成。定义所述第一挡板30b以及第二挡板30c在z方向(即垂直方向)的尺寸分别为所述第一挡板30b的高度h3、所第二挡板30c的高度h4,此时h3≥h4。在制备过程中,氧化石墨粉末发生爆炸式的剥离还原后得到石墨烯粉体,石墨烯粉体与二氧化硫等气体所形成的气流式混合物一起流动,当遇到起阻隔作用的内匣壁体、匣盖壁体以及外匣壁体时,气流式混合物会与之发生碰撞,从而使二氧化硫等气体排出,石墨烯粉体被沉积下来。为了增加气流式混合物发生碰撞的几率与次数,优选的,该第一挡板30b的高度与第二挡板30c的高度之间具有一高度差,h3>h4。当所述内匣壁体为曲面的板材结构,所述内匣壁体上可设有一内匣缺口(图未示)。在上述设计中,所述内匣缺口或者该第一挡板30b以及第二挡板30c之间的高度差均是为了利于内空腔30a与外空腔20c之间增设较多的阻碍,使石墨烯粉体与二氧化硫等气体所形成的气流式混合物与起阻隔作用的内匣壁体以及外匣壁体的碰撞的几率与次数发生碰撞而沉积,而避免石墨烯粉体随气流全部离开匣钵,从而提高最终石墨烯粉体的收率。换句话说,所述匣钵设计得如此复杂,是为了增加气体流通的通道长度,改变气流的排出方向,提高石墨烯粉体与二氧化硫等气体所形成的混合气流与内匣壁体、匣盖壁体以及外匣壁体的碰撞几率,改变气流中石墨烯粉体的流动方向,引起更多石墨烯粉体的下沉沉积,提高石墨烯粉体的收率。所述匣盖10包括匣盖顶10a和匣盖壁体10b。所述匣盖壁体10b置于所述匣钵主体20的外空腔20c内。定义所述匣盖壁体10b以及外匣壁体20a在垂直z方向的尺寸分别为所述匣盖壁体10b的高度h1、外匣壁体20a的高度h2。所述匣盖壁体10b的高度h1小于所述外匣壁体20a的高度h2,此设计的目的在于,当将所述匣盖10盖于所述匣钵主体20的顶部时,所述匣盖壁体10b伸入所述匣钵主体20的外空腔20c内,而将所述外空腔20c分为相互连通的第一子外腔20c1与第二子外腔20c2。该特定的设计,即内匣30、匣盖壁体10b将所述匣钵主体20的内部空间分为三个相互连通的子空间(内空腔30a、第一子外腔20c1、第二子外腔20c2),因此当将氧化石墨置于所述匣钵主体20内时,在高温的作用下,粉状的氧化石墨在发生还原后形成的石墨烯粉体,会被内匣壁体(即第一挡板30b、第二挡板30c)、匣盖壁体10b、外匣壁体20a反复的碰撞而沉积,得到层数较少的石墨烯材料。请参阅图2和图4,所述匣盖10包括一体的匣盖顶10a以及匣盖壁体10b。所述匣盖10的形状及大小不做限定。定义所述匣盖顶10a在x轴以及y轴方向的尺寸为匣盖顶10a的长度及宽度。所述匣盖壁体10b设于所述匣盖顶10a的靠近中部位置。具体的,请参阅图4,所述匣盖顶10a由一顶板10a1以及第一凹部10a2组成。所述第一凹部10a2形成于所述顶板10a1的四周,即所述顶板10a1的边缘四周向内凹陷形成所述第一凹部10a2,即所述顶板10a1的边缘四周的厚度较顶板10a1的中间部分的厚度较薄,以利于匣盖10相对较为稳定位于匣钵主体20的上面,不发生过多的移动。优选的,所述第一凹部10a2在所述顶板10a1的表面上任一方向的最小尺寸均大于所述匣钵主体20的外匣壁体20a的厚度。当所述匣盖10的形状为矩形板状时,所述第一凹部10a2在x方向及y方向的最小尺寸均大于所述匣钵主体20的外匣壁体20a的厚度d2。此优选设计的目的在于,将氧化石墨置于外空腔20c内时,所述匣盖顶10a的顶板10a1会部分伸入所述外空腔20c内,而尽量减小所述缺口20b的面积,进而在保证所述外空腔20c与外界相连通的同时,粉状氧化石墨被限制于所述外空腔20c内,粉状氧化石墨之间发生更多的碰撞。可选的,请参阅图2及图4,在所述第一凹部10a2可设至少一第二凹部10a3。所述第二凹部10a3在外匣壁体20a的厚度方向上的尺寸d1大于所述匣钵主体20的外匣壁体20a的厚度d2。具体的,当所述匣钵主体20为长方体时,所述第二凹部10a3在x方向的长度d1大于所述匣钵主体20的外匣壁体20a的厚度d2。所述第二凹部10a3的作用在于,作为所述外空腔20c与外界相连通的一个额外的通道,而利于小分子水、二氧化碳等的排放。本实施例中,所述匣钵主体20及内匣30的形状均为长方体,所述内匣30的第一挡板30b的高度大于第二挡板30c的高度,在所述匣盖10的第一凹部10a2设一对第二凹部10a3。所述匣钵的材料为高密度石墨。所述高密度石墨是指将石墨原料经过高温以及高压处理得到的石墨。具体的,将石墨原料在2400摄氏度~3000摄氏度的温度下并被施加1个大气压~3.6个大气压的压力处理,可得到所述高密度石墨。优选的,将石墨原料在2500摄氏度~2800摄氏度的温度下并被施加3.6个大气压的压力处理,可得到所述高密度石墨。所述石墨原料可从市场购得,在此不做赘述。可以理解,在将石墨原料经过高温及高压处理之后,还进行一车铣的步骤,以得到具有特定形状的匣钵。由于所述匣钵的材料为高密度石墨,因而可耐受高温,并且由于与制备石墨烯材料所含元素相同,均为碳元素,因此,并未带来额外的杂质。针对现有的制备石墨烯材料时粉状石墨原料密度小导致的粉尘易飞扬而不容易被固定的缺点,本申请所述匣钵专门应用于石墨烯材料的制备,可方便容纳原料以及大规模的制备石墨烯材料。该装置的结构也简单,容易制备,成本较低,利于工业化应用。本发明还提供一种利用上述匣钵制备石墨烯材料的方法。该方法包括以下步骤:s1,提供石墨原料;s2,对石墨原料进行氧化,再将氧化后的石墨置于一匣钵中并在惰性气氛中于1000摄氏度~1400摄氏度下进行还原,其中所述匣钵的材料为高密度石墨。在步骤s1中,所述石墨原料可为直接采矿得到的石墨矿石,也可为将石墨矿石进一步进行提纯和/或粉碎得到的粉状物质。对石墨矿石进行提纯和/或粉粹均为现有的技术,在此不作赘述。在步骤s2中,所述氧化的方法中,以浓硫酸作为插层剂(对石墨进行插层),硝酸钠作为插层剂助剂(硝酸钠在硫酸的存在下具有强氧化性),高锰酸钾作为强氧化剂将石墨氧化成氧化石墨。之后,可加入双氧水除去过量的高锰酸钾,以及盐酸除去钠离子和硫酸根离子,得到较为纯净的氧化石墨。所述氧化石墨被还原的机理为:在惰性的气氛下,通过高温的环境使得氧化石墨表面的含氧基团化学键在高温下被破坏而断裂,形成小分子水和二氧化碳逸出,同时大量逸出的小分子加大了氧化石墨中片层之间的层间距;即在高温还原的同时,所述层数多的氧化石墨也被自动剥离成层数较少的石墨烯材料。本申请所述石墨烯材料是指层数为1~5的石墨烯。所述惰性气氛是指氮气、氩气、氦气、氖气等惰性气体。所述还原的温度优选为1000摄氏度~1100摄氏度。所述还原的时间为20分钟~20小时,优选为,30分钟~12小时。所述高温还原以及自动剥离的步骤是通过一具有特殊结构的匣钵实现。所述匣钵的材料与所述用于制备石墨烯材料的装置的材料相同。这也是考虑到高温处理的要求,而且在反应中也不引入额外的杂质,以及从所述匣钵中方便取放物品。在步骤s2之后,还可包括一机械剥离的步骤。所述机械剥离可采用固相或者液相剥离的方法。具体的,将步骤s2得到的石墨烯材料与溶剂比如水、n-甲基吡咯烷酮、表面活性剂等混合,经过一次或者多次机械剥离,得到层数更少的石墨烯材料。石墨烯材料经过机械剥离之后,层数更少,导电性更优异。所述石墨烯材料可直接用作导电剂,或者与溶剂混合形成导电浆料而进一步应用。本发明还提供一种通过上述制备方法得到的石墨烯材料。所述石墨烯材料基本无缺陷、厚度较薄、单层率更高、金属杂质含量极低,并且具有高电导率。所述石墨烯材料的电导率在105s/m以上。以下,将结合具体的实施例进一步说明。实施例(1)(1)提供石墨原料,所述石墨原料为石墨矿石经过提纯、粉碎;(2)对石墨原料进行氧化,再将氧化后的石墨置于一匣钵中并在惰性气氛中于1000摄氏度~1050摄氏度下进行还原,得到石墨烯材料,其中所述匣钵的材料为高密度石墨。对比例(1)为了更好的说明本申请所述方法所得到的石墨烯材料的优点,本申请还提供一对比例(1)。该对比例(1)提供一种石墨烯材料的制备方法。具体为:使用hummers法,将粉碎提纯的石墨原料gc325(325目)经过浓硫酸、硝酸钠、高锰酸钾等处理,得到了氧化石墨粉末;然后将氧化石墨粉末置于一个普通的化学气相沉积的管式炉内进行剥离,得到了石墨烯粉末对实施例(1)得到的石墨烯粉末进行透射电镜测试,测试结果请参阅图5。对对比例(1)得到的石墨烯粉末进行透射电镜测试,测试结果请参阅图6。由图5、图6可见,相对与对比例(1)而言,实施例(1)的石墨烯粉末的图5出现明显的衍射条纹,这说明实施例(1)石墨烯粉末的结晶度更好。对实施例(1)得到的石墨烯粉末进行拉曼光谱测试,测试结果请参阅图7。对对比例(1)得到的石墨烯粉末进行拉曼光谱测试,测试结果请参阅图8。由图7~图8可见,实施例(1)在1350cm-1处呈现出比较弱的特征峰;并且相比对比例(1)而言,实施例(1)的强度要弱的多。实施例(1)中在1580cm-1与1350cm-1的两个特征峰的强度比ig/id比值较对比例(1)中的该两个位置的峰强度比值大,这说明经过高温石墨化处理后,石墨烯材料原有的结构缺陷被修复。对实施例(1)得到的石墨烯粉末进行xrd测试,测试结果请参阅图9。对对比例(1)得到的石墨烯粉末进行xrd测试,测试结果请参阅图10。由图9和图10可见,相对与实施例(1),对比例(1)得到的石墨烯粉末在2θ角为22°~26°处的特征峰的更宽(根据该特征峰对应计算得出晶面间距大于0.35nm),这说明对比例(1)中制备的石墨烯的片层间距更大。由图10可见,实施例(1)在2θ角为26°的位置出现了尖锐的特征峰(根据该特征峰对应计算得出晶面间距为0.345nm);并且该特征峰的半峰宽d为0.34nm,基本接近于单层石墨烯的理论厚度0.34nm。这也说明了本申请实施例(1)所述石墨烯粉末中的石墨烯有石墨化倾向,其层间距的减小。这是由于在石墨烯修复过程中的碳原子重排,而形成单层石墨烯,而相邻的两个单层石墨烯之间强烈的相互作用,又会使得其重新结合趋于形成较厚的两层或多层石墨烯。对实施例(1)得到的石墨烯粉末进行比表面积的测试。所述石墨烯粉末的比表面积为350g/cm2,这进一步证实了石墨烯粉末中含有较多的石墨烯,适合进一步应用。进一步,对实施例(1)得到的石墨烯材料进行杂质含量的测试,结果见表1。表1杂质元素alascacdcocr含量(ppm)0.0010.03337.2250.0010.0040.001杂质元素cufegehgmnmo含量(ppm)0.0375.670.0010.0010.0820.157杂质元素nipbsbsisns含量(ppm)0.4010.0360.0013.6240.00353由表1可见,实施例1)所述石墨烯材料中杂质的含量极少,这进一步验证了本申请所述制备方法所得到的石墨烯材料具有极好的应用前景。以上实施例的说明只是用于帮助理解本发明的方法及其核心思想。应当指出,对于本
技术领域:
的普通技术人员来说,在不脱离本发明原理的前提下,还可以对本发明进行若干改进和修饰,这些改进和修饰也落入本发明权利要求的保护范围内。对所公开的实施例的上述说明,使本领域专业技术人员能够实现或使用本发明。对这些实施例的多种修改对本领域的专业技术人员来说将是显而易见的,本文中所定义的一般原理可以在不脱离本发明的精神或范围的情况下,在其它实施例中实现。因此,本发明将不会被限制于本文所示的这些实施例,而是要符合与本文所公开的原理和新颖特点相一致的最宽的范围。当前第1页12