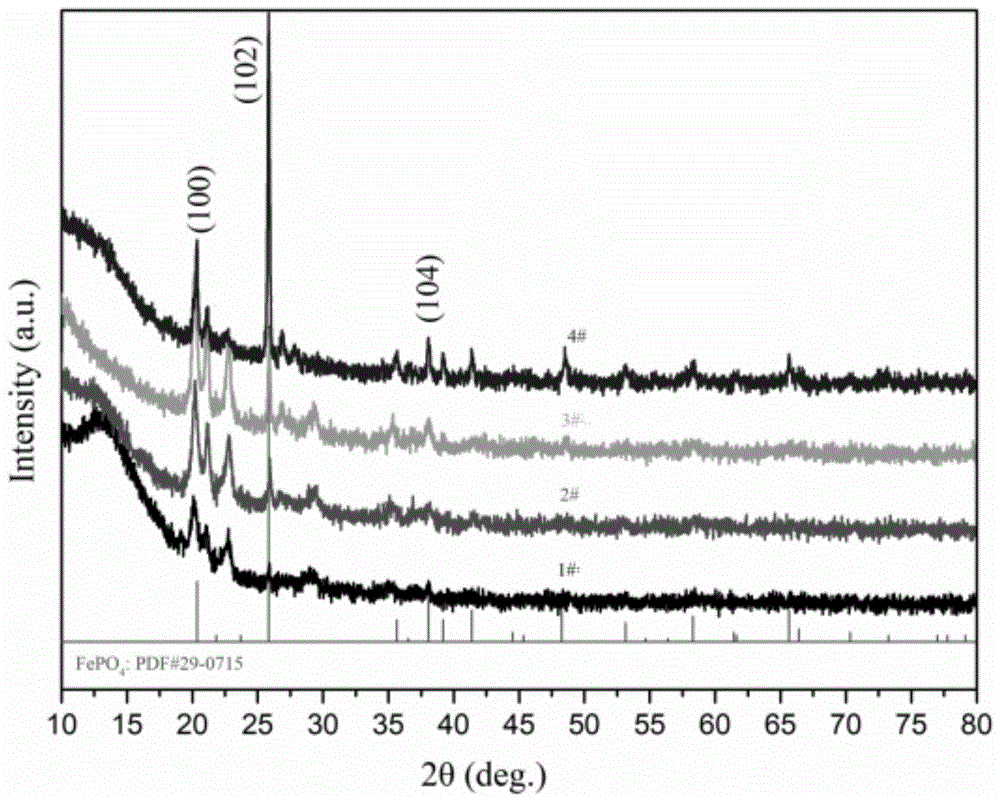
本发明涉及一种电池级无水磷酸铁的制备方法,属于锂电池新能源材料领域。
背景技术:
:电池级无水磷酸铁,目前为主流的制备磷酸铁锂的前驱体,相比较氧化铁红、草酸亚铁等前驱体,磷酸铁制备的磷酸铁锂,具有电性能好,压实密度高,工艺稳定,产品一致性好的特点。目前无水磷酸铁的制备均为磷酸盐与铁盐反应得到二水磷酸铁,再经过高温煅烧(一般温度为500-600℃)脱去两个结晶水得到无水磷酸铁,煅烧过程能耗高,且在制备二水磷酸铁过程,液相合成会产生大量的含氨氮或者磷酸根的废水,环保处理成本高。根据实际目前市面上的无水磷酸铁的价格和利润来估算,每吨无水磷酸铁的制备成本约为0.9-1.1万,再加上环保处理的成本以及其他费用,则实际成本要高于此。随着新能源汽车的发展以及国家补贴的逐步降低,对磷酸铁锂的价格越来越敏感,所以也迫切要求磷酸铁的成本要降低。技术实现要素:有鉴于此,本发明提供了一种电池级无水磷酸铁的制备方法,工艺简单,成本低,可以一步法得到无水磷酸铁,且完全无废水产生,且一次粒径大,杂质含量少,纯度高。本发明通过以下技术手段解决上述技术问题:一种电池级无水磷酸铁的制备方法,将铁粉与红磷混合,然后加入酒精,在球磨机内球磨,得到球磨料;将球磨料进行减压蒸馏,将酒精蒸发出去,蒸发出去的酒精蒸气冷凝回收其中的酒精,然后将蒸馏后剩余的铁磷混合物放入到回转炉内煅烧,煅烧过程鼓入空气,煅烧温度为550-620℃,煅烧时间为4-8h;将煅烧料冷却至料温≤60℃,然后经过气流粉碎至物料粒径为0.5-2μm,然后经过100-200目筛过筛后,4-5级电磁除铁器进行电磁铸铁,除铁至磷酸铁的磁性物质低于1ppm后,真空包装,得到电池级无水磷酸铁。所述铁粉的粒径为1-4μm,铁粉中的铁含量≥99.5%,镍钴含量≤20ppm,钙镁含量≤50ppm,硫含量低于200ppm,所述红磷的纯度≥99.5%,铁粉中的铁与红磷中的磷的摩尔比为1:1.02-1.05。加入的酒精的质量为铁粉和红磷总质量的2-4倍,得到的球磨料的粒径为0.5-2μm。减压蒸馏过程压力为0.01-0.02mpa,蒸馏温度为40-60℃.冷凝回收的酒精返回球磨使用。在回转炉煅烧过程,回转炉的转速为2-4r/min,回转炉内的气氛中,氧气体积分数大于18%,空气在回转炉的气体流速≥3m/s。气流粉碎采用露点≤-40℃的压缩空气为气源,压缩空气的压力为4-7个大气压。电磁除铁器的磁强度为10000-12000gs。球磨过程球磨机内的磨球为氧化锆磨球,氧化锆磨球的直径为0.3-3mm。本发明采用铁粉和磷单质,在高温氧气气氛下煅烧,直接一步法合成得到无水磷酸铁,完全在无水的环境下高温固相法合成,相比较液相法-煅烧脱水工艺,流程短,工艺简单,且无废水产生,且本发明采用的原料为铁粉和磷单质,每吨无水磷酸铁消耗铁粉约0.37吨,单质磷约0.21吨,原料成本仅仅只有5000元,相比较其他工艺,如磷酸盐与亚铁盐在氧化剂作用下的液相反应,其原料成本(包括纯水)达到了7000元以上,且本工艺在能耗方面,人工方面均比常规的液相法有巨大优势,最终每吨无水磷酸铁,本工艺相比较常规的液相法,成本低3500元以上,具有巨大的优势;同时,本工艺的设备投资少,不需要污水处理装置,也不需要各种液相合成所需要的设备,包括反应釜、压滤机、管件、各种泵等,根据计算,本工艺的设备投资比常规的液相合成工艺减少了20%以上,同时人工成本也降低了。本发明以固相法来合成无水磷酸铁,将铁粉、红磷加入酒精,在酒精介质球磨,磨细后的磷单质与铁单质,比表面积更大,粒径更小,活性更高,同时酒精的强分散性,可以提高铁与磷之间的混合效率,使得混合更加均匀,然后经过减压蒸馏,将酒精蒸发出来,再经过冷凝回收其中的酒精,酒精返回使用,从而降低了成本,再将混合好的铁磷混合物放入回转炉内煅烧,同时通入空气,在空气气氛下,高温条件下,发生以下反应:fe+p+2o2------fepo4。然后经过冷却,冷却的物料,电磁除铁器的除铁效率更高,然后经过气流粉碎,将少量未反应的铁单质剥离出来,经过筛分除铁后真空包装,得到电池级无水磷酸铁,采用低露点的空气,可以避免无水磷酸铁的二次吸水,同时采用4-5级电磁除铁器除铁,可以最大程度的降低磁性物质,从而满足电池级磷酸铁的要求。由于为纯固相法反应,相比较液相反应,可以得到一次粒径更大的无水磷酸铁,且由于无其他元素参与反应,如硫酸根、铵根等,所以纯度更高,杂质含量低。本发明的有益效果是:1.工艺简单,成本低,可以一步法得到无水磷酸铁,每吨无水磷酸铁相比较其他工艺少3500元以上,按照年产1万吨的无水磷酸铁,可以降低成本3500万。2.环保性好,纯固相法合成,完全无废水产生,且设备投资少。3.得到的无水磷酸铁一次粒径大,杂质含量少,纯度高。附图说明附图1为本发明实施例1-4的产品的xrd图。具体实施方式以下将结合具体实施例对本发明进行详细说明,本实施例的一种电池级无水磷酸铁的制备方法,将铁粉与红磷混合,然后加入酒精,在球磨机内球磨,得到球磨料;将球磨料进行减压蒸馏,将酒精蒸发出去,蒸发出去的酒精蒸气冷凝回收其中的酒精,然后将蒸馏后剩余的铁磷混合物放入到回转炉内煅烧,煅烧过程鼓入空气,煅烧温度为550-620℃,煅烧时间为4-8h;将煅烧料冷却至料温≤60℃,然后经过气流粉碎至物料粒径为0.5-2μm,然后经过100-200目筛过筛后,4-5级电磁除铁器进行电磁铸铁,除铁至磷酸铁的磁性物质低于1ppm后,真空包装,得到电池级无水磷酸铁。所述铁粉的粒径为1-4μm,铁粉中的铁含量≥99.5%,镍钴含量≤20ppm,钙镁含量≤50ppm,硫含量低于200ppm,所述红磷的纯度≥99.5%,铁粉中的铁与红磷中的磷的摩尔比为1:1.02-1.05。加入的酒精的质量为铁粉和红磷总质量的2-4倍,得到的球磨料的粒径为0.5-2μm。减压蒸馏过程压力为0.01-0.02mpa,蒸馏温度为40-60℃.冷凝回收的酒精返回球磨使用。在回转炉煅烧过程,回转炉的转速为2-4r/min,回转炉内的气氛中,氧气体积分数大于18%,空气在回转炉的气体流速≥3m/s。气流粉碎采用露点≤-40℃的压缩空气为气源,压缩空气的压力为4-7个大气压。电磁除铁器的磁强度为10000-12000gs。球磨过程球磨机内的磨球为氧化锆磨球,氧化锆磨球的直径为0.3-3mm。实施例1一种电池级无水磷酸铁的制备方法,将铁粉与红磷混合,然后加入酒精,在球磨机内球磨,得到球磨料;所述铁粉的粒径为2.4μm,铁粉中的铁含量≥99.5%,镍钴含量≤20ppm,钙镁含量≤50ppm,硫含量低于200ppm,所述红磷的纯度≥99.5%,铁粉中的铁与红磷中的磷的摩尔比为1:1.035。加入的酒精的质量为铁粉和红磷总质量的3倍,得到的球磨料的粒径为0.95μm。球磨过程球磨机内的磨球为氧化锆磨球,氧化锆磨球的直径为0.5mm。将球磨料取样,测激光粒度,结果如下:dmind10d50d90d99dmax0.26μm0.61μm0.95μm1.45μm1.57μm1.97μm将球磨料进行减压蒸馏,将酒精蒸发出去,蒸发出去的酒精蒸气冷凝回收其中的酒精,然后将蒸馏后剩余的铁磷混合物放入到回转炉内煅烧,煅烧过程鼓入空气,煅烧温度为590℃,煅烧时间为7h;减压蒸馏过程压力为0.015mpa,蒸馏温度为55℃,冷凝回收的酒精返回球磨使用。在回转炉煅烧过程,回转炉的转速为3r/min,回转炉内的气氛中,氧气体积分数大于18%,空气在回转炉的气体流速≥3m/s。将煅烧料冷却至料温≤60℃,然后经过气流粉碎至物料粒径为0.93μm,然后经过150目筛过筛后,5级电磁除铁器进行电磁铸铁,除铁至磷酸铁的磁性物质低于1ppm后,真空包装,得到电池级无水磷酸铁。气流粉碎采用露点≤-40℃的压缩空气为气源,压缩空气的压力为6个大气压。电磁除铁器的磁强度为12000gs。取产品,测量xrd,如图1所示,图1中的1#为本实施例的相图,从相图来看,无其他杂相。取样检测,数据如下:指标铁磷比高温水分d10d50d90数值0.9980.149%0.25μm0.42μm0.93μmd100cdcopbcana1.22μm1.5ppm4.6ppm6.7ppm19.8ppm20.5ppm振实密度硫酸根氯离子bet磁性异物一次粒径1.22g/ml7.2ppm6.1ppm4.2m2/g0.78ppm178nm实施例2一种电池级无水磷酸铁的制备方法,将铁粉与红磷混合,然后加入酒精,在球磨机内球磨,得到球磨料;将球磨料进行减压蒸馏,将酒精蒸发出去,蒸发出去的酒精蒸气冷凝回收其中的酒精,然后将蒸馏后剩余的铁磷混合物放入到回转炉内煅烧,煅烧过程鼓入空气,煅烧温度为610℃,煅烧时间为6h;将煅烧料冷却至料温≤60℃,然后经过气流粉碎至物料粒径为1.2μm,然后经过155目筛过筛后,5级电磁除铁器进行电磁铸铁,除铁至磷酸铁的磁性物质低于1ppm后,真空包装,得到电池级无水磷酸铁。所述铁粉的粒径为2.3μm,铁粉中的铁含量≥99.5%,镍钴含量≤20ppm,钙镁含量≤50ppm,硫含量低于200ppm,所述红磷的纯度≥99.5%,铁粉中的铁与红磷中的磷的摩尔比为1:1.04。加入的酒精的质量为铁粉和红磷总质量的3倍,得到的球磨料的粒径为1.2μm。减压蒸馏过程压力为0.018mpa,蒸馏温度为55℃.冷凝回收的酒精返回球磨使用。在回转炉煅烧过程,回转炉的转速为3.5r/min,回转炉内的气氛中,氧气体积分数大于18%,空气在回转炉的气体流速≥3m/s。气流粉碎采用露点≤-40℃的压缩空气为气源,压缩空气的压力为5个大气压。电磁除铁器的磁强度为11000gs。球磨过程球磨机内的磨球为氧化锆磨球,氧化锆磨球的直径为0.9mm。取产品,测量xrd,如图1所示,图1中的2#为本实施例的相图,从相图来看,无其他杂相。取样检测,数据如下:指标铁磷比高温水分d10d50d90数值0.9960.163%0.63μm1.2μm1.91μmd100cdcopbcana2.22μm2.5ppm4.9ppm8.7ppm23.6ppm21.5ppm振实密度硫酸根氯离子bet磁性异物一次粒径1.42g/ml8.5ppm4.1ppm3.9m2/g0.91ppm189nm实施例3一种电池级无水磷酸铁的制备方法,将铁粉与红磷混合,然后加入酒精,在球磨机内球磨,得到球磨料;将球磨料进行减压蒸馏,将酒精蒸发出去,蒸发出去的酒精蒸气冷凝回收其中的酒精,然后将蒸馏后剩余的铁磷混合物放入到回转炉内煅烧,煅烧过程鼓入空气,煅烧温度为605℃,煅烧时间为6.5h;将煅烧料冷却至料温≤60℃,然后经过气流粉碎至物料粒径为0.65μm,然后经过200目筛过筛后,4级电磁除铁器进行电磁铸铁,除铁至磷酸铁的磁性物质低于1ppm后,真空包装,得到电池级无水磷酸铁。所述铁粉的粒径为1.5μm,铁粉中的铁含量≥99.5%,镍钴含量≤20ppm,钙镁含量≤50ppm,硫含量低于200ppm,所述红磷的纯度≥99.5%,铁粉中的铁与红磷中的磷的摩尔比为1:1.035。加入的酒精的质量为铁粉和红磷总质量的4倍,得到的球磨料的粒径为1.35μm。减压蒸馏过程压力为0.016mpa,蒸馏温度为55℃,冷凝回收的酒精返回球磨使用。在回转炉煅烧过程,回转炉的转速为4r/min,回转炉内的气氛中,氧气体积分数大于18%,空气在回转炉的气体流速≥3m/s。气流粉碎采用露点≤-40℃的压缩空气为气源,压缩空气的压力为5.2个大气压。电磁除铁器的磁强度为10000gs。球磨过程球磨机内的磨球为氧化锆磨球,氧化锆磨球的直径为0.9mm。取产品,测量xrd,如图1所示,图1中的3#为本实施例的相图,从相图来看,无其他杂相。取样检测,数据如下:指标铁磷比高温水分d10d50d90数值0.9920.178%0.35μm0.65μm0.99μmd100cdcopbcana1.17μm3.8ppm5.3ppm8.1ppm28.6ppm26.2ppm振实密度硫酸根氯离子bet磁性异物一次粒径1.45g/ml8.2ppm4.6ppm5.3m2/g0.92ppm181nm实施例4一种电池级无水磷酸铁的制备方法,将铁粉与红磷混合,然后加入酒精,在球磨机内球磨,得到球磨料;将球磨料进行减压蒸馏,将酒精蒸发出去,蒸发出去的酒精蒸气冷凝回收其中的酒精,然后将蒸馏后剩余的铁磷混合物放入到回转炉内煅烧,煅烧过程鼓入空气,煅烧温度为600℃,煅烧时间为8h;将煅烧料冷却至料温≤60℃,然后经过气流粉碎至物料粒径为0.55μm,然后经过100目筛过筛后,5级电磁除铁器进行电磁铸铁,除铁至磷酸铁的磁性物质低于1ppm后,真空包装,得到电池级无水磷酸铁。所述铁粉的粒径为1.5μm,铁粉中的铁含量≥99.5%,镍钴含量≤20ppm,钙镁含量≤50ppm,硫含量低于200ppm,所述红磷的纯度≥99.5%,铁粉中的铁与红磷中的磷的摩尔比为1:1.025。加入的酒精的质量为铁粉和红磷总质量的4倍,得到的球磨料的粒径为1.3μm。减压蒸馏过程压力为0.015mpa,蒸馏温度为45℃.冷凝回收的酒精返回球磨使用。在回转炉煅烧过程,回转炉的转速为4r/min,回转炉内的气氛中,氧气体积分数大于18%,空气在回转炉的气体流速≥3m/s。气流粉碎采用露点≤-40℃的压缩空气为气源,压缩空气的压力为5个大气压。电磁除铁器的磁强度为11000gs。球磨过程球磨机内的磨球为氧化锆磨球,氧化锆磨球的直径为0.4mm。取产品,测量xrd,如图1所示,图1中的4#为本实施例的相图,从相图来看,无其他杂相。取样检测,数据如下:指标铁磷比高温水分d10d50d90数值0.9960.151%0.23μm0.55μm1.01μmd100cdcopbcana1.22μm4.5ppm6.1ppm10.7ppm28.6ppm29.1ppm振实密度硫酸根氯离子bet磁性异物一次粒径1.32g/ml6.3ppm4.9ppm5.5m2/g0.56ppm176nm将实施例1-4制备的无水磷酸铁采用固相法来制备碳包覆的磷酸铁锂,碳包覆量为1.5-1.8%,最终制备的磷酸铁锂的压实密度大于2.45g/ml,0.1c首次充电容量均大于159mah/g,0.1c首次放电容量均大于155mah/g,与常规的液相法合成的磷酸铁在相同工艺下制备的磷酸铁锂比较,容量基本差不多,压实密度比常规的无水磷酸铁要高3%以上。最后说明的是,以上实施例仅用以说明本发明的技术方案而非限制,尽管参照较佳实施例对本发明进行了详细说明,本领域的普通技术人员应当理解,可以对本发明的技术方案进行修改或者等同替换,而不脱离本发明技术方案的宗旨和范围,其均应涵盖在本发明的权利要求范围当中。当前第1页12