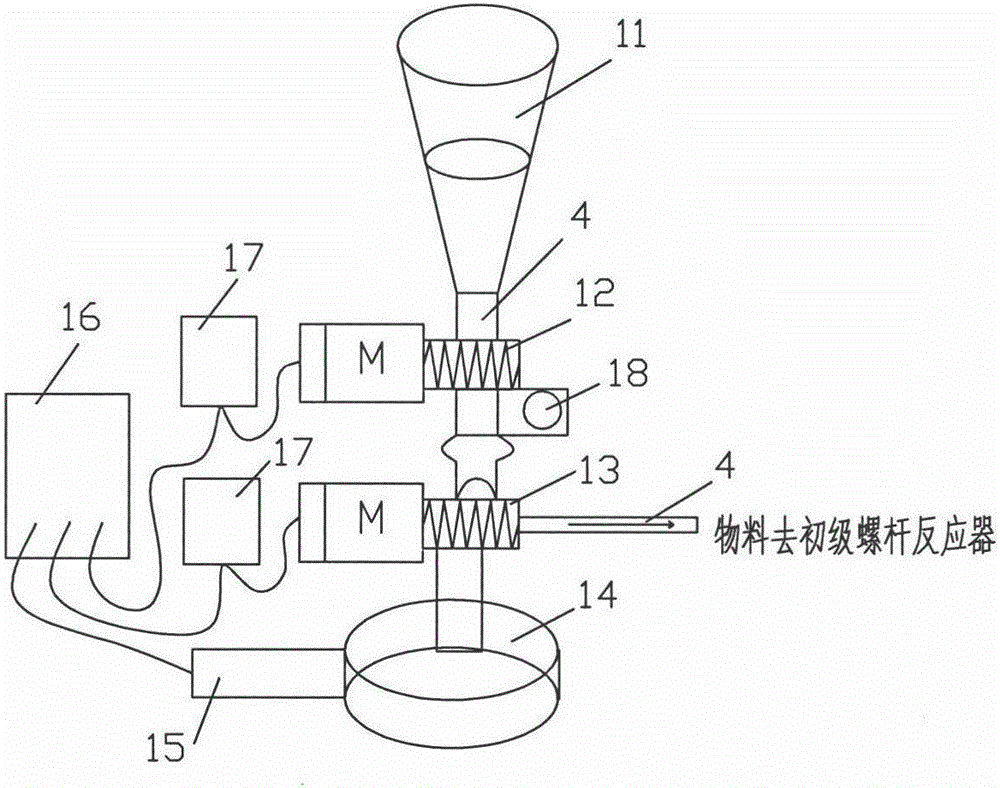
本发明涉及氨基树脂生产的
技术领域:
,尤其是一种氨基树脂的连续化生产装置及方法。
背景技术:
:氨基树脂是由含有氨基的化合物与甲醛经缩聚而成的树脂的总称,重要的氨基树脂有脲醛树脂、三聚氰胺甲醛树脂和苯胺甲醛树脂等。这类树脂的生产一直沿用传统的间歇反应釜来完成,间歇生产使每一批树脂的质量随时间的推移有所改变,分子量分布宽等各种不足,对于三聚氰胺甲醛树脂而言,质量的改变制约了由三聚氰胺甲醛树脂进一步生成三聚氰胺泡沫塑料的质量稳定性;而且间歇反应釜反应条件不易控制,废水废气较多,由此给三聚氰胺甲醛树脂的生产提出了连续化的要求。技术实现要素:本发明是针对现有间歇反应方法生产氨基树脂的缺点,提供一种氨基树脂的连续化生产装置及方法。本发明的一种氨基树脂的连续化生产装置,其特征在于包括依次连通的原料自动连续配料器、初级螺杆反应器和双螺杆圆柱钢块组合反应器,所述原料自动连续配料器包括固体原料自动连续配料器和液体原料自动连续配料器,所述固体原料自动连续配料器和液体原料自动连续配料器分别和初级螺杆反应器连通,所述初级螺杆反应器包括第一热交换容腔和密闭于第一热交容腔内的初级螺杆,所述初级螺杆设计为交替排列的若干输送段和若干混合段,所述输送段设置具有输送作用的的输送螺旋槽,所述混合段设置具有混合作用的混合螺旋槽,所述第一热交换容腔对应于初级螺杆的若干输送段和若干混合段相应地设计为若干段,每一段设置有热交换机进行温控,所述双螺杆圆柱钢块组合反应器包括第二热交换容腔和密闭于第二热交换容腔内的两根圆柱轴、安装在两根平行的圆柱轴上的圆柱钢块,所述圆柱钢块若干块为一组,每一组内各圆柱钢块前后紧贴,不同心地安装在圆柱轴上,所述每一组圆柱钢块交替安装,使得两根圆柱轴同向旋转时带动两根圆柱轴上相对的圆柱钢块组交错旋转,所述第二热交换容腔设计为若干段,每一段设置有热交换机进行温控。优选地,所述固体原料自动连续配料器包括料仓、第一螺旋泵和第二螺旋泵、失重电子秤、称重传感器、PLC、变频器,所述料仓在上方,经物料通道下连第一螺旋泵,再经物料通道连接设有称重传感器的失重电子秤,再经物料通道连接第二螺螺旋泵,所述称重传感器、变频器均与PLC相连;液体原料自动连续配料器包括料桶、流量计、柱塞泵、失重电子秤、称重传感器、PLC、变频器、隔膜泵,所述料桶在上方,经物料通道下连流量计和柱塞泵,再经物料通道连接设有称重传感器的失重电子秤,再经物料通道连接隔膜泵,所述称重传感器、变频器均与PLC相连。优选地,所述第一热交换容腔为第一自动控制热交换容腔,所述第一热交换自动控制容腔对应于初级螺杆的若干输送段和若干混合段相应地设计为若干段,每一段设置有一台自动控制的热交换机进行温控,所述第二热交换容腔为第二自动控制热交换容腔,所述第二自动控制热交换容腔设计为若干段,每一段设置有一台自动控制的热交换机进行温控。优选地,所述依次连通的原料自动连续配料器、初级螺杆反应器和双螺杆圆柱钢块组合反应器之间均为密闭连通,所述第二热交换容腔内加满阻聚剂溶液。优选地,所述圆柱钢块四块为一组,所述圆柱钢块为渗氮钢块。一种氨基树脂的连续化生产方法,其特征在于所述生产方法按如下步骤实现:步骤1,固体原料自动连续配料,固体原料通过所述固体原料自动连续配料器配料并加入生产装置;步骤2,液体原料自动连续配料,液体原料通过所述液体原料自动连续配料器配料并加入生产装置;步骤3,初级螺杆反应,加入生产装置的固体原料和液体原料,进入所述初级螺杆反应器,通过控制调整反应条件,包括第一自动控制热交换容腔各段的温度、初级螺杆的转速及反应时间,使初级螺杆反应所得产物为透明物料;步骤4,双螺杆圆柱钢块组合反应,经初级螺杆反应流出的透明物料进入双螺杆圆柱钢块组合反应器,通过控制调整反应条件,包括第二自动控制热交换容腔各段的温度、两根圆柱轴同向旋转的转速及反应时间,使双螺杆圆柱钢块组合反应得到产物满足后续工段的使用;步骤1和步骤2的顺序可以交换,也可以同时进行。优选地,所述步骤1具体为:固体原料加入所述料仓,经第一螺旋泵通过物料通道输送至失重电子秤,所述称重传感器传导数据给PLC,经比较计算再设定变频器频率,调整第一螺旋泵和第二螺旋泵的转速,所述固体原料通过第二螺旋泵经物料通道向下输送;所述步骤2具体为:液体原料加入所述料桶,经流量计和柱塞泵通过物料通道输送至失重电子称,液体原料达到设定的质量时,所述失重电子称中的称重传感器传导数据给PLC,经比较计算再设定变频器频率,调整柱塞泵和隔膜泵的转速,所述液体原料通过隔膜泵经物料通道向初级螺杆反应器输送。优选地,所述步骤3中,控制调整反应温度通过控制第一自动控制热交换容腔各段的温度来实现,所述步骤4中,控制调整反应温度通过控制第二自动控制热交换容腔各段的温度来实现。优选地,所述步骤4中,透明物料进入双螺杆圆柱钢块组合反应器之前,所述第二自动控制热交换容腔内预先充满阻聚剂溶液。本发明的一种氨基树脂的连续化生产装置及方法,连续化生产装置包括依次密闭连通的原料自动连续配料器、初级螺杆反应器和双螺杆圆柱钢块组合反应器,将固体原料和液体原料通过原料自动连续配料器加入到初级螺杆反应器,保证了单位时间内向初级螺杆反应器内输入设定量的原料数量;初级螺杆反应器内密闭于第一热交容腔内的初级螺杆设计为交替排列的若干输送段和若干混合段,第一热交换容腔对应于初级螺杆的若干输送段和若干混合段相应地设计为若干段,每一段设置有热交换机进行温控,这样可以控制温度、初级螺杆转速和混合及反应时间(输送段可以根据具体要求设计不同导程的初级螺杆输送螺旋槽)使固体、液体各组分充分混合,然后混合物料进入高温段,边推进边混合边反应,使反应混合物在初级螺杆反应器出口前完成第一阶段聚合反应,生成透明的短链氨基树脂;双螺杆圆柱钢块组合反应器内密闭于第二热交换容腔内的两根圆柱轴、安装在两根平行的圆柱轴上的圆柱钢块,圆柱钢块若干块为一组,每一组内各圆柱钢块前后紧贴不同心地安装在圆柱轴上,每一组圆柱钢块交替安装,使得两根圆柱轴同向旋转时带动两根圆柱轴上相对的圆柱钢块组交错旋转,第二热交换容腔设计为若干段,每一段设置有热交换机进行温控,并在第二热交换容腔内加满阻聚剂溶液,这样可以通过控制第二热交换容腔不同段的温度、圆柱轴转速、阻聚剂浓度和反应时间,使得先期达到双螺杆圆柱钢块组合反应器内的物料须经适当的速度边反应边推进,效果等同不反流,随后的物料紧随,效果等同不向前越界,这样保证先进入的物料经充分反应后先排出,后进入的物料经充分反应后后排出,所有液体物料效果等同不无序串流,保证物料在双螺杆圆柱钢块组合反应器内的反应程度相同,从而使得反应产物一致且程度充分,即是最先进入双螺杆圆柱钢块组合反应器的物料(树脂)分散到阻聚剂溶液中,阻聚剂浓度比较高,聚合反应得到抑制,随着物料(树脂)的进入,阻聚剂浓度减小,聚合反应速度增加,待阻聚剂溶液完全排出后物料(树脂)聚合反应已经达到平衡并调整到反应终点,此后反应速度平衡,产品便可以连续不断地供下一工段使用;依次连通的原料自动连续配料器、初级螺杆反应器和双螺杆圆柱钢块组合反应器之间均为密闭连通,优化了环保排放指标,基本达到化工原料及半成品零排放,提高了质量稳定性。附图说明图1为本发明的一种氨基树脂的连续化生产装置结构示意图;图2为本发明的原料(固体原料和液体原料)自动连续配料器结构示意图;图3为本发明的初级螺杆反应器的初级螺杆结构示意图;图4为本发明的双螺杆圆柱钢块组合反应器的两根圆柱轴、安装在两根平行的圆柱轴上的圆柱钢块的结构示意图;图5为本发明的一种氨基树脂的连续化生产方法流程示意图。其中,1-原料自动连续配料器,11-料仓(或料桶),12-第一螺旋泵(或柱塞泵),13-第二螺旋泵(或隔膜泵),14-失重电子秤,15-称重传感器,16-PLC,17-变频器,18-流量计,2-初级螺杆反应器,21-初级螺杆,211-输送螺旋槽(211a-大导程输送螺旋槽,211b-小导程输送螺旋槽),212-混合螺旋槽,22-第一热交换容腔,3-双螺杆圆柱钢块组合反应器,31-圆柱轴,32-圆柱钢块,33-第二热交换容腔,4-物料通道,5-阻聚剂溶液,6-观察视镜,图中箭头的方向为原料或产物流动的方向。图1中M为电机标识,EX-101为初级螺杆反应器的标牌号,EX-102为双螺杆圆柱钢块组合反应器的标牌号。具体实施方式以下结合实施例对本发明作进一步描述:实施例1:如图1~4所示,一种氨基树脂的连续化生产装置,包括依次连通的原料自动连续配料器1、初级螺杆反应器2和双螺杆圆柱钢块组合反应器3,原料自动连续配料器1包括固体原料自动连续配料器和液体原料自动连续配料器,根据固体原料的种类相应设置有多个固体原料自动连续配料器,本实施例有三聚氰胺、多聚甲醛、碳酸钠3种固体原料,根据液体原料的种类相应设置有多个液体原料自动连续配料器,本实施例有脱盐水、乙二醇2种液体原料;固体原料自动连续配料器包括料仓11、第一螺旋泵12和第二螺旋泵13、失重电子秤14、称重传感器15、PLC16、变频器17,料仓11在上方,经物料通道4下连第一螺旋泵12,再经物料通道4连接设有称重传感器15的失重电子秤14,再经物料通道4连接第二螺旋泵13,称重传感器15、变频器17均与PLC16相连;液体原料自动连续配料器包括料桶11、流量计18、柱塞泵12、失重电子秤14、称重传感器15、PLC16、变频器17、隔膜泵13,料桶11在上方,经物料通道4下连流量计18和柱塞泵12,再经物料通道4连接设有称重传感器15的失重电子秤14,再经物料通道4连接隔膜泵13,称重传感器15、变频器17均与PLC16相连;所述3个固体原料自动连续配料器和2个液体原料自动连续配料器分别和初级螺杆反应器2连通,初级螺杆反应器2包括第一热交换容腔22和密闭于第一热交容腔22内的初级螺杆21,初级螺杆21设计为交替排列的若干输送段和若干混合段,输送段设置具有输送作用的的输送螺旋槽211,需要大导程输送时设计大导程输送螺旋槽211a,需要小导程输送时设计小导程输送螺旋槽211b,以便控制输送时间,本实施例中设计为小导程输送螺旋槽211b,混合段设置具有混合作用的混合螺旋槽212,以达到好的混合效果,第一热交换容腔22对应于初级螺杆21的若干输送段和若干混合段相应地设计为若干段,每一段设置有热交换机进行温控,以保证对反应温度有效地控制,初级螺杆反应器2集输送(推进)、混合螺旋槽交错排列于一根螺杆上,并且温度分段控制,达到很好的反应效果,保证第一反应阶段的生成的短链氨基树脂质量均匀;双螺杆圆柱钢块组合反应器3包括第二热交换容腔33和密闭于第二热交换容腔33内的两根圆柱轴31、安装在两根平行的圆柱轴31上的圆柱钢块32,圆柱钢块32若干块为一组,本实施例中三块为一组,每一组内各圆柱钢块32前后紧贴不同心地安装在圆柱轴31上,每一组圆柱钢块32交替安装,使得两根圆柱轴31同向旋转时带动两根圆柱轴31上相对的圆柱钢块32组交错旋转,第二热交换容腔33设计为若干段,每一段设置有热交换机进行温控,以保证对反应温度有效地控制,双螺杆圆柱钢块组合反应器3使得第一反应阶段生成的短链氨基树脂在其中停留的时间长,慢推进,容量大,集合了塑料机械连续及间歇反应釜的大容量特点,能大容量地连续推进。实施例2:如图1~4所示,一种氨基树脂的连续化生产装置,与实施例1相比不同之处在于:有配备三聚氰胺、多聚甲醛、甲酸钠、邻苯二甲酸酐的4个固体原料自动连续配料器和配备脱盐水、磷酸的2个液体原料自动连续配料器;本实施例中输送螺旋槽211设计为大导程输送螺旋槽211a;第一热交换容腔22为第一自动控制热交换容腔,第一热交换自动控制容腔对应于初级螺杆21的若干输送段和若干混合段相应地设计为若干段,每一段设置有一台自动控制的热交换机进行温控,以保证对反应温度精确自动地控制;第二热交换容腔33为第二自动控制热交换容腔,第二自动控制热交换容腔设计为若干段,每一段设置有一台自动控制的热交换机进行温控,以保证对反应温度精确自动地控制;其余同实施例1。实施例3:如图1~4所示,一种氨基树脂的连续化生产装置,与实施例2相比不同之处在于:有配备三聚氰胺、多聚甲醛、碳酸钠的3个固体原料自动连续配料器和配备脱盐水、硫酸、次磷酸的3个液体原料自动连续配料器;本实施例中输送螺旋槽211设计为大导程输送螺旋槽211a,本实施例中最大导程是50mm(流量与转速也有关系,目前的转速是110转/分钟,流量的值为3公斤/分钟的树脂);本实施例中,依次用管道连通的原料自动连续配料器1、初级螺杆反应器2和双螺杆圆柱钢块组合反应器3之间均为密闭连通,反应在密闭的连续化生产装置内部进行,没有任何化学成分外排,优化了环保排放指标,基本达到零排放,这是相对于间歇反应釜有向外排放废物而言的;第二热交换容腔33内预先充满阻聚剂溶液5,阻聚剂溶液5可以为对苯醌、氯化亚铜的混合物,重量百分比各0.1%,或者用间二硝基苯与氯化铁的混合物,重量百分比各0.1%;预先充满惰性阻聚剂溶液5,阻聚剂溶液5比例大时进入双螺杆圆柱钢块组合反应器3的第一反应阶段的生成物(简称物料)浓度就小,反应速度就缓慢,随着阻聚剂溶液5的外排,物料浓度逐渐增大,反应速度也上升;当阻聚剂溶液5完全排净,物料进出和反应也达到平衡并逐渐连续稳定外排,达到连续生产目的,实际就是阻聚剂溶液5的浓度变化使先期进入的物料反应速度减慢,后期进入的物料反应速度相对较快,能达到最终反应平衡。预先充满惰性阻聚剂溶液5,能达到的实际效果即是:先期达到双螺杆圆柱钢块组合反应器3的物料须经适当的速度边反应边推进不能反流,随后的物料紧随但不能向前越界,这样保证先进的物料经充分反应后先排出,后进的物料经充分反应后后排出,所有液体物料均不得无序串流,保证物料在双螺杆圆柱钢块组合反应器3中的停留时间固定,从而反应程度一致且充分;在初级螺杆反应器2末端设置观察视镜6,使在初级螺杆反应器2中完成第一阶段聚合反应生成的短链氨基树脂,即进入双螺杆圆柱钢块组合反应器3前的反应混合物,可以透过观察视镜6看到其反应程度是否适当,通常物料呈透明状则合格,调整适当后经高温保温通过管道连通输送到双螺杆圆柱钢块组合反应器3内进行聚合反应;其余内容同实施例2。实施例4:如图5所示,对应于实施例2的连续化生产装置的一种氨基树脂的连续化生产方法,按如下步骤实现:步骤1,固体原料自动连续配料,固体原料通过所述固体原料自动连续配料器1配料并加入生产装置,即进入初级螺杆反应器2,具体为:固体原料加入所述料仓11,经第一螺旋泵12通过物料通道4输送至失重电子秤14,所述称重传感器15传导数据给PLC16,经比较计算再设定变频器17的频率,调整第一螺旋泵12和第二螺旋泵13的转速,所述固体原料通过第二螺旋泵13经物料通道4向初级螺杆反应器2输送,这样进出料永远达到平衡,保证了单位时间内向初级螺杆反应器2输入设定量的固体原料数量;步骤2,液体原料自动连续配料,液体原料通过所述液体原料自动连续配料器配料并加入生产装置,即进入初级螺杆反应器2,具体为:液体原料加入所述料桶11,经流量计18和柱塞泵12通过物料通道4输送至失重电子称14,液体原料达到设定的质量时,所述失重电子称14中的称重传感器15传导数据给PLC16,经比较计算再设定变频器17的频率,调整柱塞泵12和隔膜泵13的转速,液体原料通过隔膜泵13经物料通道4向初级螺杆反应器2进行单位时间的固定量液体原料的输送,使进出料平衡,保证计量的准确稳定;步骤3,初级螺杆反应,加入生产装置的固体原料和液体原料,进入所述初级螺杆反应器2,通过控制调整反应条件,包括第一自动控制热交换容腔各段的温度、初级螺杆21的转速及反应时间,每一段设置有一台自动控制的热交换机进行温控,使初级螺杆聚合反应所得短链氨基树脂为透明物料;所配备的自动控制的热交换机,除了设置有循环输送导热姆的油泵外,关键是还设置有给导热油加热和冷却的热交换器,经PLC16控制的温度精度高,控制灵活便捷,使得工艺控制有了保障;步骤4,双螺杆圆柱钢块组合反应,经初级螺杆反应流出的透明物料进入双螺杆圆柱钢块组合反应器3,通过控制调整反应条件,包括第二自动控制热交换容腔各段的温度、两根圆柱轴31同向旋转的转速及反应时间,每一段设置有一台自动控制的热交换机进行温控,使双螺杆圆柱钢块组合反应得到产物从双螺杆圆柱钢块组合反应器3末端逸出满足后续工段的使用;步骤1和步骤2的顺序可以交换,也可以同时进行,本实施例中两步骤同时进行。按时间顺序具体步骤内容如下:启动固体原料自动连续配料器1~4号(第一个配料器编为1号,第二个配料器编为2号,第三个配料器编为3号,第四个配料器编为4号),液体原料自动连续配料器1~2号(第一个配料器编为1号,第二个配料器编为2号),按摩尔比计算的单位时间加料的重量,同时向初级螺杆反应器2加入物料,并启动初级螺杆反应器的初级螺杆21电机对加入物料进行输送和混合,开始树脂的初级聚合反应。启动自动控制的热交换机第1台~第6台,设置第1~2台温度为50℃,为第1~20输送螺旋槽211预热,设置第3~6台自动控制的热交换机温度为80℃,为初级螺杆反应器2的其余输送螺旋槽211和混合螺旋槽212预热,设置第7~15台自动控制的热交换机温度为90℃,为双螺杆圆柱钢块组合反应器3预热。待油温和输送螺旋槽211、混合螺旋槽212及双螺杆圆柱钢块组合反应器3显示温度稳定后开始下一步的工作。约25分钟后,初级螺杆21末端观察视镜6可观察到透明物料流过,说明初级螺杆反应器2输送混合速度与设定反应量吻合,继续观察后续过程。透明物料保持约85℃进入卧式放置的双螺杆圆柱钢块组合反应器3,因为聚合反应初期吸热,中期放热,后期自身反应基本能保持热平衡,所以自动控制的热交换机的加热端和冷却端均须满足系统要求的温度条件,由系统自动调节以便加热或冷却,满足聚合反应的需要。约30分钟后双螺杆圆柱钢块组合反应器3末端开始逸出热的树脂产品,取适量样品降温至25℃检测粘度,密度,容忍度等,符合质量要求的产品可以供后续工段使用,如果检测指标需要调整,则可适当调整自动控制的热交换机控制温度、两根圆柱轴31转速来调整反应程度。实施例5:如图5所示,对应于实施例3的连续化生产装置的一种氨基树脂的连续化生产方法,按如下步骤实现:步骤1,内容同实施例4;步骤2,内容同实施例4;步骤3,初级螺杆反应,加入生产装置的固体原料和液体原料,进入所述初级螺杆反应器2,通过控制调整反应条件,包括第一自动控制热交换容腔各段的温度、初级螺杆21的转速及反应时间,每一段设置有一台自动控制的热交换机进行温控,表1列出了进入初级螺杆反应器的物料量与转速、温度的三组匹配数值;表1第一组第二组第三组固、液物料总量2.5公斤/分钟3公斤/分钟4公斤/分钟转速80-100转/分钟100-120转/分钟120-130转/分钟温度80-85℃103-105℃99-101℃初级螺杆聚合反应所得短链氨基树脂为透明物料;所配备的自动控制的热交换机,除了设置有循环输送导热姆的油泵外,关键是还设置有给导热油加热和冷却的热交换器,经PLC16控制的温度精度高,控制灵活便捷,使得工艺控制有了保障;步骤4,双螺杆圆柱钢块组合反应,经初级螺杆反应流出的短链氨基树脂(透明物料)进入双螺杆圆柱钢块组合反应器3,在此之前,所述第二自动控制热交换容腔内预先充满阻聚剂溶液5,阻聚剂溶液5为对苯醌、氯化亚铜的混合物,重量百分比各0.1%,通过控制调整反应条件,包括第二自动控制热交换容腔各段的温度、两根圆柱轴31同向旋转的转速及反应时间,每一段设置有一台自动控制的热交换机进行温控,转速一定,物料停留时间即反应时间就一定,反应程度与经初级螺杆反应流出的透明物料的浓度的变化相适应,以达到惰性阻聚剂溶液5预先填充的目的,表2列出了经初级螺杆反应流出的透明物料量与转速、温度的三组匹配数值,经双螺杆圆柱钢块组合反应得到产物从双螺杆圆柱钢块组合反应器3末端逸出满足后续工段的使用;表2步骤1和步骤2的顺序可以交换,也可以同时进行,本实施例中两步骤同时进行。按时间顺序具体步骤内容如下:启动固体原料自动连续配料器1~3号(第一个配料器编为1号,第二个配料器编为2号,第三个配料器编为3号),液体原料自动连续配料器1~3(第一个配料器编为1号,第二个配料器编为2号,第三个配料器编为3号)号,按摩尔比计算的单位时间加料的重量,同时向初级螺杆反应器2加入物料,并启动初级螺杆反应器的初级螺杆21电机对加入物料进行输送和混合,开始树脂的初级聚合反应。启动自动控制的热交换机第1台~第6台,设置第1~2台温度为50℃,为第1~20输送螺旋槽211预热,设置第3~6台自动控制的热交换机温度为80℃,为初级螺杆反应器2的其余输送螺旋槽211和混合螺旋槽212预热,设置第7~15台自动控制的热交换机温度为100℃,为双螺杆圆柱钢块组合反应器3预热。待油温和输送螺旋槽211、混合螺旋槽212及双螺杆圆柱钢块组合反应器3显示温度稳定后开始下一步的工作。约25分钟后,初级螺杆21末端观察视镜6可观察到透明物料流过,说明初级螺杆反应器2输送混合速度与设定反应量吻合,继续观察后续过程。透明物料保持约85℃进入卧式放置的双螺杆圆柱钢块组合反应器3,因为聚合反应初期吸热,中期放热,后期自身反应基本能保持热平衡,所以自动控制的热交换机的加热端和冷却端均须满足系统要求的温度条件,由系统自动调节以便加热或冷却,满足聚合反应的需要。约30分钟后双螺杆圆柱钢块组合反应器3末端开始逸出热的树脂产品,取适量样品降温至25℃检测粘度,密度,容忍度等,符合质量要求的产品可以供后续工段使用,如果检测指标需要调整,则可适当调整自动控制的热交换机控制温度、两根圆柱轴31转速来调整反应程度。连续化生产装置自洁效果良好,连续生产不需要清洗,计划停车须提前停止进料,初级螺杆反应器2和双螺杆圆柱钢块组合反应器3充分输送排空,然后进料和出料口用铝箔密封,保持设备内壁不氧化腐蚀和干燥即可;按本实施例的方法生产出来的成品氨基树脂指标是:粘度7000mpas,密度1.34公斤/升,容忍度7,适合后端工序使用;按原间歇反应釜所得的成品氨基树脂指标是:粘度6000-7500mpas,密度1.3-1.35公斤/升,容忍度5-9,7小时后粘度7000-12000mpas,质量不稳,后段工序无法使用,会造成频繁盲目调整工艺。当前第1页1 2 3