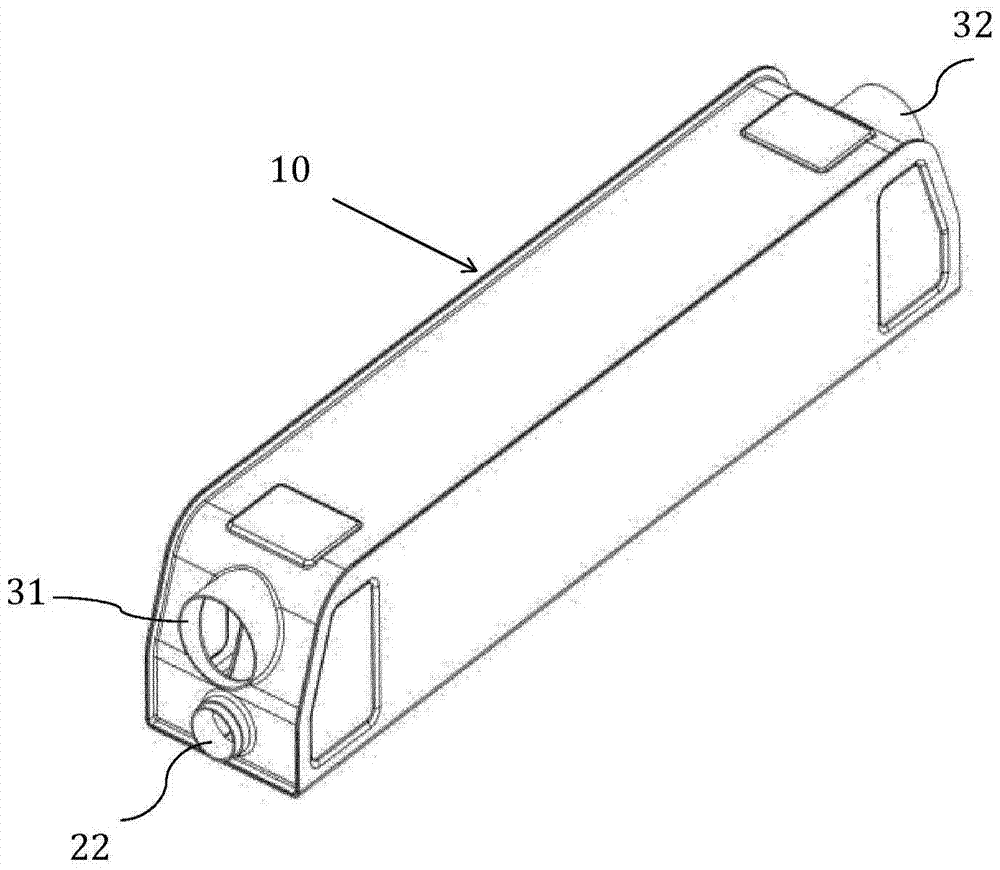
本发明涉及一种热交换器,诸如旨在用于汽车的热交换器。根据本发明的热交换器特别适合于在发动机排气管道中使用。这种类型的热交换器一般被称为排气再循环冷却器(EGR或EGRC交换器)。在汽车工业中使用的那类热交换器,更具体地说在内燃热发动机的排气管道内部使用的那类热交换器主要包括外壳或壳体,该外壳或壳体在其内部包括允许热从第一流体交换到第二流体的热交换元件。允许这样进行热交换的这些元件可以例如包括管。位于热交换器内部的这些管可以存在于包括彼此基本上平行地定位的多个管的交换管束内。这些管可以被定位成一行或彼此平行的若干行。这些管能够将所述管内的第一流体从交换管束的第一端部引导到交换管束的第二端部。相关的管在它们之间一起限定通道,这些通道将第二流体从热交换器的第二端部引导到热交换器的第一端部。因而,热交换器尤其允许该热交换器内的第一和第二流体作为逆流而循环。除了形成交换管束的这些管之外,还可以设置其它元件,诸如板、散热片和扰流器,以便提高第一流体和第二流体之间的热交换。从现有技术已知包括壳体的热交换器,该壳体能够在其内部收纳交换管束。该壳体表现为外壳,该外壳包括形成壳体的外部并限定容积的多个壁,热交换在该容积内进行。在该壳体的第一端部和第二端部中,该壳体主要设置有旨在用于第一和第二流体的入口和出口。这些入口和出口因而允许将热交换器分别连接至输入导管和输出导管,所述输入导管和输出导管适合于通过输入导管将第一流体和第二流体传导向热交换器,并且当所述第一流体和第二流体已经穿过热交换器时,通过输出导管将第一流体和第二流体传导到最终目的地。
背景技术:如上所述,在德国专利申请DE19927607中公开了一种热交换器。根据该文献,该热交换器包括多个管,这些管是通过在壳体内堆叠在彼此之上的板获得的,以便获得允许将第一流体从旨在用于该第一流体的入口引导到旨在用于该第一流体的出口的管。各种管在它们之间限定允许将第二流体从旨在用于该第二流体的入口引导到旨在用于该第二流体的出口的通道。根据德国专利申请DE19927607的热交换器适合于沿着壳体的纵向方向将第一流体从壳体的第一端部引导到壳体的第二端部。旨在用于第二流体的入口和出口位于壳体的侧壁上,以便允许所述第二流体沿着垂直于第一流体的流动方向的方向进入和退出。根据德国专利申请DE19927607的热交换器具有的第一缺陷是:流体的各种入口接头和出口接头位于形成热交换器的外部的壳体的四个不同壁上。旨在用于第一流体的入口和出口存在于壳体的在壳体的纵向方向上的端部上。旨在用于第二流体的入口和出口存在于壳体的侧壁上。这些流体入口和流体出口的定位限制了将热交换器安装在可用空间内的修改可能性。此外,根据德国专利申请DE19927607的热交换器的制造将第一流体和第二流体之间的热交换器限制于所述热交换器的长度的一部分,即限制在旨在用于第二流体的入口和出口之间。换言之,在第一流体的路径的一部分上不可能进行第一和第二流体之间的热交换。为此,相对于热交换器的外部尺寸来说,具有根据德国专利申请DE19927607的装置的热交换器并不是最佳的。如今,在汽车内部旨在用于热交换器及其部件的空间倾向于减小,以便集成汽车操作所需的其它装置。这意味着热交换器的集成越来越复杂。为此,重要的是研发出紧凑的热交换器,从而特别是在第一和第二流体的输入导管和输出导管的定位时允许相对自由地进行修改,以便能够尽可能高效地将热交换器组件集成到可用空间内。
技术实现要素:根据本发明的热交换器的目标在于通过针对交换管束的形成提出一种新的设计来找到对现有技术的已知热交换器的缺陷的补救方式,通过该设计可以提高所述热交换器的紧凑性。为此,本发明涉及一种热交换器,该热交换器允许在第一流体和第二流体之间进行交换热,所述热交换器包括:-壳体;和-位于所述壳体内的交换管束,-其中,所述交换管束包括:-主表面,该主表面包括主宽度并且由多个管形成,所述管适合于在这些管内部引导所述第一流体;-所述第一流体的入口,所述第一流体的入口朝向所述第一流体的出口并且允许在这些管外部引导所述第二流体;-所述第二流体的入口,所述第二流体的入口朝向所述第二流体的出口,-其中,所述管在至少一个第一端部处被组装,以便形成次表面,该次表面具有小于所述主宽度的次宽度,用于连接至所述第一流体的所述入口和/或所述出口,-其中,位于所述管的所述第一端部处的所述次表面被形成为用于在所述壳体和所述次表面的外面之间产生空间,该空间被连接至所述第二流体的所述入口和/或所述出口。根据本发明,可能的是,所述管在第一端部处被组装,以便形成用于连接至所述第一流体的所述入口的所述次表面,-其中,位于所述管的所述第一端部处的所述次表面被形成为用于在所述壳体和所述次表面的外面之间产生空间,该空间被连接至所述第二流体的所述出口;-并且其中,所述管在第二端部处被组装,以便形成次表面,该次表面具有小于所述宽度的次宽度,用于连接至所述第一流体的出口,位于所述管的所述第二端部处的所述次表面在所述壳体和所述次表面的外面之间产生空间,该空间被连接至所述第二流体的所述入口。因而,在第一阶段中,通过形成并组装根据本发明的交换管束,使旨在用于第一和第二流体的入口和出口位于所述壳体的相对端部处。入口和出口的这种集中增加了修改可能性并且允许以最佳方式将热交换器组件集成到可用空间中。此外,在第二阶段中,所述次表面允许将所述管的第二端部连接至所述出口而形成用于第一流体的入口的空间,并且具有能够沿着流体的全部路径(即从它们的入口到它们的相应出口)在第一和第二流体之间进行热交换的优点。由于该原因,相对于其外部尺寸增加了热交换器的效率。根据一个实施方式,根据本发明的热交换器包括允许在所述管的每个端部处覆盖所述管的密封元件。根据一个实施方式,根据本发明的热交换器包括连接元件,通过该连接元件,可通过所述连接元件将所述管的至少一个端部连接至入口或出口。根据本发明的一个实施方式,所述管相对于彼此定位成在所述管之间产生通道,并且其中所述通道包括扰流器。根据本发明的一个实施方式,所述热管束是通过彼此叠置的多个板获得的,并且其中,所述板的端部设置有边缘,该边缘允许增加在所述板和所述壳体的内部之间的表面面积。附图说明通过阅读参照附图进行的根据本发明的热交换器的优选实施方式的如下描述,本发明的目标、目的和特征及其优点将变得更清楚地明显,其中:图1示出了根据本发明的第一实施方式的热交换器的分解立体图;图2示出了处于组装形式的根据图1的热交换器;图3示出了根据图1和图2的热交换器的交换管束;图4详细地示出了一起形成根据图3的交换管束的一部分的两个板;图5示意性示出了交换管束的主表面的视图;图6示意性示出了交换管束的次表面的视图;图7示出了根据本发明的第二实施方式的热交换器的分解立体图;图8示出了根据图7的热交换器的交换管束;图9详细示出了根据图8的交换管束的端部;图10示出了根据本发明的热交换器的第三实施方式的分解立体图。具体实施方式图1以分解立体图示出了根据本发明的热交换器10的第一实施方式。热交换器10包括在组合时允许形成热交换器10的外部的第一元件11和第二元件12。组合的元件11和12形成了外壳或壳体11、12,该外壳或壳体11、12可以容纳允许使第一流体和第二流体之间的热交换最优化的元件。第二元件12包括第一和第二流体的各种入口和出口。存在于第二元件12中的入口21形成了旨在用于第一流体的入口。在相反面上,出口22形成了旨在用于第一流体的出口。入口31旨在用于第二流体。出口32旨在用于第二流体。在热交换器10的使用过程中,第一流体穿过入口21而进入所述热交换器10的内部。同时,第二流体经由入口31穿入热交换器10的内部。因而,热交换器10包括交换管束13,该交换管束13包括在组合时形成管和在所述管之间限定的通道的一叠板17。在图3和图4中更详细地示出交换管束13。如上所述,交换管束13包括一叠板17,其中由两个板构成的组件在其内部形成了允许将第一流体从其入口21引导到其出口22的管。通道限定在不同的管之间并且允许第二流体从其入口31循环到其出口32。出于实用原因并且考虑到便于参照图1所示的热交换器10,在图1中标示了尺寸L、l和h。字母L用来指代热交换器10的最大尺寸并且对应于使第一和第二流体循环的方向。字母l用来标示交换器10的宽度,而字母h用来标示热交换器10的高度。所述一叠板17能够获得交换管束13,并且根据图4中所示的布置出现。板17均具有适合于形成管的内壁并适合于暴露于第一流体的内面和相对面或外面。该外面在使用板17时与第二流体接触。图4示出了每个板17在其纵向长度上设置有弯曲元件。该弯曲元件适合于增加在板17的端部(如在纵向方向上看到的)和图1中所示的第一元件11的壁的内部之间的接触表面。这种表面增加方便使用钎焊法,从而允许将热交换器10的不同元件彼此组装在一起并确保最佳的接触,以便避免使用热交换器10时的可能流体泄漏。考虑到获得交换管束13,根据板的相关数量,将不同的板17定位成使得第一板17的内面指向第二板17的内面,所述第二板17定位成使其外面指向第三板17的内面,等等。在根据图1的热交换器10中,各种板17具有与所述热交换器10的壳体11、12内部的尺寸对应的尺寸。如图4所示,板17的宽度l对应于如图1所示的壳体11、12的内部宽度。交换管束的管的形状在这些管的端部处被修改而表现出收缩部。该交换管束在其端部中包括连接表面,不同管的出口被组装在该连接表面中。如图3所示,该连接表面适合于通过连接元件14而连接至旨在用于第二流体的出口32。图1描述了密封元件16,该密封元件16被修改成允许覆盖一起形成了交换管束13的板17的端部。该密封元件16允许将所述板17保持在一起,以便避免从管的内部向位于管的外部的通道或从位于管的外部的通道向管的内部的任何可能泄漏。连接元件14适合于将各管的连接表面连接至出口22。连接元件15设置在交换管束的相反侧上,以便将旨在用于第一流体的入口21连接至位于所述交换管束13的相反端部处的连接表面。根据本发明的热交换器的操作基于如下事实:板17的形状在它们的第一端部91和它们的第二端部92之间改变,如图4所示。在端部91和92处,这些板具有这样的形状,该形状允许在它们被组合时构成具有相对有限长度L的管,以便允许这些管具有更大宽度。位于这些管的端部处的区段的表面由术语“次表面”表示。在板17的中央93处,这些板17被修改成形成了具有相对较大L和更小宽度l的管。在本发明内,位于交换管束的中央区域中的这些管的中央的区段的表面由术语“主表面”表示。从端部91朝向中央部分,板17包括转换区域。从中央部分93朝向端部92,每个板17包括由附图标记95表示的转换区域。在图5和图6中以示意形式示出了板17的具体形状的技术效果。图5作为剖视图示出了交换管束13的一部分。这些管的内部由附图标记A表示。各个管通过表示为附图标记B的通道分开。管的内部A适合于引导第一流体,而通道B适合于引导作为逆流的第二流体。图5示出了在交换管束13的中央处,不同的流体被很好地分离并且可借助于各个壁进行热交换。在图6中从前面示意性地示出了交换管束13。根据图6,通过不同的转换区域94和95,由管和通道形成的组件的容积具体地分布在板17的端部处。这种容积分布与位于交换管束的端部之外的管和通道的容积分布不同。不同的表面A在它们的端部处形成次表面,该次表面可以经由连接元件14、15连接至旨在用于第一流体的入口/出口。位于表面A周围的自由空间允许进入不同的通道B,并且可以被连接至旨在用于第二流体的入口/出口。通过这些管的次表面,第二流体可以在包围连接元件14和管的收缩部的空间内进入穿入壳体。第一流体然后在由一起形成交换管束13的管A的组件的外部限定的通道内部被引导。第二流体在不同管之间被引导朝向包围管的收缩部和连接元件15的空间、朝向出口32。图1示出了交换管束的形状以及在它们的端部处通过板17的转换区域94和95而存在的收缩部,可在由元件11和12形成的壳体的内部以及在该收缩部及连接元件14的外部获得自由空间。在壳体内部产生的该空间允许连接旨在用于第二流体的入口31。朝向交换管束13指向入口31引导的第二流体可以因此在连接元件14外部和管的收缩部外部循环。换言之,这意味着可以通过连接元件14的壁而在第一流体和第二流体之间发生热交换,并且这可以在将第二流体引入热交换器10内之后马上发生。位于交换管束13的相对端部处的元件的相同布置允许在两种流体之间进行最佳的热交换,并且这种最佳热交换一直到旨在用于第二流体的出口32。图1中所示的不同元件通过现有技术中已知的钎焊法进行组装。考虑到将不同元件组装到热交换器10内部,将所述元件预组装成与它们在壳体11、12内的姿态相同的姿态并且引入炉内。铝和不锈钢是特别适合于通过钎焊法形成根据本发明的热交换器10的材料。图2示出了位于组装姿态的根据图1的热交换器10的立体图。图2示出了根据本发明的热交换器10是相对紧凑的。另外,不同的入口和出口21(未示出)、22、31和32集中在一起,以便使得热交换器10在例如汽车内部的最终安装最优化。图3详细示出了热交换管束13,板17被堆叠成一起从而在它们的内部形成管以及通道的不同管之间的限定部,这些管允许将第一流体从这些管的第一端部131引导到这些管的第二端部132,所述通道允许引导第二流体。扰流器18已存在于不同板17之间。所述扰流器18具有在使用热交换器10时提高第一流体和第二流体之间的热交换的作用。图7示出了根据本发明的热交换器的第二实施方式。图7示出了热交换器40,其结构类似于根据图1的热交换器10。只有形成交换管束43的板与热交换器10的那些板不同地定位。实际上,这些板相对于热交换器40的长度L竖直地定位。热交换器40包括作为组件时形成外壳或壳体41、42的第一元件41和第二元件42,以便形成所述热交换器40的外部。壳体41、42适合于容纳交换管束43。该交换管束43包括图8和图9中所示的一叠板27。组合在一起的不同板27形成管,这些管能够在它们的内部将第一流体从交换管束43的第一端部引导到第二端部。不同管一起限定了通道,所述通道允许将第二流体在这些管的外部从交换管束43的第二端部引导到第一端部。不同管的端部具有收缩部,所述端部被一起集中在该收缩部中,以便形成连接表面,所述连接表面适合于通过接头连接至旨在用于第一流体的相应入口/出口。在图8和9中清楚可见具有收缩部的端部。如图7所示,旨在用于第一流体的入口51(部分可见)和出口52存在于第二元件42中。入口51被修改成连接至连接元件45并用于通过该元件45将第一流体从其入口51引导向交换管束43的管的内部。出口52被修改成连接至连接元件44并且用于将第一流体从不同管的出口和连接元件44引导向其出口52。此外,第二元件42包括允许第二流体穿入壳体的内部的入口61和出口62(部分可见)。通过存在于交换管束43的第二端部处的收缩部,可以将第二流体引导到连接元件44的外部以及管的端部的外部,以便在由不同管限定的通道内部延续其路径。第二流体可以被引导向围绕管的第二端部和连接元件45的外部的敞开空间,以便通过出口63离开热交换器40。热交换器40包括密封元件46,该密封元件46有可能将不同的管的端部保持在一起并提高所述管的密封,因而避免可能的流体泄漏。图8示出了管66的端部与第一连接元件44和第二连接元件45的连接。图8示出了交换管束43的详细视图。交换管束包括管66,每个管66都是通过堆叠与图4中所示的板相当的两个板形成的。在不同管66之间可见扰流器68,该扰流器便于管66内部的第一流体和管66外部的第二流体之间的交换。不同的管66的端部在图7中更详细地示出。图7示出了管的不同端部一起形成了次表面。该次表面适合于连接至连接元件44,如图7所示。为了改进密封,管66的不同端部覆盖有密封元件46。图9示出了通过连接管的不同端部而获得的次表面。如图7、图8和图9中所示的不同元件可以通过钎焊法进行组装。为了实施该钎焊法,将不同元件组装成处于它们不同的相应姿态并引入到炉内。图10示出了根据本发明的第三实施方式的热交换器70,以分解立体图例示热交换器70。如图10所示,该热交换器70包括一起形成壳体的第一元件71和第二元件72。交换管束73存在于所述壳体内。根据图10和图11的热交换器70的使用与以上所述的热交换器10和40的使用类似。热交换器70与热交换器10和40之间的区别在于如下事实:不同的管在它们的收缩部之后利用它们的组装表面直接连接至存在于壳体外部的入口/出口。这意味着根据图10和图11的允许引导第二流体的连接元件位于壳体外部。