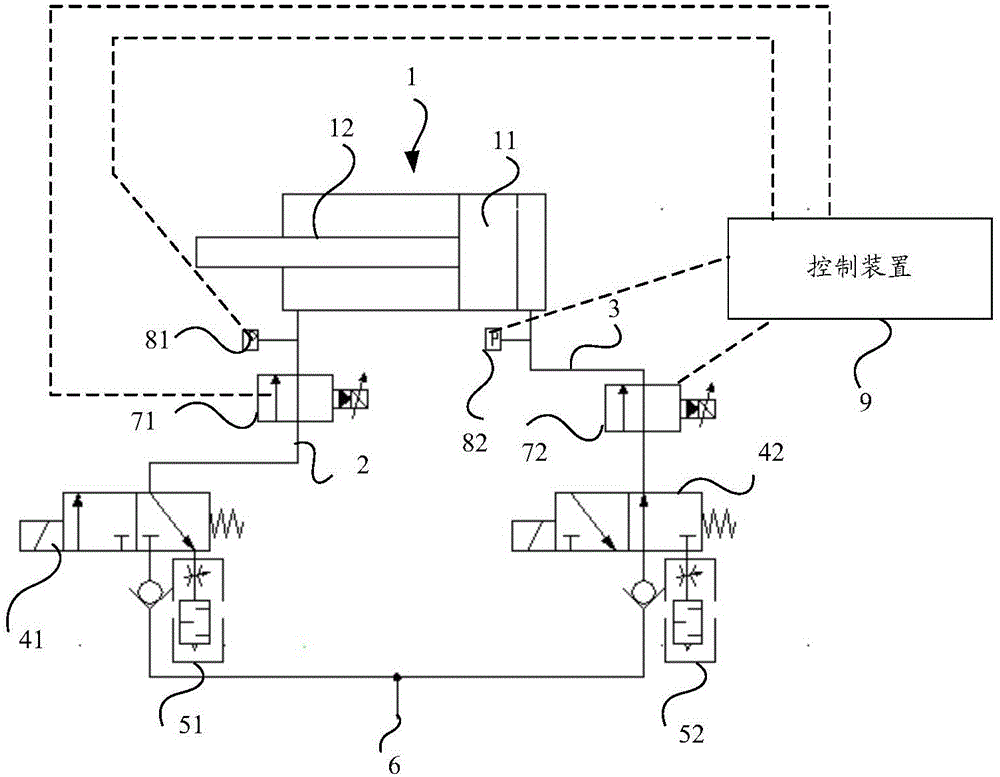
本发明涉及机械设备
技术领域:
,特别涉及一种气缸的控制方法、装置、系统以及机械设备。
背景技术:
:在干混砂浆领域,砂的计量阀多采用气动插板阀,由于砂对蝶阀的磨损过大,采用插板阀能够减少磨损。现有技术中的插板阀的结构如图1所示,图1为现有技术中的插板阀的控制系统结构示意图,主要包括:气缸01、第一输送管路02、第二输送管路03、第一单向节流阀041、第二单向节流阀042、第一换向阀051、第二换向阀052、进气管路06、第一存储箱071和第二存储箱072,气缸01上设有第一接口和第二接口、且第一接口和第二接口分别与气缸的有杆腔和无杆腔连通,第一输送管路02通过第一单向节流阀041、第一换向阀051将第一接口分别与第一存储箱071和进气管路06连通,第二输送管路03通过第二单向节流阀042、第二换向阀052将第二接口分别与第二存储箱072和进气管路06连通。气动插板阀在中间限位时(即停留在中间预定位置),需要向气缸的无杆腔和有杆腔同时通入气体,以使活塞保持在中间限位点处,但是现有的活塞无法精准定位,气缸在运行到中间限位点时,活塞在惯性的作用下将继续往前移动,从而无法精准定位中间限位点。如果将该气缸应用在气动插板阀等场合,将导致使用气动插板阀进行计量时,由于气缸的活塞在中间点限位无法精准定位,流量将无法保持稳定,从而造成计量不准确现象的发生。技术实现要素:本发明提供了一种气缸的控制系统、方法、装置和机械设备,用以提高气缸活塞的定位精度,提高工程机械的工作安全性。为达到上述目的,本发明提供如下技术方案。本发明提供了一种气缸的控制系统,包括:气缸、供气管路、一端与所述气缸的有杆腔连通、另一端与所述供气管路连通的第一输送管路、以及一端与所述气缸的无杆腔连通、另一端与所述供气管路连通的第二输送管路,还包括:采集装置,用于采集所述有杆腔内的第一压强和所述无杆腔内的第二压强;控制装置,用于确定所述气缸的活塞在运动方向上的惯性压强;还用于根据确定的所述惯性压强、所述活塞背离其运动方向的一端所在的腔室的压强以及预先存储的活塞背离其运动方向的一端的受力面积,得到所述活塞背离其移动方向的一端所受的第一压力;根据获得的所述活塞朝向其运动方向的一端所在的腔室的压强以及预先存储的活塞朝向其运动方向的一端的受力面积,得到所述活塞朝向其移动方向的一端所受的第二压力;并控制所述第一控制阀和/或第二控制阀的开度以控制有杆腔和/或无杆腔内的压强,使第一压力与第二压力的差值小于或等于预设压力值。本发明提供的气缸的控制系统,在控制气缸移动时,考虑到气缸的惯性力对气缸活塞所受的压强的影响,通过采集所述有杆腔内的第一压强和所述无杆腔内的第二压强;并确定所述气缸的活塞在运动方向上的惯性压强;根据确定的所述惯性压强、所述活塞背离其运动方向的一端所在的腔室的压强以及预先存储的活塞背离其运动方向的一端的受力面积,得到所述活塞背离其移动方向的一端所受的第一压力;根据获得的所述活塞朝向其运动方向的一端所在的腔室的压强以及预先存储的活塞朝向其运动方向的一端的受力面积,得到所述活塞朝向其移动方向的一端所受的第二压力;并控制所述第一控制阀和/或第二控制阀的开度以控制有杆腔和/或无杆腔内的压强,使第一压力与第二压力的差值小于或等于预设压力值。即可以提高控制活塞停止位置的精度。所以,本发明提供的气缸的控制系统,可以气缸的定位精度,提高机械设备的工作安全性。在一些可选的实施方式中,所述采集装置包括:分别用于采集所述第一输送管路和所述第二输送管路内的压强的第一压力传感器和第二压力传感器。在一些可选的实施方式中,上述控制系统还包括:输入装置,用于向所述控制装置输入所述惯性压强。在一些可选的实施方式中,上述控制系统还包括:惯性压强数据库;所述控制装置用于根据活塞的理论停止位置查询所述惯性压强数据库,得到所述惯性压强。在一些可选的实施方式中,上述控制系统还包括:设置于所述第一输送管路上的第一存储箱和第一换向阀,所述第一换向阀至少包括:第一工作口、第二工作口和第三工作口,所述第一工作口与所述气缸的有杆腔连通,所述第二工作口与所述供气管路连通,所述第三工作口与所述第一存储箱连通,其中:当所述第一换向阀处于第一工作状态时,所述第一工作口和所述第二工作口连通,当所述第一换向阀处于第二工作状态时,所述第一工作口和所述第三工作口连通;设置于所述第二输送管路上的第二存储箱和第二换向阀,所述第二换向阀至少包括:第一工作口、第二工作口和第三工作口,所述第一工作口与所述气缸的无杆腔连通,所述第二工作口与所述供气管路连通,所述第三工作口与所述第二存储箱连通,其中:当所述第二换向阀处于第一工作状态时,所述第一工作口和所述第二工作口连通,当所述第二换向阀处于第二工作状态时,所述第一工作口和所述第三工作口连通;所述气缸上设有第一接口和第二接口、且第一接口和第二接口分别与气缸的有杆腔和无杆腔连通,所述第一控制阀设置于所述第一接口和所述第一换向阀之间,所述第二控制阀设置于所述第二接口和所述第二换向阀之间。在一些可选的实施方式中,所述第一压力传感器设置于所述第一接口和所 述第一控制阀之间,所述第二压力传感器设置于所述第二接口和所述第二控制阀之间。本发明还提供了一种机械设备,包括气缸,还包括上述任一项所述的气缸的控制系统。本发明还提供了一种气缸的控制方法,包括:获得气缸的有杆腔内的第一压强和气缸的无杆腔内的第二压强;确定所述气缸的活塞在运动方向上的惯性压强;根据确定的所述惯性压强、所述活塞背离其运动方向的一端所在的腔室的压强以及预先存储的活塞背离其运动方向的一端的受力面积,得到所述活塞背离其移动方向的一端所受的第一压力;根据获得的所述活塞朝向其运动方向的一端所在的腔室的压强以及预先存储的活塞朝向其运动方向的一端的受力面积,得到所述活塞朝向其移动方向的一端所受的第二压力;并控制所述第一控制阀和/或第二控制阀的开度以控制有杆腔和/或无杆腔内的压强,使第一压力与第二压力的差值小于或等于预设压力值。在一些可选的实施方式中,所述确定所述气缸的活塞在运动方向上的惯性压强;具体包括:根据活塞的理论停止位置查询所述惯性压强数据库,得到所述惯性压强。在一些可选的实施方式中,所述惯性压强数据库按照以下步骤构建:S1、在控制气缸运动之前,将惯性压强设置为0;S2、根据活塞的理论停止位置,控制气缸运动和停止;S3、获取活塞的理论停止位置与实际停止位置之间的位移差;S4、为获取的所述位移差设置惯性压强数值,重复步骤S2、S3,直至所述位移差为零时,执行步骤S5;S5、获取并记录所述理论停止位置以及与所述位移差为零时对应设置的惯性压强,得到所述惯性压强数据库。在一些可选的实施方式中,所述控制所述第一控制阀和/或第二控制阀的开 度以控制无杆腔和/或有杆腔内的压强,使第一压力与第二压力的差值小于或等于预设压力值,具体包括:当所述气缸的活塞向所述气缸的缸体内移动时,控制所述第二控制阀的开度以控制无杆腔内的压强,使第一压力与第二压力的差值小于或等于预设压力值;当所述气缸的活塞向所述气缸的缸体外移动时,控制所述第一控制阀的开度以控制有杆腔内的压强,使第一压力与第二压力的差值小于或等于预设压力值。本发明还提供了一种控制装置,包括:第一获得模块,用于获得的气缸的有杆腔内的第一压强和气缸的无杆腔内的第二压强;第二获得模块,用于获得所述活塞在运动方向上的惯性压强;处理模块,用于根据确定的所述惯性压强、所述活塞背离其运动方向的一端所在的腔室的压强以及预先存储的活塞背离其运动方向的一端的受力面积,得到所述活塞背离其移动方向的一端所受的第一压力;根据获得的所述活塞朝向其运动方向的一端所在的腔室的压强以及预先存储的活塞朝向其运动方向的一端的受力面积,得到所述活塞朝向其移动方向的一端所受的第二压力;并控制所述第一控制阀和/或第二控制阀的开度以控制有杆腔和/或无杆腔内的压强,使第一压力与第二压力的差值小于或等于预设压力值。在一些可选的实施方式中,所述第二获得模块具体用于:根据活塞的理论停止位置查询所述惯性压强数据库,得到所述惯性压强。在一些可选的实施方式中,所述处理模块具体用于:当所述气缸的活塞向所述气缸的缸体内移动时,控制所述第二控制阀的开度以控制无杆腔内的压强,使第一压力与第二压力的差值小于或等于预设压力值;当所述气缸的活塞向所述气缸的缸体外移动时,控制所述第一控制阀的开 度以控制有杆腔内的压强,使第一压力与第二压力的差值小于或等于预设压力值。附图说明图1为现有技术中的插板阀的控制系统结构示意图;图2为本发明实施例提供的气缸的控制系统结构示意图;图3为本发明实施例提供的气缸的控制方法流程图;图4为本发明实施例提供的气缸的控制装置结构示意图。附图标记:01-气缸02-第一输送管路03-第二输送管路041-第一单向节流阀042-第二单向节流阀051-第一换向阀052-第二换向阀06-供气管路071-第一存储箱072-第二存储箱1-气缸11-活塞12-活塞杆2-第一输送管路3-第二输送管路41-第一换向阀42-第二换向阀51-第一存储箱52-第二存储箱6-供气管路71-第一控制阀72-第二控制阀81-第一压力传感器82-第二压力传感器9-控制装置1011-第一获得模块1012-第二获得模块102-处理模块具体实施方式下面将结合本发明实施例中的附图,对本发明实施例中的技术方案进行清 楚、完整地描述,显然,所描述的实施例仅仅是本发明一部分实施例,而不是全部的实施例。基于本发明中的实施例,本领域普通技术人员在没有做出创造性劳动前提下所获得的所有其他实施例,都属于本发明专利保护的范围。气缸的活塞在中间限位时,需要向气缸的无杆腔和有杆腔同时通入气体,以使活塞保持在中间限位点处,但是现有的活塞无法精准定位,气缸在运行到中间限位点时,活塞在惯性的作用下将继续往前移动,从而无法精准定位中间限位点。如果将该气缸应用在气动插板阀等场合,将导致使用气动插板阀进行计量时,由于气缸的活塞在中间点限位无法精准定位,流量将无法保持稳定,从而造成计量不准确现象的发生。有鉴于此,本发明提供了一种气缸的控制系统,如图2所示,图2为本发明实施例提供的气缸的控制系统结构示意图;包括:供气管路6、一端与气缸1的有杆腔连通、另一端与供气管路6连接的第一输送管路2、以及一端与气缸1的无杆腔连通、另一端与供气管路6连接的第二输送管路3,还包括:采集装置,用于采集有杆腔内的第一压强和无杆腔内的第二压强;第一控制阀71和第二控制阀72,第一控制阀71和第二控制阀72分别用于控制第一输送管路2和第二输送管路3内的压强;控制装置9,用于确定气缸的活塞在运动方向上的惯性压强,还用于根据确定的惯性压强、活塞11背离其运动方向的一端所在的腔室的压强以及预先存储的活塞背离其运动方向的一端的受力面积,得到活塞11背离其移动方向的一端所受的第一压力;根据获得的活塞11朝向其运动方向的一端所在的腔室的压强以及预先存储的活塞11朝向其运动方向的一端的受力面积,得到活塞11朝向其移动方向的一端所受的第二压力;并控制第一控制阀71和/或第二控制阀72的开度以控制有杆腔和/或无杆腔内的压强,使第一压力与第二压力的差值小于或等于预设压力值。需要说明的是,该预设压力值可以根据实际需要而设定,该预设压力值可以是零,即第一压力值和第二压力值相等;该预设压力值也可以是零附近的某 个较小数值,即需要保证第一压力值和第二压力值之间的差值很小,以保证精度。值得注意的是,本发明中,所述第一输送管路2可以是直接与供气管路6连接,也可以是间接与供气管路6连接;第二输送管路3可以是直接与供气管路6连接,也可以是间接与供气管路6连接。本发明提供的气缸的控制系统,在控制气缸1移动时,考虑到气缸1的惯性力对气缸活塞所受的压强的影响,通过采集有杆腔内的第一压强和无杆腔内的第二压强;并根据活塞11的理论停止位置、确定气缸1的活塞11在运动方向上的惯性压强;根据确定的惯性压强、活塞11背离其运动方向的一端所在的腔室的压强以及预先存储的活塞背离其运动方向的一端的受力面积,得到活塞11背离其移动方向的一端所受的第一压力;根据获得的活塞11朝向其运动方向的一端所在的腔室的压强以及预先存储的活塞朝向其运动方向的一端的受力面积,得到活塞11朝向其移动方向的一端所受的第二压力;并控制第一控制阀71和/或第二控制阀72的开度以控制有杆腔和/或无杆腔内的压强,使第一压力与第二压力的差值小于或等于预设压力值。即可以提高控制活塞停止位置的精度。所以,本发明提供的气缸的控制系统,可以气缸的定位精度,提高机械设备的工作安全性。由于整个系统中气压一直维持稳定值,也就是说供气管路内的压强时恒定的为P,则第一输送管路和第二输送管路中的气体压强与第一控制阀和第二控制阀的开度(调节系数影响开度)的关系为:若第一控制阀的调节系数为K1,则P1=p·K1,若第二控制阀的调节系数为K2,则P1=p·K2。也即可以通过调节第一控制阀的调节系数K1和/或第二控制阀的调节系数K2来调节阀的开度,以此来调节系统腔室压力。上述采集装置的具体结构可以有多种,一种具体实施方式中,上述采集装置包括:分别用于采集第一输送管路2和第二输送管路3内的压强的第一压力 传感器81和第二压力传感器82。其中:当气缸的活塞向缸体内移动时(即活塞杆缩回时),活塞11朝向活塞杆12的一端(即有杆腔,也即活塞背离其运动方向的一端所在的腔室)的压力F1=P1S1+P0S1,活塞11背离活塞杆12的一端(即无杆腔,也即活塞朝向其运动方向的一端所在的腔室)的压力F2=P2S2;当气缸1的活塞向缸体外移动时,活塞11朝向活塞杆12的一端(即有杆腔,也即活塞朝向其运动方向的一端所在的腔室)的压力F1=P1S1,活塞11背离活塞杆12的一端(即无杆腔,也即活塞背离其运动方向的一端所在的腔室)的压力F2=P2S2+P0S2;其中:F1为活塞朝向活塞杆的一端所受的压力,S1为活塞朝向活塞杆的一端的面积,P1为第一输送管路内的压强,F2为活塞背离活塞杆的一端所受的压力,S2为活塞背离活塞杆的一端的面积,P2为第二输送管路内的压强,P0为惯性压强,上述P0是由于活塞移动时的惯性产生的,上述P0本领域技术人员可以根据经验设定,可以直接输入控制装置,也可以通过其它方式获得。故一种可选的实施方式中:上述控制系统还包括:输入装置,用于向所述控制装置输入所述惯性压强。另一种可选的实施方式中:上述控制系统还包括:惯性压强数据库;控制装置9用于根据活塞的理论停止位置查询惯性压强数据库,得到惯性压强。上述惯性压强数据库可以根据如下方式得到:S1、在控制气缸运动之前,将惯性压强设置为0;S2、根据活塞的理论停止位置,控制气缸运动和停止;S3、获取活塞的理论停止位置与实际停止位置之间的位移差;S4、为获取的所述位移差设置惯性压强数值,重复步骤S2、S3,直至所述位移差为零时,执行步骤S5;S5、获取并记录所述理论停止位置以及与所述位移差为零时对应设置的惯性压强,得到所述惯性压强数据库。在活塞的运行过程中,活塞的每一理论停止位置对应一个位移差,一个位移差对应一定的惯性压强,可见活塞在运动方向上的惯性压强与活塞的理论停止位置有关,故,控制装置用于根据活塞理论停止位置、确定所述气缸的活塞在运动方向上的惯性压强。一种具体实施方式中,如图2所示,上述控制系统还包括:设置于第一输送管路2上的第一存储箱51和第一换向阀41,第一换向阀41至少包括:第一工作口、第二工作口和第三工作口,第一工作口与气缸1的有杆腔连通,第二工作口与供气管路6连通,第三工作口与第一存储箱51连通,其中:当第一换向阀处于第一工作状态时,第一工作口和第二工作口连通,当第一换向阀处于第二工作状态时,第一工作口和第三工作口连通;也就是说,当第一工作口和第二工作口连通时,气缸的有杆腔处于进气状态,当第一工作口和第三工作口连通时,气缸的有杆腔处于排气状态;设置于第二输送管路3上的第二存储箱52和第二换向阀42,第二换向阀42至少包括:第一工作口、第二工作口和第三工作口,第一工作口与气缸1的无杆腔连通,第二工作口与供气管路6连通,第三工作口与第二存储箱52连通,其中:当第二换向阀处于第一工作状态时,第一工作口和第二工作口连通,当第二换向阀处于第二工作状态时,第一工作口和第三工作口连通;也就是说,当第一工作口和第二工作口连通时,气缸的无杆腔处于进气状态,当第一工作口和第三工作口连通时,气缸的无杆腔处于排气状态;上述气缸1上设有第一接口和第二接口、且第一接口和第二接口分别与气缸1的有杆腔和无杆腔连通,第一控制阀71设置于第一接口和第一换向阀41之间,第二控制阀72设置于第二接口和第二换向阀42之间。上述第一换向阀和第二换向阀可以为机械阀或电磁阀等,这里就不再一一赘述。进一步的,上述第一压力传感器81设置于第一接口和第一控制阀71之间,第二压力传感器82设置于第二接口和第二控制阀72之间。可选的,第一控制阀71为电控阀或机械阀,和/或第二控制阀72为电控阀或机械阀。也就是说第一控制阀71为电控阀,第二控制阀72为电控阀,或者第一控制阀71为机械阀,第二控制阀72为机械阀,或者第一控制阀71为电控阀,第二控制阀72为机械阀,或者第一控制阀71为机械阀,第二控制阀72为电控阀。本发明还提供了一种机械设备,包括气缸,还包括上述任一项所述的气缸的控制系统。由于本发明提供的气缸的控制系统,可以提高气缸活塞的定位精度,故,本发明提供的机械设备具有较高的作业安全性,上述机械设备可以为混凝土泵车等。基于同一发明构思,如图3所示,图3为本发明实施例提供的气缸的控制方法流程图;本发明还提供了一种气缸的控制方法,包括:步骤S301:获得气缸的有杆腔内的第一压强和气缸的无杆腔内的第二压强;步骤S302:确定所述气缸的活塞在运动方向上的惯性压强;步骤S303:根据确定的惯性压强、活塞背离其运动方向的一端所在的腔室的压强以及预先存储的活塞背离其运动方向的一端的受力面积,得到活塞背离其移动方向的一端所受的第一压力;根据获得的活塞朝向其运动方向的一端所在的腔室的压强以及预先存储的活塞朝向其运动方向的一端的受力面积,得到活塞朝向其移动方向的一端所受的第二压力;并控制第一控制阀和/或第二控制阀的开度以控制有杆腔和/或无杆腔内的压强,使第一压力与第二压力的差值小于或等于预设压力值。即:当气缸的活塞向缸体内移动时(即活塞杆缩回时),活塞11朝向活塞杆12 的一端的压力F1=P1S1+P0S1,活塞11背离活塞杆12的一端的压力F2=P2S2;当气缸1的活塞杆向缸体外移动时,活塞11朝向活塞杆12的一端的压力F1=P1S1,活塞11背离活塞杆12的一端的压力F2=P2S2+P0S2;其中:F1为活塞朝向活塞杆的一端所受的压力,S1为活塞朝向活塞杆的一端的面积,P1为第一输送管路内的压强,F2为活塞背离活塞杆的一端所受的压力,S2为活塞背离活塞杆的一端的面积,P2为第二输送管路内的压强,P0为惯性压强,上述P0是由于活塞移动时的惯性产生的,上述P0本领域技术人员可以根据经验设定,可以直接输入控制装置,也可以通过其它方式获得。进一步的,上述步骤S302中:确定所述气缸的活塞在运动方向上的惯性压强;具体包括:根据活塞的理论停止位置查询所述惯性压强数据库,得到所述惯性压强。上述惯性压强数据库按照以下步骤构建:S1、在控制气缸运动之前,将惯性压强设置为0;S2、根据活塞的理论停止位置,控制气缸运动和停止;S3、获取活塞的理论停止位置与实际停止位置之间的位移差;S4、为获取的位移差设置惯性压强数值,重复步骤S2、S3,直至所述位移差为零时,执行步骤S5;S5、获取并记录理论停止位置以及与位移差为零时对应设置的惯性压强,得到惯性压强数据库。在活塞的运行过程中,活塞的每一理论停止位置对应一个位移差,一个位移差对应一定的惯性压强,可见活塞在运动方向上的惯性力与活塞的理论停止位置有关,故,控制装置用于根据活塞理论停止位置、确定所述气缸的活塞在运动方向上的惯性压强。上述得到的惯性压强数据库如表1所示;表1S(位移差)P0(惯性压强)0-aP1a-bP2b-cP3需要说明的是,上述表1省略了位移差对应的活塞理论停止位置。且,为了节省效率,将位移差划分一定的区间,与此对应的是,惯性压强也划分为一定对应区间。进一步的,上述步骤S303中:控制第一控制阀和/或第二控制阀的开度以控制无杆腔和/或有杆腔内的压强,使第一压力与第二压力的差值小于或等于预设压力值,具体包括:当气缸的活塞向缸体内移动时,控制第二控制阀的开度以控制无杆腔内的压强,使第一压力与第二压力的差值小于或等于预设压力值;当气缸的活塞向缸体外移动时,控制第一控制阀的开度以控制有杆腔内的压强,使第一压力与第二压力的差值小于或等于预设压力值。调节一个控制阀的开度,便于控制,且便于提高调节精度。基于同一发明构思,如图4所示,图4为本发明实施例提供的气缸的控制装置结构示意图,本发明还提供了一种气缸的控制装置,包括:第一获得模块1011,用于获得的气缸的有杆腔内的第一压强和气缸的无杆腔内的第二压强;第二获得模块1012,用于获得所述活塞在运动方向上的惯性压强;处理模块102,用于根据确定的所述惯性压强、所述活塞背离其运动方向的一端所在的腔室的压强以及预先存储的活塞背离其运动方向的一端的受力面积,得到所述活塞背离其移动方向的一端所受的第一压力;根据获得的所述活塞朝向其运动方向的一端所在的腔室的压强以及预先存储的活塞朝向其运动方向的一端的受力面积,得到所述活塞朝向其移动方向的一端所受的第二压 力;并控制所述第一控制阀和/或第二控制阀的开度以控制有杆腔和/或无杆腔内的压强,使第一压力与第二压力的差值小于或等于预设压力值。由于整个系统中气压一直维持稳定值,也就是说供气管路内的压强时恒定的为P,则第一输送管路和第二输送管路中的气体压强与第一控制阀和第二控制阀的开度(调节系数影响开度)的关系为:若第一控制阀的调节系数为K1,则P1=p·K1,若第二控制阀的调节系数为K2,则P1=p·K2。也即可以通过调节第一控制阀的调节系数K1和/或第二控制阀的调节系数K2来调节阀的开度,以此来调节系统腔室压力。进一步的,第二获得模块1012具体用于:根据活塞的理论停止位置查询所述惯性压强数据库,得到所述惯性压强。上述惯性压强数据库可以根据如下方式得到:S1、在控制气缸运动之前,将惯性压强设置为0;S2、根据活塞的理论停止位置,控制气缸运动和停止;S3、获取活塞的理论停止位置与实际停止位置之间的位移差;S4、为获取的所述位移差设置惯性压强数值,重复步骤S2、S3,直至所述位移差为零时,执行步骤S5;S5、获取并记录所述理论停止位置以及与所述位移差为零时对应设置的惯性压强,得到所述惯性压强数据库。在活塞的运行过程中,活塞的每一理论停止位置对应一个位移差,一个位移差对应一定的惯性压强,可见活塞在运动方向上的惯性力与活塞的理论停止位置有关,故,控制装置用于根据活塞理论停止位置、确定所述气缸的活塞在运动方向上的惯性压强。更进一步的,处理模块102具体用于:当气缸的活塞向缸体内移动时,控制第二控制阀的开度以控制无杆腔内的压强,使第一压力与第二压力的差值小于或等于预设压力值;当气缸的活塞向缸体外移动时,控制第一控制阀的开度以控制有杆腔内的 压强,使第一压力与第二压力的差值小于或等于预设压力值。显然,本领域的技术人员可以对本发明进行各种改动和变型而不脱离本发明的精神和范围。这样,倘若本发明的这些修改和变型属于本发明权利要求及其等同技术的范围之内,则本发明也意图包含这些改动和变型在内。当前第1页1 2 3