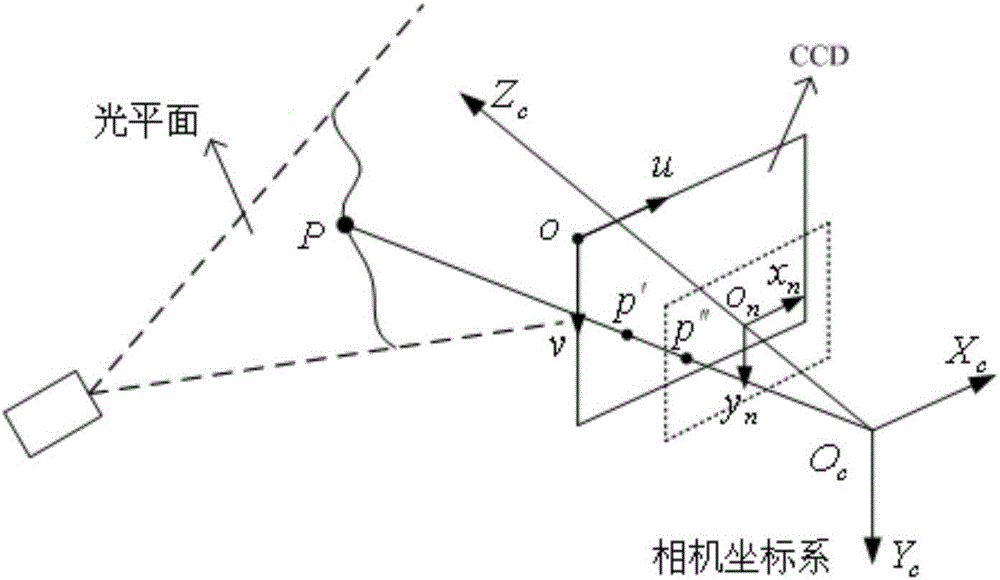
本实用新型属于自动检测及控制
技术领域:
,用于实现导管扩口锥度及型面的非接触自动检测,具体为一种导管锥度及型面的自动检测设备,采用激光视觉测量技术完成导管扩口锥面全型面非接触扫描,通过点云噪声分类滤波、二次空间锥体拟合、高斯映射圆锥轴线定位等,最终实现锥度及型面精确测量和误差分析。
背景技术:
:扩口导管的接头端是锥面,导管一端被扩口形成与管接头锥面角度一致的内锥面,而外锥面与平管嘴内锥面角度一致,通常被应用于油、水、气等非腐蚀性或腐蚀性介质管接头,与管道焊接后,具有连接牢靠、密封性能好等特点。扩口的角度误差就是造成管道渗漏问题的主要因素。如果扩口锥度不准,或者型面不均匀,而检测又未能及时发现问题,则会威胁到扩口导管传输介质的安全性和传输可靠性。目前,因为导管扩口形状特殊,其锥度及型面的检测只能采用三坐标机接触式检测方法,效率低、速度慢、费工费时,而且不能实时采集和显示、不能进行自动化控制。激光视觉测量技术是一种快速、高精度、多信息的全貌测量技术,通过配套设计相应的机械夹持机构带动测量系统平移或旋转,使测量系统能够完成全貌扫描以获取对象的3D表面数据,结合图像识别、数据处理与分析、优化理论等多学科知识领域,实现被测对象关键设计参数的精确测量、3D数据的数字化管理等。在此基础上可以进行灵活的改进和创新设计,这种设计创新思想完全符合企业产品快速高效地更新换代的需要,同时符合复杂零部件数字化设计、制造、检测一体化流程的需要。将激光视觉应用于扩口导管扩口角度的测量,对关键技术进行改进和创新,提供一种实现导管扩口锥度及型面的快速精确自动检测设备,提高检测精度和效率,目前国内市场还没有相应的设备报导和出售。基于激光视觉测量完成导管扩口锥度及扩口全型面的精确测量,为扩口测量和检测提供智能化成套装备和数字化解决方案,对于保证管道传输的可靠性,降低相关器件的故障率具有非常重要的意义。技术实现要素:本实用新型所要解决的技术问题在于提供一种导管扩口锥度及型面的自动检测设备,能实时检测扩口锥度,进而获得过扩口圆锥轴的截面与圆锥相交的两条母线之间的夹角;还可以间隔1°旋转过轴心线的截面360次,得到360对母线之间的夹角,获得360个锥度和锥角,拟合测量结果得到最终的测量锥度、锥角;通过将海量数据测量结果与最优计算结果作对比,求解出锥面各点锥度计算的最大误差、最小误差、平均误差、以及均方根误差作为锥度和型面检测的评价指标,完成全型面检测;在界面上以彩图显示测量分析结果,一目了然。本实用新型是通过下述技术方案实现的:导管扩口锥度及型面自动非接触检测设备,主要包括气动夹持机构、激光视觉检测装置及配套开发的锥度及型面检测软件系统。上述气动夹持机构、激光视觉检测装置两个部分均固定在支撑平台的上面。进一步地,所述气动夹持机构用作夹持待测扩口导管,该气动夹持机构,包括气动缸支座与自动激光校正装置。上述气动缸支座上装有气动缸,气动缸的内侧装有V型块A及软质内套;上述自动激光校正装置的内侧装有V型块B及软质内套;上述自动激光校正装置,包含一组平行的透光槽,当激光均匀穿过透光槽时,光平面与扩口圆截面垂直,认为激光器位置合适,可自动校准激光位置,确保待测扩口被全型面扫描。进一步地,所述激光视觉检测装置,包括非接触激光视觉检测单元,直线模组及其驱动装置。该部分用于待测扩口的非接触测量,可全型面扫描。上述直线模组及其驱动装置,包括高精度伺服电机、驱动器及运动控制卡组成的驱动装置,直线模组及光学微调转台。上述非接触激光视觉检测单元,包括相对位置固定的工业数字照像机和激光器。导管扩口锥度及型面自动非接触检测方法,该方法是通过与上述硬件相结合的锥度与型面检测软件来实现的:包括用户指标设定,用户根据实际要求设定检测指标、检测单元运动参数等;数据实时采集和处理,用于控制测量的开始和结束,对采集数据进行实时点云滤波、三维数据重构、锥体拟合和显示、测量过程自动诊断等;数据后处理和分析,用于锥度计算和型面各点误差分析,测量结果彩图显示等;测量结果管理,用于数据存储、查询、报表和打印等。应用于导管扩口锥度及型面自动非接触检测设备软件的设计,包括:1、非接触激光视觉检测数学模型;2、导管扩口锥度算法设计,该设计包括:基于点云噪声分类滤波的锥体建模,基于高斯圆的锥体轴线定位及锥度计算;3、导管扩口锥度及型面非接触自动检测效果验证等。本实用新型与现有技术相比具有以下特点:①实现导管扩口的自动检测,减少测量过程中的人为不确定因素,且测量速度快,大大提高工作效率;②测量方式为非接触测量方式,导管夹持采用橡胶内套,安全性能好,避免对被测导管的损伤;③所设计的导管扩口锥度和型面检测装置扩口内锥角测量精度优于0.5°;④测试界面友好,具备误差超限报警等功能,可自动进行测量诊断;⑤在检测锥角的同时,完成锥面的扩口全型面检测,可定量给出全型面误差结果并转换成不同颜色直观呈现,一目了然。⑥测试数据实时存储功能,针对测试的不同导管,实时记录测量数据备查。附图说明图1是本实用新型的结构示意图。图2是本实用新型激光视觉检测装置的数学模型。图3是扩口导管三维数字测量原理图。图4是锥度及型面测量原理图。图5是圆锥法线高斯映射示意图。图6是扩口导管结构示意图。图7是扩口扫描成功示意图。图8是图7左上角测量结果的局部放大图。图9是全型面检测彩色显示图。具体实施方式下面将结合附图,对本实用新型实施例中的技术方案进行清晰、完整地描述,显然,所描述的实施例仅仅是本实用新型一部分实施例,而不是全部的实施例。基于本实用新型中的实施例,本领域普通技术人员在没有做出创造性劳动前提下所获得的所有其他实施例,都属于本实用新型保护的范围。实施例一参照图1,导管扩口锥度及型面自动非接触检测设备,主要包括气动夹持机构和激光视觉检测两个部分,上述两个部分均固定在支撑平台1的上面。进一步地,所述气动夹持机构用作夹持待测扩口导管,该气动夹持机构,包括气动缸支座13与自动激光校正装置2。上述气动缸支座13上装有气动缸12,气动缸12的内侧装有V型块A11及软质内套10;上述自动激光校正装置2的内侧装有V型块B14及软质内套;上述V型块A11与V型块B14用于待测扩口导管的定位、夹紧固定与安装,其上设有与V型块A11与V型块B14相匹配的塑料软质内套,使扩口被夹紧的同时不被损坏,确保扩口安全,还可定准扩口夹持位置;上述自动激光校正装置2,包含一组平行的0.2mm透光槽,当激光均匀穿过透光槽时,光平面与扩口圆截面垂直,认为激光器位置合适,可自动校准激光位置,确保待测扩口被全型面扫描。进一步地,所述激光视觉检测装置,包括非接触激光视觉检测单元,直线模组及其驱动装置,用于待测扩口的非接触测量,可全型面扫描。上述直线模组及其驱动装置,包括高精度伺服电机8、驱动器9及运动控制卡组成的驱动装置,对直线模组进行拖动及控制;直线模组3及光学微调转台4。直线模组3用于激光视觉检测单元的直线运动,保证待测扩口处于激光视觉检测单元的视角范围内。光学微调转台4用于非接触激光视觉检测单元的固定和视角微调。上述非接触激光视觉检测单元,包括相对位置固定的1个工业数字照像机7和1个激光器。其中工业相机采用螺栓连接光学微调转台4;而圆柱形激光器固定困难,为此设计一体性激光器夹持机构6,并采用弹性夹持方式固定激光器5,确保测量过程中光平面模型的一致性,激光器夹持机构6固定在光学微调转台4的上面。与上述硬件相结合的锥度及型面检测软件,包括:用户指标设定,用户根据实际要求设定检测指标、检测单元运动参数等;数据实时采集和处理,用于控制测量的开始和结束,对采集数据进行实时点云滤波、三维数据重构、锥体拟合和显示、测量过程自动诊断等;数据后处理和分析,用于锥度计算和型面各点误差分析,测量结果彩图显示等;测量结果管理,用于数据存储、查询、报表和打印等。应用于导管扩口锥度及型面自动非接触检测设备软件的设计:1、非接触激光视觉检测数学模型(参照图2)。导管扩口视觉测试平台的数学模型,其中,Oc、Xc、Yc、Zc为摄像机坐标系,o-uv为CCD计算机像平面坐标系,On-XnYn为归一化平面坐标系。设点P为激光与被测物体表面相交曲线上的一点,p'和pn'分别为其在CCD像平面和归一化平面上的成像点。点P在世界坐标系下的齐次坐标为摄像机坐标系下的齐次坐标为像点p'和pn'的齐次坐标分别为和根据透视投影变换有下式:P~c=[Rt]·P~w---(1)]]>zc·p~n′=[E0]·P~c---(2)]]>p~′=K·p~n′---(3)]]>其中,R和t分别为世界坐标系到摄像机坐标系的旋转矩阵和平移向量,E为3×3的单位矩阵,K为摄像机内参数矩阵,形式如下:K=fuγu00fvv0001]]>式中,fu和fv分别为CCD像平面上u和v的尺度因子,是u和v不垂直因子,u0和v0是像平面的中心点坐标。通常相机镜头存在光学畸变,使用针孔模型不能准确地描述基于激光技术的大直径扩口导管视觉测试平台的数学模型,因此需要考虑畸变模型。一般采用一阶径向畸变即可满足系统测量精度的要求。一阶径向畸变模型如下:u~=u+Δu·k1·r2v~=v+Δv·k1·r2---(4)]]>其中,为畸变校正后的像点坐标,(u,v)为存在畸变的像点坐标,k1为一阶径向畸变系数,(u0,v0)为光学中心(畸变中心)坐标,Δu=u–u0,Δv=v–v0和设线结构光在摄像机坐标系下的方程为:a·p~c=0---(5)]]>其中,a为平面方程系数向量。图3为基于上述检测装置的导管扩口测量原理图,测量前将扩口导管加持在V型块上即可。测量过程中伺服机构带动非接触视觉检测单元运动,当扩口进入测量视野内时,激光发射器投射出的光源会在扩口内壁表面产生反射,反射的光线被相机接收。通过图像处理技术可以获取P点的计算机图像坐标通过标定可知相机内参数矩阵K和激光系统方程系数,则联立式(2)~(5),可以确定P点在相机坐标系下的三维坐标,为下一步锥体建模和锥度计算提供点云数据。标定后的K和激光系统方程系数将提供给测试平台使用者,在试验平台需要重新调试时使用。2、导管扩口锥度算法设计(参照图4)。导管扩口为锥体结构,n为锥面单位法线,可以看出n与锥面轴线的夹角θ与扩口顶角φ互为余角,即φ=90°-θ(6)锥度为上、下两底圆的直径差与锥台高度之比值。C=2(R2-R1)H=2tanφ---(7)]]>因此,设计算法首先确定锥面法线和轴线,通过计算法线角度最终得到锥面锥度和锥角。2.1基于点云噪声分类滤波的锥体建模基于非接触视觉检测技术的扩口测量过程中,不可避免的会受到环境光、被测物表面强反射光等因素的干扰,造成测量数据出现噪声点,严重影响到点云分割、特征提取、曲面重建、误差分析等一系列的后续处理过程。因此,必须首先对点云噪声进行滤除。因为扩口锥面为连续曲面,投射到其上的激光曲线也应为连续的亮线,通常噪声的作用会产生两种效果:①使激光边缘产生毛刺;②在主体点云外产生小的局部亮点。两种情况都会导致激光条纹像素识别错误。基于错误识别的像素建立扩口椎体模型必然存在较大的误差,因此必需对扫描的激光图像进行点云噪声滤波。考虑不同干扰的作用效果不同,同一种滤波方法很难同时滤除两种干扰。为此,改进邻域聚类法对激光像素点进行分类,进而实现滤波。令Si为第i个点云集合,在未被标记的点云中任选一点为p,令p∈Si,设置邻域半径r,找到离p点最近的k个点为N‾k(p)={qi|Σi=1k|qi-p|<r<Σi=1k|oi-p|,qi≠p,∀oi∈S,oi≠p}---(8)]]>对其中未被标记的点,即j≠i,令qi∈Si。所有点都被标记后,得到n个点云子集S1,S2,…,Sn。如果一个子集中点数过少,则该子集为孤立的局部亮点;如果一个子集的体积过小,则该子集为汇聚在一起的局部亮点。这些子集是前述第②种噪声引起,都可以作为噪声从点云中去除。针对第①种噪声,在式(8)的基础上,将p点也看成本身邻域中的点,得到点p的第二种邻域集合为NSk(p)={N‾k(p)∪p}---(9)]]>为反映邻域内点的变化特征,可计算协方差矩阵为Ccorr=q1-p‾...qk-p‾Tq1-p‾...qk-p‾---(10)]]>p‾=Σi=1kqik---(11)]]>其中k为邻域点数,则可得到邻域的曲面变化度为δ(p)=λ0λ0+λ1+λ2---(12)]]>λ0,λ1和λ2为矩阵Ccorr的特征值,表示邻域内点在三个方向的变化程度,且有λ0<λ1<λ2。对包含和不包含点p的两个邻域分别计算曲面变化度,二者的差别即可体现点p的特性。令曲面变化度比值为DNF/N‾(p)=δNF(p)δN‾(p)---(13)]]>δNF(p)为包含p点邻域的曲面变化度,为不含p点邻域的曲面变化度。显然若p点非噪声点,两个曲面变化度近似相等,应接近于1;若p点为毛刺噪声点,则两个曲面变化度差别较大,离1较远。所以设定合适的阈值,就可通过判断的值来去除第①种噪声。将扩口锥体看成一种二次空间曲面,其模型方程可一般化为z=c20x2+c11xy+c02y2+c10x+c01y+c00(14)(x,y,z)为扩口锥体S上某点p的三维坐标,上式写成矩阵形式z=[x2xyy2xy1]c20c11c02c10c01c00---(15)]]>根据滤波后的点云三维坐标,采用最小二乘法可拟合出系数向量[c20c11c02c10c01c00],使得J=Σ(x,y,z)∈S(z-Σi=02Σj=02-icijxiyj)2---(16)]]>取最小。此时对应的式(14)即为建立的锥体模型。2.2基于高斯圆的锥体轴线定位及锥度计算椎体模型一旦建立就可计算锥面上任意一点(x0,y0,z0)的法向方程为x-x02c20x+c11y+c10|(x0,y0,z0)=y-y0c11x+2c02y+c01|(x0,y0,z0)=z-z0-1---(17)]]>法向量为n→F=[2c20x0+c11y0+c102c02y0+c11x0+c01-1]---(18)]]>归一化后可得单位法向量n→=n→F|n→F|---(19)]]>如图5所示,将锥体各点单位法向量的起点平移到坐标原点O,因为的终点必在以原点O为球心的单位球面上,如图中点P,称为锥体的高斯映射。理想锥体所有法线映射的轨迹为一个垂直于圆锥轴线OO'的圆,称为高斯圆。高斯圆上任意一点P的坐标(x,y,z)对应映射到该点的单位法向量。显然圆的大小由圆锥顶角φ决定。φ为0°时,映射圆的直径即为1,是过原点的大圆;φ为90°时,圆的直径为0,表现为球面上的1个点。因此,高斯圆可以反映圆锥顶角或者锥度的值。设高斯圆截面方程为c1x+c2y+c3z+c4=0(20)同理通过最小二乘拟合可得系数向量[c1c2c3c4]。其中a=[c1c2c3]为高斯圆法向量,即锥体轴线方程,c4原点到高斯圆截面的距离。可以看出sinφ=c4,则锥度为C=2tanφ=2c41-c42---(21)]]>3、导管扩口锥度及型面非接触自动检测效果验证为了验证测量系统的测量速度和计算精度等指标,采用三坐标机接触式测量的结果作为参考值,与测试平台的结果比较。试验前,首先使用三坐标机(精度为微米级)对样管(参照图6)进行标准测量,测量结果为φ=72.047°,将该测量结果作为标准值。用户设定指标为72°-74°,采用所设计的检测装置对该导管测量结果如图7和图8所示。图7为点云滤波后得到的扩口椎体三维模型;图8为计算的圆锥顶角及其误差分析,对应图7中结果输出模块的放大图。测量结果为φ.=72.05°,与三坐标机测量结果极为接近,但整个流程耗时约10s,极大地提高了工作效率。将锥体各点实测数据与拟合的锥体模型比较,进行误差分析,可以检测型面平整度,图8给出最大误差、最小误差对应偏离锥体正负距离最远的点,为锥面局部特征。为给出锥体所有点的误差情况,可做以下变换Cindex=e-eminemax-emin·255---(22)]]>将误差转换成[0255]中的数,根据索引图像即可将误差转换为对应的彩色,如图9所示。根据颜色即可很直观的看到锥体上每一点的误差情况,完成型面检测。由测量结果可以判定所测扩口导管在72°-74°之间,型面误差符合要求,可以使用,测量界面显示“OK”。本实用新型的创新点在于:(1)该设备实现了导管扩口锥度及型面的非接触自动检测,改变了锥体扩口导管只能采用三坐标机接触式测量的方式。测量精度与三坐标机相近,但测量速度远远快于三坐标机测量方式,从而大大提高了工作效率;(2)硬件方面设计开发了激光自动校正装置,保证光平面与扩口锥体截面垂直,提高模型精度;(3)同时设计自定形V型块软质内套,保护扩口导管不受损坏;(4)通过V型块软质内套筒宽度调节,对待测扩口进行定位,保证测量精度。(5)软件方面首次实现了扩口锥体全型面检测,并以彩图的方式给出结果,简单直观;还可实时存储扩口数据,方便以后的复查。(6)提出一种通过确定锥体法、轴线方向,进而计算锥体顶角和锥度的方法。(7)为减小噪声的干扰作用,提出基于点云数据进行分类方法。根据点p在两类邻域点中的表现特性,判定p点是否为干扰点进行滤除;(8)在锥体建模过程中,引入高斯圆概念,确定单位法向量和锥体轴向量,最终计算锥度值。以上所述仅为本实用新型的较佳实施例而已,并不用以限制本实用新型,凡在本实用新型的精神和原则之内所作的任何修改,等同替换和改进等,均应包含在本实用新型的保护范围之内。当前第1页1 2 3