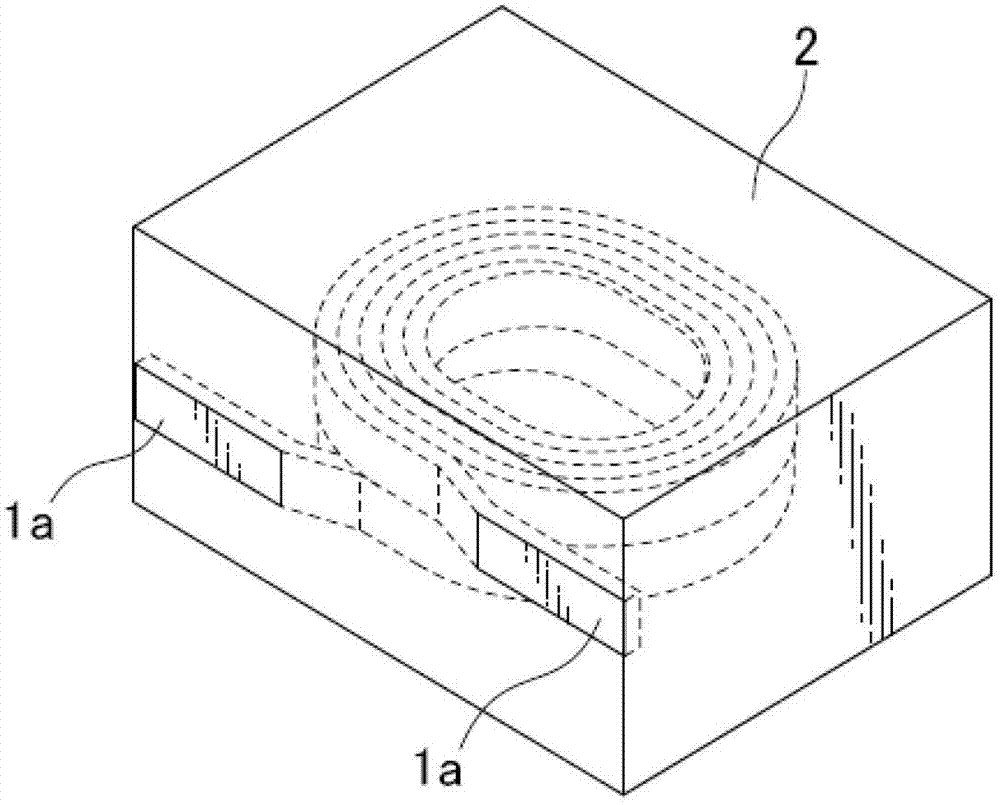
本发明涉及表面安装电感器的制造方法,特别涉及表面安装电感器的连接可靠性高的外部电极形成方法。
背景技术:一直以来,在芯片状的本体上使用导电性糊剂形成外部电极的表面安装电感器被利用。对于这种表面安装电感器,在将绕线密封而得到的树脂成形芯片的表面涂布导电性糊剂,然后使其固化形成基底电极,进而进行镀敷处理形成外部电极。现有技术文献专利文献专利文献1:日本特开2005-116708专利文献2:日本特开平10-284343
技术实现要素:发明要解决的问题在这种以往的表面安装电感器中,作为导电性糊剂使用将环氧树脂等热固性树脂和Ag等金属颗粒分散而得到的物质。这样的导电性糊剂,利用由热固性树脂的固化带来的收缩应力,使分散于树脂中的金属颗粒彼此接触或者使金属颗粒与导线接触,从而进行导通。通常热固性树脂的固化温度远远低于金属颗粒的烧结温度,因此该导通发生在与金属颗粒的接触中。因此,如果与金属颗粒的接触被解除,则导通状态会改变。此外,导电性糊剂中的树脂在高湿环境下存在劣化的倾向。在使用通常的导电性糊剂制作以往的表面安装电感器的情况下,在进行耐湿试验时直流电阻有可能改变。认为其原因之一是,导电性糊剂中的树脂在高湿环境下劣化,金属颗粒间或金属颗粒与内部的导体的接触被解除。另外,作为其它电极形成方法,已知有使导电性糊剂中的金属粉末烧结而形成基底电极的方法。这样的导电性糊剂,使用将Ag等金属粉末、玻璃粉等无机粘合材料和有机赋形剂混炼而得到的糊剂。将该导电性糊剂涂布于芯片状的本体后,施加600~1000℃的热使其烧结,形成基底电极。如果使用该方法的话,由于金属粉末彼此进行烧结,可得到比前述那样的仅金属颗粒的接触的导通更稳定的导通。然而,该方法由于需要使导电性糊剂中的玻璃粉等无机粘合材料熔融,必须在600℃以上的高温下进行热处理。因此,在制作用主要由磁性粉末和树脂组成的密封材料将由导线卷绕而成的绕线密封在密封材料内部这样的表面安装电感器的情况下,如果在比250℃更高温下进行热处理,则导致密封材料中的树脂或导线的自我融着性的皮膜等劣化,所以不可采用该方法。因此本发明的目的在于,提供具有在高湿环境下连接可靠性也高的外部电极的表面安装电感器的制造方法。用于解决问题的方案为了解决上述课题,本发明的表面安装电感器的制造方法中,将具有自我融着性的皮膜的导线卷绕而形成线圈;使用主要由金属磁性粉末和树脂组成的密封材料内包该线圈,并且按照该线圈的两端部的至少一部分在芯部表面露出的方式形成芯部;将含有烧结温度为250℃以下的金属细颗粒的导电性糊剂涂布于该芯部的表面;对该芯部进行热处理,使该金属细颗粒烧结而在该芯部的表面形成基底电极并使其与该线圈导通。发明的效果根据本发明,能够容易地制造具有连接可靠性高的外部电极的表面安装电感器。附图说明图1为本发明的第一实施例中使用的空心线圈的立体图。图2为本发明的第一实施例的芯部的立体图。图3为本发明的第一实施例的涂布了导电性糊剂的状态的芯部的立体图。图4为通过本发明的第一实施例的方法制作的表面安装电感器的立体图。图5为本发明的第二实施例的芯部的立体图。图6为本发明的第二实施例的涂布了导电性糊剂的状态的芯部的立体图。图7为通过本发明的第二实施例的方法制作的表面安装电感器的立体图。附图标记说明1、11:线圈(1a、11a:端部)2、12:芯部3、13:导电性糊剂4、14:外部电极具体实施方式以下,参照附图对本发明的表面安装电感器的制造方法进行说明。第一实施例参照图1~图4,对本发明的第一实施例的表面安装电感器的制造方法进行说明。将本发明的第一实施例中使用的空心线圈的立体图示于图1中。将本发明的第一实施例的表面安装电感器的芯部的立体图示于图2中。将第一实施例的涂布了导电性糊剂的状态的芯部的立体图示于图3中。将通过本发明的第一实施例的方法制作的表面安装电感器的立体图示于图4中。首先,使用具有自我融着性的皮膜的截面为平角形状的导线,制作线圈。如图1所示,按照将导线的两端部1a位于最外周的方式将导线卷绕为两层向外侧的螺旋状(two-tieredoutwardspiralpattern),制作线圈1。本实施例中使用的导线,使用了具有酰亚胺改性聚氨酯层作为自我融着性的皮膜的导线。自我融着性的皮膜可以为聚酰胺系、聚酯系等,优选耐热温度高者。另外,本实施例中使用截面为平角形状的导线,也可使用圆线、截面为多角形状的导线。接着,作为密封材料,使用将铁系金属磁性粉末和环氧树脂混合而造粒成粉末状的材料,通过压缩成形法,成形内包如图2所示的线圈的芯部2。此时,线圈的端部1a在芯部2的表面露出。本实施例中通过压缩成形法制作芯部,但也可通过粉末压制成形法等成形方法制作芯部。然后,通过机械剥离去除所露出的两端部1a的表面的皮膜,之后,如图3所示,通过浸涂法将导电性糊剂3涂布于芯部2的表面。本实施例中作为导电性糊剂,使用将粒径为10nm以下的Ag细颗粒和有机溶剂等混合而糊剂化的物质。金属的粒径小于100nm时,因尺寸效应而烧结温度、熔点等下降。特别在尺寸为10nm以下时,烧结温度、熔点显著下降。本实施例中使用Ag细颗粒,但也可使用Au或Cu。并且,本实施例中,作为导电性糊剂的涂布方法使用了浸涂法,但也可使用印刷法、浇灌法等方法。将涂布了导电性糊剂3的芯部2在200℃下进行热处理,使芯部2固化,并且使导电性糊剂3中的Ag细颗粒烧结。Ag细颗粒由于为10nm以下的粒径,即使在该程度的温度下也能够容易地烧结。通过使金属细颗粒烧结,形成比仅接触时更牢固的金属间的结合,因此可得到连接可靠性高的线圈与导电性糊剂的导通。即使在混合了比100nm更大的粒径的金属粉末的情况下,金属细颗粒也烧结或成为熔融状态,可通过金属细颗粒得到比仅接触时更牢固的金属间的结合。并且,由于在250℃以下的热处理即可,因此对芯部、导线的皮膜的损伤少。最后,进行镀敷处理,在导电性糊剂的表面形成外部电极4,得到如图4所示的表面安装电感器。需要说明的是,通过镀敷处理形成的电极可以从Ni、Sn、Cu、Au、Pd等中选择任一种或适当选择多种来形成。第二实施例参照图5~图7,对本发明的第二实施例的表面安装电感器的制造方法进行说明。将本发明的第二实施例的表面安装电感器的芯部的立体图示于图5中。将第二实施例的涂布了导电性糊剂的状态的芯部的立体图示于图6中。将通过本发明的第二实施例的方法制作的表面安装电感器的立体图示于图7中。第二实施例中,使用不同于第一实施例的导电性糊剂,制作具有L字状电极的表面安装电感器。需要说明的是,与第1实施例重复的部分的说明不再累述。首先,将第一实施例中使用的导线按照两端部11a位于最外周的方式卷绕为两层向外侧的螺旋状,制作线圈11。本实施例中,线圈11的端部11a按照夹着线圈11的卷绕部相对的方式引出。接着,使用与第一实施例中使用的密封材料相同组成的密封材料,通过压缩成形法,成形如图5所示的内包线圈11的芯部12。此时,线圈的端部11a在芯部2的相对的侧面上露出。接着,通过机械剥离去除所露出的两端部11a的表面的皮膜,之后,如图6所示,通过印刷法将导电性糊剂13以L字状涂布于芯部12的表面。本实施例中作为导电性糊剂,使用将粒径为10nm以下的Ag细颗粒、粒径为0.1~10μm的Ag颗粒和环氧树脂混合而糊剂化的物质。调制导电性糊剂,使得导电性糊剂中所含的粒径为0.1~10μm的Ag颗粒的比例相对于粒径为10nm以下的Ag细颗粒和粒径为0.1~10μm的Ag颗粒的总计为30wt%。通过含有30~50wt%的粒径为0.1~10μm的金属颗粒,与仅含有粒径小于100nm的金属细颗粒时相比,起到热固化时的热收缩减小的效果。进而,由于金属细颗粒的量少,也可期待材料成本的减小。并且,第二实施例中使用了含有树脂成分的导电性糊剂,其也起到提高粘着强度的效果。在如第一实施例那样覆盖芯部的两端面那样遍及5个面形成电极的情况下,即使使用不含有树脂成分类型的导电性糊剂也因锚固效果而确保一定程度的粘着强度。然而,在L字状电极、底面电极结构等电极面积少的形状的情况下,如果使用不含有树脂成分类型的导电性糊剂,则粘着强度低,存在剥离的可能性。因此,在形成如L字状电极那种电极面积少、易剥离的形状的电极的情况下,优选使用含有树脂成分类型的导电性糊剂。最后,进行镀敷处理,在导电性糊剂的表面形成外部电极14,得到如图7所示的表面安装电感器。上述实施例中,作为密封材料,使用了将以铁系金属磁性粉末作为磁性粉末、以环氧树脂作为树脂混合而得到的材料。然而并不限于此,例如,作为磁性粉末,也可使用铁氧体系磁性粉末等、进行了绝缘皮膜形成或表面氧化等表面改性的磁性粉末。另外,也可加入玻璃粉末等无机物。并且,作为树脂,也可使用聚酰亚胺树脂、酚醛树脂等的热固性树脂、聚乙烯树脂、聚酰胺树脂等的热塑性树脂。上述实施例中,作为线圈使用了卷绕为两层向外侧的螺旋状的线圈,但并不限于此,例如,也可卷绕为扁绕绕组(edgewisewinding)、对齐绕组(alignedwinding)的线圈,也可不仅卷绕为椭圆形而是圆形、矩形、梯形、半圆状、它们的组合的形状的线圈。上述实施例中,作为剥离线圈的端部表面的皮膜的方法,使用了机械剥离,但并不限于此,也可使用其它剥离方法。另外在形成芯部之前也可预先剥离端部的皮膜。