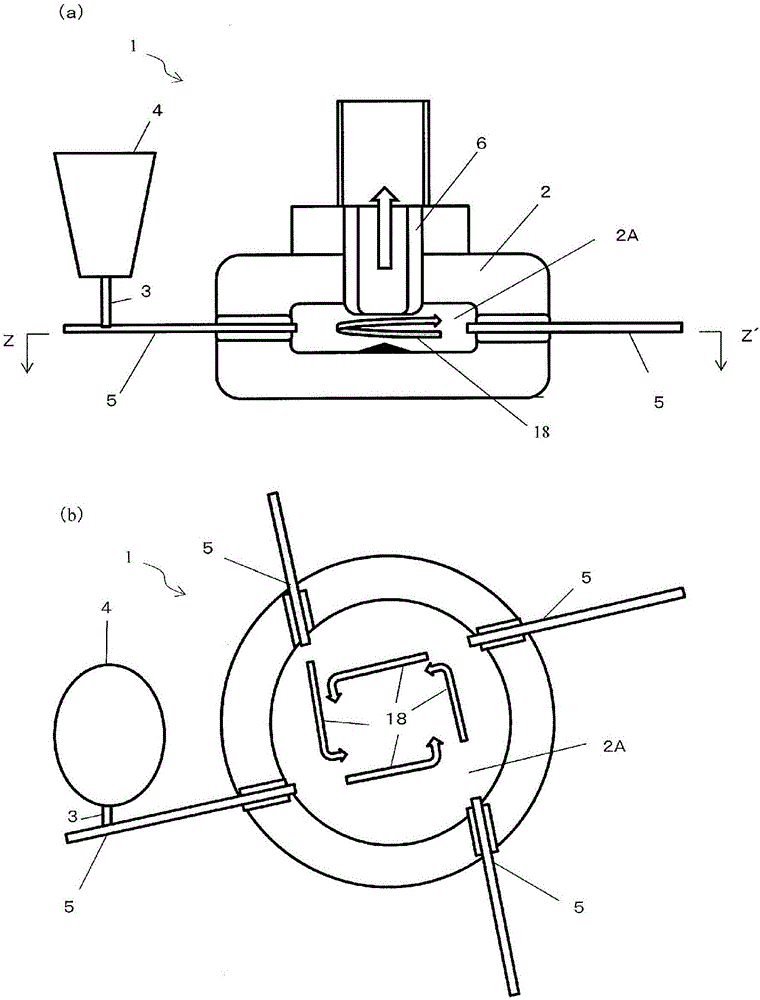
本发明涉及R-T-B系合金粉末及其制造方法、以及R-T-B系烧结磁铁及其制造方法。
背景技术:
:R-T-B系烧结磁铁(R是包含Y的稀土元素;T是以Fe为主要成分的过渡元素,具体而言是Fe或者Fe和Co;B是硼)在各种磁铁中显示最高的磁能积,价格也比较便宜,因此在各种电子设备中被广泛利用。R-T-B系烧结磁铁例如可以通过如下所述的工序制作。首先,利用铸锭法和薄带连铸法等方法,对各种原料金属进行铸造,由此来制造原料合金。接着,将所得到的原料合金提供给粉碎工序,获得规定的粒径的合金粉末。在该粉碎工序中,通常包括粗粉碎工序和微粉碎工序,前者例如利用氢脆化现象进行,后者例如使用气流式粉碎机(喷射磨)进行。接着,将上述粉末在磁场中成型为所期望的形状,提供给磁场中成型工序。通过对由此得到的成型体进行烧结,制作R-T-B系烧结磁铁。另外,烧结之后,通常进行热处理。在磁场中成型工序中,通过对上述粉末一边在规定的方向施加磁场一边成型,使各粉末颗粒的易磁化方向与施加磁场的方向一致。通过提高最终得到的R-T-B系烧结磁铁的主相晶粒的易磁化轴方向的定向度(取向度),能够获得具有高的剩余磁通密度Br的R-T-B系烧结磁铁。专利文献1公开了除了使用从粉碎气体喷嘴导入的主要的粉碎气体以外、还使用从另外配置的喷嘴导入涡流生成气体的反喷研磨机,从而能够获得具有钝角的棱线的微粉末。该微粉末的滑动性优异,可以一边在成型时施加磁场一边提高加压时的微粉末的取向度。另外,专利文献2公开了在磁场中成型之前对微粉碎的稀土合金粉末进行加热处理。加热处理后的稀土合金粉末通过球状化成为带有弧面的形状。由此,可以降低磁场中取向时的摩擦力和空间阻碍,改善取向度。现有技术文献专利文献专利文献1:日本特开2003-138335号公报专利文献2:日本特开2007-266038号公报技术实现要素:发明所要解决的课题在专利文献1所记载的技术中,虽然得到的粉末是钝角,但残存有角,取向度的提高不充分。另外,在专利文献2所记载的技术中,包括对微粉碎的粉末进行加热处理的工序,因此存在制造工序繁杂这样的问题。另外,在专利文献2所记载的技术中,通过加热处理使稀土合金粉末的颗粒彼此熔接的可能性变高,也存在不能提高取向度这样的问题。本发明是鉴于上述课题而完成的发明,其目的在于提供适用于制作磁特性更高的R-T-B系烧结磁铁的R-T-B系合金粉末及其制造方法、以及使用了上述R-T-B系合金粉末的R-T-B系烧结磁铁及其制造方法。用于解决课题的方法本发明的实施方式的R-T-B系合金粉末包含27.5质量%以上36.0质量%以下的R(R是稀土元素中的至少一种,且必须包含Nd和Pr中的至少一种)、0.85质量%以上1.05质量%以下的B(硼)、0.1质量%以上2.5质量%以下的元素M(M是选自Al、Ti、V、Cr、Mn、Ni、Cu、Zn、Ga、Zr、Nb、Mo、Ag、In、Sn、Hf、Ta、W、Pb和Bi中的至少一种)、剩余部分T(T是以Fe为主要成分的过渡元素,具体而言是Fe或者Fe和Co),在对颗粒进行二维投影得到的轮廓形状中,将长径a、短径b之比设为a/b、将周长L、当量圆直径d(具有相同面积的圆的直径)之比设为L/d时,以个数比率计,包含20%以上的满足L/d≤5.39-1.07(a/b)的条件的粉末。在某个实施方式中,以个数比率计,包含40%以上的满足上述L/d≤5.39-1.07(a/b)的条件的粉末。本发明的实施方式的R-T-B系烧结磁铁通过利用外部磁场使上述的R-T-B系合金粉末取向并进行烧结而获得。本发明的实施方式的R-T-B系合金粉末的制造方法包括:准备包含27.5质量%以上36.0质量%以下的R(R是稀土元素中的至少一种,且必须包含Nd和Pr中的至少一种)、0.85质量%以上1.05质量%以下的B(硼)、0.1质量%以上2.5质量%以下的元素M(M是选自Al、Ti、V、Cr、Mn、Ni、Cu、Zn、Ga、Zr、Nb、Mo、Ag、In、Sn、Hf、Ta、W、Pb和Bi中的至少一种)、剩余部分T(T是以Fe为主要成分的过渡元素,具体而言,是Fe或者Fe和Co)的合金粉末的工序;和将上述合金粉末和粉碎气体导入粉碎槽,对上述合金粉末进行粉碎的工序,该粉碎的工序中,通过在上述粉碎槽内利用上述粉碎气体的流动使上述合金粉末回旋并磨碎来进行粉碎,上述粉碎的工序以满足导入上述粉碎槽的上述粉碎气体的表压为0.65MPa以上且上述粉碎槽内的上述合金粉末的滞留时间为8分钟以上的条件、或者满足上述粉碎气体的表压为0.75MPa以上且上述滞留时间为5分钟以上的条件的方式进行。在某个实施方式中,上述粉碎的工序以满足上述粉碎气体的表压为0.75MPa以上且上述滞留时间为5分钟以上的条件的方式进行。本发明的实施方式的R-T-B系烧结磁铁的制造方法包括:上述获得R-T-B系合金粉末的工序;和利用外部磁场使上述R-T-B系合金粉末取向并进行烧结的工序。发明效果根据本发明的实施方式,能够提供一种角较少的R-T-B系合金粉末、提高了剩余磁通密度Br的R-T-B系烧结磁铁。附图说明图1(a)是本发明的实施方式的R-T-B系合金粉末的SEM照片,(b)是比较例的R-T-B系合金粉末的SEM照片。图2是表示本发明的实施方式中使用的旋流式粉碎装置的结构的示意图,(a)是侧面剖面图,(b)是(a)的Z-Z′剖面图。图3是表示由本发明的实施例和比较例各自的R-T-B系合金粉末的二维投影图求出的a/b与L/d的关系的图。具体实施方式[R-T-B系合金粉末]本发明的实施方式所涉及的R-T-B系合金粉末是在对合金粉末的颗粒进行二维投影得到的轮廓形状中,将长径a、短径b之比设为a/b、将周长L、当量圆直径d(具有相同面积的圆的直径)之比设为L/d时,包含20%以上的满足L/d≤5.39-1.07(a/b)的条件的粉末的合金粉末。其中,长径a表示轮廓形状的最大直径,短径b表示与长径正交的方向的轮廓形状的最大直径。此外,关于对颗粒进行二维投影得到的轮廓形状的长径a、短径b、周长L、当量圆直径d的测定方法,没有特别限定,可以从合金粉末的SEM图像的图像中抽取颗粒,利用市售的图像分析软件对抽取的颗粒的轮廓形状进行分析。优选包含40%以上的满足L/d≤5.39-1.07(a/b)的条件的合金粉末。另外,关于组成,包含27.5质量%以上36.0质量%以下的R(R是稀土元素中的至少一种,且必须包含Nd和Pr中的至少一种)、0.85质量%以上1.05质量%以下的B(硼)、0.1质量%以上2.5质量%以下的元素M(M是选自Al、Ti、V、Cr、Mn、Ni、Cu、Zn、Ga、Zr、Nb、Mo、Ag、In、Sn、Hf、Ta、W、Pb和Bi中的至少一种)、剩余部分T(T是以Fe为主要成分的过渡元素,具体而言是Fe或者Fe和Co)。M优选为选自Al、Cu、Ga、Zr、Nb中的至少一种。R的浓度小于27.5质量%时,在烧结过程中难以生成液相。另一方面,R的浓度超过36.0质量%时,R-T-B系烧结磁铁的磁化会显著降低。R的浓度优选为28.5质量%以上33.0质量%以下。B的浓度小于0.85质量%时,会生成软磁性相,存在使R-T-B系烧结磁铁的矫顽力降低的可能性。另一方面,B的浓度超过1.05质量%时,会生成非磁性相,R-T-B系烧结磁铁的磁化降低。B的浓度优选为0.90质量%以上1.05质量%以下。元素M处于不引起磁化大幅降低的0.1质量%以上2.5质量%以下的范围内。元素M的范围优选为0.1重量%以上1.5重量%以下,进一步优选为0.25重量%以上0.9重量%以下。T是剩余部分。T是以Fe为主要成分的过渡元素,可以包含Co。T是Fe或者Fe和Co,在Fe和Co的合计中,Fe占50原子%以上。作为不可避免的杂质,有O、C、N、H、Si、Ca、S、P等。为了磁铁的高性能化,均优选将其含量在工业上可能的范围内控制为较低。[R-T-B系烧结磁铁]本发明的实施方式的R-T-B系烧结磁铁通过利用外部磁场使上述R-T-B系合金粉末取向并进行烧结而获得。[R-T-B系合金粉末的制造方法]本发明的实施方式的R-T-B系合金粉末通过以下的工序制作,即,使合金粉末在粉碎装置的粉碎槽内回旋,并且利用磨碎对合金粉末彼此进行微粉碎,获得包含27.5质量%以上36.0质量%以下的R(R是稀土元素中的至少一种,且必须包含Nd和Pr中的至少一种)、0.85质量%以上1.05质量%以下的B(硼)、0.1质量%以上2.5质量%以下的元素M(M是选自Al、Ti、V、Cr、Mn、Ni、Cu、Zn、Ga、Zr、Nb、Mo、Ag、In、Sn、Hf、Ta、W、Pb和Bi中的至少一种)、剩余部分T(T是以Fe为主要成分的过渡元素,具体而言是Fe或者Fe和Co)的R-T-B系合金粉末。在上述的微粉碎的工序中,导入粉碎槽的粉碎气体的表压为0.65MPa以上时,使合金粉末在粉碎层内滞留8分钟以上,另外,为0.75MPa以上时,使合金粉末在粉碎层内滞留5分钟以上。其结果,在本发明的实施方式中得到的R-T-B系合金粉末容易成为角较少的形状。关于本发明的实施方式的R-T-B系合金粉末,通过具有角较少的形状,可以降低空间阻碍,在磁场中成型工序中合金粉末容易旋转,因此取向度提高。其结果,使用该合金粉末制得的R-T-B系烧结磁铁的剩余磁通密度Br提高。以下,参照附图,对本发明的更加详细的实施方式进行说明,但本发明并不限定于以下的实施方式。[母合金]母合金可以利用铸锭法、薄带连铸法中的任意种进行制作,优选利用作为骤冷法的薄带连铸法进行制作。由此,在铸造组织中不会残存α-Fe,能够容易地进行粉碎。关于母合金的组成,考虑中途工序中的各元素的减少部分来适当决定,使得所得到的R-T-B系合金粉末的组成为规定的组成即可。[粉碎]在粉碎工序中,包括粗粉碎工序和微粉碎工序的二阶段的粉碎工序。首先,对粗粉碎工序进行说明。母合金的粗粉碎可以利用机械粉碎法或氢粉碎法进行。在这些方法中,优选通过利用氢脆化现象的氢粉碎法对母合金进行粗粉碎。该方法利用伴随于氢吸留的母合金的脆化现象和体积膨胀现象,在母合金产生微细的裂缝,对母合金进行粉碎。采用氢粉碎法,在晶界破裂的概率变高,故而优选。在晶界破裂的概率高时,颗粒内所含的主相结晶(2-14-1化合物)成为1个,易磁化方向成为1个方向,因此磁场取向变得容易,Br提高。氢粉碎法例如通过常温中暴露在加压氢中一定时间来进行。接着,升高温度使过剩的氢排出后,进行冷却。在氢脆化后的合金粉末内存在大量裂缝,比表面积大幅增加。因此,活性非常强,由于在大气中的操作中氧量显著增加,因此希望在N2、Ar等的不活泼气体中进行操作。利用粗粉碎工序得到的合金粉末的粒度例如为500μm以下。此外,在粗粉碎工序之后、后述的微粉碎工序之前,例如也可以使用筛子等使粒度成为特定范围以下。在接下来进行的微粉碎工序中,通过使粗粉碎后的合金粉末彼此在粉碎装置的粉碎槽内回旋并磨碎来进行微粉碎。作为例子,在以下对使用旋流式粉碎装置的微粉碎工序进行说明。在使用旋流式粉碎装置的气流粉碎方式中,向设置于粉碎装置的粉碎槽的内部导入高压的粉碎气体。由此,可以在粉碎槽的内部产生高速回旋的气体的流动,利用该气体的流动使合金粉末在粉碎槽内回旋。通过使用旋流式粉碎装置的粉碎方式,在回旋中利用磨碎而形成角较少的合金粉末。粉碎气体通常使用N2气体,也可以使用He和Ar气体等的稀有气体。在本说明书中,所谓旋流式粉碎装置,广泛包括在通常被称为喷射磨的气流式粉碎机中、主要利用回旋力进行粉碎的方式、更具体而言可以获得磨碎效果的装置。将从粗粉碎粉供给喷嘴开始供给直到在回收容器(未图示)中确认到合金粉末的时间定义为滞留时间。导入粉碎槽中的气体压力以表压(与大气压的差)表示。以表压计,粉碎气体的压力优选设定为0.75MPa以上。更加优选为0.75MPa以上1.5MPa以下,进一步优选为0.75MPa以上0.95MPa以下。滞留时间优选为5分钟以上。更加优选为5分钟以上10分钟以下,进一步优选为6分钟以上10分钟以下。在本实施方式中,为了延长滞留时间,例如,可以采用使供给量比以往少的方法。通过使粉碎槽内的合金粉末在喷射0.75MPa以上的粉碎气体而形成的回旋流中滞留5分钟以上,可以获得全部消除了角的合金粉末。以D50(是利用气流分散型激光衍射法得到的粉末粒径,体积基准中心值)计,在该微粉碎工序后回收的合金粉末的粒径例如为1.0μm以上5.5μm以下。另外,在本实施方式中,为了进一步提高磁特性,以D50计,粒径优选为2.5μm以上5.0μm以下,更加优选为2.51μm以上4.63μm以下。以下,对本实施方式中使用的旋流式粉碎装置的详细情况进行说明。图2(a)是表示旋流式粉碎装置1的示意图。另外,图2(b)表示沿图2(a)的Z―Z′线切断的剖面。旋流式粉碎装置1具有收纳在其内部回旋的粉碎气体和粉碎粉的粉碎槽2A。其中,粉碎槽2A是利用外壳2所围成的空间。在外壳2安装有与粉碎槽2A连通的多个粉碎气体导入喷嘴5。使各喷射口朝向粉碎槽2A的内部(其中,朝向从中心偏离的方向)来固定设置粉碎气体导入喷嘴5。如图2(a)和(b)所示,在粉碎气体导入喷嘴5中的1个上设置有用于向粉碎槽内供给粗粉碎后的合金粉末的粗粉碎粉供给口3。利用该粗粉碎粉供给口3,将从漏斗状的粗粉碎粉供给部4供给的合金粉末与从粉碎气体导入喷嘴5喷射的高速的粉碎气体一起向粉碎槽2A内喷射、导入。通过送气管,从未图示的高压气体供给装置向粉碎气体导入喷嘴5分别输送高压的气体(粉碎气体)。在本实施方式中,上述的高压气体供给装置构成为能够使供给粉碎槽2A的粉碎气体的压力以表压计达到0.75MPa以上的方式。导入粉碎槽2A的内部的合金粉末被卷入利用从沿内侧壁配设的多个粉碎气体导入喷嘴5喷出的气体而产生的高速回旋流18中,在粉碎槽2A内回旋。此时,利用磨碎,合金粉末被粉碎。通过在旋流式粉碎装置1的粉碎槽2A内滞留规定的时间,制作角较少的R-T-B系合金粉末。然后,在粉碎槽内的滞留量成为一定以上时,从位于粉碎槽2A的中央部的上方的微粉碎粉排出口6取出通过粉碎得到的R-T-B系合金粉末。在图2(a)和(b)所示的结构中,能够在粉碎槽2A内滞留的合金粉末的量根据每个装置、每个运转条件而决定。将超过其量的合金粉末导入粉碎槽2A内时,向槽外排出与导入的分量相当的合金粉末。因此,通过调整向粉碎槽2A的导入量,能够调整粉碎槽内的粉末的滞留时间。[R-T-B系烧结磁铁的制造方法][利用外部磁场的主相结晶的取向]利用外部磁场使上述R-T-B系合金粉末取向。其中,利用外部磁场取向是指,可以在具有磁场施加线圈的模具压力机中进行,也能够在填充容器中高密度地填充粉末后,利用外部磁场使上述R-T-B系合金粉末的主相结晶取向。另外,也能够在填充容器中磁场取向后,利用静水压机成型。另外,施加的磁场既可以是静磁场,也可以是脉冲磁场。[成型]使用模具压力机时,将成型体的密度例如设定为3.7g/cm3以上4.7g/cm3以下。调整至该范围内时,容易保持成型体的强度,并且容易提高取向度。小于3.7g/cm3时,虽然取向度提高,但利用模具压力机进行成型时,强度不足,在对成型体进行处理时有破裂的危险。超过4.7g/cm3时,虽然成型体强度变高,但有时会抑制磁场成型时的颗粒的移动,取向度降低。利用模具压力机或者静水压机制作上述的R-T-B系合金粉末的成型体时,为了抑制碳的进入,希望将润滑剂等的使用限定在最小限度。在烧结工序(或之前的工序)中,为了能够脱脂,选择挥发性高的润滑剂。只要是本发明的实施方式的R-T-B系合金粉末,无论是减少润滑剂的使用量的情况,还是不使用润滑剂的情况,都可以获得高的取向。在模具压力机或者静水压机中,对于成型时施加的压力,没有特别限定,例如为9.8MPa以上,更加优选为19.6MPa以上,为245MPa以下,更加优选为147MPa以下。[烧结]烧结工序优选在保持在真空中或大气压以下的不活泼气体气氛中的烧结炉内进行。此处的不活泼气体是指Ar或He气体。关于保持大气压以下的不活泼气体气氛的方法,优选利用真空泵进行真空排气并将少量不活泼气体导入烧结炉内的方法。在这种情况下,可以间歇地进行真空排气,也可以间歇地进行不活泼气体的导入。另外,也能够使真空排气和导入两者都间歇地进行。通常,烧结通过将成型体在950℃至1100℃的温度范围内保持30分钟至16小时来进行。也可以在相同的温度或不同的温度分多次进行烧结。烧结后的冷却的条件,包括以下的热处理,可以组合适当的条件,使得所得到的磁铁的矫顽力的值成为目标值。除了上述的烧结方法以外,也能够应用从外部施加压力并进行加温的热压机、利用焦耳热对成型体进行加热的电烧结等在粉末冶金法中使用的所有的烧结方法。使用这些方法时,烧结温度、时间不限定于上述的情况。烧结后,优选作为烧结体的磁铁的密度为7.3g/cm3以上。更加优选为7.5g/cm3以上。[热处理]出于提高矫顽力的目的,在烧结结束后,能够在烧结温度以下进行热处理。另外,也可以将该热处理在相同的温度或改变温度进行多次。作为热处理时的冷却条件,能够选择各种条件。此外,对于以烧结后的状态获得充分的矫顽力的情况,并不需要进行热处理。[加工]有时作为烧结体而得到的磁铁具有接近于最终产品的形状,但也存在不是那样的情况,通常利用切断、研削、研磨等的机械加工将烧结后的R-T-B系烧结磁铁加工成规定形状。另外,关于该加工,只要是在烧结后即可,无论在热处理之前还是热处理之后,或者在多次的热处理的中间都可以进行。[表面处理]为了防锈,优选对所得到的R-T-B系烧结磁铁实施表面涂敷处理。作为表面涂敷处理的例子,有镀Ni、镀Sn、镀Zn、蒸镀Al、蒸镀Al合金、涂装树脂等。以下,对本发明的实施例进行说明。(实施例1)以纯度99.5%以上的Nd、电解铁、低碳硼铁合金为主要原料,将添加元素(Co和M)以纯金属或与Fe的合金的形式进行添加,以最终使R-T-B系合金粉末和烧结磁铁的组成成为Nd:30.5、B:0.94、Co:0.9、Cu:0.1、Al:0.1、Ga:0.1、Fe:剩余部分[质量%]的方式,将熔融的合金熔液利用薄带连铸法进行骤冷,得到厚度0.1~0.3mm的板状的合金。使用能够加压的热处理炉将该合金保持在氢加压气氛后,在真空中加热至600℃,冷却。从炉中取出后,利用筛子进行粒度的调整,得到粒度为425μm以下的合金粉末。接着,使用图2(a)和(b)所示的旋流式粉碎装置1,改变供给量、滞留时间,将微粉碎的粉碎条件和得到的粉末的粒径(D50)表示在表1中。本实施例中使用的装置的粉碎槽的容积为314cm3。其中,粉碎气体是将氧浓度控制在8000ppm以下的N2气体。粉碎气体压力是以表压表示导入粉碎槽的粉碎气体的压力的值。供给量是在1分钟内向粉碎槽投入的合金粉末的量。将从粗粉碎粉供给喷嘴开始供给直至经过旋风分离器(未图示)在回收容器(未图示)内确认到存在合金粉末所需要的时间定义为滞留时间。将即使是少量也在4分钟后也能够回收的情况记为4分钟,将在4分钟不能回收而在6分钟回收的情况记为6分钟。[表1]在图1(a)中表示粉碎气体的压力为0.75MPa且滞留时间为6分钟的样品1(实施例)的合金粉末的照片(SEM图像)。如图1(a)所示,样品1的合金粉末的表面角较少,全部是具有弧面的形状。另一方面,在图1(b)中表示气体压为0.75MPa且滞留时间为4分钟的样品2(比较例)的合金粉末的照片。如图1(b)所示,可以确认样品2的合金粉末与样品1相比,有棱角。为了对实施例和比较例的粉末的形状进行评价,根据合金粉末的SEM图像,利用作为图像分析软件的SCANDIUM(Olympus公司制)对二维投影的颗粒的轮廓形状进行分析,算出长径/短径(a/b)、周长/当量圆直径(L/d)。在表2中表示从上述合金粉末中任意抽取的合金粉末的a/b和L/d。关于作为实施例的样品1(颗粒a~m)的合金粉末,根据SEM图像,对各颗粒进行二维投影得到的轮廓形状满足L/d≤5.39-1.07(a/b)的条件式。在图3中表示与表2的测定结果对应的分布图(散点图)。从该图可知,实施例的合金粉末位于a/b、L/d满足本发明的条件式的上述图3的左下方的区域内。另一方面,可知比较例的样品2(颗粒n~v)的合金粉末不满足条件式L/d≤5.39-1.07(a/b),没有包含在上述图3的左下方的区域内。在数学意义上,形状为圆时,a/b为1,L/d为π。[表2]在实施例的合金粉末(样品1)和比较例的合金粉末(样品2)中混合0.16质量%的辛酸甲酯后,在1.36MA/m的磁场中磁场施加方向与加压方向正交的条件下,利用25MPa的成型压力,制作下述表3所示的样品1(实施例)、样品2(比较例)的成型体。然后,在减压Ar气体气氛中,在1080℃、4小时的条件下对样品1、2进行烧结。接着,在真空气氛中,在500℃对所得到的R-T-B系烧结磁铁进行2小时的热处理,之后冷却。对这些样品进行机械加工后,利用B-H示踪器测定室温中的剩余磁通密度Br和矫顽力HcJ。R-T-B系烧结磁铁的取向度是将得到的R-T-B系烧结磁铁的易磁化方向设为X轴方向、将X轴方向的剩余磁通密度设为Brx、将与取向磁场方向正交的2个方向的剩余磁通密度设为Bry和Brz,利用作为Brx相对于(Brx2+Bry2+Brz2)1/2的比的3个方向取向度(Brx/(Brx2+Bry2+Brz2)1/2)算出的值。另外,表中的成型体密度、烧结体密度是由尺寸和质量的测定结果算出的值。[表3]如表3所示,样品1(实施例)尽管是与样品2(比较例)相同的组成,并且成型体密度也高,剩余磁通密度Br、矫顽力HcJ和取向度的值还是提高了。这可以考虑是由于样品1是没有角的粉末,从而在磁场中成型时颗粒容易移动,作为结果,成为高的取向度,Br提高。(实施例2)以纯度99.5%以上的Nd、电解铁、低碳硼铁合金为主要原料,将添加元素(Co和M)作为纯金属或与Fe的合金进行添加,以最终使R-T-B系合金粉末和烧结磁铁的组成成为Nd:29.1、B:0.94、Co:0.9、Cu:0.1、Al:0.1、Ga:0.1、Fe:剩余部分[质量%]的方式,将熔融的合金熔液利用薄带连铸法进行骤冷,得到厚度0.1~0.3mm的板状的合金。使用能够加压的热处理炉将该合金保持在氢加压气氛后,在真空中加热至600℃,冷却。从炉中取出后,利用筛子进行粒度的调整,得到粒度为425μm以下的合金粉末。本实施例中使用的装置的粉碎槽的容积为314cm3。其中,粉碎气体是氮气。粉碎气体压力是以表压表示导入粉碎槽内的粉碎气体的压力的值。使用图2(a)和(b)所示的旋流式粉碎装置1,改变供给量、滞留时间,将微粉碎的粉碎条件和得到的粉末的粒径(D50)表示在表4中。对于表4所示的样品3~12,使粉碎的粉末氧化后,在每个样品中随机抽取10个合金粉末,利用市售的分析软件对二维投影的颗粒的轮廓形状进行评价,评价是否满足L/d≤5.39-1.07(a/b)的条件式,并记载满足条件式的合金粉末的比例。[表4]如上述表4所示,样品5包含20%的满足条件式的合金粉末,样品13包含40%的满足条件式的合金粉末。其中,“满足条件的合金粉末的比例”利用满足条件的粉末的个数相对于测定的粉末的全部个数(即个数比率)而求出。样品7~9、11、14包含100%的满足条件式的合金粉末。为了测定磁特性,微粉碎工序后,使用油将样品3~14的合金粉末制成浆料,在1.36MA/m的磁场中磁场施加方向与加压方向正交的条件下,利用25MPa的成型压力,制作成型体。然后,如表5所示,在减压Ar气体气氛中,在1080℃、4小时的条件下对样品3~14进行烧结。接着,在真空气氛中,在500℃对得到的R-T-B系烧结磁铁进行2小时的热处理,之后冷却。对这些样品进行机械加工后,利用B-H示踪器测定室温中的剩余磁通密度Br、矫顽力HcJ和取向度。与实施例1同样利用3个方向取向度算出取向度。[表5]NoBr(T)HcJ(kA/m)取向度样品31.4349080.988样品41.4339120.988样品51.4409140.989样品61.4369520.988样品71.4559610.992样品81.4579600.992样品91.4579620.992样品101.4349890.988样品111.4569970.992样品121.43510280.988样品131.45410360.992样品141.45510370.992如上述表4和表5所示,在表压为0.65MPa的样品3、4中,在滞留时间为4分钟时和6分钟时,剩余磁通密度Br、矫顽力HcJ和取向度几乎没有差别。在滞留时间为8分钟的样品5中,剩余磁通密度Br、矫顽力HcJ和取向度提高了。对表压为0.75MPa的样品6~9进行比较时,滞留时间为6分钟以上时,剩余磁通密度Br、矫顽力HcJ和取向度提高了。对表压为0.85MPa的样品10、11进行比较时,与滞留时间为4分钟的样品10相比,滞留时间为6分钟的样品11的剩余磁通密度Br、矫顽力HcJ和取向度优异。对表压为0.95MPa的样品12~14进行比较时,滞留时间为5分钟以上时,剩余磁通密度Br、矫顽力HcJ和取向度提高了。由样品13可知,满足L/d≤5.39-1.07(a/b)的条件式的粉末的比例(个数)为40%以上时,剩余磁通密度Br、矫顽力HcJ和取向度成为特别优异的值。此外,在上述使用喷射磨进行粉碎工序的情况中,显示了在获得包含20%以上的满足L/d≤5.39-1.07(a/b)的粉末的合金粉末时剩余磁通密度Br、矫顽力HcJ和取向度提高的例子,但利用其它的方法也可以获得同样的合金粉末。(实施例3)以纯度99.5%以上的Nd、Pr、Dy、Tb、电解铁、低碳硼铁合金为主要原料,将添加元素M作为纯金属或与Fe的合金进行添加,以最终使R-T-B系合金粉末和烧结磁铁的组成成为Nd:22.8、Pr:7.6、Dy:1.0、Tb:1.0、B:1.05、Cu:0.1、Al:0.3、Nb:0.5、Fe:剩余部分[质量%]的方式,将熔融的合金熔液利用薄带连铸法进行骤冷,得到厚度0.1~0.3mm的板状的合金。使用能够加压的热处理炉将该合金保持在氢加压气氛后,在真空中加热至660℃,冷却。从炉中取出后,利用筛子进行粒度的调整,得到粒度为425μm以下的合金粉末。本实施例中使用的装置的粉碎槽的容积为314cm3。其中,粉碎气体是将氧浓度控制在8000ppm以下的氮气。粉碎气体压力是以表压表示导入粉碎槽的粉碎气体的压力的值。使用图2(a)和(b)所示的旋流式粉碎装置1,改变供给量、滞留时间,将微粉碎的粉碎条件和得到的粉末的粒径表示在表6中。对于表6所示的样品15、16,使粉碎的粉末氧化后,在每个样品中随机抽取10个合金粉末,利用市售的分析软件对二维投影的颗粒的轮廓形状进行评价,评价是否满足L/d≤5.39-1.07(a/b)的条件式,并记载满足条件式的合金粉末的比例。[表6]如上述表6所示,在样品16中,包含100%的满足条件式的合金粉末。另一方面,在样品15中,不含满足条件式的合金粉末。为了测定磁特性,微粉碎工序后,使用油将样品15、16的合金粉末制成浆料,在1.36MA/m的磁场中磁场施加方向与加压方向正交的条件下,利用25MPa的成型压力,制作成型体。然后,在减压Ar气体气氛中,在1080℃、4小时的条件下对样品15、16进行烧结。接着,在真空气氛中,在500℃对得到的R-T-B系烧结磁铁进行2小时的热处理,之后冷却。对这些样品进行机械加工后,利用B-H示踪器测定室温中的剩余磁通密度Br、矫顽力HcJ和取向度。与实施例1同样利用3个方向取向度算出取向度。[表7]NoBr(T)HcJ(kA/m)取向度样品151.30016600.981样品161.31116830.992如上述表6和表7所示,对表压为0.65MPa的样品15和表压为0.75MPa的样品16进行比较,作为实施例的样品16与为相同组成的样品15相比,剩余磁通密度Br、矫顽力HcJ和取向度提高了。(实施例4)以纯度99.5%以上的Nd、Pr、电解铁、低碳硼铁合金为主要原料,将添加元素(Co和M)作为纯金属或与Fe的合金进行添加,以最终使R-T-B系合金粉末和烧结磁铁的组成成为Nd:21.9、Pr:7.3、B:0.94、Co:2.0、Cu:0.1、Al:0.05、Ga:0.1、Fe:剩余部分[质量%]的方式,将熔融的合金熔液利用薄带连铸法进行骤冷,得到厚度0.1~0.3mm的板状的合金。使用能够加压的热处理炉将该合金保持在氢加压气氛后,在真空中加热至580℃,冷却。从炉中取出后,利用筛子进行粒度的调整,得到粒度为425μm以下的合金粉末。本实施例中使用的装置的粉碎槽的容积为628cm3。其中,粉碎气体是氦气。粉碎气体压力是以表压表示导入粉碎槽的粉碎气体的压力的值。使用图2(a)和(b)所示的旋流式粉碎装置1,改变供给量、滞留时间,将微粉碎的粉碎条件和得到的粉末的粒径表示在表8中。对于表8所示的样品17、18,使粉碎的粉末氧化后,在每个样品中随机抽取10个合金粉末,利用市售的分析软件对二维投影的颗粒的轮廓形状进行评价,评价是否满足L/d≤5.39-1.07(a/b)的条件式,并记载满足条件式的合金粉末的比例。[表8]如上述表8所示,在样品18中,包含100%的满足条件式的合金粉末。另一方面,在样品17中,不含满足条件式的合金粉末。为了测定磁特性,在微粉碎工序后,使用油将样品17和18的合金粉末制成浆料,在1.36MA/m的磁场中磁场施加方向与加压方向正交的条件下,利用15MPa的成型压力,制作成型体。然后,在减压Ar气体气氛中,在1040℃、4小时的条件下对样品17、18进行烧结。接着,在真空气氛中,在500℃对得到的R-T-B系烧结磁铁进行2小时的热处理,之后冷却。对这些样品进行机械加工后,利用B-H示踪器测定室温中的剩余磁通密度Br、矫顽力HcJ和取向度。与实施例1同样利用3个方向取向度算出取向度。[表9]NoBr(T)HcJ(kA/m)取向度样品171.43913450.982样品181.45013940.990如上述表8和表9所示,对表压为0.65MPa的样品17和表压为0.85MPa的样品18进行比较,作为实施例的样品18与为相同组成的样品17相比,剩余磁通密度Br、矫顽力HcJ和取向度提高了。(实施例5)以纯度99.5%以上的Nd、Pr、Dy、Tb、电解铁、低碳硼铁合金为主要原料,将添加元素(Co和M)作为纯金属或与Fe的合金进行添加,以最终使R-T-B系合金粉末和烧结磁铁的组成成为Nd:22.5、Pr:7.5、Dy:0.1、Tb:0.1、B:0.90、Co:0.9、Cu:0.15、Al:0.1、Ga:0.5、Zr:0.1、Fe:剩余部分[质量%]的方式,将熔融的合金熔液利用薄带连铸法进行骤冷,得到厚度0.1~0.3mm的板状的合金。使用能够加压的热处理炉将该合金保持在氢加压气氛后,在真空中加热至550℃,冷却。从炉中取出后,利用筛子进行粒度的调整,得到粒度为425μm以下的合金粉末。本实施例中使用的装置的粉碎槽的容积为314cm3。其中,粉碎气体是氩气。粉碎气体压力是以表压表示导入粉碎槽的粉碎气体的压力的值。使用图2(a)和(b)所示的旋流式粉碎装置1,改变供给量、滞留时间,将微粉碎的粉碎条件和得到的粒径表示在表10中。对于表10所示的样品19、20,使粉碎的粉末氧化后,在每个样品中随机抽取10个合金粉末,利用市售的分析软件对二维投影的颗粒的轮廓形状进行评价,评价是否满足L/d≤5.39-1.07(a/b)的条件式,并记载满足条件式的合金粉末的比例。[表10]如上述表10所示,样品20包含100%的满足条件式的合金粉末。另一方面,在样品19中,不含满足条件式的合金粉末。为了测定磁特性,在微粉碎工序后,使用油将样品19、20的合金粉末制成浆料,在1.36MA/m的磁场中磁场施加方向与加压方向正交的条件下,利用25MPa的成型压力,制作成型体。然后,在减压Ar气体气氛中,在1060℃、4小时的条件下对样品19、20进行烧结。接着,在真空气氛中,在500℃对得到的R-T-B系烧结磁铁进行2小时的热处理,之后冷却。对这些样品进行机械加工后,对这些样品进行机械加工后,利用B-H示踪器测定室温中的剩余磁通密度Br、矫顽力HcJ和取向度。与实施例1同样利用3个方向取向度算出取向度。[表11]NoBr(T)HcJ(kA/m)取向度样品191.39215000.980样品201.40615200.991如上述表10和表11所示,对表压为0.65MPa的样品19和表压为0.75MPa的样品20进行比较,作为实施例的样品20与为相同组成的样品19相比,剩余磁通密度Br、矫顽力HcJ和取向度提高了。此外,在本发明的实施例中,列举了粉碎槽的容积为314cm3、628cm3的2个例子,根据容积的大小,以合金粉末的滞留时间处于本发明的范围内的方式适当调整供给量即可,不受容积的大小的限定。工业上的可利用性本发明的实施方式的R-T-B系合金粉末适用于制作R-T-B系烧结磁铁。符号说明1旋流式粉碎装置2外壳2A粉碎槽3粗粉碎粉供给口4粗粉碎粉供给部5粉碎气体导入喷嘴6微粉碎粉排出口18高速回旋流当前第1页1 2 3