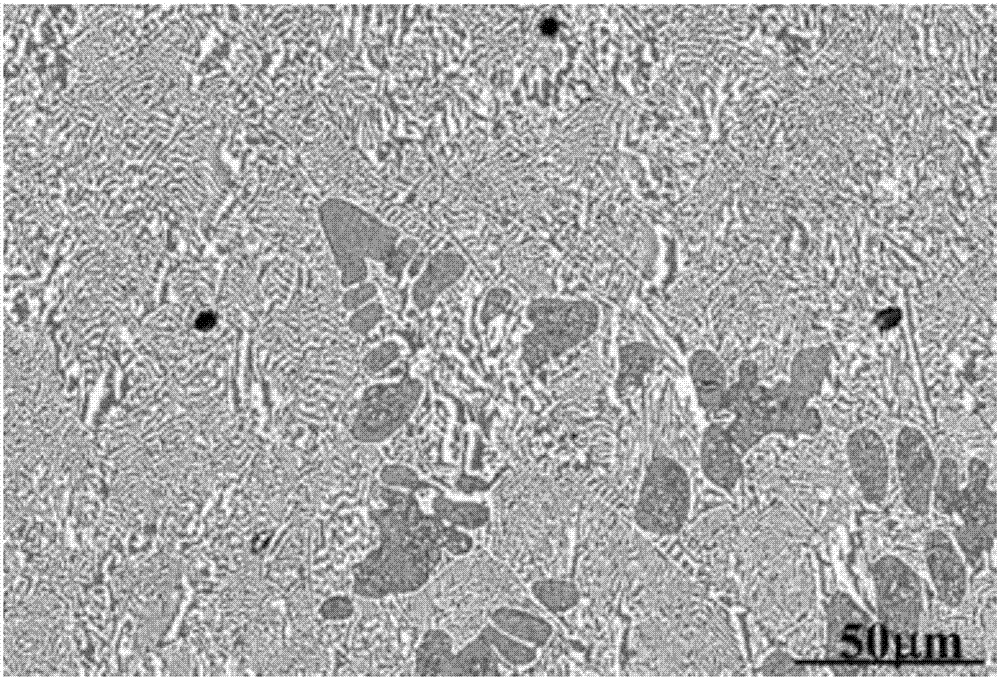
本发明涉及一种电子封装用sn-bi系复合钎料及其制备方法。
背景技术:
:微电子焊接技术所采用的互连材料是实现焊点可靠连接的物质基础。长期以来,sn-pb钎料由于具有成本低、力学性能好、导电性能强、工艺性能好以及可焊性能好等优点已被广泛应用到电子封装领域数十年。但是pb危害人体健康和自然环境,许多国家近年来已经提出了有关法律法规来禁止pb的使用,在这种情况下,钎料的无铅化已经成为了目前的主流趋势。随着电子封装技术的不断提高,微型连接领域所需要的微焊点尺寸也越来越小,与此同时焊接部位所需要承受的力、电、热能负荷量却与日俱增,对于钎焊接头的可靠性要求达到了前所未有的高度。在众多的无铅钎料中,作为低温无铅钎料的sn-58bi钎料,其拉伸强度和抗蠕变性能都优于sn-37pb钎料,这使得sn-58bi钎料在温度敏感区以及分级封装的外层钎焊连接中都体现出了巨大的优势。但是由具有硬脆性质的富bi相在液态sn-58bi钎料冷却过程中易结晶形成粗大的长条状/块状的不规则形体,导致合金的脆性随着bi相的含量增高,使其延展性明显降低,焊接接头的力学性能较差。目前研究改善无铅钎料性能的方法分为两种,一种是合金化,以现有的sn基无铅钎料为基础,通过添加合金元素,以添加组元的方式来改善基础钎料的性能;另一种方法是颗粒增强,即在sn基钎料中内生成或直接加入第二相颗粒,制备出复合无铅钎料,从而改善钎料的性能。但还很难找到一种综合性能能够完全与传统sn-pb共晶钎料相匹敌的无铅钎料。石墨烯是一种具有优良的电学、热学、力学性能的二维材料,添加进入无铅钎料中可以明显改善钎料的润湿性,导电导热性和力学性能。但因其密度较低,加入钎料后在重熔的过程中会出现上浮现象,起不到预期的改善效果。经研究发现,氧化铈作为一种优秀的增强相可抑制钎料与基体界面金属间化合物颗粒的长大,改善抗拉性能。但对于石墨烯负载氧化铈作为增强相改善钎料性能的研究还是一片空白。技术实现要素:本发明是要解决sn-58bi钎料中硬脆性质的富bi相所导致的合金延展性能降低,以及重熔服役和时效过程中,过厚的金属间化合物导致钎焊接头可靠性能变差的问题,而提供一种电子封装用sn-bi系复合钎料及其制备方法。一种电子封装用sn-bi系复合钎料由增强体和sn-58bi钎料组成;所述电子封装用sn-bi系复合钎料中增强体的质量分数为0.005%~0.5%;所述增强体为石墨烯负载纳米级氧化铈或石墨烯负载微米级氧化铈,且所述增强体中石墨烯的质量分数为30%~90%。一种电子封装用sn-bi系复合钎料的制备方法是按以下步骤完成的:一、将增强体与sn-58bi钎料采用周期球磨的方式球磨2h~3h,得到混料;所述周期球磨中每个周期内球磨5min,停止5min,球磨速度为100r/min~200r/min;所述增强体为石墨烯负载纳米级氧化铈或石墨烯负载微米级氧化铈,且所述增强体中石墨烯的质量分数为30%~90%;二、向混料中加入助焊膏并搅拌至膏状,得到混合物;三、将混合物倒入坩埚中,将坩埚于180℃条件下加热12min后,每3min搅拌1次,搅拌4次后倒入模具冷却;四、冷却后取出钎料块超声清洗3min,得到电子封装用sn-bi系复合钎料;所述电子封装用sn-bi系复合钎料中增强体的质量分数为0.005%~0.5%。本发明优点:本发明通过在石墨烯上负载氧化铈颗粒,从而降低了石墨烯与钎料基体之间的密度差,避免复合钎料在重熔过程中出现的石墨烯上浮现象,增强改善效果;复合钎料细化了焊点微观组织,提高了钎料的硬度,降低了钎料与基体界面的金属间化合物厚度,从而提高焊点的剪切强度。采用石墨烯纳米片作为增强相,可批量生产,成本远低于单层石墨烯,同时又具有石墨烯优异的电学、热学、力学性能;采用熔铸的方法,不破坏石墨烯原有的结构,并使钎料块的孔隙率降低。本发明的电子封装用sn-bi系复合钎料相比于单纯的sn-58bi钎料硬度提高18%~44%,剪切强度提高5%~20%。附图说明图1为sn-58bi钎料互连焊点组织形貌图;图2为实施例三得到的复合钎料的互连焊点组织形貌图;图3为实施例五得到的复合钎料的互连焊点组织形貌图。具体实施方式具体实施方式一:本实施方式一种电子封装用sn-bi系复合钎料由增强体和sn-58bi钎料组成;所述电子封装用sn-bi系复合钎料中增强体的质量分数为0.005%~0.5%;所述增强体为石墨烯负载纳米级氧化铈或石墨烯负载微米级氧化铈,且所述增强体中石墨烯的质量分数为30%~90%。具体实施方式二:本实施方式与具体实施方式一不同的是:所述石墨烯负载纳米级氧化铈中石墨烯的粒径为2~10μm、厚度为20~50nm,纳米级氧化铈的粒径为10~20nm;所述石墨烯负载微米级氧化铈中石墨烯的粒径为2~10μm、厚度为20~50nm,微米级氧化铈的粒径为2~5μm。其他与具体实施方式一相同。具体实施方式三:本实施方式与具体实施方式一或二不同的是:所述电子封装用sn-bi系复合钎料中增强体的质量分数为0.01%。其他与具体实施方式一或二相同。具体实施方式四:本实施方式与具体实施方式一至三之一不同的是:所述电子封装用sn-bi系复合钎料中增强体的质量分数为0.1%。其他与具体实施方式一至三之一相同。具体实施方式五:本实施方式与具体实施方式一至四之一不同的是:所述电子封装用sn-bi系复合钎料中增强体的质量分数为0.2%。其他与具体实施方式一至四之一相同。具体实施方式六:本实施方式与具体实施方式一至五之一不同的是:所述增强体中石墨烯的质量分数为50%。其他与具体实施方式一至五之一相同。具体实施方式七:本实施方式与具体实施方式一至六之一不同的是:所述增强体中石墨烯的质量分数为70%。其他与具体实施方式一至六之一相同。具体实施方式八:本实施方式与具体实施方式一至七之一不同的是:所述石墨烯负载纳米级氧化铈的制备方法是按以下步骤进行的:①、将六水合硝酸铈溶于水配成浓度为0.01mol/l的硝酸铈溶液;将石墨烯分散于无水乙醇中,超声处理1h得到石墨烯分散液;将石墨烯分散液与浓度为0.01mol/l的硝酸铈溶液混合,得到混合溶液;②、向混合溶液中逐滴加入氨水,调节ph值至9,再向其中加入h2o2,搅拌1h后转移到水热反应釜中,在温度为230℃的条件下加热24h,离心分离,先用去离子水清洗两次再采用无水乙醇清洗两次,在温度为60℃的条件下加热12h后研磨,得到石墨烯负载纳米级氧化铈;所述石墨烯负载纳米级氧化铈中石墨烯的质量分数为30%~90%。其他与具体实施方式一至七之一相同。本实施方式中h2o2的作用是氧化还原,使得纳米级氧化铈上可以负载更多的石墨烯。具体实施方式九:本实施方式与具体实施方式一至八之一不同的是:所述石墨烯负载微米级氧化铈的制备方法是按以下步骤进行的:①、配制浓度为2.2mol/l的草酸溶液;将石墨烯分散于无水乙醇中,超声处理1h得到石墨烯分散液;将石墨烯分散液和浓度为2.2mol/l的草酸溶液混合,再向其中加入氨水调节ph至3,得到含有白色絮状沉淀的溶液;②、将cecl2溶于去离子水中配制成浓度为1mol/l的cecl2溶液,将浓度为1mol/l的cecl2溶液与含有白色絮状沉淀的溶液混合,在搅拌速度为200r/min的条件下反应3min,陈化40min后采用温度为85℃~90℃的热水洗涤5次,烘干,得到前驱体;③、将前驱体在温度为800℃的条件下煅烧3h,研磨得到石墨烯负载微米级氧化铈;所述石墨烯负载微米级氧化铈中石墨烯的质量分数为30%~90%。其他与具体实施方式一至八之一相同。具体实施方式十:本实施方式一种电子封装用sn-bi系复合钎料的制备方法是按以下步骤完成的:一、将增强体与sn-58bi钎料采用周期球磨的方式球磨2h~3h,得到混料;所述周期球磨中每个周期内球磨5min,停止5min,球磨速度为100r/min~200r/min;所述增强体为石墨烯负载纳米级氧化铈或石墨烯负载微米级氧化铈,且所述增强体中石墨烯的质量分数为30%~90%;二、向混料中加入助焊膏并搅拌至膏状,得到混合物;三、将混合物倒入坩埚中,将坩埚于180℃条件下加热12min后,每3min搅拌1次,搅拌4次后倒入模具冷却;四、冷却后取出钎料块超声清洗3min,得到电子封装用sn-bi系复合钎料;所述电子封装用sn-bi系复合钎料中增强体的质量分数为0.005%~0.5%。具体实施方式十一:本实施方式与具体实施方式十不同的是:步骤一中所述石墨烯负载纳米级氧化铈的制备方法是按以下步骤进行的:①、将六水合硝酸铈溶于水配成浓度为0.01mol/l的硝酸铈溶液;将石墨烯分散于无水乙醇中,超声处理1h得到石墨烯分散液;将石墨烯分散液与浓度为0.01mol/l的硝酸铈溶液混合,得到混合溶液;②、向混合溶液中逐滴加入氨水,调节ph值至9,再向其中加入h2o2,搅拌1h后转移到水热反应釜中,在温度为230℃的条件下加热24h,离心分离,先用去离子水清洗两次再采用无水乙醇清洗两次,在温度为60℃的条件下加热12h后研磨,得到石墨烯负载纳米级氧化铈;所述石墨烯负载纳米级氧化铈中石墨烯的质量分数为30%~90%;所述石墨烯负载纳米级氧化铈中石墨烯的粒径为2~10μm、厚度为20~50nm,纳米级氧化铈的粒径为10~20nm。其他与具体实施方式十相同。本实施方式中h2o2的作用是氧化还原,使得纳米级氧化铈上可以负载更多的石墨烯。具体实施方式十二:本实施方式与具体实施方式十或十一不同的是:步骤一中所述石墨烯负载微米级氧化铈的制备方法是按以下步骤进行的:①、配制浓度为2.2mol/l的草酸溶液;将石墨烯分散于无水乙醇中,超声处理1h得到石墨烯分散液;将石墨烯分散液和浓度为2.2mol/l的草酸溶液混合,再向其中加入氨水调节ph至3,得到含有白色絮状沉淀的溶液;②、将cecl2溶于去离子水中配制成浓度为1mol/l的cecl2溶液,将浓度为1mol/l的cecl2溶液与含有白色絮状沉淀的溶液混合,在搅拌速度为200r/min的条件下反应3min,陈化40min后采用温度为85℃~90℃的热水洗涤5次,烘干,得到前驱体;③、将前驱体在温度为800℃的条件下煅烧3h,研磨得到石墨烯负载微米级氧化铈;所述石墨烯负载微米级氧化铈中石墨烯的质量分数为30%~90%;所述石墨烯负载微米级氧化铈中石墨烯的粒径为2~10μm、厚度为20~50nm,微米级氧化铈的粒径为2~5μm。其他与具体实施方式十或十一相同。具体实施方式十三:本实施方式与具体实施方式十至十二之一不同的是:步骤一中所述增强体中石墨烯的质量分数为50%。其他与具体实施方式十至十二之一相同。具体实施方式十四:本实施方式与具体实施方式十至十三之一不同的是:步骤一中所述增强体中石墨烯的质量分数为70%。其他与具体实施方式十至十三之一相同。具体实施方式十五:本实施方式与具体实施方式十至十四之一不同的是:步骤四中所述电子封装用sn-bi系复合钎料中增强体的质量分数为0.01%。其他与具体实施方式十至十四之一相同。具体实施方式十六:本实施方式与具体实施方式十至十五之一不同的是:步骤四中所述电子封装用sn-bi系复合钎料中增强体的质量分数为0.1%。其他与具体实施方式十至十五之一相同。具体实施方式十七:本实施方式与具体实施方式十至十六之一不同的是:步骤四中所述电子封装用sn-bi系复合钎料中增强体的质量分数为0.2%。其他与具体实施方式十至十六之一相同。采用以下实施例验证本发明的有益效果:实施例一:一种电子封装用sn-bi系复合钎料的制备方法是按以下步骤完成的:一、将增强体与20gsn-58bi钎料采用周期球磨的方式球磨2h~3h,得到混料;所述周期球磨中每个周期内球磨5min,停止5min,球磨速度为100r/min~200r/min;所述增强体为石墨烯负载纳米级氧化铈,且所述增强体中石墨烯的质量分数为30%;二、向混料中加入助焊膏并搅拌至膏状,得到混合物;三、将混合物倒入坩埚中,将坩埚于180℃条件下加热12min后,每3min搅拌1次,搅拌4次后倒入模具冷却;四、冷却后取出钎料块超声清洗3min,得到电子封装用sn-bi系复合钎料;所述电子封装用sn-bi系复合钎料中增强体的质量分数为0.005%;步骤一中所述石墨烯负载纳米级氧化铈的制备方法是按以下步骤进行的:①、将58mg六水合硝酸铈溶于水配成浓度为0.01mol/l的硝酸铈溶液;将10mg石墨烯分散于50ml无水乙醇中,超声处理1h得到石墨烯分散液;将石墨烯分散液与浓度为0.01mol/l的硝酸铈溶液混合,得到混合溶液;②、向混合溶液中逐滴加入氨水,调节ph值至9,再向其中加入h2o2,搅拌1h后转移到水热反应釜中,在温度为230℃的条件下加热24h,离心分离,先用去离子水清洗两次再采用无水乙醇清洗两次,在温度为60℃的条件下加热12h后研磨,得到石墨烯负载纳米级氧化铈,即为增强体;所述石墨烯负载纳米级氧化铈中石墨烯的粒径为2~10μm、厚度为20~50nm,纳米级氧化铈的粒径为10~20nm。实施例二:本实施例与实施例一的不同之处在于:步骤四中所述电子封装用sn-bi系复合钎料中增强体的质量分数为0.01%。其他与实施例一相同。实施例三:本实施例与实施例一的不同之处在于:步骤四中所述电子封装用sn-bi系复合钎料中增强体的质量分数为0.1%。其他与实施例一相同。实施例一、实施例二和实施例三得到的复合钎料细化了焊点的微观组织,对其进行硬度测试和力学性能测试,检测结果显示复合钎料的硬度提高了17.9%~43.9%;剪切强度提高了4.7%-19.5%。实施例四:一种电子封装用sn-bi系复合钎料的制备方法是按以下步骤完成的:一、将增强体与20gsn-58bi钎料采用周期球磨的方式球磨2h~3h,得到混料;所述周期球磨中每个周期内球磨5min,停止5min,球磨速度为100r/min~200r/min;所述增强体为石墨烯负载微米级氧化铈,且所述增强体中石墨烯的质量分数为90%;二、向混料中加入助焊膏并搅拌至膏状,得到混合物;三、将混合物倒入坩埚中,将坩埚于180℃条件下加热12min后,每3min搅拌1次,搅拌4次后倒入模具冷却;四、冷却后取出钎料块超声清洗3min,得到电子封装用sn-bi系复合钎料;所述电子封装用sn-bi系复合钎料中增强体的质量分数为0.1%;步骤一中所述石墨烯负载微米级氧化铈的制备方法是按以下步骤进行的:①、配制浓度为2.2mol/l的草酸溶液;将10mg石墨烯分散于50ml无水乙醇中,超声处理1h得到石墨烯分散液;将石墨烯分散液和浓度为2.2mol/l的草酸溶液混合,再向其中加入氨水调节ph至3,得到含有白色絮状沉淀的溶液;②、将34mgcecl2溶于去离子水中配制成浓度为1mol/l的cecl2溶液,将浓度为1mol/l的cecl2溶液与含有白色絮状沉淀的溶液混合,在搅拌速度为200r/min的条件下反应3min,陈化40min后采用温度为85℃~90℃的热水洗涤5次,烘干,得到前驱体;③、将前驱体在温度为800℃的条件下煅烧3h,研磨得到石墨烯负载微米级氧化铈,即为增强体;所述石墨烯负载微米级氧化铈中石墨烯的粒径为2~10μm、厚度为20~50nm,微米级氧化铈的粒径为2~5μm。实施例五:本实施例与实施例四的不同之处在于:步骤四中所述电子封装用sn-bi系复合钎料中增强体的质量分数为0.2%。其他与实施例四相同。实施例六:本实施例与实施例四的不同之处在于:步骤四中所述电子封装用sn-bi系复合钎料中增强体的质量分数为0.5%。其他与实施例四相同。实施例四、实施例五和实施例六的复合钎料细化了焊点的微观组织,对其进行硬度测试和力学性能测试,检测结果显示复合钎料的硬度提高了24.3%~31.1%;剪切强度提高了13.5%~17.2%。分别取sn-58bi钎料、实施例一至实施例六得到的复合钎料作为待测的钎料样品,进行钎料焊点微观组织观察、硬度测试以及剪切强度试验。结果如表1~表4。图1为sn-58bi钎料互连焊点组织形貌图;图2为实施例三得到的复合钎料的互连焊点组织形貌图;图3为实施例五得到的复合钎料的互连焊点组织形貌图;由三个图比较可以看出sn-58bi钎料微观组织中富sn相呈粗大的树枝状排列,富bi相成小面积块状或长条状分布,而加入石墨烯负载纳米氧化铈颗粒增强相和石墨负载微米级氧化铈颗粒增强相后,可以细化互连焊点组织,避免出现粗大相。表1sn-58bi钎料与实施例一、实施例二、实施例三得到的复合钎料的硬度值对比表钎料成分硬度(维氏hv)提高百分比(%)sn-58bi钎料20.7实施例一24.417.9实施例二24.719.5实施例三29.843.9表2sn-58bi钎料与实施例四、实施例五、实施例六得到的复合钎料的硬度值对比表钎料成分硬度(维氏hv)提高百分比(%)sn-58bi钎料20.7实施例四25.724.3实施例五27.131.1实施例六25.322.4表3sn-58bi钎料与实施例一、实施例二、实施例三得到的复合钎料的剪切强度对比表钎料成分剪切强度(mpa)提高百分比(%)sn-58bi钎料35.6实施例一37.24.7实施例二37.86.1实施例三42.519.5表4sn-58bi钎料与实施例四、实施例五、实施例六得到的复合钎料的剪切强度对比表钎料成分剪切强度(mpa)提高百分比(%)sn-58bi钎料35.6实施例四40.413.5实施例五41.717.2实施例六36.812.8从表1和表2可以看出复合钎料的硬度值都有不同程度的提高,说明增强相的加入可以提高钎料的硬度。从表3和表4可以看出复合钎料的剪切强度都有不同程度的提高,说明说明增强相的加入可以提高钎料的剪切强度。当前第1页12