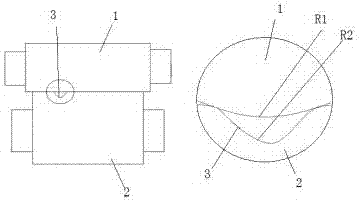
本发明涉及一种对冷轧支撑辊工作面进行快速局部修磨的方法,特别适用于在现场快速确定裂纹深度和辊面局部修磨,属于轧辊探伤与维修方法
技术领域:
。
背景技术:
:目前冶金企业在处理冷轧支撑辊工作面局部剥落或裂纹的问题时,大多采用轧辊工作面整体修磨的方法,采用整体磨削消除辊面的局部缺陷是对轧辊的巨大浪费,同时对轧辊进行整体磨削不仅占用了磨床时间,造成各种辅料资源的巨大损耗,也容易造成支撑辊备辊作业运转不畅。在轧辊维修工艺中,除了对轧辊整体进行磨削修复外,局部修磨也是处理局部缺陷的常见方法。采用局部修磨首先需要确定辊面缺陷的形状和深度,然后确定局部修磨的尺寸和形状。目前,对于冷轧支撑辊维修时应该如何掌握局部修磨的尺寸和形状,行业内没有明确认定,而确定辊面缺陷的形状和深度是采用渗透探伤的方法,但是现有的渗透探伤方法只能判定辊面是否存在裂纹,以及显示裂纹的长度、宽度和形状,而不能确定裂纹的深度,因此给采用局部修磨造成很大难度,也无法保证修磨的质量,影响轧辊上机后的正常使用。迄今为止,在轧辊表面缺陷维修中,整体磨削工艺会造成轧辊的浪费,局部修磨又存在难以保证质量的问题,因此如何对轧辊表面缺陷进行合理、高效的维修处理成为一直没有解决的难题,亟待技术人员突破常规,找到有效的解决方法。技术实现要素:本发明所要解决的技术问题是提供一种对冷轧支撑辊工作面进行局部修磨的方法,这种局部修磨方法针对冷轧支撑辊辊面的局部缺陷,可以解决辊面裂纹深度快速测量,并可以为局部修磨确定所需遵循的尺寸与形状,保证修磨的质量。解决上述技术问题的技术方案是:一种对冷轧支撑辊工作面进行局部修磨的方法,它采用以下步骤进行:步骤一确定辊面裂纹深度a.在辊面表面喷涂渗透剂,渗透剂渗入表面开口缺陷,对辊面表面进行清洗,使表面多余渗透剂除去,而缺陷中的渗透剂保留,再喷涂显像剂,在喷涂显像剂后2-5分钟内观察裂纹图案;b.根据显像出的裂纹的宽度判断裂纹的深度,判断标准如下:裂纹的宽度为0.5mm以下,裂纹的深度为0-1mm之间;裂纹的宽度在0.5-1mm之间,裂纹的深度为1-1.5mm之间;裂纹的宽度在1-1.5mm之间,裂纹的深度为1.5-4mm之间;裂纹的宽度在1.5-2mm之间,裂纹的深度为4-4.5mm之间;裂纹的宽度大于2mm,裂纹的深度大于4.5mm;步骤二确定局部修磨的尺寸及形状通过步骤一确定裂纹的长度、宽度和深度后,确定局部修磨的尺寸及形状,局部修磨为规则的圆弧形凹坑,凹坑直径大于裂纹的长度,凹坑深度大于裂纹的深度,凹坑深度与凹坑直径的关系应满足以下关系式:,其中h为凹坑深度,l为凹坑直径。步骤三进行局部修磨计算出修磨尺寸后,在辊面画出修磨的范围,进行修磨,打磨到预计深度后,需用渗透探伤,确定裂纹被磨削干净,最后进行细节处理,修磨凹坑内部和边部应是平滑过渡的曲面,不能有尖锐棱角。上述对冷轧支撑辊工作面进行局部修磨的方法,所述步骤一中根据显像出的裂纹的宽度判断裂纹的深度时,在每一个裂纹宽度范围内,裂纹的深度随着渗透剂颜色的加深而增加。上述对冷轧支撑辊工作面进行局部修磨的方法,所述步骤二中确定凹坑深度与凹坑直径的关系还要满足以下要求:支撑辊修磨凹坑在支撑辊轴向的曲率应大于相应部位中间辊的cvc曲率,并满足以下关系式:,其中r1为中间辊的cvc曲率半径。上述对冷轧支撑辊工作面进行局部修磨的方法,所述步骤二中确定凹坑深度与凹坑直径的关系还要满足以下要求:支撑辊修磨凹坑在支撑辊径向的曲率应大于纵向视图的中间辊的曲率,并满足以下关系式:,其中d为中间辊的直径;上述对冷轧支撑辊工作面进行局部修磨的方法,所述步骤二中确定凹坑深度与凹坑直径的关系还要满足以下要求:在轧制力的作用下,中间辊的弯曲挠度y小于修磨凹坑深度h,并满足以下关系式:,其中q为均布轧制力,e为轧辊弹性模量,i为轧辊截面惯性矩。本发明的有益效果是:本发明通过渗透剂对轧辊裂纹进行喷涂后显像,根据裂纹图像显示的裂纹的宽度和颜色确定裂纹的深度,然后通过公式计算出修磨凹坑直径和深度,为局部修磨轧辊提供了快速、有效的方法。本发明突破了常规的技术方案,创造性提出了一种仅利用渗透剂就能够确定裂纹深度的方法,同时创造性地为修磨凹坑提供了确定尺寸与形状要求的计算公式,大大提高了冷轧支撑辊的修磨效率,有效降低了辊耗和轧辊修复成本。本发明的局部修磨方法工具易得、操作简便、成本低廉,修复后轧辊具有良好的稳定性与可靠性,是一种简便、高效处理冷轧支撑辊工作面局部缺陷的方法,特别适用于生产单位在现场对冷轧支撑辊进行修磨处理,在行业内有极好的推广使用价值。附图说明图1是轧辊辊面修磨凹坑直径与深度示意图;图2是轧辊轴向视图与局部放大图;图3是轧辊纵向视图与局部放大图;图4是修磨凹坑部位中间辊的受力分析和挠曲变形示意图。图中标记如下:中间辊1、支撑辊2、凹坑3、凹坑深度h、凹坑直径l、中间辊cvc曲率半径r1、凹坑的曲率半径r2、中间辊直径d、中间辊弯曲挠度y、均布轧制力q。具体实施方式本发明的支撑辊工作面快速局部修磨法的实施步骤为:(1)利用渗透探伤确定裂纹深度;(2)确定局部修磨的尺寸及形状;(3)进行辊面修磨。步骤一利用渗透探伤确定裂纹深度冷轧支撑辊在外力的作用下产生的裂纹。发生轧制事故时,轧辊之间的接触应力突然增大,或者带钢卷入,造成支撑辊表面裂纹。通过观察冷轧支撑辊裂纹状态,总结渗透探伤图谱规律,创造性提供一种裂纹深度判断方法。渗透探伤的原理是利用毛细管现象使渗透剂渗入表面开口缺陷,经清洗使表面多余渗透剂除去,而使缺陷中的渗透剂保留,再利用显像剂的毛细管作用吸附出缺陷内余留渗透剂,而达到检验缺陷的目的。本方法需要在喷涂显像剂后2-5分钟内观察裂纹图案。裂纹图案特征与裂纹中余留渗透剂的多少有关。随着裂纹深度的加深,裂纹中余留渗透剂对裂纹深度的反应准确性逐渐降低。裂纹线条宽度可分为:0.5mm、1mm、1.5mm、2mm和>2mm的5个范围,不同宽度范围内的裂纹对应不同的裂纹深度:裂纹的宽度为0.5mm以下,裂纹的深度为0-1mm之间;裂纹的宽度在0.5-1mm之间,裂纹的深度为1-1.5mm之间;裂纹的宽度在1-1.5mm之间,裂纹的深度为1.5-4mm之间;裂纹的宽度在1.5-2mm之间,裂纹的深度为4-4.5mm之间;裂纹的宽度大于2mm,裂纹的深度大于4.5mm;同时,通过渗透剂显像后的裂纹线条颜色可分为浅紫色、紫色、深紫色三个层次,结合裂纹宽度和显像颜色可以更加精细地判断裂纹的深度,具体见下表。裂纹深度的判断方法为:线条宽度/mm线条颜色裂纹深度/mm0.5浅紫色0.50.5紫色11浅紫色11紫色1.51.5浅紫色1.51.5紫色3.51.5深紫色42深紫色4.5>2深紫色>5上述支撑辊不同深度的裂纹所对应的裂纹图案规律,裂纹深度在0-4.5mm范围内的准确性高。步骤二确定局部修磨凹坑的尺寸与形状本发明创造性提供了一种带有明确尺寸与形状要求的局部修磨法,可保证局部修磨后轧辊的正常使用,要求如下:图1显示,要求1:修磨凹坑截面形状必须为平滑过渡的圆弧,凹坑深度h与凹坑直径l的关系应满足:。图2显示,要求2:轧辊的轴向视图中,中间辊1具有cvc曲线,支撑辊2修磨凹坑3部位的曲率应大于相应部位中间辊1的cvc曲率。计算公式为:图3显示,要求3:轧辊径向视图中,修磨凹坑3的截面曲率应大于纵向视图里中间辊1的曲率。计算公式为:。图4显示,要求4:在轧制力的作用下,中间辊1的弯曲挠度y不应大于修磨凹坑3的深度h,满足,其中q为均布轧制力,e为轧辊弹性模量,i为轧辊截面惯性矩。步骤三局部修磨冷轧支撑辊局部修磨的工具为:渗透探伤剂、抛光机、深度卡尺、直尺和粉笔。计算出修磨尺寸后,在辊面画出修磨的范围。打磨到预计深度后,需用渗透探伤,确定裂纹被磨削干净。最后进行细节处理,修磨凹坑内部和边部应是平滑过渡的曲面,不能有尖锐棱角。在现场中,采用该方法处理的冷轧支撑辊,修磨凹坑直径l最大为150mm。本发明的一个实施如下:裂纹深度为4mm,长度为30mm,该处中间辊cvc曲率半径r1为3.05e5mm,中间辊直径d为510mm,支撑辊长度为1780mm。修磨凹坑深度h>4mm,凹坑直径长度l>30mm,同时还应满足以下要求:、、、若修磨凹坑直径l定为50mm,深度h应满足1.3mm<h<25mm。该处裂纹的深度为4mm,所以该处裂纹最后的修磨深度应在5mm<h<25mm的范围内。当前第1页12