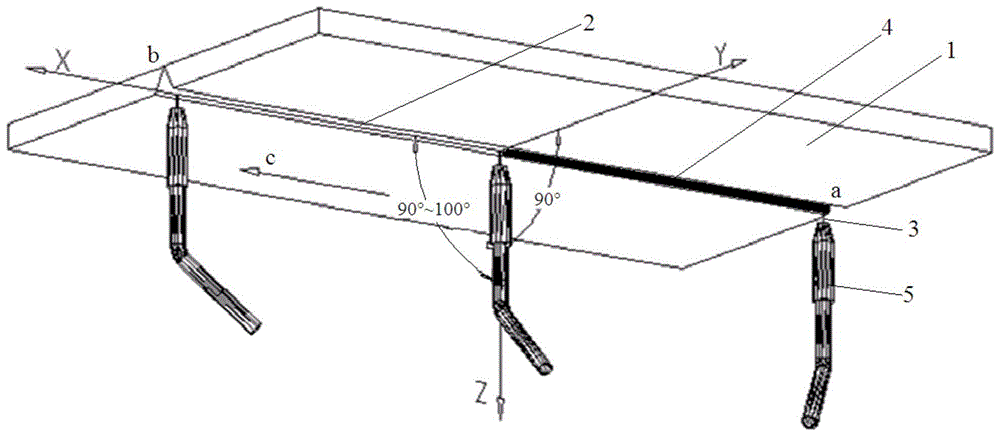
本申请属于焊接
技术领域:
,具体涉及一种用于板件的mag仰对接单面焊双面成型焊接方法。
背景技术:
:仰对接是所有焊接位置中操作难度最大的一种焊接接头形式。焊缝成型是在坡口一侧施焊,通常采用在焊缝熔池前方的坡口根部形成熔孔的操作方法,以此达到焊缝单面焊双面成型。在仰对接实际操作过程中,由于工件钝边薄、间隙大,加之熔滴自身重力及表面张力减小,液态金属受重力作用容易下坠,容易出现熔孔处被电弧烧损变大的情况,迫使停弧去进行修补,因此不能采取连弧焊接,造成焊缝背面形成凹陷、未焊透等缺陷,背面焊缝成型难以达到要求。填充层间内部难以控制,层间不易熔合,容易形成密集气孔和夹渣等缺陷。盖面层焊缝外观成型难以控制,容易形成表面成型不良、接头过高和脱节、咬边等缺陷。焊接质量得不到保障,造成极大浪费。技术实现要素:为解决上述技术问题,本发明提供了一种mag仰对接单面焊双面成型焊接方法,无需在焊缝熔池前方的坡口根部形成熔孔,可达到焊缝单面焊双面成型。实现本发明目的所采用的技术方案为,一种mag仰对接单面焊双面成型焊接方法,采用mag实心焊丝对具有坡口的板件进行仰对接焊接,所述坡口的装配间隙为1.5mm~2.5mm;该方法具体包括如下步骤:打底层焊接:采用连弧焊接,在焊接过程中,焊枪与焊接方向的倾角为90°~100°,利用电弧挺力,沿板件厚度方向击穿坡口钝边,并将熔池内的部分熔液顶向坡口背面,在所述坡口和所述坡口背面均形成熔池;所述熔池前方坡口处焊缝穿透后,在所述熔池前方坡口处未出现熔孔时沿焊接方向保持匀速推进,完成打底层的焊接;填充层焊接:采用连弧焊接;盖面层焊接:采用连弧焊接。进一步地,所述打底层焊接前,首先在所述板件坡口两端进行定位焊接。进一步地,所述定位焊接包括:在所述坡口两端的背面进行定位焊接,焊接长度为5mm~10mm。进一步地,所述打底层焊接,还包括:在所述坡口的端头起弧,起弧后直接沿所述焊接方向匀速推进,所述焊丝始终处于熔池前端1/4位置。进一步地,所述填充层焊接,包括:在所述坡口的端头起弧,起弧后焊枪作运条摆动,当电弧运行到坡口两侧时停留0.5s~1s。进一步地,所述填充层焊接的过程中,焊枪与焊接方向的倾角为80°~90°。进一步地,所述盖面层焊接,包括:在所述坡口的端头起弧,起弧后焊枪作运条摆动,回压熔池前端1/3~1/2处,当电弧运行到坡口两侧时停留0.5s~1s,熔合坡口棱角两侧1mm~2mm。进一步地,所述盖面层焊接的过程中,焊枪与焊接方向的倾角为80°~90°。进一步地,所述板件的对接部位预留有向板件背面弯曲的反变形角,且预留的所述反变形角不大于3°。进一步地,所述坡口钝边的厚度为0~1.5mm。由上述技术方案可知,本发明提供的mag仰对接单面焊双面成型焊接方法,通过改变焊枪角度,减小工件装配间隙以及改进操作工艺,无需在焊缝熔池前方的坡口根部形成熔孔,即可达到焊缝单面焊双面成型,具体工艺原理如下:首先,本申请改变了打底层的焊枪角度,焊枪与焊接方向的倾角为90°~100°,即焊枪处于前冲姿态,指向坡口的终焊端,可以利用mag焊接(熔化极活性气体保护电弧焊)的电弧挺力,沿板件厚度方向击穿坡口钝边,将熔池内的部分熔液顶向坡口背面,以在坡口和坡口背面均形成熔池,从而得到背面余高。再者,本申请采用mag连弧焊接,连弧焊接配合焊枪角度,可以使得熔池始终保持高温(铁水熔化状态),因此可以缩小坡口的装配间隙至1.5mm~2.5mm,且不要求熔池前方坡口处出现熔孔即可穿透坡口钝边,从而杜绝出现熔孔处被电弧烧损变大的情况。最后,由于缩小了坡口的装配间隙(现有技术中装配间隙为3mm~4mm,或更大),使得相同规格板材的坡口打底焊不仅提高了焊接速度,减小打底层焊缝厚度,减少了焊缝填充量,降低了焊接劳动强度;而且提高了焊缝熔敷效率,缩短了焊缝熔池的冷却时间,减小了板件的反变形量,使得预留的反变形角不大于3°。附图说明图1为本发明实施例中mag仰对接单面焊双面成型焊接方法的实施示意图;图2为本发明实施例中板件对接的结构示意图;图3为本发明实施例中焊缝的坡口分布图;图4为本发明实施例中箱型梁仰对接焊接结构示意图;附图标记说明:1-板件,11-钝边;2-坡口,21-装配间隙,22-棱角;3-焊丝;4-焊缝,41-打底层,42-填充层,43-盖面层,44-背面余高;5-焊枪;6-箱型梁。具体实施方式为了使本申请所属
技术领域:
中的技术人员更清楚地理解本申请,下面结合附图,通过具体实施例对本申请技术方案作详细描述。参见图1,在本发明实施例中,一种mag仰对接单面焊双面成型焊接方法,用于对具有坡口2的板件1进行仰对接焊接,板件1包括两块待连接的板件,焊接时两块板件应水平放置,也可具有一定的夹角,但是应该尽量避免两块板件错位(错边量≤1mm)。两块板件待连接的一端具有焊接用坡口2,该坡口2可以通过在两块板件临近的端面均设置斜面而形成(如图2所示),也可以由单块板件在两块板件临近的端面设置斜面而形成。其中,沿板件1厚度方向(图1中z轴方向)未开坡口的端面称为钝边11,本实施例中坡口2钝边的厚度为0~1.5mm;坡口斜面向下延伸与板件下表面形成的钝角称为棱角22,如图2所示。坡口2的开口角度与板件1的板厚有关,常规开角为60°。本实施例中,坡口2的装配间隙为1.5mm~2.5mm,例如1.5mm、1.8mm、2.0mm、2.3mm、2.5mm等。当装配间隙较大时,坡口钝边厚度可相应增加,例如采用2.5mm的装配间隙时,坡口钝边厚度为1mm~1.5mm。由图2可以看出,坡口2的开口沿板件1厚度方向向下逐渐增大,以便于进行仰位焊接。板件1在焊接前,一般在板件1的对接部位预留向板件1背面弯曲的反变形角,以抵消焊接造成的变形,本实施例中反变形角不大于3°。本实施例的mag仰对接单面焊双面成型焊接方法,采用mag焊(熔化极活性气体保护电弧焊,简称气保焊)配合mag实心焊丝3进行仰对接焊接,参见图3,包括打底层41、填充层42和盖面层43的焊接,具体工艺如下:s1、打底层41焊接:采用直线运条方法进行连弧焊接。起弧时在坡口2的端头(即图1中始焊端a)起弧,起弧后不需摆动,直接沿焊接方向(图1中箭头c所指方向)匀速推进,焊丝3始终处于熔池前端1/4位置(熔池呈椭圆形,长轴沿焊接方向,朝向终焊端b的方向为前端)。参见图1,在焊接过程中,焊枪5与焊接方向的倾角为90°~100°,例如90°、92°、94.5°、96°、98°、100°等,与焊缝4宽度方向(图1中y轴方向)的夹角为90°。起弧后,利用电弧挺力,沿板件1厚度方向击穿钝边11,并将熔池内的部分熔液顶向坡口2背面,以在坡口2和坡口背面均形成熔池。其中,判断坡口背面是否形成熔池可以通过坡口背面发出“噗噗”声音(焊缝穿透时发出的声音)来判断。该“噗噗”的声音仅是示例性的说明,仅是用以说明坡口钝边已经熔透,但坡口钝边熔透的声音因实际情况而异。打底层41焊接过程中,在熔池前方坡口2处未出现熔孔时沿焊接方向保持匀速推进,即熔池前方坡口处焊缝穿透后(例如听到焊缝穿透声后),无需待坡口处出现熔孔就保持向前匀速推进,直至完成打底层41的焊接。由于本方法不需要待熔池前方坡口处出现熔孔就保持向前匀速推进,因此也杜绝出现熔孔处被电弧烧损变大的情况。在一优选实施方案中,在打底层41焊接前,需要在坡口2两端进行定位焊接。定位焊接可以在坡口侧(板件下表面)进行,也可以在坡口背面进行。若在坡口侧进行定位焊接,则定位焊接会在坡口2两端形成一定焊缝厚度,相当于预先进行了一定长度的打底焊,在进行打底焊工序时,为控制打底焊厚度,起弧点应该设置在定位焊接焊缝的末端,这样就无法实现坡口2端头起弧。而在起弧时,板件是常温状态,因此坡口不容易烧透,背面焊缝不易成型。本实施例中,在坡口2两端的背面进行定位焊接,焊接长度为5mm~10mm。坡口2两端的背面进行定位焊接,相当于在坡口2两端的背面形成余高。由于坡口中并无焊缝,因此可以从坡口2端头起弧,在打底焊在5mm~10mm定位焊接段进行的过程中,板件1焊接处已达到高温,因此在打底焊焊接至定位焊接段末端位置时,可以轻易将坡口背面击穿,使得背面的打底焊与定位焊接融为一体,保证背面焊缝成型质量。s2、填充层42焊接:采用锯齿形运条方法进行连弧焊接。起弧时在坡口2的端头起弧,起弧后焊枪5作小弧度锯齿形运条摆动,摆动时中间过渡速度要快,两边要稍作停留,即当电弧运行到坡口2两侧时停留0.5s~1s,既能保证焊缝之间熔合良好,又能避免焊缝正面金属液滴下坠形成焊瘤。填充层42焊缝表面距离坡口棱角处留有1~2mm的盖面层余量,注意不要将棱角22烧损。在其他实施例中,填充层焊接也可采用月牙形运条方法、反月牙形运条方法、三角形运条方法等运条方法,本申请不做限制。在填充层42焊接过程中,焊枪5与焊接方向的倾角为80~90°,与焊缝宽度方向的夹角为90°。即焊枪处于后冲姿态,指向坡口的始焊端a,焊枪角度控制焊接速度,焊枪5反向姿态可以控制填充层42的焊接速度慢于打底层41。由于越靠近坡口棱角22,坡口面越宽、板厚越厚,焊接速度慢可以延长熔池停留时间,而停留时间决定熔池温度,因而可以保证填充层焊缝两侧与母材充分熔合,以及打底层41与填充层42焊缝之间充分熔合。s3、盖面层43焊接:采用月牙形运条方法进行连弧焊接。起弧时在坡口2的端头起弧,起弧后焊丝3带动熔池快速向焊道两侧摆动,避免焊缝正面形成焊瘤。焊丝3在熔池内作月牙形运条摆动,回压(压弧)熔池前端1/3~1/2处,即焊丝3摆动始终在熔池前端1/3~1/2处,相应的焊条向前推移距离即为熔池长度的1/6。由于熔池表面在焊接方向上呈斜面,即熔池高度从前(终焊端b侧)往后(始焊端a侧)递增,与已凝固焊缝相接处厚度最大,因此将运条限制在熔池前端1/3~1/2处,即熔池前半部分,可使得盖面层43与填充层42焊缝之间充分熔合。在其他实施例中,盖面层焊接也可采用锯齿形运条方法、反月牙形运条方法、三角形运条方法等运条方法,本申请不做限制。当电弧运行到坡口2两侧时停留0.5s~1s,熔合坡口2棱角两侧1mm~2mm,能避免焊缝两侧产生坡口未填满和咬边缺陷。收弧时,要填满焊缝收弧弧坑,防止产生弧坑未填满和裂纹,从而保证盖面层43焊缝成型美观。在盖面层43焊接的过程中,焊枪5与焊接方向的倾角为80°~90°,优选90°,与焊缝宽度方向的夹角为90°,相应效果同填充层42。应用实例:某公司在长大型特种车辆生产过程中应用本实施例的mag仰对接单面焊双面成型焊接方法,具体应用于箱型梁焊接。参见图4,箱型梁6作为车辆主要承载部分,坡口2位于底部板件1上,焊缝要求全熔透。现有技术在箱型梁6焊接时,常出现因作业空间狭小造成仰对接焊缝反面无法清根,导致焊缝出现焊接缺陷。采用本实施例的mag仰对接单面焊双面成型焊接方法后,达到较好的焊缝单面焊双面成型效果。具体工艺方法及工艺参数如下:(一)试板母材性能分析试板均为高强度耐候钢q450nqr1的材料,板厚均为10mm。q450nqr1属于高强度耐大气腐蚀钢,该材料性能优越主要表现在强度高,耐大气腐蚀强度好的优点,q450nqr1的化学成分与力学性能分别见表1和表2。表1q450nqr1化学成分(%)表2q450nqr1力学性能(二)焊材性能分析为了使焊接接头具有与母材相匹配的力学性能,选用高强度焊丝牌号为th550nq-ⅱ,直径为焊丝的化学成分及力学性能分别见表3和表4。表3th550nq-ⅱ化学成分(%)表4th550nq-ⅱ力学性能(三)装配工艺要求坡口钝边厚度0~0.5mm;定位焊在板件两端坡口反面,长度5~10mm;装配间隙1.5mm;预留的反变形量:2°~3°;错边量:≤1mm。(四)焊接技术介绍1、焊接设备:焊机选用气体保护焊机krⅱ-500,选用直流反接的连接方式。焊机状态应良好,能在所要求的电流范围内提供稳定的电弧,熔深大,飞溅小,而且安全可靠。2、焊前清理:将工件正、反面两侧20mm范围内,及坡口表面的油、锈、水和氧化物等杂质彻底清除干净,直至露出金属光泽。将坡口内侧点固焊打磨平整,靠工件中心一端打磨至斜坡状,焊枪上焊丝前端小球状氧化物剪除。3、焊接工艺参数:合理的焊接工艺参数是决定焊接质量优劣的重要保证,不仅对焊缝的成形起到关键作用,而且对焊缝组织产生影响。焊前必须对焊机进行调试,在试板上试焊。将焊接电流、电弧电压和气体流量等焊接参数合理匹配,具体参数见表5。表-5焊接工艺参数焊接层次焊接电流i/a电弧电压u/v打底焊110~12017~18填充焊130~14018~19盖面焊120~13018~19保护气体流量:15~20l/min;焊丝伸出长度:10~15mm;打底焊焊接速度:170~190mm/min。(五)焊接流程参见图1,包括打底层41、填充层42和盖面层43的焊接,具体工艺如下:s1、打底层41焊接:采用直线运条方法进行连弧焊接。起弧时在坡口2的端头起弧,起弧后不需摆动,直接沿焊接方向匀速推进,焊丝3始终处于熔池前端1/4位置。在焊接过程中,焊枪5与焊接方向的倾角为90°~100°,与焊缝4宽度方向的夹角为90°,利用电弧挺力,沿板件1厚度方向击穿钝边11,并将熔池内的部分熔液顶向坡口2背面,在坡口2和坡口2背面均形成熔池。打底层41焊接过程中,在熔池前方坡口2处未出现熔孔时沿焊接方向保持匀速推进,完成打底层41的焊接。s2、填充层42焊接:采用锯齿形运条方法进行连弧焊接。起弧时在坡口2的端头起弧,起弧后焊枪5作小弧度锯齿形运条摆动,摆动时中间过渡速度要快,两边要稍作停留,即当电弧运行到坡口2两侧时停留0.5s~1s,既能保证焊缝之间熔合良好,又能避免焊缝正面金属液滴下坠形成焊瘤。在填充层42焊接过程中,焊枪5与焊接方向的倾角为80~90°,与焊缝宽度方向的夹角为90°。填充层42焊缝表面距离坡口棱角处留有1~2mm的盖面层余量,注意不要将棱角22烧损。s3、盖面层43焊接:采用月牙形运条方法进行连弧焊接。起弧时在坡口2的端头起弧,起弧后焊丝3带动熔池快速向焊道两侧摆动,避免焊缝正面形成焊瘤。焊丝3在熔池内作月牙形运条摆动,回压(压弧)熔池前端1/3~1/2处,当电弧运行到坡口2两侧时停留0.5s~1s,熔合坡口2棱角1mm~2mm,能避免焊缝两侧产生坡口未填满和咬边缺陷。收弧时,要填满焊缝收弧弧坑,防止产生弧坑未填满和裂纹,从而保证盖面层43焊缝成型美观。在盖面层43焊接的过程中,焊枪5与焊接方向的倾角90°,与焊缝宽度方向的夹角为90°。经测定,坡口正面焊缝焊缝高低和宽窄均匀一致,无咬边,成型美观;焊缝背面余高0.5~1mm,焊接质量得到保证。通过上述实施例,本发明具有以下有益效果或者优点:本发明提供的mag仰对接单面焊双面成型焊接方法,此焊接技术在长大型特种车辆生产及反面无法清根的箱型梁焊接时得到成功运用。通过减小工件装配间隙,改变焊枪角度及操作方法,无需在焊缝熔池前方的坡口根部形成熔孔,可达到焊缝单面焊双面成型。该焊接方法可简化操作动作,降低操作难度和劳动强度,可大幅降低电焊工的操作难度,能让操作工在较短时间熟悉并掌握该操作方法,同时将此焊接技术向大众化方向推进。尽管已描述了本申请的优选实施例,但本领域内的普通技术人员一旦得知了基本创造性概念,则可对这些实施例作出另外的变更和修改。所以,所附权利要求意欲解释为包括优选实施例以及落入本申请范围的所有变更和修改。显然,本领域的技术人员可以对本申请进行各种改动和变型而不脱离本申请的精神和范围。这样,倘若本申请的这些修改和变型属于本申请权利要求及其等同技术的范围之内,则本申请也意图包含这些改动和变型在内。当前第1页1 2 3