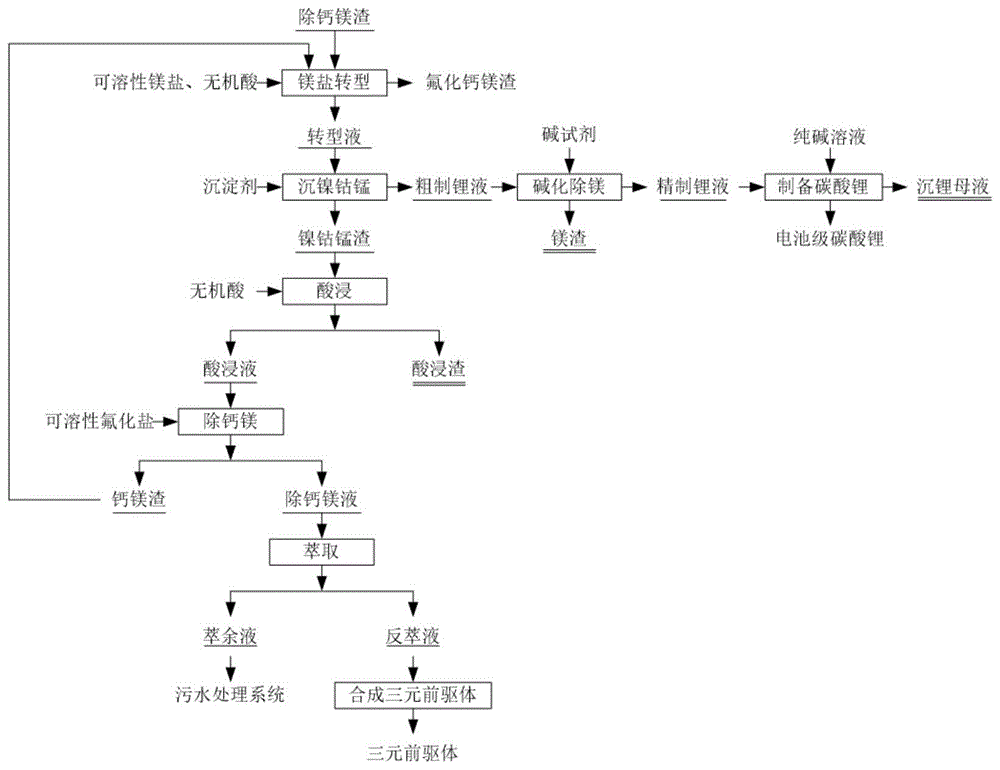
本发明涉及废旧锂电池湿法回收领域,特别是一种除钙镁渣回收锂及制备三元前驱体材料的方法。
背景技术:
:锂电池因其具有能量密度高,开路电压高,充放电速度快,寿命长等优点,被广泛用于手机,电脑,相机等数码产品。随着我国大力发展新能源汽车产业,近年来,锂电池产业呈现爆发式增长。根据ggii调研数据显示,2017年中国动力电池产量44.5gwh,占全球总量的50%以上,我国已成为全球最大的锂电池生产和消费市场。锂电池在经过近千次充放电循环后,其内部工作离子将逐渐丧失活性。锂电池日益广泛地应用势必会产生大量的废旧电池。若随意丢弃不但对环境带来威胁,而且造成金属资源的浪费,因此对废旧锂电池的回收利用具有十分重要的意义。废旧锂电池回收工艺分为前端预处理和后端化学回收。而目前废旧锂电池后端化学回收主要以湿法为主。以三元材料电池为例,湿法回收工艺广泛采取:还原酸浸-净化除杂-萃取分离工艺流程。在净化除杂工序中,其关键在于去除浸出液中的钙、镁杂质。专利cn106505225a通过加入可溶性氟化盐,使钙、镁以难容性的氟化钙和氟化镁的形式去除。但由于钴、镍、锰、锂的氟化物的属于微溶性物质,在除钙镁的同时势必会有大量的镍钴锰金属以氟化物的形式沉淀出来。此种除钙镁渣中含有大量的有价金属镍、钴、锰、锂等,而文中只涉及到了锂的回收,大大降低了有价金属的回收率。本专利在回收锂制备碳酸锂的同时进一步回收了有价金属镍、钴、锰制备三元前驱体材料,实现了资源的综合利用,且本发明的镍钴锰的回收率均在98%以上,锂的回收为96%以上。技术实现要素:为了解决上述存在的问题,本发明公开了一种除钙镁渣回收锂及制备三元前驱体材料的方法,包括如下步骤:(1)镁盐转型,将除钙镁渣与镁离子浓度为30-100g/l的镁盐制成浆液,加入无机酸,调节体系ph为1.0-5.0,加热搅拌1-5h,过滤,得到转型液和氟化钙镁渣;(2)沉钴镍锰,向步骤(1)中的转型液中加入沉淀剂,控制体系温度为25-100℃,将转型液中的钴镍锰以氢氧化镍钴锰沉淀的形式与锂镁分离,得到镍钴锰渣和粗制锂液;(3)酸浸镍钴锰渣,将步骤(2)中的镍钴锰渣和自来水调浆,控制液固质量比为2-5:1,制得浆料,向浆料中加入无机酸,调节ph为0-5,搅拌反应0.5-1h,得到酸浸液和酸浸渣;(4)除钙镁:向步骤(3)得到的酸浸液中加入可溶性氟化盐,控制体系温度50-100℃,搅拌反应0.5-2h后过滤,得到除钙镁液和除钙镁渣;(5)萃取:用有机萃取剂萃取除钙镁液中的金属钴镍锰,再经反萃得到含钴镍锰的反萃液;(6)合成前驱体:向步骤(5)的反萃液中配加钴镍锰可溶性盐,加入氢氧化钠和氨水,控制体系ph至9-12,保持反应温度为60-70℃搅拌1-5h得到球形氢氧化镍钴锰;(7)烘干:步骤(6)中所述球形氢氧化镍钴锰经100-500℃高温烘干2-5h得到三元前驱体材料。按上述方案,步骤(1)中所述除钙镁渣中钴、镍、锰、锂的质量百分比分别为1-10%。作为本发明的优选方案,包括至少一种以下技术特征:所述除钙镁渣与镁盐制浆的液固质量比为2-5:1;所述加热搅拌的温度为50-100℃;所述加热搅拌的搅拌速率为:100-400rpm/s;所述镁盐为硫酸镁、硝酸镁、氯化镁中的至少一种;所述镁盐的加入量为氟化钙镁渣中钴、镍、锰、锂全部转换成可溶性盐按化学反应方程式计算所需理论用质量的1.1-2.0倍。作为本发明的优选方案,步骤(2)中,所述沉淀剂为氢氧化钠、氢氧化钾、氨水中的至少一种;所述沉淀剂的加入量为转型液中钴、镍、锰全部转换成氢氧化物按化学反应方程式计算所需理论用质量的1.0-2.0倍。作为本发明的优选方案,步骤(1)和(3)中的所述无机酸为硫酸、硝酸、盐酸中的至少一种。作为本发明的优选方案,步骤(4)中包括至少一种以下技术特征:所述可溶性氟化盐为氟化钠、氟化氨中的至少一种;控制反应体系ph为0-5;搅拌速率为100-400rpm/s。作为本发明的优选方案,所述步骤(5)中的除钙镁液ph值为3.0-6.0,所述有机萃取剂为p507、磺化煤油的有机混合物,其体积比为1:1-5,皂化度为40%-70%。作为本发明的优选方案,所述步骤(6)中按镍钴锰摩尔比为8:1:1或6:2:2或5:2:3配入所需的钴镍锰硫酸盐制备三元前驱体材料,所述三元前驱体材料为ni0.8co0.1mn0.1(oh)2型、或ni0.6co0.2mn0.2(oh)2型或ni0.5co0.2mn0.3(oh)2型。作为本发明的优选方案,还包括以下步骤:s1:碱化除镁,向步骤(2)中的粗制锂液中加入碱式剂,调节溶液ph值至10.0-13.0,过滤,得到精制锂液和氢氧化镁渣;s2:制备碳酸锂,向步骤s1中的精制锂液中加入碳酸钠溶液,使锂以碳酸锂的形式沉淀出来,经洗涤、烘干后制得电池级碳酸锂。作为本发明的优选方案,所述步骤s1中碱式剂为氢氧化钠、氢氧化钾、氢氧化锂、氨水中的至少一种。工作原理:所述步骤(1)中涉及的反应方程式为:cof2+mg2+→mgf2↓+co2+;nif2+mg2+→mgf2↓+ni2+;mnf2+mg2+→mgf2↓+mn2+;lif+mg2+→mgf2↓+li+所述步骤(2)中涉及的反应方程式为:2oh-+co2+=co(oh)2↓;2oh-+ni2+=ni(oh)2↓2oh-+mn2+=mn(oh)2↓所述步骤(3)中涉及的反应方程式为:mn(oh)2+2h2+=mn2++2h2oco(oh)2+2h2+=co2++2h2oni(oh)2+2h2+=ni2++2h2o所述步骤(4)中涉及的反应方程式为:mg2++2f-=mgf2↓ca2++2f-=caf2↓所述步骤(6)中涉及的反应方程式为:co2++oh-=co(oh)2↓ni2++oh-=ni(oh)2↓mn2++oh-=mn(oh)2↓所述步骤s1中涉及的反应方程式为:2oh-+mg2+=mg(oh)2↓所述步骤s2中涉及的反应方程式为:2li++co32-=li2co3↓本发明具有的有益效果是:(1)本发明是以废旧锂电池浸出液除钙镁渣为回收对象,首先对除钙镁渣进行镁盐转型,得到镍钴锰锂溶液,经过沉镍钴锰,酸浸,除钙镁,萃取,再经过合成反应得到球形氢氧化镍钴锰、烘干制备得到镍钴锰相应摩尔比的三元前驱体材料。其沉镍钴锰后的粗制锂液,先后加入碱式剂将粗制锂液中的锂与镁进行分离,碱化后的精制锂液可制备电池级碳酸锂。(2)本发明方法工艺简单,能耗低,安全稳定,过程中钴镍锰与锂的分离效率高,且粗制锂液中镍钴的含量为100ppm以下,镍钴锰渣中锂的含量为0.1%以下,各有价金属综合回收率高,镍钴锰的收率均在95%以上;锂转型收率为95%以上。制备的碳酸锂纯度高达99.61%,品质好,可达到电池级碳酸锂标准。(3)传统的氟化锂以及除钙镁渣回收锂未涉及有价金属镍钴的回收,本发明特点在于通过引入沉镍钴工序,从而实现了镍、钴与锂的分离,达到资源的综合回收利用、且有价金属的回收率高达95%以上。附图说明图1是本发明的工艺流程图。具体实施方式下面结合附图中的图1对本发明中的一种除钙镁渣回收锂及制备三元前驱体材料的方法进一步详细说明。一种除钙镁渣回收锂及制备三元前驱体材料的方法,参考图1,工艺流程如下:(1)镁盐转型,将除钙镁渣与镁离子浓度为30-100g/l的镁盐制成浆液,加入无机酸,调节体系ph为1.0-5.0,加热搅拌1-5h,过滤,得到转型液和氟化钙镁渣;所述除钙镁渣与镁盐制浆的液固质量比为2-5:1;所述加热搅拌的温度为50-100℃;所述加热搅拌的搅拌速率为:100-400rpm/s;所述镁盐为硫酸镁、硝酸镁、氯化镁中的至少一种;所述镁盐的加入量为氟化钙镁渣中钴、镍、锰、锂全部转换成可溶性盐按化学反应方程式计算所需理论用质量的1.1-2.0倍。(2)沉钴镍锰,向步骤(1)中的转型液中加入沉淀剂,控制体系温度为25-100℃,将转型液中的钴镍锰以氢氧化镍钴锰沉淀的形式与锂镁分离,得到镍钴锰渣和粗制锂液。所述沉淀剂为氢氧化钠、氢氧化钾、氨水中的至少一种;所述沉淀剂的加入量为转型液中钴、镍、锰全部转换成氢氧化物按化学反应方程式计算所需理论用质量的1.0-2.0倍。(3)酸浸镍钴锰渣,将步骤(2)中的镍钴锰渣和自来水调浆,控制液固质量比为2-5:1,制得浆料,向浆料中加入无机酸,调节ph为0-5,搅拌反应0.5-1h,得到酸浸液和酸浸渣;(4)除钙镁:向步骤(3)得到的酸浸液中加入可溶性氟化盐,控制体系温度50-100℃,体系ph为0-5,搅拌反应0.5-2h后过滤,得到除钙镁液和除钙镁渣;所述可溶性氟化盐为氟化钠、氟化氨中的至少一种;搅拌速率为100-400rpm/s。(5)萃取:用有机萃取剂萃取除钙镁液中的金属钴镍锰,再经反萃得到含钴镍锰的反萃液;本步骤中的除钙镁液ph值为3.0-6.0,所述有机萃取剂为p507、磺化煤油的有机混合物,其体积比为1:1-5,皂化度为40%-70%。(6)合成前驱体:向步骤(5)的反萃液中配加钴镍锰可溶性盐,加入氢氧化钠和氨水,控制体系ph至9-12,保持反应温度为60-70℃搅拌1-5h得到球形氢氧化镍钴锰;(7)烘干:步骤(6)中所述球形氢氧化镍钴锰经100-500℃高温烘干2-5h得到三元前驱体材料。按上述方案,步骤(1)中所述除钙镁渣中钴、镍、锰、锂的质量百分比分别为1-10%。所述步骤(1)和(3)的无机酸为硫酸、硝酸、盐酸中的至少一种。作为本发明的优选方案,所述步骤(6)中按镍钴锰摩尔比为8:1:1或6:2:2或5:2:3配入所需的钴镍锰硫酸盐制备三元前驱体材料,所述三元前驱体材料为ni0.8co0.1mn0.1(oh)2型或ni0.6co0.2mn0.2(oh)2型或ni0.5co0.2mn0.3(oh)2型。作为本发明的优选方案,还包括以下步骤:s1:碱化除镁,向步骤(2)中的粗制锂液中加入碱式剂,调节溶液ph值至10.0-13.0,过滤,得到精制锂液和氢氧化镁渣;s2:制备碳酸锂,向步骤s1中的精制锂液中加入碳酸钠溶液,使锂以碳酸锂的形式沉淀出来,经洗涤、烘干后制得电池级碳酸锂。作为本发明的优选方案,所述步骤s1中碱式剂为氢氧化钠、氢氧化钾、氢氧化锂、氨水中的至少一种。实施例1(1)镁盐转型:取除钙镁渣200kg与0.54m3镁离子浓度为77g/l氯化镁溶液制成浆液,镁盐的加入量为钙镁渣中钴、镍、锰、锂全部浸出所需理论用质量的1.1倍,然后用20l盐酸将体系的ph值调至3.0。开启加热,保持体系温度为95℃搅拌1h后过滤,搅拌速率为200rpm/s,得到0.52m3转型液。转型液主要成分分析结果见表1如下:表1转型液主要成分分析结果元素conimnlicamgfeal含量g/l12.8029.0315.0628.53.2130.0010.002(2)沉镍钴锰:按上述得到的0.52m3转型液中钴、镍、锰全部转换成氢氧化镍钴锰按化学反应方程式计算所需理论用质量的1.1倍加入氢氧化钠45kg,使钴、镍、锰以氢氧化物的形式与锂、镁分离。替换搅拌0.5h后过滤,得0.46m3粗制锂液和130kg镍钴锰渣。粗制锂液主要成分分析结果见表2如下:表2粗制锂液主要成分分析结果元素conimnlicamgfeal含量g/l0.010.050.0832.192.913.20.0010.002(3)酸浸:往反应釜中加入130kg步骤(2)中的沉镍钴锰渣和0.4m3的自来水制成浆液,用51kg浓盐酸将浆料ph调节至ph为1.0。搅拌0.5h过滤,得到0.42m3酸浸液。(4)除钙镁:向步骤(3)得到的酸浸液中加入17.8kg氟化钠,控制体系温度90℃搅拌反应2h后过滤,搅拌速率为300rpm/s,得到0.4m3除钙镁液。经测定除钙镁液中钙含量为0.0002g/l,镁含量为0.0005g/l。(5)萃取:将步骤(4)中的除钙镁液ph值调至3.0,p507/磺化煤油(体积比为1:3),皂化度为65%的有机萃取剂,经8级逆流萃取,5级反萃后得反萃液0.32m3,其中各成分的结果见表4。表4反萃液中主要成分分析结果元素conimncamgfeal含量/(g/l)20.3845.9923.490.0010.0015未检出0.0002(6)合成前驱体:按设计的镍、钴、锰摩尔比为5:2:3。向步骤(7)中反萃液中配加硫酸镍和硫酸锰。向反应釜中加入氢氧化钠和氨水,控制体系ph至11.5,保持反应温度为65℃搅拌4h得到球形氢氧化镍钴锰。(7)烘干:将本实施例制备的球形氢氧化镍钴锰经150℃高温烘干5h得到ni0.5co0.2mn0.3(oh)2型三元前驱体51.02kg,其从回收到成品镍钴锰的总回收率均为97%。其中钴的回收率为:98.0%;镍的回收率为:97.5%;锰的回收率为:96.0%。实施例2本实施例是在实施例1的基础上做了进一步优化,具体是:s1:碱化除镁:向步骤(2)中得到的0.46m3粗制锂液中加入0.1m332wt%氢氧化钠溶液,调节溶液ph值至12.0。搅拌1h过滤,得0.52m3精制锂液。精制锂液主要成分分析结果见表3如下:表3精制锂液主要成分分析结果元素conimnlicamgfeal含量g/l0.0001未检出0.000528.470.120.00010.00050.0002s2:制备碳酸锂:将精制锂液升温至95℃,然后缓慢加入300g/l的碳酸钠溶液0.37m3,搅拌0.5h过滤,搅拌速率为250rpm/s。滤渣再经洗涤、烘干得到75.77kg碳酸锂产品。本实施例中碳酸锂产品技术指标见表13、14。实施例3(1)镁盐转型:取除钙镁渣200kg与0.6m3镁离子浓度为61g/l硫酸镁溶液制成浆液,镁盐的加入量为钙镁渣中钴、镍、锰、锂全部浸出所需理论用量的1.2倍,然后用20l浓硫酸将体系的ph值调至1.0。开启加热,保持体系温度为95℃搅拌1h后过滤,搅拌速率为200rpm/s,得到0.63m3转型液。转型液主要成分分析结果见表5如下:表5转型液主要成分分析结果元素conimnlicamgfeal含量g/l6.314.63.222.11.18.50.0020.001(2)沉淀钴镍锰:按步骤(1)的0.63m3转型液中钴、镍、锰全部转换成氢氧化镍钴锰按化学反应方程式计算所需理论用量的1.1倍加入氢氧化钠23kg,使钴、镍、锰以氢氧化物的形式与锂、镁分离。替换搅拌0.5h后过滤,得0.59m3粗制锂液和80kg镍钴锰渣。粗制锂转型液主要成分分析结果见表6如下:表6粗制锂液主要成分分析结果元素conimnlicamgfeal含量g/l0.020.020.4423.131.0516.380.0010.002(3)酸浸:往反应釜中加入80kg步骤(2)中的沉镍钴锰渣和0.3m3的自来水制成浆液,用25kg浓硫酸将浆料ph调节至2.0。搅拌0.5h过滤,搅拌速率为250rpm/s,得到0.35m3酸浸液。(4)除钙镁:向步骤(3)得到的酸浸液中加入5.6kg氟化钠,控制体系温度90℃搅拌反应2h后过滤,搅拌速率为300rpm/s,得到0.32m3除钙镁后液。经测定除钙镁后液中钙含量为0.0003g/l,镁含量为0.0004g/l。(5)萃取:将步骤(4)中的除钙镁后液ph值调至3.0,p507/磺化煤油(体积比为1:3),皂化度为65%的有机萃取剂,经8级逆流萃取,5级反萃后得反萃液0.28m3,其中各成分的结果见表8。表8反萃液中主要成分分析结果元素conimncamgfeal含量/(g/l)13.7831.476.980.0010.0015未检出0.0002(6)合成前驱体:按设计的镍、钴、锰摩尔比为8:1:1。向步骤(6)中反萃液中配加硫酸镍和硫酸锰。向反应釜中加入氢氧化钠和氨水,控制体系ph至11.5,保持反应温度为65℃搅拌4h,搅拌速率为150rpm/s,得到球形氢氧化镍钴锰。(7)烘干:将本实施例制备的球形氢氧化镍钴锰经150℃高温烘干5h得到5:3:2型三元前驱体60.26kg,其从回收到成品镍钴锰的总回收率均为97%。其中钴的回收率为:97.2%;镍的回收率为:95.8%;锰的回收率为:97.0%。实施例4本实施例是在实施例3的基础上做了进一步优化,具体是:s1:碱化除镁:向步骤(2)中得到的0.59m3粗制锂液中加入0.08m332%氢氧化钠溶液,调节溶液ph值至12.0。搅拌1h过滤,搅拌速率为200rpm/s,得0.56m3精制锂液。粗制锂转型液主要成分分析结果见表7如下:表7精制锂液主要成分分析结果元素conimnlicamgfeal含量g/l0.00040.00010.000823.880.080.00010.00040.0003s2:制备碳酸锂:将合格锂液升温至90℃,然后缓慢加入220g/l的碳酸钠溶液0.46m3,搅拌0.5h过滤,搅拌速率为200rpm/s,滤渣再经洗涤、烘干得到71.29kg碳酸锂产品。本实施例中碳酸锂产品技术指标见表13、14。实施例5(1)镁盐转型:取除钙镁渣200kg与0.5m3镁离子浓度为82.12g/l硝酸镁溶液制成浆液,镁盐的加入量为钙镁渣中钴、镍、锰、锂全部浸出所需理论用量的1.2倍,然后用15l浓硫酸将体系的ph值调至4.0。开启加热,保持体系温度为85℃搅拌1h后过滤,搅拌速率为400rpm/s,得到0.54m3转型液。转型液主要成分分析结果见表9如下:表9转型液主要成分分析结果元素conimnlicamgfeal含量g/l11.221.039.6326.60.7512.030.0040.003(2)沉淀钴镍锰:按步骤(1)的0.54m3转型液中钴、镍、锰全部转换成氢氧化镍钴锰按化学反应方程式计算所需理论用量的1.05倍加入氢氧化钾45.95kg,使钴镍锰以氢氧化物的形式与锂、镁分离。在25℃下搅拌0.5h后过滤,搅拌速率为350rpm/s,得0.52m3粗制锂液和115kg镍钴锰渣。粗制锂液主要成分分析结果见表10如下:表10粗制锂液主要成分分析结果元素conimnlicamgfeal含量g/l0.080.070.2127.070.5614.080.0030.002(3)酸浸:往反应釜中加入115kg步骤(2)中的沉镍钴锰渣和0.4m3的自来水制成浆液,用18kg硝酸将浆料ph调节至1.5。搅拌0.5h过滤,搅拌速率为200rpm/s,得到0.43m3酸浸液。(4)除钙镁:向步骤(3)得到的酸浸液中加入7.8kg氟化钠,控制体系温度85℃搅拌反应2h后过滤,搅拌速率为200rpm/s,得到0.41m3除钙镁后液。经测定除钙镁后液中钙含量为0.0002g/l,镁含量为0.0001g/l。(5)萃取:将步骤(4)中的除钙镁后液ph值调至4.0,p507/磺化煤油(体积比为1:3),皂化度为70%的有机萃取剂,经8级逆流萃取,5级反萃后得反萃液0.22m3,其中各成分的结果见表12。表12反萃液中主要成分分析结果元素conimncamgfeal含量/(g/l)27.0850.9923.140.0020.002未检出0.0004(6)合成前驱体:按设计的镍、钴、锰摩尔比为6:2:2。向步骤(6)中反萃液中配加硫酸镍和硫酸锰。向反应釜中加入氢氧化钠和氨水,控制体系ph至11.0,保持反应温度为70℃搅拌4h,搅拌速率为200rpm/s,得到球形氢氧化镍钴锰。(7)烘干:将本实施例制备的球形氢氧化镍钴锰经150℃高温烘干5h得到6:2:2型三元前驱体46.51kg,其从回收到成品镍钴锰的总回收率均为98%。其中钴的回收率为:98.5%;镍的回收率为:98.8%;锰的回收率为:97.9%。实施例6本实施例是在实施例5的基础上做了进一步优化,具体是:s1:碱化除镁:向步骤(2)中得到的0.59m3粗制锂液中加入0.08m332%氢氧化钠溶液,调节溶液ph值至12.5。搅拌1h过滤,搅拌速率为150rpm/s,得0.53m3精制锂液。精制锂液主要成分分析结果见表11如下:表11精制锂液主要成分分析结果元素conimnlicamgfeal含量g/l未检出未检出0.000226.560.220.00030.00010.0003s2:制备碳酸锂:将精制锂液加热至95℃,然后缓慢加入240g/l的碳酸钠溶液0.49m3,搅拌0.5h过滤,搅拌速率为200rpm/s,滤渣再经洗涤、烘干得到73.55kg碳酸锂产品。本实施例中碳酸锂产品技术指标见表13、14。根据实施例2、4、6对镍、钴、锰、锂的回收率值见下表13:表13实施例2、4、6对镍、钴、锰、锂的回收率本发明实施例1、3、5碳酸锂的化学成分分析见表14:表14电池级碳酸锂产品技术指标从表13、14可知,实施例1、3、5制得的碳酸锂的主含量均高于99%,满足ys/t582—2006电池级标准要求,其中,实施例1制得的碳酸锂的主含量高达99.61%,品质高;实施例2、4、6对镍、钴、锰、锂的回收率值均高于95%,总回收率高于97%,其中实施例6中:总回收率高达98.5%,镍的回收率高达98.80%,经实验测试还发现,本发明中粗制锂液中镍钴的含量均为100ppm以下,镍钴锰渣中锂的含量均为0.1%以下;传统的氟化锂以及除钙镁渣回收锂未涉及有价金属镍钴的回收,本发明通过引入沉镍钴工序,从而实现了镍、钴与锂的分离,达到资源的综合回收利用、且有价金属的回收率高。当前第1页12