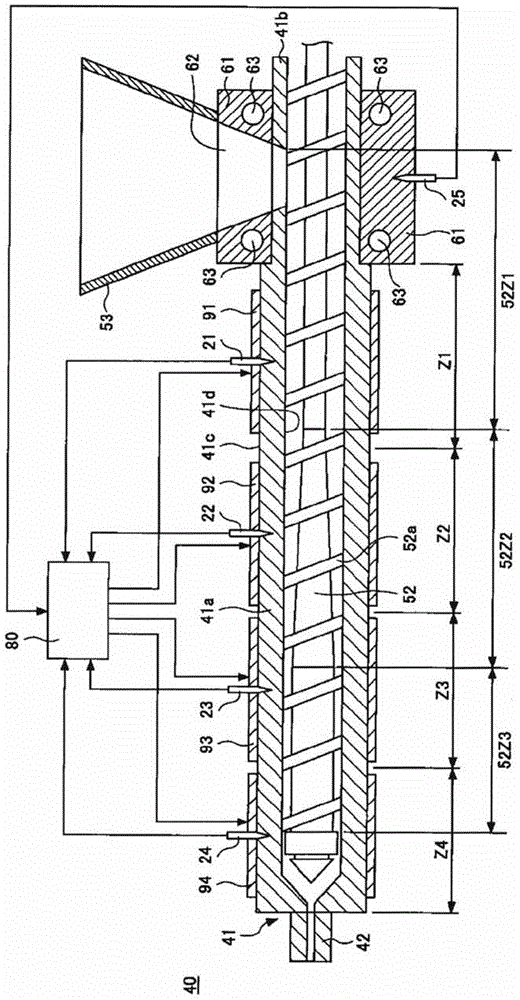
本发明涉及注射成型机。
背景技术:注射成型机具备向模具装置内注射熔融的树脂的注射装置。模具装置由定模以及动模构成,合模时在定模与动模之间形成型腔空间。注射装置将在缸内熔融的树脂从设置在缸的前端的喷嘴注射,并填充到模具装置内的型腔空间中。在型腔空间中被冷却固化的树脂在开模后作为成型品取出。注射装置包括在缸内旋转自如且在轴向移动自如地配设的螺杆。从料斗向螺杆的一端部中供给树脂材料。在螺杆旋转时,螺杆的刮板(螺纹牙)运动,填充到螺杆的螺纹槽内的树脂从料斗侧传送到喷嘴侧。缸的喷嘴侧的温度被维持成树脂的熔融温度。另一方面,缸的料斗侧的温度被维持成树脂不软化熔融的温度,以使得不会发生树脂的架桥(结块)。为此,缸的料斗侧被内部具有制冷剂流路的冷却部件冷却。缸包括在冷却部件与喷嘴之间延伸的缸主体部。缸主体部沿轴向被划分为多个区,在每个区中均设置加热源以及温度传感器。基于各温度传感器的测量温度与各温度传感器的测量位置处的目标温度之差反馈控制多个加热源(例如参照专利文献1)。专利文献1:日本特开平11-227019号公报各温度传感器以探针测量各区的温度,将测量的温度作为各区的代表温度进行管理。因此,对缸的径向或轴向的温度分布不进行管理,对缸内壁的缸轴向的温度分布也不进行管理。图11是表示以往的缸内壁的缸轴向的温度分布的图。图11中,以实线表示目标温度分布、虚线表示取得的温度分布的一例,点划线表示取得的温度分布的其他例,黑圆表示缸轴向的温度传感器的测量位置。在温度传感器的测量位置附近,由于进行反馈控制,目标温度与取得的温度(实际温度)大致一致。而从温度传感器的测量位置离开的位置,有可能目标温度与取得的温度(实际温度)较大偏离。由于缸内壁与树脂接触,因此在缸内壁的温度分布偏离目标温度分布时,树脂的温度过高或过低。在树脂的温度过高时,树脂因热而变质。而在树脂的温度过低时,树脂的流动性恶化,注射装置的负荷过大。
技术实现要素:本发明即是鉴于上述问题而做出的,其目的是提供一种能够管理缸内的树脂温度的注射成型机。为了解决上述问题,基于本发明的一实施方式的注射成型机的特征在于,具备:缸,被供给树脂材料,多个加热源,加热该缸;多个温度传感器,检测上述缸的不同位置的温度;以及基于该各温度传感器的测量温度与该各温度传感器的测量位置处的目标温度之差,控制上述多个加热源,预先设定上述缸内壁的缸轴向的目标温度分布,上述控制装置基于上述目标温度分布计算上述各温度传感器的测量位置处的目标温度,使用计算出的该目标温度进行上述多个加热源的控制。发明的效果:根据本发明,能够提供一种能够管理缸内的树脂的温度的注射成型机。附图说明图1是表示本发明第一实施方式的注射成型机的概略的图。图2是表示第一实施方式的注射成型机的主要部分的图。图3是第一实施方式的目标温度的设定的说明图。图4是表示本发明第二实施方式的注射成型机的主要部分的图。图5是表示图4的缸中的预先设定目标温度的位置的第1例的图。图6是表示图4的缸的预先设定目标温度的位置的第2例的图。图7是表示图4的缸的预先设定目标温度的位置的第3例的图。图8是本发明第二实施方式的缸的热传导方程式的说明图。图9是本发明第二实施方式的缸内的物质的热传导方程式的说明图。图10是表示本发明第二实施方式的加热源的热的流出流入的式子的说明图。图11是表示现有的缸内壁的缸轴向的温度分布的图。符号说明10注射成型机21~24温度传感器30模具装置32定模33动模40注射装置41缸41a缸主体部42喷嘴61冷却部件(冷却部)80控制装置91~94加热器(加热源)具体实施方式以下,参考附图对用于实施本发明的方式进行说明,在各附图中对相同或对应的结构附加相同或对应的符号并省略说明。另外,将注射装置的树脂的注射方向设为前方,将与注射方向相反的方向设为后方来进行说明。(第一实施方式)图1是表示本发明第一实施方式的注射成型机的概略的图。图1表示合模的状态。注射成型机10具备:框架11;固定在框架11上的固定压板12;和从固定压板12延伸的多根(例如四根)连接杆16。并且,注射成型机10还具备与固定压板12对置配置且能够沿连接杆16移动(图中的左右方向移动)地配设的可动压板13。可动压板13的与固定压板12的对置面上安装有动模33,在固定压板12的与可动压板13的对置面上安装有定模32。由定模32与动模33构成模具装置30。通过可动压板13相对固定压板12接触分离来进行闭模、合模以及开模。合模状態的动模33与定模32之间形成型腔空间C。注射成型机10还具备将缸41内熔融的树脂从喷嘴42注射并填充到模具装置30内的型腔空间C中的注射装置40。注射装置40具备注射用马达43。注射用马达43的旋转被传递给滚珠丝杠轴44。通过滚珠丝杠轴44的旋转前进后退的滚珠丝杠螺母45被固定在压力板46上。压力板46能够沿固定在基架(未图示)上的引导杆47、48移动。压力板46的前进后退运动经由轴承49、测力传感器50、注射轴51传递给螺杆52。螺杆52被旋转自如且沿轴向移动自如地配设在缸41内。从料斗53向螺杆52的后端部供给树脂颗粒(树脂材料)。经由带或带轮等连结部件54将计量用马达55的旋转运动传递给注射轴51。即,由计量用马达55旋转驱动注射轴51,由此将螺杆52旋转。在计量工序中,驱动计量用马达55,使螺杆52旋转,将供给到螺杆52的后端部的树脂颗粒输送到螺杆52的前方。在该过程中,树脂颗粒软化熔融。由于在螺杆52的前方贮存有树脂,因此,螺杆52后退。在注射工序中,驱动注射用马达43,使螺杆52前进,推压树脂从喷嘴42注射。树脂经由形成在定模32上的浇道S而被压入到定模32与动模33之间形成的型腔空间C中。推压树脂的力通过测力传感器50作为反力被检测。即,检测来自喷嘴42的树脂的注射压力。检测到的注射压力被输入到控制装置80中。并且,在型腔空间C内树脂因冷却而热收缩,所以为了补充热收缩量的树脂,在保压工序中,树脂的注射压力被保持为预定的压力。压力板46上安装有用于检测螺杆52的移动量的位置检测器57。位置检测器57的检测信号被输入到控制装置80中。位置检测器57的检测信号也可以用于检测螺杆52的移动速度。注射用马达43以及计量用马达55也可以分别为伺服马达,具备用于检测转速的编码器43a、55a。由编码器43a、55a检测到的转速被分别输入到控制装置80中。控制装置80基于编码器43a、55a的检测结果反馈控制注射用马达43以及计量用马达55。控制装置80控制注射成型机10的各种动作。控制部80由微型计算机等构成,例如具有CPU、存储器、计时器、计数器、输入接口以及输出接口等。图2是表示第一实施方式的注射成型机的主要部分的图。缸41的后部41b被插入到冷却部件(冷却部)61中,并通过冷却部件61冷却。冷却部件61以及缸41上形成有树脂供给口62。经由树脂供给口62从料斗53向缸41内供给的树脂颗粒被填入到螺杆52的螺纹槽内。若螺杆52旋转,则螺杆52的刮板(螺纹牙)52a运动,将螺杆52的螺纹槽内的树脂颗粒向前方输送。缸41的后部41b的树脂被冷却到不软化或不熔化的温度。冷却部件61上所形成的制冷剂流路63中被供给有冷却水等制冷剂,并通过制冷剂冷却缸41。温度传感器25的前端被埋设在冷却部件61中,温度传感器25的检测信号被输入到控制装置80中。缸41包括在冷却部件61与喷嘴42之间延伸的缸主体部41a。在缸主体部41a的外壁41c上设置有多个加热源(例如加热器)91~94,将缸主体部41a加热到预定的温度。在缸主体部41a内向前方移动的树脂被来自加热源91~94的热加热。树脂伴随向缸主体部41a的前方的移动而成为熔融状态。在缸主体部41a的前端部,树脂成为完全熔融的状态。并且,伴随在螺杆52的前方蓄积熔融树脂,螺杆52后退。在螺杆52后退预定距离、螺杆52的前方蓄积预定量的树脂时,停止螺杆52的旋转。并且,在停止螺杆52的旋转的状态下,螺杆52前进,由此,熔融树脂从喷嘴42向模具装置30内注射。螺杆52沿轴向从后方(树脂供给侧)到前方(喷嘴侧)被划分为供给部52Z1、压缩部52Z2、计量部52Z3。供给部52Z1为供给树脂并向前方输送的部分。压缩部52Z2为一边将所供给的树脂进行压缩一边熔融的部分。计量部52Z3为将熔融的树脂按一定量计量的部分。螺杆52的螺纹槽的深度在供给部52Z1处深,在计量部52Z3处浅,在压缩部52Z2中越朝向前方越浅。缸主体部41a沿轴向被划分为多个(例如4个)区Z1~Z4,在区Z1~Z4上分别设置加热源91~94。向各加热源91~94的供给电流被分别控制,缸主体部41a按各区Z1~Z4被加热。各加热源91~94被设置成包围缸主体部41a的外周。虽然未图示,但是可以在喷嘴42的外周设置加热源。在区Z1~Z4上分别设置温度传感器(例如热电偶)21~24。各温度传感器21~24的前端被埋设在缸主体部41a中,各温度传感器21~24以针尖测量温度。各温度传感器21~24的检测信号被输入到控制装置80。控制装置80基于各温度传感器21~24的测量温度与其目标温度之差控制多个加热源91~94。向各加热源91~94的供给电流被控制例如PID控制为使与各加热源91~94对应的区Z1~Z4的温度传感器21~24的测量温度与其目标温度之差变小。另外,向各加热源91~94的供给电流也可以基于与各加热源91~94的区Z1~Z4邻接的区的温度传感器的测量温度进行控制。考虑缸轴向的热流通量,能够将各温度传感器的测量位置处的温度迅速地收敛到目标温度。并且,温度传感器21~24在各区Z1~Z4上分别各设置一个,但是也可以各设置多个。一个区上所设置的多个温度传感器既可以设在缸轴向不同的位置,也可以设在缸径向不同的位置。接着,基于图3对各温度传感器的测量位置处的目标温度的设定方法进行说明。图3是第一实施方式的目标温度的设定方法的说明图。图3(a)表示实际的缸主体部的形状,图3(b)表示传热模型用的缸主体部的形状,图3(c)表示缸主体部内壁的温度分布。图3(c)中,实线表示由使用者设定的目标温度分布,点划线表示由传热模型计算出的最适合的温度分布。在本实施方式中,首先,使用者操作注射成型机10的输入装置(例如键盘)82,设定缸内壁的缸轴向的目标温度分布而非各温度传感器21~24的测量位置处的目标温度。另外,目标温度分布也可以读取控制装置80的存储器等记录介质中预先记录的内容来进行设定。为了简化后述的计算,对缸主体部41a进行目标温度分布的设定,对于缸后部41b也可以省略。缸后部41b的外周被冷却部件61包围,所以缸后部41b的温度能够成为大致一定。表示利用输入装置82的使用者的操作的操作信号被输入到控制装置80,并被记录在存储器等记录介质中。目标温度分布将缸主体部内壁41d沿缸轴向划分为多个划区,对每个划区输入温度来设定。使用者可以将各划区的位置与各划区的设定温度建立对应的图像显示在显示装置84中,以使得一边确认设定温度的划区的位置一边设定各划区的温度。划区的个数(即使用者进行温度设定的位置的个数)比在缸轴向上隔开间隔配设的温度传感器21~24的个数(图3中四个)多。代替各划区的温度,可以输入表示目标温度分布的函数。划区个数实质上增加。多个划区中,缸主体部41a的从后端(冷却部件61侧的端)到前方的预定距离以内的划分中,只要树脂不软化熔融即可,作为目标温度分布,设定温度的上限值,但不设定温度的下限值。即,在从缸主体部41a的后端向前方的预定距离MZ以内的位置设定使缸内壁的温度为设定温度以下的目标温度分布。接着,控制装置80基于记录在记录介质中的目标温度分布,计算各温度传感器21~24的测量位置处的目标温度。目标温度的计算中,使用基于各加热源91~94的温度能够计算缸主体部41a的温度分布的传热模型。另外,也可以使用基于各加热源91~94的温度以及冷却部件61的温度能够计算缸主体部41a的温度分布的传热模型。传热模型用的缸主体部41a的形状如图3(b)所示为近似的圆筒形状。缸主体部41a的温度由于在缸主体部41a的中心线的周围大致均匀,因此,能够基于用下述式(1)表示的二维热扩散方程式做成传热模型。式1上述式(1)中,z表示缸轴向的位置坐标,r表示缸径向的位置坐标,T表示坐标(z,r)处的温度,t表示时刻。z坐标的原点为缸主体部41a的前端面,r坐标的原点为缸主体部41a的中心线。预先测量缸主体部41a的尺寸(内径、外径、轴向长度)、热扩散率α(m2/s),并存储到控制装置80的存储器等中。缸主体部41a的尺寸等的温度依存性非常小,可以使用室温(25℃)下测量的数据。另外,如式(1)所示,热扩散率α能够由热传导率λ(J/(s·m·℃))、密度ρ(kg/m3)、以及定压比热Cp(J/(kg·℃))计算。因此,代替热扩散率α,可以将热传导率λ、密度ρ以及定压比热Cp存储到控制装置80的存储器中。并且,定压比热Cp(J/(kg·℃))也可以通过热容量C(J/℃)与质量W(kg)之比(Cp=C/W)计算。因此可以代替定压比热Cp将热容量C以及质量W存储到控制装置80的存储器中。为了求解上述式(1),给出边界条件。例如,能够对缸主体部41a与各加热源91~94之间的边界B1~B4、缸主体部41a与外气之间的边界B5、以及缸主体部41a与树脂之间的边界B6适用热传递条件。并且,能够对缸主体部41a的后端B7适用温度固定条件。另外,作为边界条件可以使用热流通量边界条件,边界条件的种类可以为一般的种类。边界条件中使用的数据由边界条件的种类决定。例如,上述边界条件的情况可以使用(1)缸主体部41a与各加热源91~94之间的热传导率(W/(m2·℃))、(2)各加热源91~94的温度、(3)缸主体部41a与外气之间的热传导率(W/(m2·℃))、(4)外气的温度、(5)缸主体部41a与树脂之间的热传导率(W/(m2·℃))、(6)树脂的温度、(7)缸主体部41a的后端温度(冷却部件61的温度)。这些数据可以由使用者输入,也可以预先存储在控制装置80的存储器等中。但是,在解决后述的凸优化问题时,(2)各加热源91~94的温度作为应求解的变量被使用。另外,作为应求解的变量,可以追加(7)缸主体部41a的后端B7的温度(冷却部件61的温度)。上述式(1)为了将缸主体部41a分割为多个有限要素而被离散化,做成线性系统(联立线性微分方程式)。通过求解作成的线性系统的稳态解,得到缸主体部41a的温度分布的稳态解,并能够得到缸主体部内壁41d的温度分布的稳态解。离散化的方法可以为一般的方法。控制装置80作成在缸主体部内壁41d的温度分布的稳态解与目标温度分布之间的差越小数值越好(变小)的评价函数。评价函数可以为凸优化问题中所使用的一般的函数。作为凸优化问题的制约条件,可以使用使用者设定的温度上限值。即,在从缸主体部41的后端B7向前方的预定距离MZ以内的位置,缸主体部内壁41d的温度为设定温度以下这样的制约条件加到凸优化问题中。控制装置80通过二次规划法求解评价函数的最优解(各加热源91~94的稳定状态下的温度的最优解)。接着,控制装置80将得到的最优解作为边界条件再次求解线性系统的稳态解。由此,得到缸主体部41a的温度分布的最优的稳态解。并且,参照预先记录在记录介质中的表示各温度传感器21~24的测量位置的数据(r坐标、z坐标),求出各温度传感器21~24的在测量位置处的最适合温度。采用该最适合的温度作为目标温度。控制装置80使用最适合温度即目标温度控制多个加热源91~94。由此,能够使缸主体部内壁41d的实际的温度分布尽可能地接近目标温度分布。由于缸主体部内壁41d的实际的温度分布不能测量,因此,可以代替其而在显示装置84上图像显示缸主体部内壁41d的温度分布的最优的稳态解。为了比较,可以同时在显示装置84上图像显示目标温度分布。例如,可以在显示装置84上图像显示图3(c)所示的信息。使用者能够比较并目视确认。如以上所说明的那样,根据本实施方式,各温度传感器21~24的测量位置处的目标温度能够基于由使用者设定的缸内壁的目标温度分布来计算。因此,能够管理缸41内的树脂的温度。另外,使用者进行温度设定的位置的个数比温度传感器21~24的个数(图3为四个)多。由于也考虑温度传感器彼此之间的位置处的温度来确定各温度传感器的测量位置处的目标温度,因此,实际的温度分布与目标温度分布之差小,能够高精度管理缸41内的树脂的温度。并且,从缸主体部41a的后端(冷却部件61侧的一端)B7到前方预定距离MZ以内的位置,作为目标温度分布,设定温度的上限值,不设定温度的下限值,因此设定温度有灵活性。这时由于在接近冷却部件61的区域中只要树脂不软化熔融,就不会在树脂的输送上产生不良影响。接近冷却部件61的区域中目标温度分布的条件降低,因此相对应地能够使树脂熔融的区域处的实际的温度分布与目标温度分布之差小,能够使熔融的树脂的流动性最优化。(第二实施方式)上述第一实施方式中预先设定缸内壁的缸轴向的目标温度分布。在本实施方式中,预先设定缸以及/或缸内部的预定位置处的目标温度。图4是表示本发明第二实施方式的注射成型机的主要部分的图。注射成型机具备缸141、在缸141内输送树脂的螺杆152、对缸141进行加热的多个加热源H1~H4和冷却缸141的后部的冷却部件161。螺杆152被旋转自如且沿轴向移动自如地配设在缸141内。随着螺杆152的旋转,沿着形成在螺杆152上的螺旋状的槽将树脂颗粒向前方输送。加热源H1~H4加热缸141而使缸141内的树脂熔融。作为加热源H1~H4例如可以使用从外侧加热缸141的加热器。加热器被设置成围绕缸141的外周。多个加热源H1~H4沿缸141的轴向排列,将缸141在轴向上分为多个区(图4中四个区Z1~Z4)而分别加热。为了使各区Z1~Z4的温度成为设定温度而通过控制装置180反馈控制多个加热源H1~H4。各区Z1~Z4的温度由温度传感器S1~S4测量。另外,喷嘴142上也可以设置加热源。控制装置180基于各温度传感器S1~S4的测量位置的测量温度与目标温度之间的温度偏差控制多个加热源H1~H4。向各加热源H1~H4的供给电流被控制例如PID控制成使上述温度偏差变小。控制装置180基于缸以及/或缸内部的预定位置的目标温度计算各温度传感器S1~S4的在测量位置处的目标温度,使用计算出的该目标温度进行多个加热源H1~H4的控制。目标温度的计算中使用传热模型。图5表示图4的缸中预先设定目标温度的位置的第1例。图6表示图4的缸中的预先设定目标温度的位置的第2例。图7表示图4的缸中的预先设定目标温度的位置的第3例。在图5~图7中,黑圆表示预先设定目标温度的位置。设定图5所示的预先设定目标温度的位置与第一实施方式同样,为缸内壁,且沿缸轴向隔开间隔排列。能够以缸内壁的温度成为所希望的温度的方式计算各温度传感器S1~S4的测量位置处的目标温度。由此,能够管理缸内壁附近的树脂的温度。图6所示的预先设定目标温度的位置为距缸外壁的深度与各温度传感器S1~S4的测量位置相同深度的位置,沿缸轴向隔开间隔排列。因此,能够管理温度传感器S1~S4的测量位置间的温度。图7所示的预先设定目标温度的位置为缸内部,且沿缸轴向隔开间隔排列。能够以缸内部的树脂的温度成为所希望的温度的方式计算各温度传感器S1~S4的测量位置处的目标温度,并能够管理缸内部的树脂的温度。另外,预先设定目标温度的位置可以在缸或缸内部的任何位置。例如,预先设定目标温度的位置可以为距缸外壁的深度比温度传感器的测量位置更接近缸内壁的位置。并且,预先设定目标温度的位置也可以为在缸轴向隔开间隔排列,也可以在缸的径向上隔开间隔排列。并且,预先设定目标温度的位置可以在缸和缸内部的两者上,例如可以为图6的黑圆所示的位置和图7中用黑圆所示的位置双方。预先设定目标温度的位置可以预先确定也能够由使用者选择。传热模型为能够基于各加热源H1~H4的温度计算缸141(包括缸主体部141a)以及缸141内部的温度分布的式子。例如,传热模型为基于缸141的热传导方程式、缸141内的物质(以下也称为“缸内物质”)的热传导方程式、以及各加热源Hk(图4中k=1、2、3、4)中的表示热流出流入的式子的式子。以下,参照图8~图10对各式进行说明。在各式中,相同记号为相同意思。图8为本发明第二实施方式的缸热传导方程式的说明图。缸的热传导方程式例如由下述式(2)等表示。式(2)中,为了简化式子,将缸141的温度近似为在缸141的中心线周围大致均匀,二维化。另外,在后述的式(3)以及式(4)中也同样二维化。式2上述式(2)中,x表示缸轴向(前后方向)的位置坐标,y表示缸径向的位置坐标,Rout表示缸141的外周面的半径,T(t)表示时刻t的坐标(x,y)处的温度,α表示缸141的热扩散率(m2/s)。x坐标的原点为缸141的前端面,从前端面朝向后端面x越大。并且,y坐标的原点为缸141的外周面,从外周面越朝向内周面y越大。将上述式(2)离散化,将定义上述式(2)的区域(即缸141)分割成多个微小区域(要素)。将坐标(i×Δx,j×Δy)的微小区域的时刻t的温度设为Ti,j(t)。i为0~m的整数、j为0~n的整数。将缸141的轴向长度设为L时,L=m×Δx的式子成立。并且,将缸141的内周面的半径设为Rin、缸141的外周面的半径设为Rout时,Rout-Rin=n×Δy的式子成立。缸141的微小区域的个数(m+1)×(n+1)被设定为能解缸141的任意位置的温度。微小区域的升温速度(温度Ti,j(t)的一次微分)由相对于该微小区域的热量的流出流入确定,并由该微小区域的温度Ti,j(t)和与该微小区域邻接的微小区域的温度之间的温度差等确定。因此,微小区域的温度Ti,j(t)的一次微分成为微小区域的温度Ti,j(t)、以及邻接的微小区域的温度Ti-1,j(t)、Ti+1,j(t)、Ti,j-1(t)、Ti,j+1(t)的函数(其中,i为1~m-1的整数、j为1~n-1的整数)。缸后端(坐标x=m×Δx)中的微小区域的温度Tm,j(t)通过冷却部件161被保持成与外气的温度Ta大致相同的温度。因此,作为缸后端与外气之间的边界条件,能够给出温度固定条件。即,Tm,j(t)=Ta的式子成立。另外,缸后端的温度Tm,j(t)可以被保持成比外气的温度Ta高的预定温度Tc(Tc>Ta)。另一方面,作为缸前端(坐标x=0)与外气之间的边界条件、缸外周(坐标y=0)与外气之间的边界条件、缸外周(坐标y=0)与加热源Hk之间的边界条件以及缸内周(坐标y=n×Δy)与缸内的物质之间的边界条件,给出热流通量边界条件。因此,缸前端(坐标x=0)的微小区域的升温速度(温度T0,j(t)的一次微分)由该微小区域的温度、与该微小区域邻接的微小区域的温度、外气的温度Ta、缸141与外气之间的热传导系数(W/(m2·℃))等决定。同样,缸外周(坐标y=0)中与外气接触的微小区域的升温速度(温度Ti,0(t)的一次微分)由该微小区域的温度、与该微小区域邻接的微小区域的温度、外气的温度Ta、缸141与外气之间的热传导系数(W/(m2·℃))等决定。并且,缸外周(坐标y=0)中、与加热源Hk接触的微小区域的升温速度(温度Ti,0(t)的一次微分)由该微小区域的温度、与该微小区域邻接的微小区域的温度、加热源Hk的温度Thk(t)、缸141与加热源Hk之间的的热传导系数(W/(m2·℃))等决定。另外,缸外周与冷却部件161之间的边界条件可以与缸外周和加热源Hk之间的边界条件相同。缸内周(坐标y=n×Δy)的微小区域的升温速度(温度Ti,n(t)的一次微分)由该微小区域的温度、与该微小区域邻接的微小区域的温度、缸内物质的温度Tfli(t)、缸内物质与缸141之间的热传导系数(W/(m2·℃))等决定。对于缸内物质的温度Tfli(t)后述。另外,缸内物质可以为例如成型开始前的缸141的升温时的空气,成型时的树脂,中途变化也可以。图9是本发明第二实施方式的缸内物质的热传导方程式的说明图。缸内物质的热传导方程式例如用下述的式(3)等表示(其中,i为1~m-1的整数)。式(3)中,为了使式子简单化,缸内物质的温度分布在缸141的径向均匀。式3上述式(3)中,Tfli(t)表示坐标x=i×Δx的微小空间的时刻t的温度(℃),ρin表示缸内物质的密度(kg/m3)、cin表示缸内物质的定压比热(J/kg)。q1表示在坐标x(x=i×Δx)的微小区域中从前方(图9中左侧)的微小区域流入的每单位时间的流入热量(W)。流入热量q1成为微小区域间的温度差(Tfli-1(t)-Tfli(t))的函数。该温度差越大,流入热量q1越增加。流入热量q1的计算中使用缸内物质的热传导率(W/(m·℃))等。q2表示从坐标x(x=i×Δx)的微小区域向后方(图9中右侧)的微小区域流出的每单位时间的流出热量(W)。流出热量q2成为微小区域间的温度差(Tfli(t)-Tfli+1(t))的函数。该温度差越大,流出热量q2越增加。流出热量q2的计算中使用缸内物质的热传导率(W/(m·℃))等。q3表示坐标x(x=i×Δx)的微小区域中每单位时间从缸141流入的热量(W)。该热量q3成为缸内物质与缸141之间的温度差(Ti,n(t)-Tfli(t))的函数。该温度差越大,热量q3越增加。在热量q3的计算中,使用缸内物质与缸141之间的热传导系数(W/(m2·℃))等。缸内物质的后端(坐标x=m×Δx)的温度Tflm(t)通过冷却部件161被保持成与外气的温度Ta大致相同的温度。因此,作为缸内物质的后端与外气之间的边界条件,给出温度固定条件。即,Tflm(t)=Ta的式子成立。另外,缸内物质的后端的温度Tflm(t)可以被保持成比外气的温度Ta高的预定温度Tc(Tc>Ta)。另一方面,作为缸内物质的前端(坐标x=0)与外气之间的边界条件,给出热流通量边界条件。因此,缸内物质的前端(坐标x=0)的升温速度(温度Tfl0(t)的一次微分)由该微小区域的温度、与该微小区域邻接的微小区域的温度、外气的温度Ta、缸内物质与外气之间的热传导系数(W/(m2·℃))、缸内物质与缸之间的热传导系数(W/(m2·℃))等决定。图10为表示本发明第二实施方式的加热源的热量流出流入的式子的说明图。表示加热源Hk中的热量流出流入的式子例如用下述式(4)等表示。式(4)中,为了式子的简化,在各加热源Hk中,设为温度分布一样。式4上述式(4)中,THk(t)表示加热源Hk的时刻t的温度(℃)、Ta表示外气的温度(℃)、Ck表示加热源Hk的热容量(J/℃)、Zk表示加热源Hk的电阻(Ω)、Ak表示加热源Hk与外气的接触面积、Hk表示加热源Hk与外气之间的热传导系数(W/(m2·℃))、Vk(t)表示时刻t的加热源Hk的电压(V)。Vk(t)2/Zk表示加热源Hk的输出(每单位时间的发热量)(W)、Hk×Ak×(Thk-Ta)表示从加热源Hk向外气泄漏的每单位时间的散热量(W)、Qk表示从加热源Hk向缸141流入的每单位时间的流入热量(W)。热传导系数hk可以为加热源Hk与外气之间的温度差(Thk(t)-Ta)的函数。其温度差越大,热传导系数Hk越大。流入热量Qk可以为加热源Hk与缸141之间的温度差(Thk(t)-Ti,0(t))的函数。该温度差越大,流入热量Qk越增加。其中,i为表示缸141的多个微少区域中的与加热源Hk接触的微少区域的坐标的整数。这样,基于缸141的热传导方程式(式(2))、缸内物质的热传导方程式(式(3))、以及表示各加热源Hk的热流出流入的式子(式(4))等做成传热模型。传热模型为了缩短计算时间可以为被低维化的式子。例如,缸141的热传导方程式(式(2))、以及缸内物质的热传导方程式(式(3))为线性方程式,因此,既能保持输入与输出的关系,也能够通过平衡实现法等低维化。另一方面,表示各加热源Hk的热量的流出流入的式子(式(4))由于为非线性方程式且原本为低维,因此不进行低维化也可以。控制装置180通过将预定时刻的各加热源Hk的输出(W)输入到传热模型中,能够计算出预定时刻的缸141的任意位置的温度Ti,j(t)。缸141的微小区域的个数(m+1)×(n+1)比温度传感器Sk(图4中k=1,2,3,4)的个数(图4中为4个)明显多,因此,可以明了缸141的详细的温度分布。另外,各加热源Hk的输出可以作为从初始时刻(t=0)到预定时刻为止的输出波形输入到传热模型中。并且,控制装置180通过将预定时刻的各加热源Hk的输出(W)输入到传热模型中,也能计算预定时刻的缸内物质的微小区域的温度Tfli(t)、预定时刻的各加热源Hk的温度Thk(t)。因此,也能够明了缸141的内部的详细温度分布、各加热源Hk的温度。另外,各加热源Hk的输出可以作为从初始时刻(t=0)到预定时刻为止的输出波形输入到传热模型中。传热模型由于为微分方程式,所以,能够给出初始值Ti,j(t=0)、Tfli(t=0)、Thk(t=0),由此求解Ti,j(t)、Tfli(t)、Thk(t)。初始时刻(t=0)可以为例如缸141的升温开始时刻,初始值Ti,j(t=0)、Tfli(t=0)、Thk(t=0)与外气的温度Ta相同也可以。另外,各初始值Ti,j(t=0)、Tfli(t=0)、Thk(t=0)可以为已知,也可以与外气的温度Ta相同。即,初始时刻(t=0)可以不为缸141的升温开始时刻。本实施方式中,使用评价函数求解Ti,j(t)、Tfli(t)、Thk(t)的稳态解,因此可以不知道初始值Ti,j(t=0)、Tfli(t=0)、Thk(t=0)。控制装置180可以通过加热源Hk的功率计Pk(参照图4)等检测输入到传热模型中的加热源Hk的输出(W)。基于加热源Hk的实际的输出波形推测温度,因此,推测精度高。并且,控制装置180也可以通过加热源Hk的反馈控制模型(例如PID控制模型)的控制常数(例如比例增益、积分增益、微分增益)计算输入到传热模型中的加热源Hk的输出。首先,控制装置180由温度传感器Sk的测量位置的温度Ti,j(t)与设定温度之间的偏差以及控制常数来预测比时刻t稍微靠后的未来时刻t+Δt的加热源Hk的输出。接着,控制装置180将预测的加热源Hk的输出输入到传热模型中,预测时刻t+Δt的温度传感器Sk的测量位置的温度。这样,反复进行加热源Hk的输出预测和温度预测,由此,控制装置180不仅能够预测现在的温度以及过去的温度,还能够预测将来的温度。另外,现在为止的加热源Hk的输出通过功率计Pk检测,将来的加热源Hk的输出使用反馈控制模型的控制常数来预测也可以。控制装置180做成使用预先设定目标温度的预定位置处的传热模型计算出的温度与预先设定的目标温度之差越小值越精确(变小)的评价函数。评价函数可以为在凸优化问题中所使用的一般的函数。凸优化问题中可以施加制约条件,该制约条件为使在从缸主体部141a的后端(冷却部件161侧的一端)到前方预定距离MZ(参照图2)以内的位置预先设定的目标温度为设定温度以下。并且,作为制约条件,还可以给出在比缸主体部141a的后端还靠后方的位置处预先设定的目标温度为设定温度以下这样的制约条件。控制装置180通过二次规划法求解评价函数的最优解(各加热源H1~H4的稳定状态下的温度的最优解)。接着,控制装置180将所得到的最优解设为边界条件再次求解传热模型的稳态解。由此,能够得到缸或缸内部的温度分布的最优稳态解。并且,参照表示预先记录在记录介质中的各温度传感器S1~S4的测量位置的数据(x坐标、y坐标),能够求出各温度传感器S1~S4的测量位置处的最适合温度。将该最适合温度作为目标温度加以采用。控制装置180利用最适合温度即目标温度控制多个加热源H1~H4。由此,能够使预定位置处的实际的温度尽量接近预先设定的目标温度。控制装置180可以用显示装置图像显示由传热模型计算出的温度分布的最优稳态解。控制装置180也可以用显示装置图像显示预先设定的目标温度的分布。以上对本发明的实施方式以及变形例进行了说明,但本发明并不局限于上述实施方式等,在技术方案记载的本发明的要点的范围内,可以实施各种变形、替换。例如,在上述第一实施方式中,求解了稳态问题的热扩散方程式,但也可以求解非稳态问题的热扩散方程式,此时,除了边界条件以外还给出了初始条件。并且,在上述第一实施方式以及上述第二实施方式中,从缸主体部的后端(冷却部件侧的一端)到前方预定距离以内的位置,没有设定温度的下限值,但是设定温度在一定范围内也可以设定温度的下限值。温度的下限值可以为例如室温(25℃)。并且,在上述第一实施方式以及上述第二实施方式中,由于解决带制约条件的凸优化问题,所示使用二次规划法,但在没有制约条件时,也可以使用最小二乘法。并且,上述第一实施方式以及上述第二实施方式中,螺杆上所形成的槽的深度根据情况而不同,但也可以为一定。