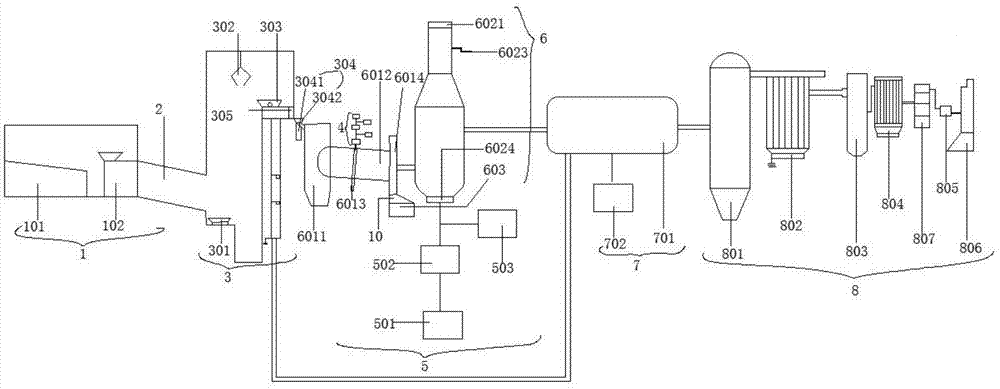
本实用新型涉及环保系统领域,具体涉及一种改良型危险废物焚烧系统。
背景技术:
:随着科学技术的迅猛发展和社会的进步,各行各业得到了较快的发展,生产中产生的废弃物越来越多,这些废弃物多数属于危险废弃物。危险废弃物具备反应性、传染性、放射性、腐蚀性、急性毒性、浸出毒性、易燃或易爆性等特点,容易对生物群体和生态环境造成短期或长期的危害影响危害。目前的处理危险废弃物的系统相对不完整,同时存在工作效率低、燃烧不充分的缺点,由于危险废弃物不能完全燃烧,燃烧产生的二恶英、飞灰等危险物将直接排入大气中,对环境造成威胁,针对不同状态的危险废物不能够处理完善,亟待相关技术提供一种改良型危险废物焚烧系统。技术实现要素:为解决上述问题,本实用新型公开了一种改良型危险废物焚烧系统,其目的在于解决目前对于危险废物处理系统相对不完善的问题。为了达到以上目的,本实用新型提供如下技术方案:一种改良型危险废物焚烧系统,包括:破碎系统、配伍系统、进料系统、助燃系统、助燃空气系统、焚烧系统、余热利用系统、尾气净化系统;焚烧系统包括回转窑、二燃室,所述回转窑由前端板、回转窑筒体、传动机构以及支撑机构组成,所述前端板设置进料系统,所述前端板采用耐火材料,其下部设置废料收集器用来收集危险废物漏料,所述回转窑筒体后端与二燃室连接,其下端设置出渣机,所述二燃室通过一个内嵌耐火材料的烟道与烟气急冷塔入口段相连;回转窑焚烧炉采用顺流式,废弃物从回转窑筒体的头部进入,助燃的空气由头部进入,随着筒体的转动缓慢地向尾部移动,完成干燥、燃烧、燃烬的全过程,焚烧后的炉渣由窑尾排出,落入出渣机内,炉渣经冷却降温后由出渣机带出,外运填埋;焚烧产生的烟气,由窑体尾部进入二燃室,该设计结构简单清晰,各组件之间紧密联系又不相互影响,所需部件更换方便,易于日后产品在使用过程中的维修保养。破碎系统由破碎机和破碎机进料系统组成,所述破碎机采用剪切式破碎机,所述破碎机进料系统采用行车抓斗进料;对于尺寸较大的废物或金属箱装废物,先对其进行破碎处理有利于提高后续对其燃烧的充分性同时避免了对焚烧炉的损耗,延长焚烧炉的使用寿命。配伍系统,将危险废物经过配伍后热值为3500kcal/kg;将危险废物配伍后元素成分占比如下表所示:C%H%O%N%S%CL%F%A%W%总计35.003.605.003.000.602.000.523.3027.00100通过添加配伍系统,均衡了废物的热值和水分,保证焚烧稳定,节省辅助燃料;均衡入窑废物的成分,尽量避免有害成分物质的集中焚烧,保证烟气排放达标;控制重金属含量,保证焚烧系统正常运行和烟气达标排放;控制磷含量,焚烧产生的P2O5在400-700℃会对金属产生加大的腐蚀,降低设备使用寿命,采用此设计,保证了入炉磷含量:P<0.5%。入炉磷最高含量:P<1.0%。进料系统由行车、抓斗、上料斗、密封门及推料机构组成,所述行车选用QD型抓斗桥式起重机,在炉前贮库布置,用于预处理混料和焚烧进料,所述上料斗设置在回转窑前端,料斗口部设置监视器,所述密封门采用两级液压密封门,其包括第一级密封门和第二级密封门,所述第一级密封门材料为钢板,第二级密封门材料为耐火隔热材料,所述上料斗下端设置冷却系统,所述推料机构设置在上料斗的下端,料斗内的危险废物通过推料机构推至回转窑内焚烧,所述推料机构为往复式运动方式;助燃系统,包括燃烧器、一次鼓风机、油泵、油箱、油罐组成,油罐车将油卸入所述油罐内,由油泵输送至中间油箱内,再经油泵、燃烧器喷入回转窑内助燃;该助燃系统设计简单、清晰,在对危险废物进行焚烧的过程中,通过添加助燃系统的设计能够有效提高废物燃烧比,保证进入二燃室的废气以及废渣能够充分燃烧。助燃空气系统,设置在二燃室端,包括二次鼓风机、二次风换热器以及压力雾化喷头;废物在被扬起落下的过程中,物料与空气中的氧充分混合,同时保证在焚烧炉内燃烧时间足够,通过空气换热器的设计有效减少了辅助燃料消耗量。余热利用系统,包括烟道水套和热水箱,所述二燃室的烟气作热源,将送至烟道水套进行加热后的水传送至水箱内;高温烟气离开二燃室后,进入急冷塔前,二燃室排出的烟气做热源,通过一段内衬耐火材料带水冷的烟道。一方面可降低部分烟气温度,一方面回收部分热量用于生产生活用热水,真正做到节能环保生产;尾气净化系统包括烟气急冷塔、旋风除尘器、脱酸塔、布袋除尘器、引风机以及烟气排放装置,所述脱酸塔与布袋除尘器之间喷置干活性炭粉,所述布袋除尘器的后部与引风机的前部还布置有洗涤除雾塔,所述洗涤除雾塔的顶部设置气水分离装置。因危险废物的待处理物的不确定性,为确保烟气达标排放,采用“急冷降温+旋风除尘器+干法脱酸+活性炭吸附+布袋除尘+湿法脱酸”的尾气净化系统,洗涤除雾塔吸收酸性气体作为干法脱酸的补充,用来保证二氧化硫、氯化氢及氟化氢的排放达标,废物中成份硫、氯需要用湿式吸收塔来得到有效排除,实际运行过程时废物所含硫、氯和氟化物的波动通过自动调整氢氧化钠的加药量来调节,采用烟气急冷的方式,此时高温烟气均匀地分布在塔内,急冷水雾与烟气直接接触,使烟气温度急速下降,从1000℃骤冷至250℃,可以避开二噁英再合成的温度段,从而达到抑制二噁英再生成的目的,同时能够起到降温、洗涤以及除尘的作用。作为本实用新型的一种改进,所述破碎机每小时处理量为3吨,出料尺寸≤200mm,破碎后物料平均尺寸为20cmx5cm。作为本实用新型的一种改进,所述推料机构由液压驱动机构驱动,所述液压驱动机构包括液压缸、液压站以及液压泵。作为本实用新型的一种改进,所述回转窑筒体后端与二燃室连接处的风冷夹套密封结构采用摩擦式及迷宫式的组合式金属密封技术,由耐热钢片、弹簧钢片以及耐火纤维毡三种密封组件组成。密封组件能在回转窑窑内温度1000℃、窑内压力为-30Pa的条件下,提供可靠密封,防止烟气泄漏。作为本实用新型的一种改进,所述回转窑的窑尾还设有清焦燃烧器,回转窑出口与二燃室设观察孔和高温摄像装置。通过在回转窑出口与二燃室设观察孔和高温摄像装置的设计,解决了传统焚烧系统中二燃室中燃烧过程不可控、智能化程度低的缺点。作为本实用新型的一种改进,所述烟气排放装置采用烟囱,在烟囱上设置取样口以及在线检测装置。可及时观察窑内运行状况。作为本实用新型的一种改进,所述二燃室包括壳体、防爆门、废液喷枪以及辅助燃烧器,在末端烟气出口烟道上设置有热电偶,辅助燃烧器设置在二燃室的下端,所述壳体内设置耐火隔热内衬材料。作为本实用新型的一种改进,所述前端板为自支撑结构。前端板为自支撑结构,避免推料机构产生的推力传递到回转窑。作为本实用新型的一种改进,所述洗涤除雾塔为圆柱塔体,塔内装有旋流塔板、除雾波纹板,所述旋流塔板材质为玻璃钢,塔体材质为碳钢。工作时,烟气由塔底向上流动,呈发散状进入洗涤塔底部,然后继续垂直往上通过布流层,酸性气体的吸收就发生在这个部位。通过带喷嘴的喷头将循环液扩散布到整个塔截面,确保所有气体都能够与循环液充分接触。布流层下面的喷头用来确保烟气进入布流层之前达到露点温度。布流层上面有一个波纹状除雾器,通过该除雾器可从烟气流中去除所有液滴。除雾器带有冲洗喷头,可间歇地喷入高压清洁水清洗除雾器,去除可能沉淀其上的盐类物质。作为本实用新型的一种改进,所述脱酸塔采用干式脱酸塔,利用脱酸剂进行脱酸,所述脱酸剂为熟石灰。相对与现有技术,本实用新型具有如下优点:1)回转窑焚烧炉采用顺流式,废弃物从回转窑筒体的头部进入,助燃的空气由头部进入,随着筒体的转动缓慢地向尾部移动,完成干燥、燃烧、燃烬的全过程,焚烧后的炉渣由窑尾排出,落入出渣机内,炉渣经冷却降温后由出渣机带出,外运填埋;焚烧产生的烟气,由窑体尾部进入二燃室,该设计结构简单清晰,各组件之间紧密联系又不相互影响,所需部件更换方便,易于日后产品在使用过程中的维修保养;2)通过添加配伍系统,均衡了废物的热值和水分,保证焚烧稳定,节省辅助燃料;均衡入窑废物的成分,尽量避免有害成分物质的集中焚烧,保证烟气排放达标;控制重金属含量,保证焚烧系统正常运行和烟气达标排放;控制磷含量,焚烧产生的P2O5在400-700℃会对金属产生加大的腐蚀,降低设备使用寿命,采用此设计,保证了入炉磷含量:P<0.5%。入炉磷最高含量:P<1.0%;3)因危险废物的待处理物的不确定性,为确保烟气达标排放,采用“急冷降温+旋风除尘器+干法脱酸+活性炭吸附+布袋除尘+湿法脱酸”的尾气净化系统,洗涤除雾塔吸收酸性气体作为干法脱酸的补充,用来保证二氧化硫、氯化氢及氟化氢的排放达标,废物中成份硫、氯需要用湿式吸收塔来得到有效排除,实际运行过程时废物所含硫、氯和氟化物的波动通过自动调整氢氧化钠的加药量来调节,采用烟气急冷的方式,此时高温烟气均匀地分布在塔内,急冷水雾与烟气直接接触,使烟气温度急速下降,从1000℃骤冷至250℃,可以避开二噁英再合成的温度段,从而达到抑制二噁英再生成的目的,同时能够起到降温、洗涤以及除尘的作用;4)通过在回转窑出口与二燃室设观察孔和高温摄像装置的设计,解决了传统焚烧系统中二燃室中燃烧过程不可控、智能化程度低的缺点;5)本实用新型实现了热量的循环利用、提高了燃烧效率,保证了排放烟气的各项指数含量达标。附图说明图1为本实用新型一种改良型危险废物焚烧系统整体结构示意图;图2为本实用新型中助燃系统组件构成图;图3为本实用新型中液压驱动机构构成示意图;附图标记列表:1、破碎系统;101、破碎机;102、破碎机进料系统;2、配伍系统;3、进料系统;301、行车;302、抓斗;303、上料斗;304、密封门;3041、第一级密封门;3042、第二级密封门;305、推料机构;4、助燃系统;401、燃烧器;402、一次鼓风机;403、油泵;404、油箱;405、油罐;5、助燃空气系统;501、二次鼓风机;502、二次风换热器;503、压力雾化喷头;6、焚烧系统;601、回转窑;6011、前端板;6012、回转窑筒体;6013、传动机构;6014、支撑机构;602、二燃室;6021、壳体;6022、防爆门;6023、废液喷枪;6024、辅助燃烧器;603、出渣机;7、余热利用系统;701、烟道水套;702、热水箱;8、尾气净化系统;801、烟气急冷塔;802、旋风除尘器;803、脱酸塔;804、布袋除尘器;805、引风机;806、烟气排放装置;807、洗涤除雾塔;9、液压驱动机构;901、液压缸;902、液压站;903、液压泵;10、清焦燃烧器;具体实施方式为了使本发明所要解决的技术问题、技术方案及有益效果更加清楚明白,以下结合附图及实施例,对本发明进行进一步详细说明。应当理解,此处所描述的具体实施例仅仅用以解释本发明,并不用于限定本发明。需要说明的是,当元件被称为“固定于”或“设置于”另一个元件,它可以直接在另一个元件上或者间接在该另一个元件上。当一个元件被称为是“连接于”另一个元件,它可以是直接连接到另一个元件或间接连接至该另一个元件上。需要理解的是,术语“长度”、“宽度”、“上”、“下”、“前”、“后”、“左”、“右”、“竖直”、“水平”、“顶”、“底”“内”、“外”等指示的方位或位置关系为基于附图所示的方位或位置关系,仅是为了便于描述本发明和简化描述,而不是指示或暗示所指的装置或元件必须具有特定的方位、以特定的方位构造和操作,因此不能理解为对本发明的限制。此外,术语“第一”、“第二”仅用于描述目的,而不能理解为指示或暗示相对重要性或者隐含指明所指示的技术特征的数量。由此,限定有“第一”、“第二”的特征可以明示或者隐含地包括一个或者更多个该特征。在本发明的描述中,“多个”的含义是两个或两个以上,除非另有明确具体的限定。实施例1:参见图1、图2和图3,现对本实用新型提供的一种改良型危险废物焚烧系统进行说明,包括:破碎系统1、配伍系统2、进料系统3、助燃系统4、助燃空气系统5、焚烧系统6、余热利用系统7、尾气净化系统8;焚烧系统6包括回转窑601、二燃室602,所述回转窑601由前端板6011、回转窑筒体6012、传动机构6013以及支撑机构6014组成,所述前端板6011设置进料系统2,所述前端板6011采用耐火材料,其下部设置废料收集器用来收集危险废物漏料,所述回转窑筒体6012后端与二燃室602连接,其下端设置出渣机603,所述二燃室602通过一个内嵌耐火材料的烟道与烟气急冷塔801入口段相连;回转窑焚烧炉采用顺流式,废弃物从回转窑筒体的头部进入,助燃的空气由头部进入,随着筒体的转动缓慢地向尾部移动,完成干燥、燃烧、燃烬的全过程,焚烧后的炉渣由窑尾排出,落入出渣机内,炉渣经冷却降温后由出渣机带出,外运填埋;焚烧产生的烟气,由窑体尾部进入二燃室,该设计结构简单清晰,各组件之间紧密联系又不相互影响,所需部件更换方便,易于日后产品在使用过程中的维修保养。破碎系统1由破碎机101和破碎机进料系统102组成,所述破碎机101采用剪切式破碎机,所述破碎机进料系统102采用行车抓斗进料;对于尺寸较大的废物或金属箱装废物,先对其进行破碎处理有利于提高后续对其燃烧的充分性同时避免了对焚烧炉的损耗,延长焚烧炉的使用寿命。配伍系统,将危险废物经过配伍后热值为3500kcal/kg,其元素成分占比如下表所示:C%H%O%N%S%CL%F%A%W%总计35.003.605.003.000.602.000.523.3027.00100通过添加配伍系统,均衡了废物的热值和水分,保证焚烧稳定,节省辅助燃料;均衡入窑废物的成分,尽量避免有害成分物质的集中焚烧,保证烟气排放达标;控制重金属含量,保证焚烧系统正常运行和烟气达标排放;控制磷含量,焚烧产生的P2O5在400-700℃会对金属产生加大的腐蚀,降低设备使用寿命,采用此设计,保证了入炉磷含量:P<0.5%。入炉磷最高含量:P<1.0%。进料系统3由行车302、抓斗302、上料斗303、密封门304及推料机构305组成,所述行车301选用QD型抓斗桥式起重机,在炉前贮库布置,用于预处理混料和焚烧进料,所述上料斗303设置在回转窑601前端,料斗口部设置监视器,所述密封门304采用两级液压密封门,其包括第一级密封门3041和第二级密封门3042,所述第一级密封门3041材料为钢板,第二级密封门3042材料为耐火隔热材料,所述上料斗303下端设置冷却系统,所述推料机构305设置在上料斗303的下端,料斗内的危险废物通过推料机构推至回转窑内焚烧,所述推料机构305为往复式运动方式;助燃系统4,包括燃烧器401、一次鼓风机402、油泵403、油箱404、油罐405,油罐车将油卸入所述油罐405内,由油泵403输送至中间油箱内,再经油泵403、燃烧器401喷入回转窑601内助燃,该助燃系统设计简单、清晰,在对危险废物进行焚烧的过程中,通过添加助燃系统的设计能够有效提高废物燃烧比,保证进入二燃室的废气以及废渣能够充分燃烧。助燃空气系统5,设置在二燃室602端,包括二次鼓风机501、二次风换热器502以及压力雾化喷头503;废物在被扬起落下的过程中,物料与空气中的氧充分混合,同时保证在焚烧炉内燃烧时间足够,通过空气换热器的设计有效减少了辅助燃料消耗量。余热利用系统7,包括烟道水套701和热水箱702,所述二燃室602的烟气作热源,将送至烟道水套701进行加热后的水传送至水箱702内;高温烟气离开二燃室602后,进入急冷塔前,二燃室排出的烟气做热源,通过一段内衬耐火材料带水冷的烟道。一方面可降低部分烟气温度,一方面回收部分热量用于生产生活用热水,真正做到节能环保生产;尾气净化系统8包括烟气急冷塔801、旋风除尘器802、脱酸塔803、布袋除尘器804、引风机805以及烟气排放装置806,所述脱酸塔803与布袋除尘器804之间喷置干活性炭粉,所述布袋除尘器804的后部与引风机805的前部还布置有洗涤除雾塔807,所述洗涤除雾塔807的顶部设置气水分离装置。因危险废物的待处理物的不确定性,为确保烟气达标排放,采用“急冷降温+旋风除尘器+干法脱酸+活性炭吸附+布袋除尘+湿法脱酸”的尾气净化系统,洗涤除雾塔吸收酸性气体作为干法脱酸的补充,用来保证二氧化硫、氯化氢及氟化氢的排放达标,废物中成份硫、氯需要用湿式吸收塔来得到有效排除,实际运行过程时废物所含硫、氯和氟化物的波动通过自动调整氢氧化钠的加药量来调节,采用烟气急冷的方式,此时高温烟气均匀地分布在塔内,急冷水雾与烟气直接接触,使烟气温度急速下降,从1000℃骤冷至250℃,可以避开二噁英再合成的温度段,从而达到抑制二噁英再生成的目的,同时能够起到降温、洗涤以及除尘的作用。实施例2:参见图1,作为本实用新型的一种改进,所述破碎机101每小时处理量为3吨,出料尺寸≤200mm,破碎后物料平均尺寸为20cmx5cm。实施例3:参见图3,作为本实用新型的一种改进,所述推料机构305由液压驱动机构9驱动,所述液压驱动机构9包括液压缸901、液压站902以及液压泵903。实施例4:参见图1,作为本实用新型的一种改进,所述回转窑筒体6012后端与二燃室602连接处的风冷夹套密封结构采用摩擦式及迷宫式的组合式金属密封技术,由耐热钢片、弹簧钢片以及耐火纤维毡三种密封组件组成。密封组件能在回转窑窑内温度1000℃、窑内压力为-30Pa的条件下,提供可靠密封,防止烟气泄漏。实施例5:参见图1,作为本实用新型的一种改进,所述回转窑601的窑尾还设有清焦燃烧器10,回转窑601出口与二燃室602设观察孔和高温摄像装置。通过在回转窑出口与二燃室设观察孔和高温摄像装置的设计,解决了传统焚烧系统中二燃室中燃烧过程不可控、智能化程度低的缺点。实施例6:参见图1,作为本实用新型的一种改进,所述烟气排放装置806采用烟囱,在烟囱上设置取样口以及在线检测装置。可及时观察窑内运行状况。实施例7:参见图1,作为本实用新型的一种改进,所述二燃室602包括壳体6021、防爆门6022、废液喷枪6023以及辅助燃烧器6024,在末端烟气出口烟道上设置有热电偶,辅助燃烧器设置在二燃室的下端,所述壳体设置耐火隔热内衬材料。实施例8:参见图1,作为本实用新型的一种改进,所述前端板6011为自支撑结构。前端板为自支撑结构,避免推料机构产生的推力传递到回转窑。实施例9:参见图1,作为本实用新型的一种改进,所述洗涤除雾塔807为圆柱塔体,塔内装有旋流塔板、除雾波纹板,所述旋流塔板材质为玻璃钢,塔体材质为碳钢。工作时,烟气由塔底向上流动,呈发散状进入洗涤塔底部,然后继续垂直往上通过布流层,酸性气体的吸收就发生在这个部位。通过带喷嘴的喷头将循环液扩散布到整个塔截面,确保所有气体都能够与循环液充分接触。布流层下面的喷头用来确保烟气进入布流层之前达到露点温度。布流层上面有一个波纹状除雾器,通过该除雾器可从烟气流中去除所有液滴。除雾器带有冲洗喷头,可间歇地喷入高压清洁水清洗除雾器,去除可能沉淀其上的盐类物质。实施例10:参见图1,作为本实用新型的一种改进,所述脱酸塔803采用干式脱酸塔,利用脱酸剂进行脱酸,所述脱酸剂为熟石灰。本实用新型还可以将实施例2、3、4、5、6、7、8、9、10所述技术特征中的至少一个与实施例1组合形成新的实施方式。本实用新型方案所公开的技术手段不仅限于上述实施方式所公开的技术手段,还包括由以上技术特征任意组合所组成的技术方案。应当指出,对于本
技术领域:
的普通技术人员来说,在不脱离本实用新型原理的前提下,还可以做出若干改进和润饰,这些改进和润饰也视为本实用新型的保护范围。当前第1页1 2 3