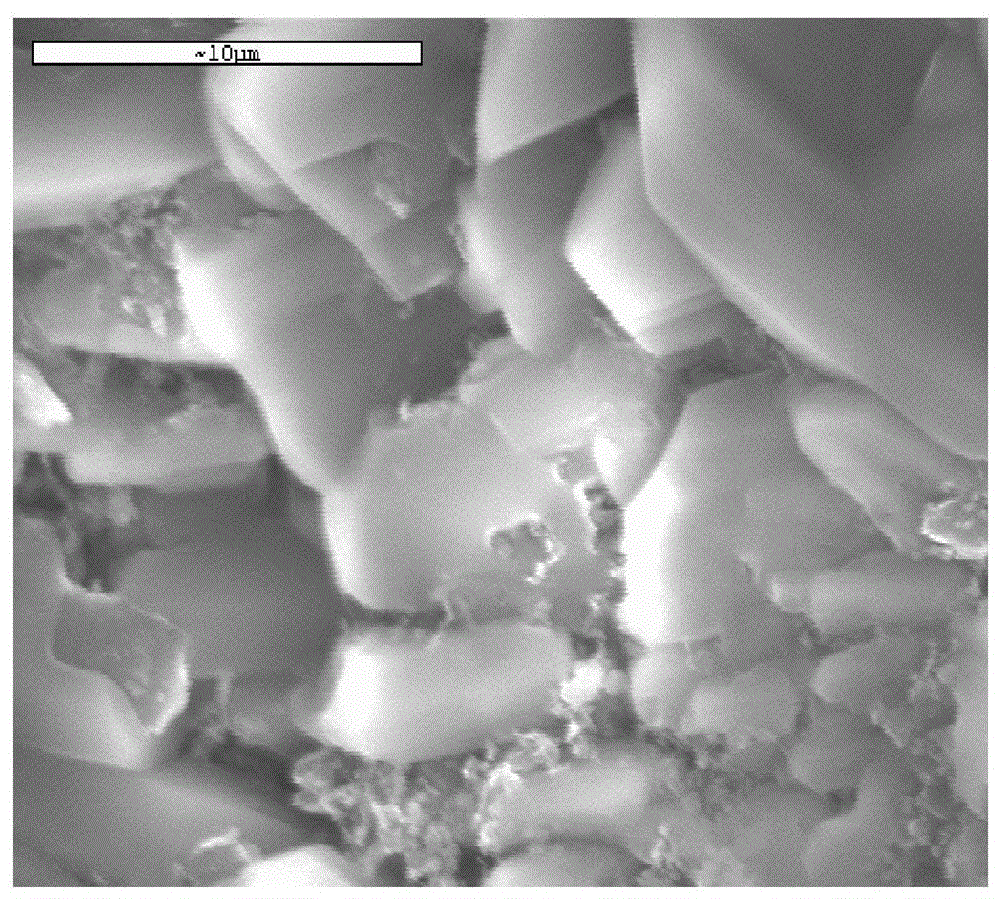
本发明是有关于一种催化剂及其制造方法,特别是指一种用于减少废气中氮氧化物的催化剂及其制造方法。
背景技术:烧结方法是利用高温燃烧方式将粉粒状的原料改变成为块状组织,使此加工后的块状原料适用于后续的高炉冶金熔炼方法,避免粉粒状原料因熔炼过程中随着鼓入的热气流而逸出。因此,将粉粒状原料经烧结方法转换成块状是高炉冶金熔炼中必要的步骤。利用高温燃烧方式,虽然可使粒状的烧结原料固结成块状的烧结饼,但也因粉粒状的原料的燃烧不完全,而伴随产生氮氧化物(NOx)污染。近年随着环保意识日渐高涨,环保法规日趋严格,如何有效降低氮氧化物的排放浓度,成为相关业者努力改善的目标。现有技术主要利用氨气(NH3)、碳或一氧化碳(CO)作为还原剂,将废气中的氮氧化物转换成氮气而加以去除,以降低氮氧化物的排放浓度。以氨气降低氮氧化物的排放浓度是目前最为常见的方法,其主要是藉由额外通入氨气与空气,并在300℃~400℃的高温催化下,与氮氧化物进行氧化还原反应,而将氮氧化物转化成氮气与水气,亦即所谓的SCR方法(SelectiveCatalyticReduction)。但是,一般烧结厂废气大多维持在150℃以下,因此,实际应用时还需要额外将废气加热至300℃以上以利反应的进行,不但额外增加能源的消耗,更会增加整体的处理成本,而且氨气为有害物质因此在操作时需格外小心。此外,额外通入的氨气与废气中的硫氧化物(SOx)在220℃以下更会反应生成具腐蚀性的产物,而造成设备受损。而利用碳作为降低氮氧化物排放浓度的还原剂,虽然效果较氨气更为优越,而且也不会产生具腐蚀性的产物而造成设备受损问题,但是,其反应温度必需在500℃以上,因此较SCR方法更为耗能,而且操作时还需要将废气中的氧气浓度控制在3%以下,避免燃烧的发生。而以一氧化碳为还原剂,主要是以附着于活性焦碳(ActivatedCoke,AC)的重金属(铜、钴、镍或铁)作为催化剂,并在300℃~500℃间与氮氧化物进行氧化还原反应,降低废气中氮氧化物的浓度。由于其反应温度300℃~500℃仍大于一般废气的150℃,因此,仍难以避免需额外加热,而导致处理成本过高的问题。如何减少额外能量的耗损且能降低处理成本,并维持良好氮氧化物的处理效率,成为相关业者接下来所欲改善的目标。
技术实现要素:因此,本发明的一个目的,即在提供一种能减少额外能量的耗损并降低操作成本,且具有良好处理效率的用于减少废气中氮氧化物的催化剂。本发明的另一目的在于,提供一种能减少额外能量的耗损并降低操作成本,且具有良好处理效率的用于减少废气中氮氧化物的催化剂的制造方法。于是,本发明用于减少废气中氮氧化物的催化剂的制造方法,包含混合搅拌步骤、水分去除步骤、加热步骤,及冷却出料步骤。该混合搅拌步骤是将褐煤焦碳(LigniteCoke,LC)、含钠溶液与纯水混合搅拌预定时间,而成为混合物;该水分去除步骤是将该混合物加热至干燥温度并维持设定时间,以去除该混合物中的水分。该加热步骤是将经过该水分去除步骤的混合物加热至加热温度,并维持加热时间,该加热温度是高于该干燥温度;而该出料步骤是将经过该加热步骤的混合物冷却后获得催化剂。而本发明用于减少废气中氮氧化物的催化剂,包含6至7wt%的钠,以及平衡量且不为0的褐煤焦碳。本发明的有益效果在于:采用简单的混合搅拌与高温处理的方式将钠附着于便宜的褐煤焦碳,而成为一种能在较低温度下即与废气中的氮氧化物进行氧化还原反应,以降低废气中氮氧化物浓度的催化剂,进而有效减少额外能量的耗损并降低操作成本,且具有良好的氮氧化物的处理效率。附图说明图1是一流程图,说明本发明用于减少废气中氮氧化物之催化剂的制造方法的一个优选实施例;及图2是一示意图,说明本发明用于减少废气中氮氧化物的催化剂的一个优选实施例于电子显微镜下的相片。具体实施方式有关本发明的前述及其它技术内容、特点与功效,在以下配合参考附图的一个优选实施例的详细说明中,将可清楚的呈现。参阅图1,本发明用于减少废气中氮氧化物的催化剂的制造方法的优选实施例包含混合搅拌步骤21、水分去除步骤22、加热步骤23,及冷却出料步骤24。该混合搅拌步骤21是将褐煤焦碳(LigniteCoke,LC)、含钠溶液与纯水混合搅拌预定时间,而成为混合物。在本优选实施例中该混合搅拌步骤21是将褐煤焦碳、含钠溶液与纯水加入能隔绝外界空气的旋转搅拌槽(图未示)中进行混合搅拌,而该预定时间是1.5小时。该水分去除步骤22是将置于搅拌槽中的混合物加热至干燥温度并维持设定时间,以去除该混合物中的水分。在本优选实施例中,该水分去除步骤22中的干燥温度是介于200℃至250℃之间,而该设定时间是2小时。该加热步骤23是将经过该水分去除步骤22的混合物加热至加热温度,并维持加热时间,以产生煅烧作用,使氢氧化钠(NaOH)转变成为氧化钠(Na2O),而将孔洞内的水去除。在本优选实施例中,该加热步骤23中的加热温度是介于280℃至300℃之间,而该加热时间是3小时。在此要特别说明的是,经测试褐煤焦碳需达350℃才会燃烧,因此,在能隔绝外界空气的旋转搅拌槽中的褐煤焦碳,并不会在该水分去除步骤22与该加热步骤23时产生闷烧。而该冷却出料步骤24是将经过该加热步骤23的混合物冷却后获得如图2所示含有6至7wt%的钠的催化剂。图2中在白色柱状结晶旁的小粒状物即是钠。在本优选实施例中,是该混合物冷却至室温后再由该搅拌槽中取出,而该催化剂是含有约6.9wt%的钠。由表1可知,该催化剂3与一般褐煤焦碳的物理性质差异不大。表1物理性质比较表物理性质比表面积(m2/g)孔径体积(cm3/g)孔径大小(nm)褐煤焦碳2880.2161.6催化剂240-2900.198-0.2191.602-1.782为验证本发明的催化剂的效果,发明人将约2吨本发明的催化剂,以及一般的褐煤焦碳送至烧结工场分别并安装于德商NusserIngenieurges所研发的废气处理设备上进行实验,以验证本发明的催化剂的功效。该废气处理设备是类似固定/流动床过滤器,但是,该废气处理设备不会生松动的吸附床,且气流通过时也不会产生凿沟(channeling)现象,而该废气处理设备的操作温度是介于68℃~118℃之间(平均温度为99℃),通入的废气流量为16,500~20,000m3/hr,其结果如表2所示。表2脱除效率比较表脱氮氧化物效率脱一氧化碳效率脱硫效率褐煤焦碳1%3%5%催化剂32~81%33~83%21~69%由表2可知本发明的催化剂在平均温度99℃的操作环境下,即具有较一般褐煤焦碳更优异的脱氮氧化物效率、脱一氧化碳效率与脱硫(硫氧化物)效率。由此可知,本发明的催化剂确实能在无需额外加热废气的情况下,即可进行废其中氮氧化物的脱除作业。因此,本发明的催化剂确实能有效减少额外能量的耗损以降低操作成本,且具有优异的脱氮氧化物效率、脱一氧化碳效率与脱硫(硫氧化物)效率。且由表2可以推知,本发明的催化剂的脱氮氧化物效率与脱一氧化碳效率是成正比关系,也就是说,本发明的催化剂是利用下列反应式(1),以废气中一氧化碳作为还原剂而将氮氧化物转化成氮气而加以去除,并不是以催化剂中的褐煤焦碳作为还原剂参与反应,因此,还可以有效避免原料的浪费。2NO+4CO+O2→N2+4CO2…………………(1)综上所述,本发明用于减少废气中氮氧化物的催化剂及其制造方法,采用简单的混合搅拌与高温处理的方式将钠附着于便宜的褐煤焦碳,而成为一个能在较低温度下即与废气中的氮氧化物进行氧化还原反应,以降低废气中氮氧化物浓度的催化剂,进而有效减少额外能量的耗损以降低操作成本,且具有良好之氮氧化物的处理效率,故确实能达成本发明的目的。惟以上所述者,仅为本发明的优选实施例而已,当不能以此限定本发明实施之范围,即大凡依本发明申请专利范围及发明说明内容所作之简单的等效变化与修饰,皆仍属本发明专利涵盖之范围内。附图标记21············混合搅拌步骤22············水分去除步骤23············加热步骤24············冷却出料步骤