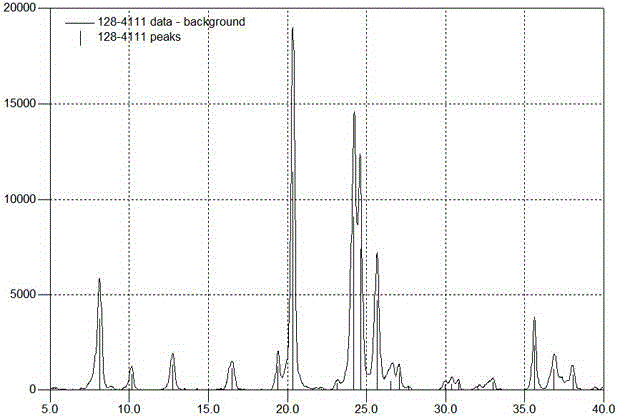
本发明涉及一种含贵金属和TON型分子筛催化剂的再生方法,更具体地说,涉及一种含贵金属和TON型分子筛的临氢异构化催化剂的再生方法,尤其是石蜡烃临氢异构化催化剂的再生方法,特别适合于润滑油的临氢异构脱蜡过程使用的催化剂再生方法。
背景技术:
:异构脱蜡技术主要应用于柴油、蜡油以及其他特种油品的临氢处理,以达到降低正构烷烃含量,提高油品质量的目的。该技术对改善柴油的低温流动性也有重要的意义。一般来说,直馏柴油或二次加工柴油中蜡含量较高,因此其凝点或冷滤点不合格,降低柴油的产率,加氢异构化可有效地将正构烷烃转化为低凝点的异构烷烃,而且还能保留其高十六烷值的特点。至于关于VGO加氢裂化或改质的尾油制取高质量的特种油,加氢异构化更是关键技术。通过长链正构烷烃的异构化,可制取低倾点、高粘度指数、低挥发度的馏分油组分,所以开发异构脱蜡催化剂再生技术不仅具有良好的经济效益,而且其社会意义是相当重要和深远的。炼油化工过程使用的催化剂在使用过程中活性会逐渐降低,即催化剂失活,归纳起来原因一般分为结焦失活(造成催化剂孔堵塞)、中毒失活(造成催化剂酸性中心中毒)和烧结失活(造成催化剂晶相的改变)等。工业加氢催化剂失活的主要原因是焦炭生成和金属堵塞、活性金属组分迁移或聚集、相组成的变化、活性中心数减少、载体烧结、沸石结构塌陷与崩溃等。对于积炭造成的失活催化剂可用再生的方法恢复其活性,而对于金属沉积污染造成的失活催化剂,不能再生使之恢复活性,只能废弃。催化剂再生分为器内再生和器外再生两种,器内再生常用介质为氮气和空气,尽量不用水蒸气和空气,因为水蒸气能促使催化剂上金属聚集、沸石晶型结构遭到破坏。由于器内再生缺点太多,已经很少采用该方式进行催化剂再生。目前工业上,特别是大型反应器中的催化剂都采用器外再生技术。催化剂器外再生技术的主要优点是催化剂再生过程中不易产生局部过热,催化剂活性恢复程度较高;可以增加装置的开工天数;而且装置反应系统也不用再承受再生气体中含硫气体的腐蚀。器外再生专利技术的实质是通过失活催化剂与含氧气体的接触,除去表面的积炭,即通过烧炭的方式使催化剂再生。与新鲜催化剂相比,再生催化剂的孔容、比表面都有一定程度的下降,而活性的下降幅度也较大。为了提高再生后催化剂的活性,在专利技术中也阐述了一些方法,对再生后的催化剂进行后处理,如CN1187215A提出将催化剂与添加剂接触而活化,之后在一定条件下干燥所述催化剂以使所述添加剂基本保留在催化剂中,所述添加剂是选自至少两个羟基和2~10个碳原子的化合物和这些化合物的醚的至少一种化合物。WO01/02092描述了一种通过以下方式将用过的基于添加剂的催化剂再生和活化的方法:在最高温度为500℃下将该催化剂与含氧气体接触,随后通过与有机添加剂接触使其活化,再经过一定温度干燥,以保证至少50%的所述添加剂保持在该催化剂中。优选的添加剂是选自包含至少两个含氧部分和2~10个碳原子的化合物以及由这些化合物衍生的化合物。所提及的实例包括酸、脂族二醇、脂族二醇醚、糖类和含氧化合物。CN1890351A所述方法为:将催化剂与酸和沸点为80~500℃以及在水中的溶解度至少为5g/L的有机添加剂接触,在一定条件下干燥以使至少50wt%的所述添加剂保留在催化剂中。上述的器外再生方法由于要经过高温烧炭步骤,然后再用有机添加剂处理,该方法不适宜用于以贵金属和分子筛材料为活性组分的异构脱蜡催化剂中。异构脱蜡催化剂采用的活性金属一般为贵金属,载体一般采用TON分子筛,是一种同时含有贵金属和分子筛的催化剂。该催化剂具有适宜的酸性中心和高的加氢活性,使其选择加氢裂化和加氢异构化功能达到很好的平衡,这样可以使催化剂的蜡异构化反应活性和选择性大大提高,具体表现在脱蜡油收率和粘度指数均得到提高,倾点得到明显降低。异构脱蜡催化剂在临氢异构脱蜡反应中活性下降的主要原因包括以下几点:(1)催化剂上积炭覆盖了催化剂的活性位或者堵塞了催化剂的孔道;(2)原料中的硫、氮等化合物使催化剂中毒;(3)金属的聚集或者载体结构的破坏;(4)原料中金属或者非金属的沉积,例如硅、砷、铁等。由于异构脱蜡催化剂是一种高分子筛含量贵金属催化剂,分子筛是一种亚稳态结晶,在一定条件下(例如高温、光照、长时间等)会转化为更稳定的结构(一般为ZSM-5分子筛结构),会丧失原有催化剂的反应性能,在高温下很容易导致分子筛结晶结构的破坏,而且也容易导致金属的聚集,一旦金属聚集,不能像重整催化剂那样进行金属的氯化更新(在高温下,氯和水蒸气对分子筛结构的破坏极大),即使烧炭后采用有机添加剂等常规方法处理,也很难使其再得到很好地分散。由此可见,常规的催化剂高温烧炭再生方法将会严重破坏该异构脱蜡催化剂的性能。所以一般的贵金属催化剂(例如重整催化剂)再生方法不适合异构脱蜡催化剂的再生,在整个再生过程中,必须严格控制催化剂颗粒表面的温度过高,并且保证氧化彻底,为此特别要求催化剂再生过程中严格控制再生温度和含氧量。所以异构脱蜡催化剂再生关键在于找到一个能够尽量脱除催化剂上的积炭,同时又能抑制对分子筛破坏和降低金属聚集的操作条件。在已有的有关积炭失活催化剂再生专利中,大多数专利着重考虑如何防止失活催化剂在再生过程中集中或过量放热的问题。如US5,037,785建议在含氧的气体下,采用激光照射的方法对催化剂除焦,US4,202,865建议用间歇式注氧,US4,780,195和US4,417,975等则认为在气氛中添加一定量的水来防止催化剂烧结等。CN1768956A认为催化剂上的积炭可以通过不同方法处理以获得更好的结果,有利于控制其再生时的温度,减少高温对催化剂性能的影响,提高再生催化剂的活性。其处理方式是先加入积炭清洗剂如丙二醇甲醚乙酸酯、丙二醇乙醚、二丙二醇甲醚、丙二醇甲醚等有机溶剂对失活催化剂进行浸泡洗涤。但是该方法溶剂用量过大,洗涤剂中的大分子副产物也难以分离。而且该方法先用有机溶剂除去部分容易除去的积炭,以减少在烧炭再生时放出的热量,但最终仍需要高温烧炭过程,仍然存在异构脱蜡催化剂在高温再生时遇到的问题,特别是金属铂发生聚集、分子筛结构被破坏等问题。技术实现要素:为了克服现有技术中的不足之处,本发明提供了一种含贵金属和TON型分子筛催化剂的再生方法,尤其适用于含TON型分子筛和第Ⅷ族贵金属组分的催化剂再生方法,特别是石蜡烃临氢异构化催化剂的再生方法。采用本发明的再生方法不但能够在低温下有效除去积炭,保证催化剂孔结构不被破坏,而且能使金属铂得到很好的分散,使再生后催化剂的反应性能可恢复至新鲜催化剂水平。本发明一种含贵金属和TON型分子筛催化剂的再生方法,该催化剂包括TON型分子筛和第Ⅷ族贵金属组分,再生过程包括:先用有机溶剂处理积炭失活催化剂,再采用浸渍法负载含镍化合物和含锡化合物,浸渍后催化剂上负载的镍与催化剂中金属铂的原子比为6:1~1:1,催化剂上负载的锡与催化剂中金属铂的原子比为10:1~1:1,然后在含氧气体作用下进行第一焙烧,第一焙烧完成后进行还原处理,再在含氧气体作用下进行第二焙烧,第一焙烧过程的最高温度不高于450℃,第二焙烧处理完成后经碱溶液浸泡洗涤,最后经干燥得到再生后催化剂。本发明的方法中所涉及的TON型分子筛可以是ZSM-22、SSZ-32、Nu-10、KZ-2和ISI-1中的一种或几种,优选含有ZSM-22分子筛,贵金属组分选自第Ⅷ族金属铂。还可以含有耐熔多孔无机氧化物,比如氧化铝、氧化硅、氧化钛、氧化锆等中的一种或多种。以催化剂的重量为基准,TON型分子筛的含量为10wt%~90wt%,优选30wt%~80wt%,贵金属的含量为0.05wt%~5.0wt%,耐熔多孔无机氧化物为余量。本发明方法中,失活催化剂先用有机溶剂进行处理,其中所用的有机溶剂一般可采用苯、乙醇、汽油、煤油中的一种或几种,有机溶剂处理失活催化剂的方法可以采用浸泡、蒸馏等常用的方法。有机溶剂与催化剂的体积比可以为8:1~1:1。本发明方法中,在浸渍法负载含镍化合物和含锡化合物时,可以采用一步浸渍法,也可以采用分步浸渍法,优选为一步浸渍法。当采用一步浸渍法时,浸渍法所用的浸渍液采用溶解有含镍化合物和含锡化合物的水溶液,其中,含镍化合物可以为硝酸镍、醋酸镍、硫酸镍等可溶性镍盐中的一种或多种,含镍化合物的浓度以镍元素计为1.0wt%~10wt%,含锡化合物水溶液可以为氯化亚锡、四氯化锡、硫酸亚锡等可溶性锡盐中的一种或多种,含锡化合物的浓度以锡元素计为5.0wt%~20wt%。当采用分步浸渍法时,可以采用常规的分步浸渍方法进行负载含镍化合物的水溶液和含锡化合物,可以先负载含镍化合物的水溶液,也可以先负载含锡化合物。分步浸渍的浸渍液包括含镍化合物的水溶液和含锡化合物的水溶液两种溶液,含镍化合物可以为硝酸镍、醋酸镍、硫酸镍等可溶性镍盐中的一种或多种,含镍化合物的水溶液的浓度以镍元素计为1.0wt%~10wt%,含锡化合物水溶液可以为氯化亚锡、四氯化锡、硫酸亚锡等可溶性锡盐中的一种或多种,含锡化合物的水溶液的浓度以锡元素计为5.0wt%~20wt%。浸渍法负载含镍化合物和含锡化合物后,催化剂上负载的镍与失活催化剂中铂的原子比为4:1~2:1,催化剂上负载的锡与失活催化剂中铂的原子比为8:1~3:1。本发明方法中,第一焙烧和第二焙烧的焙烧条件可以相同也可以不同。所述的第一焙烧的条件是:将所述催化剂与含氧气体接触,温度300℃~450℃,优选为320℃~420℃,接触时间为1.0h~10h,优选为2.0h~8.0h。所述的第二焙烧的条件是:将所述催化剂与含氧气体接触,温度300℃~450℃,优选为320℃~420℃,接触时间为1.0h~10h,优选为2.0h~8.0h。含氧气体中氧含量可以为0.2v%~25v%,优选为0.5v%~10v%。本发明方法中,所述的还原处理可以采用本领域常规使用的还原性气体进行还原,优选采用氢气进行还原,氢气采用纯度>99.9v%的氢气原料,所述的还原处理的操作条件为:将所述催化剂与氢气接触,温度为100℃~500℃,优选为200℃~450℃,时间为1.0h~15h,优选为5.0h~10h,氢气压力为0.5MPa~6.0MPa,优选为1.0MPa~4.0MPa。本发明方法中,所述的碱溶液可以采用本领域常用的碱溶液,优选为NaOH溶液或KOH溶液。所述的碱溶液的浓度为0.1wt%~20wt%,优选为1.0wt%~10wt%,浸泡时间可以为0.5h~20h,优选为1.0h~15h,更优选为5.0h~10h,浸泡和洗涤温度为室温。洗涤之后的催化剂再经干燥处理,干燥温度可以为60℃~200℃,优选为70℃~160℃,更优选为80℃~120℃,干燥时间可以为1.0h~20h,优选为3.0h~15h,更优选为5.0h~10h。本发明方法具有如下优点:(1)先用有机溶剂对失活催化剂进行处理,可降低失活催化剂上的积炭含量,有利于控制其再生时的温度,防止再生时放热过多或过于集中,避免催化剂的过热反应,导致催化剂性质发生变化,如分子筛的结构遭到破坏,或负载金属的富集对催化剂的性质造成负面影响。(2)在第一焙烧的烧炭过程中严格控制再生温度和含氧量,这是由于催化剂中含有较高比例的TON型分子筛,由于其分子筛的特殊性(容易转化为结构更稳定的ZSM-5分子筛结构),烧炭温度过高,严重影响分子筛的结晶度,研究显示烧炭温度在420℃之前催化剂的结构没有明显变化,但当烧炭温度450℃时,催化剂的结构发生了明显的变化,同新鲜催化剂相比,相对结晶度下降到97%(图1是新鲜剂的XRD图),所以在氧化烧焦过程中,烧炭温度是一个重要因素。当烧炭温度较低时,积炭消除率较低,但随着烧炭温度的升高,会造成活性金属的聚集并破坏分子筛的结构,使催化剂的性能受到较大影响。在整个再生过程中,必须严格控制催化剂颗粒表面的温度过高,并且保证氧化彻底,但由于在烧炭的过程中,催化剂上的碳在燃烧的过程中也放出热量,所以综合考虑为确保催化剂不被烧坏控制温度在450℃以下。(3)在经有机溶剂处理之后的催化剂上负载一定量的含镍化合物和含锡化合物,并在较低的温度下进行第一焙烧和第二焙烧。由于在高温下含镍化合物和含锡化合物容易被碳还原,而镍/锡遇氧又很容易被氧化,在氧化过程中会产生活性氧,活性氧能够快速的氧化催化剂上的积碳生成二氧化碳,这样不但能够有效地除去积炭,而且在第一焙烧过程中镍/锡与失活催化剂上的铂形成Pt-Sn-Ni复合化合物进行分散,又再经过还原处理和第二焙烧,能更有效的避免贵金属的聚集,提高贵金属铂的分散,同时避免了TON型分子筛结构的破坏,烧炭再生后的催化剂采用碱洗的方式除去锡,这样得到的再生后的催化剂不但能保证催化剂孔结构不被破坏,金属Pt具有更好的分散,而且能在此过程中还可以防止金属Ni与Pt流失,由于Ni-Pt的协同作用,能提高催化剂的加氢/脱氢反应活性,使催化剂的性能恢复至新鲜催化剂水平。附图说明图1为FD-1新鲜剂的XRD谱图(100%);图2为FD-1失活剂的XRD谱图(结晶度~99%);图3为R-420的XRD谱图(结晶度~99%);图4为R-450的XRD谱图(结晶度~97%);图5为R-500的XRD谱图(结晶度~92%)。其中,图3-图5中的R-是指FD-1失活剂的焙烧温度,例如R-420表示FD-1失活剂经420℃焙烧处理后,括号中的数字代表相对结晶度。具体实施方式下面通过实施例来进一步说明本发明催化剂的制备过程,但不应认为本发明仅局限于以下的实施例中。本发明中,wt%为质量分数,v%为体积分数。本发明再生催化剂是采用200mL中型固定床反应器进行评价,催化剂装填量为100mL,进料前对催化剂进行预还原,使催化剂上的贵金属转变为还原态,还原条件如下:在氢气存在下,温度300℃~500℃,压力0.5MPa~10MPa,时间1h~12h,评价所使用的原料油主要性质见表1。表1原料油主要性质密度(20℃),kg/m3861.1硫,μg/g4.0氮,μg/g1.2粘度(40℃),mm/s229.69倾点,℃21蜡含量,wt%9.8馏程,℃(D1160)IBP/10%227/39930%/50%428/44170%/90%455/46995%/EBP477/500本发明涉及到的FD-1失活催化剂为FD-1新鲜催化剂在中国石化齐鲁石化加氢裂化尾油异构脱蜡装置工业运转后的失活剂。FD-1失活催化剂的物化性质如下:比表面积为103m2/g,孔容为0.28mL/g,Pt含量0.45wt%,C含量为7.24wt%。FD-1新鲜剂的组成及性质如下:比表面积为235m2/g,孔容为0.35mL/g,Pt含量0.50wt%,ZSM-22分子筛的含量为70wt%。本发明涉及的FD-2失活催化剂的物化性质如下:比表面积为110m2/g,孔容为0.26mL/g,Pt含量0.45wt%,C含量为8.12wt%。FD-2新鲜剂的组成及性质如下:比表面积为245m2/g,孔容为0.36mL/g,Pt含量0.50wt%,NU-10分子筛的含量为50wt%。本发明涉及的FD-3失活催化剂的物化性质如下:比表面积为120m2/g,孔容为0.27mL/g,Pt含量0.44wt%,C含量为10.02wt%。FD-3新鲜剂的组成及性质如下:比表面积为270m2/g,孔容为0.37mL/g,Pt含量0.50wt%,SSZ-32分子筛的含量为40wt%。其中FD-2和FD-3为实验室快速失活剂。实施例1本发明催化剂E-1的制备。在2000mL的烧瓶内加入1450mL有机溶液(其中乙醇和苯体积比为2:1),对工业运转后的200mL失活催化剂FD-1进行处理,蒸馏2.0h后的催化剂编号为Ca-1。取11.8g硝酸镍(镍含量3.0wt%)、9.52g四氯化锡(Sn含量10.0wt%)配制含镍/锡的浸渍液,取Ca-1催化剂100g进行饱和浸渍,制得Ni与Pt、Sn与Pt的原子比分别为3:1和4:1的含镍/锡的催化剂样品,再以3℃/min的升温速度,升温至350℃恒温5h。所得催化剂编号为Ea-1。上述催化剂Ea-1在空气氛围下进行第一焙烧处理,具体条件是:以3℃/min的升温速度,升温至350℃恒温5h。将第一焙烧后的催化剂在在氢气氛围下进行还原处理,具体条件是:氢气压力为3.5MPa,还原温度为430℃,还原时间为6h。将还原处理后的催化剂在空气氛围下第二焙烧处理,具体条件为:以3℃/min的升温速度,升温至410℃恒温3h,所得催化剂编号为Ea-2。取8.5wt%(以NaOH计)氢氧化钠水溶液300g,加入100g上述催化剂Ea-2,室温下浸泡10h,再经120℃干燥10h,得本发明催化剂E-1,其具体处理条件见表2,反应结果见表3。实施例2本发明催化剂E-2的制备。取7.38g醋酸镍(镍含量8.0wt%)配制成浸渍液,按照实施例1方法制备Ca-1催化剂100g,进行饱和浸渍,制得Ni与Pt的原子比为5:1的含镍催化剂样品,经干燥和焙烧之后,取7.14g硫酸亚锡(Sn含量10.0wt%)配制成浸渍液,取上述含镍的催化剂进行过饱和浸渍,制得Sn与Pt的原子比为3:1的含镍/锡的催化剂样品,再以3℃/min的升温速度,升温至420℃恒温4h。所得催化剂编号为Eb-1。上述催化剂Eb-1在空气氛围下进行第一焙烧处理,具体条件是:以3℃/min的升温速度,升温至420℃恒温4h。将第一焙烧后的催化剂在氢气氛围下进行还原处理,具体条件是:氢气压力为4.5MPa,还原温度为480℃,还原时间为5h;将还原处理后的催化剂在空气氛围下第二焙烧处理,具体条件为:以3℃/min的升温速度,升温至450℃恒温3h,所得催化剂编号为Eb-2。取7.5wt%(以NaOH计)氢氧化钠水溶液300g,加入100g上述催化剂Eb-2,室温下浸泡10h,再经120℃干燥10h,得本发明催化剂E-2,其具体处理条件见表2,反应结果见表3。实施例3本发明催化剂E-3的制备。在2000mL的烧瓶内加入1450mL有机溶剂(其中汽油和煤油体积比为1:1),对200mL工业运转后失活催化剂FD-1进行处理,蒸馏2h后的催化剂编号为Cb-1。取35.4g硝酸镍(镍含量2.0wt%)、9.52g氯化亚锡(Sn含量20.0wt%)配制含镍/锡的浸渍液,取Cb-1催化剂100g进行饱和浸渍,制得Ni与Pt、Sn与Pt的原子比分别为6:1和8:1的含镍/锡的催化剂样品,再以3℃/min的升温速度,升温至350℃恒温5h。所得催化剂编号为Ec-1。上述催化剂Ec-1在空气氛围下进行第一焙烧处理,具体条件是:以3℃/min的升温速度,升温至350℃恒温5h。将第一焙烧后的催化剂在氢气氛围下进行还原处理,具体条件是:氢气压力为2.5MPa,还原温度为450℃,还原时间为7h;将还原处理后的催化剂在空气氛围下进行第二焙烧处理,具体条件为:以3℃/min的升温速度,升温至350℃恒温3h。所得催化剂编号为Ec-2。取15wt%(以NaOH计)氢氧化钠水溶液300g,加入100g上述催化剂Ec-2,室温下浸泡10h,再经120℃干燥10h,得本发明催化剂E-3,其具体处理条件见表2,反应结果见表3。实施例4~6本发明催化剂E-4~E-6的制备。本发明催化剂E-4~E-6的制备过程同实施例1,不同之处在于用所用的失活催化剂、含镍和锡溶液以及焙烧和还原的温度不同,制备出的本发明催化剂E-4~E-6,其具体处理条件见表2,反应结果见表3。对比例1本发明对比催化剂C-1制备。催化剂的制备方法同实施例1,不同之处在于催化剂不使用含镍化合物,编号为C-1,其物化性质见表2,反应结果见表3。对比例2本发明对比催化剂C-2制备。催化剂的制备方法同实施例1,不同之处在于催化剂不使用含锡化合物,编号为C-2,其具体处理条件见表2,反应结果见表3。对比例3本发明对比催化剂C-3制备。催化剂的制备方法同实施例1,不同之处在于催化剂虽然经过含镍/锡溶液处理,但是只经过一次焙烧处理,不经过还原处理和第二焙烧,编号为C-3,其具体处理条件见表2,反应结果见表3。对比例4本发明对比催化剂C-4制备。催化剂的制备方法同实施例1,不同之处在于催化剂虽然经过镍/锡溶液处理,又经过第一焙烧、还原处理和第二焙烧,但是不经过碱溶液处理,编号为C-4,其具体处理条件见表2,反应结果见表3。表2各实施例和比较例的处理条件表2续各实施例和比较例的处理条件编号氢气压力,MPa温度第二焙烧氢氧化钠浓度,wt%E-13.5430℃×6h410℃×3h8.5E-24.5480℃×5h450℃×3h7.5E-32.5450℃×7h350℃×3h15E-4③3.2400℃×5h410℃×4h2.5E-53.8410℃×5h370℃×2h5.0E-6④4.0270℃×10h400℃×5h13.5C-13.5410℃×6h420℃×3h8.5C-23.5410℃×6h420℃×3h8.5C-3------8.5C-43.5410℃×6h420℃×3h--注:乙醇/苯,②汽油/煤油,③FD-2失活催化剂,④FD-3失活催化剂表3催化剂评价条件及结果表3续催化剂评价条件及结果表3的评价结果显示,与对比催化剂相比,采用本发明方法再生的催化剂,用于润滑油馏分的加氢处理过程中,在润滑油基础油倾点相近时,C5+液收提高10wt%以上,润滑油基础油收率提高15wt%左右,产品的粘度指数提高近12个单位,说明本发明方法再生后的催化剂在处理润滑油原料过程中,效果具有显著提高。由图1至图5可见,FD-1新鲜剂的结晶度定为100%,其XDR结构见图1,失活剂的结构见图2,不同烧炭温度(420℃、450℃和500℃)得到的样品的XRD表征结果见图3~图5,从图3的结果可以看出:在烧炭温度在420℃之前催化剂的结构没有明显变化,但当烧炭温度450℃时,催化剂的结构发生了一些改变,当烧炭温度达到500℃时,催化剂的结构发生了明显的变化。因此,本发明要求第一焙烧的烧炭温度控制不高于450℃,最好不高于420℃。当前第1页1 2 3