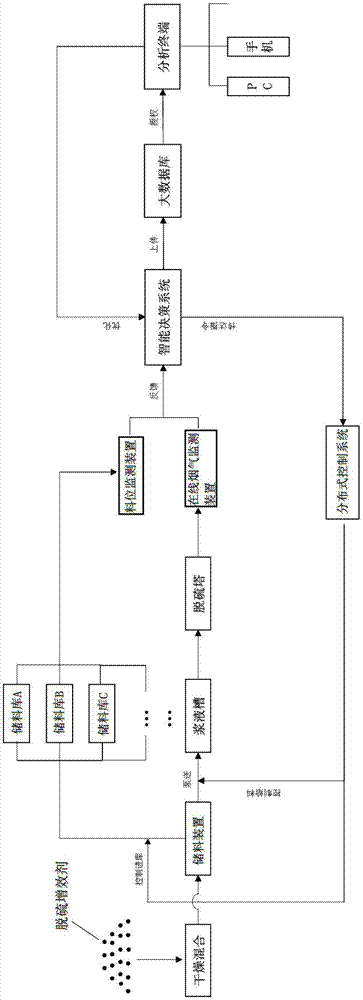
本发明涉及加料控制系统,属于电厂烟气脱硫
技术领域:
,具体地涉及一种湿法脱硫增效剂的智能加料控制系统及方法。
背景技术:
石灰石-石膏湿法烟气脱硫技术以其原料价廉易得、脱硫效率高等优点成为当今应用最广泛的脱硫技术,占据烟气脱硫市场的87%。随着电站锅炉燃用高硫煤比例的增大及2012年颁布的火电厂大气污染物排放标准gb13223-2011的实施,现有脱硫设备即便是在其设计脱硫效率下运行也很难达到日益严格的排放标准。研究表明,在湿法脱硫过程中,加入适量的增效剂,既可以提高其脱硫效率及脱硫剂的利用率、降低运行费用,同时还能减缓设备结垢、提高系统的可靠性。当前湿法脱硫增效剂的加料作业大部分都是人工按时、按量完成的,少部分具有技术经验的运行维护人员会根据电厂实时负荷、烟气so2浓度和以往经验调整加料作业,不同电厂因为情况不同每日消耗的增效剂量也不尽相同,并且增效剂中有些成分具有微毒性,长期接触会对人体健康造成影响,因此,人工作业效率低也不利于安全。同时,实际生产过程烟气中so2浓度受到多因素的影响是不断变化的,比如燃煤煤种、炉内温度等,但so2排放限值是固定的,始终采用一种增效剂配方可能会导致实时so2排放不达标或者大材小用的境况,因此,本发明提出一种湿法脱硫增效剂的智能加料方法,结合常用、替代、速效三种增效剂配方的使用,实现对湿法脱硫装置脱硫效率的实时调控,既能保证so2在线排放达标,又能最大限度降低脱硫成本,自动化加料的方式省去了人工作业的繁琐,降低安全隐患,并且电厂通用性好、响应快延时短、自动化程度高,不同电厂只需根据自身需要修改加料程序即可通用,从而提升作业水平,为智能化电厂建设的蓝图补上重要的一块。技术实现要素:为解决上述技术问题,本发明公开了一种可采用多种具有不同效力和成本增效剂的湿法脱硫增效剂的智能加料控制系统及方法。为实现上述目的,本发明公开了一种湿法脱硫增效剂的智能加料控制系统,包括储料装置、在线烟气监测装置、料位监测装置、智能决策系统、分布式控制系统、浆液槽及脱硫塔,其中,所述储料装置包括若干个用于盛装不同种脱硫增效剂的储料库,每个储料库分别与浆液槽构成单独的回路;所述在线烟气监测装置用于实时监测电厂锅炉负荷、脱硫塔烟气量、脱硫塔中so2浓度及脱硫效率并反馈至智能决策系统;所述料位监测装置连接智能决策系统,用于监测目标储料库的实时料位信息并反馈至智能决策系统;所述智能决策系统对接收到信息进行分析处理,制定出脱硫增效剂的加料方案并通过分布式控制系统控制储料装置中的目标储料库按照加料方案将脱硫增效剂送至浆液槽。进一步地,所述脱硫增效剂包括配方a、配方b和配方c;所述配方a由如下各质量份数的组分组成:己二酸65~75份、乙酸钠5~9份、柠檬酸钠6~10份、苯甲酸钠5~9份、硫酸镁6~10份;优选的,所述配方a由己二酸65份、乙酸钠5份、柠檬酸钠6份、苯甲酸钠5份、硫酸镁6份组成。优选的,己二酸75份、乙酸钠9份、柠檬酸钠10份、苯甲酸钠9份、硫酸镁10份。所述配方b由如下各质量份数的组分组成:羧甲基纤维素钠65~75份、乙酸钠6~10份、十二烷基硫酸钠5~9份、苯甲酸钠5~9份、硫酸镁6~10份;优选的,所述配方b由羧甲基纤维素钠65份、乙酸钠6份、十二烷基硫酸钠5份、苯甲酸钠5份、硫酸镁6份组成。优选的,所述配方b由羧甲基纤维素钠75份、乙酸钠10份、十二烷基硫酸钠9份、苯甲酸钠9份、硫酸镁10份组成。所述配方c由如下各质量份数的组分组成:己二酸65~75份、乙酸钠6~10份、十二烷基硫酸钠5~9份、苯甲酸钠5~9份、硫酸镁6~10份。优选的,所述配方c由己二酸65份、乙酸钠6份、十二烷基硫酸钠5份、苯甲酸钠5份、硫酸镁6份组成。优选的,所述配方c由己二酸75份、乙酸钠10份、十二烷基硫酸钠9份、苯甲酸钠9份、硫酸镁10份组成。其中,配方a中有机酸(己二酸)、弱酸盐(乙酸钠、柠檬酸钠和苯甲酸钠)都是强力的ph缓冲剂,可以长时间保持浆液碱性,从而利于so2的吸收,同时己二酸可以缩短石灰石溶解时间,硫酸镁可以提高液体的传质能力促进石灰石的溶解,故配方a浆液适应能力强、脱硫效果不易衰退,主要能增强so2的吸收以及促进石灰石的溶解这两个基本过程。配方b的主要成分羧甲基纤维素钠是廉价安全的螯合剂、分散剂,可以与钙离子产生络合反应,促进石灰石消溶,表面活性剂十二烷基硫酸钠可以促进浆液中离子的传质,对so2吸收、石灰石溶解和硫酸钙结晶过程均有促进,使用后起泡明显,脱硫效果提升快,故配方b响应快、成本低廉,主要起促进石灰石溶解过程的作用。配方c以缓冲剂为主要成分,能长时间保持浆液ph碱性环境,联合表面活性剂十二烷基硫酸钠的起泡作用和硫酸镁的增强传质作用可以快速的提升石灰石溶解速度,从而使得配方c见效快、效果强。并且,所述配方a适用锅炉负荷在400~500mw时的电厂脱硫,所述配方b适用锅炉负荷在300mw~400mw时的电厂脱硫,所述配方c适用锅炉负荷在500mw~600mw时的电厂脱硫。选取市面上其他类型的脱硫增效剂作为本系统配套增效剂使用时,应以增效性能为主、成本为辅,从这两方面作为选择标准,所选配套增效剂必须具有明显的性能差异以适用不同工况下的使用,同时从各不同性能增效剂中优选最为经济的增效剂,组合使用以降低脱硫成本。进一步地,所述智能决策系统为人机智能系统dss,所述在线烟气监测装置包括在线烟气检测系统cems,所述智能决策系统dss对接收到信息汇总形成大数据库并授权给分析终端用于制定出优化的加料方案,根据所述优化的加料方案可更改智能决策系统的加料程序库。进一步地,所述加料程序库包括用于存储脱硫增效剂配方、加料周期及加料量。进一步地,所述分布式控制系统还控制传送带将配置好的脱硫增效剂输送至相对应的储料库。为了更好的实现本发明的技术目的,本发明还公开了一种湿法脱硫增效剂的智能加料控制方法,它为利用上述湿法脱硫增效剂的智能加料控制系统,包括:1)分布式控制系统控制储料装置中各储料库的储料过程;2)未加脱硫增效剂时,智能决策系统接收在线烟气监测装置监测到的电厂锅炉负荷、脱硫塔烟气量、脱硫塔中so2浓度及脱硫效率,做出使用哪种脱硫增效剂及所述脱硫增效剂的加料周期与加料量的加料方案的指令,并将该加料方案的指令传递给分布式控制系统;3)所述分布式控制系统按照所述指令完成脱硫增效剂的添加;4)完成添加所述脱硫增效剂后,所述在线烟气监测装置实时监测电厂锅炉负荷、脱硫塔烟气量、脱硫塔中so2浓度及脱硫效率并评价所述加料方案,所述智能决策系统做出继续使用所述加料方案或改变所述加料方案中至少任意一个参数的指令并转递给分布式控制系统做出相应行为,重复步骤4)的操作至电厂脱硫完成。进一步地,所述步骤4)中,完成添加某脱硫增效剂后,若智能决策系统分析发现脱硫塔中so2浓度较未加脱硫增效剂时仍处于正常可控程度则做出继续使用所述加料方案的指令;若智能决策系统分析发现脱硫塔中so2浓度较未加脱硫增效剂时有下降趋势,则做出延长加料周期或/和降低加料量的指令;若智能决策系统分析发现脱硫塔中so2浓度较未加脱硫增效剂时有增加趋势,则做出缩短加料周期或/和增加加料量的指令。进一步地,若智能决策系统分析发现使用某脱硫增效剂效果不佳,则做出放弃所述加料方案,采用另一种脱硫增效剂及加料周期与加料量的加料方案。优选的,智能决策系统对接收到信息汇总形成大数据库并授权给分析终端,如电脑或手机等经专家分析后制定出优化的加料方案,根据所述优化的加料方案可更改智能决策系统的加料程序库,所述加料程序库包括用于存储脱硫增效剂配方、加料周期及加料量等信息。优选的,还可采用神经网络算法等方法对大数据库中的信息进行优化以制定出更加优化的加料方案。本发明的有益效果主要体现在如下几个方面:1、本发明设计采用多种具有不同效力和成本的增效剂,如配方a、b、c实现了对脱硫效率的实时精确控制,既可以满足实际复杂生产条件下so2达标排放的要求,同时避免能源浪费,降低脱硫成本;2、本发明设计的控制方法可以用于不同湿法脱硫系统的加料作业,只需根据自身生产情况对生产管理区中的脱硫程序进行不同参数设定即可适用,自动化程度高、响应快延时短,省去了人工操作,避免了安全隐患;3、本发明设计的控制系统通过对生产过程中的数据积累,汇总存储并形成大数据库,专业人员可以通过分析端获取数据库信息,进行数据对比分析,从而发现制定出更好的加料方案,优化作业水平,同时也可借助神经网络算法等方法进行自动优化。附图说明图1为本发明控制方法的工艺流程图;图2为本发明智能决策系统的系统控制流程图;图3为本发明某电厂在使用a、b、c三种不同配方增效剂后的脱硫效果图。具体实施方式如图1所示,本发明公开了一种湿法脱硫增效剂的智能加料控制系统,包括储料装置、在线烟气监测装置、料位监测装置、智能决策系统、分布式控制系统、浆液槽及脱硫塔,其中,所述储料装置包括若干个用于盛装不同种脱硫增效剂的储料库,每个储料库分别与浆液槽构成单独的回路;并且所述储料库的个数≥3,本发明优选在标号为a、b和c的储料库中分别盛装配方a、配方b和配方c的脱硫增效剂,所述配方a由如下各质量份数的组分组成:己二酸65~75份、乙酸钠5~9份、柠檬酸钠6~10份、苯甲酸钠5~9份、硫酸镁6~10份;所述配方b由如下各质量份数的组分组成:羧甲基纤维素钠65~75份、乙酸钠6~10份、十二烷基硫酸钠5~9份、苯甲酸钠5~9份、硫酸镁6~10份;所述配方c由如下各质量份数的组分组成:己二酸65~75份、乙酸钠6~10份、十二烷基硫酸钠5~9份、苯甲酸钠5~9份、硫酸镁6~10份。且配方a、配方b和配方c的成本价如表1所示:表1本发明采用的各配方的成本名称配方a配方b配方c价格(元/吨)9564930010060同时,所述配方a适用锅炉负荷在400~500mw时的电厂脱硫,所述配方b适用锅炉负荷在300mw~400mw时的电厂脱硫,所述配方c适用锅炉负荷在500mw~600mw时的电厂脱硫。选取市面上其他类型的脱硫增效剂作为本系统配套增效剂使用时,应以增效性能为主、成本为辅,从这两方面作为选择标准,所选配套增效剂必须具有明显的性能差异以适用不同工况下的使用,同时从各不同性能增效剂中优选最为经济的增效剂,组合使用以降低脱硫成本。所述在线烟气监测装置用于实时监测脱硫塔中电厂锅炉负荷、脱硫塔烟气量、so2浓度、脱硫效率并反馈至智能决策系统;所述料位监测装置连接智能决策系统,用于监测目标储料库的实时料位信息并反馈至智能决策系统;所述智能决策系统对接收到信息进行分析处理,制定出脱硫增效剂的加料方案并通过分布式控制系统控制储料装置中的目标储料库按照加料方案将脱硫增效剂送至浆液槽,同时当料位监测装置监测到目标储料库的库存不足时,所述分布式控制系统还控制传送带将配置好的脱硫增效剂输送至相对应的储料库。与此同时,智能决策系统对接收到信息汇总形成大数据库并授权给分析终端,如电脑或手机等用于制定出优化的加料方案,根据所述优化的加料方案可更改智能决策系统的加料程序库,所述加料程序库包括用于存储脱硫增效剂配方、加料周期及加料量等数据信息。此外,还可采用神经网络算法等方法对大数据库中的信息进行优化以制定出更加优化的加料方案。为了更好地解释本发明,以下结合具体实施例进一步阐明本发明的主要内容,但本发明的内容不仅仅局限于以下实施例,并且以下实施例所采用智能决策系统均为图2所示的系统控制流程图,同时,结合图3可知,结合图3可知,控制其它变量相同,本发明所采用的配方c的脱硫效率相对更好,配方a和配方b的脱硫效果相当。实施例1一种湿法脱硫增效剂的智能加料控制方法,在某600mw电厂锅炉配套湿法脱硫系统上进行测试,工艺流程如图1所示,具体步骤如下:(1)脱硫增效剂的配制:取7000kg己二酸、700kg乙酸钠、800kg柠檬酸钠、700kg苯甲酸钠、800kg硫酸镁五种化学药剂经80℃干燥2h后,倒入混料机中混合均匀得到常用配方增效剂a十吨,通过传送带送入储料装置的储料库a中备用;取羧甲基纤维素钠7000kg、800kg乙酸钠、700kg十二烷基硫酸钠、700kg苯甲酸钠、800kg硫酸镁五种化学药剂经80℃干燥2h后,倒入混料机中混合均匀得到替代配方增效剂b十吨,通过传送带送入储料装置的储料库b中备用;取7000kg己二酸、800kg乙酸钠、800kg硫酸镁、700kg十二烷基硫酸钠、700kg苯甲酸钠五种化学药剂经80℃干燥2h后,倒入混料机中混合均匀得到速效配方增效剂c十吨,通过传送带送入储料装置的储料库c中备用;(2)在线烟气监测装置实时监测及反馈:未加入脱硫增效剂以前,所述在线烟气监测装置实时监测锅炉负荷、烟气量、脱硫前后so2浓度、脱硫效率、加料方案等并将该工况信息反馈给智能决策系统,本实施例检测到锅炉在正常450mw实时负荷下,进脱硫塔烟气量为1500~1700km3/h,此时湿法脱硫前实际so2量在1200~1800mg/nm3的可控正常范围。无增效剂加入时脱硫效率为84%~86%。(3)智能决策系统反馈处理:由于锅炉负荷变化必然影响烟气量,则实际so2含量也会增多或减少,所以首先判断实时负荷是否有变化,预估进入脱硫塔烟气量的变化趋势,从而得到so2含量增大或减少的趋势。为保证实时so2排放达标并且最大化降低脱硫成本确定合适的加料方案。具体地,接收到上述工况信息后,智能决策系统dss对比分析实时负荷、烟气量、脱硫前后so2含量、脱硫效率和加料方案等信息,其中,由于常用配方a可满足400~500mw负荷条件下的脱硫要求,故确定选用脱硫增效剂常用配方a,由人工或者加料程序设定常用配方a的加料周期和加料量,生成加料方案i,传达加料指令给分布式控制系统dcs;(4)加料:分布式控制系统dcs按照上述加料方案打开储料库a,将脱硫增效剂配方a通过传送带和加料泵按设定加料周期和加料量加入到浆液槽中;(5)反馈循环:采用加料方案i期间,在线烟气监测装置再将实时监测锅炉负荷、烟气量、脱硫前后so2含量、脱硫效率、加料方案等新的工况信息反馈给智能决策系统dss,其中,检测到采用常用配方a后的脱硫效率为96%;(6)反馈循环处理:如果智能决策系统dss判断实时锅炉负荷、烟气量和湿法脱硫前so2含量仍然处于1200~1800mg/nm3的正常范围,并且实时so2排放达标,则说明方案i依然可行,智能决策系统会按照既定的程序重复(4)的步骤继续采用加料方案i加料;如果此时电网要求锅炉降低目前450mw负荷运转(小于450mw大于400mw),则进入脱硫塔烟气量将会减少,一段时间内脱硫前so2含量则会有下降的趋势,智能决策系统dss对上述工况经过对比分析,so2保持降低趋势再继续保持方案i的加料周期和加料量使用常用配方a会导致脱硫成本增高,因此确定出配方a的新加料方案ii:由人工或者加料程序适当设定延长常用配方a的加料周期或者减少常用配方a的每次加料量,重复(4)的步骤进行常用配方a的加料方案ii的加料作业;如果此时电网要求锅炉增加目前450mw负荷运行(小于500mw大于450mw),则进入脱硫塔烟气量将会增加,一段时间内脱硫前so2含量则会有上升的趋势,智能决策系统dss对上述工况对比分析,so2保持升高的趋势再继续保持方案i的加料周期和加料量会导致so2排放不达标,因此确定配方a的新加料方案iii:由人工或者加料程序适当设定缩短增效剂a的加料周期或者增加增效剂a的每次加料量,重复(4)的步骤进行配方a的加料方案iii的加料作业;(7)补库存:加料作业期间储料库中脱硫增效剂库存不足时,分布式控制系统还控制传送带将步骤(1)配置好的脱硫增效剂输送至相对应的储料库;。(8)专业优化:专业优化:智能决策系统dss会将所有与脱硫相关作业信息(so2浓度、脱硫效率、增效剂类型、加料周期和加料量等)汇总形成大数据库,授权给企业分析端口比如电脑、手机使用,专业人员可以对作业数据进行对比分析,根据实际信息制定更好的加料方案,对加料程序库和设备进行调整,一是不同工况下依据实际生产针对常用配方a、替代配方b、速效配方c的加料周期和加料量进行优选,保证so2排放实时达标的同时最大化降低脱硫成本,优选后的加料周期和加料量参数在智能决策系统dss的加料程序库中进行设置,在以后相同工况下即可自动调取优选加料方案进行加料作业;二是由于增效剂的加入可以提高石灰石利用率和脱硫效率,降低石灰石的消耗量,因此根据增效剂使用情况可以选择性的在实际生产中关闭一部分浆液循环泵和增压风机,降低全年电耗成本同时减少石灰石原料使用量。实施例2一种湿法脱硫增效剂的智能加料控制方法,与所述实施例1不同的是步骤(5)和步骤(6),以下是对步骤(5)和步骤(6)的详细说明:(5)反馈循环:采用加料方案ii期间,在线烟气监测装置将实时负荷、烟气量、脱硫前后so2含量、脱硫效率、加料方案等新的工况信息反馈给智能决策系统dss。(6)反馈循环处理:此时电网需要锅炉在350mw(<400mw)低负荷下长时间运转,则相比于450mw负荷时烟气量会有明显降低,so2含量会一直低于正常范围限值1200mg/nm3。智能决策系统dss对比上述工况以及加料方案ii分析,发现长时间so2含量低,继续长时间使用常用配方a会导致脱硫成本增高、性能浪费,替代配方b适用于低负荷(<400mw)条件下使用,此时需采用替代配方b以应对so2浓度持续降低情况,保证so2排放达标的同时最大程度降低脱硫成本,智能决策系统dss根据实时工况信息确定替代配方b的加料方案iv:由人工或者加料程序设定替代配方b的加料周期以及加料量等参数,传递给分布式控制系统,并重复(4)的步骤进行替代配方b的加料方案iv的加料作业实施例3一种湿法脱硫增效剂的智能加料控制方法,与所述实施例1不同的是步骤(5)和步骤(6),以下是对步骤(5)和步骤(6)的详细说明:(5)反馈循环:采用加料方案iii期间,在线烟气监测装置再将实时负荷、烟气量、脱硫前后so2含量、脱硫效率、加料方案等新的工况信息反馈给智能决策系统dss。(6)反馈循环处理:此时电网需要锅炉高负荷550mw(>400mw)长时间运转,则相比于450mw负荷时烟气量会有明显增加,so2含量会一直超过正常范围限值1800mg/nm3。智能决策系统dss对比分析上述工况以及加料方案iii,发现长时间so2含量高,因为常用配方a所能提升的脱硫效率有限,继续使用常用配方a会导致so2排放不达标,此时需要采用用速效配方c以应对so2浓度持续升高情况,智能决策系统dss根据实时工况信息确定速效配方c的加料方案v:由人工或者加料程序设定速效配方c的加料周期以及加料量等参数,传递给分布式控制系统,并重复(4)的步骤进行速效配方c的加料方案v的加料作业。结合图3可知,在本发明配套的增效剂使用情况下,采用本发明的智能加料控制系统及方法,脱硫效率有了极大的提高与改善。以上实施例仅为最佳举例,而并非是对本发明的实施方式的限定。除上述实施例外,本发明还有其他实施方式。凡采用等同替换或等效变换形成的技术方案,均落在本发明要求的保护范围。当前第1页12