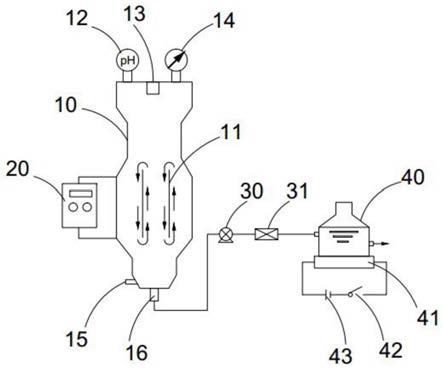
[0001]
本发明涉及一种应用于两相分配生物反应器的在线回收工艺,属于生物技术领域的用于废气处理的装置,特别适用于以纳米磁性硅油为非水相的两相分配生物反应器的废气处理装置。
背景技术:[0002]
在工业发展的过程当中会产生大量的工业废气,在这些废气中往往存在疏水性vocs组分,亟需高效的治理技术。生物法是基于微生物的代谢活动降解有毒有害污染物,其对低浓度废气的处理在环境友好性、运行费用、可处理废气量等方面具有明显的优势。然而,传统的生物法在降解水溶性差的有机污染物时往往难以达到理想的效果。废气生物净化是一个涉及气、液、生物膜相传质与生化降解的复杂过程。对于医药、化工等行业广泛存在的疏水性有机污染物,微生物降解过程由于气液相间与液相到生物相的传质限制,污染物去除效果较差,从而严重制约了生物法在该类废气中的推广应用。根据“相似相溶”理论,若在反应体系(水相)中添加非水相介质(nap)构成两相分配体系(tppb),由于疏水性有机污染物可快速溶解于nap,其从气态到nap的传质过程得到明显增强,表观去除速率显著提高;吸收至nap中的有机污染物也可缓慢释放至水相,从而为微生物提供代谢活动所必需的碳源。因此针对疏水性的vocs,采用基于nap的两相分配体系用于处理疏水性废气,可以有效的净化废气。
[0003]
硅油是一种稳定性高、生物相容性好的非水相介质,但存在回收难、易乳化等缺点,尚难以在两相反应体系中进行规模化应用。
技术实现要素:[0004]
为了解决现有技术的不足,本发明的目的在于提供一种基于磁性硅油的两相分配生物反应的在线回收工艺,对反应器内菌体生长无影响,实现了实现反应器内磁性硅油的较高次数的回收和添加,并且减少了磁性硅油的损耗量,所回收的磁性硅油对dcm有较高的降解效率。
[0005]
本发明为实现上述目的所采取的技术方案为:一种应用于两相分配生物反应器的硅油在线回收装置,包括:
[0006]
反应器本体,
[0007]
吸收容器,吸收容器设于反应器本体一侧,吸收容器通过连通管体与反应器本体连通;
[0008]
反应器本体底部分别设有气相入口和液相进出口,液相进出口和连通管体连通,连通管体上还设有泵体和流量控制器;
[0009]
吸收容器底部设有磁场产生装置,磁场产生装置包括设置在吸收容器底部的吸盘式电磁铁,吸盘式电磁铁通过线路连接开关和电源。本发明通过在反应器内放入纳米磁性硅油为助剂的方式,在进行更换营养液的过程中通过设置在吸收容器底部的磁场产生装置
产生磁吸力将纳米磁性硅油吸附,实现实时在线回收磁性硅油,减少磁性硅油的回收时的损失量,从而提高其利用率和利用次数,这样将磁场产生装置设置在反应器本体外防止其对反应器本体内菌体生长的不良影响,且避免磁力引起任何与反应器本体内发热而导致需要散热和传质的问题。
[0010]
根据本发明一实施方式,反应器本体上部依次设有气相出口、ph测控器和微量酸碱添加器。微量酸碱添加器和与其连接泵连接的软管管道可任意调节长短。通过微量酸碱添加器来调节ph,开设的气相出口便于反应器本体内气体从反应器本体上部快速排出。
[0011]
根据本发明一实施方式,反应器本体的夹套层连接有冷凝水控制装置,反应器本体内设竖直设置的导流板体。通过冷凝水控制装置控制反应器运行的温度,工业废气通过空气泵鼓入反应器,反应器内底部设有曝气头用于工业废气曝气使用,并且工业废气经反应器底部液相进出口的液体输入流体带动下,工业废气向上曝气过程中沿导流板体流动,在反应器的上升区范围部分气体通过气液分离区从反应器上部排出,部分气体进入下降区,随后又从底部进入上升区,形成稳定的气体循环,进而实现营养液、菌体、污染物在反应器内形成内部循环。
[0012]
根据本发明一实施方式,磁场产生装置是由吸盘式电磁铁连接稳恒电压直流电源而产生的磁场,磁场产生方式是纵向的。通过磁场产生装置可实现解决减少由于常规替换营养液时,磁棒吸附不完全,而导致磁性硅油的流失的问题。
[0013]
根据本发明一实施方式,气相入口通过管体连接进气控制组件,进气控制组件包括进气基件,进气基件一侧设有竖直设置且用于接入工业废气的第一通道,另一侧竖直设置且用于排出工业废气的第五通道,进气基件内设轴线水平的通气柱腔且进气基件内还开设有用于连通通气柱腔和第一进气通道的第二通道,第五通道与通气柱腔上端部连通。对于送入反应器本体的工业废气而言其具有一定的热量且送入的工业废气在不同工况下其温度存在波动,将其直接送入反应器本体的情况下将造成冷凝水控制装置的持续工作,能源过于浪费,通过设有的进气控制组件使工业废气依次通过第一通道、第二通道、通气柱腔、第五通道再送入反应器本体内,在工业废气通过第一通道和第二通道的过程中其流动路径改变以减缓工业废气进入第二通道和通气柱腔内的流动速度,这样有利于工业废气中的热量在上述通道内释放以及将热量传导至控制组件的各部件上,流经控制组件的工业废气可由吸收较多稳定热量的进气控制组件的部件进行换热使排出工业废气温度恒定,实现调节并稳定送入反应器本体内工业废气的温度,经过第二通道的工业废气在较大容积的通气柱腔内聚集实现稳定换热,在后续第二通道内不断输入的工业废气推压作用下使通气柱腔内的工业废气向第五通道内排出气体流速得到提高,实现排出气体流速提升。
[0014]
根据本发明一实施方式,通气柱腔内设同轴的活塞件,活塞件连接有柱状的伸缩柱,伸缩柱一端部伸出进气基件且伸出端连接铰接杆体,伸缩柱与进气基件为活动连接,铰接杆体与转动圆盘连接,工业废气不断通第一通道和第二通道进入通气柱腔内的过程中其流速降低不利于后期排气速度,通过设计活塞件来限制工业废气在通气柱腔内的充入量,随着工业废气的不断进入通气柱腔在内部压力以及后续不断注入的工业废气推力下推动活塞件在通气柱腔滑移,这样保持通气柱腔内的工业废气压力恒定,使工业废气进入第五通道的流速得到有效提高并且排气速度处于较快范围,通过在进气基件外设交接杆体和转动圆盘的方式可通过电机驱动转动圆盘来带动铰接杆体运动进而带动伸缩柱往复运动,这
样可主动控制通气柱腔内部可充填废气的量,通过外设的铰接杆体也可控制伸缩柱的伸缩范围,防止通气柱腔内气压过小。
[0015]
根据本发明一实施方式,活塞件和伸缩柱上同轴开设相互连通的第四通道,伸缩柱上还开设有与伸缩柱轴线垂直且与第四通道连通的第三通道,第四通道内设有与其等径的第二球体且第二球体背离活塞件方向通过第二弹簧与伸缩柱连接。在通气柱腔内设有的活塞件可有效保证通气柱腔内的工业废气压力,通过开设的第四通道来使部分工业废气排至活塞件后侧的通气柱腔内这样避免活塞件前部的通气柱腔内工业废气压力过大或者在送入工业废气过量的情况下通气内腔压力无法控制,设有的第四通道配合第三通道来实现将部分废气排放至第五通道内,并且需要足够强的气压驱使第二球体对第二弹簧施加相应压力来实现第四通道和第三通道的贯通,这样对于过大的气压而言可以起到调节通气柱腔内的压力,并且部分气体存留在活塞件后侧的通气内腔内对活塞件在通气内腔内形成一定的滑行阻力避免其滑移速度过快导致腔内压力失调。
[0016]
根据本发明一实施方式,第一通道内设有与其等径的第一球体,第一球体背离第一通道进口方向通过第一弹簧与其底部的进气基件连接。送入第一通道内的气体在其流速及气压不足的情况下难以推动第一球体,在其达到推动第一球体的情况下开放第二通道使工业废气流入通气柱腔内,保证足够的推动力用以推动活塞件。
[0017]
使用一种应用于两相分配生物反应器的硅油在线回收工装置的回收工艺,步骤如下:
[0018]-在反应器本体内加入无菌营养液、菌液和10%的磁性硅油,将工业废气送入反应器本体中,反应器本体内的营养液、菌体、污染物内部循环;以磁性硅油为助剂,以二氯甲烷为底物,以methylobacteriumrhodesianum h13为菌液接种。
[0019]-控制本体和流量控制器使需要更换的液体进入吸收容器内,启动磁场产生装置吸附磁性硅油,剩余废液排出吸收容器,待废液排放完毕后,加入新鲜营养液,关闭磁场产生装置,控制本体和流量控制器使吸收容器内液体送入反应器本体;
[0020]-重复上述步骤。磁性硅油为纳米磁性硅油。
[0021]
本装置减少了由于常规替换营养液时,磁棒吸附不完全,而导致磁性硅油的流失。在研究磁性硅油的量对污染物的影响时,且可以通过泵体和流量控制器来控制进入吸收容器里面磁性硅油的量,从而控制反应器内磁性硅油的量。
[0022]
根据本发明一实施方式,反应器本体内的气体流量控制在3l
·
min-1,停留时间控制在1.5min,温度通过与冷凝水控制装置相连的外层水浴夹层控制在30℃,ph通过微量酸碱自动添加器控制在7.5;优选的,在线回收两相体系中,以总体积计,磁性硅油体积终浓度为10%。
[0023]
本发明采用以上技术方案,与现有技术相比,具有以下优点:本发明通过在反应器内放入纳米磁性硅油为助剂的方式,在进行更换营养液的过程中通过设置在吸收容器底部的磁场产生装置产生磁吸力将纳米磁性硅油吸附,实现实时在线回收磁性硅油,减少磁性硅油的回收时的损失量,从而提高其利用率和利用次数,这样将磁场产生装置设置在反应器本体外防止其对反应器本体内菌体生长的不良影响,且避免磁力引起任何与反应器本体内发热而导致需要散热和传质的问题。
附图说明
[0024]
图1为应用于两相分配生物反应器的在线回收工艺一示意图;
[0025]
图2为纳米磁性硅油次数及其回收率;
[0026]
图3为不同纳米磁性硅油回收次数对二氯乙烷去除效果图;
[0027]
图4为应用于两相分配生物反应器的在线回收工艺二示意图;
[0028]
图5为进气控制组件内部示意图;
[0029]
图6为应用于两相分配生物反应器的在线回收工艺三示意图;
[0030]
图7为调节组件与反应器本体安装示意图;
[0031]
图8为调节组件结构示意图;
[0032]
图9为应用于两相分配生物反应器的在线回收工艺示四意图;
[0033]
图10为吸收容器内部结构示意图;
[0034]
图11为过滤基绳与饶接绳体连接示意图。
[0035]
附图标号:10-反应器本体;11-导流板体;12-ph测控仪;13-气相出口;14-微量酸碱自动添加器;15-气相入口;16-液相进出口;17-导流弧板;20-冷凝水控制装置;30-泵体;31-流量控制器;40-吸收容器;41-吸盘式电磁铁;42-开关;43-电源;44-三通阀;45-吸收瓶身;46-瓶底基件;47-集液管体;48-出液管体;49-第一换液通道;410-过滤柱腔室;411-第二换液通道;50-进气控制组件;51-第一通道;52-第一球体;53-第一弹簧;54-第二通道;55-活塞件;56-第三通道;57-第二弹簧;58-进气基件;59-转动圆盘;510-铰接杆体;511-伸缩柱;512-通气柱腔;513-第五通道;514-第二球体;515-第四通道;60-调节组件;61-液压缸;62-安装基板;63-滑移板体;64-形变薄板;65-第一驱动电机;66-第一套接块;67-配重块;68-第二套接块;69-转轴;70-过滤套桶;71-第一连接件;72-过滤基绳;73-饶接绳体。
具体实施方式
[0036]
以下结合具体实施方式和附图对本发明的技术方案作进一步详细描述:
[0037]
实施例1:
[0038]
一种应用于两相分配生物反应器的硅油在线回收装置,包括:
[0039]
反应器本体10,
[0040]
吸收容器40,吸收容器40设于反应器本体10一侧,吸收容器40通过连通管体与反应器本体10连通;
[0041]
反应器本体10底部分别设有气相入口15和液相进出口16,液相进出口16和连通管体连通,连通管体上还设有泵体30和流量控制器31;
[0042]
吸收容器40底部设有磁场产生装置,磁场产生装置包括设置在吸收容器40底部的吸盘式电磁铁41,吸盘式电磁铁41通过线路连接开关42和电源43。本发明通过在反应器内放入纳米磁性硅油为助剂的方式,在进行更换营养液的过程中通过设置在吸收容器40底部的磁场产生装置产生磁吸力将纳米磁性硅油吸附,实现实时在线回收磁性硅油,减少磁性硅油的回收时的损失量,从而提高其利用率和利用次数,这样将磁场产生装置设置在反应器本体10外防止其对反应器本体10内菌体生长的不良影响,且避免磁力引起任何与反应器本体10内发热而导致需要散热和传质的问题。
[0043]
反应器本体10上部依次设有气相出口13、ph测控器12和微量酸碱添加器14。微量
酸碱添加器14和与其连接泵连接的软管管道可任意调节长短。通过微量酸碱添加器14来调节ph,开设的气相出口13便于反应器本体10内气体从反应器本体10上部快速排出。
[0044]
反应器本体10的夹套层连接有冷凝水控制装置20,反应器本体10内设竖直设置的导流板体11。通过冷凝水控制装置20控制反应器运行的温度,工业废气通过空气泵鼓入反应器,反应器内底部设有曝气头用于工业废气曝气使用,并且工业废气经反应器底部液相进出口16的液体输入流体带动下,工业废气向上曝气过程中沿导流板体11流动,在反应器的上升区范围部分气体通过气液分离区从反应器上部排出,部分气体进入下降区,随后又从底部进入上升区,形成稳定的气体循环,进而实现营养液、菌体、污染物在反应器内形成内部循环。
[0045]
磁场产生装置是由吸盘式电磁铁连接稳恒电压直流电源而产生的磁场,磁场产生方式是纵向的。通过磁场产生装置可实现解决减少由于常规替换营养液时,磁棒吸附不完全,而导致磁性硅油的流失的问题。
[0046]
气相入口15通过管体连接进气控制组件50,进气控制组件50包括进气基件58,进气基件58一侧设有竖直设置且用于接入工业废气的第一通道51,另一侧竖直设置且用于排出工业废气的第五通道513,进气基件58内设轴线水平的通气柱腔512且进气基件58内还开设有用于连通通气柱腔512和第一进气通道51的第二通道54,第五通道513与通气柱腔512上端部连通。对于送入反应器本体10的工业废气而言其具有一定的热量且送入的工业废气在不同工况下其温度存在波动,将其直接送入反应器本体10的情况下将造成冷凝水控制装置20的持续工作,能源过于浪费,通过设有的进气控制组件50使工业废气依次通过第一通道51、第二通道54、通气柱腔512、第五通道513再送入反应器本体10内,在工业废气通过第一通道51和第二通道54的过程中其流动路径改变以减缓工业废气进入第二通道54和通气柱腔512内的流动速度,这样有利于工业废气中的热量在上述通道内释放以及将热量传导至控制组件50的各部件上,流经控制组件50的工业废气可由吸收较多稳定热量的进气控制组件50的部件进行换热使排出工业废气温度恒定,实现调节并稳定送入反应器本体10内工业废气的温度,经过第二通道54的工业废气在较大容积的通气柱腔512内聚集实现稳定换热,在后续第二通道54内不断输入的工业废气推压作用下使通气柱腔512内的工业废气向第五通道513内排出气体流速得到提高,实现排出气体流速提升。
[0047]
通气柱腔512内设同轴的活塞件55,活塞件55连接有柱状的伸缩柱511,伸缩柱511一端部伸出进气基件58且伸出端连接铰接杆体510,伸缩柱511与进气基件58为活动连接,铰接杆体510与转动圆盘59连接,工业废气不断通第一通道51和第二通道54进入通气柱腔512内的过程中其流速降低不利于后期排气速度,通过设计活塞件55来限制工业废气在通气柱腔512内的充入量,随着工业废气的不断进入通气柱腔512在内部压力以及后续不断注入的工业废气推力下推动活塞件55在通气柱腔512滑移,这样保持通气柱腔512内的工业废气压力恒定,使工业废气进入第五通道513的流速得到有效提高并且排气速度处于较快范围,通过在进气基件58外设交接杆体510和转动圆盘59的方式可通过电机驱动转动圆盘59来带动铰接杆体510运动进而带动伸缩柱511往复运动,这样可主动控制通气柱腔512内部可充填废气的量,通过外设的铰接杆体510也可控制伸缩柱511的伸缩范围,防止通气柱腔512内气压过小。
[0048]
活塞件55和伸缩柱511上同轴开设相互连通的第四通道515,伸缩柱511上还开设
有与伸缩柱511轴线垂直且与第四通道515连通的第三通道56,第四通道515内设有与其等径的第二球体514且第二球体514背离活塞件55方向通过第二弹簧57与伸缩柱511连接。在通气柱腔512内设有的活塞件55可有效保证通气柱腔512内的工业废气压力,通过开设的第四通道515来使部分工业废气排至活塞件55后侧的通气柱腔512内这样避免活塞件55前部的通气柱腔512内工业废气压力过大或者在送入工业废气过量的情况下通气内腔512压力无法控制,设有的第四通道515配合第三通道56来实现将部分废气排放至第五通道513内,并且需要足够强的气压驱使第二球体514对第二弹簧57施加相应压力来实现第四通道51和第三通道56的贯通,这样对于过大的气压而言可以起到调节通气柱腔512内的压力,并且部分气体存留在活塞件55后侧的通气内腔512内对活塞件55在通气内腔512内形成一定的滑行阻力避免其滑移速度过快导致腔内压力失调。
[0049]
第一通道51内设有与其等径的第一球体52,第一球体52背离第一通道51进口方向通过第一弹簧53与其底部的进气基件58连接。送入第一通道51内的气体在其流速及气压不足的情况下难以推动第一球体52,在其达到推动第一球体52的情况下开放第二通道54使工业废气流入通气柱腔512内,保证足够的推动力用以推动活塞件55。
[0050]
实施例2:
[0051]
使用一种应用于两相分配生物反应器的硅油在线回收工装置的回收工艺,步骤如下:
[0052]-装置用来处理二氯甲烷(dcm),在反应器本体10内加入无菌营养液、菌液和10%的磁性硅油,将工业废气送入反应器本体10中,反应器本体10内的营养液、菌体、污染物内部循环;以磁性硅油为助剂,以二氯甲烷为底物,以methylobacteriumrhodesianum h13为菌液接种;反应器本体10内的气体流量控制在3l
·
min-1,停留时间控制在1.5min,温度通过与冷凝水控制装置20相连的外层水浴夹层控制在30℃,ph通过微量酸碱自动添加器14控制在7.5;
[0053]-实验过程中每隔24h就要更换500ml的营养液来维持反应器的稳定运行,此时需要对磁性硅油回收,然后再更换营养液。控制本体30和流量控制器31使需要更换的液体进入吸收容器40内,启动磁场产生装置吸附磁性硅油,剩余废液排出吸收容器,待废液排放完毕后,加入新鲜营养液,关闭磁场产生装置,控制本体30和流量控制器31使吸收容器40内液体送入反应器本体;
[0054]-重复上述步骤,磁性硅油为纳米磁性硅油;
[0055]-反应器本体10,总体积为5l,工作体积为4.5l,罐体内径为0.120m,罐体高度为0.425m,导流筒内径为0.06m,导流筒长度为0.30m,反应器本体10底部的曝气头类型为微孔,以总体积计,磁性硅油体积终浓度为10%;
[0056]
本装置减少了由于常规替换营养液时,磁棒吸附不完全,而导致磁性硅油的流失。在研究磁性硅油的量对污染物的影响时,且可以通过泵体30和流量控制器31来控制进入吸收容器40里面磁性硅油的量,从而控制反应器内磁性硅油的量。
[0057]
本发明通过收集每次更换营养液次数,来记录磁性硅油的回收次数。并通过排放出的废液中含有的磁性硅油量,来记录磁性硅油的回收率。
[0058]
营养液终浓度组成:na
2
hpo
4 4.5g/l、kh
2
po
4 1.0g/l、(nh4)
2
so
4 0.5g/l、mgso
4
·
7h
2
o 0.2g/l、cacl
2 0.023g/l、微量元素母液1ml/l、ph 7.0,;其中微量元素母液浓度组成:
feso
4
·
7h
2
o 1.0g/l、cuso
4
·
5h
2
o 0.02g/l、h
3
bo
3 0.014g/l、mnso
4
·
4h
2
o 0.10g/l、znso
4
·
7h
2
o 0.10g/l、na
2
moo
4
·
2h
2
o 0.02g/l、cocl
2
·
6h
2
o 0.02g/l,溶剂均为去离子水。
[0059]
如图2所示,以第一次回收的磁性硅油作为对比,从图中可以看出,在回收使用了20次以后相比于第一次回收的纳米磁性硅油仍然能达到92.5%的回收率,可以看出这种两相分配生物反应器在线回收工艺既为回收纳米磁性硅油节约了时间,又减少了在更换营养液时的损失量。
[0060]
实施例3:
[0061]
不同运行阶段的性能评估:分别向两个条件相同的反应器中以10%的体积分数向其中加入新的磁性硅油(a组)和回收20次的磁性硅油(b组),研究其对两相生物反应器中dcm去除性能的影响。其中两个反应器的气体流量都控制在3l
·
min-1,停留时间控制在1.5min,温度通过冷凝水控制装置控制在30℃,ph通过ph测控仪和控制酸碱度的微量酸碱自动添加器控制在7.5。反应器中不同阶段dcm浓度和相对应的去除率如图3所示。在两相期的运行前期阶段,dcm浓度维持在1000mg
·
m-3左右。可以从图3中发现,从第1天开始,a、b两组去除率都有个逐步提升的过程,其中a组(新的磁性硅油)的去除率逐渐提高到81%左右,而b组(第20次回收的磁性硅油)的去除率也提高到75%左右,该现象说明不管是加入新的纳米磁性硅油还是被回收20次的磁性硅油都对dcm有较好的降解效率。在反应器中dcm去除率稳定后,第8天开始进行两相中浓度梯度实验。随着实验的进行,可以发现两组反应器在相同的dcm进气浓度下,由627mg
·
m-3提升到9031mg
·
m-3,a组反应器中去除率由84%降低到47%,同时,b组中dcm去除率由81%降低到46%。a、b组最大的去除浓度分别可以达到4286mg
·
m-3和4172mg
·
m-3。结果表明,整个浓度提升的过程中,含磁性硅油的a组去除效率要略高于b组。另一方面,当两相组中dcm浓度提高到9000mg
·
m-3左右,a、b反应器中出现了去除浓度下降的情况。第18天开始,将反应器浓度调回1000mg
·
m-3,在反应器初始浓度下运行一段时间,观察反应器稳定运行情况,结果发现,两组反应器在高浓度调回来后能恢复到接近原来的降解性能,并能维持其稳定运行。
[0062]
结果表明,由于a、b两组中反应器控制条件一致,当dcm浓度维持在1000mg
·
m-3左右,两组两相反应器中去除浓度会随之上升,且都对dcm有较高的去除效率,相对地,随着进气浓度的提高,两组去除效率都在下降。反应器中a组的去除效率要略高于b组可能是因为磁性硅油在回收过程中会溶出少量的铁,但从图中可以看出,回收20次的纳米磁性硅油仍能维持反应器运行性能,表明在线回收工艺中回收的纳米磁性硅油能满足反应器长期运行。
[0063]
实施例4:
[0064]
本实施例在实施例1的基础上优化方案如下:反应器本体10内导流板11上下部分别对应设有半弧形状的导流弧板17,反应器内的气液在反应器内所形成的循环流动可能受底部曝气气体以及底部上升的水体影响而破坏循环流动轨迹,通过设计导流弧板17的方式来降低反应器本体内底部向上流动的介质对所形成循环流动轨迹的影响,且导流板11上部的导流弧板17可对部分上升气流截留避免部分气体在循环上升流的作用下过快的气液分离降低废气停留时间。
[0065]
实施例5:
[0066]
本实施例在实施例1的基础上优化方案如下:反应器本体10内上部设有调节组件
60,调节组件60包括轴线水平设置的转轴69,转轴69两端部分别与反应器本体10两侧内壁连接,且转轴69一端部穿透反应器本体10与设置在反应器本体10外的第一驱动电机65连接,第一驱动电机65驱动转轴69旋转,转轴69与反应器本体10内连接处设有轴承以及密封圈,转轴69上同轴套接第一套接块66和第二套接块68,第一套接块66与第二套接快68之间具有间隔距离且第一套接块66设于靠近第一驱动电机65端,第一套接块66与转轴69连接方式为固接,第二套接块68与转轴69连接方式为活动连接,第二套接块68可相对转轴69滑移,第一套接块66上端和第二套接块68上端通过金属材质的形变薄板64连接,且形变薄板64中部固设有配重块67,第一套接块66下端和第二套接块68下端通过金属材质的形变薄板64连接,且形变薄板64中部固设有配重块67,转轴69远离第一驱动电机65段同轴连接有滑移板体63,滑移板体63设于第二套接块68和反应器本体10内壁之间,所述反应器本体10外设有液压缸61,液压缸61通过安装基板62固色在反应器本体10上,液压缸61的液压伸缩杆端部设于反应器本体10内,且液压伸缩杆与反应器本体10连接处设有密封圈,液压伸缩杆端部与滑移板体63固接,用于推动滑移板体63相对转轴69滑移。在反应器的上升区范围部分气体会通过气液分离从反应器上部排出,通过气相出口13排出反应器本体10,通过在反应器本体10上升区设置调节组件60这样对于反应器上部气液分离速度起到实际性控制,具体的,控制第一驱动电机65的旋转速度来控制转轴69的转速,进而控制转轴69带动形变薄板64和配重块67的转速,形变薄板64和配重块67的控制实现了控制反应器本体10上部液体与空气之间的接触面,形变薄板64和配重块67在旋转过程中可带部分液体短暂停留在反应器本体10上部中空部分与空气接触,这样扩大也液面与空气接触面来提高气液交换,对于形变薄板64和配重块67对反应器内介质的搅动作用对反应器下部介质流动可起到异响使气液在反应器内的上升速度提高,这样对于工业废气在反应器内的处理效率可以得到快速提升,当然这需要保证废气处理质量的情况下来提升第一驱动电机65的转速,在形变薄板64和配重块67旋转过程中可通过液压缸61来推动滑移板体63来推动第二套接块68位移,这样第二套接块68和第一套接块66之间的间距可以得到控制,第二套接块68和第一套接块66间距变化的过程中形变薄板64随之产生相应形变,在第二套接块68和第一套接块66两间距扩大过程中形变薄板64相对转轴69的间距缩小这样对于反应器内的介质搅动缩小,以降低对反应器中循环流动路径以及内部上述气液影响过大,第二套接块68和第一套接块66两间距的缩小过程中形变薄板64相对转轴69的间距扩大并且随配重块67的甩动进一步保证形变薄板64相对转轴69间距的扩大使气液在反应器内的上升速度提高,在配重块67的作用下两形变薄板64在甩动过程中形成菱形构造,这样对于上升气流而言其可较为集中聚集在菱形段,即配重块67对应方向,有利于集中排气且实现气液分离效率提高,以及页面水汽交换量的扩大,并且本申请的调节组件60适用于大分部存在气液交换的设备,如利用水体介质净化气体的设备。
[0067]
实施例6:
[0068]
本实施例在实施例1的基础上优化方案如下:吸收容器40包括吸收瓶身45,吸收瓶身45一侧连接有集液管体47,另一侧连接有出液管体48,吸收瓶身45底部设有瓶底基件46,瓶底基件46内设轴线平行的过滤柱腔室410,瓶底基件46内开设有第二换液通道411,第二换液通道411竖直开设与瓶底基件46内,第二换液通道411一端口与瓶底基件46底面平齐且贯通,另一端口与过滤柱腔室410连通,瓶底基件46上还开设有第一换液通道49,第一换液
通道49用于连通过滤柱腔室410和吸收瓶身45内腔室,连接有泵体30和流量控制器31的连通管体上还设有三通阀44,三通阀一端口通过连通管体与集液管体47连通,三通管另一端口通过连通管体与第二换液通道411连通,磁场产生装置设置在过滤柱腔室410下方。在需要更换营养液的过程中将反应器中的介质输送至第二换液通道411内,并同步启动磁性装置,这样将纳米磁性硅油吸附在过滤柱腔室410内而营养液通过第一换液通道49内送入吸收瓶身45内,由出液管体48排出,之后加入新的营养液后同时断开磁场产生装置电源将纳米磁场硅油送入吸收瓶身45内,在纳米磁性硅油及营养液进入吸收瓶身45的过程中经过过滤套筒70的过滤将杂质截留,实现高效分离回收利用。
[0069]
过滤柱腔室410内设有与其轴线同轴的过滤套筒70,过滤套筒70靠近第二换液通道411端口敞开设置,另一端口连接有第一连接件71且连接端口封口处理,过滤柱腔室410的一端口与瓶底基件46侧面平齐且贯通,第一连接件71与过滤柱腔室410贯通端口螺纹密封连接,过滤套筒70由过滤基绳72和饶接绳体73编织,过滤基绳72之间相邻平行排布设,饶接绳体73依次饶接过滤基绳72,上下饶接绳体73在过滤基绳72间隙处交错连接。通过对过滤套筒70采用上述编织方法进行编织这样磁性硅油可通过过滤基绳72之间的间隙处通过过滤套筒70,在过滤基绳72间隙处有饶接绳体73交错连接来缩小过滤基绳72间隙范围,缩小过滤孔目,同时磁性硅油可沿上下交错的饶接绳体73之间的间隙流出过滤套筒70,这样避免了磁性硅油难以通过过滤套筒70造成堵塞或粘接在过滤套筒70的部件上的问题,同时又有效对颗粒杂质进行过滤。
[0070]
当然,上述说明并非对本发明的限制,本发明也不仅限于上述举例,本技术领域的普通技术人员在本发明的实质范围内所做出的变化、改型、添加或替换,也属于本发明的保护范围。