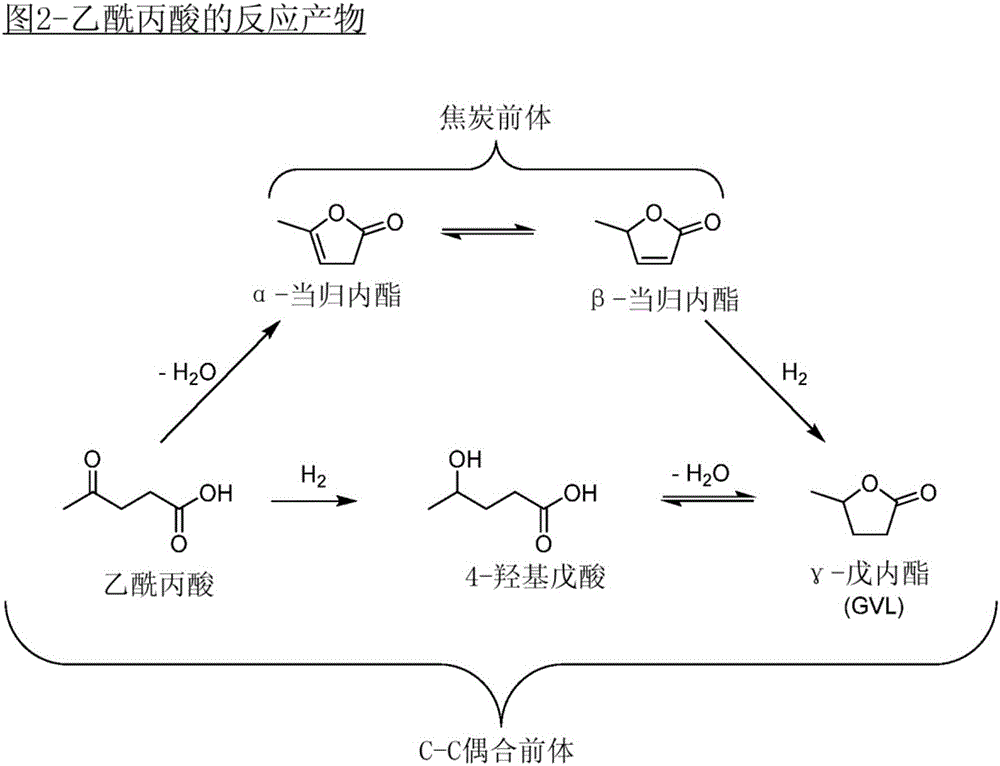
本发明涉及酮酸的催化转化,包括用于增加酮酸分子量的方法、通过这样的方法可得到的产物和这样的产物用于生产液体烃和/或汽油或柴油机燃料或基础油组分的用途。
背景技术:
:由生物质生产用作燃料或基础油组分和化学品的烃受到越来越多的关注,因为它们是由可持续的有机化合物源生产的。酮酸乙酰丙酸(LA,4-氧代戊酸)是许多可源自生物质的平台分子(platformmolecules)中的一种。其可由木质纤维素材料的戊糖和己糖二者以相对低的成本生产(参见图1)。使用乙酰丙酸作为平台分子的一些优点和缺点涉及由于它的酮基和酸官能团二者其被认为是活性分子的事实。乙酰丙酸的酯已被建议作为燃料组分以及柴油机燃料中的冷流添加剂,且特别地甲基和乙基酯已被用作柴油机燃料中的添加剂。γ-戊内酯(GVL),其可通过乙酰丙酸的还原得到,已被用作汽油中的燃料添加剂。GVL进一步还原为2甲基四氢呋喃(MTHF)提供了可与高达60%汽油混合的产品。由乙酰丙酸生产的戊酸烷基酯也已被建议作为生物燃料。通过多个催化路线,包括产生烯烃分布的方法,所述分布以C12为中心,涉及在第一反应器系统中将水性GVL转化为丁烯然后在第二反应器中经过酸性催化剂(例如70)进行低聚反应,乙酰丙酸也已被用于液体烃燃料的生产SerranoRuiz等人(Appl.Catal.,B,2010,100,184)通过在一个反应器中经过Ru/C催化剂将乙酰丙酸还原为GVL,然后在另一个反应器中在325-425℃,14bar,WHSV=0.8-0.5h-1下在Pd/Nb2O5+二氧化铈-氧化锆双床配置中在水和0.02MH2SO4中使40重量%GVL反应制备了C9-酮(5-壬酮)。使用多个反应器可能是有利的,因为其相比较于使用单个反应器可提供对工艺的更多控制。然而,多个反应器增加了过程步骤的数目,这增加了过程的资本支出。US2006/0135793A1(属于Blessing和Petrus)公开了乙酰丙酸在氢的存在下使用包含氢化金属的强酸多相催化剂例如离子交换树脂催化剂在60-170℃的温度范围内和1-200bar压力下(绝对压力)二聚为C10单元。该实例表明作为主要产物的乙酰丙酸二聚物(26%)和未反应的乙酰丙酸(70%)。由于离子交换树脂在大于150℃的温度下的热不稳定性,相对低的反应温度是优选的。技术实现要素:相比较于多个反应器,使用单个反应器可能有利的方面在于它们降低了反应步骤的数目并因此增加过程经济性。与升级的直接路线例如使用单个反应器相关的一些缺点为这些反应产生具有多于一个官能团的高度活性的中间体,其可进一步与其他不需要的分子反应。通过升级的直接路线降低不需要的分子通常引起所需产物组合物的更低收率。通常通过使用稀释的乙酰丙酸水溶液作为原料来实现抑制产生不需要的分子的副反应。因此,相比较于升级的直接路线,使用多个反应器或在单个反应器中的多个催化剂床的升级进料的间接路线在一些情况下可以是优选的。因此,存在对用于将乙酰丙酸和其他酮酸升级为较高分子量化合物的额外工艺的需要,所述较高分子量化合物适合用作例如燃料或基础油组分或化学品或作为在燃料或基础油组分或化学品的生产中的组分。特别地,存在对通过特别是(i.a.)提高所需组分或化学品的收率来降低过程成本和/或通过提高催化剂的寿命来降低整个催化剂的消耗这样的额外工艺的需要。本发明是考虑到上述现有技术做出的,且本发明的一个目的是提供能够将酮酸例如乙酰丙酸升级为较高分子量化合物的方法。本发明的另一个目的是以良好收率和低的过程成本提供酮酸至较高分子量化合物的升级。为了解决该问题,本发明提供一种用于增加酮酸的分子量的方法,该方法包括在反应器中提供包含至少一种酮酸的原料;和使原料经受一个或多个的C-C偶合反应的步骤,其中该C-C偶合反应在包含第一金属氧化物和第二金属氧化物的固体酸催化剂体系的存在下进行且其中在原料中所述至少一种酮酸的含量为至少30重量%。在使原料经受一个或多个C-C偶合反应的步骤中,所述至少一种酮酸经受与在原料中存在的另一种酮酸或酮酸衍生物的至少一次C-C偶合反应以增加所述酮酸的分子量。参与C-C-偶合反应的酮酸可为具有相同化学式的相同类型或不同类型。所述酮酸衍生物包括通过C-C-偶合反应或其他反应直接可从酮酸得到的所有化合物。所述酮酸衍生物可选自由酮酸的内酯和内酯衍生物,和戊酸组成的组。在C-C偶合反应中,所述至少一种酮酸与另一种反应物反应,在产物中形成新的碳-碳键。换句话说,使用酮酸作为直接前体(一步反应)且在单个反应器或单个催化剂床内增加酮酸的分子量。自然地,可发生进一步的C-C-偶合反应以进一步增加C-C-偶合反应产物的分子量。这些进一步的反应在相同(单个)反应器或催化剂床中进行。即,在本发明的第一方面,本发明的发明人发现,包含第一金属氧化物和第二金属氧化物的固体酸催化剂可在酮酸的强溶液(至少30重量%)中催化多种类型的酮酸的C-C-偶合反应,能够以良好的收率和在反应器中生产出酮酸的更高分子量化合物。使用酮酸的强溶液允许两种酮酸之间的C-C-偶合反应的高可能性,因此提供了所需产物的高收率和副产物低的量。所述(强)溶液的溶剂可为任何酮酸,优选所述“至少一种酮酸”。此外,也可使用水和/或有机溶剂。优选地,所述至少一种酮酸用作溶剂。所述催化剂体系的比表面积优选为10-500m2/g。通常通过测量氮的等温吸附线的BET方法测定比表面积(ASTMD-3663)。优选地,所述催化剂体系的酸位点总量为30-500μmol/g。可以使用NH3-TPD方法测量酸位点总数,它是一种用于确定酸位点数的常用方法并且已经公开于例如M.Lashdaf等人的MicroporousandMesoporousMaterials75(2004)149-158中。在NH3-TPD方法中,使用200℃的NH3的吸附温度。在本发明中,所述至少一种酮酸优选为γ-酮酸,最优选乙酰丙酸。除了所述至少一种酮酸,也可以使用一种或多种其他酮酸。在本发明的方法中使用的反应器可为流动反应器,优选连续流动反应器或间歇反应器,优选在搅拌下。从生产效率的观点看,流动反应器类型是优选的。当使用流动反应器时,催化剂体系优选固定在反应器中。本发明提供了用于工业规模生产更高分子量酮酸产物的方法,和因此,优选使用具有高浓度酮酸的原料进行所述C-C偶合反应。优选所述至少一种酮酸在原料中的含量为至少40重量%,优选至少50重量%,更优选至少70重量%,甚至更优选至少90重量%,和甚至更优选至少95重量%。如果原料中存在多种酮酸,“所述至少一种酮酸的含量”指所有酮酸的总含量。在该方面,应注意的是,本发明中的术语“原料”包括供应至反应器的所有材料,除了构成催化剂体系的材料外。因此,原料中所述至少一种酮酸的含量的计算不考虑催化剂的量。已发现水可以减少C-C偶合反应期间焦炭前体的形成,但是也已发现它会降低催化剂体系的活性。原料中水的含量为少于5.0重量%,更优选少于2.0重量%,甚至更优选少于1.0重量%。原料中水含量的计算不考虑催化剂的量。有多种金属氧化物可用在所述催化剂体系中以催化酮酸的C-C-偶合反应。优选地,所述第一金属氧化物包含W、Be、B、Mg、Si、Ca、Sc、Ti、V、Cr、Mn、Fe、Co、Ni、Cu、Zn、Ga、Sr、Y、Zr、Nb、Mo、Cd、Sn、Sb、Bi、La、Ce、Th之一的氧化物,且所述第二金属氧化物包含Zr、Ti、Si、Al、V、Cr之一的氧化物或它们的组合,第一金属氧化物不同于第二金属氧化物。金属氧化物的组合包括单个金属氧化物(固体溶液),混合的金属氧化物和负载的金属氧化物的混合物。优选地,催化剂体系包含第一金属氧化物和第二金属氧化物的混合物,其中第二金属氧化物是选自氧化锆、二氧化钛、二氧化硅、氧化钒、氧化铬的至少一种,优选氧化锆或二氧化钛。在本发明中,金属氧化物的混合物包括如下物质的混合物:单个金属氧化物材料,例如以粉末形式,混合的金属氧化物,其中所述金属氧化物形成共同的基质,和负载的金属氧化物,其中更加活性的金属氧化物沉积在作为载体的金属氧化物上。多种方法可用于制备金属氧化物的混合物。在混合的金属氧化物制备中,金属氧化物前体在转化成氧化物形式前从气相或液相溶液汇集。在负载的金属氧化物制备中,在金属氧化物前体转化成氧化物形式前,将金属氧化物前体以氧化物(或氢氧化物)形式从气相或液相溶液带到固体载体上。优选地,所述第一金属氧化物负载在第二金属氧化物载体上,其中所述第二金属氧化物优选选自由氧化锆、二氧化钛、二氧化硅、氧化钒、氧化铬组成的组,优选氧化锆或二氧化钛。优选地,负载在第二金属氧化物上的第一金属氧化物的金属原子的表面密度为0.5-20金属原子/nm2。以催化剂中金属氧化物的含量和催化剂体系的比表面积为基础计算催化剂体系中第一金属氧化物的金属原子的表面密度。优选地,所述催化剂体系包含负载在金属氧化物载体上的氧化钨、二氧化铈或二氧化硅,其中所述载体优选选自由氧化锆、二氧化钛、二氧化硅、氧化钒、氧化铬组成的组,优选氧化锆或二氧化钛。也可以使用选自上述第二金属氧化物的由多元氧化物构成的载体。优选地,第一金属氧化物是氧化钨、二氧化铈或二氧化硅,以金属氧化物重量相对于催化剂总质量计算,催化剂体系中第一金属氧化物的含量为1.0-40.0重量%,优选2.0-30.0重量%,进一步优选13.0-30.0重量%。通过测量催化剂中的金属含量并计算金属氧化物的含量来确定所述金属氧化物含量,其中如果一种金属存在多种(稳定的)氧化物,那么计算金属以最高的氧化值存在的金属氧化物的含量。优选地,以液相,与例如气相相反将所述原料引入反应器中。以液相将原料引入反应器中的一个优点是其不需要加热原料以制备气态流。此外,原料中固体组分的存在可导致催化剂的堵塞。因此,优选所述原料为液相且不包括相当大量的固体材料,例如,少于4.0重量%,优选少于1.0重量%,更优选少于0.2重量%的固体材料。在此,固体材料包括悬浮或分散在液相中的固体材料。可通过调节多个参数来控制C-C-偶合反应,包括通过选择反应条件例如:温度、压力和重时空速(WHSV)(kg原料/kg催化剂每小时)C-C-偶合反应优选在200-350℃,优选210-300℃,更优选220-280℃且甚至更优选220-260℃的温度下进行。发现该温度范围特别适用于得到高程度的中等分子量(C8-C25)反应产物,同时避免了过多聚合和催化剂焦化。优选地,C-C-偶合反应在0.5-100bar,优选1.0-50bar,更优选1.0-20bar的压力下进行。C-C-偶合反应优选在0.05h-1-2.0h-1,优选0.1h-1-1.8h-1,更优选0.2h-1-1.5h-1,最优选0.25h-1-1.25h-1的重时空速下进行。WHSV对所得材料的组成有影响,因为它决定反应物和催化剂的有效接触时间。已显示上述范围提供高程度的有利产物。C-C-偶合反应可在氢气存在下进行。在此情况下,将氢气作为原料的一部分供应至反应器,与剩余原料一起同时供应或者是经过反应器内的单独入口引入。也可能在无氢气的情况下进行C-C-偶合反应并通过不时将氢气添加至反应中或在洗涤步骤中加到混合物中回收催化剂。C-C-偶合反应可在100-3000Nl/l,优选200-2000Nl/l,更优选500-1800Nl/l且最优选500-1500Nl/l的进料比(H2/液体原料)下进行。在此,液体原料指在反应条件下主要以液体形式存在的原料。如果在氢气存在下进行C-C-偶合反应,所述催化剂体系也可包含至少一种选自元素周期表第VIII族,优选选自Co、Ni、Ru、Rh、Pd和Pt的氢化金属。在本发明的另一方面,提供了通过根据本发明的方法可得到的C-C偶合反应产物。在本发明的另一方面,提供了用于由含至少一种酮酸的原料制备烃的方法。在本发明的又一方面,提供了由根据本发明的方法可得到的烃组合物。附图说明图1示出了说明木质纤维素材料至乙酰丙酸转化的方案。图2示出了说明乙酰丙酸的一些反应产物,包括潜在的焦炭前体和潜在的C-C偶合前体的方案。该图不旨在覆盖乙酰丙酸的所有反应产物,也不旨在显示所有类型的焦炭前体。图2示出一种用于通过氢化反应减少当归内酯焦炭前体的可能机理,并且还示出了4-羟基戊酸的分子间酯,GVL,可以与4-羟基戊酸本身平衡。图3示出了进一步升级来自C-C-偶合反应的产物的可能工艺方案的概观。图4示出了制备和升级来自C-C-偶合反应的产物的可能工艺方案的概观。具体实施方案通过C-C-偶合反应增加酮酸分子量的挑战之一是产物中间体的高活性,这导致起始组分太高程度的低聚作用。本发明人已发现,在固体碱催化剂例如K2O/TiO2的存在下,酮酸特别地乙酰丙酸的低聚作用导致高的焦炭和焦油的形成,其通过抑制催化剂表面上的活性位点使催化剂中毒并最终导致反应器的堵塞。不束缚于任何理论,建议这是由于乙酰丙酸至更活性的前体例如当归内酯的反应而发生的,所述前体已知在大于200℃的温度下高度倾向于聚合。试图通过在稀的水溶液中进行反应以减少不希望的聚合反应并控制低聚反应和焦化。然而,发现加入水以抑制焦化反应会降低碱催化剂的性能,造成所希望的低聚反应产物的低收率。本发明是基于这样一个意外发现:可以通过在包含第一金属氧化物和第二金属氧化物的固体酸催化剂体系的存在下使酮酸经受C-C偶合反应,选择性地增加酮酸的分子量。已发现使用包含第一和第二金属氧化物的固体酸催化剂体系抑制反应中间体的焦化倾向并同时催化多种类型的C-C偶合反应,导致在溶液中在反应物之间形成新的碳-碳键。因此,本发明的一个方面是用于增加酮酸的分子量的方法,该方法包括在反应器中提供包含至少一种酮酸的原料;和使原料经受一个或多个的C-C偶合反应的步骤,其中该C-C偶合反应在包含第一金属氧化物和第二金属氧化物的固体酸催化剂体系的存在下进行且其中在原料中所述至少一种酮酸的含量为至少30重量%。本发明还涉及用于增加酮酸分子量的方法。酮酸是具有酮官能(>C=O)和羧酸(COOH)或羧酸酯(COO–)官能二者的有机分子。在本说明书中,特殊形式的酮酸包括其中酮官能为醛(CH=O)的实施方案。在本发明中,所述酮酸可例如为α-酮酸(如丙酮酸、草酰乙酸和α-酮戊二酸)、β-酮酸(如乙酰乙酸)、γ-酮酸(如乙酰丙酸)或δ-酮酸。所述酮酸可具有多于一个的酮官能团和多于一个的羧酸官能。优选地,所述酮酸仅具有一个酮官能团和一个羧酸官能团。图示1示出了根据本发明的示例性酮酸,例如其中n和m为整数,各自彼此独立地选自由0、1、2、3、4、5、6、7、8、9、10组成的组。优选地,所述酮酸是γ-酮酸,更优选乙酰丙酸(m=2,n=0)。优选地,原料中酮酸的分子量增加至少40%或更多。优选地,分子量增加为150-1000g/mol,例如160-500g/mol。当所述酮酸为C4-C7-酮酸时,分子量可增加至具有C8-C35碳链,例如C8-C30碳链的相应分子。例如,优选的是,超过50重量%的反应产物属于含酮酸的二聚、三聚、四聚、五聚和六聚产物的组。二聚、三聚、四聚、五聚和六聚产物指与一种或多种酮酸的二、三、四、五和六个分子偶合在一起相关的反应产物。在原料除酮酸还包含酮酸衍生物的情况下,所述二聚、三聚、四聚、五聚和六聚产物可额外地包含含一种或多种酮酸和/或其衍生物的混合的C-C偶合产物。二聚、三聚、四聚、五聚和六聚产物从至少一种酮酸衍生,例如至少两种酮酸、至少三种酮酸、至少四种酮酸、至少五种酮酸、至少六种酮酸。在本发明中,通过一个或多个C-C-偶合反应增加酮酸的分子量。许多C-C-偶合反应是本领域中已知的,且技术人员基于所提供的反应条件将能够鉴定这样的C-C-偶合反应。特别地,所述C-C-偶合反应可为酮基化反应或通过烯醇或烯醇化物中间体进行的反应。在本发明中,所述C-C-偶合反应可以选自含羟醛型反应和缩合反应、酮基化作用、其中C-C-偶合涉及烯烃的反应和其他低聚合反应的组。可使用两个相同类型的分子(即相同化合物)进行所述C-C偶合反应,或所述C-C偶合反应可为两个不同类型分子之间(即不同化合物之间)的交叉反应。催化剂的活性取决于催化剂表面上的活性位点数和催化剂的比表面积。优选地,所述催化剂体系的比表面积为10-500m2/g。具有该范围内的比表面积的催化剂体系已显示提供足够的反应性以得到高收率的所需的C-C-偶合反应产物,例如酮酸的二聚物、三聚物、四聚物、五聚物和六聚物,但同时使酮酸至焦炭前体的反应最小化。固体酸催化剂的活性还取决于酸位点的总量,其优选为30-500μmol/g的范围内。优选地,原料包含作为主要组分的一种或多种酮酸。例如,所述至少一种酮酸在原料中的含量为至少40重量%,例如至少50重量%,至少70重量%,更优选至少90重量%,或至少95重量%。优选地,原料中水的含量为少于5.0重量%,优选少于2.0重量%,更优选少于1.0重量%。优选地,原料中没有水。然而,在一些缩合反应中可以产生内部水。发现酮酸至所需C-C-偶合反应产物的转化随着原料中酮酸含量的增加而增加。发现水的存在降低乙酰丙酸至焦炭前体的反应,但水的添加也降低催化剂活性且降低所需C-C-偶合反应产物的收率。C-C-偶合反应产物的收率必须足够高以使经济可行的用于由酮酸生产燃料组分和化学品的工艺成为可能。所述原料可通过处理木质纤维素材料获得,且在本发明的方法中可直接使用这样处理的材料,或在用作原料之前将其纯化不同的程度。所述乙酰丙酸可例如使用US5608105中公开的生物精炼(Biofine)方法制备。优选地,原料包含乙酰丙酸,并且乙酰丙酸可与一种或多种其他酮酸或酮酸衍生物组合。所述酮酸衍生物可选自由酮酸的内酯和内酯衍生物,和戊酸组成的组。所述原料可包含乙酰丙酸与酮酸衍生物组合的混合物,例如基于原料总质量至少30重量%的乙酰丙酸和至少10重量%的乙酰丙酸衍生物。除酮酸和酮酸衍生物外,所述原料还可包含醛类,例如糠醛或羟甲基糠醛。优选地,本发明中使用的催化剂体系的第一金属氧化物包含W、Be、B、Mg、Si、Ca、Sc、Ti、V、Cr、Mn、Fe、Co、Ni、Cu、Zn、Ga、Sr、Y、Zr、Nb、Mo、Cd、Sn、Sb、Bi、La、Ce、Th之一的氧化物,且所述第二金属氧化物包含Zr、Ti、Si、Al、V、Cr之一的氧化物或它们的组合,第一金属氧化物不同于第二金属氧化物。金属氧化物的组合包括金属氧化物材料、混合的金属氧化物和负载的金属氧化物的固体混合物。更优选地,催化剂体系包含第一金属氧化物和第二金属氧化物的混合物,其中第二金属氧化物是选自氧化锆、二氧化钛、二氧化硅、氧化钒、氧化铬的至少一种,优选氧化锆或二氧化钛。催化剂体系可包含氧化钨、二氧化铈或二氧化硅和至少一种由氧化锆、二氧化钛、二氧化硅、氧化钒、氧化铬,优选氧化锆或二氧化钛中选择的氧化物的混合物。优选地,所述催化剂体系包含负载在金属氧化物载体上的氧化钨、二氧化铈或二氧化硅,其中所述载体选自由氧化锆、二氧化钛、二氧化硅、氧化钒、氧化铬组成的组,优选氧化锆或二氧化钛。这里,钨、铈或硅的氧化物代表具有更高活性的金属氧化物。已表明这些氧化物提供了良好的反应性质。此外,已显示上面提到的载体提供了良好的负载性能而不影响更活性部分的功能,包括协同交互作用。此外,上面提到的组合允许在酸性反应介质中长时间使用催化剂而不劣化和/或分解并因此允许降低的总催化剂消耗。优选地,以金属氧化物的重量相对于催化剂的总质量计算,催化剂体系中第一金属氧化物的含量为1.0-40.0重量%,优选2.0-30.0重量%,进一步优选13.0-30.0重量%。优选地,将原料提供至单个反应器中,或单个反应器床中。所述反应器应能够被加压和容纳原料和催化剂体系。所述反应器应具有用于供应气体和添加/取出原料的装置,例如一个或多个入口和/或出口。此外,优选存在用于控制压力和温度的装置。优选地,以液相,与例如气相相反将所述原料引入反应器中。以液相将原料引入反应器中的一个优点是其不需要加热原料以制备气态流。此外,原料中固体组分的存在可导致催化剂的堵塞。因此,优选所述原料为液相且不包括相当大量的固体材料,例如,少于4.0重量%,优选少于1.0重量%,更优选少于0.2重量%的固体材料。在此,固体材料包括悬浮或分散在液相中的固体材料。C-C偶合反应主要在液相进行,而不是气相,这意味着该反应是至少主要发生在液相中的催化剂上。C-C偶合反应可以完全在液相中进行。发明人发现,可通过调节多个参数来控制C-C-偶合反应,包括适当选择反应条件例如:温度、压力和重时空速(WHSV)和反应时间/停留时间。已发现反应温度对产物分布具有显著的影响。在低于200℃温度下,酮酸的C-C-偶合产物的收率可能太低,且在400℃以上的温度下由于形成焦炭和其他不需要的聚合产物,所述收率也可能减小。C-C-偶合反应优选在200-400℃,优选210-300℃,更优选220-280℃且最优选220-260℃的温度下进行。发现上述温度范围特别适用于得到高程度的中等分子量(C8-C30)反应产物,同时避免了过多聚合和催化剂焦化。由于大部分C-C偶合反应发生在液相中,合适地选择压力和温度以便保持反应物在液相中。有利地,C-C-偶合反应在0.5-100bar,优选1.0-50bar,更优选1.0-20bar的压力下进行。C-C-偶合反应优选在0.05h-1-2.0h-1,优选0.1h-1-1.8h-1,更优选0.2h-1-1.5h-1,最优选0.25h=-1.25h-1的重时空速(kg原料/kg催化剂*小时)下进行。WHSV对所得材料的组成有影响,因为它决定反应物和催化剂的有效接触时间。已显示上述范围提供高程度的有利产物。C-C偶合反应可以在作为原料的一部分供应至反应器中的氢气存在下进行。氢气可以与一种或多种其他气体,优选惰性气体如氮气、氩气、氦气或另一种惰性气体,或者对本发明的反应条件表现为惰性的气体混合。表现惰性被认为是该气体不应该在很大程度上参与作为反应成员,并且优选地惰性气体应当尽可能少参与,例如根本不参与。发现催化剂体系的性能可以通过在原料中添加氢进一步提高,减少低聚程度和酮酸向不希望组分的转化。氢的添加不会引入氢化活性,除非该催化剂体系包含氢化金属,但提出了修改催化剂体系一部分的可还原的金属氧化物的表面性质。C-C-偶合反应可在100-3000Nl/l,优选200-2000Nl/l,更优选500-1800Nl/l且最优选500-1500Nl/l的流量比(H2/液体原料)下进行。当在氢气存在下反应时,该催化剂体系除了第一和第二金属氧化物外可以包含至少一种氢化金属。氢化金属优选选自元素周期表第VIII族,优选选自Co、Ni、Ru、Rh、Pd和Pt。发现包含氢化金属的催化剂体系可以进一步提高催化剂的稳定性并抑制至不适合用作燃料组分或化学品的组分的低聚反应。在本发明的另一方面,提供了通过根据本发明的方法可得到的C-C偶合反应产物。该产物可直接用作燃料或基础油组分或化学品或作为在燃料或基础油组分或化学品生产中的中间体组分。如果需要的话,通过本发明的方法可得到的C-C偶合反应产物可进一步经受加氢脱氧(HDO)步骤以移除氧,这优选地产生完全脱氧的材料(即,不含氧原子的烃化合物)。所产生的烃可用作燃料或基础油组分或化学品或作为在燃料或基础油组分或化学品生产中的起始组分。所述加氢脱氧的产物也可进一步被异构化为异链烷烃。本发明的一个优势是由可再生材料制备的酮酸可被升级至更高分子量的烃和/或烃衍生物,其可被用作燃料或基础油组分或化学品或作为在燃料或基础油组分或化学品生产中的起始组分。C-C-偶合反应产物可被分馏以移除潜在的未反应的酮酸单体和其他低分子量组分例如来自反应产物的在C-C-偶合反应中形成的水和CO2,如在图3中所示。可通过任何常规的方法例如蒸馏来进行所述分馏。所述未反应的酮酸单体可任选地被回收并与第一反应器的进料结合。本发明的另一个方面涉及一种用于生产烃的方法,所述方法包括使用本发明的方法增加酮酸分子量以得到C-C偶合反应产物和使所述C-C偶合反应产物经受加氢脱氧步骤和任选地经受异构化步骤的步骤。在加氢脱氧步骤中使用的HDO催化剂可包含在支撑物上的氢化金属,诸如例如选自由Pd、Pt、Ni、Co、Mo、Ru、Rh、W或它们任何组合组成的组的HDO催化剂。所述加氢脱氧步骤可例如在100-500℃的温度和10-150bar的压力下进行。可使用任何常规的方法例如蒸馏将水和轻气体从HDO产物中分离。在移除水和轻气体后,HDO产物可被分馏至一种或多种适合作为汽油、航空燃料、柴油或基础油组分的馏分。可通过任何常规的方法例如蒸馏来进行所述分馏。任选地,部分HDO步骤的产物可被再循环和与HDO反应器的进料结合。本发明的另一方面涉及通过根据本发明的方法可得到的烃组合物。该产物可用作燃料或基础油组分或化学品或在燃料或基础油组分或化学品的生产中作为中间体组分。本发明的另一个方面涉及一种烃组合物,其包含至少30重量%的链烷烃,至少50重量%的环烷,少于10重量%的芳族化合物,并且其中该烃中的至少70重量%具有的碳原子数为8-10。这种烃组合物可以由根据本发明的方法得到。优选地,这种烃组合物被用作汽油燃料或汽油燃料组分。本发明的另一个方面涉及一种烃组合物,其包含至少60重量%的脂族烃,至少30wt%的芳族化合物,并且其中该烃中的至少70重量%具有碳原子数为9-24。这种烃组合物可以由根据本发明的方法得到。优选地,这种烃组合物被用作柴油燃料或柴油燃料组分。加氢脱氧步骤的产物也可在氢和异构化催化剂存在下经受异构化步骤。加氢脱氧步骤和异构化步骤二者可在同一反应器中进行。所述异构化催化剂可为贵金属双功能催化剂,例如Pt-SAPO或Pt-ZSM-催化剂。所述加氢脱氧步骤可例如在200-400℃的温度和20-150bar的压力下进行。优选仅部分HDO产物经受异构化步骤,特别地所述经受异构化的部分HDO产物可为在300℃或以上的温度下沸腾的重馏分。由加氢脱氧和/或异构化步骤可得到的烃产物可用作燃料或基础油组分或化学品或用作在燃料或基础油组分或化学品的生产中的中间体组分。通常使HDO产物经受异构化的选择高度依赖于最终产品所需的性能。在HDO产物包含大量的正链烷烃的情况下,HDO产物可经受异构化步骤以将至少部分的正链烷烃转化为异链烷烃以改善最终产品的冷性能。实施例材料作为催化剂例子,在乙酰丙酸的C-C偶合反应中可以使用具有表1所示组成的WO3/ZrO2、CeO2/ZrO2和SiO2/ZrO2。这些催化剂可以得自Saint-GobainNORPRO。表1.催化剂的组成WO3/ZrO2CeO2/ZrO2SiO2/ZrO2类型SZ6*143SZ6*191SZ6*152表面积,m2/g130110140WO3,重量%18CeO2,重量%18SiO2,重量%3.3原子密度3.6W/nm25.7Ce/nm22.4Si/nm2各自的氧化物的重量百分比通过催化剂的总质量来计算。第一金属氧化物的金属的原子密度已基于催化剂的比表面积和催化剂中各金属氧化物的含量被计算。通过催化剂生产商提供的比表面积已经通过测量氮的等温吸附线的BET方法测定(ASTMD-3663)。实施例1通过使用WO3/ZrO2-催化剂体系的C-C偶合反应增加乙酰丙酸的分子量WO3/ZrO2-催化剂(样品SZ6*143)的性能在连续的管式流动反应器测试运行中使用商用级乙酰丙酸(97%,Sigma-Aldrich)作为原料进行评估。C-C-偶合反应在约200℃至约240℃的温度和约20bar的压力下使用0.25、0.5和1.0h-1的重时空速(WHSV)进行。所述反应在氮气或氢气流(50ml/min)中进行以研究添加至进料中的氢气的影响。根据进料至容器中乙酰丙酸的量计算WHSV。对于不同条件下的反应,由液体收率确定所形成气体的量(气体=100-液体产物)。所述液体产物由包含在反应中形成的水的有机相组成。通过热重分析(TGA)获得对液体产物中水量的大致评估。通过HPLC分析确定LA(乙酰丙酸)和GVL(γ-戊内酯)在液体产物中的定量量。由GPC色谱图得到有机相中二聚物和低聚物的相对量。相对于干液体产物(不含水)计算包括未反应的LA的有机相的组成。表2和表3中示出了在氮气和氢气流中在WO3/TiO2催化剂体系上用于乙酰丙酸转化的有机相的产物收率和组成。表2.使用WO3/ZrO2-催化剂的工艺条件和产物收率。表3.使用WO3/ZrO2-催化剂的有机相中的产物分布在实验8中,在实验期间从反应混合物连续除去水,因此产物中的水量低于其他实验。实验8的产物在实施例3中用作用于加氢脱氧实验的C-C偶合反应产物原料。实施例2通过使用WO3/ZrO2-、CeO2/ZrO2-和SiO2/ZrO2-催化剂体系的C-C偶合反应增加乙酰丙酸的分子量在间歇反应器测试运行中使用商用级乙酰丙酸(97%,SigmaAldrich)作为进料对比WO3/ZrO2-、CeO2/ZrO2-和SiO2/ZrO2-催化剂的性能。在装入反应器之前将催化剂在120℃在氮气流中干燥过夜。反应器中装载5g催化剂和50g乙酰丙酸。在200℃和20bar在氮气下进行测试运行。通过GPC方法分析在200℃下2小时后取出的液体样品的组成。表4.有机相中的产物分布表4中乙酰丙酸、二聚物和低聚物的含量是基于GPC色谱中的峰面积。实施例3C-C偶合反应产物馏分加氢脱氧以生产烃在该实施例中,实施例1中实验8的C-C偶合反应产物经受加氢脱氧(HDO)步骤,以除去杂原子(特别是氧)和以稳定油产物。用作HDO反应器进料的C-C偶合反应产物含有24重量%的低聚物、35重量%的二聚物和41重量%的未反应的乙酰丙酸,其在进料到HDO步骤之前未被除去。在管式流动反应器中在硫化的NiMo/Al2O3催化剂存在下,在310℃温度和80bar压力下使用3300Nl/l的氢/进料(H2/进料)比和0.3h-1的重时空速(WHSV)进行加氢脱氧反应。根据进料到容器中的测试油的量计算WHSV和氢/烃比。表5中所示的HDO产物分布通过模拟GC-蒸馏确定和除氧的成功性由FTIR光谱进行评估。该HDO产物蒸馏成汽油和柴油馏分。汽油馏分的化学组成通过GC-MS和PIONA分析测定。在PIONA分析中,存在于样品中的化合物进行定量和分组为链烷烃、烯烃,环烷、芳族化合物和含氧化物。组分分析是作为碳数的函数表示。对于柴油馏分,测定芳族化合物和极性化合物的量。表5.加氢处理产物收率。存在于HDO进料中的未反应的LA被部分转化为戊烷,这是在气相中相对高的C5-C9收率看出的。氧气可以在脱水和HDO反应中作为H2O被除去,在脱羧反应中作为CO2被除去。除去的氧量(40重量%)与在LA中的氧含量(41重量%)对应良好。汽油馏分的PIONA分析表明,它含有37.4重量%的链烷烃(主要是异链烷烃),58.2重量%的环烷(主要是石蜡环烷)和4.1重量%的芳族化合物。还观察到少量的含氧化物(0.2重量%)。含氧化物被确定为是戊基醚(0.1重量%)和丙酮(0.1重量%)。汽油馏分的化合物主要分布在C8-C10范围中。碳含量为85.3重量%,氢含量为14.6重量%,相应于H/C-摩尔比为2.0。芳族化合物和极性化合物在柴油馏分中的含量通过HPLC方法进行分析,它表明柴油含有37.6重量%的芳族化合物和0.1重量%的极性化合物。柴油馏分的剩余部分(62.3重量%)为脂族烃。这些实施例表明,可以通过在包含第一金属氧化物和第二金属氧化物的固体酸催化剂体系的存在下进行的C-C偶合反应增加乙酰丙酸的分子量。这些实施例还表明,乙酰丙酸的C-C-偶合反应产物可以通过使乙酰丙酸的C-C-偶合反应产物在典型的HDO催化剂和氢存在下经受加氢脱氧反应而被进一步加工为具有典型的燃料组分例如汽油和柴油组分的沸点范围的烃。本发明涉及酮酸的催化转化,包括用于增加酮酸分子量的方法,所述方法包括在反应器中提供含至少一种酮酸的原料的步骤。然后将原料在包含第一金属氧化物和第二金属氧化物的催化剂体系存在下经受一个或多个C-C偶合反应当前第1页1 2 3