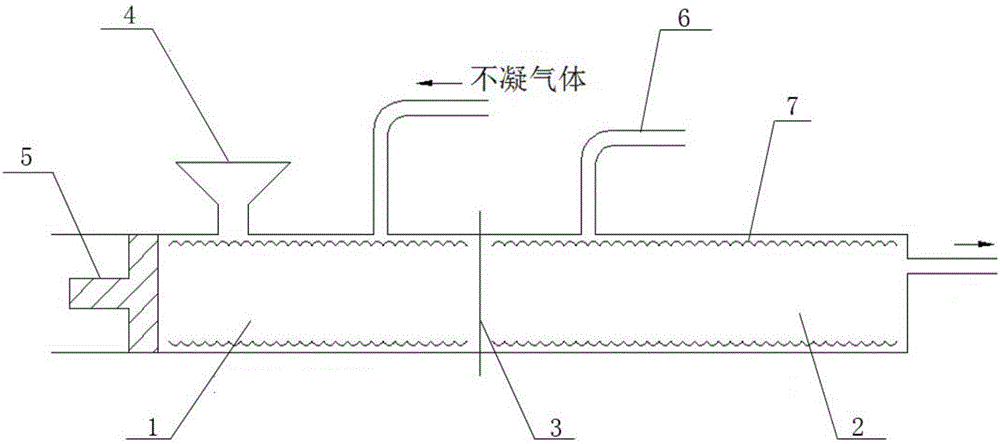
本发明涉及生物质能、固体废弃物利用
技术领域:
,尤其涉及到一种以秸秆、废塑料为原料进行高温热裂解产液体燃料的装置。
背景技术:
:时下,化石能源的储量日益减少,其带来的环境污染亦愈加严重,面对双重压力,寻找一种可持续的、无污染的能源是人类社会继续的关键之举。有研究发现秸秆-废塑料共裂解制备液体燃料的转化率可达50%-70%,这一发现不仅解决了秸秆和废塑料难以合理利用的难题,避免了处置过程中引发的污染问题,并且对缓解眼下的能源危机、从根本上解决我国的能源格局具有深远的意义。由此,秸秆-废塑料共热裂解产液体燃料作为一种可替代的清洁能源,已成为新能源领域研究和开发的热点之一。秸秆作为一种生物质资源常常以焚烧的这种不当的方法处理掉,不仅损失了大量的生物质能,同时也带来了严重的环境灾难;废塑料一旦进入环境,很难进行自然降解,而其巨量的排放已然成为经济社会向前发展的绊脚石。为应对来自这两方面的环境难题,以遵循生物质资源、固态废弃物资源化直接利用、节能减排的国际原则,国内陆续出现一些利用反应炉等设备对二者进行深度加工实现裂解产液体燃料的解决方法。目前研究发现,针对生物质资源、固态废弃物二者同时进行热裂解的反应装置不很常见,并且在生产过程中伴随传热效果不佳、能耗高、产油率低、品质不高的缺点。其中,授权公告号为CN102618312B的专利文献公开了一种生物质与废塑料共裂解制备燃料油的新方法,由于该工艺是将原料与催化剂直接混合进行,那么反应后催化剂与原料的分离以及催化剂再生就会非常困难,很难实现连续进料,如果再不进行后处理,势必导致很大的资源浪费和严重的环境污染。再者,授权公开号为CN201660599U的专利文献公开了一种卧式裂解炉,但该炉体只是单一的加热体系,无法实现对原料分段加热,这样就容易造成生物质、废塑料的极速碳化,直接造成产率低、产品品质不高的问题。技术实现要素:本发明提供了一种秸秆-废塑料裂解产液体燃料的装置,在很大程度上缓解了我国的能源危机。也为“秸秆、废塑料”这种“环境垃圾”找到一种合理的处置方法,为促进秸秆和废塑料高效资源化利用提供技术和设备,以解决上述
背景技术:
中提出的问题。为达到上述目的,本发明技术方案如下:一种秸秆-废塑料裂解产液体燃料装置,所述装置主要包括分段式热解反应系统、固气分离系统和冷凝回收系统;分段式热解反应系统包括低温预热系统和高温裂解系统;秸秆-废塑料颗粒经低温预热系统预热后,进入高温裂解系统进行裂解,产生的气体进入固气分离系统,残炭会被截留下来,挥发气体进入冷凝回收系统,收集可凝气体,可凝气体冷却后即为液体燃料,不可凝气体将通过回收管导入低温预热系统。所述分段式热解反应系统由低温预热室和高温裂解室构成,且二者之间以隔板分开;所述预热室的上方设有进料口,预热室远离隔板一侧设有活塞;所述高温裂解室靠近隔板一侧的上端开口处设有N2吹扫系统,高温裂解室远离隔板一侧末端设有气体出口,用于连接固气分离系统。所述分段式热解反应系统为卧式圆筒反应炉,包括圆筒式反应管、加热组件和保温层;其中,所述加热组件由不同线径的加热丝来完成,预热室使用相对较细的加热丝,而裂解室使用相对较粗的加热丝;所述保温层均匀铺设于炉壁与反应管间,其中加热丝内嵌于保温层内面,且与反应管接触。所述保温层为保温棉层,每段加热丝独立供电,分别控制,这样每段加热丝的温度可以灵活控制。所述反应炉内部设有热电偶,通过温控仪控制反应管外加热丝的加热功率,所述温控系统设于圆筒反应炉外壁,所述加热丝通过热瓦加热器实现程序升温。分段式热解反应系统的气体出口管段和固气分离系统的气体出口管段均设置电伴热;可有效避免气体过早凝结,导致液态燃料产率低及管道堵塞的问题。所述固气分离系统是由母部件和子部件构成,所述母子部件均为筒体,共同形成二级串联环形气旋管;其中,母部件上部呈圆柱形,下部呈圆锥形,子部件呈圆柱形,设于母部件的圆柱形内部,母子部件之间留有气流下行的环形通道;所述子部件下端部连接进气口,使进气在离心力的作用下螺旋上升。所述母部件的顶部设有封盖,封盖的中心设有出气口,出气口的口径小于子部件的筒径,略大于锥底出口的口径;所述母部件筒壁内嵌有加热丝,呈环形缠绕于筒壁,防止气体分离过程中过早冷凝。气体从固气分离系统的进气口进入后会先沿子部件螺旋上升进行一次分离,气体在子部件中上升是依靠离心力沿筒壁向上盘旋的,大量残碳被甩在筒壁上,在这个过程中大部分残碳会在重力作用下沉下去。当气体上升至子部件顶部时,封盖在气流的切线方向会给其一定的阻力(这里的切线方向解释:气流螺旋上升至接触到封盖,受离心力的作用其给予封盖的力并不是在竖直方向的,而是与气流方向相切的),一部分较干净的气体本身质量较轻会沿封盖水平方向移动,直到从出气口排出。而含有残碳的气体在封盖的阻力及自身重力作用下进入环形通道螺旋下降至圆锥体部分做二次分离,残碳下落,可凝气在锥筒反作用力下螺旋上升,由顶部排气口排出进入冷凝系统,继续二次分离。所述冷凝系统为低温萃取循环吸收塔,塔内设有多层堆积的PVP网格填充物,塔顶设有喷头和不凝气体出口,喷头连接有乙醇瓶,塔底设有进气口和出液口,出液口连接收集瓶。所述收集瓶中挥发的乙醇导入乙醇瓶循环利用;所述不凝气体出口处设有至少一个不凝气体外排通道且通道外包有充满自来水的导管。一种利用上述装置裂解秸秆-废塑料产液体燃料的方法,将已粉碎并得到充分混匀的秸秆-废塑料颗粒通过进料口进入低温预热室,预热至100-150℃时将混合物料推入高温裂解室进行快速裂解,产生的气体沿高温裂解室末端的出气口进入固气分离系统,残炭会被截留下来,挥发气体进入冷凝回收系统,可凝气体在塔内与乙醇接触,二者的混合物通过塔底的导管进入收集瓶,不可凝气体将通过回收管导入预热系统,而冷凝下来的液体作进一步地乳化提质即得到液体燃料。所述秸秆-废塑料颗粒直径控制在80-100目,含水量低于10%;所述秸秆与废塑料的质量比为(1∶5)~(5∶1)。所述混合原料中还加入Ni/HZSM-5(金属镍负载HZSM-5分子筛)或Ni/HZSM-22作为催化剂,所述催化剂的添加量为秸秆与废塑料总质量的5%~20%。本发明具有如下有益效果:本发明的裂解装置与传统的裂解装置相比,由于其采用了低温萃取循环吸收塔,喷淋的方式实现了二者的充分接触,进而将可凝气体快速冷凝下来。同时,二者混合物进入收集瓶后经轻微加热吹走乙醇并将其导入乙醇瓶,可再次循环利用。最后,将脱除乙醇后的液体燃料通入添加有十氢萘和正丁醇的乳化瓶中,实现产出燃料的初步乳化,在某种程度上提高高温下产出液体燃料的稳定性,并且综合利用了秸秆和废塑料共热裂解反应的协同促进作用,大大提高了液体燃料的产率。该工艺下的裂解装置具有更低的能耗及更佳的燃料品质。本发明结构合理科学,所述分段式裂解反应炉由低温预热室和高温裂解室构成,这种分段式加热方式避免了粉碎后的秸秆、废塑料迅速碳化的问题,从而保证更高的产率、更优的品质。本发明结构简单、操作方便、并且遵循了节能、高效、环保的设计原则,该装置的推广使用可在一定程度上产生良好的环境效益和经济效益。附图说明图1为本发明裂解装置的流程图。图2为本发明分段式裂解系统结构示意图。图3为本发明固气分离系统结构示意图。图4为本发明冷凝系统-低温萃取循环吸收塔结构示意图。具体实施方式下面将结合本发明实施例中的附图,对本发明实施例中的技术方案进行清楚、完整地描述。显然,所描述的实施例仅仅是本发明一部分实施例,而不是全部的实施例。基于本发明中的实施例,本领域普通技术人员在没有做出创造性劳动前提下所获得的所有其他实施例,都属于本发明保护的范围。实施例1一种秸秆-废塑料裂解产液体燃料装置,主要包括分段式热解反应系统、固气分离系统和冷凝回收系统。所述分段式热解反应系统由低温预热室1和高温裂解室2构成,且二者之间以隔板3分开;所述预热室1的上方设有进料口4,预热室远离隔板一侧设有活塞5;所述高温裂解室靠近隔板一侧的上端开口处设有吹扫系统6,高温裂解室远离隔板一侧末端设有气体出口,用于连接固气分离系统。所述分段式热解反应系统为卧式圆筒反应炉,包括圆筒式反应管、加热组件和保温层(保温棉层);其中,所述加热组件7由不同线径的加热丝来完成,预热室1使用相对较细的加热丝,而裂解室2使用相对较粗的加热丝;所述保温层均匀铺设于炉壁与反应管间,其中加热丝内嵌于保温层内面,且与反应管接触。所述反应炉内部设有热电偶,通过温控仪控制反应管外加热丝的加热功率,所述温控系统设于圆筒反应炉外壁,所述加热丝通过热瓦加热器实现程序升温。分段式热解反应系统的气体出口管段和固气分离系统的气体出口管段均设置电伴热。所述固气分离系统是由母部件8和子部件9构成,所述母子部件均为筒体,共同形成二级串联环形气旋管;其中,母部件8上部呈圆柱形,下部呈圆锥形,子部件9呈圆柱形,设于母部件的圆柱形内部,母子部件之间留有气流下行的环形通道;所述子部件9下端部连接进气口10,使进气在离心力的作用下螺旋上升。所述母部件8的顶部设有封盖11,封盖的中心设有出气口,出气口的口径小于子部件的筒径,略大于锥底出口的口径;所述母部件8筒壁内嵌有加热丝12,呈环形缠绕于筒壁。所述冷凝系统为低温萃取循环吸收塔,塔内设有多层堆积的PVP网格填充物13,塔顶设有喷头14和不凝气体出口,喷头14连接有乙醇瓶15,塔底设有进气口和出液口,出液口连接收集瓶16。收集瓶16中挥发的乙醇导入乙醇瓶15循环利用;所述不凝气体出口处设有3个不凝气体外排通道17且通道外包有充满自来水的导管。实施例2根据图1所示,使用本发明装置对秸秆-废塑料裂解制液体燃料工艺方法包括以下实施步骤:(1)按工艺流程连接好三部分系统,将已粉碎的粒径为80-100nm的生物质原料-秸秆(要求其含水量<10%)经进料口进入低温预热室,预热约10分钟;将秸秆与废塑料的质量比定为1∶1(A组)和3∶2(B组)以及4∶1(C组)做三组实验做对比研究。同时,每组原料中加入秸秆与废塑料总质量20%的Ni/HZSM-5作催化剂。(2)在高温预热室的底端通入N2,通过质量流量控制器控制适当的气速吹扫高温热解室,将其中空气排尽,使室内处于惰性气体氛围;同时热瓦加热器对加热丝开始加热升温,温度控制在500℃左右。(3)抽掉隔板,利用活塞将预热好的原料推送至N2氛围的高温裂解室,热解蒸气经裂解室右侧末端的气体出口通道进入固气分离系统,之后气体会先沿子部件螺旋上升进行一次分离,在这个过程中大部分残碳会在重力作用下沉下去,可凝气体则由顶部排气口排出;剩余的一小部分未被分离的气体沿母子部件之间的下行通道螺旋下降至圆锥体部分做二次分离,残碳下落,可凝气在锥筒反作用力下螺旋上升,由顶部排气口排出进入冷凝系统。使挥发气体中的残炭先被分离出来。(4)分段式热解反应系统的气体出口管段和固气分离系统的气体出口管段采用电伴热保证通道温度稳定在300℃,低温萃取循环吸收塔会快速将可凝气体冷凝下来,变成液态燃料。不可凝气体将进入低温预热室,使热量二次利用。(5)冷凝下来的液体生物燃料进入乳化瓶对其提质,得到相对稳定的燃料。所述乳化瓶内加有十氢萘和正丁醇。(6)通过对秸秆、废塑料在以上改进的裂解装置内实地实验研究,我们发现得到的液体燃料相比于传统裂解装置的产出油,在液体流动性上得到了很大的改善,并且相关数据表明,本装置对“秸秆、废塑料共裂解制备液体燃料”有了明显地提高,其中,最大转化率达到了75%左右,产率在65%左右,与传统设备相比均提高了将近20%,当然,这种良好的效果与催化剂致使的“原料协同裂解作用”也是分不开的。表1秸秆与废塑料在催化剂下裂解的转化率与产率m1/m2A组B组C组转化率(%)697562产率(%)636857表2秸秆与废塑料未添加催化剂的裂解转化率与产率m1/m2A组B组C组转化率(%)586554产率(%)495545注释:秸秆质量m1;废塑料质量m2;A组(1∶1);B组(3∶2);C组(4∶1);催化剂:Ni/HZSM-5。当前第1页1 2 3