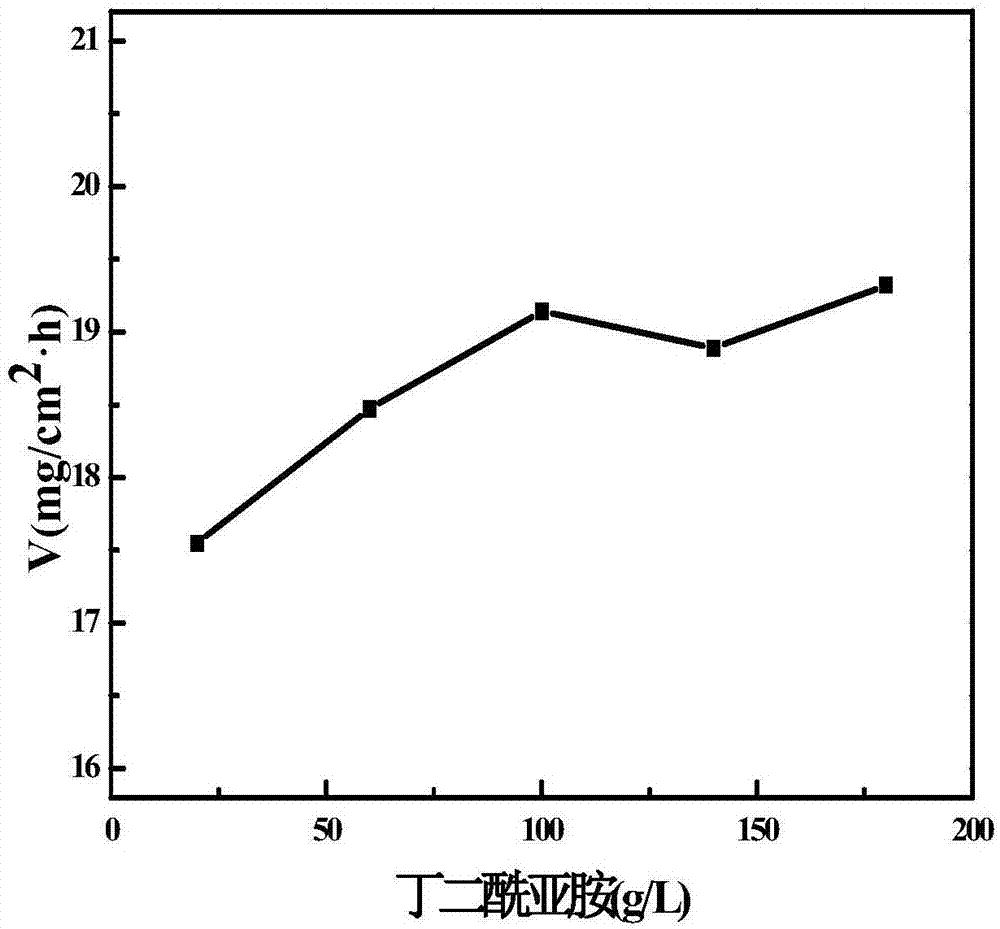
本发明属于电镀领域,尤其涉及银/石墨复合银镀溶液及其制备方法和电沉积工艺。
背景技术:
:高压隔离开关是电力系统中使用量最多的输变电设备之一,也是重要的控制和保护装置,其运行状况是否正常关系到整个电网的安全和稳定。操作失灵、绝缘子断裂、导电回路过热以及锈蚀是目前隔离开关运行中反映出来的4个主要问题。目前国内隔离开关动、静触头材质多选用铜,为保证良好的导电性表面一般进行镀银处理,即以纯银板作阳极,铜触头作阴极,在氰化镀银体系下进行电沉积。但是随着电力建设的迅猛发展,特别是超高压、特高压线路以及智能电网的建设,普通镀银层的使用寿命已经很难满足高压隔离开关等输变电设备的实际需求,普通镀银层质软,耐磨性差,抗变色及自清洁能力不强等问题亟待解决。而且,氰化物是剧毒,对生态环境和生产人员的健康都有极大的危害,同时对废液处理的技术和成本要求较高。目前,有学者提出采用新型镀银溶液制备银/石墨复合材料,但当前仍存在银/石墨复合镀层中石墨没有很好的结合到复合镀层中,造成复合镀层性能下降的技术问题。技术实现要素:有鉴于此,本发明公开的银/石墨复合银镀溶液及其制备方法和电沉积工艺能有效解决当前利用银/石墨复合材料电沉积得到的镀层性能难以达到电力设备需要的技术缺陷。本发明还提供了银/石墨复合银镀溶液,包括:水溶性的含银化合物、丁二酰亚胺、焦磷酸钾、石墨和吐温80。作为优选,上述银/石墨复合银镀溶液包括下列组分:次优选的,上述银/石墨复合银镀溶液,包括下列组分:更为优选,上述银/石墨复合银镀溶液,包括下列组分:作为优选,上述水溶性的含银化合物为硝酸银。其中,本发明的银/石墨复合银镀溶液的溶剂为水。更为优选的,所述银/石墨复合银镀溶液的溶剂为去离子水。本发明还公开了银/石墨复合银镀溶液的制备方法,包括以下步骤:1)将水溶性的含银化合物、丁二酰亚胺和焦磷酸钾混合,得到混合溶液;2)将步骤1)的混合溶液与石墨和吐温80混合,在超声条件使石墨溶解,获得银/石墨复合银镀溶液。作为优选,所述石墨为除杂后的石墨。作为优选,步骤1)所述混合溶液的ph为8.5-10.5。次优选的,步骤1)所述混合溶液的ph为9-10。更为优选,步骤1)所述混合溶液的ph为9。本发明还公开了一种电沉积工艺,包括以下步骤:1))制备银/石墨复合银镀溶液;2))设置铜片和银板;3))将步骤2)的铜片和银板置于步骤1)的银/石墨复合银镀溶液中进行电沉积,得到银/石墨复合镀液。作为优选,所述电沉积的电流密度为0.2-0.7a/dm2。次优选的,所述电沉积的电流密度为0.3-0.6a/dm2。更为优选,所述电沉积的电流密度为0.5a/dm2。作为优选,所述电沉积的搅拌速度为800-1400r/min。次优选的,所述电沉积的搅拌速度为1000-1200r/min。更为优选,所述电沉积的搅拌速度为1200r/min。作为优选,所述电沉积的电沉积的施镀温度为20-60℃。次优选的,所述电沉积的施镀温度为30-50℃。更为优选,所述电沉积的施镀温度为40℃。作为优选,所述电沉积的电沉积时间为30-120min。次优选的,所述电沉积的电沉积时间为60-120min。更为优选,所述电沉积的电沉积时间为120min。本发明提供的银/石墨复合银镀溶液,包括水溶性的含银化合物、丁二酰亚胺、焦磷酸钾、石墨和吐温80,在所述特定组分范围和特定的制备方法和特定的电沉积方法下石墨能均匀地机械嵌入到银/石墨复合镀层之中,其得到的银/石墨复合镀层都具有良好的表面形貌、截面形貌、镀层成分和组织结构,本发明的制备得到的银/石墨复合镀层的性能能达到当前电力设备需要。此外,本发明还公开了一种电沉积工艺,相比于传统的热加工方法,由于热加工方法需要在500℃以上的高温条件下才能进行,所以需要昂贵的生产设备,而本发明公开的电沉积工艺利用银/石墨复合银镀溶液进行加工,不需要高温条件,操作温度可直接在室温下进行,对生产设备要求较低,因此,该电沉积工艺的投资费用少、所需设备简单且易于控制。附图说明为了更清楚地说明本发明实施例或现有技术中的技术方案,下面将对实施例或现有技术描述中所需要使用的附图作简单地介绍。图1示硝酸银浓度对镀速的影响;图2示丁二亚酰胺浓度对镀速的影响;图3示焦磷酸钾浓度对镀速的影响;图4示ph值对镀速的影响;图5示不同ph值下阳极银板的外观;图6示石墨添加量对镀层厚度的影响;图7示石墨添加量对镀层表面形貌的影响;图8示电流密度对镀层厚度的影响;图9示电流密度对镀层表面形貌的影响;图10示搅拌速度对镀层厚度的影响;图11示搅拌速度对镀层表面形貌的影响;图12示施镀温度对镀层厚度的影响;图13示施镀温度对镀层表面形貌的影响;图14示电沉积时间对镀层厚度的影响;图15示电沉积时间对镀层表面形貌的影响;图16示镀银层与银/石墨复合镀层的表面形貌;图17示镀银层与银/石墨复合镀层的截面形貌;图18示镀银层表面与银/石墨复合表面镀层能谱分析;图19示镀银层与银/石墨复合镀层表面银和碳元素分布;图20示镀银层与银/石墨复合镀层的xrd图谱。具体实施方式本发明提供了银/石墨复合银镀溶液及其制备方法和电沉积工艺,能有效解决当前利用银/石墨复合材料电沉积得到的镀层性能难以达到电力设备需要的技术缺陷。下面将对本发明实施例中的技术方案进行清楚、完整地描述,显然,所描述的实施例仅仅是本发明一部分实施例,而不是全部的实施例。基于本发明中的实施例,本领域普通技术人员在没有做出创造性劳动前提下所获得的所有其他实施例,都属于本发明保护的范围。其中,以下实施例的原料和试剂均为市售。实施例1agno3是镀液中的主盐,用于提供ag+,镀液中主盐浓度的增加或减少,都会对电沉积过程以及镀银层的质量有直接的影响。试验组1:10g/l硝酸银、60g/l丁二酰亚胺、60g/l焦磷酸钾、ph值:9,制得镀银溶液;试验组2:20g/l硝酸银、60g/l丁二酰亚胺、60g/l焦磷酸钾、ph值:9,制得镀银溶液;试验组3:30g/l硝酸银、60g/l丁二酰亚胺、60g/l焦磷酸钾、ph值:9,制得镀银溶液;试验组4:40g/l硝酸银、60g/l丁二酰亚胺、60g/l焦磷酸钾、ph值:9,制得镀银溶液;试验组5:50g/l硝酸银、60g/l丁二酰亚胺、60g/l焦磷酸钾、ph值:9,制得镀银溶液;试验组6:60g/l硝酸银、60g/l丁二酰亚胺、60g/l焦磷酸钾、ph值:9,制得镀银溶液。将进行除油、打磨、超声波清洗、碱洗和酸洗的铜片基板和银片置于上述试验组1~试验组6的镀银溶液后,电沉积的参数统一设置为电流密度:0.5a/dm2;搅拌速度:1200r/min;施镀温度:30℃。表1为硝酸银浓度变化对镀银溶液制备的镀银层外观的影响,图1为硝酸银浓度变化对镀速的影响。当agno3浓度较低时,极限电流密度低,电沉积的速率较慢,镀银层的外观呈灰色。随着镀液中agno3浓度的升高,镀液导电性增强,电流效率和极限电流密度提高,银的沉积速率加快,镀层的外观也得到有效改善,变得均匀、光亮。但当agno3浓度高于50g/l时,镀液不稳定,银的沉积速率过快,导致镀层外观变得粗糙。这是因为晶核的生长速度大于银的成核速度,导致结晶粗大,体现为镀银层外观的粗糙。综合考虑镀银层的质量和电沉积速率,agno3浓度为30-40g/l时镀层外观也得到有效改善,变得均匀、光亮。表1硝酸银浓度变化对镀银层外观的影响组别试验组1试验组2试验组3试验组4试验组5试验组6银镀层外观#灰色,不光亮#半光亮#光亮#光亮#边缘粗糙#粗糙#实施例2丁二酰亚胺是镀液中的络合剂,络合剂有稳定镀液,提高镀液深镀能力和均镀能力以及细化晶粒、提高镀层质量的作用。试验组1:30g/l硝酸银、30g/l丁二酰亚胺、60g/l焦磷酸钾、ph值:9,制得镀银溶液;试验组2:30g/l硝酸银、60g/l丁二酰亚胺、60g/l焦磷酸钾、ph值:9,制得镀银溶液;试验组3:30g/l硝酸银、90g/l丁二酰亚胺、60g/l焦磷酸钾、ph值:9,制得镀银溶液;试验组4:30g/l硝酸银、120g/l丁二酰亚胺、60g/l焦磷酸钾、ph值:9,制得镀银溶液;试验组5:30g/l硝酸银、150g/l丁二酰亚胺、60g/l焦磷酸钾、ph值:9,制得镀银溶液。将进行除油、打磨、超声波清洗、碱洗和酸洗的铜片基板和银片置于上述试验组1~试验组5的银镀溶液后,电沉积的参数统一设置为电流密度:0.5a/dm2;搅拌速度:1200r/min;施镀温度:30℃。在碱性环境下丁二酰亚胺产生阴离子与ag+配位。如表2所示,丁二酰亚胺浓度较低时,镀银液制备的镀银层外观不光亮,呈灰白色,当丁二酰亚胺浓度达到90g/l时,镀层外观变得均匀、光亮。图2为丁二酰亚胺浓度变化对镀速的影响,从中可以看出,随着丁二酰亚胺浓度的增加,电沉积速率有所提升但并不明显,因此,丁二酰亚胺浓度为90g/l时,镀层外观变得均匀、光亮。表2丁二亚酰胺浓度对镀层外观的影响组别试验组1试验组2试验组3试验组4试验组5银镀层外观#灰白色#半光亮#光亮#光亮#光亮#实施例3焦磷酸钾在镀液中作辅助络合剂的同时也作为导电盐,能够有效提高镀液的导电能力,其浓度变化对镀层质量也有着重要影响。试验组1:30g/l硝酸银、60g/l丁二酰亚胺、0g/l焦磷酸钾、ph值:9,制得镀银溶液;试验组2:30g/l硝酸银、60g/l丁二酰亚胺、30g/l焦磷酸钾、ph值:9,制得镀银溶液;试验组3:30g/l硝酸银、60g/l丁二酰亚胺、60g/l焦磷酸钾、ph值:9,制得镀银溶液;试验组4:30g/l硝酸银、60g/l丁二酰亚胺、90g/l焦磷酸钾、ph值:9,制得镀银溶液;试验组5:30g/l硝酸银、60g/l丁二酰亚胺、120g/l焦磷酸钾、ph值:9,制得镀银溶液。将进行除油、打磨、超声波清洗、碱洗和酸洗的铜片基板和银片置于上述试验组1~试验组5的镀银溶液后,电沉积的参数统一设置为电流密度:0.5a/dm2;搅拌速度:1200r/min;施镀温度:30℃。如表3所示,在未加入焦磷酸钾时,镀银液制备的镀银层质量较差,外观为灰色,不光亮,添加焦磷酸钾后镀银层质量得到逐步改善,焦磷酸钾浓度为90g/l时,镀层均匀、光亮。同时从图3中可以看出,焦磷酸钾浓度的变化对电沉积速率影响不大,综合以上因素,焦磷酸钾的浓度为90g/l时,镀层均匀、光亮。表3焦磷酸钾浓度对银镀层外观的影响组别试验组1试验组2试验组3试验组4试验组5银镀层外观#灰色,不光亮#灰色,不光亮#半光亮#光亮#光亮#实施例4采用氢氧化钾调节镀银液的ph值,ph值对镀液的稳定性和镀层的质量影响非常大。试验组1:30g/l硝酸银、60g/l丁二酰亚胺、60g/l焦磷酸钾、ph值:8.5,制得镀银溶液;试验组2:30g/l硝酸银、60g/l丁二酰亚胺、60g/l焦磷酸钾、ph值:9.0,制得镀银溶液;试验组3:30g/l硝酸银、60g/l丁二酰亚胺、60g/l焦磷酸钾、ph值:9.5,制得镀银溶液;试验组4:30g/l硝酸银、60g/l丁二酰亚胺、60g/l焦磷酸钾、ph值:10.0,制得镀银溶液;试验组5:30g/l硝酸银、60g/l丁二酰亚胺、60g/l焦磷酸钾、ph值:10.5,制得镀银溶液。将进行除油、打磨、超声波清洗、碱洗和酸洗的铜片基板和银片置于上述试验组1~试验组5的银镀溶液后,电沉积的参数统一设置为电流密度:0.5a/dm2;搅拌速度:1200r/min;施镀温度:30℃。由于银离子与丁二亚酰胺的络合作用主要发生在碱性溶液中,当ph值低于8.5时,银离子未完全配位,镀液出现浑浊或灰褐色沉淀。提高镀液的ph值,电沉积速率增大,镀银液制备的镀银层外观变得光亮、均匀。但丁二酰亚胺随ph值的升高越容易发生水解,导致电沉积速率下降。试验发现ph值为10.5时,阳极钝化严重,银板表面出现咖啡色的粉末状沉淀物,如图5b)所示,此时所得镀层的表面也变得粗糙,综合考虑ph值应在9.0~10.0之间为宜。在配置镀银溶液时,加入氢氧化钾40g/l,镀银液ph值稳定在9.0左右,因此本发明取氢氧化钾用量在40g/l。表4ph值对银镀层外观的影响组别试验组1试验组2试验组3试验组4试验组5银镀层外观#半光亮#光亮#光亮#光亮#粗糙#实施例5试验组1:40g/l硝酸银、90g/l丁二酰亚胺、90g/l焦磷酸钾、5g/l石墨、0.5g/l吐温-80、氢氧化钾:40g/l,充分搅拌后超声1h,制得银/石墨复合银镀溶液;试验组2:40g/l硝酸银、90g/l丁二酰亚胺、90g/l焦磷酸钾、10g/l石墨、1g/l吐温-80、氢氧化钾:40g/l,充分搅拌后超声1h,制得银/石墨复合银镀溶液;试验组3:40g/l硝酸银、90g/l丁二酰亚胺、90g/l焦磷酸钾、20g/l石墨、2g/l吐温-80、氢氧化钾:40g/l,充分搅拌后超声1h,制得银/石墨复合银镀溶液;试验组4:40g/l硝酸银、90g/l丁二酰亚胺、90g/l焦磷酸钾、30g/l石墨、3g/l吐温-80、氢氧化钾:40g/l,充分搅拌后超声1h,制得银/石墨复合银镀溶液;试验组5:40g/l硝酸银、90g/l丁二酰亚胺、90g/l焦磷酸钾、40g/l石墨、4g/l吐温-80、氢氧化钾:40g/l,充分搅拌后超声1h,制得银/石墨复合银镀溶液。将进行除油、打磨、超声波清洗、碱洗和酸洗的铜片基板和银片置于上述试验组1~试验组5的银/石墨复合银镀溶液后,进行复合电沉积制备得到银/石墨复合镀层,复合电沉积的参数统一设置为电流密度:0.5a/dm2;搅拌速度:800r/min;施镀温度:30℃,电沉积时间30min。图6为镀液中石墨质量浓度的变化对镀层厚度的影响。从图中可以看出,银/石墨复合镀层的厚度随着镀液中石墨质量浓度的增加先增大后减小,在30g/l的条件下达到最大值。相对应的银/石墨复合镀层的表面微观形貌如图7所示,从中可以较为直观的看出银/石墨复合镀层中石墨含量的变化。当石墨质量浓度为5g/l时,镀液中悬浮的石墨微粒较少,通过吸附作用沉积到阴极表面的石墨量相应较少。随着镀液中石墨质量浓度的增加,被输送并吸附在阴极的石墨微粒增多,而石墨是导电微粒,银能够直接沉积在石墨微粒的表面,所以增大了电沉积速率,银/石墨复合镀层的厚度得到增加。但石墨质量浓度为10g/l~20g/l时,银/石墨复合镀层仍较为疏松,如图7b)、c)所示,疏松多孔的银/石墨复合镀层难以用作电接触材料。石墨质量浓度30g/l时制备的银/石墨复合镀层如图7d)所示,此时的银/石墨复合镀层较为致密,呈珊瑚状均匀地生长在基体表面。继续增加石墨微粒的质量浓度,银/石墨复合镀层的厚度反而减小。这主要是因为镀液中石墨微粒浓度太大不利于分散从而导致石墨微粒的团聚,同时微粒相互间的位阻效应使微粒的扩散迁移受到控制,阴极表面能够吸附的石墨微粒有限,从而影响电沉积速率,银/石墨复合镀层的厚度相应降低。因此,在复合电沉积过程中,镀液中的石墨微粒的添加量不宜过高。实施例6试验组1至试验组6:40g/l硝酸银、90g/l丁二酰亚胺、90g/l焦磷酸钾、20g/l石墨、2g/l吐温-80、氢氧化钾:40g/l,充分搅拌后超声1h,制得银/石墨复合银镀溶液。将进行除油、打磨、超声波清洗、碱洗和酸洗的铜片基板和银片置于上述试验组1~试验组6的复合银镀溶液后,进行复合电沉积制备得到银/石墨复合镀层。复合电沉积的参数设置为:试验组1:电流密度:0.1a/dm2;搅拌速度:800r/min;施镀温度:30℃,电沉积时间30min;试验组2:电流密度:0.2a/dm2;搅拌速度:800r/min;施镀温度:30℃,电沉积时间30min;试验组3:电流密度:0.3a/dm2;搅拌速度:800r/min;施镀温度:30℃,电沉积时间30min;试验组4:电流密度:0.4a/dm2;搅拌速度:800r/min;施镀温度:30℃,电沉积时间30min;试验组5:电流密度:0.5a/dm2;搅拌速度:800r/min;施镀温度:30℃,电沉积时间30min;试验组6:电流密度:0.6a/dm2;搅拌速度:800r/min;施镀温度:30℃,电沉积时间30min。图8为电流密度变化对复合镀层厚度的影响。从中可以看出电流密度对银/石墨复合镀层厚度的影响较大,随着电流密度的增大,银/石墨复合镀层厚度明显增加,但电流密度达到0.5a/dm2之后,厚度增加的趋势有所减缓。图9是不同电流密度下银/石墨复合镀层的表面形貌图。在低电流密度下,阴极过电位较小,表面活性部位少,镀层晶核形成几率小、形成速度慢,吸附到阴极表面的石墨微粒难以及时被银包覆实现共沉积,图9a)中可以清晰看到镶嵌在镀层中但未被完全包覆的石墨片层,此时对应的银/石墨复合镀层厚度较小且镀层中石墨微粒含量较少。随着电流密度增大,阴极的极化作用增强使沉积过电位增大,银的沉积速率加快,同时能够有效地包覆石墨微粒,银/石墨复合镀层的厚度和致密度逐渐增加,如图9b)~e)所示。然而,电流密度并非越大越好,在高电流密度下,浓差极化严重,银离子扩散至阴极附近的速度小于其消耗速度,电沉积速率增加较小,镀层厚度的增加减慢。一旦电流密度超过极限电流密度,阴极由于严重缺乏放电金属离子使析氢速度急剧增大,阴极附近的ph值迅速上升,电流效率降低,银/石墨复合镀层形貌变得粗糙甚至出现烧焦、发黑等现象。综合考虑,控制电流密度为0.5a/dm2,此时银/石墨复合镀层较为平整、致密。实施例7试验组1至试验组5:40g/l硝酸银、90g/l丁二酰亚胺、40g/l焦磷酸钾、20g/l石墨、2g/l吐温-80、氢氧化钾:40g/l,充分搅拌后超声1h,制得银/石墨复合银镀溶液。将进行除油、打磨、超声波清洗、碱洗和酸洗的铜片基板和银片置于上述试验组1~试验组5的复合银镀溶液后,进行复合电沉积制备得到银/石墨复合镀层。复合电沉积的参数设置为:试验组1:电流密度:0.5a/dm2;搅拌速度:600r/min;施镀温度:30℃,电沉积时间30min;试验组2:电流密度:0.5a/dm2;搅拌速度:800r/min;施镀温度:30℃,电沉积时间30min;试验组3:电流密度:0.5a/dm2;搅拌速度:1000r/min;施镀温度:30℃,电沉积时间30min;试验组4:电流密度:0.5a/dm2;搅拌速度:1200r/min;施镀温度:30℃,电沉积时间30min;试验组5:电流密度:0.5a/dm2;搅拌速度:1400r/min;施镀温度:30℃,电沉积时间30min。搅拌对于复合电沉积来说有着非常重要的作用。搅拌可以加快石墨微粒的运动,防止电沉积过程中出现团聚和沉降,从而使石墨微粒均匀分布在镀层中,同时搅拌还能有效缓解阴极附近的浓差极化,保证较高的电沉积速率和镀层质量。图10为搅拌速度变化对银/石墨复合镀层厚度的影响。从中可以看出银/石墨复合镀层的厚度随搅拌速度的增加先增加后减小,与此对应的复合镀层形貌如图11所示,银/石墨复合镀层先变得致密而后又出现疏松多孔的现象。这是因为搅拌速度较低时,石墨微粒不能充分分散在镀液中,能够被输送并吸附到阴极表面的石墨微粒较少,银/石墨复合镀层的厚度较小且表面疏松不平整,如图11a)、b)所示。随着搅拌速度的增大,银离子与石墨微粒的运动速率增大,石墨微粒被输送并吸附到阴极表面的几率大大增加,银在石墨微粒表面的沉积加快,银/石墨复合镀层的厚度随之增大,镀层中石墨含量也逐渐增多,同时镀层变得平整、致密,如图11c)、d)所示。但搅拌速度不宜过大,搅拌转速过大时液流以及微粒对阴极表面的冲刷作用太强,石墨微粒难以粘附到阴极表面或者在阴极表面呈弱吸附状态的石墨微粒容易被冲刷脱附,不利于银与石墨的共沉积,银/石墨复合镀层中石墨微粒含量减少,镀层厚度随之下降,镀层的质量也相对较差,如图11e)所示。综上所述,控制搅拌速度为1200r/min。实施例8试验组1至试验组5:40g/l硝酸银、90g/l丁二酰亚胺、90g/l焦磷酸钾、20g/l石墨、2g/l吐温-80、氢氧化钾:40g/l,充分搅拌后超声1h,制得银/石墨复合银镀溶液。将进行除油、打磨、超声波清洗、碱洗和酸洗的铜片基板和银片置于上述试验组1~试验组5的复合银镀溶液后,进行复合电沉积制备得到银/石墨复合镀层。复合电沉积的参数设置为:试验组1:电流密度:0.5a/dm2;搅拌速度:800r/min;施镀温度:20℃,电沉积时间30min;试验组2:电流密度:0.5a/dm2;搅拌速度:800r/min;施镀温度:30℃,电沉积时间30min;试验组3:电流密度:0.5a/dm2;搅拌速度:800r/min;施镀温度:40℃,电沉积时间30min;试验组4:电流密度:0.5a/dm2;搅拌速度:800r/min;施镀温度:50℃,电沉积时间30min;试验组5:电流密度:0.5a/dm2;搅拌速度:800r/min;施镀温度:60℃,电沉积时间30min。施镀温度对银/石墨复合镀层的影响如图12所示,随着温度的升高,复合镀层的厚度先增加后降低,在50℃时达到最大值。在温度较低时,升高温度有利于银离子的迁移和石墨微粒的运动,使到达阴极表面的银离子和石墨微粒增加,电流效率和极限电流密度增大,电沉积速度加快,从而使镀层的厚度和石墨含量得到增加,银/石墨复合镀层也越来越致密,如图13a)~c)所示。图13d)、e)分别是50℃与60℃下银/石墨复合镀层的形貌,从中可以看出温度达到50℃以上时,银沉积的结晶开始变粗,银/石墨复合镀层变得粗糙,镀层厚度也开始下降。这是因为温度过高时,银离子和石墨微粒运动速率进一步加快,阴极表面难以吸附高速运动的银离子和石墨微粒,加上粒子的冲刷作用,从而导致镀层变得疏松,镀层厚度下降,同时阴极极化的降低使得银/石墨复合镀层结晶粗大。另外,温度过高使得镀液挥发严重,影响了镀液有效成分的含量,这些多重因素的叠加,致使银/石墨复合镀层的性能变差。因此选择40℃为施镀温度,此时银/石墨复合镀层的厚度和表面形貌均较好。实施例9试验组1至试验组5:40g/l硝酸银、90g/l丁二酰亚胺、90g/l焦磷酸钾、20g/l石墨、2g/l吐温-80、氢氧化钾:40g/l,充分搅拌后超声1h,制得银/石墨复合银镀溶液。将进行除油、打磨、超声波清洗、碱洗和酸洗的铜片基板和银片置于上述试验组1~试验组5的复合银镀溶液后,进行复合电沉积制备得到银/石墨复合镀层。复合电沉积的参数设置为:试验组1:电流密度:0.5a/dm2;搅拌速度:800r/min;施镀温度:30℃,电沉积时间10min;试验组2:电流密度:0.5a/dm2;搅拌速度:800r/min;施镀温度:30℃,电沉积时间30min;试验组3:电流密度:0.5a/dm2;搅拌速度:800r/min;施镀温度:30℃,电沉积时间60min;试验组4:电流密度:0.5a/dm2;搅拌速度:800r/min;施镀温度:30℃,电沉积时间90min;试验组5:电流密度:0.5a/dm2;搅拌速度:800r/min;施镀温度:30℃,电沉积时间120min。图14是电沉积时间的变化对银/石墨复合镀层厚度的影响。从图中可以看出,电沉积时间对镀层厚度的影响较大,随着电沉积时间的延长镀层厚度呈直线增长。电沉积60min镀层厚度为10.5um,电沉积120min镀层厚度能达到24um左右。图3-19是不同电沉积时间下银/石墨复合镀层的表面形貌。图15a)、b)分别为电沉积10min、30min的镀层形貌,此时吸附并沉积到镀层中的石墨量较少,复合镀层疏松多孔,电沉积时间达到60min后复合镀层开始变得致密。但并不是电沉积时间越长越好,试验发现电沉积时间过长复合镀层表面边缘会出现褶皱起皮甚至脱落现象,同时电沉积时间过长还不利于石墨微粒在阴极表面沉积,因为石墨微粒难以在镀液中长时间悬浮分散,随着时间延长部分石墨微粒渐渐沉淀至镀液底部,从而导致银/石墨复合镀层中石墨的含量减少。综上所述,应严格控制电沉积的时间,确保获得性能良好的银/石墨复合镀层。实施例10试验组1:40g/l硝酸银、90g/l丁二酰亚胺、90g/l焦磷酸钾、30g/l石墨、3g/l吐温-80、氢氧化钾:40g/l,充分搅拌后超声1h,制得银/石墨复合银镀溶液。镀银溶液:30g/l硝酸银、60g/l丁二酰亚胺、60g/l焦磷酸钾、ph值:8.5,制得镀银层。将进行除油、打磨、超声波清洗、碱洗和酸洗的铜片基板和银片置于上述试验组1的复合银镀溶液和镀银溶液后,进行复合电沉积制备得到银/石墨复合镀层和镀银溶液。复合电沉积的参数设置为:试验组:电流密度:0.5a/dm2;搅拌速度:1200r/min;施镀温度:40℃,电沉积时间120min。图16是镀银层与银/石墨复合镀层的表面形貌。从图16中可以看出,镀银层表面非常光滑、平整和致密。银/石墨复合镀层表面粗糙呈珊瑚状结构,相较镀银层来说要更为疏松,但其表面并无明显毛刺和裂纹。图17为镀银层与银/石墨复合镀层的截面形貌,同样可以对比看出,镀银层的表面较为平整致密,而银/石墨复合镀层则较为疏松,但其与基体的结合良好,结合处没有任何缝隙与孔洞。为了确定镀层的主要成分,对镀层表面进行面扫描分析,eds扫描结果见图18。图18a)为镀银层的能谱分析,ag元素含量为100%,说明所制备的镀银层无任何杂质。图18b)为银/石墨复合镀层的能谱分析,所含主要元素为ag元素和c元素。其中c元素的含量达到了7.01%,初步证明是石墨微粒进入到了复合镀层中。图19为银/石墨复合镀层面扫描测得的ag元素和c元素的分布图,从图中可知,ag元素和c元素均匀分布在银/石墨复合镀层中,从而证明石墨微粒在复合镀层中沉积较为均匀,这有益于获得良好的镀层性能。实施例11将实施例10的试验组1和镀银溶液制备的银/石墨复合镀层和镀银层进行xrd分析,明确材料的微观组织结构。图20是镀银层与银/石墨复合镀层的xrd图谱。图20a)中五个衍射峰位置分别对应纯银的(111)、(200)、(220)、(311)以及(222)晶面,这些衍射峰的位置与面心立方结构的纯银表征图谱相吻合,镀银层的结晶表现在(111)面择优生长。在图20b)放大部分可以看到,银/石墨复合镀层的xrd图谱中在2θ=26.55°的位置出现了一个c(002)峰,可以认为是石墨的衍射峰。由于石墨颗粒在复合镀层中所占的质量分数很低,所以该衍射峰很弱。综合两个xrd图谱来看,所制备的银镀层纯度较高,而添加石墨颗粒并未改变银的晶体结构,银的择优生长方向仍为(111)面。以上实施例是本发明提供的银/石墨复合银镀溶液及其制备方法和电沉积工艺制备得到的银/石墨复合镀层和镀银层的性能测试分析,包括表面形貌、截面形貌、镀层成分、组织结构以及生长机制,采用本发明公开的银/石墨复合银镀溶液及其制备方法和电沉积工艺能有效解决当前当前利用银/石墨复合材料电沉积得到的镀层性能难以达到电力设备需要的良好导电、抗变色、耐蚀和耐磨的能力的技术缺陷。本发明提供的银/石墨复合银镀溶液及其制备方法和电沉积工艺制备得到的银/石墨复合镀层具有良好的镀层的表面形貌、截面形貌、镀层成分、组织结构以及生长机制。以上所述仅是本发明的优选实施方式,应当指出,对于本
技术领域:
的普通技术人员来说,在不脱离本发明原理的前提下,还可以做出若干改进和润饰,这些改进和润饰也应视为本发明的保护范围。当前第1页12