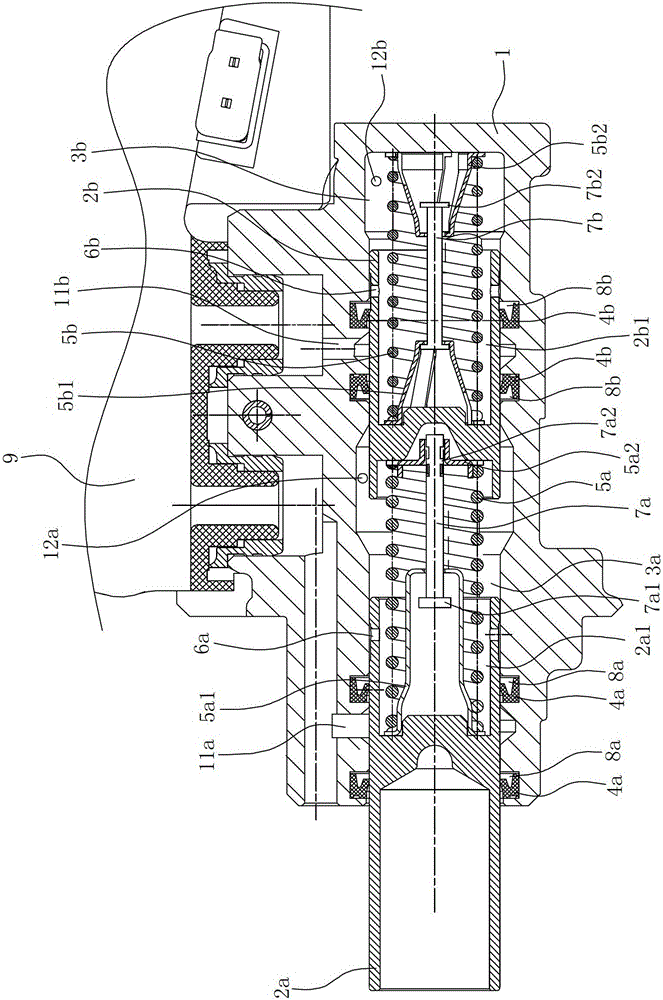
本发明属于汽车制动系统领域,尤其涉及一种柱塞式液压制动主缸。
背景技术:目前液压制动主缸多采用活塞式、中心阀式。工作时通过活塞的运动,带动皮圈工作,从而产生液压油的输出。这种制动主缸普遍存在结构复杂、零件数量繁多、回油流量限制等多种问题,故障率高、成本高,造成不必要的浪费。如一专利号为ZL02218139.3(公告号为CN2558559)的中国实用新型专利《中心阀式制动主缸》披露了这样一种汽车制动系统的中心阀式制动主缸,包括缸体、活塞、回位弹簧及中心阀,中心阀装配在活塞头端开设的台肩空腔内,它由阀顶杆、阀密封圈、阀回位弹簧、限位销构成,中心阀随活塞移动开启或关闭,控制制动腔的制动液压力。
技术实现要素:本发明所要解决的技术问题是针对上述现有技术现状而提供一种结构简单紧凑、零部件少的柱塞式液压制动主缸,其还具有工作稳定性好、输出效率高、降低产品重量和制造成本的优点。本发明解决上述技术问题所采用的技术方案为:一种柱塞式液压制动主缸,包括具有第一进油口、第二进油口、第一出油口和第二出油口的缸体;其特征在于:所述缸体内设有第一柱塞和第二柱塞,第一柱塞一端外露出缸体供与踏板相连;第一柱塞和第二柱塞之间形成第一压力腔,所述第一出油口与第一压力腔连通,第二柱塞后部形成第二压力腔,所述第二出油口与第二压力腔连通;第一柱塞的外周面与缸体内壁之间设有两个第一皮圈密封,该两个第一皮圈位于第一进油口的两侧,第二柱塞的外周面与缸体内壁之间设有两个第二皮圈密封,该两个第二皮圈位于第二进油口的两侧;第一柱塞和第二柱塞之间支承有第一弹簧,第二柱塞和缸体的后内壁之间支撑有第二弹簧;第一柱塞上开有第一补偿孔,第二柱塞上开有第二补偿孔,在第一柱塞和第二柱塞处于初始状态下,第一进油口通过第一补偿孔与第一压力腔连通,第二进油口通过第二补偿孔与第二压力腔连通,在第一柱塞和第二柱塞后移状态下,所述第一进油口和第一压力腔阻断,第二进油口和第二压力腔阻断。上述第一柱塞的后端具有第一凹腔,所述第一补偿孔设置在第一凹腔的侧壁上,且第一补偿孔有多个;所述第二柱塞的后端具有第二后凹腔,所述第二补偿孔设置在第二后凹腔的侧壁上,且第二补偿孔有多个。在柱塞上设置凹腔便于加工补偿孔,另外凹腔还给弹簧提供安装空间。上述第二柱塞的前端具有第二前凹腔,所述第一弹簧的前端通过第一前弹簧座支撑在第一凹腔的底部,第一弹簧的后端通过第一后弹簧座支撑在第二前凹腔的底部,所述第二弹簧的前端通过第二前弹簧座支撑在第二后凹腔的底部,第二弹簧的后端通过第二后弹簧座支撑在缸体的后内壁上。上述第一前弹簧座和第一后弹簧座之间通过第一连杆连接在一起,即第一连杆的前端活动穿过第一前弹簧座后通过第一连杆上的前挡肩与第一前弹簧座限位,第一连杆的后端活动穿过第一后弹簧座后通过第一连杆上的后挡肩与第一后弹簧座限位;所述第二前弹簧座和第二后弹簧座之间通过第二连杆连接在一起,即第二连杆的前端活动穿过第二前弹簧座后通过第二连杆上的前挡肩与第二前弹簧座限位,第二连杆的后端活动穿过第二后弹簧座后通过第二连杆上的后挡肩与第二后弹簧座限位。第一柱塞和第二柱塞通过连杆连接,保证第一柱塞和第二柱塞在静止状态下,两者相对位置不会改变,对各柱塞起到限位作用。上述缸体的内壁设有沿前后间隔设置的两个第一环形槽,该两个第一环形槽位于第一进油口的前后两侧,所述两个第一皮圈分别安装在所述两个第一环形槽内;所述缸体的内壁设有沿前后间隔设置的两个第二环形槽,该两个第二环形槽位于第二进油口的前后两侧,所述两个第二皮圈分别安装在所述两个第二环形槽内。由于皮圈安装在缸体内壁的环形槽内,这样即使柱塞前后滑移,也不会带动皮圈滑移,皮圈位置更为稳定,磨损少,保证制动主缸工作稳定性。与现有技术相比,本发明的优点在于:第二,取消传统制动主缸采用补偿孔和中心阀补油方式,而采用柱塞式补油;第二,缸体长度缩短,结构紧凑;第三,皮圈固定在缸体上,保证了工作的稳定性;第四,零数量较普通型结构减少了30%;多方面的创新保证了制动主缸的工作稳定性,提高了制动输出效率,降低了产品重量和制造成本。附图说明图1为本发明实施例的结构剖视图(活塞静止状态);图2为本发明实施例的结构剖视图(制动状态)。具体实施方式以下结合附图实施例对本发明作进一步详细描述。如图1、2所示,为本发明的一个优选实施例。一种柱塞式液压制动主缸,包括具有第一进油口11a、第二进油口11b、第一出油口12a和第二出油口12b的缸体1。第一进油口11a和第二进油口11b与油杯9连通,油杯始终对第一进油口11a和第二进油口11b进行补油。缸体1内设有第一柱塞2a和第二柱塞2b,第一柱塞2a和第二柱塞2b与缸体1内壁之间为间隙配合,并能相对缸体1前后滑移,第一柱塞2a一端外露出缸体1供与踏板相连。第一柱塞2a和第二柱塞2b之间形成第一压力腔3a,第一出油口12a与第一压力腔3a连通,第二柱塞2b后部形成第二压力腔3b,第二出油口12b与第二压力腔3b连通。第一柱塞2a的外周面与缸体1内壁之间设有两个第一皮圈4a密封,该两个第一皮圈4a位于第一进油口11a的两侧,第二柱塞2b的外周面与缸体1内壁之间设有两个第二皮圈4b密封,该两个第二皮圈4b位于第二进油口11b的两侧。缸体1的内壁设有沿前后间隔设置的两个第一环形槽8a,该两个第一环形槽8a位于第一进油口11a的前后两侧,两个第一皮圈4a分别安装在两个第一环形槽8a内;缸体1的内壁设有沿前后间隔设置的两个第二环形槽8b,该两个第二环形槽8b位于第二进油口11b的前后两侧,两个第二皮圈4b分别安装在两个第二环形槽8b内。第一柱塞2a和第二柱塞2b之间支承有第一弹簧5a,第二柱塞2b和缸体1的后内壁之间支撑有第二弹簧5b。第一柱塞2a上开有第一补偿孔6a,第二柱塞2b上开有第二补偿孔6b,在第一柱塞2a和第二柱塞2b处于初始状态下,第一进油口11a通过第一柱塞2a与缸体1内壁之间的间隙及第一补偿孔6a与第一压力腔3a连通,第二进油口11b通过第二柱塞2b与缸体1内壁之间的间隙及第二补偿孔6b与第二压力腔3b连通,在第一柱塞2a和第二柱塞2b后移状态下,第一进油口11a和第一压力腔3a之间被两个第一皮圈4a阻断,第二进油口11b和第二压力腔3b之间被两个第二皮圈4b阻断。第一柱塞2a的后端具有第一凹腔2a1,第一补偿孔6a设置在第一凹腔2a1的侧壁上,且第一补偿孔6a有多个;第二柱塞2b的后端具有第二后凹腔2b1,第二补偿孔6b设置在第二后凹腔2b1的侧壁上,且第二补偿孔6b有多个。第二柱塞2b的前端具有第二前凹腔2b2,第一弹簧5a的前端通过第一前弹簧座5a1支撑在第一凹腔2a1的底部,第一弹簧5a的后端通过第一后弹簧座5a2支撑在第二前凹腔2b2的底部,第二弹簧5b的前端通过第二前弹簧座5b1支撑在第二后凹腔2b1的底部,第二弹簧5b的后端通过第二后弹簧座5b2支撑在缸体1的后内壁上。第一前弹簧座5a1和第一后弹簧座5a2之间通过第一连杆7a连接在一起,即第一连杆7a的前端活动穿过第一前弹簧座5a1后通过第一连杆7a上的前挡肩7a1与第一前弹簧座5a1限位,第一连杆7a的后端活动穿过第一后弹簧座5a2后通过第一连杆7a上的后挡肩7a2与第一后弹簧座5a2限位;第二前弹簧座5b1和第二后弹簧座5b2之间通过 第二连杆7b连接在一起,即第二连杆7b的前端活动穿过第二前弹簧座5b1后通过第二连杆7b上的前挡肩7b1与第二前弹簧座5b1限位,第二连杆7b的后端活动穿过第二后弹簧座5b2后通过第二连杆7b上的后挡肩7b2与第二后弹簧座5b2限位。本柱塞式液压制动主缸的工作原理及过程如下:如图1所示,活塞静止时,在没有踏板力的作用下,第一进油口11a通过第一柱塞2a与缸体1内壁之间的间隙及第一补偿孔6a与第一压力腔3a连通,第二进油口11b通过第二柱塞2b与缸体1内壁之间的间隙及第二补偿孔6b与第二压力腔3b连通,通过第一补偿孔6a和第二补偿孔6b释放压力,使第一压力腔3a、第二压力腔3b分别与第一进油口11a和第二进油口11b保持大气压力状态。如图2所示,制动时,当踩下踏板工作时,第一柱塞2a和第二柱塞2b均后移,第一进油口11a和第一压力腔3a之间被两个第一皮圈4a阻断,第二进油口11b和第二压力腔3b之间被两个第二皮圈4b阻断,同时第一压力腔3a和第二压力腔3b中的第一弹簧5a和第二弹簧5b被压缩,容积也随之压缩,从而产生液压,分别从第一出油口12a和第二出油口12b输出液压油及压力,随着踏板力的增加,产生制动系统所需的压力。如图1所示,当踏板撤回时,第一柱塞2a和第二柱塞2b均前移回位,第一压力腔3a和第二压力腔3b中产生真空,当踏板力释放后,第一柱塞2a和第二柱塞2b移动至初始状态下,第二进油口11b通过第二柱塞2b与缸体1内壁之间的间隙及第二补偿孔6b与第二压力腔3b连通,产生制动液的补偿作用。