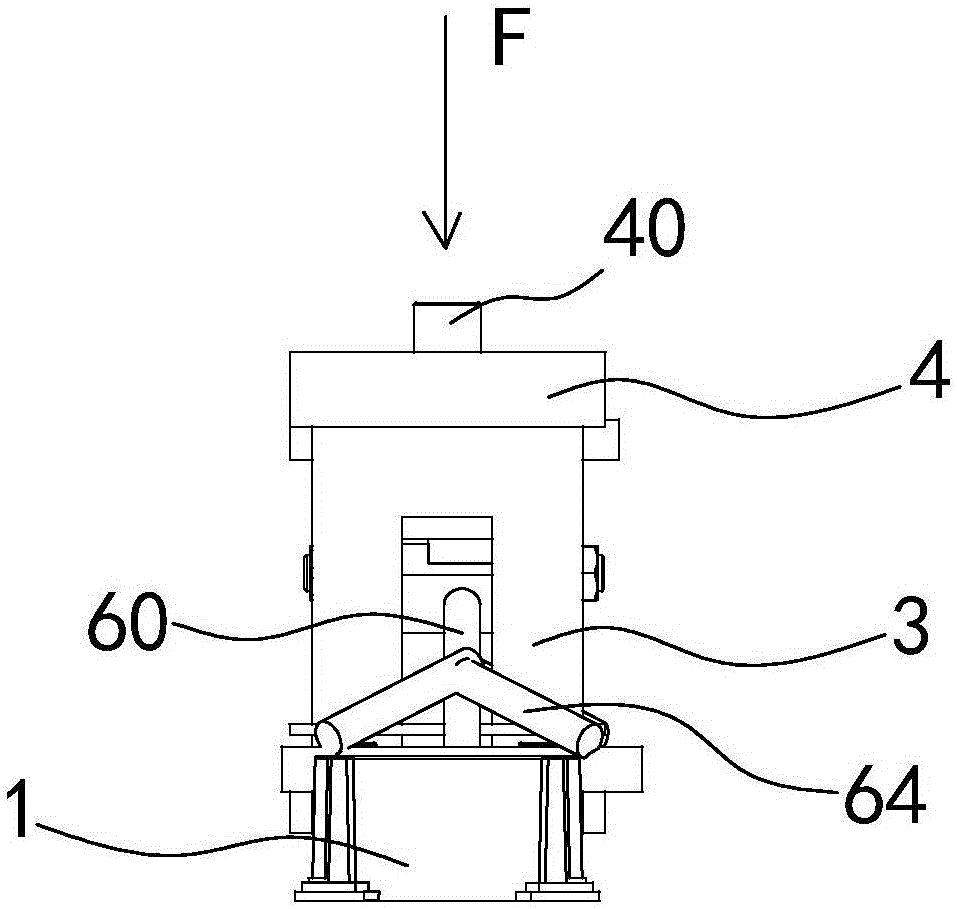
本发明涉及一种检测工装和检测方法,具体涉及用于检测轨下基板复合载荷的检测工装及其检测方法,尤其是用于检测轨下基板U型槽面复合载荷的检测工装及其检测方法。
背景技术:
:轨下基板在服役期间,特别是处于线路弯道、紧急刹车、轨下基板在轨道板上无挡肩支撑、车轮与钢轨啮合型面存在误差等因素引起离心力通过钢轨和弹条等扣件对基板单侧冲击状态下,轨下基板应该具有很高的强度值。为了保证轨下基板具有承受规定复合载荷的能力,在轨下基板投入使用前,必须对该轨下基板进行严格的复合载荷试验。然而,目前中国市面上还没有一套完整且对轨下基板进行复合载荷的检测工装,因此无法对轨下基板进行有效的检测试验。因此,为了填补这一空白,提出一种用于检测轨下基板复合载荷的检测工装及检测方法是本发明所要研究的课题。技术实现要素:本发明目的是提供一种用于检测轨下基板复合载荷的检测工装及检测方法,以填补轨下基板的复合载荷检测的空白。为达到上述目的,本发明采用的技术方案是:一种用于检测轨下基板复合载荷的检测工装,所述的轨下基板包括两个U型槽,该两个U型槽分别位于轨下基板的左右两侧,所述检测工装包括上压板基座、上压板立柱、支撑架、垫板以及连接结构;所述垫板层叠在轨下基板的上方,所述上压板立柱垂直轨下基板布置,且上压板立柱一端压在垫板的顶面,另一端连接在上压板基座底面,所述上压板立柱上开设有避让通孔,所述上压板基座和轨下基板平行布置;所述连接结构一端为固定端且固定连接上压板基座,另一端为枢纽端且朝向轨下基板布置,所述枢纽端悬设在上压板基座和轨下基板之间,且枢纽端设有连接轴;所述支撑架包括两组支撑架,每组支撑架均至少包括一横杆和一竖杆,横杆和竖杆固定连接形成一“T”字形的支撑结构;所述的两组支撑架中,定义第一组支撑架的横杆为第一横杆,第一组支撑架的竖杆为第一竖杆,第二组支撑架的横杆为第二横杆,第二组支撑架的竖杆为第二竖杆;在装配状态下,所述第一横杆水平嵌设在轨下基板位于左侧的U型槽中,第二横杆水平嵌设在轨下基板位于右侧的U型槽中;所述第一竖杆一端固定连接在第一横杆的中点,另一端通过避让通孔连接至连接结构的枢纽端;第二竖杆一端固定连接在第二横杆的中点,另一端通过避让通孔连接至连接结构的枢纽端;在试验状态下,所述上压板基座上作用有一试验机施加在上压板基座的载荷力F,该载荷力F向下迫使上压板基座往下压,上压板基座受到的载荷力通过第一竖杆和第二竖杆分解且传递至第一横杆和第二横杆中,第一横杆和第二横杆再将各自受到的分解力传递给各自所位于的U型槽中。上述技术方案中的有关内容解释如下:1、上述方案中,针对每组支撑架,均设有加固连接杆。2、上述方案中,所述加固连接杆为一倒V型结构,该倒V型结构的顶端固定连接在竖杆上,该倒V型结构的两个末端分别固定连接在横杆的两端区域,以形成一牢固的三角形结构。3、上述方案中,所述上压板基座的顶端还设有一上压板固定轴,通过该上压板固定轴实现该检测工装和试验机之间的匹配安装。4、上述方案中,所述连接结构包括连接套、连接轴以及连接芯,所述连接套上端固定在上压板基座的底面上,下端悬空,所述连接芯中设有插孔,且位于连接套的下端区域;在装配状态下,所述第一竖杆和第二竖杆均连接至所述连接芯上,并通过连接轴锁定。5、上述方案中,所述垫板用于模拟轨底与位于轨底下方的橡胶垫板的组合。6、上述方案中,所述支撑架用于模拟轨道弹条的作用,相当于弹条尾部扣压在轨下基板的U型槽内。7、上述方案中,用试验机对检测工装加载载荷力,再通过检测工装的支撑架传递给U型槽的作用力的方向模拟火车车轮传递给钢轨和弹条扣件的力对轨下基板的U型槽接触点的作用力。8、上述方案中,通过上压板基座与试验机匹配连接,该上压板基座是便于后期试验而设计的。为达到上述目的,本发明采用的另一种技术方案是:一种用于检测轨下基板复合载荷的检测工装,采用所述的检测工装,配合复合载荷试验机,按以下步骤进行操作:步骤1,将轨下基板安装在所述检测工装的下方,使得检测工装的第一横杆位于左侧的U型槽中,第二横杆位于右侧的U型槽中;步骤2,将安装有轨下基板的检测工装的上压板基座与所述试验机的压头连接,并保证轨下基板相对于试验机的压头中心垂线对称;步骤3,根据轨枕的类型及我国《铁道车辆动力学性能评定和试验鉴定规范》(GB5599-1985)中的施加于轨道上的横向水平力的限值公式获得施加于轨道上的横向水平力F′的值,并根据一经验公式F=F′*K计算出试验机的载荷力F的值,将该载荷力F的值作为试验机作用于上压板基座的作用力的值,其中K为经验系数1.35;步骤4,启动试验机下行按钮,所述试验机通过压头向检测工装的上压板基座上加载载荷力F,上压板基座将受到的载荷力F传递给轨下基板的U型槽面,试验机保载T秒后卸载对上压板基座的载荷力F;步骤5,重复步骤3进而连续试验至少两次:步骤6,将轨下基板从检测工装中取下,并检查经过所述步骤5试验的轨下基板有无损坏或变形;步骤7,若该步骤6中的轨下基板未发生损坏或变形值小于或等于阈值T,则判定检测合格;反之判定检测不合格。上述技术方案中的有关内容解释如下:1、上述方案中,所述试验机以1kN/秒的加载速度向轨下基板U型槽面加载。2、上述方案中,所述步骤3中,在计算试验机的载荷力F的值时,取该载荷力的值大于或等于F′*1.35的值。本发明工作原理是:本发明通过检测工装模拟轨下基板在服役期间,特别是处于线路弯道、紧急刹车、塑料基板在轨道板上无挡肩支撑、车轮与钢轨啮合型面存在误差等因素引起离心力通过钢轨和扣件对轨下基板单侧冲击状态下,校核轨下基板应该具有的强度值,从而有效实现了对该轨下基板复合载荷的检测。在试验过程中个,通过试验机传递给支撑架、支撑架再作用在轨下基板的力,模拟车轮压到钢轨,然后钢轨传递到弹条扣件的力、弹条扣件再作用在轨下基板上的力。由于上述技术方案运用,本发明与现有技术相比具有下列优点:本发明构思巧妙、结构简单、成本低廉,使用操作便捷,加大了测量结果的可靠性,通过检测工装及检测方法,有效实现了轨下基板的复合载荷的精确检测,保证了质量、间接地提高了产品生产效率,填补了轨下基板复合载荷测试的这一空白,起到了意料不到的效果。附图说明附图1为本实施例中主视结构示意图;附图2为本实施例中侧视结构示意图;附图3为本实施例中侧视立体结构图。以上附图中:1、轨下基板;2、垫板;3、上压板立柱;4、上压板基座;40、上压板固定轴;5、连接结构;50、连接套;51、连接轴;52、连接芯;6、支撑架;60、第一横杆;61、第二横杆;62、第一竖杆;63、第二竖杆;64、加固连接杆。具体实施方式下面结合附图及实施例对本发明作进一步描述:实施例:一种用于检测轨下基板复合载荷的检测工装参见附图1-3,所述的轨下基板1包括两个U型槽,该两个U型槽分别位于轨下基板1的左右两侧,所述检测工装包括上压板基座4、上压板立柱3、支撑架6、垫板2以及连接结构5。本实施例中,为了与试验机连接,上压板基座4的顶端还设有一上压板固定轴40,通过该上压板固定轴40实现该检测工装和试验机之间的匹配安装。所述垫板2层叠在轨下基板1的上方,所述上压板立柱3垂直轨下基板1布置,且上压板立柱3一端压在垫板2的顶面,另一端连接在上压板基座4底面,所述上压板基座4和轨下基板1平行布置,所述上压板立柱3上开设有避让通孔。所述连接结构5一端为固定端且固定连接上压板基座4,另一端为枢纽端且朝向轨下基板1布置,所述枢纽端悬设在上压板基座4和轨下基板1之间,且枢纽端设有连接轴51。所述连接结构5包括连接套50、连接轴51以及连接芯52,所述连接套50上端固定在上压板基座4的底面上,下端悬空,所述连接芯52中设有插孔,且位于连接套50的下端区域;在装配状态下,所述第一竖杆62和第二竖杆63均连接至所述连接芯52上,并通过连接轴锁定。所述支撑架6包括两组支撑架6,每组支撑架6均至少包括一横杆和一竖杆,横杆和竖杆固定连接形成一“T”字形的支撑结构;所述的两组支撑架6中,定义第一组支撑架6的横杆为第一横杆60,第一组支撑架6的竖杆为第一竖杆62,第二组支撑架6的横杆为第二横杆61,第二组支撑架6的竖杆为第二竖杆63。在装配状态下,所述第一横杆60水平嵌设在轨下基板1位于左侧的U型槽中,第二横杆61水平嵌设在轨下基板1位于右侧的U型槽中;所述第一竖杆62一端固定连接在第一横杆60的中点,另一端通过避让通孔连接至连接结构5的枢纽端;第二竖杆63一端固定连接在第二横杆61的中点,另一端通过避让通孔连接至连接结构5的枢纽端。在试验状态下,所述上压板基座4上作用有一试验机施加在上压板基座4的载荷力F,该载荷力F向下迫使上压板基座4往下压,上压板基座4受到的载荷力通过第一竖杆62和第二竖杆63分解且传递至第一横杆60和第二横杆61中,第一横杆60和第二横杆61再将各自受到的分解力传递给各自所位于的U型槽中。本实施例中,针对每组支撑架6,均设有加固连接杆64,每个加固连接杆64为一倒V型结构,该倒V型结构的尖端固定连接在竖杆上,该倒V型结构的两个末端分别固定连接在横杆的两端区域,以形成一牢固的三角形结构。上述实施例检测轨下基板1复合载荷的检测工装,所对应的方法如下:采用所述检测工装,并配合复合载荷试验机使用,按以下步骤进行操作:步骤1,将轨下基板1安装在所述检测工装的下方,使得检测工装的第一横杆60位于轨下基板1左侧的U型槽中,第二横杆61位于轨下基板1右侧的U型槽中。步骤2,将安装有轨下基板1的检测工装的上压板基座4与所述试验机的压头连接,并保证轨下基板1相对于试验机的压头中心垂线对称。步骤3,根据轨枕的类型及我国《铁道车辆动力学性能评定和试验鉴定规范》(GB5599-1985)中的施加于轨道上的横向水平力的限值公式获得施加于轨道上的横向水平力F′的值,并根据一经验公式F=F′*K计算出试验机的载荷力F的值,将该载荷力F的值作为试验机作用于上压板基座1的作用力的值,其中K为经验加载系数1.35。步骤4,启动试验机下行按钮,所述试验机通过压头向检测工装的上压板基座4上加载载荷力F,上压板基座4将受到的载荷力F传递给轨下基板1的U型槽面,试验机保载T秒后卸载对上压板基座4的载荷力F。步骤5,重复步骤3进而连续试验至少两次,本实施例中,重复步骤3进行试验三次。步骤6,将轨下基板1从检测工装中取下,并检查经过所述步骤5试验的轨下基板1有无损坏或变形。步骤7,若该步骤6中的轨下基板未发生损坏或变形值小于或等于阈值T,则判定检测合格;反之判定检测不合格。本实施例中,阈值T取0.8mm,若经过以上测试的轨下基板1变形值小于或阈值0.8mm,则说明该轨下基板1合格,若轨下基板的也就是说如果测试过的轨下基板1的变形值大于或等于0.8mm,则说明该轨下基板1不合格。本实施例的工作原理如下:采用如上试验机和检测工装配合使用对轨下基板1进行复合载荷试验。其中,每组支撑架6相当于轨道弹条,而本实施例中的垫板2模拟钢轨轨底和轨底下方的橡胶垫板2的组合。假定:轴重F1=12.7吨,折合F1=124.46kN,在车轮与钢轨接触点处以法线方向传递给钢轨。轨枕为混凝土轨枕,根据我国《铁道车辆动力学性能评定和试验鉴定规范》(GB5599-1985)规定,对施加于轨道上的横向水平力F′采用如下的限值公式:F′≤0.85*(15+F/2)=0.85*(15+124.46/2)=65.65(kN),得到限值载荷的水平分力F′大约为65.65kN。也就是说,此时,理论上轨下基板1的限值载荷的水平分力F′不能超过65.65kN。定量测定值:U型槽面复合载荷检测:U型槽面经复合载荷试验后不得有伤损,其弯曲变形量不得超过0.8mm。考虑本项试验为扣件零件模拟试验、车轮对钢轨的冲击、轨下基板1制造误差、试验装置制造误差、扣件安装误差以及电液伺服材料试验机加载速度较慢等因素,所以,本项试验经验加载系数1.35。因此,试验机载荷F=F′*1.35=65.65*1.35=88.63kN,取值90kN。其中,经验加载系数取1.35,大于系数1,而90kN大于88.63kN,这样取值是为了对严格把关试验条件,从而保证轨下基板试验的有效性,但是试验机载荷的取值也不能过于苛刻,否则生产的轨下基板1就不会合格了。将轨下基板1放置在电液伺服材料试验机的平台上,保证轨下基板1相对于试验机压头中心垂线处于对称条件,并将试验工装的两撑杆顶分别靠在轨下基板1U型槽面的外侧面,启动下行按钮,试验机以1kN/秒的加载速度通过压头向轨下基板1U型槽面加载,当试验机载荷F=90kN时,保载60秒,然后卸载,连续进行该试验3次。此后,取下轨下基板,检查有无损坏或变形,当没发生损坏或变形值≤0.8mm,则判定检测合格。参见下表为轨下基板U型槽面复合载荷试验参数。表:轨下基板U型槽面复合载荷试验参数序号项目名称符号数值单位1试验机载荷F90kN2保载时间T60S3循环次数n3次4加载速度V1kN/s针对上述实施例,本实施例进一步解释及可能产生的变化描述如下:1、上述实施例中,试验机采用1kN/秒的加载速度,事实上,试验机的加载速度可以为除了1kN/秒以外的其它值,不仅限于11kN/秒,试验员可以根据需求调整该加载速度。2、上述实施例中,在通过检测轨下基板1有无形变及形变大小从而判定轨下基板1是否合格时,阈值T取0.8mm,事实上阈值T除了取0.8mm外,还可以取其它值,不仅限于0.8mm,试验员可以根据需求调整阈值大小。3、上述实施例中,复合载荷试验进行3次,事实上,该试验还可以是2次、4次及4次以上,理论上是试验次数越多,越精确,其实,试验1次也是可行的,只是,试验1次可能存在一定误差,试验员可以根据需求调整试验次数。上述实施例只为说明本发明的技术构思及特点,其目的在于让熟悉此项技术的人士能够了解本发明的内容并据以实施,并不能以此限制本发明的保护范围。凡根据本发明精神实质所作的等效变化或修饰,都应涵盖在本发明的保护范围之内。当前第1页1 2 3