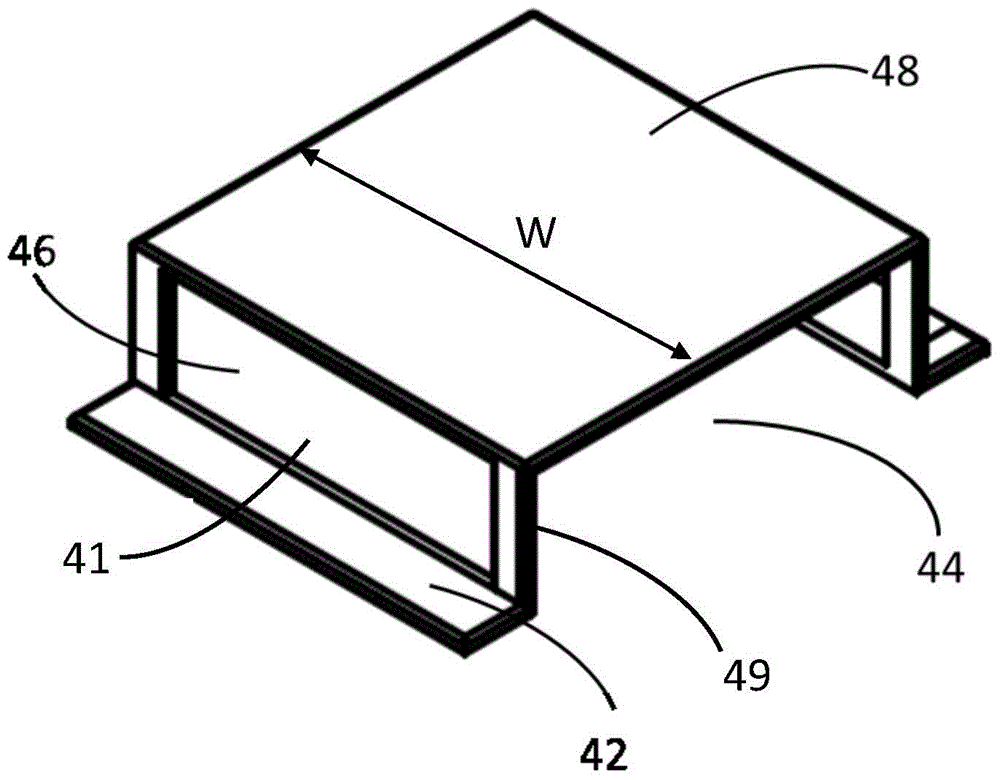
本发明涉及锂离子电池领域,特别涉及一种锂离子电池和电池包。
背景技术:随着锂离子电池在电动汽车和电网储能等领域中的应用日趋广泛,锂离子电池的安全性能也越来越受到重视。锂离子电池安全问题的起因通常是热失控。当锂离子电池发生热失控时,锂离子电池内的活性材料的放热量可以达到几百焦耳每克,瞬间产热可引起活性材料与电解液之间剧烈的氧化还原反应,产生大量的可燃性气体,这些气体使电池内压急剧升高,从而冲破防爆阀形成快速的气体流动,喷出的可燃性气体与空气接触并混合;同时,在电池内部可燃性气体喷出的过程中,会带出大量高温的固体颗粒,这些固体颗粒形成明亮的火星并点燃空气与可燃性气体的混合物,从而导致发生燃烧、爆炸。中国专利申请公开号CN103474599A公开了一种带通孔网罩的具有理想安全性的锂离子电池和电池包,其通过网罩来过滤掉高温的固体颗粒,达到使可燃性气体与高温固体颗粒分离的目的。然而,本申请发明人发现中国专利申请公开号CN103474599A的网罩仍然存在一些缺陷:当电池发生热失控时,电池内部的可燃性气体会带着高温固体颗粒快速喷出,由于网罩上的通孔仅设置于网罩的顶面上并位于气体喷出的方向上,如果网罩顶面上的通孔过大,在高速气流的作用下,高温固体颗粒会从电池内部喷出,引起燃烧、爆炸;而且,通孔过大会使网罩的强度降低,在混合有高温固体颗粒的高速气流的冲击下,网罩易损坏;如果通孔过小,气流又无法及时从电池内部排出,降低排气效率,并且,电池内部发生失控时,溶化的塑胶件、随气流喷出的固体颗粒或金属熔渣易堵塞网孔,使电池内压急剧升高,引起爆炸的风险较高。
技术实现要素:本发明所要解决的技术问题在于,提供一种安全性能好的锂离子电池和电池包。本发明是这样实现的,提供一种锂离子电池,包括电池壳体、安装于所述电池壳体上的电池顶盖,以及设置在所述电池壳体和/或所述电池顶盖上的泄压阀;还包括设置在所述电池壳体和/或所述电池顶盖上的与泄压阀固定配合的安全防护装置;所述安全防护装置包括与所述泄压阀相对的遮挡板、侧壁和气流通道结构;所述侧壁自所述遮挡板朝向所述电池壳体或所述电池顶盖延伸并与所述电池壳体或所述电池顶盖连接;所述气流通道结构形成在所述侧壁上。进一步地,所述气流通道结构仅设置在所述侧壁上。进一步地,所述气流通道结构包括形成在所述侧壁上的至少一个开口结构、至少一个通孔阵列或至少一个缺口。进一步地,当所述气流通道结构为通孔阵列时,所述通孔阵列中每一通孔的面积不小于1mm2。进一步地,所述遮挡板上设有多个通孔;所述遮挡板上的每个通孔的面积小于1mm2。进一步地,所述气流通道结构包括间隔地形成在所述侧壁上的第一气流通道和第二气流通道;所述第一气流通道为开口结构、通孔阵列或缺口中之一;所述第二气流通道为开口结构、通孔阵列或缺口中之一;所述第一气流通道和所述第二气流通道的结构不同。进一步地,所述泄压阀包括泄压孔;所述气流通道结构的面积之和不小于所述泄压孔面积的0.5倍。进一步地,当所述第一气流通道或所述第二气流通道为通孔阵列时,所述通孔阵列中每一通孔的面积不小于1mm2。进一步地,所述锂离子电池还包括收容于所述电池壳体中的电芯;所述安全防护装置设置在所述电芯与所述电池顶盖之间;所述安全防护装置的高度比所述电池顶盖上与所述电芯相邻的表面到所述电芯的最小距离小至少1mm;所述安全防护装置的宽度与所述电池壳体的内表面间距不小于1mm;所述安全防护装置的长度比所述电芯正负极耳最小间距小至少1mm。进一步地,所述安全防护装置还包括连接部;所述连接部设置在所述侧壁的端部并与所述遮挡板间隔设置;所述侧壁通过所述连接部与所述电池壳体或所述电池顶盖连接。进一步地,所述锂离子电池还包括另一安全防护装置;所述另一安全防护装置和所述安全防护装置设置在所述泄压阀的两侧,并分别覆盖所述泄压阀;所述另一安全防护装置包括与所述泄压阀相对的遮挡板、侧壁和气流通道结构;所述侧壁自所述遮挡板朝向所述电池壳体或所述电池顶盖延伸并与所述电池壳体或所述电池顶盖连接;所述气流通道结构形成在所述侧壁和/或遮挡板上。进一步地,所述安全防护装置由金属材料或无机非金属陶瓷材料制成。进一步地,所述安全防护装置表面设有特氟龙涂层、环氧树脂涂层、酚醛树脂涂层、聚对苯二甲酸乙二酯涂层、聚丙烯涂层或陶瓷涂层。本发明还提供一种锂离子电池包,包括若干个并联和/或串联的上述的锂离子电池。本发明一实施例的锂离子电池包及锂离子电池通过将安全防护装置的气流通道结构形成在侧壁上,使得安全防护装置的遮挡板与气流通道结构形成相对分离设计,既可利用遮挡板对固体火星颗粒进行有效阻挡,又可利用位于安全防护装置侧面的气流通道结构高效排气,降低了可能因排气效率不足引起内压升高导致爆炸的风险,提高锂离子电池的安全性能。同时,利用遮挡板及位于安全防护装置侧面的气流通道结构可以改变气体流向,可避免烟气高速垂直喷出后与空气大范围混合,进一步提高锂离子电池的安全性能。附图说明图1为本发明一实施例中锂离子电池的立体分解示意图。图2为图1中锂离子电池的安全防护装置的放大示意图。图3为图2中安全防护装置的俯视图。图4为图2中安全防护装置的主视图。图5至图11为本发明实施例中安全防护装置的几种具体实施方式的示意图。图12为本发明另一实施例中锂离子电池的立体分解示意图。具体实施方式为了使本发明所要解决的技术问题、技术方案及有益效果更加清楚明白,以下结合附图及实施例,对本发明进行进一步详细说明。应当理解,此处所描述的具体实施例仅仅用以解释本发明,并不用于限定本发明。图1为本发明一实施例中锂离子电池的立体分解示意图。如图1所示,锂离子电池包括电池壳体10、装设于电池壳体10中的电芯20、灌注于电池壳体10中的电解液(未图示),以及安装于电池壳体10上的电池顶盖50。其中,电池顶盖50上设有正极柱和负极柱505(图示正负极柱未作区分),正负极柱505分别通过导电连接体30与电芯20的正、负极进行电连接。电池顶盖50于正极柱和负极柱505之间的中央位置处设有泄压孔510,泄压孔510上密封装设有防爆泄压片60。泄压片60与泄压孔510共同组成泄压阀。具体地,泄压片60可由与电池顶盖50相同的金属材料制成,如此,可以克服不同金属之间因存在电势差而与外界空气或电解液形成电解池,降低发生腐蚀反应的风险。在图1所示的实施方式中,泄压片60可采用铝、铝合金、镍、镍合金、不锈钢中的一种制成。泄压片60具有良好的延展性,在破裂泄压时不会飞出。根据本发明的一个实施方式,泄压片60上可涂覆或粘接一层耐腐蚀材料,例如PE和/或PP,可防止泄压片60被电解液腐蚀。根据本发明的另一个实施方式,泄压片60上设有薄弱线或薄弱面,薄弱面或薄弱线在电池内部压力过大的情况下先破裂,从而使得泄压片60的破裂位置可控。根据本发明的一个实施方式,泄压片60达到破裂临界状态时可承受的压力值为0.3~1.2MPa。如图1所示,锂离子电池还包括与泄压阀固定配合的安全防护装置40。安全防护装置40可设置在电池顶盖50上与电芯20相对的第一面如下表面(当锂离子电池处于图1所示位置时),并位于电池顶盖50与电芯20之间。根据本发明的一个实施方式,在从电池顶盖50到电芯20的方向上,安全防护装置40可设置在泄压片60的正下方。具体地,如图2至图4所示,安全防护装置40包括与泄压阀相对的遮挡板48、侧壁49、连接部42和气流通道结构41。在一实施例中,遮挡板48可覆盖在泄压片60的正下方,且遮挡板48在泄压阀上的投影面积不小于泄压阀面积的1.0倍,以便更好地阻挡住正面喷出的火星,并使火星产生反射从而改变运动轨迹和喷出速度。在图2所示的实施例中,遮挡板48为一个连续结构,即遮挡板48上未设置通孔等可供气流通过的通孔,或者说,气流通道结构仅设置在侧壁上,从而可以完全地阻挡住正面喷出的火星,并使火星产生反射从而改变运动轨迹和喷出速度。侧壁49大致垂直或倾斜地设置在遮挡板48上,并自遮挡板48朝向电池顶盖50延伸。侧壁49可以沿着遮挡板48的边缘连续设置(如图6、7、9、10所示),也可以沿着遮挡板48的边缘不连续设置(如图2、5、8)。在图2所示的实施例中,侧壁49沿着遮挡板48的边缘不连续设置;侧壁49包括大致垂直或倾斜地设置在遮挡板48上的两个侧板。连接部42设置在侧壁49的端部并与遮挡板48间隔设置。连接部42固定在电池顶盖50上。连接部42可通过冲压或模具成型等方式与电池顶盖50集成为一体,也可通过粘结、焊接、铆接、夹持连接、螺纹连接、卡扣连接等方式连接固定在电池顶盖50上。在一实施例中,连接部42可通过焊接方式固定在电池顶盖50上,使得连接拉力不小于50N;如连接力过小,在电池生产组装过程或后续电池使用过程中的振动易导致安全防护装置40脱落。在实际使用过程中,如图11所示,可根据实际情况省略连接部42,而令侧壁49直接通过粘结、焊接、卡扣连接等方式连接固定在电池顶盖50上。气流通道结构41形成在侧壁49上。在图2所示的实施例中,气流通道结构41包括形成在侧壁49的侧板上的第一气流通道46,以及形成在侧壁49的两个侧板之间的第二气流通道44。第一气流通道46包括形成在侧板上的开口结构;开口结构可以为如图2中所示的完全开口的矩形孔或其它形状的孔,使得侧板大致呈框状。开口结构的面积之和不小于泄压孔510面积的0.5倍;若面积过小,在电池内部发生失效时,内部气体无法及时排出,造成内部气压富集,超出壳体的爆破压力极限,导致壳体爆破,易发生爆炸。第二气流通道44可以为侧壁49的两个侧板之间的间隙,也可以理解为:侧壁49沿着遮挡板48的边缘连续设置,第二气流通道44为形成在侧壁49上的缺口,即将位于两个侧板之间且位于侧壁49的自由端与遮挡板48之间的部分全部切除。在实际应用中,安全防护装置40的材料可以为金属材料及无机非金属陶瓷材料。在一实施例中,安全防护装置40可采用金属材料如铝、铝合金、镍、镍合金或不锈钢制成;安全防护装置40可采用与电池顶盖50的材料相同的金属材料制成,这是由于不同种材料会与壳体在电解液及湿润环境下形成电化学池,降低电池的可靠性。安全防护装置40上至少朝向电芯20的表面(例如,当安全防护装置40位于电池顶盖50与电芯20之间时,安全防护装置40上远离泄压阀的一侧的表面;当安全防护装置40位于电池顶盖50外侧时,安全防护装置40上面对泄压阀的一侧的表面)可喷涂特氟龙、环氧树脂、酚醛树脂、聚对苯二甲酸乙二酯(PET)、聚丙烯(PP)、陶瓷等涂层进行绝缘处理,涂层的厚度不小于10um,涂层需均匀涂覆于金属表面,涂层厚度过薄时易出现漏金属,该涂层可有效实现绝缘和防腐功效。如安全防护装置40表面绝缘做得不到位,存在正负极联通短路的风险。在实际应用中,如图4所示,安全防护装置40的连接部42到遮挡板48的高度H,与电池顶盖50的第一表面如下表面到电芯20上表面的间距相比至少小1mm,如该高度H过大,遮挡板48会对电芯20中的正负极极片造成挤压,导致极片变形,甚至引起正负极间短路发生。安全防护装置40的两侧板49间的长度L比正负极极耳最小间距小至少1mm,如该长度L过大,极耳易与遮挡板48和侧板46的交界边沿形成干涉,易损伤极耳。如图1和图2所示,安全防护装置40的宽度W比壳体10的内表面S间距小至少1mm,如该宽度W距离过大,会干涉电池顶盖50与壳体10间的装配。按图1所示实施方式完成组装后的锂离子电池进行安全测试时,锂离子电池内部温度急剧上升并产生大量烟汽,此时,泄压片60破裂、翻转,以释放锂离子电池内部夹带着高温固体火星颗粒的烟汽。由于在泄压片60下方设置有覆盖泄压片60的安全防护装置40,飞溅出的固体火星颗粒被安全防护装置40的遮挡板48阻挡,同时,烟气可通过第一气流通道46、第二气流通道44顺利排出电池壳体10,依旧保持泄压的功能。在此过程中,由于飞溅出的固体火星颗粒的运动轨迹主要为直线,因此,当飞溅出的固体火星颗粒随烟气流到安全防护装置40时,飞溅出的固体火星颗粒会被安全防护装置40的遮挡板48反弹回到壳体10的内部,从而可阻挡高温固体火星颗粒随着高速气流喷射到电池外部,降低了烟气在电池外部燃烧的风险。同时,高速喷出的烟气流到安全防护装置40时,烟气被安全防护装置的遮挡板48阻挡而改变气体流向,并从位于安全防护装置40侧面的第一气流通道46、第二气流通道44排出,进而降低烟气喷出电池外部时的喷出速度、减小了烟气喷出的距离、减小了烟气与空气接触面积,从而降低了可燃性气体发生燃烧的风险。此外,降低烟气喷出电池外部时的喷出速度还可降低烟气接触外部其他物质导致燃烧的可能性,避免造成更大的损失。如上所述,与中国专利申请公开号CN103474599A相比,本发明一实施例中的安全防护装置40通过遮挡板48与第一气流通道46、第二气流通道44的相对分离设计,既可利用遮挡板48对固体火星颗粒进行有效阻挡,又可利用位于安全防护装置40侧面的第一气流通道46、第二气流通道44高效排气,降低了可能因排气效率不足引起内压升高导致爆炸的风险。同时,利用遮挡板48及位于安全防护装置40侧面的第一气流通道46、第二气流通道44可以改变气体流向,可避免烟气高速垂直喷出后与空气大范围混合。因此,本发明一实施例中的安全防护装置40可将高速喷出的烟气如可燃性气体、电解液蒸汽与固体火星颗粒分离,防止可燃性气体、电解液蒸汽与固体火星颗粒一起喷出并在远离泄压阀的区域与空气混合着火燃烧。固体火星颗粒的过滤可有效将电池可能的着火失控的方式由火星引燃改变为烟气自燃。从物理角度来讲,烟气引燃的温度通常小于60度即可,而烟气自燃的温度通常要高于450度,如此,安全防护装置40可显著提高锂离子电池的安全性能。另外,与中国专利申请公开号CN103474599A相比,本发明通过遮挡板48与第一气流通道46、第二气流通道44的相对分离设计,由于遮挡板48位于气体喷出的方向上,因此,由遮挡板48对固体火星颗粒进行有效阻挡;位于安全防护装置40侧面的第一气流通道46、第二气流通道44不会受到固体火星颗粒的直接冲击或仅会受到少量固体火星颗粒的直接冲击,因此,第一气流通道46、第二气流通道44的尺寸和形状有较宽的选择范围从而可确保高效排气,且不易被固体火星颗粒等堵塞。图5所示为本发明一实施方式中安全防护装置的立体示意图。图5中的安全防护装置与图2中的安全防护装置相似,两者之间的主要不同之处在于:图5中的安全防护装置的第一气流通道46包括形成在侧壁上的多个通孔,即通孔阵列。在一实施例中,每一通孔的面积不小于1mm2,通孔的总面积不小于泄压孔510面积的0.5倍。图5中的安全防护装置,可综合平衡火星阻挡效果和排气速率。图6所示为本发明一实施方式中安全防护装置的立体示意图。图6中的安全防护装置与图5中的安全防护装置相似,两者之间的主要不同之处在于:侧壁49沿着遮挡板48的边缘连续设置,第二气流通道44包括形成在侧壁上的多个通孔,即第一气流通道46和第二气流通道44均包括形成在侧壁上的多个通孔,即均为带孔网状结构。通孔的形状可为圆形、菱形、方形、椭圆形、跑道形等。每一通孔的面积不小于1mm2,通孔的总面积不小于泄压孔510面积的0.5倍。若单个通孔的面积过小,一方面难以保证气流通道面积的要求,另一方面电池内部熔融塑胶件和固体颗粒易堵塞网孔,导致气体无法及时排出,导致内压富集造成安全隐患。第一气流通道46和第二气流通道44采用带孔网状结构可有效地阻挡可能从第一气流通道46和第二气流通道44逸出的火星,更好地分离火星和可燃性气体。图7所示为本发明一实施方式中安全防护装置的立体示意图。图7中的安全防护装置与图2中的安全防护装置相似,两者之间的主要不同之处在于:图7中安全防护装置的侧壁49沿着遮挡板48的边缘连续设置,第二气流通道44包括形成在侧壁上的多个通孔。在一实施例中,每一通孔的面积不小于1mm2,通孔的总面积不小于泄压孔510面积的0.5倍。图7中的安全防护装置,可综合平衡火星阻挡效果和排气速率。图8所示为本发明一实施方式中安全防护装置的立体示意图。图8中的安全防护装置与图2中的安全防护装置相似,两者之间的主要不同之处在于:遮挡板48上设有多个通孔,即遮挡板48为带孔网状结构。遮挡板48上的通孔只能允许气体通过,不允许高温固体颗粒通过,例如,在一实施例中,单个通孔的面积小于1mm2,可有效地增大气流通道面积,降低壳体10内部气压富集程度。若单个孔面积过大,可能会有部分粒径小的火星从孔中穿过,火星阻挡效果会恶化。图9所示为本发明一实施方式中安全防护装置的立体示意图。图9中的安全防护装置与图7中的安全防护装置相似,两者之间的主要不同之处在于:遮挡板48上设有多个通孔,即遮挡板48为带孔网状结构。遮挡板48上的通孔只能允许气体通过,不允许高温固体颗粒通过,例如,在一实施例中,单个通孔的面积小于1mm2,可有效地增大气流通道面积。图9中的安全防护装置可有效平衡火星阻挡效果和排气速率。图10所示为本发明一实施方式中安全防护装置的立体示意图。图10中的安全防护装置与图2中的安全防护装置相似,两者之间的主要不同之处在于:图10中安全防护装置的侧壁49沿着遮挡板48的边缘连续设置,第二气流通道44包括形成在侧壁上的开口结构,使得侧板大致呈框状。图10中的安全防护装置可增强安全防护装置的强度。图12所示为本发明另一实施方式中锂离子电池的立体分解图。图12中的锂离子电池与图1中的锂离子电池相似,两者之间的不同之处在于:图12中的锂离子电池还包括另一安全防护装置70,安全防护装置70和安全防护装置40设置在电池顶盖50的两侧,并分别覆盖泄压片60。安全防护装置70的结构可以与上述实施例中的任一安全防护装置40的结构相同。此外,安全防护装置70也可以将气流通道结构仅设置在遮挡板48上。安全防护装置40、70在电芯安全测试过程中对电芯20的安全施加了双重保护,在保证气流通道顺畅的同时,对固体火星颗粒施加了两层有效的阻挡,可更加有效的隔离固体火星颗粒和烟气如可燃烟气,保证电芯20的安全。需要说明的是,在图示实施方式中,锂离子电池为方形锂离子电池。但是,可以理解的是,本发明对锂离子电池的外形没有特别限制,锂离子电池也可以是其他形状的锂离子电池,例如,棱柱形锂离子电池和圆柱形锂离子电池。此外,在图示实施方式中,虽然仅仅以泄压片为例对本发明进行了说明,但是本发明中描述的安全防护装置也可以应用在其他锂离子电池的泄压阀上。此外,安全防护装置也可以采用与上述类似的方式设置在壳体10上,或分别设置在壳体10和电池顶盖50上。以上所述仅为本发明的较佳实施例而已,并不用以限制本发明,凡在本发明的精神和原则之内所作的任何修改、等同替换和改进等,均应包含在本发明的保护范围之内。