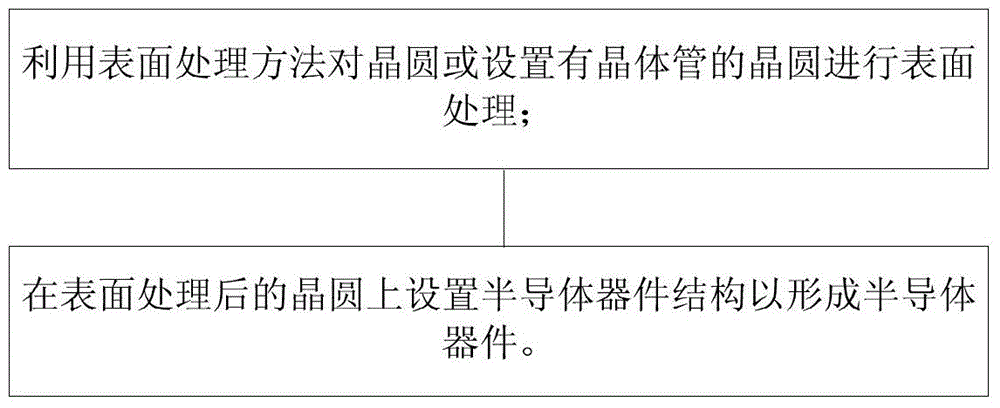
本申请涉及集成电路
技术领域:
,具体而言,涉及一种晶圆的表面处理方法、半导体器件及其制作方法。
背景技术:
:现有集成电路工艺中,通常需要采用预清洗工艺来对具有晶体管的晶圆进行表面处理以去除晶圆表面的杂质,然后再在晶圆上制作后续器件。预清洗工艺的种类很多,有些预清洗工艺是通过反应气体与晶圆表面的杂质反应以形成反应产物,然后通过去除反应产物以实现去除晶圆表面杂质的作用。例如,现有自对准工艺中采用沉积镍金属来形成金属硅化物,且在形成镍金属前通常采用SiCoNi预清洗工艺对衬底进行表面处理。SiCoNi预清洗工艺是一种低强度的化学刻蚀方法,其工艺包括两个步骤:首先,利用NF3和NH3作为前驱气体形成作为反应气体的NH4F和NH4F·HF,然后,利用形成的反应气体与衬底表面上的杂质SiO2反应形成反应产物;最后,利用退火处理(退火温度一般高于100℃)使反应产物分解,从而达到去除晶圆表面杂质的作用。然而,现有预清洗工艺(即表面处理工艺)中产生的反应产物为不易分解的固体物质,从而使反应产物在退火处理工艺后难以完全分解,进而在晶圆表面上形成反应产物的残留物。而且晶圆表面上的残留物会对最终形成的半导体器件性能造成影响,严重时会导致器件失效。技术实现要素:本申请的主要目的在于提供一种晶圆的表面处理方法、半导体器件及其制作方法,以减少表面处理工艺中晶圆表面上产生的反应产物的残留物。为了实现上述目的,根据本申请的一个方面,提供了一种晶圆的表面处理方法,该表面处理方法包括以下步骤:将晶圆放置于具有反应气体的反应室中;反应气体与晶圆表面上的氧化物进行反应形成反应产物;以及对晶圆进行至少两次退火处理分解去除反应产物。进一步地,各次退火处理的退火温度不同。进一步地,各次退火处理的退火温度随次数增加依次递增。进一步地,各次退火处理的退火时间为1~10min,且各次退火处理的退火时间间隔为10~60s。进一步地,各次退火处理的退火温度在110℃~160℃的范围内。进一步地,在退火处理的步骤中,进一步向反应室中通入H2。进一步地,H2的气体流量为200sccm~1000sccm。进一步地,对晶圆进行两次退火处理,且第一次退火处理的退火温度为110~130℃,第二次退火处理的退火温度为140~160℃。进一步地,晶圆在进行表面处理之前,还包括在晶圆上形成晶体管的步骤。为了实现上述目的,根据本申请的一个方面,提供了一种半导体器件的制作方法,该制作方法包括以下步骤:利用上述的表面处理方法对晶圆或设置有晶体管的晶圆进行表面处理;在表面处理后的晶圆上设置半导体器件结构以形成半导体器件。进一步地,当表面处理方法是对设置有晶体管的晶圆进行表面处理时,半导体器件结构为与晶体管电连接的金属硅化物。进一步地,形成金属硅化物的步骤包括:在表面处理后的晶圆上沉积金属层;进行热处理以使金属层和晶圆反应形成金属硅化物。进一步地,金属层为NiPt层,形成金属硅化物的步骤包括:进行第一次热处理以使部分金属层和晶圆反应形成Ni2Si层;湿法刻蚀去除剩余金属层;以及进行第二次热处理以使Ni2Si层转变成NiSi层,且NiSi层构成金属硅化物。进一步地,形成金属硅化物后,制作方法还包括在金属硅化物上形成掩膜层的步骤。进一步地,在形成金属硅化物的步骤中,形成与晶体管的源漏极和/或晶体管的栅极电连接的金属硅化物。根据本申请的另一方面,提供了一种半导体器件,该半导体器件由上述的制作方法制作而成。应用本申请的技术方案,本申请提供的晶圆的表面处理方法通过对晶圆进行多次退火处理,从而使表面处理工艺中产生的反应产物能够被多次分解,且每次退火处理均会对反应产物进行分解以使反应产物的厚度不断减小,同时也降低了由于反应产物的厚度过厚导致的反应产物的分解难度,进而使晶圆表面上的反应产物更容易被分解掉,减少了表面处理工艺中晶圆表面上产生的反应产物的残留物。附图说明构成本申请的一部分的说明书附图用来提供对本申请的进一步理解,本申请的示意性实施例及其说明用于解释本申请,并不构成对本申请的不当限定。在附图中:图1示出了本申请实施方式所提供的晶圆的表面处理方法的流程示意图;图2示出了本申请实施方式所提供的半导体器件的制作方法的流程示意图。具体实施方式需要说明的是,在不冲突的情况下,本申请中的实施例及实施例中的特征可以相互组合。下面将参考附图并结合实施例来详细说明本申请。需要注意的是,这里所使用的术语仅是为了描述具体实施方式,而非意图限制根据本申请的示例性实施方式。如在这里所使用的,除非上下文另外明确指出,否则单数形式也意图包括复数形式,此外,还应当理解的是,当在本说明书中使用术语“包含”和/或“包括”时,其指明存在特征、步骤、操作、器件、组件和/或它们的组合。为了便于描述,在这里可以使用空间相对术语,如“在……之上”、“在……上方”、“在……上表面”、“上面的”等,用来描述如在图中所示的一个器件或特征与其他器件或特征的空间位置关系。应当理解的是,空间相对术语旨在包含除了器件在图中所描述的方位之外的在使用或操作中的不同方位。例如,如果附图中的器件被倒置,则描述为“在其他器件或构造上方”或“在其他器件或构造之上”的器件之后将被定位为“在其他器件或构造下方”或“在其他器件或构造之下”。因而,示例性术语“在……上方”可以包括“在……上方”和“在……下方”两种方位。该器件也可以其他不同方式定位(旋转90度或处于其他方位),并且对这里所使用的空间相对描述作出相应解释。正如
背景技术:
中所介绍的,现有预清洗工艺(即表面处理工艺)中产生的反应产物为不易分解的固体物质,从而使反应产物在退火处理工艺后难以完全分解,进而在晶圆表面上形成反应产物的残留物。本申请的发明人针对上述问题进行研究,提出了一种晶圆的表面处理方法。如图1所示,该处理方法包括以下步骤:将晶圆放置于具有反应气体的反应室中;反应气体与晶圆表面上的氧化物进行反应形成反应产物;以及对晶圆进行至少两次退火处理去除反应产物。上述表面处理方法通过对晶圆进行多次退火处理,从而使表面处理工艺中产生的反应产物能够被多次分解,且每次退火处理均会对反应产物进行分解以使反应产物的厚度不断减小,同时也降低了由于反应产物的厚度过厚导致的反应产物的分解难度,进而使晶圆表面上的反应产物更容易被分解掉,减少了表面处理工艺中晶圆表面上产生的反应产物的残留物。下面将更详细地描述根据本申请提供的晶圆的表面处理方法的示例性实施方式。然而,这些示例性实施方式可以由多种不同的形式来实施,并且不应当被解释为只限于这里所阐述的实施方式。应当理解的是,提供这些实施方式是为了使得本申请的公开彻底且完整,并且将这些示例性实施方式的构思充分传达给本领域普通技术人员。首先,将晶圆放置于具有反应气体的反应室中。其中,反应气体可以通过前驱气体生成。本领域的技术人员可以根据实际工艺需求选择合适前驱气体,在一种优选的实施方式中,在向反应室中通入前驱气体的步骤中,前驱气体为NF3和NH3,且前驱气体在射频功率的作用 下生成反应气体NH4F和NH4F·HF。反应气体能够与晶圆表面的杂质进行很好的反应,并且通过后续的退火处理,就能够去掉晶圆表面的杂质。完成将晶圆放置于具有反应气体的反应室中的步骤之后,反应气体与晶圆表面上的氧化物进行反应形成反应产物。上述反应产物根据产生的反应气体及晶圆表面杂质的不同而不同,在一种优选的实施方式中,该反应气体为NH4F和NH4F·HF,且NH4F和NH4F·HF冷凝在晶圆表面与作为杂质的SiO2发生反应,能够在常温下生成固态的(NH4)2SiF6作为反应产物。完成反应气体与晶圆表面上的氧化物进行反应形成反应产物的步骤之后,对晶圆进行多次退火处理分解去除反应产物。由于上述退火处理为多次,从而使表面处理工艺中产生的残留物能够被多次分解,且每次退火处理均会对残留物进行分解以使残留物的厚度不断减小,同时也降低了由于残留物的厚度过厚导致的残留物的分解难度,进而使晶圆表面上的残留物更容易被分解掉,并减少了表面处理工艺中晶圆表面上产生的残留物。在一种优选的实施方式中,对晶圆进行多次退火处理,各次退火处理的退火温度不同。更为优选地,各次退火处理的退火温度随次数增加依次递增。退火处理的温度的依次递增使反应产物多次退火处理中不断变薄,从而有利于反应产物的分解反应。各次退火处理的退火温度和退火时间可以根据现有技术进行设定。优选地,各次退火处理的退火温度在110℃~160℃的范围内。其中,作为晶圆表面杂质的氧化物通过与反应气体形成反应产物,该反应产物在退火温度为110℃~160℃的高温处理下能够被更好的分解,且温度越高,越有利于除去该反应产物。同时,优选地,各次退火处理的退火时间为1~10min,且各次退火处理的退火时间间隔为10~60s。本领域的技术人员可以根据本申请的教导设定退火处理的次数,在一种优选的实施方式中,对晶圆进行两次退火处理,且第一次退火处理的退火温度为110~130℃,第二次退火处理的退火温度为140~160℃。其具体工艺过程为:首先,反应气体选用NH4F和NH4F·HF,在110~130℃的退火温度下进行第一次退火处理,此时未与晶圆表面杂质反应的NH4F和NH4F·HF,以及反应产物(NH4)2SiF6因受热升华而从晶圆表面去除,但是仍然有部分(NH4)2SiF6没有因为受到退火处理而被分解二残留在晶圆表面;然后,在140~160℃的较高退火温度下进行第二次退火处理,由于上一步退火处理后反应产物的厚度变薄,从而有利于进一步去除残留的反应产物(NH4)2SiF6。在上述优选的实施方式中,进一步地,在退火处理的步骤中,还可以进一步向反应室中通入H2。在多次退火处理以分解反应产物的工艺中,通入H2能够有利于反应产物的分解。本领域的技术人员可以根据实际工艺需求选择合适的气体流量,优选地,H2的气体流量为200sccm~1000sccm。上述优选的工艺参数能够进一步促进反应气体与反应产物的分解,使晶圆表面的残留物被更多的分解掉。在一种优选的实施方式中,晶圆在进行表面处理之前,还包括在晶圆上形成晶体管的步骤。在晶圆表面形成上述晶体管之后,再对晶圆进行表面处理,可以减少在形成晶体管的工艺中在晶圆表面产生的反应产物,从而能够提高后续形成的半导体器件的性能。本申请还提供了一种半导体器件的制作方法,如图2所示,该制作方法包括以下步骤:利用上述的表面处理方法对晶圆或设置有晶体管的晶圆进行表面处理;在表面处理后的晶圆上设置半导体器件结构以形成半导体器件。上述半导体器件的制作方法通过对晶圆进行多次退火处理,从而使表面处理工艺中产生的反应产物能够被多次分解,且每次退火处理均会对反应产物进行分解以使反应产物的厚度不断减小,同时也降低了由于反应产物的厚度过厚导致的反应产物的分解难度,进而使晶圆表面上的反应产物更容易被分解掉,减少了表面处理工艺中产生的反应产物的残留物对半导体器件性能的影响,使半导体器件具有更高的器件稳定性与良率。下面将更详细地描述根据本申请提供的半导体器件的制作方法的示例性实施方式。然而,这些示例性实施方式可以由多种不同的形式来实施,并且不应当被解释为只限于这里所阐述的实施方式。应当理解的是,提供这些实施方式是为了使得本申请的公开彻底且完整,并且将这些示例性实施方式的构思充分传达给本领域普通技术人员。首先,利用上述的表面处理方法对晶圆或设置有晶体管的晶圆进行表面处理。由于上述表面处理的步骤包括对晶圆进行多次退火处理的步骤,从而使表面处理工艺中产生的残留物能够被多次分解,且每次退火处理均会对残留物进行分解以使残留物的厚度不断减小,同时也降低了由于残留物的厚度过厚导致的残留物的分解难度,进而使晶圆表面上的残留物更容易被分解掉,并减少了表面处理工艺中晶圆表面上产生的残留物。完成利用上述的表面处理方法对晶圆进行表面处理的步骤之后,在表面处理后的晶圆上设置半导体器件结构以形成半导体器件。优选地,当表面处理方法是对设置有晶体管的晶圆进行表面处理时,半导体器件结构为与晶体管电连接的金属硅化物。形成该金属硅化物的方法有很多种,在一种优选的实施方式中,形成金属硅化物的步骤包括:在表面处理后的晶圆上沉积金属层;进行热处理以使金属层和晶圆反应形成金属硅化物。上述金属硅化物能够降低源漏接触电阻和寄生串联电阻,以此提高半导体器件的性能。在一种优选的实施方式中,晶体管为源极和漏极,在形成金属硅化物的步骤中,形成与晶体管的源漏极和/或晶体管的栅极电连接的金属硅化物。由于上述经表面处理的晶圆表面具有较少的杂质及反应产物,因此金属硅化物的形成能够更为有效地效降低源漏接触电阻和寄生串联电阻,并进一步提高半导体器件的性能。在上述优选的实施方式中,更为优选的,金属层为NiPt层,形成金属硅化物的步骤包括:进行第一次热处理以使部分金属层和晶圆反应形成Ni2Si层;湿法刻蚀去除剩余金属层;以及进行第二次热处理以使Ni2Si层转变成NiSi层,且NiSi层构成金属硅化物。上述工艺步骤通过在Ni中掺入少量Pt以及两步退火处理,从而获得了具有较高的高温稳定性能的NiSi层; 并且,NiSi层的形成过程对源/漏极中硅的消耗较少,而靠近表面的硅刚好是掺杂浓度最大的区域,因而对于降低整体的接触电阻十分有利。需要注意的是,形成金属硅化物的步骤并不仅限于上述优选实施方式。例如,形成金属硅化物的步骤还可以为:在表面处理后的晶圆上沉积金属层;进行热处理以使金属层和晶圆反应形成金属硅化物;在金属硅化物上形成掩膜层。上述掩膜层可以采用本领域常见的介质材料。优选地,掩膜层的材料为TiN,形成上述掩膜层的工艺可以为化学气相沉积等,本领域的技术人员可以根据实际工艺需求选择合适的工艺及其参数。本申请还提供了一种半导体器件。该半导体器件包括形成有晶体管的晶圆,以及与晶体管电连接的金属硅化物,且半导体器件由上述的制作方法制作而成。由于上述制作方法中包括对晶圆进行多次退火处理的步骤,从而使表面处理工艺中产生的反应产物能够被多次分解,且每次退火处理均会对反应产物进行分解以使反应产物的厚度不断减小,同时也降低了由于反应产物的厚度过厚导致的反应产物的分解难度,使晶圆表面上的反应产物更容易被分解掉,并减少了表面处理工艺中晶圆表面上产生的反应产物的残留物。进而使通过上述晶圆形成的半导体器件具有更高的器件稳定性与良率。下面将结合实施例进一步说明本申请提供的晶圆的表面处理方法。实施例1本实施例提供的晶圆的表面处理的步骤包括:首先,将晶圆置于反应室中;然后,向反应室中通入NF3和NH3作为前驱气体,以生成NH4F和NH4F·HF作为反应气体;接下来,利用反应气体与晶圆表面上的SiO2杂质进行反应以形成反应产物;最后,对晶圆进行两次退火处理,以分解去除反应产物,其中,两次退火处理的温度均为140℃,退火时间均为1min。实施例2本实施例提供的晶圆的表面处理的步骤包括:首先,将晶圆置于反应室中;然后,向反应室中通入NF3和NH3作为前驱气体,以生成NH4F和NH4F·HF作为反应气体;接下来,利用反应气体与晶圆表面上的SiO2杂质进行反应以形成反应产物;最后,对晶圆进行两次退火处理,以分解去除反应产物,其中,第一次退火处和第二次退火处理的退火处理的温度依次为110℃和160℃,退火时间均为5min。实施例3本实施例提供的晶圆的表面处理的步骤包括:首先,将晶圆置于反应室中;然后,向反应室中通入NF3和NH3作为前驱气体,以生成NH4F和NH4F·HF作为反应气体;接下来,利用反应气体与晶圆表面上的SiO2杂质进行反应以形成反应产物;最后,对晶圆进行三次退火处理,以分解去除反应产物,其中,第一次退 火处理、第二次退火处理和第三次退火处理的温度依次为110℃、130℃和150℃,退火时间均为10min。对比例1本对比例提供的晶圆的表面处理的步骤包括:首先,将晶圆置于反应室中;然后,向反应室中通入NF3和NH3作为前驱气体,以生成NH4F和NH4F·HF作为反应气体;接下来,利用反应气体与晶圆表面上的SiO2杂质进行反应以形成反应产物;最后,对晶圆进行一次退火处理,以分解去除反应产物,其中,退火处理的温度为140℃,退火时间均为5min。利用扫描电镜观察对实施例1至3及对比例1中的晶圆进行表面处理前后的形貌,并计算对晶圆进行表面处理前后的残留物去除率,其结果请见表1。从表1可以看出,对实施例1至3中的晶圆进行表面处理前后的残留物去除率为88%~93%,而对对比例1中的晶圆进行表面处理前后的残留物去除率仅为67%。可见,本发明提供的表面处理方法能够减少表面处理工艺中晶圆表面上产生的残留物。表1残留物去除率实施例192%实施例293%实施例388%对比例167%分别在上述实施例1至3和对比例1中进行了表面处理的晶圆上设置半导体器件结构以形成半导体器件。由于上述实施例1至3中表面处理后的晶圆表面具有更少的残留物,并且越少的残留物对形成的半导体器件性能的影响也就越小,因此利用实施例1至3中表面处理后的晶圆形成的半导体器件具有更高的器件稳定性以及良率。从以上的描述中,可以看出,本申请上述的实施例实现了如下技术效果:本申请提供的晶圆的表面处理方法通过对晶圆进行多次退火处理,从而使表面处理工艺中产生的反应产物能够被多次分解,且每次退火处理均会对反应产物进行分解以使反应产物的厚度不断减小,同时也降低了由于反应产物的厚度过厚导致的反应产物的分解难度,进而使晶圆表面上的反应产物更容易被分解掉,减少了表面处理工艺中晶圆表面上产生的反应产物的残留物。以上仅为本申请的优选实施例而已,并不用于限制本申请,对于本领域的技术人员来说,本申请可以有各种更改和变化。凡在本申请的精神和原则之内,所作的任何修改、等同替换、改进等,均应包含在本申请的保护范围之内。当前第1页1 2 3