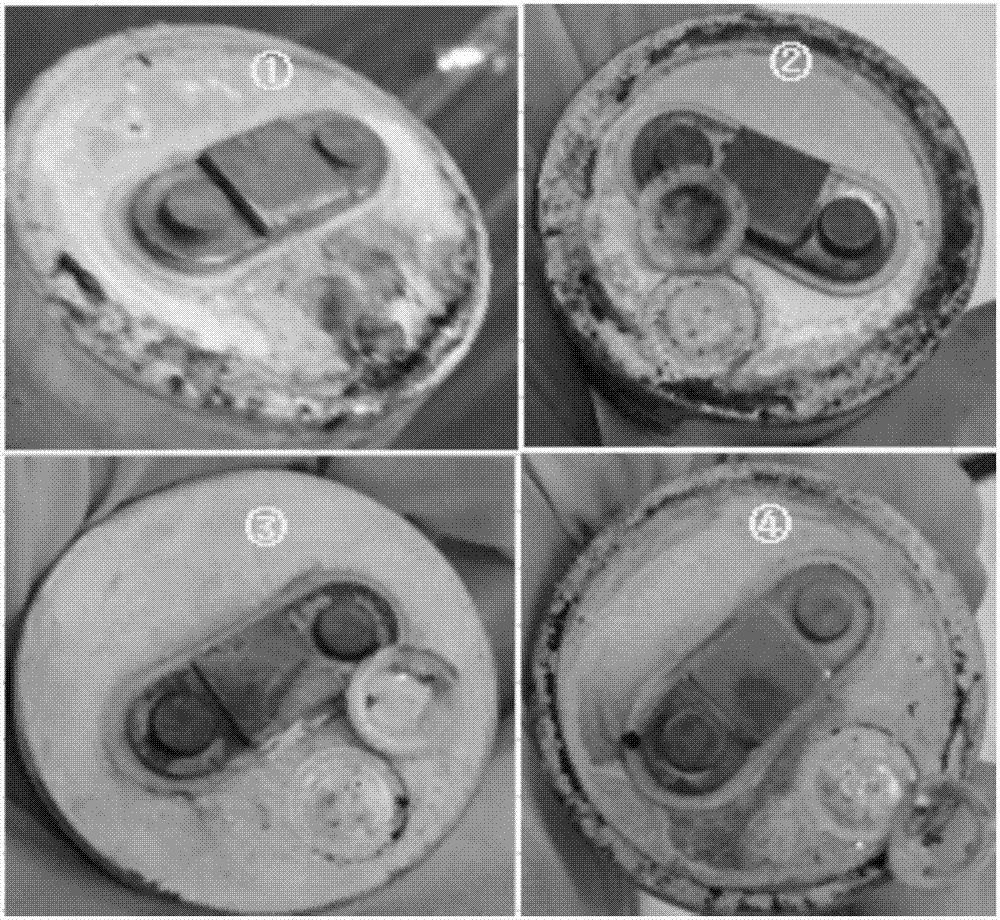
本发明涉及电池制备技术,特别是通过产线制程对锂离子电池铝外壳与负极电压影响的研究,具体的,其展示一种制程对锂离子电池铝外壳与负极间电压影响的分析方法。
背景技术:
:随着全球能源日趋消耗及环境污染不断加剧,作为绿色环保新能源的锂离子电池引起了大家的高度重视和青睐;为减少传统汽油车尾气污染,锂离子电池正逐步运用到纯电动大巴、轿车等领域,锂离子电池的安全性和寿命就成为大家关注的焦点,但锂离子电池铝外壳与负极电压偏低,会引起壳腐蚀,严重时会腐穿壳体,导致电解液流出,对安全性和寿命存在严重的不利隐患;因此,搞清楚在实际制造生产过程中,导致锂离子电池铝外壳与负极电压偏低的制程因素,对于后期改善预防该类问题,提高锂离子电池产品质量等方面都具有重要的指导意义。因此,有必要提供一种制程对锂离子电池铝外壳与负极间电压影响的分析方法来解决上述问题。技术实现要素:本发明通过如下技术方案实现上述目的:一种制程对锂离子电池铝外壳与负极间电压影响的分析方法,包括如下分析实验:1)负极与壳内壁接触短路分析实验:选用①分切后空箔部位毛刺较长的负极片、②卷芯负极耳绝缘胶带移位、③卷芯负极耳金属部位与铝壳内壁接触、④卷芯外圈隔膜破损负极片与铝壳内壁接触,将①~④分别做成电池;①~④分别做成电池,开口经化成后,测试铝外壳与负极电压2)化成未充到电电池的分析实验:s1,将因开口化成柜柜点接触不好,导致未充到电的电池(0%soc)选出,测试其壳电压;s2,将该类电池再次重新化成均充到电后(0.05c恒流充电2h,10%soc),复测壳电压;s3,根据s1,s2绘制对比化成有无充到电对壳电压的影响,电压曲线图图2;3)电解液粘附于铝外壳和负极间的电池的分析实验:s1:分别取将合格电池中开口化成后电解液粘附于铝外壳和负极间的电池、以及铝外壳洁净的合格电池各5只;s2,分别测试对比各自壳电压;4)铝外壳与负极被金属搭接的电池分析试验:s1,取铝外壳与负极被金属部件搭接的电池,及未被金属部件搭接的合格电池各5只;s2,进行取化成、分容、pack周转和测试过程,测试对比各自壳电压;s3,取6只壳电压在1~2v内的合格电池,2只一组共3组,测试初始壳电压,然后分别用金属导线搭接铝外壳与负极,搭接时间分别为5s、1h、18h,移去金属导线,测试静置0s、2h、24h、48h、7d各时间段各组的壳电压;s4,取壳电压为1~2v的合格电池,用导线将其外壳与负极搭接,并用透明胶带固定好,,然后以0.5c倍率对其连续充放电10周,查看铝壳腐蚀情况;5)pack串联电池中铝壳碰接电池的实验:取在制程pack站,出现不同节数电池铝壳碰接的模组电池,2个样品模组电池,测试记录各模组各节电池的壳电压;然后对2个样品模组进行0.5c循环;6)壳电压正常品与不合格品电压值对比实验:取产线化成分容后壳电压合格与ng的批量产电池,测试各自壳电压数据;7)壳电压偏低电池的正短实验取负极与铝壳内壁短路类电池即壳电压为0v电池2只,1.4中负极与铝壳外壁短路类电池中,壳电压在0.1~0.3v范围电池2只,壳电压在0.3~0.5v范围电池2只,测试其初始的壳电压,然后用导线碰接导通电池正极与铝外壳2h后,移去导线,测试此时电池的开始壳电压,静置7天后再次测试壳电压,然后做循环测试(0.5c充电至100%soc,0.5c放电至2.0v),测试循环后的壳电压及对比铝外壳腐蚀情况;8)壳电压偏低电池的铝壳腐蚀机理实验:查阅北京大学化学与分子工程学院倪江锋等人的《锂离子电池集流体的研究》文献中,关于集流体al本身嵌锂性能的研究,发现al在低电压0.2~0.4v平台段,发生锂铝合金的副反应。与现有技术相比,本发明通过一系列的实验分析生产支持对锂离子电池外壳与负极电压的影响,为后期改善预防该类问题,提高锂离子电池产品质量等方面提供支持。附图说明图1是本发明的实施例的实验1的示意图;图2是本发明的实施例的实验2的示意图;图3是本发明的实施例的实验3的示意图;图4是本发明的实施例的实验4的示意图之一;图5是本发明的实施例的实验4的示意图之二;图6是本发明的实施例的实验4的示意图之三;图7是本发明的实施例的实验5的示意图之一;图8是本发明的实施例的实验5的示意图之二;图9是本发明的实施例的实验5的示意图之三;图10是本发明的实施例的实验6的示意图;图11是本发明的实施例的实验7的示意图之一;图12是本发明的实施例的实验7的示意图之二;图13是本发明的实施例的实验7的示意图之一;图14是本发明的实施例的实验7的示意图之二;具体实施方式实施例:本实施例展示一种制程对锂离子电池铝外壳与负极间电压影响的分析方法,包括如下分析实验1)负极与壳内壁接触短路分析实验:选用①分切后空箔部位毛刺较长的负极片、②卷芯负极耳绝缘胶带移位、③卷芯负极耳金属部位与铝壳内壁接触、④卷芯外圈隔膜破损负极片与铝壳内壁接触,将①~④分别做成电池;①~④分别做成电池,开口经化成后,测试铝外壳与负极电压,结果如表1;再经续化成和分容,然后循环5次(0.5c充电至100%soc,0.5c放电至2.0v),对比铝壳腐蚀情况,结果如下表:类型化成分容后壳电压/v方案①0方案②0方案③0方案④0由表中可以看得出,负极与铝壳内壁短路类电池的壳电压全部为0v,说明电池内部,卷芯负极与壳内壁发生接触短路时,会造成铝外壳与负极短路,壳电压偏低不良;在此低电压状态下,锂离子电池经几次短暂充放电后,铝壳腐蚀情况参照图1所展示的四组腐蚀照片;参照图1,可以得出负极与铝壳内壁短路类电池,经过短暂几次充放电后,铝壳最薄处的防爆阀出现腐蚀,腐穿后电解液流出;原因在于制程中的负极分切站毛刺、卷绕或组装站的极耳贴胶、组装站的极耳焊接、组装站的卷芯入壳,四个制程因素均易出现负极与壳内壁接触短路,从而引起后续壳电压偏低不良的问题,电池充放电过程中,铝壳发生电化学腐蚀。2)化成未充到电电池的分析实验:s1,将因开口化成柜柜点接触不好,导致未充到电的电池(0%soc)选出,测试其壳电压;s2,将该类电池再次重新化成均充到电后(0.05c恒流充电2h,10%soc),复测壳电压;s3,根据s1,s2绘制对比化成有无充到电对壳电压的影响,电压曲线图图2,参照图2,可以得出:化成未充到电的电池,即初始soc为0%时,电池壳电压异常偏低均为负值,分布在-50mv~-100mv之间;当对这些电池重新化成充到电后,即初始soc为10%后,电池壳电压全部变为正值,分布在1.5-2.0v之间;说明化成如果未充上电,此因素也会出现电池壳电压偏低的问题。3)电解液粘附于铝外壳和负极间的电池的分析实验:s1:分别取将合格电池中开口化成后电解液粘附于铝外壳和负极间的电池、以及铝外壳洁净的合格电池各5只;s2,分别测试对比各自壳电压;参照图3,可以得出化成后的带电锂离子电池,外壳洁净品的壳电压全部在1~2v范围内;若铝外壳和负极间粘附导电的电解液液体,即被电解液导通铝外壳与负极,则壳体电压全部偏低,分布在0~0.4v范围内;说明导电液体粘附于带电锂离子电池的铝外壳与负极间,也是导致壳电压偏低的制程因素之一。4)铝外壳与负极被金属搭接的电池分析试验:s1,取铝外壳与负极被金属部件搭接的电池,及未被金属部件搭接的合格电池各5只;s2,进行取化成、分容、pack周转和测试过程,测试对比各自壳电压;参照图4,可得出被充放电过的电池在周转或测试过程中,未被金属部件搭接铝外壳与负极的电池,其壳电压全部在1~2v范围内,但被搭接的电池,其壳电压在0~0.4v范围内,说明铝外壳与负极被金属搭接,也是导致壳电压偏低的制程因素之一;s3,取6只壳电压在1~2v内的合格电池,2只一组共3组,测试初始壳电压,然后分别用金属导线搭接铝外壳与负极,搭接时间分别为5s、1h、18h,移去金属导线,测试静置0s、2h、24h、48h、7d各时间段各组的壳电压,如下表;同时参照图5,可得出:初始壳电压在1.5~1.9v内的合格电池,①被金属导线导通后,移去导线初期均出现壳电压偏小问题;②移去导线后,壳电压均有所反弹恢复,但均低于初始值,即无法恢复如初;③以y轴中的某一定值作与x轴平行线与3组曲线相交,发现导线搭接的时间越短,后期导线移去后壳电压恢复至该定值电压所需的时间越短,反之越长;④以x轴中的某一定值作与y轴平行线与3组曲线相交,发现后期导线移去后在该相同静置定值时间内,导线搭接的时间越短,壳电压恢复值相对越大,反之越小;s4,取壳电压为1~2v的合格电池,用导线将其外壳与负极搭接,并用透明胶带固定好,,然后以0.5c倍率对其连续充放电10周,查看铝壳腐蚀情况;参照图6,可得出:初始壳电压1~2v的合格电池,铝壳防爆阀无腐蚀及漏液,但经导线搭接并做几次充放电后,铝壳防爆阀就出现腐蚀及漏液问题。说明铝外壳和负极间若被导电液体或金属导通,在此状态下,电池若进行充放电,易出现铝壳的腐蚀及腐穿漏液。5)pack串联电池中铝壳碰接电池的实验:取在制程pack站,出现不同节数电池铝壳碰接的模组电池,2个样品模组电池,测试记录各模组各节电池的壳电压,下表:样品模组内各节电池壳电压模组16.77v、0.182v、其余均在1-2v内模组29.56v、-0.105v、其余均在1-2v内然后对2个样品模组进行0.5c循环,后得出图7评估循环性能图和铝壳腐蚀情况图图8;同模组内不同节数电池若外壳出现碰接,则碰接的两个单节电池各自的壳电压,一个偏高,一个偏低;偏高值高出满电电池正负极电压,偏低值低于0v,而化成分容后的电池壳电压一般为1~2v,100%soc满电电池正负极电压3.4v左右,所以理论上单节壳电压范围应该在0~3.4v,不可能出现表3中的6-10v和负值壳电压值,但是一旦串联模组内不同节数电池若外壳出现碰接,就会出现该问题,说明pack站模组中串联电池铝外壳碰接,也是导致壳电压偏低的制程因素之一;模组中串联电池铝外壳碰接的壳电压偏低的电池,在循环一定圈数后,铝壳防爆阀开始腐蚀,随着循环充放电次数增加,防爆阀被腐穿,壳内电解液流出,导致循环性能变差,循环50周,容量保持率只有初始的50%~70%;导致表格、图7、图8中壳电压异常及腐蚀的原因分析如下。后参照图9,pack的一个模组里含有3串电池即节数为3节,视总负第1节负极相对电位为0v,壳电位为1.5v,电池正极电位为3v,那么各节相对正负极及壳电压数值如图9所标,当第1节与第3节电池铝外壳未碰接时,则外部未形成回路,对各节电池的壳电压无影响;但当第1节与第3节电池铝外壳发生碰接时,相当于图9红色虚线示意的用导线连通一样,此时外部形成回路,那么图9中第3节电池的壳电压v5=7.5v与第1节电池的壳电压v1=1.5v,会出现6v的压差,两者电压势必要不断趋于平衡,v5不断变小而v1不断变大,直至平衡,那么对于第3节电池则出现v5-v4=7.5↓-6=1.5↓壳电压不断减小的变化,而对于第1节电池则出现v1-v0=1.5↑-0=1.5↑壳电压不断增大的变化;若模组中串联电池的节数越多,壳电压数值变化越大,最终外壳碰接的两节电池的壳电压,一个偏大,一个偏小,出现上表中的数值情况;壳电压偏小者,存在铝壳防爆阀腐蚀及腐穿问题,于此同时由于电解液漏出,内部卷芯干枯,直接影响到电池的循环性能。6)壳电压正常品与不合格品电压值对比实验取产线化成分容后壳电压合格与ng的批量产电池,测试各自壳电压数据,将数值按升序排序后得出图10;经过化成分容充放电后的电池,壳电压ng品的壳电压范围为0~0.5v,壳电压ok品的壳电压范围为1~2v,因此将0.5v定义为壳电压是否合格的临界点标准较为合理。7)壳电压偏低电池的正短实验取负极与铝壳内壁短路类电池即壳电压为0v电池2只,1.4中负极与铝壳外壁短路类电池中,壳电压在0.1~0.3v范围电池2只,壳电压在0.3~0.5v范围电池2只,测试其初始的壳电压,然后用导线碰接导通电池正极与铝外壳2h后,移去导线,测试此时电池的开始壳电压,静置7天后再次测试壳电压,然后做循环测试(0.5c充电至100%soc,0.5c放电至2.0v),测试循环后的壳电压及对比铝外壳腐蚀情况,结果如下表、图11、图12;可得出:①负极与铝壳内壁短路类电池,通过导线将正极与铝外壳短路,壳电压从0v回升至>2.5v,但7天后仍跌回0v,循环后出现铝外壳防爆阀腐蚀且腐穿的问题,电解液流出,循环容量保持率下跌迅速;②负极与铝壳外壁短路类电池中,壳电压在0.1~0.3v和0.3~0.5v两类电池,通过导线将正极与铝外壳短路,壳电压回升至>2.5v,7天后壳电压均出现回跌,数值比初始壳电压要大;③0.1~0.3v类电池7天回跌至在0.5~1.0v之间,比0.3~0.5v类电池循环后,7天回跌值在1~2v之间要小;④0.3~0.5v、0.1~0.3v、0v三类初始壳电压电池,循环性能依此变差,铝外壳腐蚀程度逐渐增大;其中0.3~0.5v类电池,经过导线将正极与铝外壳后,壳电压恢复正常(>1v),铝外壳未腐蚀且循环性能ok;⑤循环后,负极与铝壳内壁短路类电池,壳电压仍为0v不变,而负极与铝壳外壁短路类电池,壳电压均有所增大。综合①~⑤,我们可以发现,经过正短实验后:第一,负极与铝壳内壁短路类电池,由于循环性能差,铝壳腐蚀严重的问题,无法将其挽救成合格品;第二,负极与铝壳外壁短路类电池中壳电压偏低品(0.1~0.3v),此部分正短2h移去导线,静置7天后壳电压在0.5~1v,存在循环性能不佳,铝壳轻微腐蚀的问题,所以此部分电池存在较大的品质隐患;第三,负极与铝壳外壁短路类电池中壳电压偏低品(0.3~0.5v),此部分正短2h移去导线,静置7天后壳电压在>1v,电位较高,循环性能ok,铝壳无腐蚀,此部分电池可通过正短方式,将其挽救成合格品。8)壳电压偏低电池的铝壳腐蚀机理实验:查阅北京大学化学与分子工程学院倪江锋等人的《锂离子电池集流体的研究》文献中,关于集流体al本身嵌锂性能的研究,发现al在低电压0.2~0.4v平台段,发生锂铝合金的副反应,如图13;生成锂铝合金后al变灰黑色,失去金属光泽,al粉化严重,如图14。综合上述实验,可得出结论:1)壳电压偏低可以分为四大类:负极与铝壳内壁短路,壳电压偏低;电池化成未充到电,壳电压偏低;负极与铝壳外壁短路,壳电压偏低;pack串联电池铝外壳碰接,壳电压偏低。2)引起负极与铝壳内壁短路壳电压偏低的制程因素有①负极分切站负极片分切后空箔部位毛刺较长、②卷绕或组装站的极耳贴胶,胶带移位、③组装站的极耳焊接其极耳金属部位与铝壳内壁接触、④组装站的卷芯入壳,外圈隔膜破损负极片与铝壳内壁接触。3)引起电池化成未充到电壳电压偏低的制程因素,主要是化成柜柜点与电池极耳接触不好,导致电池未充上电。4)引起负极与铝壳外壁短路壳电压偏低的制程因素有①周转过程中铝外壳与负极被导电液体粘附导通(如电解液);②化成、分容、pack周转和测试过程中铝外壳与负极被金属搭接。5)pack串联电池铝外壳碰接,壳电压偏低的制程因素,主要为电池外表面未热缩绝缘套或模组盒设计不当,在其内电池过挤,磨破热缩的绝缘套,致使串联电池铝外壳出现碰接。6)壳电压偏低时,在此低电位下充放电,电池循环性能差,铝壳出现电化学腐蚀,生成锂铝合金。7)通过正短方式即用导线碰接导通电池正极与铝外壳2h后,可将负极与铝壳外壁短路类中壳电压在0.3~0.5v范围内电池,壳电压恢复至1~2v成合格品且合格品循环性能ok及铝壳未出现腐蚀;但负极与铝壳外壁短路类中壳电压在在0.1~0.3v范围内电池,壳电压只能恢复至0.5-1v之间,存在循环性能偏差和铝外壳腐蚀的隐患;而负极与铝壳内壁短路类电池,根本无法补救,循环性能差,铝壳腐蚀,属于永久ng品。8)al形成锂铝合金的电压0.2~0.4v平台段,进一步说明在上述2.5中壳电压正常品与不合格品电压值对比测试,将0.5v定义为判定壳电压是否合格的临界点标准,较为合理。本实施例一系列的实验分析生产支持对锂离子电池外壳与负极电压的影响,为后期改善预防该类问题,提高锂离子电池产品质量等方面提供支持。以上所述的仅是本发明的一些实施方式。对于本领域的普通技术人员来说,在不脱离本发明创造构思的前提下,还可以做出若干变形和改进,这些都属于本发明的保护范围。当前第1页12