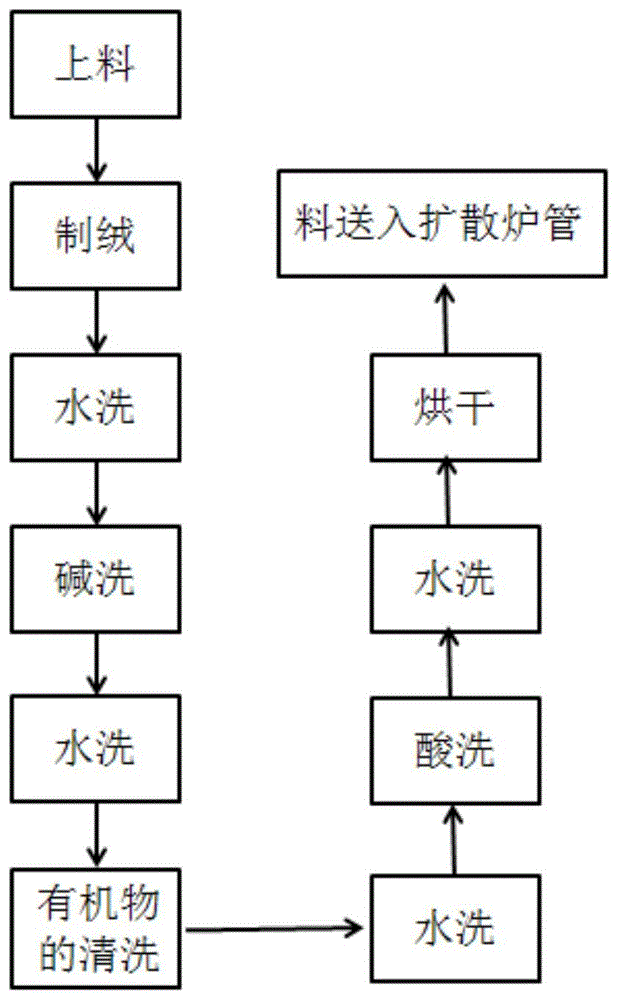
本发明涉及晶体硅太阳能电池
技术领域:
,尤其涉及一种下降漏电提升效率的多晶清洗工艺。
背景技术:
:晶体硅太阳能电池技术迭代带来的成本下降逐步成为推动行业发展的主要动力,近两年来,多晶金刚线切割带来多晶成本上的明显下降,每片在0.6元以上。但基于多晶的制绒原理,金刚线切割带来的低损伤层不利于绒面的形成,成本下降的同时,不可避免带来效率的损失,因此目前多晶金刚线制绒工序都需要添加剂的辅助完成。多晶制绒工序的流程是:上料→硝酸+氢氟酸+制绒添加剂混合液形成制绒→水洗→碱洗→水洗→氢氟酸和盐酸混酸清洗→水洗→烘干→下料→进入扩散工序。因添加剂的主要成分是有机物,有机物很难被清洗干净,留在绒面表面,在电池片后道工序中影响就是增加了表面漏电的比例和一定程度的效率下降。中国发明专利申请号为cn201710355691.0的专利,公开了一种降低多晶电池片漏电的工艺方法,其采用槽式清洗的方法,在清洗机的第一槽体中加入双氧水、氢氟酸、和水的混合物,用双氧水氧化掉硅片表面的有机脏污,把金属离子由低价氧化成高价态,同时在硅片表面形成一层二氧化硅薄层,用氢氟酸洗掉带走部分有机污染和金属离子。该专利解决了槽式多晶制绒的有机脏污残留,但在链式多晶生产线未能推广,另外对多晶酸制绒产生的多孔硅复合结构也没有起到良好的去除效果。技术实现要素:为了解决多晶制绒添加剂带来有机物残留导致后续漏电增加,效率存在一定影响的缺点,本发明提供了一种改善多晶添加剂制绒导致的太阳能电池rsh偏低、irev大的清洗工艺,该工艺利用过氧化氢分解附着在制绒后硅片表面的添加剂成分,并用低浓度的碱水去除酸制绒产生的不利于pn结多孔硅,和二次修饰易磨损的绒面凸起,再经后续的盐酸和氢氟酸清洗金属离子及二氧化硅,达到清洁绒面、保护pn结的目的,从而提升多晶电池rsh的目的。本发明的具体技术方案为:一种下降漏电提升效率的多晶清洗工艺,包括以下步骤:(1)上料:将p型原始硅片导入制绒机;(2)制绒:用制绒混合液对p型原始硅片进行制绒;(3)水洗:将经步骤(2)制绒后的硅片表面的残酸进行喷淋清洗;(4)碱洗:将经步骤(3)水洗后的硅片用koh溶液进行碱洗;此步骤的效果主要是制绒完成之后消除硅片表面形成的多孔硅。(5)水洗:将经步骤(4)碱洗后的硅片表面的残碱进行喷淋清洗;(6)有机物的清洗:将经步骤(5)水洗后的硅片用清洗液进行清洗;此步骤的效果主要是通过双氧水和碱的混合液对硅片表面残留的有机物进行进一步的清洁和绒面的再次修饰。(7)水洗:将经步骤(6)清洗后硅片表面的残留物进行喷淋清洗;(8)酸洗:将经步骤(7)清洗后的硅片用混合酸液进行酸洗;此步骤的效果主要是通过混酸的清洗,对硅片表面的氧化物和金属离子进行清洗,提高硅片的洁净度,以此提升成品电池的开路电压和转换效率。(9)水洗:将经步骤(8)酸洗后的硅片表面的残酸进行喷淋清洗;(10)烘干:将经步骤(9)水洗后的硅片用压缩空气烘干;(11)下料送入扩散炉管:将经步骤(10)烘干后的硅片在30min内送入扩散炉管进行扩散。此步骤的主要关键在于下料至扩散炉管的时间,硅片在空气中滞留时间越长,遭遇二次污染的概率和氧化会加大,不利于硅片的清洁。本发明的目的在于提供一种下降漏电提升效率的多晶清洗工艺,该工艺采用在现有的制绒完成之后,再对硅片进行相应配比浓度的化学品清洗,达到对硅片表面的有机物和其余杂质的再一次清洁,从而下降电池的表面漏电,提升电池的效率。目前现有技术中普通多晶硅片的转换效率较低,多晶硅片的表面被氧化或污染后,转换效率会有所下降,影响太阳能多晶电池片的性能。本发明人通过调节多晶硅片清洗过程中的试剂浓度和清洗时间,在除去多晶硅片表面的杂质和氧化层的同时提高了多晶硅片的rsh。本发明通过用水、碱溶液、有机物清洗和混合酸溶液清洗多晶硅片,处理温度温和,多晶硅片表面更洁净,有利于后续处理工艺的进行。本发明在现有的制绒完成之后,再对硅片进行相应配比浓度的化学品清洗,达到对硅片表面的有机物和其余杂质的再一次清洁,从而可以提升电池片的效率和电池片的rsh,一般效率提升在0.01~0.02%左右,rsh可以增加50以上,最终的成品电池中漏电不良品可以下降0.3~0.4%。本发明的清洗工艺,看似与现有技术中的同类产品制绒清洗的区别不是很大,但是在太阳能多晶硅片清洗领域中,常用的清洗剂就那么几种,目前清洗剂的选用上已很难有突破,而多晶硅片清洗后的性能的差异主要来自于不同清洗剂浓度和配比的调整。针对多晶硅片清洗后的某一种性能来说,也许可以通过简单的有限次试验就能够获得较佳的性能,但是要使清洗后的太阳能多晶硅片的综合性能整体得到提升,却并没有想象地那么简单。例如,在清洗过程中,增加某一种清洗剂的浓度或用量也许能够极大的提升多晶电池rsh,但是同时却会影响多晶硅片的表面反射率、漏电和短路电流,而目前来说,人们还无法从这种复杂的大量试验中总结出一套较为明显的规律。这也是目前还没有一条既能将多晶硅片表面杂质除净又能降低漏电、提高多晶硅片的转化效率的原因。作为优选,步骤(2)中,所述制绒混合液中硝酸的浓度为9~14wt%、氢氟酸的浓度为28~38wt%、制绒添加剂的浓度为0.3~2wt%。作为优选,所述制绒添加剂为三峰多晶制绒添加剂。本发明所用的制绒添加剂为现有技术的制绒添加剂,购自湖州三峰能源科技有限公司,本领域技术人员也可适购现有技术中的其他制绒添加剂。制绒添加剂能够加速反应液在硅片表面的反应速率,并且在抛光处能够获得更多的绒面作为优选,所述制绒时带速控制在1.6~2.3m/min,制绒温度控制在7~9℃。作为优选,步骤(4)中,所述koh溶液的浓度为1~7wt%;所述碱洗时间为10~60s。氢氧化钾溶液可洗去多晶硅片表面的油污,并对多晶硅片的绒面进行再修饰。氢氧化钾的浓度过高会导致清洗后的多晶硅片的表面反射率的变化值过大,降低多晶硅片的短路电流。作为优选,步骤(6)中,所述清洗液中双氧水浓度为4~7wt%,koh浓度为1~7wt%;清洗时槽体温度为40~70℃,清洗时间20~70s。本发明利用过氧化氢分解附着在制绒后硅片表面的添加剂成分,并用低浓度的碱水去除酸制绒产生的不利于pn结多孔硅,和二次修饰易磨损的绒面凸起,再经后续的盐酸和氢氟酸清洗金属离子及二氧化硅,达到清洁绒面、保护pn结的目的,从而提升多晶电池rsh的目的。作为优选,步骤(8)中,所述混合酸液中盐酸浓度为10~30wt%,氢氟酸浓度为8~25wt%;所述酸洗为在25~30℃清洗30~90s。酸洗可去除多晶硅片表面的金属杂质和氧化硅层。本发明采用盐酸溶液和氢氟酸溶液的混合酸溶液清洗多晶硅片,盐酸溶液能有效去除多晶硅片表面的金属杂质,氢氟酸溶液能去除多硅片表面的氧化硅。作为优选,步骤(3)中,所述喷淋清洗温度为15~30℃,时间为4~8s;步骤(5)中,所述喷淋清洗温度为15~30℃,时间为4~8s;步骤(7)中,所述喷淋清洗温度为15~30℃,时间为4~8s;步骤(9)中,所述喷淋清洗温度为15~30℃,时间为4~8s。与现有技术对比,本发明的有益效果是:本发明采用双氧水和氢氧化钾的混合液对硅片表面的有机物再一次清洁,并在制绒完成之后30min内送入扩散炉管,避免有机物的残留和空气的二次污染带来的电池表面漏电和效率损失。附图说明图1为本发明的一种下降漏电提升效率的多晶清洗工艺的流程图。具体实施方式下面结合实施例对本发明作进一步的描述。在本发明中所涉及的装置、连接结构和方法,若无特指,均为本领域公知的装置、连接结构和方法。实施例1一种下降漏电提升效率的多晶清洗工艺,包括以下步骤:(1)上料:将p型原始硅片导入制绒机;(2)制绒:用制绒混合液对p型原始硅片进行制绒;所述制绒混合液中硝酸的浓度为12wt%、氢氟酸的浓度为33wt%、制绒添加剂的浓度为1wt%;制绒添加剂为三峰多晶制绒添加剂;所述制绒时带速控制在2m/min,制绒温度控制在8℃;(3)水洗:将经步骤(2)制绒后的硅片表面的残酸在25℃喷淋清洗6s;(4)碱洗:将经步骤(3)水洗后的硅片用浓度为2wt%的koh溶液碱洗20s;(5)水洗:将经步骤(4)碱洗后的硅片表面的残碱在25℃喷淋清洗6s;(6)有机物的清洗:将经步骤(5)水洗后的硅片用清洗液在55℃清洗30s;清洗液中双氧水浓度为5wt%,koh浓度为3wt%;(7)水洗:将经步骤(6)清洗后硅片表面的残留物在25℃喷淋清洗6s;(8)酸洗:将经步骤(7)清洗后的硅片用混合酸液在25℃酸洗70s;混合酸液中盐酸浓度为15wt%,氢氟酸浓度为9wt%;(9)水洗:将经步骤(8)酸洗后的硅片表面的残酸在25℃喷淋清洗6s;(10)烘干:用压缩机对空压进行压缩,将经步骤(9)水洗后的硅片用风刀烘干;(11)下料送入扩散炉管:将经步骤(10)烘干后的硅片在30min内送入扩散炉管进行扩散。实施例2一种下降漏电提升效率的多晶清洗工艺,包括以下步骤:(1)上料:将p型原始硅片导入制绒机;(2)制绒:用制绒混合液对p型原始硅片进行制绒;所述制绒混合液中硝酸的浓度为14wt%、氢氟酸的浓度为28wt%、制绒添加剂的浓度为2wt%;制绒添加剂为三峰多晶制绒添加剂;所述制绒时带速控制在2.3m/min,制绒温度控制在9℃;(3)水洗:将经步骤(2)制绒后的硅片表面的残酸在30℃喷淋清洗4s;(4)碱洗:将经步骤(3)水洗后的硅片用浓度为3wt%的koh溶液碱洗15s;(5)水洗:将经步骤(4)碱洗后的硅片表面的残碱在30℃喷淋清洗4s;(6)有机物的清洗:将经步骤(5)水洗后的硅片用清洗液在60℃清洗50s;清洗液中双氧水浓度为6wt%,koh浓度为3wt%;(7)水洗:将经步骤(6)清洗后硅片表面的残留物在30℃喷淋清洗4s;(8)酸洗:将经步骤(7)清洗后的硅片用混合酸液在25~30℃酸洗30~90s;混合酸液中盐酸浓度为20wt%,氢氟酸浓度为20wt%;(9)水洗:将经步骤(8)酸洗后的硅片表面的残酸在30℃喷淋清洗4s;(10)烘干:用压缩机对空压进行压缩,将经步骤(9)水洗后的硅片用风刀烘干;(11)下料送入扩散炉管:将经步骤(10)烘干后的硅片在20min内送入扩散炉管进行扩散。实施例3一种下降漏电提升效率的多晶清洗工艺,包括以下步骤:(1)上料:将p型原始硅片导入制绒机;(2)制绒:用制绒混合液对p型原始硅片进行制绒;所述制绒混合液中硝酸的浓度为9wt%、氢氟酸的浓度为38wt%、制绒添加剂的浓度为1.5wt%;制绒添加剂为三峰多晶制绒添加剂;所述制绒时带速控制在1.6m/min,制绒温度控制在7℃;(3)水洗:将经步骤(2)制绒后的硅片表面的残酸在20℃喷淋清洗7s;(4)碱洗:将经步骤(3)水洗后的硅片用浓度为1wt%的koh溶液碱洗60s;(5)水洗:将经步骤(4)碱洗后的硅片表面的残碱在20℃喷淋清洗7s;(6)有机物的清洗:将经步骤(5)水洗后的硅片用清洗液在70℃清洗20s;清洗液中双氧水浓度为7wt%,koh浓度为1wt%;(7)水洗:将经步骤(6)清洗后硅片表面的残留物在20℃喷淋清洗7s;(8)酸洗:将经步骤(7)清洗后的硅片用混合酸液在30℃酸洗30s;混合酸液中盐酸浓度为30wt%,氢氟酸浓度为8wt%;(9)水洗:将经步骤(8)酸洗后的硅片表面的残酸在20℃喷淋清洗7s;(10)烘干:用压缩机对空压进行压缩,将经步骤(9)水洗后的硅片用风刀烘干;(11)下料送入扩散炉管:将经步骤(10)烘干后的硅片在25min内送入扩散炉管进行扩散。对比例1对比例1与实施例1的不同之处在于:对比例1未经有机物的清洗这一步骤,在碱洗、水洗后直接进行酸洗。其他均与实施例1相同。对比例2对比例2与实施例2的不同之处在于:对比例2未经有机物的清洗这一步骤,在碱洗、水洗后直接进行酸洗。其他均与实施例2相同。对比例3对比例3与实施例3的不同之处在于:对比例3未经有机物的清洗这一步骤,在碱洗、水洗后直接进行酸洗。其他均与实施例3相同。性能评价实施例1~3和对比例1~3除清洗工艺不同外,其他制电池片工序条件都确保一样。下表1给出了实施例1~3及对比例1~3测得的电性参数。表1uociscrsrshffncell数量漏电计数漏电比例对比例10.64009.0070.0018153.480.210.1882958101.04%实施例10.63989.0260.0018272.680.170.188495760.63%对比例20.63999.0120.0019194.280.110.188096090.94%实施例20.63999.0120.0018245.580.150.188195960.63%对比例30.64009.0050.0018174.680.130.187995690.94%实施例30.63989.0060.0018262.580.220.188195750.52%由表1可以看出,本发明在现有的制绒完成之后,再对硅片进行相应配比浓度的化学品清洗,达到对硅片表面的有机物和其余杂质的再一次清洁,从而可以提升电池片的效率和电池片的rsh,一般效率提升在0.01~0.02%左右,rsh可以增加50以上,最终的成品电池中漏电不良品可以下降0.3~0.4%。以上所述,仅是发明的较佳实施例,并非对本发明作任何限制,凡是根据本发明技术实质对以上实施例所作的任何简单修改、变更以及等效结构变换,均仍属于本发明技术方案的保护范围。当前第1页12