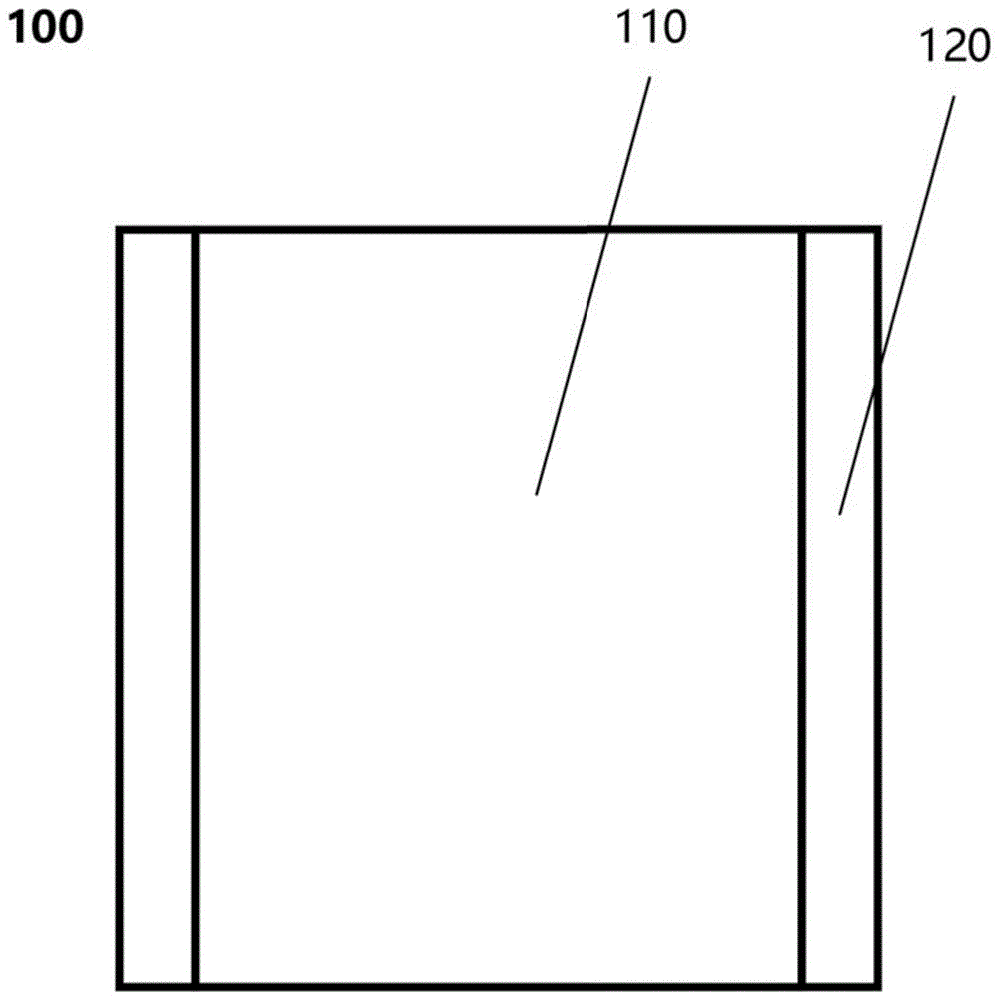
本申请属于锂离子电池
技术领域:
,具体地涉及一种复合聚合物固态电解质及锂电池。
背景技术:
:锂电池是目前发展最快的电池之一。然而随着锂电池市场需求量的增大,锂电池安全性日益凸显。许多手机和汽车的自燃事故都是由于电池内部发生短路产生大量热,导致内部电解液分解而引起的。同时电解液还存在其它问题,如电化学窗口和工作温度受限制,难以兼容金属锂负极和高电势正极材料;在大电流通过时,电池内阻会因离子浓度梯度的出现而增加(浓差极化),导致电池性能下降等缺点。目前,使用固态电解质代替有机电解液,有望从根本上解决上述问题。固态电解质分为无机电解质和有机电解质,其中,无机电解质包括氧化物、硫化物和氟化物等,它们有着高的锂离子电导率/迁移数量和温度范围,但是固相与固相接触导致界面电阻高;有机电解质包括聚环氧乙烷(peo)、聚丙烯腈(pan)、聚偏氟乙烯(pvdf)等,它们有着易制备,形状可控,在低成本下可获得等优点,但由于锂离子电导率不高限制其发展。在固态锂电池中,界面作用对于电池性能有着根本性的影响。在全固态锂电池中,电极与电解质之间的界面接触由固液接触变为固固接触,且由于固相无润湿性特点,固固界面将形成更高的接触电阻。陶瓷电解质中有大量的晶界存在,导致较高的晶界电阻进而不利于锂离子在正负极之间传输(通常晶界电阻高于材料本体电阻)。还有在充过电过程中,电解质和正负极极片之间的界面会有不同程度的膨胀作用,导致界面电阻增大。因此,有必要开发一种新的固态电解质,能够降低固固接触界面电阻,提高电池性能以及安全性。技术实现要素:本申请提供一种复合聚合物固态电解质,能够降低固固接触界面电阻,提高电池性能以及安全性。本申请的一个方面提供一种复合聚合物固态电解质,包括锂盐,聚合物,无机固态电解质以及自修复材料,所述自修复材料选自如结构式(1)所示的化合物中的至少一种:其中,所述n为2,3,4,5或6,所述m为2,3,4,5或6;所述结构中的双键上的氢可以被氨基、巯基、脲基、羟基、f-或cl-取代;所述结构中的甲基上的氢可以被氨基、巯基、脲基、羟基、羧基、羰基、c1-5烷基、c2-6烯基和卤素取代。在本申请的一些实施例中,所述锂盐和所述聚合物的质量比为(1∶3)-(1∶2)。在本申请的一些实施例中,所述无机固态电解质的质量占比为40-65%。在本申请的一些实施例中,所述自修复材料的质量占比为10-20%。在本申请的一些实施例中,所述锂盐为libob、litfsi、lipf6、libf4、liasf6中的一种或多种。在本申请的一些实施例中,所述聚合物为peo、pan、pmma、ppo和pvdf改性结构中的一种或多种。在本申请的一些实施例中,所述无机固态电解质为llzto、li1+xalxti2-x(po4)3、li7la3zr2o12、la2/3-yli3ytio、li1+zalzge2-z(po4)3、li4-age1-apas4、li2s-b2s3-p2s5、li2s-sis2、li2s-p2s5、li2s·sis2·li3po4、li2s·sis2·li3sio4中的一种或多种,其中,所述x为0-2之间;所述y为0-3之间;所述z为0-2之间;所述a为0-1之间。本申请的另一个方面提供一种复合聚合物固态电解质的制备方法,包括:制备无机固态电解质;通过热压方法将所述无机固态电解质、聚合物以及锂盐混合制成聚合物固态电解质;将自修复材料涂敷于所述聚合物固态电解质与正、负电极相连的表面,所述自修复材料选自如结构式(1)所示的化合物中的至少一种:其中,所述n为2,3,4,5或6,所述m为2,3,4,5或6;所述结构中的双键上的氢可以被氨基、巯基、脲基、羟基、f-或cl-取代;所述结构中的甲基上的氢可以被氨基、巯基、脲基、羟基、羧基、羰基、c1-5烷基、c2-6烯基和卤素取代。在本申请的一些实施例中,制备所述无机固态电解质的方法包括:将无机固态电解质材料在800℃-1000℃煅烧3-12小时后制成粉体。本申请的另一个方面还提供一种复合聚合物固态电解质的制备方法,包括:制备无机固态电解质;通过热压方法将所述固态电解质、聚合物、锂盐以及自修复材料均匀混合制成复合聚合物固态电解质,所述自修复材料选自如结构式(1)所示的化合物中的至少一种:其中,所述n为2,3,4,5或6,所述m为2,3,4,5或6;所述结构中的双键上的氢可以被氨基、巯基、脲基、羟基、f-或cl-取代;所述结构中的甲基上的氢可以被氨基、巯基、脲基、羟基、羧基、羰基、c1-5烷基、c2-6烯基和卤素取代。在本申请的一些实施例中,制备所述无机固态电解质的方法包括:将无机固态电解质材料在800℃-1000℃煅烧3-12小时后制成粉体。本申请还一个方面提供一种锂电池,包括正极、负极和以上所述的复合聚合物固态电解质。在本申请的一些实施例中,所述正极包括正极活性物质,所述正极活性物质为磷酸铁锂、licoo2、lifebmncpo4、linio2、linibmnco4、镍钴锰三元材料或富锂锰基中的一种或多种,其中所述b为0-1之间,c为0-1之间。本申请提供的复合聚合物固态电解质,基于无机锂盐、无机固态电解质和聚合物电解质自身的优点,再加入包含氢键的自修复材料,利用所述氢键的作用力来提高界面作用力,既提高了界面接触附着力和兼容性,又降低了界面电阻,同时也优化了固态电解质内部结构。附图说明以下附图详细描述了本申请中披露的示例性实施例。其中相同的附图标记在附图的若干视图中表示类似的结构。本领域的一般技术人员将理解这些实施例是非限制性的、示例性的实施例,附图仅用于说明和描述的目的,并不旨在限制本公开的范围,其他方式的实施例也可能同样的完成本申请中的发明意图。应当理解,附图未按比例绘制。其中:图1为本申请的一些实施例中所述复合聚合物固态电解质的结构示意图。图2为本申请的另一些实施例中所述复合聚合物固态电解质的结构示意图。图3为本申请的一些实施例中所述锂电池的结构示意图。图4为本申请的另一些实施例中所述锂电池的结构示意图。图5为本申请的不同实施例中所述复合聚合物固态电解质的电导率对比图。具体实施方式以下描述提供了本申请的特定应用场景和要求,目的是使本领域技术人员能够制造和使用本申请中的内容。对于本领域技术人员来说,对所公开的实施例的各种局部修改是显而易见的,并且在不脱离本公开的精神和范围的情况下,可以将这里定义的一般原理应用于其他实施例和应用。因此,本公开不限于所示的实施例,而是与权利要求一致的最宽范围。下面结合实施例和附图对本发明技术方案进行详细说明。近年来发展的自修复材料,是一种带有多种功能性基团的聚合物,有着自行发现损伤和裂纹并自动愈合的特效,所述修复过程中不需要内植修复剂,依靠分子内或分子间氢键的断裂和重组,且具有温度低,重复性好等特点。基于以上所述,本申请提供一种复合聚合物固态电解质,基于无机锂盐、无机固态电解质和聚合物电解质自身的优点,加入包含氢键的自修复材料,利用所述氢键的作用力来提高界面作用力,既提高了界面接触附着力和兼容性,又降低了界面电阻,同时也优化了固态电解质内部结构。本申请实施例提供一种复合聚合物固态电解质,包括锂盐,聚合物,无机固态电解质以及自修复材料,所述自修复材料选自如结构式(1)所示的化合物中的至少一种:其中,所述n为2,3,4,5或6,所述m为2,3,4,5或6;所述结构中的双键上的氢可以被氨基、巯基、脲基、羟基、f-或cl-取代;所述结构中的甲基上的氢可以被氨基、巯基、脲基、羟基、羧基、羰基、c1-5烷基、c2-6烯基和卤素取代。其中,所述聚合物可以溶解锂盐;所述锂盐可以提高锂离子的迁移量,提高电池容量;所述无机固态电解质和锂离子之间可以相互作用,在所述无机固态电解质表面形成多个快速锂离子通道,从而提高电导率;所述自修复材料能通过氢键,胺基和羰基等活性基团提高电极与电解质之间的附着力,同时降低电极与电解质界面间的颗粒空隙,抑制材料膨胀,从而提高界面之间的兼容性,降低界面内阻。同时,所述锂盐和无机固态电解质还可以对所述聚合物进行改性,对所述聚合物的基团与其它聚合物进行交联或共聚,打乱聚合物分子链的排列秩序或形成枝化结构来抑制聚合物结晶。在本申请的一些实施例中,所述锂盐为libob、litfsi、lipf6、libf4、liasf6中的一种或多种。在本申请的一些实施例中,所述锂盐为二草酸硼酸锂(libob),所述libob的优势是具有更好的温度稳定性,且对石墨电极稳定,可以提高锂负极的循环稳定性,并且价格便宜,环境友好。在本申请的一些实施例中,所述聚合物为peo、pan、pmma、ppo和pvdf改性结构中的一种或多种。在本申请的一些实施例中,所述聚合物为聚环氧乙烷(peo),所述peo分子链具有相对较高的介电常数,分子链中的氧原子存在两对孤对电子,拥有很强的配位能力,可以溶解众多锂盐,且有一定的电导率。在本申请的一些实施例中,所述锂盐为libob,所述聚合物为peo,所述libob与所述peo络合制得的电解质在30℃时的电导率可以达到10-5s/cm。在本申请的一些实施例中,所述无机固态电解质为llzto、li1+xalxti2-x(po4)3、li7la3zr2o12、la2/3-yli3ytio、li1+zalzge2-z(po4)3、li4-age1-apas4、li2s-b2s3-p2s5、li2s-sis2、li2s-p2s5、li2s·sis2·li3po4、li2s·sis2·li3sio4中的一种或多种,其中,所述x为0-2之间;所述y为0-3之间;所述z为0-2之间;所述a为0-1之间。在本申请的一些实施例中,所述无机固态电解质为li6.4la3zr1.4ta0.6o12(llzto)。所述llzto有着高的热稳定、化学稳定性以及锂离子电导率。在本申请的一些实施例中,所述llzto可以对所述peo进行改性,提高所述peo的导电性能。所述llzto可以打乱所述peo链的排列秩序或形成枝化结构来阻止peo结晶,使得含peo结构单元的基团为侧链嫁接在其它聚合物链上形成梳形聚合物,通过改性来提高界面的附着力(正负极与固态电解质之间)以及兼容性,提高锂离子的迁移能力。在本申请的一些实施例中,所述锂盐和所述聚合物的质量比为(1∶3)-(1∶2)。具体地可以根据不同种类的锂盐以及聚合物来选择合适的质量比。在本申请的一些实施例中,所述无机固态电解质的质量占比为40-65%,例如40%,45%,50%,55%,60%,65%等。所述无机固态电解质为主要成分,其质量占比最多,可以根据需要确定其具体质量占比。在本申请的一些实施例中,所述自修复材料的质量占比为10-20%,例如10%,12%,14%,16%,18%,20%等。所述自修复材料不能太少,否则降低所述界面电阻的能力不够;所述自修复材料不能太多,否则挤占了无机固态电解质的质量占比,影响电解质性能。在本申请的一些实施例中,所述自修复材料涂敷于所述电解质与电极相连的表面。在本申请的一些实施例中,所述自修复材料均匀混合与所述电解质中。本申请提供的复合聚合物固态电解质,利用无机锂盐、无机固态电解质和聚合物电解质自身的优点,再加入包含氢键的自修复材料,利用所述氢键的作用力来提高界面作用力,既提高了界面接触附着力和兼容性,又降低了界面电阻,同时也优化了固态电解质内部结构。本申请的实施例还提供一种复合聚合物固态电解质的制备方法,包括:制备无机固态电解质;通过热压方法将所述无机固态电解质、聚合物以及锂盐混合制成聚合物固态电解质;将自修复材料涂敷于所述聚合物固态电解质与正、负电极相连的表面,所述自修复材料选自如结构式(1)所示的化合物中的至少一种:其中,所述n为2,3,4,5或6,所述m为2,3,4,5或6;所述结构中的双键上的氢可以被氨基、巯基、脲基、羟基、f-或cl-取代;所述结构中的甲基上的氢可以被氨基、巯基、脲基、羟基、羧基、羰基、c1-5烷基、c2-6烯基和卤素取代。通过热压法制备所述复合聚合物固态电解质,所述制备过程无需使用有机溶剂,污染小。在本申请的一些实施例中,制备所述无机固态电解质的方法包括:将无机固态电解质材料在800℃-1000℃煅烧3-12小时后制成粉体。具体地以llzto为例,使用传统的固相法合成,按照llzto,即li6.4la3zr1.4ta0.6o12的化学计量比配比,首先将前驱粉体研磨6小时,然后在900℃温度条件下煅烧12小时,再次研磨6小时;将粉体压实成所需要的形状,然后进行高温煅烧;再通过热压方法将其制备成薄膜,之后放入70℃真空箱烘干12小时。在本申请的一些实施例中,所述热压方法的压力为8-12mpa,例如8mpa,10mpa,12mpa等。采用热压法制备所述无机固态电解质,所述制备过程无需使用有机溶剂,污染小;电解质颗粒直径小于常规方法中的电解质颗粒,提高界面接触点,降低颗粒内间隙;同时也提高了电解质密度,降低接触电阻以及晶界电阻,有利于锂离子传输。图1为本申请的一些实施例中所述复合聚合物固态电解质的结构示意图。参考图1,所述复合聚合物固态电解质100包括聚合物固态电解质110以及自修复材料120。其中,所述聚合物固态电解质110是通过热压方法将所述无机固态电解质、聚合物以及锂盐混合制成,所述自修复材料120涂敷于所述聚合物固态电解质110与电极相连的面上。本申请提供的复合聚合物固态电解质的制备方法,利用无机锂盐、无机固态电解质和聚合物电解质自身的优点,再加入包含氢键的自修复材料,利用所述氢键的作用力来提高界面作用力,既提高了界面接触附着力和兼容性,又降低了界面电阻,同时也优化了固态电解质内部结构。本申请的另一些实施例中还提供了一种复合聚合物固态电解质的制备方法,包括:制备无机固态电解质;通过热压方法将所述固态电解质、聚合物、锂盐以及自修复材料均匀混合制成复合聚合物固态电解质,所述自修复材料选自如结构式(1)所示的化合物中的至少一种:其中,所述n为2,3,4,5或6,所述m为2,3,4,5或6;所述结构中的双键上的氢可以被氨基、巯基、脲基、羟基、f-或cl-取代;所述结构中的甲基上的氢可以被氨基、巯基、脲基、羟基、羧基、羰基、c1-5烷基、c2-6烯基和卤素取代。通过热压法制备所述复合聚合物固态电解质,所述制备过程无需使用有机溶剂,污染小。在本申请的一些实施例中,制备所述无机固态电解质的方法包括:将无机固态电解质材料在800℃-1000℃煅烧3-12小时后制成粉体。具体地以llzto为例,使用传统的固相法合成,按照llzto,即li6.4la3zr1.4ta0.6o12的化学计量比配比,首先将前驱粉体研磨6小时,然后在900℃温度条件下煅烧12小时,再次研磨6小时;将粉体压实成所需要的形状,然后进行高温煅烧;再通过热压方法将其制备成薄膜,之后放入70℃真空箱烘干12小时。在本申请的一些实施例中,所述热压方法的压力为8-12mpa,例如8mpa,10mpa,12mpa等。采用热压法制备所述无机固态电解质,所述制备过程无需使用有机溶剂,污染小;电解质颗粒直径小于常规方法中的电解质颗粒,提高界面接触点,降低颗粒内间隙;同时也提高了电解质密度,降低接触电阻以及晶界电阻,有利于锂离子传输。图2为本申请的另一些实施例中所述复合聚合物固态电解质的结构示意图。参考图2,所述复合聚合物固态电解质100包括锂盐,无机固态电解质,聚合物以及自修复材料120。其中,与图1所示结构不同的是,所述自修复材料120不是涂敷与所述聚合物固态电解质110与正、负电极相连的面上,而是与锂盐,聚合物,无机固态电解质均匀混合在一起。本申请提供的复合聚合物固态电解质的制备方法,利用无机锂盐、无机固态电解质和聚合物电解质自身的优点,再加入包含氢键的自修复材料,利用所述氢键的作用力来提高界面作用力,既提高了界面接触附着力和兼容性,又降低了界面电阻,同时也优化了固态电解质内部结构。本申请的实施例还提供一种锂电池,包括正极、负极和以上所述的复合聚合物固态电解质。在本申请的一些实施例中,所述正极包括正极活性物质,所述正极活性物质为磷酸铁锂、licoo2、lifebmncpo4、linio2、linibmnco4、镍钴锰三元材料或富锂锰基中的一种或多种,其中所述b为0-1之间,c为0-1之间。在本申请的一些实施例中,所述负极为金属锂。在本申请的一些实施例中,制备所述锂电池的方法包括:在氩气手套箱里将自修复材料分别涂敷在带有活性物质的正极集流体和负极锂金属片上;在氩气手套箱里按照正极、固态电解质和负极结构形式进行组装,放入电池壳体,最终获得锂电池。在本申请的一些实施例中,涂敷与所述正极集流体和负极锂金属上的自修复材料的厚度为8-12微米,例如8微米,10微米,12微米等。在本申请的一些实施例中,所述电池壳体为不锈钢壳体。图3为本申请的一些实施例中所述锂电池的结构示意图。参考图3所示,所述锂电池包括正极130,复合聚合物固态电解质以及负极140。其中,所述复合聚合物固态电解质包括聚合物固态电解质110以及涂敷于所述聚合物固态电解质110与正极130和负极140相连的面上的自修复材料120。图4为本申请的另一些实施例中所述锂电池的结构示意图。参考图4所示,所述锂电池包括正极130,复合聚合物固态电解质以及负极140。其中,所述复合聚合物固态电解质包括自修复材料120,所述自修复材料120均匀混合于所述复合聚合物固态电解质中。本申请提供的锂电池,包括复合聚合物固态电解质,利用无机锂盐、无机固态电解质和聚合物电解质自身的优点,再加入包含氢键的自修复材料,利用所述氢键的作用力来提高界面作用力,既提高了界面接触附着力和兼容性,又降低了界面电阻,同时也优化了固态电解质内部结构。示例性实施例1将lioh·h2o预先在200℃烘干12h到完全脱水,然后按照化学计量比(li6.4la3zr1.4ta0.6o12)将lioh(过量10wt%)、la(oh)3、zro2和ta2o5混合后研磨3h,将该混合物在900℃煅烧6h,再次研磨3h制成lltzo粉体;通过热压方法将peo、llzto和libob混合制成所述聚合物固态电解质;将自修复材料分别涂敷在所述电解质与电极相连的面上。示例性实施例2按照化学计量比(li6.4la3zr1.4ta0.6o12)将lico3,la(oh)3,zro2和ta2o5混合后研磨3h,将该混合物在900℃煅烧6h,再次研磨3h制成lltzo粉体;通过热压方法将peo、llzto和libob混合制成所述聚合物固态电解质;将自修复材料分别涂敷在所述电解质与电极相连的面上。示例性实施例3按照化学计量比(li6.4la3zr1.4ta0.6o12)将lico3,la(oh)3,zro2和ta2o5完全混合在异丙醇里8h,通过加入过量(10wt%)的锂盐抵补高温过程锂的损失,将所述混合浆料在900℃煅烧6h;煅烧后的粉体采用行星式球磨机在异丙醇中研磨12h后干燥;通过热压方法将peo、llzto和libob混合制成所述聚合物固态电解质;将自修复材料分别涂敷在所述电解质与电极相连的面上。示例性实施例4按照化学计量比(li6.4la3zr1.4ta0.6o12)将lioh·h2o(使用前在200℃烘干12h到完全脱水)、la2o3(使用前在900℃煅烧10h)、zro2和ta2o5完全混合在异丙醇中8h,加入过量(10wt%)的锂盐抵补高温过程锂的损失,将所述混合浆料在900℃煅烧6h;煅烧后的粉体采用行星式球磨机在异丙醇中研磨12h后干燥;通过热压方法将peo、llzto和libob混合制成所述聚合物固态电解质;将自修复材料分别涂敷在所述电解质与电极相连的面上。示例性实施例5将lioh·h2o预先在200℃烘干12h到完全脱水,然后按照化学计量比(li6.4la3zr1.4ta0.6o12)将lioh(过量1owt%)、la(oh)3、zro2和ta2o5混合后研磨3h,将该混合物在900℃煅烧6h;再次研磨3h制成lltzo粉体;将peo、llzto和libob与自修复材料均匀混合,最后在热压法条件下压实成为复合聚合物固态电解质。示例性实施例6按照化学计量比(li6.4la3zr1.4ta0.6o12)将lico3,la(oh)3,zro2和ta2o5混合后研磨3h,将该混合物在900℃煅烧6h;煅烧后的粉体再次研磨2h,然后和自修复材均匀混合;通过热压法(10mpa)将peo、llzto、libob和自修复材料制成复合聚合物固态电解质。示例性实施例7按照化学计量比(li6.4la3zr1.4ta0.6o12)将lico3,la(oh)3,zro2和ta2o5完全混合在异丙醇中8h,加入过量(10wt%)的锂盐抵补高温过程锂的损失,将混合浆料在900℃煅烧6h;煅烧后的粉体采用行星式球磨机在异丙醇中研磨12h,之后干燥;将peo、llzto和libob与自修复材均匀混合,最后通过热压方法制成复合聚合物固态电解质。示例性实施例8按照化学计量比(li6.4la3zr1.4ta0.6o12)将lioh·h2o、la2o3(使用前在900℃煅烧10h)、zro2和ta2o5完全混合在异丙醇中8h,加入过量(10wt%)的锂盐抵补高温过程锂的损失,将混合浆料在900℃煅烧6h;煅烧后的粉体采用行星式球磨机在异丙醇中研磨12h,之后干燥;将peo、llzto和libob与自修复材均匀混合,最后通过热压方法制成复合聚合物固态电解质。图5为本申请的不同实施例中所述复合聚合物固态电解质的电导率对比图。其中实例a是不添加自修复材料条件下制备的聚合物电解质(制备方法同实例2)。参考图5,可以发现不同实施例中使用的材料以及合成方法不同,电解质的电导率也不相同,经添加自修复材料后固态电解质的电导率有所提高,其中实施例5为最高。发明人还对比了不同电解质的锂电池的性能。所述锂电池的正极包括磷酸铁锂,superp和pvdf,质量比例为90∶5∶5,金属锂为负极,电解质为本申请的不同实施例,将所述正极,负极和电解质组装成扣式电池。经测试,在25℃条件下,所述锂电池电池在0.1c和0.5c下的最大放电容量如表1所示:表1倍率实施例1实施例2实施例5实施例60.2c(mah/g)1401361511450.5c(mah/g)98959493参考表1所示,实施例1和实施例2为将自修复材料涂敷于聚合物固态电解质上的方式;实施例5和实施例6为将自修复材料与聚合物,锂盐以及固态电解质均匀混合的方式。数据表明涂敷法以及均匀混合法所制备的固态电解质以及组装的锂电池的性能差别不大。综上所述,在阅读本详细公开内容之后,本领域技术人员可以明白,前述详细公开内容可以仅以示例的方式呈现,并且可以不是限制性的。尽管这里没有明确说明,本领域技术人员可以理解本申请意图囊括对实施例的各种合理改变,改进和修改。这些改变,改进和修改旨在由本公开提出,并且在本公开的示例性实施例的精神和范围内。应当理解,本实施例使用的术语″和/或″包括相关联的列出项目中的一个或多个的任意或全部组合。应当理解,当一个元件被称作″连接″或″耦接″至另一个元件时,其可以直接地连接或耦接至另一个元件,或者也可以存在中间元件。还应当理解,术语″包含″、″包含着″、″包括″和/或″包括着″,在此使用时,指明存在所记载的特征、整体、步骤、操作、元件和/或组件,但并不排除存在或附加一个或多个其他特征、整体、步骤、操作、元件、组件和/或它们的组。还应当理解,尽管术语第一、第二、第三等可以在此用于描述各种元件,但是这些元件不应当被这些术语所限制。这些术语仅用于将一个元件与另一个元件区分开。因此,在没有脱离本发明的教导的情况下,在一些实施例中的第一元件在其他实施例中可以被称为第二元件。相同的参考标号或相同的参考标志符在整个说明书中表示相同的元件。此外,通过参考作为理想化的示例性图示的截面图示和/或平面图示来描述示例性实施例。因此,由于例如制造技术和/或容差导致的与图示的形状的不同是可预见的。因此,不应当将示例性实施例解释为限于在此所示出的区域的形状,而是应当包括由例如制造所导致的形状中的偏差。例如,被示出为矩形的蚀刻区域通常会具有圆形的或弯曲的特征。因此,在图中示出的区域实质上是示意性的,其形状不是为了示出器件的区域的实际形状也不是为了限制示例性实施例的范围。当前第1页1 2 3