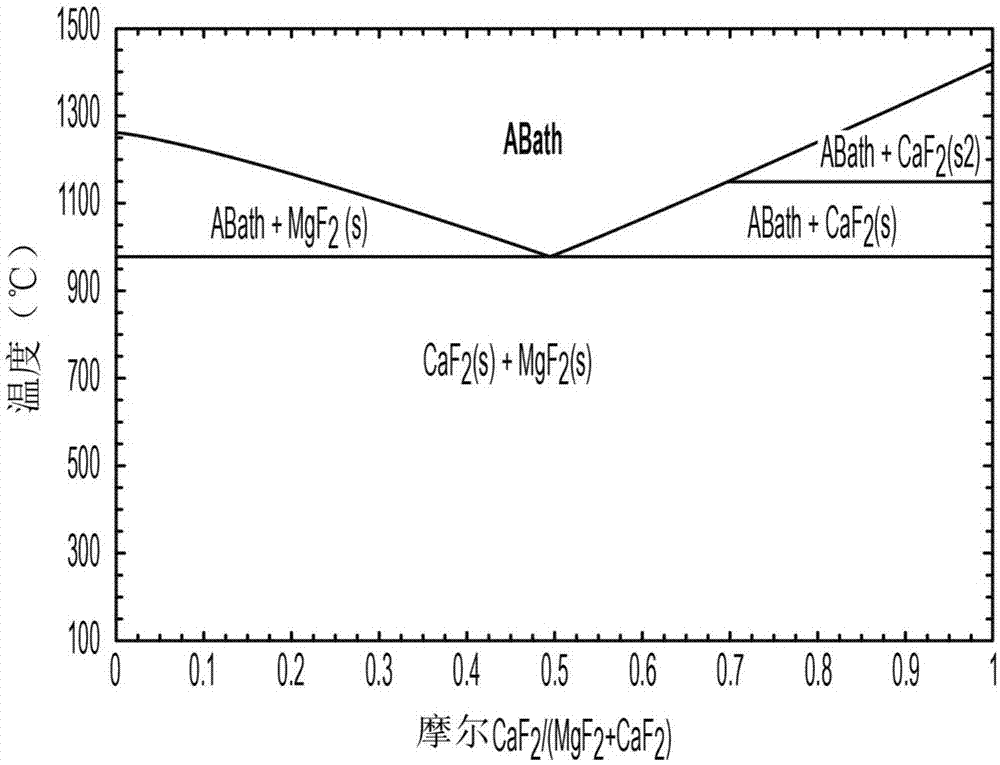
本公开涉及分段式磁体,例如,内部分段式钕磁体。
背景技术:
:电动车辆中通常可以使用永磁马达。由于烧结nd-fe-b磁体的高电导率和槽/齿谐波,所以会在磁体内产生涡流损耗。这会增大磁体温度并可能劣化永磁体的性能,可能会导致马达效率相应的减小。为试图解决这些问题并使磁体在提高的温度下工作,可以在马达中使用高矫顽力磁体。这些磁体通常包括诸如tb和dy的昂贵的重稀土(hre)元素。减少涡流损耗可以改善马达效率,并且材料成本可以被降低。为减小涡流损耗,磁体的电阻率必须增加。通常有两种方法来提高电阻率。第一种方法是通过将高电阻率的材料混合到磁体中来增加磁体的整体电阻率。然而,这通常导致磁性性能的劣化。第二种方法是通过将nd-fe-b磁体分隔成薄片并且绝缘材料位于其间来对磁体进行分段。这样的磁体通常通过利用聚合物粘合分片的磁体来制备。这样的磁体分段工艺包括各种制造步骤并增加磁体的制造成本。技术实现要素:在至少一个实施例中,提供了一种内部分段式磁体。磁体可以包括:第一层,包括永磁材料;第二层,包括永磁材料;绝缘层,使第一层和第二层分开,并且包括陶瓷混合物,所述陶瓷混合物至少包括第一陶瓷材料和第二陶瓷材料,所述陶瓷混合物具有达到1100℃的熔点。在一个实施例中,第一陶瓷材料或第二陶瓷材料可以包括具有化学式为ah2的化合物,其中,a为碱土金属,h为卤素。卤素可以包括氟或氯,碱土金属可以从由镁(mg)、钙(ca)和锶(sr)组成的组中选择。在另一实施例中,第一陶瓷材料或第二陶瓷材料可以包括具有化学式为mh3的化合物,其中,m是具有+3价氧化态的金属,h为卤素。在另一实施例中,第一陶瓷材料或第二陶瓷材料可以包括具有化学式为bh的化合物,其中,b为碱金属,h为卤素。陶瓷混合物可以具有比第一陶瓷材料和第二陶瓷材料中的每个的熔点低的熔点。绝缘层还可以包括金属或金属合金。金属或金属合金可以包括铁、铝、铜、稀土金属或它们的合金。在一个实施例中,金属包括小于绝缘层的20wt%。在至少一个实施例中,提供了一种形成内部分段式磁体的方法。所述方法可以包括:形成包括粉末状永磁材料的第一层;在第一层上方沉积包括陶瓷混合物的绝缘层,所述陶瓷混合物至少包括第一陶瓷材料和第二陶瓷材料;在绝缘层上方沉积包括粉末状永磁材料的第二层,以形成内部分段的磁体堆叠;烧结磁体堆叠。在一个实施例中,第一陶瓷材料和第二陶瓷材料可以从由下列化合物组成的组中选择:具有化学式为ah2的化合物,其中,a为碱土金属,h为卤素;具有化学式为mh3的化合物,其中,m是具有+3价氧化态的金属,h为卤素;具有化学式为bh的化合物,其中,b为碱金属,h为卤素。陶瓷混合物可以具有比第一陶瓷材料和第二陶瓷材料中的每个的熔点低的熔点。绝缘层还可以包括金属或金属合金。金属或金属合金可以包括铁、铝、铜、稀有金属或它们的合金,金属可以包括小于陶瓷混合物的20wt%。绝缘层还可以包括具有30℃至400℃的低熔点(lmp)材料。lmp材料可以具有比烧结步骤的烧结温度低的沸点。在第一沉积步骤之前,可以将绝缘层压成片。可以在比lmp材料的熔点高且比lmp材料的沸点低的温度下将绝缘层压成片。所述方法也可以包括在烧结步骤之前执行热压步骤,其中,热压步骤包括将磁体堆叠加热到lmp材料的熔点以下的温度。在至少一个实施例中,可以提供一种内部分段式磁体生坯。生坯可以包括:第一层,包括粉末状永磁材料;第二层,包括粉末状永磁材料;绝缘片,使第一层和第二层分开,并且包括陶瓷混合物和具有30℃至400℃的熔点的低熔点(lmp)材料,所述陶瓷混合物至少包括第一陶瓷材料和第二陶瓷材料。附图说明图1是根据实施例的内部分段式磁体的示意性剖视图;图2是包括caf2和mgf2的混合物的共晶反应的二元相图的示例;图3是对比caf2绝缘层和包括caf2和mgf2的混合物的绝缘层的sem图像;图4是根据实施例的形成内部分段式磁体的方法的示意图;以及图5是根据实施例形成的内部分段式磁体的图像。具体实施方式按照要求,在这里公开了本发明的详细实施例;然而,将理解的是,所公开的实施例仅是可以以各种可替换形式实施的本发明的举例说明。附图不一定按比例绘出;一些特征可以被夸大或最小化以示出具体组件的细节。因此,在这里所公开的特定结构性和功能性细节不被解释为限制性的,而是仅作为教导本领域技术人员各种各样地应用本发明的代表性基础。为减少工艺成本,已经开发出分段磁体的可选方法,这可被称为内部分段技术。在这种技术中,可以在烧结期间通过将绝缘层置入生坯来使磁体分段。可以选择绝缘材料以使它们不劣化磁性性能,因此,绝缘层不与硬磁相反应。然而,已经发现,内部分段式磁体的机械性能很差,具体地说在绝缘层厚且均匀以使硬磁相完全绝缘时。因此,内部分段式磁体已经被形成为具有很薄的绝缘层,其中,绝缘层太薄而不连续,这由于绝缘不充分导致电阻率的增大十分有限。例如,绝缘层相比于磁性相仅会提供电阻率2倍至3倍的增大。为了充分地使磁性材料绝缘,电阻率必须很高,诸如高出磁性材料自身的数千倍、数百万倍或数十亿倍。公开的内部分段式磁体及其形成方法可以增强/增加内部分段式磁体的机械性能。为了改善机械性能,考虑到这种材料的异构本质,需要增加“粘合力”和“内聚力”两者。前者,粘合力可以指磁体和绝缘层(il)之间的界面附近的相互作用。后者,内聚力可以反映形成il的绝缘材料的机械性能。在夹层磁体-il-磁体结构中,粘合力可以是绝缘材料和磁性材料(例如,nd-fe-b)之间的相互作用,而内聚力可以依赖于绝缘层自身的机械性能。用于内部分段式磁体的绝缘材料可以是陶瓷,可以不与磁体的主要相反应,因此不劣化磁性性能。然而,这种相互作用的缺乏会意味着没有形成绝缘层和nd-fe-b之间的化学键。因此,粘合力可以包括这两种材料之间的相对弱的静电相互作用,也被称作范德华力。已经发现,如果绝缘材料在烧结期间被熔化,则可以改善机械性能。这被认为这种改善是由于绝缘材料薄地分散并且很好地润湿磁体的表面,从而改善粘合力。参照图1,在截面图中示出了内部分段式磁体10。磁体10可以具有多层磁性层12以及一层或更多层绝缘层(il)14。绝缘层14可以设置在磁性层12之间以增大磁体10的电阻并减少涡流损耗。绝缘层14可以与两层分隔开的并相对的磁性层12直接接触。磁性层12和/或绝缘层14可以具有均匀或基本上均匀的厚度(例如,在平均厚度的5%内)。可以有多层绝缘层14,例如,一层绝缘层14位于每对相邻的磁性层12之间。在一个实施例中,如果有“x”层磁性层12,那么可以有“x-1”层绝缘层14。在图1中示出的示例中,有四层磁性层12和三层绝缘层14,然而,可以有任意适合的每种层的数量。磁体可以包括至少两层磁性层12,使得它们被绝缘层14分开。但是,可以有3、4、5、10或更多的磁性层12,其可以包括设置在每对磁性层12之间的相应的2、3、4、9或更多的绝缘层14。在至少一个实施例中,绝缘层14可以是相对薄的。例如,绝缘层14可以具有1μm至1000μm的厚度(例如平均厚度),或其中的任意子范围。在一个实施例中,绝缘层14可以具有5μm至500μm、5μm至300μm、5μm至200μm、5μm至150μm、5μm至100μm、5μm至50μm、5μm至25μm、10μm至500μm、10μm至250μm、10μm至150μm、25μm至250μm、25μm至150μm、50μm至250μm、100μm至250μm或150μm至250μm的厚度。然而,在这些范围之外的厚度也是可能的。在一个实施例中,该厚度可以足够厚以提供电阻材料的连续层而与磁性层12的表面粗糙度无关。磁性层12可以由任意适合的硬磁或永磁材料形成。在一个实施例中,磁性材料可以包括诸如钕或钐的稀土(re)元素。例如,磁性材料可以是钕-铁-硼(nd-fe-b)磁体或钐-钴(sm-co)磁体。特定的磁性材料组分可以包括nd2fe14b或smco5,然而,将理解的是,也可以使用这些组分或其它永磁体组分的变型。其它材料和/或元素也可以被包括在磁性材料中以改善磁体的性能(例如,诸如矫顽力的磁性性能),例如,诸如y、tb、dy、ho、er、tm、yb和lu的重稀土元素。绝缘层14可以由比磁性层12的电阻大的任意适合的材料来形成。在一个实施例中,绝缘层14可以包括陶瓷材料。已经测试的材料的一个示例为氟化钙(caf2)。然而,已经发现caf2的绝缘层必须相对地厚以提供适当的电阻率。但是,厚的caf2层是脆的,并导致磁体具有差的机械性能。已经发现,可以在绝缘层中使用陶瓷材料的混合物,这可以获得比成分陶瓷低的熔点。这些混合物可以利用共晶反应。虽然陶瓷倾向于具有高的熔点,但是陶瓷之间的共晶反应可以显著地降低陶瓷混合物的熔点。即使系统的混合物的整体组分不在共晶点处或共晶点附近,在混合物的颗粒的表面处,也可以显著地降低熔点。对于陶瓷的致密化过程,形成液相可以提高致密率,因此增加绝缘层的内聚力。在液相烧结中,在液态中存在于颗粒间间隙中的空隙产生的毛细作用力的辅助下,通过连续的液态晶界薄膜,材料传输快得多。此外,在烧结期间增加液相的体积也可以改善磁体和绝缘层之间的相互作用。在一个实施例中,绝缘层可以包括包含碱土金属和卤素的化合物的混合物(例如,两种或更多种)。这些化合物可以具有ah2的化学式,其中,a为碱土金属,h为卤素。碱土金属可以包括铍(be)、镁(mg)、钙(ca)、锶(sr)、钡(ba)和镭(ra)。卤素可以包括氟(f)、氯(cl)、溴(br)、碘(i)和砹(at)。在至少一个实施例中,碱土金属可以是钙和/或镁。在至少一个实施例中,卤素可以是氟(f)或氯(cl)。混合物可以由两个或更多个上述的任意组合来形成。例如,混合物可以包括mgf2和caf2。图2中示出了示出mgf2和caf2的混合物的相图。这个系统的共晶温度为约980℃,这比任意一个单独的熔点1410℃(caf2)和1252℃(mgf2)低得多。除了碱土金属和卤素的化合物之外,混合物可以包括包含碱金属和卤素的一种或更多种化合物。碱金属可以包括锂(li)、钠(na)、钾(k)、铷(rb)或铯(cs)。因此,混合物可以包括诸如lif、naf、kf、licl、nacl、kcl的化合物或任意其它组合。这些化合物可以具有bh化学式,其中,b为碱金属,h为卤素。混合物也可以包括一种或更多种其它金属(诸如,过渡金属或基本金属)和卤素的化合物。这些化合物可以具有mh3化学式,其中,m为是具有+3价氧化态的金属,h为卤素。例如,金属可以包括铝(al)、锆(zr)、钛或其它。化合物可以包括alf3、alcl3、zrf4、zrcl4或其它。上述化合物可以以任意组合混合以形成二元、三元、四元系统或更多元系统(例如,具有2、3、4或更多化合物的系统)。系统可以包括诸如mgf2和caf2二元系统或lif-naf-kf三元系统的所有的一种类型的化合物(例如,具有所有的碱土金属-卤素或所有的碱金属-卤素化合物的二元或三元系统)。或者,系统还可以包括至少两种类型的化合物,例如,具有碱土金属-卤素和碱金属-卤素化合物的二元系统或者具有碱土金属-卤素和碱金属-卤素化合物中的两种以及其它化合物中的一种的三元系统。类似地,金属-卤素化合物可包括在上述的任意的系统中。这些二元、三元、四元或更多元系统可以是共晶系统。用于绝缘材料混合物的整体组分可以处于共晶点或在共晶点附近,从而与成分组分相比,减小了混合物的熔点。例如,组分可以在共晶点的诸如5%、10%、15%、20%、25%或30%的特定的摩尔比内。这是诸如mgf2和caf2的二元系统的最简单的描述。该系统的共晶点为大约50mol%的caf2和50mol%的mgf2,因此,对于在共晶点的20%内的组分,该组分可以是30mol%至70mol%的caf2和30mol%至70mol%的mgf2。如上所述,即使混合物的组分不是共晶组分,在颗粒或粉末的表面处也仍可以以低于熔点的温度熔化。因此,即使相对少量的第二化合物或附加化合物也可以改善烧结。因此,组分可以包括至少5摩尔%的第二化合物或附加化合物,例如,至少10摩尔%、15摩尔%、20摩尔%或25摩尔%。第二化合物或附加化合物可以是二元系统中的任意一种化合物。例如,如果在mgf2和caf2系统中存在20摩尔%的第二化合物,那么组分可以是20摩尔%的mgf2或20摩尔%的caf2。同样可以适用于其它二元系统或者适用于三元或四元系统。换言之,用于绝缘材料混合物的整体组分可以处于共晶点或在共晶点附近,从而混合物的熔点处于共晶点温度或在共晶点温度附近。例如,可以配置组分使得熔点在共晶点温度的特定温度内,诸如,5℃、10℃、25℃、50℃、75℃或100℃内。因此,如果组分被配置为具有在mgf2和caf2的混合物的共晶点温度(共晶点为980℃)的50℃内的熔点,那么组分可以具有930℃至1030℃的熔点。然而,因为共晶点通常表示最小熔点(或至少局部最小值),所以组分可以具有共晶点温度(980℃)至1030℃的熔点。根据用于绝缘层的混合物的组分,熔点可以不同。可以配置绝缘材料混合物的组分使得熔点可以小于或等于1100℃、1050℃或1000℃,例如,850℃至1100℃、850℃至1000℃、900℃至1050℃、950℃至1100℃或者950℃至1000℃。混合物的熔点可以小于磁性材料的烧结温度。在一个实施例中,磁性材料的烧结温度可以是1000℃至1100℃,例如,1025℃至1075℃或约1060℃。如上所述,即使混合物的组分不是共晶组分(例如,对于mgf2和caf2摩尔比约1:1),在颗粒或粉末的表面处也仍可以熔化,从而改善在烧结期间的材料传输和致密化。通过减小绝缘层材料的熔化温度,可以改善绝缘层的内聚力。增加的内聚力可以允许绝缘层变厚而不损害其机械性能。因此,内部分段式磁体可以是厚的,因此,对于磁体所需的电阻,绝缘层仍提供稳定和机械可靠的结构。例如,绝缘层可以具有至少106ωm、107ωm或108ωm的电阻率。图3中示出了具有caf2+mgf2绝缘层的内部分段式nd-fe-b磁体的示例。caf2和mgf2的混合物具有3:7的摩尔比并在1060℃下烧结4小时。当与仅通过caf2绝缘的磁体(左)比较时,可以从sem图像看到共晶反应的效果(右)。在包括caf2和mgf2的混合物的绝缘层中有明显的晶粒长大,这可以改善绝缘层和磁体的机械性能。相比之下,熔化温度远高于烧结温度的caf2颗粒不熔化、烧结或经历晶粒长大。因此,在左侧的绝缘层具有很低的内聚力且很脆。在另一实施例中,绝缘层可以包括包含碱土金属和卤素的一种或更多种化合物以及一种或更多种金属。前者的化合物可以具有ah2的化学式,其中,a为碱土金属,h为卤素。这些可以类似于如上描述的那些。通常,金属具有比陶瓷低的熔点。此外,一些金属可以改善磁性材料的磁性性能。然而,金属通常具有十分低的电阻,并且在绝缘层中包括它们会与绝缘层的目的相反。然而,已经发现金属材料和介电材料的混合物的电导率可以由逾渗理论来支配。因此,电导率可以通过控制混合物中的金属或合金粉末的量来调整。当金属组分的体积比小于阈值时,混合物的电导率可以接近零。当金属组分的体积比在阈值以上时,近似地,介电组分和金属组分的混合物的电导率可被表示为:σ~(p-pc)μ其中μ为临界指数,所述临界指数描述电导率与变化的金属材料和绝缘材料的体积比的行为,p可以看作金属组分的体积比,pc为指示金属相的长程连接的形成的阈值。因此,金属粉末可以与绝缘粉末混合通过增强界面反应来改善内部分段式磁体的机械性能。如果金属粉末的体积比低于阈值,那么绝缘层仍将是介电的。当与陶瓷绝缘材料和磁性材料对比时,可包括在混合物中的金属可以具有相对低的熔化温度。例如,金属可以具有小于磁性材料的烧结温度的熔点(例如,小于1060℃)。可与绝缘材料混合物混合的金属的示例可以包括铁、铝、铜、镓(ga)、钛(ti)、铟(in)、稀土金属(例如,铈(ce)、镝(dy)、铒(er)、铕(eu)、钆(gd)、钬(ho)、镧(la)、镥(lu)、钕(nd)、镨(pr)、钷(pm)、钐(sm)、钪(sc)、铽(tb)、铥(tm)、镱(yb)和钇(y))或其它。也可以使用上述材料的合金(彼此的合金或与其它元素的合金)。下面示出了若干示例的绝缘材料混合物的电阻率值的表格。混合物包括caf2和变化的量的铁。如所示,在15wt%和20wt%的铁之间的点处,存在从介电行为到可测量电阻的转换。从5wt%到15wt%,混合物表现为介电的,从20wt%到40wt%,混合物的电阻率迅速地减小。然而,在绝缘材料中包括多达约15wt%的金属可以减小整体绝缘材料的熔化温度(如上所述,这改善内聚力和界面接合),同时还改善磁性材料的磁性性能。可以在不牺牲绝缘层的电阻率的情况下实现这些改善。虽然已经利用单个ah2化合物描述混合物,但是还可以使用诸如上面所述的那些化合物的混合物。如前所述,化合物的混合物还可以降低绝缘层的熔化温度。材料电阻率(ω·cm)caf2+5wt%fen/acaf2+10wt%fen/acaf2+15wt%fen/acaf2+20wt%fe1.501×105caf2+30wt%fe1.46×103caf2+40wt%fe2.6×10-4在上述实施例中,可以在磁性层上以悬浮物或粉末施用或沉积绝缘层。例如,绝缘材料可以在悬浮物中,然后被喷洒到磁性层上。可选地,绝缘材料可以是粉末,所述粉末可以直接地施用或沉积到磁性层上。因此,在烧结前形成磁体结构可以包括:例如在模具或压模中铺设或沉积磁性粉末(例如,nd-fe-b粉末)的层;然后在磁性粉末上施用绝缘材料的层。可以重复这个工艺以形成未烧结的磁性材料和绝缘材料的交替层。在施用接下来的层之前,可以使所述层变结实或压紧所述层。可选地,所述层可以仅在施用每个磁性层之后被压紧。在一个实施例中,可以在非反应气氛(诸如,氩气或氮气)中或利用其它方法来免受氧化的情况下将磁性材料沉积到模具或压模中。一旦沉积了所有层,可以将磁体压成生坯并烧结。虽然上述绝缘层材料(例如,喷洒或粉末)的松散或非刚性的应用可以是有效的,但是使用用于绝缘层的片或其它预先形成的层可以更易控制层的厚度和均匀性。当将松散的绝缘材料施用到压紧的但未烧结的磁性层时,可能难以确保绝缘层的厚度均匀或者确保在绝缘层中没有间隙或裂缝。已经发现预先形成的绝缘层(例如,片)可以提供改善的绝缘层的厚度和均匀性的控制以及更易操作。然而,绝缘层可以由很脆且难于制备成很薄的层的陶瓷形成。此外,这些层在施压期间会易于损坏,这可能大大地降低电阻率。参照图4,示出了组装内部分段式磁体20的示意图。磁体20可以形成有磁性层22和绝缘层24,所述磁性层22可以与如上描述的磁性层(例如,nd-fe-b粉末)类似,所述绝缘层24可以预先形成绝缘片26。如所示,例如,可以在例如模具或压模中沉积第一磁性层22。然后可以压紧该磁性层22,并可以在磁性层22上或上方(例如,直接接触)施用或插入绝缘片26。由于绝缘片26被预先形成,所以它可以具有预定的厚度,所述预定的厚度可以是均匀的或基本上均匀的。在插入绝缘片26之后,可以在绝缘片26上或上方(例如,直接接触)沉积另一层磁性层22。可以与第一沉积层类似压紧这一磁性材料层,然而,一旦已经插入绝缘片26,在任意或全部施压期间可以施加热。如下面更详细地解释,增加的热可以防止或减少在烧结之前绝缘片26的破碎或开裂。可以将附加的磁性材料层和绝缘片以交替的顺序添加到压模或模具以形成最终内部分段的、未烧结的生坯。如上所述,由陶瓷形成的绝缘片通常是脆的且难以形成薄层。已经发现通过将绝缘材料与软的、低熔点(lmp)材料混合可以形成更具延展性的或韧性的绝缘片。lmp材料可以用作粘合剂或胶合剂以改善片的韧性,防止它们破碎/开裂,并提高其操作能力。在一个实施例中,lmp材料可以具有略高于室温(例如,高出25℃)的熔点。因此,lmp材料可以在制备和处理片时为固体,但可以在不增加大量热的情况下开始熔化。然而,可以在室温下执行工艺,因此,所述熔点可以小于室温。在一个实施例中,lmp材料可以具有0℃至500℃的熔点或其中的任意子范围。例如,lmp材料的熔点可以是10℃至450℃、20℃至400℃、25℃至400℃、30℃至400℃、30℃至350℃、30℃至300℃、30℃到250℃、30℃至200℃、30℃至150℃、30℃到100℃、35℃至90℃、40℃至90℃、45℃至85℃、45℃至80℃、50℃至80℃、55℃至80℃、55℃到75℃、60℃到75℃、60℃至70℃或约64℃(例如,±3℃)。在一个实施例中,lmp材料可以具有相对低的沸点,所述沸点可以小于磁性材料的烧结温度(例如,1060℃)。例如,lmp材料的沸点可以不高于500℃,诸如,小于或等于450℃、400℃、350℃、300℃、250℃、200℃,150℃、125℃或100℃。lmp材料的沸点可以是100℃至500℃,或其中的任意子范围,诸如,100℃至450℃、150℃至400℃、150℃至350℃、150℃至300℃、175℃至300℃、175℃至250℃、175℃至225℃或约200℃(例如±5℃)。lmp材料与绝缘材料混合物的比例可以是任意适合的量以将绝缘材料粘合并保持为片。在一个实施例中,lmp材料可以包括绝缘片的1wt%至50wt%或其中的任意子范围。例如,lmp材料可以包括1wt%至40wt%、5wt%至50wt%、5wt%至40wt%、10wt%至40wt%、10wt%至35wt%、15wt%至35wt%、20wt%至30wt%或约25wt%(例如,±5wt%)。当与绝缘材料(例如,粉末)混合时,胶状的lmp材料可以将粉末结合或粘合在一起。可以对lmp材料和绝缘材料加热并施压以形成片。可以将混合物加热到lmp材料的熔点以上但在lmp材料的沸点以下的温度。可以将混合物加热到熔点以上但在熔点的特定温度内的温度,诸如5℃、10℃、20℃或50℃内。例如,如果lmp材料的熔点为60℃,混合物将被加热到该熔点的20℃内,那么可以将混合物加热到60℃和80℃之间。lmp材料可以被交替地加热到上述温度然后与绝缘材料混合(例如,材料可以混合然后加热或者加热然后混合)。片可以针对特定磁体改变尺寸或可以稍大并在之后切割到适当尺寸。施压片可以增加绝缘材料的密度,因此,增加磁体的电阻率。在片已经被压和改变尺寸(如果需要)之后,可以将片插入到模具或压模中在已压紧的磁性层(例如,nd-fe-b粉末)的顶部上。可以在绝缘片的顶部上沉积磁性材料的另一层,然后压紧所述层。如参照图4所述,施压可以是“热”压。对包括一个或更多个绝缘片的未烧结磁体堆叠执行的任意施压可以是热压。热压的温度可以在lmp材料的熔点附近且在lmp材料的熔点以下。这可以软化绝缘片并使得片在热压操作期间具有增大的韧性。在一个实施例中,热压可以处于lmp材料的熔点的55%至99%的温度,或者其中任意子范围。例如,热压可以处于lmp材料的熔点的60%至99%、70%至99%、75%至99%、80%至99%、85%至99%或90%至99%的温度。换言之,可以在lmp材料的熔点的特定度数内且低于lmp材料的熔点的温度下执行热压。在一个实施例中,可以在lmp材料的熔点的100、75、50、40、30、20、10度内且低于lmp材料的熔点的温度下执行热压。在另一实施例中,热压可以处于在lmp材料的熔点以上的温度。一旦磁性粉末和绝缘片的交替层已经被压成最终生坯,可以烧结磁体。因此,可以在没有任何粘合剂或树脂(诸如,聚合物或环氧树脂)的情况下发生磁性层和绝缘层之间的结合。在一个实施例中,绝缘层可以仅由无机材料(例如,陶瓷)和金属构成。如上所述,烧结温度可以取决于磁性材料的组成。在一个实施例中,磁性材料的烧结温度可以是1000℃至1100℃,例如,1025℃至1075℃或约1060℃。然而,可以基于材料采用其它烧结温度。由于lmp材料可以具有烧结温度以下的沸点,所以lmp材料可以在烧结工艺期间蒸发。这可以留下绝缘材料后在磁性层之间形成高电阻层,从而减小涡流损耗。在一个实施例中,烧结温度可以慢慢地提高或者可以有低温和高温的两步烧结工艺。这可以防止lmp材料快速蒸发,可能使剩余的绝缘材料层不稳定。若相反,将lmp材料缓慢加热或最初加热到较低温度,则可以允许在绝缘层内重新排列绝缘材料,因此当lmp材料蒸发时更稳定。所述较低温度可以在lmp材料的沸点附近或在lmp材料的沸点以上,但在磁体的任意相的熔点以下。在预先形成的片的实施例中,绝缘材料可以是上述公开的任意材料或材料的混合物。例如,绝缘材料可以包括mgf2和caf2粉末的混合物或者ah2化合物和一种或更多种金属(例如,fe、al、cu、re)的混合物。胶状的lmp材料可以是具有公开的相对低的熔点和相对低的沸点的任意适合的材料。lmp材料可以是天然的或合成的蜡。可用的类型的蜡的示例可以包括动物蜡(如蜂蜡)、植物蜡(例如,巴西棕榈蜡)、矿物蜡(例如,泥煤蜡)、石油蜡(如石蜡)或合成蜡(例如,聚乙烯蜡)。lmp材料可以包括诸如热塑性塑料(例如以pe或pp为例的聚烯烃)的其它材料或者由诸如热塑性塑料(例如以pe或pp为例的聚烯烃)的其它材料形成。在一个示例中,图5中示出,磁体形成有被绝缘层片分隔的两层nd-fe-b磁性层。包括作为lmp材料具有64℃的熔点和200℃的闪点的蜂蜡的绝缘层,意味着蜂蜡在200℃下蒸发。可以通过将蜂蜡与以2:8的比例的caf2和mgf2的粉末的混合物(例如,约20摩尔%的caf2)混合来制备预先形成的片。lmp材料与绝缘材料(mgf2和caf2的混合物)的比例为1:3。然后将绝缘片混合物加热达到80℃并施压。层的厚度为约150μm。在第一压紧的nd-fe-b磁性粉末的段的顶部上放置绝缘片,然后在绝缘片的顶部上放置nd-fe-b粉末并施压。在30℃的温度下执行第二/最后施压。然后,生坯在200℃下烧结30分钟,然后在1060℃下烧结4小时。在图5中示出了根据上述步骤制备的烧结的磁体。公开的磁体可用于使用硬磁/永磁的任何磁性应用。所述磁体对于产生涡流的地方可以是有益的。在一个实施例中,所述磁体可以用于电动马达或发电机(诸如在混合或电动车辆中使用的电动马达或发电机)。公开的磁体及其形成方法可以减小磁体的温度,从而对于磁体需要低矫顽力。因此,需要较少的hre材料,这降低了电动马达的成本。也节省了能源,这可以增加mpg(英里/加仑)或者电动车辆的电动里程。内部分段式磁体和工艺还可以减少与外部分段式磁体相关的加工成本。虽然在上面描述了示例性实施例,但是这些实施例不意图描述本发明的所有可能形式。相反,在说明书中所使用的词语是描述性词语而非限制性词语,并且理解的是,在不违背本发明的精神和范围的情况下,可以做出各种改变。此外,可以结合各种实施实施例的特征以形成本发明的另外的实施例。当前第1页12