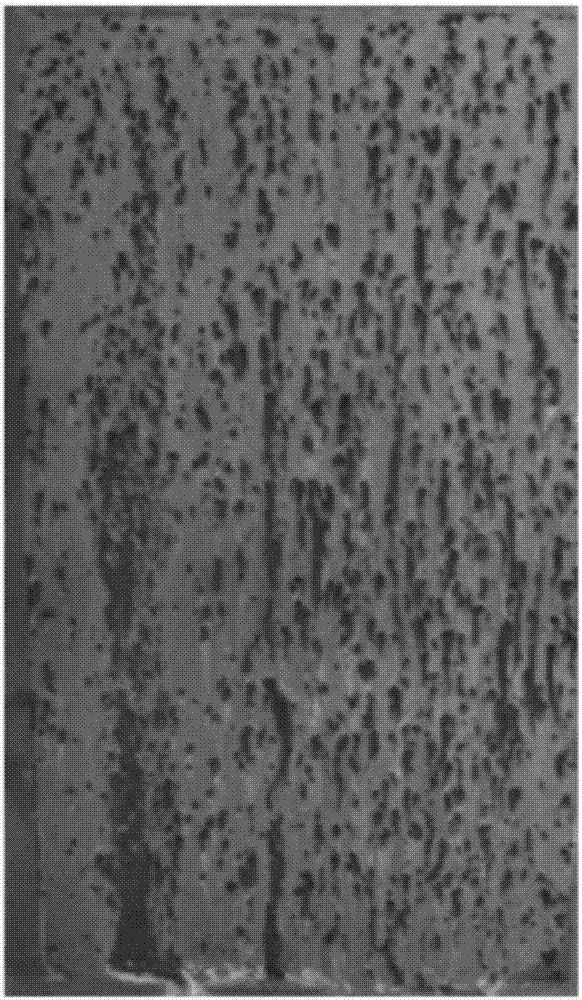
本发明涉及腐蚀控制
技术领域:
,尤其涉及在高温暴露期间和高温暴露后金属基底的腐蚀控制。更特别地,本发明涉及一种用于在金属基底上产生阴极高温腐蚀防护的涂层,更特别是高温腐蚀控制涂层。本发明还涉及一种用于生成阴极腐蚀控制层的第一涂层组合物和用于生成氧阻隔层的第二涂层组合物。此外,本发明涉及一种用于在金属基底上生成高温腐蚀控制涂层的方法。此外,本发明涉及一种包含腐蚀控制涂层的涂覆金属基底。此外,本发明涉及氧阻隔层在改善阴极腐蚀控制涂层的温度稳定性方面的应用。最后,本发明涉及涂层组合物在改善阴极腐蚀控制涂层的温度稳定性方面的应用。金属的腐蚀现象在所有工业领域都能普遍见到,并且具有重要的影响,因为机器、车辆、工业设备、甚至建筑的耐用性或使用寿命经常决定性地依赖于所用金属的耐腐蚀性能。腐蚀意味着金属部件必须更换或修复,这些操作总是耗费时间、材料和成本。根据dineniso8044,腐蚀是金属与其环境之间的物理化学相互作用,这导致了金属性质的改变并能导致对金属的功能、使用金属所处的环境或技术系统产生相当大的不利影响。金属腐蚀通常包括电化学过程,具体是任选在电解质水溶液存在下,金属被氧氧化,形成金属氧化物层。因为腐蚀过程通常决定了金属或金属组件的耐用性或使用寿命,因此有必要降低金属的易腐蚀性和腐蚀速率。保护金属免受腐蚀的一种方式是使用被动系统-涂层,例如保护性涂层-旨在保护金属免受环境影响以免腐蚀。另一种方式是使用主动系统,其中待保护的金属组件用作阴极-使用电化学过程-因此立即降低了金属的氧化或形成金属离子。该阴极腐蚀控制一方面通过施加外部电压获得,另一方面,也还能够使待保护的金属组件与一碱性金属,即具有低电化学标准电势的一种金属电接触。两种金属形成了电化学体系,其中碱性金属代表阳极,称为牺牲阳极,被氧化,同时更昂贵的金属为阴极,其上发生还原。阴极腐蚀控制的一种具体形式是用比待保护的金属碱性更强的金属涂覆待保护的金属部件。一种更普遍的涂覆金属形式,特别是涂覆钢板的形式是镀锌形式。利用镀锌,在称为热浸镀锌的工艺中,通过通常将钢,特别是钢板浸入到熔融锌的熔池涂覆元素锌,以形成热浸镀锌钢板-hdgs。镀锌的另一普遍可能性是电解镀锌或电镀锌,其中钢板或钢组件通过在包含锌离子的电解质池中施加外电压涂覆一层锌。上述两种方法都得到了均匀的,耐久的锌涂层,这能够显著延长金属组件的寿命,但在一定的使用条件下也具有一系列的弊端。在高强度钢的情况下,电镀过程中形成的氢是一个弊端,因为存在氢脆化的可能性。用于涂覆的复杂几何形状或块材也不能无缺陷的热浸镀锌,因为,如凹陷区域将会充满锌,或者精细结构表面形态将会堆积锌。此外,纯的元素锌涂层在温度负载下不具有令人满意的结果,这些不令人满意的结果一方面归因于锌的低熔点,约420℃,另一方面归因于即使在远低于熔点的温度,空气中的氧都加速锌氧化成氧化锌。为了至少避免一些热浸镀锌或电镀锌金属部件的弊端,实践中经常使用所谓的锌片涂层。锌片涂层在主要的无机粘合剂中包含有锌薄片,即片状的锌颜料。粘合剂和锌薄片的混合物通常以分散液的形式涂覆到待保护的金属部件上,粘合剂随后交联形成不能渗透的、均匀层,厚度为5-15μm。尽管锌颗粒嵌入粘合剂基底中,但锌片涂层具有导电性并保证了较高的阴极保护;特别地,在按照dineniso9227的带标记的盐雾试验中,锌片涂层相对于镀锌或电镀锌的金属部件具有显著改善的耐腐蚀性。锌片涂层通常由二氧化硅或二氧化钛的主要无机基质组成,其中嵌入有锌层。通常以相应涂层组合物形式应用至基底的锌片涂层,也被称为锌片底漆,如wo2007/130838a2中所述。在正常情况下,电镀锌、热浸镀锌获得涂层或者锌片涂层都具有高水平的耐腐蚀保护。然而在高温下,锌涂层,特别是锌片涂层提供的阴极腐蚀控制,即使在很短的高温暴露后,也会显著降低,甚至完全破坏。例如,用锌薄片底漆处理的钢板,在经受几小时的200℃高温暴露后,或者300℃的加速高温暴露,并随后经受根据dineniso9227的带标记的盐雾试验,也不再具有腐蚀控制或者至少不再具有足够的腐蚀控制,事实归因于锌氧化形成氧化锌,氧化锌并不会提供阴极保护。因此,在现有技术中,并不缺乏增加锌涂层温度稳定性的努力。在一些情况下,例如,使用包含极少量锰的锌合金涂层,以使得涂覆钢部件短暂加热到900℃温度进行随后的热成型操作,而不损伤阴极腐蚀控制。然而,极少量的锰的使用使该过程成本高。此外,此类阴极腐蚀控制仅能耐受短时间的温度负载。经过长时间后,在高温不能保持阴极腐蚀控制。含锌涂层的温度稳定性能够通过所谓的镀锌工艺获得,其中首先将第一锌层涂覆到钢基底上,通过随后的热处理,在基底表面上获得确定的铁-锌合金。相比于纯锌涂层,铁-锌合金对温度负载和对机械应力都不太敏感,但它们表面快速地呈现红锈,迫使在随后的涂覆中进行昂贵的和不方便的清洁。考虑到易发生红锈,镀锌钢基底的表面具有较低美观度,因此通常排除了在无其他涂覆的可视部分中的应用。镀锌涂层的另一缺点在于形成了铁-锌合金,从技术和能量的角度看,铁-锌合金在惰性气氛下以高成本且不便利的方式形成,高温下涂层也具有增加腐蚀的倾向,尽管比纯锌情况下少。de102012005806a1描述了一种两层的涂层体系,具有包含锌粒子的第一层,和所述层上方的包含铝粒子的第二层。两个层都包含环氧化物改性的烷氧基硅烷粘合剂。通过选择合适的催化剂,试图实现两个层的同时固化,因此推测产生了具有阴极腐蚀控制性能的良好附着力的涂层。然而,该涂层也仅能耐受约300℃的短期温度负载而无阴极腐蚀控制显著降低或破坏。因此在现有技术中,目前还缺少适当的主动腐蚀控制,特别是基于锌涂层的,即使在较长持续的温度负载和随后经受这样的温度负载也能维持阴极腐蚀控制效果。此类耐高温的腐蚀控制涂层将能够获得如在加热区域内的引擎、排气系统和螺旋系统、能量回收装置或工业设备中金属部件耐用性或使用寿命的显著增加。因此,本发明的目的在于提供一种高温腐蚀控制涂层,其中上述以及现有技术中存在的问题和弊端将至少大部分避免或者至少减少。本发明的另一目的在于提供一种在较长持续温度负载或间隔类温度负载下具有高水平腐蚀控制,更特别是阴极腐蚀控制的涂层。特别是要试图保证涂层还提供根据dineniso9227的带标记盐雾试验中随着高温暴露的良好结果。最后,本发明的又一目的在于提供一种涂层,该涂层可灵活地用于各种应用中,同时具有显著的高温腐蚀控制。根据本发明的第一方面,本发明的主题是根据权利要求1的一种用于产生阴极高温腐蚀保护的涂层,更特别是高温腐蚀控制涂层。本发明该方面的其他优选实施方式是相关从属权利要求的主题。根据本发明的第二方面,本发明的另一主题是用于生成阴极腐蚀控制涂层的涂层组合物。根据本发明的第三方面,本发明的又一主题是用于生成氧阻隔涂层的涂层组合物。此外,根据本发明的第四方面,本发明的又一主题是根据权利要求12,用于在金属基底上生成高温腐蚀控制涂层的方法。根据本发明的第五方面,本发明还提供了根据权利要求13,一种包含腐蚀控制涂层的涂覆基底。本发明的又一主题是根据权利要求14,氧阻隔涂层用于获得阴极腐蚀控制涂层的高温稳定性的用途。最后,本发明的又一主题是根据权利要求15,氧阻隔涂层组合物用于改善阴极腐蚀控制涂层温度稳定性的用途。容易理解的是,特性、特征、形式和实施方式,以及优点等仅在下文中就本发明的一个方面进行了阐述,为了避免不必要的重复,不言而喻也可用于本发明的其他方面,而无需明确说明。同样容易理解的是,下文说明的任何数值、数字和范围都不应该解释为限制各个数值、数字和范围的说明;本领域的技术人员可以理解,在特定情况下或对于特定应用,偏离所述范围和说明是可能的,都不脱离本发明的范围。此外,下文说明的任何数值/参数特定值等原则上可使用标准化的或明确说明的确定方法或者用本领域的技术人员熟悉的确定方法进行确定。此外,不言而喻的是,所有重量或质量百分比都将由本领域的技术人员选择共计为100%的方式,然而这是不言而喻的。接着上文,下面更详细地说明本发明。根据本发明的第一方面,本发明的主题因此是一种用于在金属基底上生成阴极高温腐蚀保护的涂层,特别是一种高温腐蚀控制涂层,具有至少两个层,其中所述涂层具有:(a)阴极腐蚀控制涂层形式的第一层和(b)另一腐蚀控制涂层形式,尤其是氧阻隔涂层形式的第二层。在本发明的上下文中,因此能够使用一种包含阴极腐蚀控制层和另一腐蚀控制层,尤其是氧阻隔层的涂层,来获得阴极高温腐蚀防护,由此不仅在高温暴露期间保护金属基底,此外,还随着温度暴露以及在重复温度暴露的情况下也不会失去其阴极保护效果。因此,本发明的涂层不仅在较长持续的温度暴露情况下具有阴极腐蚀控制,而且,在间断等温度暴露情况下也如此,例如发动机车辆的引擎所发生的。用于本发明目的的氧阻隔层是腐蚀控制层或腐蚀控制涂层,其保护金属特别是铁和/或钢免受气体尤其是氧气的氧化,优选在高温下如此。特别地,与还没有进行涂覆的腐蚀控制涂层相比,或者与其他如用清漆或油漆涂覆的腐蚀控制涂层相比,基底和第一个阴极保护层的氧化所需要的氧渗透被阻止或者至少显著延迟。适合的氧阻隔涂层原则上是已知的,并通常用于金属的热成型,特别是钢的热成型中,例如用于可压力硬化的钢—也称压力硬化钢的加工中。在可压力硬化钢的加工中,将具有氧阻隔层的金属基底,加热到约950℃,然后在压力下成型(形成)。氧阻隔层防止了金属表面结垢即金属表面氧化,因此通常也称为结垢控制层或结垢控制涂层。结垢妨碍了金属基底随后的处理或其应用,因为结垢层迫使在制备随后涂层中进行高成本和不方便的清洁过程。结垢层的形成也改变了组件的尺寸,结垢的黑色脆性层也不利地影响组件的美观和表面质量。特别是,结垢层的剥落也引起在机械加工操作中污染的问题。在本发明的上下文中,对于通常的阴极腐蚀控制涂层,特别是锌基的那些涂层,以及对于涂覆其上的结垢控制涂层,都能获得良好的结果。令人惊奇的是,在金属上的锌涂层,例如电镀锌的和热浸镀锌的钢,特别是钢上的锌片涂层,在温度暴露时快速地失去了它们的阴极腐蚀控制效果。阴极腐蚀防护的失去一方面归因于锌的氧化,另一方面归因于涂层中裂纹的发生以及涂层的部分分层。特别地,锌片涂层,根据dineniso9227,在使用标记的盐雾试验中于1000小时或更多,10μm的层厚通常在标记处具有红锈抑制作用,但在300℃以上的温度暴露后仅具有低水平的阴极腐蚀控制,甚至不再有阴极腐蚀控制,这一缺点在标记处和表面中都适用。用于本发明目的的至少两层涂层防止了这一问题出现,因为具有本发明涂层的金属基底,即使经如500℃的较长持续的温度暴露后,根据dineniso9227的带标记的盐雾试验中,还具有显著的阴极腐蚀控制效果。本文中特别令人惊奇的事实在于,即使将根据本发明涂覆的基底长时间或重复加热到元素锌的熔点之上,本发明的涂层的阴极腐蚀控制效果也能保持。正如上文已观察到的,使用标准商用阴极腐蚀控制涂层,以及同样的标准商用氧阻隔涂层,更特别是结垢控制涂层,能够获得杰出的效果。具体地互相精细调整两个层,可另外显著地改善高温阴极腐蚀控制。特别是本发明已经发现,即使是在500℃以上温度的较长持续地加热涂覆的金属基底后还保持有阴极腐蚀控制。因此,具有本发明涂层的基底能够加热到高于纯锌熔点或所用锌合金熔点之上的温度,而不会降低或甚至完全破坏阴极腐蚀控制。金属基底通常包括至少一种选自铝和铁的金属,优选铁,或者由其合金组成。根据本发明优选的实施方式,基底由钢组成。在本发明的上下文中,存在通用规定,即第一层设置在第二层和基底之间。尤其是,第二层直接涂覆到第一层时,在本发明中获得了特别好的结果。本发明的涂层因此优选应用为基底上的两层涂层,由底漆或底层,以及顶层构成。此处可规定有其他的层,例如附着促进层,例如转换层,设置在涂层和基底之间。就涂层涂覆到基底上的厚度而言,可在较宽范围内变化。然而,如果涂层的层厚在0.5-200μm,更特别是1-180μm,优选2-150μm,更优选3-120μm,还更优选4-100μm的范围时,获得了特别好的结果。如果第一层以锌片涂层形式涂覆到基底上时,涂层通常的层厚范围从1-30μm,更特别是2-20μm,优选3-15μm,更优选4-10μm。因此,特别是当使用锌片涂层时,本发明的涂层仅具有小的层厚,因此基底中的轮廓仍然可见且不会失去它们的辨别性或清晰度。此外,本发明的涂层可灵活使用,也能容易地重新涂覆或涂覆。如上文已观察到的,本发明的涂层具有杰出的腐蚀控制效果。通常,在本发明的上下文中,根据dineniso4628评估时,先经30天300℃高温暴露后至少500小时的一段时间内,更特别是600小时,优选800小时,更优选900小时,还更优选1000小时,在根据dineniso9227的带标记的盐雾试验中,于具有涂层的基底上,规定并未在标记处形成红锈和/或未观察到涂层的损坏。对于本发明的目的,dineniso9227的参考通常涉及2012年9月,即09/2012的标准版本。dinen35iso4628的参考通常涉及2013年3月即03/2013的标准标版。此外,在本发明的上下文中,根据dineniso4628评估时,先经30天300℃高温暴露后500小时-3000小时的一段时间内,更特别是600-2500小时,优选800-2000小时,更优选900-1800小时,还更优选1000-1500小时,在根据dineniso9227的带标记的盐雾试验中,于具有涂层的基底上,未在标记处形成红锈和/或未观察到涂层的损坏。通常,具有本发明涂层的基底,根据dineniso4628评估时,先经30天300℃高温暴露后,在根据dineniso9227的带标记的盐雾试验中,与没有额外氧阻隔层的阴极腐蚀控制涂层相比,仅在两倍的测试持续时间后于标记处具有红锈形成,更特别是五倍的持续时间,优选10倍,更优选20倍的持续时间。根据本发明的一优选实施方式,根据dineniso4628评估时,先经48小时以上450℃高温暴露后至少80小时的一段时间内,更特别是100小时,优选150小时,更优选200小时,还更优选250小时,在根据dineniso9227的带标记的盐雾试验中,于具有涂层的基底上,并未在标记处形成红锈和/或未观察到涂层的损坏。同样可能的是,根据dineniso4628评估时,先经48小时以上450℃高温暴露后至少80-1000小时的一段时间内,更特别是100-800小时,优选150-600小时,更优选200-500小时,还更优选250-350小时,在根据dineniso9227的带标记的盐雾试验中,于具有涂层的基底上,并未在标记处形成红锈和/或未观察到涂层的损坏。通常,具有本发明涂层的基底,根据dineniso4628评估时,先经48小时以上450℃高温暴露后,在根据dineniso9227的带标记的盐雾试验中,与没有额外氧阻隔层的阴极腐蚀控制涂层相比,仅在三倍的测试持续时间后于标记处具有红锈形成,更特别是五倍的持续时间,优选10倍,更优选20倍的持续时间。在本发明的上下文中,因此可能的是,根据dineniso4628评估时,先经48小时以上500℃高温暴露后至少80小时的一段时间内,更特别是100小时,优选150小时,更优选200小时,还更优选250小时,在根据dineniso9227的带标记的盐雾试验中,于具有涂层的基底上,并未在标记处形成红锈和/或未观察到涂层的损坏。同样对其规定的是,根据dineniso4628评估时,先经48小时以上450℃高温暴露后至少80-1000小时的一段时间内,更特别是100-800小时,优选150-500小时,更优选200-450小时,还更优选250-350小时,在根据dineniso9227的带标记的盐雾试验中,于具有涂层的基底上,并未在标记处形成红锈和/或未观察到涂层的损坏。通常,具有本发明涂层的基底,根据dineniso4628评估时,先经48小时以上500℃高温暴露后,在根据dineniso9227的带标记的盐雾试验中,与没有额外氧阻隔层的阴极腐蚀控制涂层相比,仅在两倍的测试持续时间后于标记处具有红锈形成,更特别是三倍的持续时间,优选5倍,更优选10倍,还更优选20倍的持续时间。因此本发明的涂层能够在高温和/或实际上位于所用牺牲金属的,更特别是锌和适当锌合金的熔点温度之上高温暴露后进行阴极腐蚀控制。这是非常令人惊奇的,因为,特别是基底牺牲金属通常更容易在高温增强和快速腐蚀。特别地,该结果相对于本文中优先使用的锌片体系而言是非常令人惊奇的。不希望被理论束缚,锌片体系在高温暴露后改善的腐蚀控制可归因于以下事实,即含锌涂层体系中的惰性粘合剂,通常主要是无机基的,确保了锌粒子一方面在融化期间大部分保持它们的形状或者在粘合剂中至少存在单个的锌岛状物,另一方面,通过粘合剂合并氧阻隔层额外保护锌免受氧化。本发明的涂层的第一层层厚范围通常为0.1-180μm,更优选0.5-150μm,优选1-140μm,更优选2-110μm,还更优选2-90μm。如果第一层以锌片涂层形式涂覆到基底上时,那么第一层通常的层厚范围为0.1-25μm,更特别1-15μm,优选2-10μm,更优选4-8μm。在本发明的上下文中对于第一层通常的规定是包含至少一种金属,选自由锌、铝、镁、铋、锡、镍和锰以及其混合物和合金组成的组中,优选第一层金属包含锌、铝、镁以及其混合物和合金。为了能够保证阴极腐蚀控制,所用的金属必须具有低于基底材料的电化学标准电势,或者基底材料,由于钝化,特别是自我钝化,必须防止以氧化涂层金属的方式氧化。相对基底而言,上述金属形成了所谓的牺牲金属或牺牲阳极,其取代基底被腐蚀。如果第一层包含锌和/或锌合金,本发明的上下文中获得了良好的结果。在经济有利的情况下,锌和锌合金保证了最有效的腐蚀控制,更特别是高温腐蚀控制。在本发明的上下文中,优选的是,如果涂层表面面对的环境是,特别是至少基本无铁时,特别是无铁-锌合金时。为本发明的目的优先使用的阴极腐蚀控制涂层优选非铁-锌合金,特别是镀锌涂层。下面就第一层的形成而言,将金属或多种金属以不同方式涂覆到基底上。然而在本发明的上下文中,如果第一层通过电解或热浸镀锌涂覆形成在锌层基础上时,能够获得特别好的效果。在热浸镀锌的情况下,待处理的基底浸入到液态锌槽中,随后冷却,在基底上保留下一层薄的锌涂层。对于电解镀锌,也称为电镀锌,将待涂覆的基底浸入到含锌离子的电解槽中。施加外部电压,金属基底用作阴极,使得均匀的锌层沉积在金属基底上。热浸镀锌和电镀锌或电解镀锌都是制备具有活性阴极腐蚀控制的锌涂层钢基底中的常规方法。如果第一层形成在包含金属粒子,更特别是金属抗腐蚀颜料的基质基础上时,在本发明的上下文中获得了最佳的结果。在本文中已证实是特别合适的是,如果至少一些金属粒子包含锌和/或锌合金。用于本发明目的的基质是固化的粘合剂,优选围绕和完全润湿金属粒子。用于本发明目的的基质特别包含任选的小部分有机物的无机体系或无机-有机杂化材料,优选基于任选改性的二氧化硅、二氧化钛和二氧化锆形成。对于第一层中金属粒子的数量,它当然可在较宽范围内变化。然而,为了本发明的目的,如果以第一层计,第一层包含至少50wt%,更特别是至少60wt%,优选至少70wt%的金属粒子时,获得了特别好的结果。同样地,如果以第一层计,第一层包含金属粒子的百分数范围为50-95wt%,更特别是60-95wt%,优选70-90wt%。正如已发现的,不仅组合物中的金属粒子部分或它们的化学组合物,对产生阴极保护效果都是关键的,而且粒子形态也对腐蚀保护具有关键的影响。第一层通常包括片状和/或粒状,更特别是球状的金属粒子。优选的是,第一层包含片状的金属粒子。在现有技术的语言中,片状金属粒子也称为片或片层。片状金属粒子在一个空间方向上具有显著低的尺寸,下面也称为厚度;在其他两个空间方向上的尺寸下文称为直径。粒状金属粒子是不规则形状的金属粒子,而球状金属粒子具有约球体的形状。球形金属粒子的使用优于粒状金属粒子的使用。本发明使用的金属粒子的尺寸可同样根据其他条件在较宽范围内变化。然而如果片状金属粒子的厚度为50-1000nm,更特别是60-750nm,优选80-600nm,更优选100-500nm时,获得了特别好的结果。同样规定了片状金属粒子的直径为1-25μm,更特别是2-20μm,优选5-18μm,更优选5-15μm。此外,在本发明的上下文中,如果粒状,更特别是球状金属粒子的粒子直径范围500nm-20μm,更特别是500nm-10μm,优选500-5μm时,是优选的。对于上述尺寸的金属粒子,能够获得杰出的腐蚀控制的涂层,特别是结合精确的定量协调。通常,金属离子形成在纯锌和/或锌合金的基础上。对于本发明上下文中优先使用的锌合金,锌合金选自锌-铋合金、锌-铝合金和/或锌-铝-镁合金、更特别是锌铝合金和/或锌-铝-镁合金,优选锌-铝-镁合金。根据本发明的一优选实施方式,第一层包含锌片层作为片状金属粒子,更特别是在纯锌和/或上述锌合金的基础上。已经发现,对于基于锌-铝-镁合金的片状金属粒子能够获得特别好的结果,特别是由于镁通常发生的快速的腐蚀,这是令人惊奇的。然而,令人惊讶的是,已经发现,对于包含基于锌-铝-镁合金的片状金属粒子的腐蚀控制涂层来说,能够获得显著改善的腐蚀保护。具有基于锌-铝-镁合金的片状金属粒子的涂覆体系,相对于常规锌片体系而言,即使没有额外的氧阻隔层,高温暴露下也具有显著改善的腐蚀控制性能。然而,氧阻隔层由于多个因素同样增加了这些体系的温度稳定性。在本发明的上下文中,规定了第一层形成在锌片涂层的基础上。特别是为了本发明的目的,对于锌片涂层,特别在高温暴露下,获得了特别好的腐蚀保护效果。此外,规定了第一层包含至少一种填料,以第一层计,数量为0.5-10wt%,更特别是1-8wt%,优选1-5wt%。可使用的填料几乎是任何在应用条件下惰性和稳定的粒子物质,更特别是无机矿物、玻璃、陶瓷物质和金属。然而,已经发现,如果填料选自金属,更特别是al、sn、ni、mn、bi、w或不锈钢以及其混合物和合金时,获得了特别好的结果,优选al,更优选铝片。如果填料选自氮化硼、碳化钨和玻璃时,同样获得了较好的结果。这些填料可替换金属填料使用或与其一起使用。根据本发明的一特别的实施方式,由其获得第一层的涂层组合物称为超高固体含量组合物,即固体百分数达到100wt%,更特别是95-100wt%固体部分的涂层组合物。以组合物计,超高固体含量组合物还可具有达5wt%的溶剂部分。该溶剂部分通常用于调节涂层组合物的粘度和用于改善涂层组合物的应用性质。已经发现,如果涂层由超高固体含量的组合物获得,必须对金属粒子的数量选择不同的优选范围。如果本发明的涂层的第一层由固体含量为95-100wt%的涂层组合物获得。已经证实,以第一层计,第一层包含至少35wt%、更特别是至少50wt%、优选至少70wt%,更优选至少80wt%的金属粒子是合适的。同样,根据该实施方式,以第一层计,第一层的金属粒子百分数范围为35-95wt%,更特别是50-95wt%,优选70-90wt%,更优选80-90wt%。根据该实施方式,以第一层计,如果第一层包含粒状,更特别是球状金属粒子的数量为35-95wt%,更特别是50-90wt%,优选70-90wt%,更优选80-90wt%,获得了特别好的结果。此处已经证实,如果金属粒子形成在锌或锌合金,优选元素锌的基础上是合适的。根据该实施方式,如果粒状或球状金属粒子形成在锌粉基础上时可获得特别好的结果。此外,根据该实施方式,规定了以第一层计,第一层包含片状金属粒子的数量为0.1-50wt%,更特别是0.2-25wt%,优选0.3-10wt%,更优选0.5-5wt%。如果片状金属粒子形成在锌或锌合金,优选元素锌的基础上时,在本文中获得了特别好的结果。适当的锌合金特别是上述用于锌片底漆的合金。当使用固体含量为95-100wt%的涂层组合物时,与溶剂基或水基涂层组合物相比,优选使用球状金属粒子。特别是如果目的在于获得例如通过喷涂涂覆的低粘度涂层组合物,因为球形金属粒子相比片状金属粒子引起更少的涂层组合物粘度的增加。如上所述,本发明的涂层的第一层可具有无机基的基底。在本文中,如果无机基的基底经有机改性,即包含键合到无机框架上的有机基团和/或有机官能团时,已经证明是有利的。效果是能够获得第一层以及因此整个涂层柔性的增加,从而防止了如涂层剥落和/或从基底分离,或者在涂层中形成裂纹。通常,第一层的无机基基底包含无机氧化物,更特别是硅、钛和/或锆的氧化物,优选二氧化硅和/或二氧化钛,或者特别是基本上至少由上述的氧化物组成。上述的无机氧化物形成无机基的基质框架,且无机基的基值也可由所述氧化物的混合物和/或共缩合物组成。通常,第一层的无机基基质可通过无机或有机基团的缩合反应和/或有机基团的聚合反应,更特别是有机基团的缩合反应,所述有机基团来自硅烷、聚硅烷、硅烷水解物、聚硅氧烷、硅酸酯、钛酸酯、聚钛酸酯,锆酸酯以及它们的混合物。如果有机基的基质来自硅烷、硅烷水解物、聚硅氧烷、钛酸酯、聚钛酸酯,锆酸酯及其混合物,获得了特别好的结果。这些缩合和/或聚合反应可热诱导或通过电磁辐射诱导。在本文中,所有缩合和/或聚合所需的反应物或催化剂可存在于待使用的涂层组合物中。替代地,用于开始化学反应的单个反应物和/或催化剂可不必加入,直到用涂层组合物涂覆基底之前或之后不久,或者扩散到涂层组合物中,如大气湿度。本发明上下文中的聚合反应涉及导致单个分子和/或形成无机基质的粒子连接的有机官能基团的反应。聚合反应例如可通过烯烃发生,例如丙烯酸酯、乙烯基或环氧化物。用于本发明目的的缩合反应是两个或两个以上分子和/或粒子的反应,其中在单个分子和/或粒子之间形成化学键并脱去水。有机基团的缩合反应实例是酯化和酰胺化。无机基团的缩合反应实例是无机酸衍生物,源生自钛酸酯和/或烷氧硅烷和锆酸酯的水解,并导致聚合无机氧化物的形成,更特别是二氧化硅、二氧化钛和氧化锆。高含量的无机化合物,即特别是二氧化硅、二氧化钛和/或二氧化锆,导致此处特别耐受高温暴露的耐用涂层,通常一定含量的有机基团是必要的,用于提供涂层需要的柔韧性。纯无机基的涂层是非常脆的,当有大量的机械负载时被破坏,导致了阴极腐蚀控制的降低或损失。对于第一层中无机基基质的数量,它可以在宽范围内变化。然而,以第一层计,如果第一层包含无机基基质的数量为5-45wt%,更特别是5-40wt%,优选10-30wt%,更优选10-20wt%时,获得了特别好的结果。根据本发明的一优选实施方式,无机基基质通过有机基团进行改性。在本文中,已经证明了合适的有机基团选自烷基、芳基和烯烃基团以及其混合物和反应产物。根据本发明的又一优选实施方式,该有机基团是c1至c10烷基,更特别是c1至c5烷基,优选c1至c3烷基,更优选c1和/或c2的烷基。同样优选的有机基团是c6至c20芳基,更特别是c6至c15芳基,优选c6至c10的芳基。另外规定了有机基团是c2至c10的烯烃基团,更特别是c2至c8烯烃基团,优选c2至c5的烯烃基团,更优选c2和/或c3的烯烃基团,非常优选乙烯基团。对于上述有机基团,能够获得特别耐用同时又柔韧的无机基基质。如果有机基团是甲基和/或乙基基团和/或乙烯基团,是特别优选的。本发明的上下文中,进一步规定了有机基团另外具有极性化学基团,更特别选自醇、醚、硫醇、胺、醛、酮、酯、酰胺、氨基甲酸乙酯和/或羧酸,优选醇、胺和/或羧酸。本发明涂层的第一层通常通过含溶剂的和/或水基涂层组合物获得,该组合物在室温或高温下交联。这一交联在暴露到大气湿度时可通过涂层组合物中存在的组分发生,特别是在溶剂基体系的情况下。然而,此外,如上所观察到的,本发明的涂层的第一层也可能来自固体百分数为95-100wt%的涂层组合物,即来自所谓的超高固体涂层组合物。如果本发明的涂层的第一层获得自固体含量95-100wt%的涂层组合物,那么第一层包含以第一层计,通常数量为5-65wt%,更特别是5-50wt%,优选10-30wt%,更优选10-20wt%的无机基基质。通常,以组合物计,固体百分数95-100wt%的涂层组合物暴露到大气湿度时交联。对于本发明涂层的第二层,它优选以氧阻隔层形式形成。通常,本发明涂层的第二层层厚范围为0.1-50μm,更特别是0.5-40μm,优选0.7-30μm,更优选1-10μm,极优选1-5μm,特别优选1-3μm。本发明涂层的第二层,更特别是氧阻隔层,可由多种材料组成。因此例如第二层可以是仅由金属组成的氧阻隔层,更特别是通过热浸镀铝涂覆的铝层。在本发明的上下文中,也规定了本发明涂层的第二层包含无机基的基质,更特别是固化粘合剂或固化粘合体系。在本发明的上下文中,以第二层计,如果第二层包含的无机基的基质数量为50-100wt%,更特别是60-100wt%,优选65-95wt%,更优选70-85wt%时,经发现是合适的。本发明的涂层的第二层可完全或者几乎完全由无机基的基质组成,即整体的或交联的粘合剂的无机基基质组成,因此可以透明涂层的形式存在。通常,第二层的无机基基质通过无机氧化物形成,更特别是硅、钛和/或锆的氧化物,优选二氧化硅和/或二氧化钛,更优选二氧化硅,在本文中,规定了联合使用如含硅、钛-和锆的前体物质的混合氧化物和/或共缩合物。然而,如果无机氧化物是二氧化硅是优选的,它任选包含少量的二氧化钛。根据本发明的一优选实施方式,无机基基质是有机改性的。无机基基质的有机改性导致第二层,更特别是氧阻隔层的柔性增加,从而防止了涂层的剥落或分层以及涂层内部开裂。在本发明的上下文中,粘合剂通过有机基团改性时获得了特别好的结果,特别是,有机基团选自烷基、芳基和烯烃基团及其混合物和反应产物。在本文中,规定了有机基团是c1-c10烷基基团,更特别是c1-c5烷基基团,优选c1-c3烷基基团,更优选c1和/或c2烷基基团。同样规定了有机基团是c6至c20的芳基,更特别是c6至c15的芳基,优选c6至c10的芳基。此外,有机基团可以是c2至c10烯烃基团,更特别是c2至c8烯烃基团,优选c2~c5烯烃基团,更优选c2和/或c3烯烃基团,非常优选乙烯基团。如果有机基团选自甲基和或乙基基团以及甲苯基基团时,在本发明的上下文中获得了特别好的结果。通常,第二层的无机基的基质可来自硅烷、聚硅烷、硅烷水解物、聚硅氧烷、硅醇盐(siliconates)、硅酸盐(silicates)、钛酸盐、聚钛酸酯、锆酸盐和磷酸二氢铝,更具体是硅烷、硅烷水解物和聚硅氧烷及其混合物。基于二氧化硅的无机基基质,特别显示出高温不透气性以及涂层的优良柔韧性。类似于第一层的无机基基质,第二层的无机基基质可通过有机和无机基团的聚合和缩合反应来获得。根据本发明的一优选实施方式,第二层的无机基基质通过无机基团的缩合反应获得。因此第二层的无机基基质优选通过无机氢氧化物的缩合反应生成,例如通过相应的烷氧基化合物水解获得。这样,获得了特别耐用的涂层,该涂层在高温也是耐氧化的。在高温经由有机基团连接涂层组合物的单个分子和/或粒子时,观察到至少碳链的部分氧化,这导致涂层的腐蚀控制效果退化。此外,在本发明的上下文中,如果以无机基基质计,第二层的无机基基质的碳含量不超过50wt%,更特别是40wt%,优选35wt%,更优选30wt%时,获得了非常好的结果。以无机基基质计,如果第二层的无机基基质的碳含量范围从0.01-50wt%,更特别是0.05-40wt%,优选0.1-35wt%,更优选0.1-30wt%时,也是优选的。如上已观察到的,无机基基质中一定的碳百分数通常是有利的,也是必要的,以便赋予涂层具有必要的柔韧性,尽管已经发现,太高的碳百分数,特别是使用较长的碳链基团时,导致了高温时有机组分的氧化,这弱化了涂层的结构以及腐蚀控制效果。如果第二层的涂料组合物的粘合剂选自聚硅酸盐,更特别是水玻璃,优选钠和/或钾的水玻璃,或磷酸二氢铝时,获得了具有良好机械性能的完全无碳的基质。类似于第一层,第二层的无机基基质也获得自溶剂基和/或水基涂层组合物或者获得自以涂层组合物计,固体含量95-100wt%的超高固体含量的涂层组合物。如上所述,本发明涂层的第二层也可是无金属粒子的,即以透明涂层的形式,从而实现高温下的腐蚀保护,这也是对现有技术中使用的腐蚀控制涂层显著的改进。第二层还可以设置为惰性陶瓷或玻璃基颗粒,特别是薄片。然而,如果第二层包括金属颗粒时,它能够实现阴极腐蚀控制的温度稳定性的进一步显著改善。在本发明的上下文中,如果第二层包含金属粒子是有利的。在那种情况下,规定了以第二层计,第二层包含至少5wt%,更特别是至少10wt%,优选至少15wt%的金属粒子。如果以第二层计,第二层包含的金属粒子的百分数范围从5-50wt%,更特别是10-40wt%,优选15-30wt%时,是优选的。以第二层计,如果第二层包含的金属粒子的百分数范围从35-95wt%,更特别是45-80wt%,优选55-70wt%时,也能获得特别好的结果。如果本发明涂层的第二层确实包含金属粒子,那么这些粒子通常基于锌、铝和/或镁及其合金形成。此处特别优选的是金属粒子为铝粒子。同样规定了第二层包含片状和/或粒状的金属粒子,更特别是球形金属粒子,优选片状金属粒子。已经发现,片状金属粒子,特别是铝片,组成了杰出的氧阻隔并有效防止了高温下阴极腐蚀控制层的氧化。在本文中,已经发现片状金属粒子的厚度为10-1000nm,更特别是25-750nm,优选40-600nm,更优选50-500nm。如果片状金属粒子的直径为50nm-25μm,更特别是100nm-20μm,优选250nm-15μm,优选500nm-10μm,非常优选1-8μm,特别优选3-5μm。对于所用的金属粒子的尺寸,它可在较宽范围内变化。然而,如果片状金属粒子的厚度为50-1000nm,更特别是60-750nm,优选80-600nm,更优选100-500nm,获得了特别好的结果。如果片状金属粒子的直径为1-25μm,更特别是2-20μm,优选5-18μm,更优选5-15μm时,同样是有利的。如果本发明涂层的第二层包括粒状和/或球形金属粒子,这些粒子通常的直径范围从500nm-10μm,更特别是500nm-5μm,优选500nm-3μm。进一步规定了第二层包括其他粒子,更特别是填料。如果第二层包含填料,其数量可在较宽范围内变化。然而,已经发现第二层包含填料的数量以第二层计为0.5-10wt%,更特别是1-8wt%,优选2-5wt%合适。本文中的填料应该是温度稳定的和氧化稳定的,且也是惰性的,意味着他们必须在应用条件下不能与涂层、基底或环境的其他组分反应,更特别是与大气氧反应。如果填料选自碳化钨、氮化硼、玻璃粒子、磷化铁、二氧化锆、不锈钢和它们的混合物。附图说明图1显示了具有本发明的涂层1的金属基底2;图2显示了具有基于纯锌片的阴极腐蚀控制涂层的钢板,先经48小以上时400℃高温暴露后,根据dineniso9227实施带标记的盐雾试验;图3显示了具有基于锌-铝-镁合金片的阴极腐蚀控制涂层的钢板,先经48小时以上400℃高温暴露后,根据dineniso9227实施带标记的盐雾试验;图4显示了具有阴极腐蚀控制涂层和氧阻隔涂层的钢基底,先经48小时以上400℃高温暴露后,根据dineniso9227实施带标记的盐雾试验;图5显示了具有阴极腐蚀控制涂层的钢板,经48小时以上500℃高温暴露后,根据dineniso9227实施带标记的盐雾试验;和图6显示了具有阴极腐蚀控制涂层和具有氧阻隔涂层的钢板,经48小时以上500℃高温暴露后,根据dineniso9227实施带标记的盐雾试验;根据本发明的第二方面,本发明进一步提供了用于生产阴极腐蚀控制涂层的涂层组合物,更特别是具有高温暴露后增强的腐蚀控制的涂层组合物,包括:(a)至少一种基质形成剂,(b)金属粒子和(c)任选的添加剂和辅料。此处本发明的上下文中的基质形成剂含义是包含和封闭着金属粒子的粘合剂以及任选的其他添加剂和辅料,且交联和/或固化时形成固体基质,其中嵌入了金属粒子和任选的其他佐剂。在固化和/或交联用于生产阴极腐蚀控制涂层的涂层组合物时,基质形成剂优选形成本发明涂层的第一层的无机基基质。为了本发明的目的,基质形成剂应该理解为形成优选的无机基基质一部分的涂层组合物的所有组分和/或化合物。在本发明的上下文中,此处特别地指出粘合剂和交联剂之间不加以区别,因为申请人已经发现,通常的用于硅烷基体系和/或聚硅氧烷基体系的交联剂,如钛酸四丁酯,本身也可以是固化和/或交联的粘合剂和/或无机基基质的主要成分。因此,基质形成剂根据在期望的交联和/或固化时间呈现涂层最大均匀性的标准选择。因此,主要因素是选择具有彼此相容的反应速率的基质形成剂,以便在基质部分设置期望的固化和交联特性。本发明的涂层组合物通常是分散质的形式。用于本发明目的的分散质是任何一种至少两相的混合物,更特别是均匀的混合物,由连续相、分散介质和不连续相组成,分散物质精细且均匀地分散在分散介质中。在本文中,规定了组合物包含有机溶剂和/或水以使组合物具有以组合物计95-100wt%的固体含量。如果涂层组合物包含有机溶剂和/或水,那么涂层组合物以组合物计,通常包含它们的数量是0.5-60wt%,更特别是1-50wt%,优选2-40wt%,更优选5-30wt%。可使用的有机溶剂是所有适当的有机溶剂。特别合适的是芳族烃和脂族烃以及极性有机溶剂,如丙酮、醇,尤其是c1至c20的醇,优选c2至c10的醇,更优选c2至c8醇,腈或硝基化合物,特别是硝基丙烷。涂层组合物以组合物计,优选包含至少30wt%,更特别是至少40wt%,优选至少45wt%,更优选至少50wt%的金属粒子。如果涂层组合物以组合物计,金属粒子的百分数范围从35-95wt%,更特别是40-80wt%,优选45-70wt%,更优选50-60wt%。此外,在本发明的上下文中,如果至少一些金属粒子包含锌和/或锌合金,获得了良好的结果。根据本发明一优选的实施方式,涂层组合物包含片状和/或粒状,更特别是片状的金属粒子。对于所用金属粒子的尺寸,它可在较宽范围内变化。然而,如果片状金属粒子的厚度为50-1000nm,更特别是60-750nm,优选80-600nm,更优选100-500nm时,获得了特别好的结果。同样,如果片状金属粒子的直径为1-25μm,更特别是2-20μm,优选5-18μm,更优选5-15μm时,是有利的。如果本发明的涂层组合物的确包含粒状金属粒子,特别是球状金属粒子,本发明的上下文中,优选粒状,更特别是球状金属粒子的粒子直径范围是500nm-20μm,更特别是500nm-10μm,优选500nm-5μm。进一步规定了组合物包含至少一种填料,更特别是惰性填料,以组合物计,数量为0.1-10wt%,更特别是0.5-8wt%,优选0.5-5wt%。特别在涂层组合物中使用的是针对本发明涂层的第一层上述的填料。对于用于生产无机基基质的基质形成剂,通常选自硅烷、聚硅烷、硅烷水解物、聚硅氧烷、硅酸盐、聚硅酸盐、钛酸盐、聚钛酸盐和锆酸盐,更特别是硅烷、硅烷水解物、聚硅氧烷、钛酸盐、聚钛酸盐及其混合物。此外,为了本发明的目的,如果基质形成剂经有机改性是优选的。在本发明的上下文中,进一步规定了基质形成剂通过有机基团和/或无机基团的缩合反应交联和/或固化。也规定了基质形成剂通过有机基团聚合反应交联和/或固化。然而,如上所述,如果基质形成剂通过缩合反应,特别是无机基团的缩合反应交联和/或固化,在本发明的上下文中是优选的。特别地,如果基质形成剂用有机基团至少部分改性,在本发明的上下文中获得了特别好的结果。在本文中,如果有机基团选自烷基、芳基和烯烃基团时已经证明是合适的。如果基质形成剂包含烷基基团,它们通常选自c1至c10烷基,更特别c1至c5烷基,优选c1至c3烷基,更优选c1和/或c2烷基。如果基质形成剂包含芳基基团,它们通常选自c6至c20的芳基基团,更特别是c6至c15芳基基团,优选c6至c10的芳基基团。如果基质形成剂包含烯烃基团,它们通常选自c2至c10烯烃基基团,更特别是c2至c8烯烃基基团,优选c2至c5的烯烃基基团,更优选c2和/或c3烯烃基基团,非常优选乙烯基团。如果基质形成剂包含甲基和/或乙基基团和/或乙烯基团时,在本发明的上下文中获得了特别好的结果。此外,在本发明的上下文中,规定了有机基团还具有极性化学基团,更特别选自羟基、醚、硫醇、胺、醛、酮和/或羧酸,优选羟基、醚、胺和/或羧酸。根据本发明的一优选实施方式,基质形成剂选自通式i的硅烷:r4-nsixn(i)其中,r是烷基,更特别是c1-c5烷基,优选c1-c3烷基,更优选c1和/或c2烷基;芳基,更特别是c6-c20芳基,优选c6-c15芳基,更优选c6-c10芳基;烯烃基,更特别是端烯烃基,优选c2-c10烯烃基,更优选c2-c8烯烃基,非常优选c2-c5烯烃基,特别优选c2和/或c3烯烃基,更特别优选乙烯;胺,更特别是c2-c10胺,优选c2-c8胺,更优选c2-c5胺,非常优选c2和/或c3胺;羧酸,更特别是c2-c10羧酸,优选c2-c8羧酸,更优选c2-c5羧酸,非常优选c2和/或c3羧酸;醇,更特别是c2-c10的醇,优选c2-c8醇,更优选c2-c5醇,非常优选c2和/或c3的醇;x是卤化物,更特别是氯化物和/或溴化物;烷氧基,更特别是c1至c6烷氧基,非常优选c1至c4烷氧基,尤其优选c1和/或c2烷氧基;且n为1-4,优选2或3。在本文中,已经发现,基质形成剂选自通式ia的硅烷是合适的:r4-nsixn(ia)其中,r是c1-c3烷基,特别是c1和/或c2烷基;c6-c15芳基,特别是c6-c10芳基;c2和/或c3烯烃,特别是乙烯;x是烷氧基,特别是c1-c6烷氧基,更优选c1-c4烷氧基,非常优选c1和/或c2烷氧基;且n为2或3。如果基质形成剂选自烷基硅烷、更特别是三烷氧基烷基硅烷、二烷氧基二烷基硅烷,和/或烷氧基三烷基硅烷,和或选自乙烯硅烷、更特别是三烷氧基乙烯硅烷、二烷氧基二乙烯硅烷和/或烷氧基三乙烯硅烷,在本发明的上下文中可以得到特别好的结果。特别是根据通式i和ia的硅烷来说是特别好的。如果基质形成剂选自硅烷水解物、聚硅氧烷、特别是烷基聚硅氧烷,优选c1-c3烷基聚硅氧烷和/或c1-c3烷氧基烷基聚硅氧烷,和/或选自乙烯基聚硅氧烷,和选自聚钛酸酯时,同样在本发明的上下文中是优选的。如果基质形成剂的重均分子量mw的范围为200-200,000g/mol,更特别是500-150,000g/mol,优选1000-100,000g/mol,更优选2000-75,000g/mol,最优选5000-50,000g/mol时,在本发明中获得了特别好的结果。此外,在本发明的上下文中,如果基质形成剂选自通式ii的钛酸盐,获得了良好的结果tix4(ii)其中,x为卤化物,更特别是氯化物和/或溴化物;烷氧基,特别是c1-c8烷氧基,优选c1-c6烷氧基,更优选c1-c4烷氧基。在本文中,如果基质形成剂选自通式iia的钛酸酯,已经证明是合适的tix4(iia)其中,x为烷氧基,特别是c1-c8烷氧基,优选c1-c6烷氧基,更优选c1-c4烷氧基。此外,同样基质形成剂能够选自通式iii的锆酸盐zrx4(iii)其中,x为卤化物,特别是氯化物和/或溴化物;烷氧基,特别是c1-c8烷氧基,优选c1-c6烷氧基,更优选c1-c4烷氧基。如果基质形成剂选自通式iiia的锆酸盐时,此处获得了特别好的结果:zrx4(iiia)其中,x为烷氧基,特别是c1-c8烷氧基,优选c1-c6烷氧基,更优选c1-c4烷氧基。此外,在本发明的上下文中,能够将硅醇盐(siliconate)用作基质形成剂。如果使用通式iv的硅醇盐时,在这种情况下获得了特别好的结果:ho-[si(r)(om)-o-]nh(iv)其中n为1-6,特别是1-3,优选1;r为c1-c10烷基和/或c6-c15芳基,特别是c1-c8烷基和/或c6-c12芳基,优选c1-c6烷基和/或c6-c12芳基,更优选c1-c4烷基,最优选c1-c3烷基;m为一价金属,特别是碱金属,优选钠或钾。在本文中,已经证明硅醇盐选自甲基硅醇钠、甲基硅醇钾、丙基硅醇钠和丙基硅醇钾是合适的。此外,基质形成剂可能选自二氧化硅更特别是硅石,二氧化钛和/或氧化锆。如果涂层组合物包含二氧化硅、二氧化钛和/或氧化锆作为基质形成剂,它们通常在涂层组合物中以粒子形式存在,更特别是少量存在,以涂层组合物计,更特别数量为0.1-10wt%,优选0.2-5wt%,更优选0.5-2wt%。在本发明的上下文中,如果涂层组合物包含至少两种不同的基质形成剂,特别是两种反应性的基质形成剂,获得了特别好的结果。因此,为了本发明的目的,反应性的基质形成剂是具有反应性功能化学基团的基质形成剂。如可以是可水解基团或可聚合基团。功能性化学基团必须能在交联条件下与其他基质形成剂的分子或基质形成剂的粒子发生反应。每种基质形成剂的反应性应该进行选择,以发生均匀的交联,能够均匀包含金属粒子和其他添加剂。如果涂层组合物包含至少一种基于硅化合物的基质形成剂和一种基于钛化合物的基质形成剂,在本发明的上下文中获得了特别好的结果。通常,组合物包含的基质形成剂数量以组合物计,为1-45wt%,更特别是2-40wt%,优选5-30wt%,更优选5-20wt%。进一步规定了组合物包含至少一种有机聚合物,更特别是惰性聚合物,优选有机氟聚合物。如果组合物包含一种有机聚合物,其包含聚合物的数量以组合物计,为0.1-10wt%,更特别是0.2-5wt%,优选0.5-1wt%。如果有机聚合物选自聚四氟乙烯、聚氟乙烯、聚偏氟乙烯,优选聚偏氟乙烯时,这里获得了特别好的结果。对于本发明的涂层组合物的粘度,可在较宽范围内变化。然而,如果组合物具有用勃罗克费尔特(brookfield)粘度计法在20℃测得的范围是1到50000mpas,更特别是2至10000mpas,优选5至1000mpas,更优选5至500mpas,最优选10到100mpas时的动态粘度,已经发现是合适的。为了本发明的目的,进一步规定了涂层组合物包含其他的添加剂和/或辅料。如果用于生成阴极腐蚀控制层的本发明的涂层组合物包含其他的添加剂和/或辅料时,它们通常选自流变添加剂、防腐剂、稳定剂、酸和/或碱、表面活性剂、消泡剂组分、成膜剂、蜡、活性生物源成分、ph值稳定剂和ph调节剂。在本发明的上下文中,规定了组合物在高温下和/或通过辐射交联和/或固化,更特别是在高温下。对于组合物交联和/或固化的温度,它们可在较宽范围内变化。然而,已经证明组合物交联和/或固化的温度范围从30-350℃,优选50-300℃,更优选100-250℃,最优选100-200℃。通常,组合物,特别是基质形成剂,交联和/或固化的时间为1分钟-2小时,更特别是2分钟-1小时,优选3-30分钟,更优选4-20分钟,最优选5-15分钟。高温下,本发明的涂层组合物在极短的时间内固化,如在工业生产中能够有很高的产量。根据本发明的再一实施方式,组合物,更特别是基质形成剂,在室温交联和/或固化,室温固化的体系对基底来说是十分适合的,因为考虑到基底的尺寸,不能对其加热和/或辐射,如工业设备和/或钢结构部件。本发明的涂层和涂层组合物在本文中特别适合用于重建对现有设备以及结构的腐蚀保护。如果组合物和/或基质形成剂在室温交联和/或固化,那么组合物,更特别是基质形成剂的交联和/或固化优选的时间从1分钟到2小时,更特别是2分钟到1小时,优选3-45分钟,更优选5-30分钟。在室温交联的组合物,特别是基质形成剂的情况下,另外规定了交联通过大气湿度引发。根据本发明的一特别实施方式,涂层组合物的固体含量以组合物计为95-100wt%。根据该实施方式,本发明的涂层组合物具有无溶剂和/或无水的形式,或者低溶剂和/或低水的超高固体含量的涂层组合物。以组合物计,本发明的固体含量95-100wt%的涂层组合物,优选在室温和/或在大气湿度中固化。一方面从环境保护的观点看,优选完全不存在溶剂,另一方面,其是法定实施。通常,本发明的以组合物计,固体含量95-100wt%的涂层组合物是液体形式并经历完全的固化和/或交联。因此,本发明的涂层组合物可以像水基和溶剂基体系那样处理,特别是可以通过喷射涂覆。在粘度方面,本发明的涂层组合物相当于溶剂基和水基体系。超高固体含量的涂层组合物的特别合适的基质形成剂是烷基聚硅氧烷树脂,更特别是烷氧基烷基硅氧烷树脂,更特别是具有上述的重均分子量mw。如果本发明的用于生产阴极腐蚀控制层的涂层组合物具有以组合物计,固体含量95-100wt%的形式,那么以组合物计,如果组合物包含至少35wt%,更特别是至少50wt%,优选至少70wt%,更优选至少80wt%的金属粒子时,获得了特别好的结果。同样已经证明了,组合物的金属离子百分数范围以组合物计为35-95wt%,更特别是50-95wt%,优选70-90wt%,更优选80-90wt%是合适的。根据该特定的实施方式,如果以涂层组合物计,包含粒状,更特别是球状的金属粒子的数量为35-95wt%,更特别是50-90wt%,优选70-90wt%,更优选80-90wt%时,是优选的。在本文中,如果金属粒子基于锌或锌合金形成,优选基于元素锌形成是优选的。此外,根据该实施方式,规定了以组合物计,涂层组合物包含片状金属粒子,更特别是锌片的含量为0.1-50wt%,更特别是0.2-25wt%,优选0.3-10wt%,更优选0.5-5wt%。在文本中,已经证明,如果金属粒子基于锌或锌合金形成,优选基于元素锌形成是有利的。此外,根据该实施方式,通常规定了以组合物计,组合物包含的基质形成剂的数量为5-65wt%,更特别是5-50wt%,优选10-30wt%,更优选10-20wt%。对于本发明的用于生产阴极腐蚀控制涂层的涂层组合物的其他细节,可参照上述相关的本发明涂层的观察,这相应适用于本发明的用于生产阴极腐蚀控制涂层的涂层组合物。根据本发明的第三方面,本发明还提供了一种用于生产氧阻隔涂层的涂层组合物,包含无机基基质形成剂和任选的辅料和添加剂。通常,涂覆到基底上的涂层组合物的层厚范围为0.1-60μm,更特别是0.5-50μm,优选0.7-35μm,更优选1-10μm,非常优选1-5μm,特别优选1-3μm。涂层组合物通常是分散质的形式。在本文中,规定了组合物包含有机溶剂和/或水,和/或规定了组合物具有以组合物计,固体含量为95-100wt%的涂层组合物形式。预期的有机溶剂是所有适当的溶剂,特别是所述的与生产阴极腐蚀控制层的涂层组合物相关的。第二涂层组合物优选水基体系的形式或者具有以组合物计,固体含量95-100wt%的体系形式,优选水基体系的形式。水基体系对环境是友好的,不需要高成本和不方便的装置来收集和/或回收有机溶剂。此外,水基体系的使用也允许涂层组合物广泛应用于应对工作场所安全的背景,因为不存在火灾危险,且不会有有害健康的有机溶剂排入环境,特别是吸入的空气。如果涂层组合物包含有机溶剂和/或水,那么以涂层组合物计,涂层组合物包含的有机溶剂和/或水的数量为30-90wt%,更特别是40-80wt%,优选50-75wt%。然而,对于水基体系,特别是以涂层组合物计,如果涂层组合物包含不超过10wt%,更特别是不超过5wt%,优选不超过3wt%,更优选不超过1wt%的有机溶剂,获得了最好的结果,特别是对于获得涂层的温度稳定性而言。对于本发明的涂层组合物的粘度而言,它当然可在较宽范围内变化。然而,如果涂层组合物通过勃罗克费尔特粘度计法于20℃测量的动态粘度范围为1-50000mpas,更特别是2-10000mpas,优选5-1000mpas,更优选5-500mpas,最优选10-100mpas,获得了特别好的结果。此外,在本发明的上下文中规定了涂层组合物包含基质形成剂的数量以组合物计,是10-100wt%,更特别是15-90wt%,优选20-80wt%,更优选25-70wt%,最优选20-60wt%。根据本发明的一优选实施方式,基质形成剂选自硅烷、聚硅烷、硅烷水解物、聚硅氧烷、硅醇盐(siliconates)、硅酸盐(silicates)、钛酸盐、聚钛酸盐和锆酸盐,更特别是硅烷、硅烷水解物、聚硅氧烷和硅酸盐,及上述物质的混合物。上述基质形成剂反应生成相应的无机氧化物,更特别是硅的、钛的和/或锆的氧化物,气体腐蚀控制层形成中优选硅基试剂。根据一优选的实施方式,涂层组合物的基质形成剂经有机改性以生成氧阻隔层1。通常,用于生产氧阻隔层的涂层组合物的基质形成剂通过无机和/或有机基团的缩合反应和/或通过有机化学基团的聚合反应交联和/或固化。然而,如果基质形成剂通过无机基团的缩合反应交联和/或固化时是优选的。这样,能够获得特别耐用、气密的,特别是氧稳定的氧阻隔层。然而,对基质形成剂进行一定的小的有机改性是有利的,因为有机基团易于使涂层产生更多的柔韧性。因此在本发明的上下文中,如果基质形成剂通过有机基团改性是优选的。在这种情况下,优选有机基团选自烷基、芳基和烯烃基及其混合物,更特别是烷基和芳基基团及其混合物。如果用于生产气体腐蚀控制层的涂层组合物包含烷基基团,已经证明合适的烷基基团是c1-c10烷基基团,更特别是c1-c5烷基基团,优选c1-c3烷基基团,更优选c1和/或c2烷基基团。如果芳基基团是c6至c20芳基基团,更特别是c6至c15芳基基团,优选c6至c10的芳基基团时,同样是有利的。进一步也规定了烯烃基团是c2-c10烯烃基团,更特别是c2-c8的烯烃基团,优选c2-c5的烯烃基团,更优选c2和/或c3烯烃基团,最优选乙烯基团。然而,在本文的上下文中,已经证明特别有利的有机基团是甲基和/或乙基基团和/或甲苯基基团。在本发明的上下文中,如果基质形成剂选自通式i的硅烷,获得良好的结果。r4-nsixn(i)其中,r为烷基,更特别是c1-c5烷基,优选c1-c3烷基,更优选c1和/或c2烷基;芳基,更特别是c6-c20芳基,优选c6-c15芳基,更优选c6-c10芳基;烯烃基,更特别是端烯烃基,优选c2-c10烯烃基,更优选c2-c8烯烃基,极优选c2-c5烯烃基,特别优选c2和/或c3烯烃基,更特别优选乙烯基;胺,更特别是c2-c10胺,优选c2-c8胺,更优选c2-c5胺,非常优选c2和/或c3胺;羧酸,更特别是c2-c10羧酸,优选c2-c8羧酸,更优选c2-c5羧酸,非常优选c2和/或c3羧酸;醇,更特别是c2-c10的醇,优选c2-c8醇,更优选c2-c5醇,非常优选c2和/或c3的醇;x为卤化物,更特别是氯化物和/或溴化物;烷氧基,更特别是c1至c6烷氧基,非常优选c1至c4烷氧基,尤其优选c1和/或c2烷氧基;且n为1-4,优选2或3。在本文中,如果基质形成剂选自通式ia的硅烷,获得了良好的结果。r4-nsixn(ia)r为c1-c3烷基,特别是c1和/或c2烷基;c6-c15芳基,特别是c6-c10芳基;c2和/或c3烯烃,特别是乙烯基;x为烷氧基,特别是c1-c6烷氧基,更优选c1-c4烷氧基,非常优选c1和/或c2烷氧基;且n为2或3。涂层组合物的基质形成剂优选包含烷基硅烷、更特别是三烷氧基烷基硅烷、二烷氧基二烷基硅烷,和/或烷氧基三烷基硅烷,和/或芳基硅烷、更特别是三烷氧基芳基硅烷、二烷氧基二芳基硅烷和/或烷氧基三芳基硅烷。如果基质形成剂选自硅烷水解物、聚硅氧烷、特别是烷基聚硅氧烷,优选c1-c3烷基聚硅氧烷和/或c1-c3烷氧基烷基聚硅氧烷,和/或选自芳基聚硅氧烷,优选c6-c10芳基聚硅氧烷和c6-c10烷氧基芳基聚硅氧烷时,在本发明的上下文中获得了非常好的结果。如果基质形成剂的重均分子量mw的范围是200-200,000g/mol,更特别是500-150,000g/mol,优选1000-100,000g/mol,更优选2000-75,000g/mol,最优选5000-50,000g/mol时,在本发明中是优选的。在本文中,已经证明合适的是涂层组合物包含作为基质形成剂的烷氧基甲基硅树脂和/或烷氧基甲基苯基硅树脂。此外,规定了基质形成剂选自通式ii的钛酸盐。tix4(ii)其中,x为卤化物,更特别是氯化物和/或溴化物;烷氧基,特别是c1-c8烷氧基,优选c1-c6烷氧基,更优选c1-c4烷氧基。在本文中,如果基质形成剂选自通式iia的钛酸盐,已经证明是合适的tix4(iia)其中,x为烷氧基,特别是c1-c8烷氧基,优选c1-c6烷氧基,更优选c1-c4烷氧基。此外,同样规定了基质形成剂选自通式iii的锆酸盐:zrx4(iii)其中,x为卤化物,特别是氯化物和/或溴化物;烷氧基,特别是c1-c8烷氧基,优选c1-c6烷氧基,更优选c1-c4烷氧基。如果基质形成剂选自通式iiia的锆酸盐,此处获得了特别好的结果zrx4(iiia)其中,x为烷氧基,特别是c1-c8烷氧基,优选c1-c6烷氧基,更优选c1-c4烷氧基。此外,在本发明的上下文中,能够将硅醇盐用作基质形成剂。如果使用通式(iv)的硅醇盐,在这种情况下获得了特别好的结果:ho-[si(r)(om)-o-]nh(iv)其中n为1-6,特别是1-3,优选1;r为c1-c10烷基和/或c6-c15芳基,特别是c1-c8烷基和/或c6-c12芳基,优选c1-c6烷基和/或c6-c12芳基,更优选c1-c4烷基,非常优选c1-c3烷基;m为一价金属,特别是碱金属,优选钠或钾。在本文中,已经证明硅醇盐选自甲基硅醇钠、甲基硅醇钾、丙基硅醇钠和丙基硅醇钾是合适的。基质形成剂还可能选自聚硅酸盐,更特别是水玻璃,优选钠和/或钾的水玻璃,或磷酸二氢铝。利用上述基质形成剂,能够获得具有良好机械性能的完全无碳的基质。同样规定了基质形成剂选自硅石、二氧化钛和/或氧化锆,所述基质形成剂通常以粒子形式存在,特别是少量存在,以涂层组合物计,优选数量为0.1-10wt%,更优选1-5wt%。如果硅石、二氧化钛和/或氧化锆用作基质形成剂,涂层组合物通常包含至少一种另外的基质形成剂以确保涂层必要的结合。在本发明的上下文中,涂层组合物也可能包含多种不同的基质形成剂,更特别是反应性的基质形成剂。如果涂层组合物只包含硅基基质形成剂,在本文中获得了特别好的结果。根据本发明的一优选实施方式,涂层组合物包含金属粒子。因此,一种优选的涂层组合物包含:(a)至少一种无机基的基质形成剂,(b)金属粒子和(c)任选的辅料和添加剂。如果本发明的用于生产气体腐蚀控制层的涂层组合物包含金属粒子,其数量可在较宽范围内变化。然而,已经证明合适的是,以组合物计,第二涂层组合物包含至少1wt%,更特别是至少2wt%,优选至少5wt%的金属粒子。如果以组合物计,第二涂层组合物包含的金属粒子的百分数范围为1-50wt%,更特别是2-30wt%,优选5-20wt%,更优选5-15wt%时,也获得了特别好的结果。在本文中,特别规定了组合物包含片状和/或粒状的,更特别是球形金属粒子,优选片状金属粒子。更特别是如上所述的。如果组合物包含基于锌、铝和/或镁及其合金的片状金属粒子,优选片状铝粒子时,在本发明的上下文中获得了特别好的结果。通常,涂层组合物中的添加剂和/或辅料选自流变添加剂、防腐剂、稳定剂、酸和/或碱、表面活性剂、消泡剂组分、成膜剂、蜡、有机紫外吸收剂、活性生物源成分、流动控制剂、分散助剂、乳化剂、润湿剂、填料、ph值稳定剂和ph调节剂。在本发明的上下文中,进一步规定了组合物在高温和/或通过辐射射,优选高温交联和/或固化。如果组合物在高温交联,组合物交联和/或固化的温度,可在较宽范围内变化。然而,如果组合物固化和/交联的温度范围为10-250℃,优选15-150℃,更优选20-100℃时,获得了特别好的结果。在本发明的上下文中,因此能够提供在室温,更特别是在20-30℃温度范围固化和/或交联的体系。在室温固化和/或交联的体系具有的优点在于不需要特殊装置或设备来固化和/或交联涂层组合物。如果组合物在高温下交联和/或固化,那么组合物通常交联和/或固化的时间为1分钟到2小时,更特别是2分钟到1小时,优选3-30分钟,更优选4-20分钟,非常优选5-15分钟。然而,同样规定了组合物在室温固化和/或交联。如果考虑到待涂覆基底尺寸不能放入炉中或者通过辐射加热器加热时,该实施方式是特别有利的。同样能够节省大量的能源。如果组合物在室温交联和/或固化,那么组合物通常交联和/或固化的时间为1分钟到2小时,更特别是2分钟到1小时,优选3-45分钟,更优选5-30分钟。为了本发明的目的,在室温交联的水基涂层组合物优选用于气体腐蚀控制层的生产。根据本发明一特定的实施方式,用于生产气体腐蚀控制层的涂层组合物的固体百分数以组合物计为95-100wt%。根据该特定的实施方式,本发明的涂层组合物形成为无溶剂的或低溶剂的超高固体含量涂层组合物。以组合物计,固体含量95-100wt%的涂层组合物通常用暴露于大气湿度作为交联引发剂。正如上文已观察到的,在本发明的上下文中,固体含量95-100wt%的涂层组合物优选是液体形式并且其粘度与水基和/或溶剂基体系没有什么差异。然而,为了调节粘度,固体含量95-100wt%的涂层组合物可包含最高到5wt%的溶剂或水。在本发明的上下文中,已经发现合适的是,根据该特定的实施方式,以涂层组合物计,涂层组合物包含的基质形成剂的数量为50-100wt%,更特别是60-100wt%,优选70-95wt%,更优选75-90wt%。根据该实施方式,也规定了以涂层组合物计,涂层组合物包含至少5wt%,更特别是至少10wt%,优选至少15wt%的金属粒子。此外,以涂层组合物计,如果涂层组合物包含的金属粒子百分数范围为5-50wt%,更特别是10-30wt%,优选15-25wt%,根据该特定的实施方式,获得了良好的结果。关于本发明该方面的更多细节,可参照涉及本发明其他方面的观察,这相应地适用于本发明的用于生产气体腐蚀控制层的涂层组合物。根据本发明的第四方面,本发明还另外提供了一种用于在金属基底上生产高温腐蚀控制涂层的方法,其中,(a)在第一步中,将用于生产阴极腐蚀控制涂层的腐蚀控制涂层和/或涂层组合物涂覆到金属基底上,获得阴极腐蚀控制层,且(b)在随后的第二步中,将用于生产氧阻隔层的第二腐蚀控制涂层和/或涂层组合物涂覆到基底上,更特别是第一腐蚀控制层上,获得氧阻隔层。本发明的方法通常进行使得在方法步骤(a)中,腐蚀控制涂层和/或涂层组合物涂覆到基底上的层厚范围为0.1-180μm,更特别是0.5-150μm,优选1-140μm,更优选2-90μm,非常优选3-40μm。如果方法步骤(a)中的涂层组合物以锌片涂层的方式涂覆到基底上时,那么涂层通常的层厚范围是0.1-25μm,更特别是1-15μm,优选2-10μm,更优选4-8μm。为了本发明的目的,在方法步骤(a)中,金属锌层作为阴极腐蚀控制层特别是通过热浸镀锌或电镀锌涂覆到基底上。根据本发明的一优选实施方式,在方法步骤(a)中,包含金属粒子的第一涂层组合物,更特别是如上所述的,涂覆到基底上以产生阴极腐蚀控制层,并随后交联和/或固化。对于方法步骤(a)中实际的涂覆操作,可通过不同的方式进行。然而,在本发明的上下文中,已经证明有利的是,在方法步骤(a)中,腐蚀控制涂层和/或涂层组合物通过喷涂、浸渍、旋涂、浸渍-旋涂、刮涂或辊涂,更特别是通过喷涂、浸渍、旋涂或浸渍旋涂,优选喷涂的方式涂覆到基底上。非常杰出地喷涂特别适合较大的物体,而对于较小的物体,如螺纹件,优选浸渍-旋涂,因为浸渍-旋涂能使大量待涂覆的基底同时涂覆。在本发明的上下文中,规定了方法步骤(a)中的涂层组合物在室温固化或交联。如果涂层组合物在室温交联和/或固化,这通常在上述时间段内完成。然而,同样也可能方法步骤(a)中的涂层组合物在高温下和/或通过辐射交联和/或固化,优选在高温下。在本文中,已经证明有利的是,涂层组合物的交联和/或固化温度范围为30-350℃,优选50-300℃,更优选100-250℃,最优选150-200℃。如果涂层组合物在高温下交联和/或固化,这通常在上述时间段内完成。在本发明的上下文中,方法步骤(b)通常通过腐蚀控制涂层和/或涂层组合物涂覆到基底上来完成,层厚范围是0.1-60μm,更特别是0.5-50μm,优选0.7-35μm,更优选1-10μm,非常优选1-5μm,特别优选1-3μm。通常,本发明涂层的第二层层厚范围为0.1-50μm,更特别是0.5-40μm,优选0.7-30μm,更优选1-10μm,非常优选1-5μm,特别优选1-3μm。如果在方法步骤(b)中,涂层组合物,更特别是如上所述的,涂覆到基底上以产生气体腐蚀控制层,随后交联和/或固化时,获得了特别好的结果。通常在方法步骤(b)中,涂层通过氧阻隔涂层和/或涂层组合物经由喷涂、浸渍、旋涂、浸渍-旋涂、刮涂和辊涂,更特别是经由喷涂、浸渍、旋涂、浸渍-旋涂,优选经由喷涂被涂覆到基底上,更特别是阴极腐蚀控制层上来完成。为了本发明的目的,如果在方法步骤(b)中,涂层组合物在室温交联和/或固化是优选的。在本文中,交联和/或固化操作通常进行的时间为1分钟到2小时,更特别是1分钟到60分钟,优选3-45分钟,更优选5-30分钟。然而,为了本发明的目的,还规定了方法步骤(b)中的涂层组合物在高温下和/或通过辐射交联和/或固化,优选在高温下。如果方法步骤(b)中的涂层组合物在高温下交联和/或固化,那么通常温度范围为30-350℃,优选50-150℃,更优选40-200℃。此处优选的是,涂层组合物交联和/或固化的时间段为1分钟到2小时,更特别是2分钟到1小时,优选3-30分钟,更优选4-20分钟,非常优选5-15分钟。此外,在本发明的上下文中规定了待涂覆基底在先于方法步骤(a)的制备步骤中制备。在本文中,已经证明有利的是,基底被清洁,特别是通过去油脂来清洁。这可通过用如有机溶剂处理、喷砂、研磨、特别是使用酸和/或碱酸洗,优选通过用有机溶剂处理、喷砂和/或研磨。用有机溶剂处理、喷砂和/或研磨防止了用酸处理之后可发生的氢脆。根据本发明的一具体的实施方式,规定了可将粘合促进层涂覆到基底上,特别是在已经清洁基底之后,和在方法步骤(a)中涂覆阴极腐蚀控制涂层和/或涂层组合物之前。粘合促进层改善了本发明的涂层和基底之间的粘合,但也降低了阴极腐蚀控制层和基底之间的电接触。然而已经发现,在本发明的上下文中,可使用特定的粘合促进层或底漆,且没有观察到阴极腐蚀控制效果有任何降低。在本发明的上下文中,优选的是,粘合促进层通过用溶液处理基底而生成转换层的形式,所述溶液包含铬(iii)化合物、钛化合物和/或锆化合物。这种转换层是良好的粘合促进剂,且它们不降低阴极腐蚀控制,或者至少仅在较小程度上降低。粘合促进层也可通过磷酸化,更特别是铁磷酸化或锌磷酸化而产生。在本发明的上下文中,粘合促进层也可通过用硅酸盐基的预处理体系或适当的硅烷处理产生。对于本发明该方面的更多细节,可参照上述涉及本发明其他方面的观察,这同样相应地适用于本发明的方法。根据本发明的第五方面,本发明还进一步提供了一种涂覆基底,其包含有上述定义的涂层和任选的粘合促进层。对于本发明该方面的更多细节,可参照上述涉及本发明其他方面的观察,这同样相应地适用于本发明的涂覆基底。根据本发明的第六方面,本发明还进一步提供了氧阻隔涂层,更特别是如上所述的氧阻隔涂层,或氧阻隔涂层组合物在一部分阴极腐蚀控制涂层上获得高温抗性的用途。对于涉及本发明氧阻隔涂层用途的更多细节,可参照上述涉及本发明其他方面的观察,这同样相应地适用于本发明的用途。最后根据本发明的第七方面,本发明进一步提供了涂层组合物,更特别是氧阻隔涂层组合物,优选如上所述的涂层组合物,用于改善阴极腐蚀控制涂层的温度稳定性的用途。对于涉及本发明该方面的更多细节,可参照上述涉及本发明其他方面的观察,这同样相应地适用于本发明的用途。图1显示了具有本发明涂层1的金属基底2。本发明的涂层1由优选包含金属粒子,更特别是锌片的阴极腐蚀控制层3和优选包含铝片的氧阻隔层4组成。阴极腐蚀控制层3中的金属粒子优选镶嵌在基于有机改性的二氧化硅和二氧化钛的有机基基质中,同时气体腐蚀控制层4的铝片优选镶嵌在有机改性的二氧化硅保护层中,其具有以气体腐蚀控制层4的基质材料计,少于50wt%的碳含量。涂层1和基底2任选经由粘合促进层5连接。替代地或另外地,根据图1中未显示的实施方式,在阴极腐蚀控制层3和氧阻隔层4之间设置有另外的层,特别是具有粘合促进性能和/或氧阻隔性能。涂层1的多层结构特别降低了在加热和冷却操作中因热膨胀和收缩引起的开裂。本发明通过具体实施方式以非限制性的方式在下文中举例进行说明。具体实施方式对于下面的试验,将具有阴极腐蚀控制的涂覆体系涂覆到钢板和螺钉件上并研究它们的抗腐蚀性能,特别是在高温暴露之后。也研究了阴极腐蚀控制涂层(下面也称为底层)和氧阻隔涂层(下面也称为顶层)的不同组合,并与仅基于阴极腐蚀控制涂层的涂层体系进行比较。i底层下面说明了所研究的底层的组成,以及它们的涂覆和固化条件。也表明了没有预先加热时,根据dineniso9227的盐雾试验中可能发生红锈的时间点。实施例1:基于纯锌颜料的溶剂基锌片底漆涂覆:喷涂或浸渍-旋涂固化:热处理;200℃下30分钟干膜厚度:6-8μm表1底层1的组成粘合剂组分重量份数三甲氧基乙烯基硅烷9.8乙基己酸钛(四-2-乙基己基钛酸酯)24.9聚钛酸正丁酯(钛酸-四丁酯,聚合物)36.8醇14.5防沉剂11.4润湿和分散添加剂2.6粘合剂总计100.0锌片50.00红锈(小时,盐雾试验)2000实施例2:基于纯锌色素的液态锌片底漆涂覆:喷涂或浸渍-旋涂固化:热处理;200℃下30分钟干膜厚度:6-8μm表2:底层2的组成粘合剂组分重量份数二丙二醇(dpg)5.25环氧硅烷低聚物10.00乙氧基化异十三烷醇4.001-硝基丙烷0.75锌片(在丙二醇中)50.00软化水32.00正磷酸(0.1%溶液)3.50钠水玻璃(25%溶液)0.50钠磺基琥珀酸二辛酯(润湿添加剂)0.5聚醚硅氧烷共聚物(消泡剂)0.5黄原胶(增稠剂)3.00红锈(小时,盐雾试验)2000实施例3:基于锌铝颜料(4znal7)的溶剂基锌片底漆涂覆:喷涂或浸渍-旋涂固化:热处理;200℃下30分钟干膜厚度:6-8μm表3:底层3的组成粘合剂组分重量份数三甲氧基乙烯基硅烷9.8乙基己酸钛(四-2-乙基己基钛酸酯)24.9聚钛酸正丁酯(钛酸-四丁酯,聚合物)36.8醇14.5防沉剂11.4润湿和分散添加剂2.6粘合剂总计100.0锌片50红锈(小时,盐雾试验)2000实施例4基于锌铝颜料(4znal7)的含水锌片底漆涂覆:喷涂或浸渍-旋涂固化:热处理;200℃下30分钟干膜厚度:6-8μm表4:底层4的组成实施例5基于锌铋颜料(5wt%bi)的溶剂基锌片底漆涂覆:喷涂或浸渍-旋涂固化:热处理;200℃下30分钟干膜厚度:6-8μm表5:底层5的组成粘合剂组分重量百分数三甲氧基乙烯基硅烷9.80乙基己酸钛(四-2-乙基己基钛酸酯)24.90聚钛酸正丁酯(钛酸-四丁酯,聚合物)36.80醇14.50防沉剂11.40润湿分散添加剂2.60粘合剂总计100.00锌片50.00红锈(小时,盐雾试验)2000实施例6基于锌铋颜料(5wt%bi)的含水锌片底漆涂覆:喷涂或浸渍-旋涂固化:热处理;200℃下30分钟干膜厚度:6-8μm表6:底层6的组成实施例7基于锌铝镁颜料(znmg8al8)的溶剂基锌片底漆涂覆:喷涂或浸渍-旋涂固化:热处理;200℃下30分钟干膜厚度:6-8μm表7:底层7的组成粘合剂组分重量份数三甲氧基乙烯基硅烷9.80乙基己酸钛(四-2-乙基己基钛酸酯)24.90聚钛酸正丁酯(钛酸-四丁酯,聚合物)36.80醇14.50防沉剂11.40润湿分散添加剂2.60粘合剂总计100.00锌片50.00红锈(小时,盐雾试验)2000实施例8基于锌铝镁颜料(znmg8al8)的含水锌片底漆涂覆:喷涂或浸渍-旋涂固化:热处理;200℃下30分钟干膜厚度:6-8μm表8:底层8的组成粘合剂组分重量百分数二丙二醇(dpg)5.25环氧硅烷低聚物10.00乙氧基化异十三烷醇4.001-硝基丙烷0.75锌片(在丙二醇中)50.00软化水32.00正磷酸(0.1%溶液)3.50钠水玻璃(25%溶液)0.50钠磺基琥珀酸二辛酯(润湿添加剂)0.50聚醚硅氧烷共聚物(消泡剂)0.50黄原胶(增稠剂)3.00红锈(小时,盐雾试验)2000实施例9基于锌镁颜料(>5wt%mg)的溶剂基锌片底漆涂覆:喷涂或浸渍-旋涂固化:热处理;200℃下30分钟干膜厚度:6-8μm表9:底层9的组成实施例10基于锌铝镁颜料(>5wt%mg)的含水锌片底漆涂覆:喷涂或浸渍-旋涂固化:热处理;200℃下30分钟干膜厚度:6-8μm表10:底层10的组成粘合剂组分重量百分数二丙二醇(dpg)5.25环氧硅烷低聚物10.00乙氧基化异十三烷醇4.001-硝基丙烷0.75锌片(在丙二醇中)50.00软化水32.00正磷酸(0.1%溶液)3.50钠水玻璃(25%溶液)0.50钠磺基琥珀酸二辛酯(润湿添加剂)0.50聚醚硅氧烷共聚物(消泡剂)0.50黄原胶(增稠剂)3.00红锈(小时)2000实施例11按照wo2009/132102的实施例2的锌片底漆。表11:底层11的组成实施例12:根据wo2009/132102的实施例c1的锌片底漆实施例13:按照具有锌铝镁颜料的实施例12的锌片底漆表13:底层13的组成实施例14:电解镀锌基底锌层从酸性电解质中沉积到eg平坦钢上。涂覆锌的基底厚度为5mm。实施例15:热浸镀锌表面,具有10μm锌层厚度。ii.顶层下面的实施例具体说明了所用顶层的组成。实施例16-18:基于含水的硅氧烷分散质的顶层实施例16的顶层t16和实施例18的顶层18是透明层并不包含金属粒子。顶层16包含玻璃片。实施例17的顶层17包含铝颜料。表14:顶层t16-t18的组成实施例19如同us7645404实施例3的顶层将120g来自赢创(evonik)的mtes(烷基三烷氧基硅烷)和40g的四乙氧基硅烷与100g的1%三氟乙酸溶液混合,搅拌水解硅烷。然后加入150g的溶剂混合物(乙二醇丁醚),0.2g的disperbyk180(润湿分散剂)和35g的铝颜料。实施例20(顶层20)热浸镀铝,层厚5μm。iii.用途实施例实施例21:400℃加热48小时后的盐雾试验中的底层和顶层体系不同涂层涂覆到dco4钢板上,钢板已经进行了碱性脱脂并通过喷砂操作清洁。底层根据实施例1-15进行涂覆并干燥。顶层涂覆的干膜厚度为2-4μm并在室温干燥。随后,使用标记工具,在涂层中产生下压到钢板上的标记,然后这样制备的样品根据dineniso9227进行盐雾试验。表15概括了在盐雾试验中确定的标记处出现红锈的时间。表15:先经400℃温度暴露48小时以上后,于盐雾试验中针对不同的涂层体系在标记处发生红锈的时间(h)在另一形式的图像中,图2和图3显示了底层对阴极腐蚀控制效果的温度稳定性的影响,这根据表15是显而易见的。图2显示了钢板,具有根据实施例11的底层,即基于纯锌片材的锌片涂层,在24小时测试时段后根据dineniso9227进行盐雾测试。涂覆钢板经受400℃温度48小时以上。在盐雾测试24小时后,在标记处和在钢板表面中两者都已经明显有红锈大量形成。图3显示了具有根据实施例7的底层的钢板,即具有锌-铝-镁合金基片材的锌片涂层,在72小时测试时段后根据dineniso9227进行盐雾测试。涂覆钢板经受400℃温度48小时以上。仅仅在盐雾试验中72小时后,才在标记处以及涂覆钢板表面中红锈的起始区域存在显著形成的红锈。表中的数据和图2以及图3深刻地揭示了使用基于锌合金特别是锌-铝-镁合金的锌片,相对基于纯锌片材的锌片涂层,能够获得阴极腐蚀控制温度稳定性的显著改善。实施例22:针对不同温度的比较腐蚀测试将不同的底层体系如上所述涂覆到钢板上,并通过浸渍-旋涂涂覆到螺纹件上。干燥和固化的底层厚度为5-8μm。随后,一些基底接受顶层涂覆,涂覆层厚2-4μm,涂层体系暴露到高温下一定的时间。涂层的耐腐蚀性随后根据dineniso9227在带标记的盐雾测试中评估钢板,并根据dineniso9227,在没有标记的盐雾测试中评估螺纹件。基底的温度暴露为450℃下48小时以上,500℃下48小时以上,300℃下30天以上。比较腐蚀测试的结果显示在下面的表16中,在每种情况下都参照无顶层的体系。测试结果在表16中评估如下:+++所有高温下的三次测试中,盐雾测试中标记处形成红锈前的时间至少是仅涂覆有基于纯锌片涂层底层的基底时间的两倍。++高温下的两次测试中,盐雾测试中标记处形成红锈前的时间至少是仅涂覆有基于纯锌片涂层底层的基底时间的两倍。+高温下的一次测试中,盐雾测试中标记处形成红锈前的时间至少是仅涂覆有基于纯锌片涂层底层的基底时间的两倍。-在相对于基于纯锌片涂层的底层的盐雾测试中,腐蚀控制温度稳定性渐渐改善。--相对于基于纯锌片涂层的底层没有改善。表16:不同涂层体系参照各自的无顶层体系经三种不同的温度暴露的比较腐蚀测试实施例23:比较有氧阻隔层(顶层)和无氧阻隔层(顶层)的涂层体系a)螺纹件的涂层根据实施例7的底层通过浸渍-旋涂涂覆到钢制螺纹件上,干膜厚度为6-8μm。部分基底用根据实施例17的顶层组合物t17涂覆,包括铝颜料且层厚为2-4μm,室温干燥。涂覆的螺纹件在300-500℃高温暴露,抗腐蚀性通过后续的根据dineniso9227的无标记盐雾测试评价,结果如表17所示。表17:具有和不具有顶层的涂覆钢螺纹件的耐腐蚀性;在盐雾试验中红锈发生之前的时间(b)钢板的涂覆根据实施例7的底层涂覆到钢板上,干膜厚度为6-8μm。一些涂覆基底涂覆有根据实施例17的顶层组合物t17,层厚为2-4μm,在室温干燥。涂覆钢板暴露到300-500℃之间的高温,随后根据dineniso9227在带标记的盐雾测试中评估耐腐蚀性。结果汇总在下面的表18中。表18:具有和不具有顶层的涂覆钢板的耐腐蚀性;在红锈发生之前盐雾试验中的时间表16中列举的数值再次显示在图3到图6的图像形式中,用于示出在400-500℃温度暴露后的测量值。图3,如上所述,示出了具有根据实施例7底层的钢板,随后根据dineniso9227进行盐雾试验,测试时间72小时。在进行盐雾测试之前,涂覆的钢板暴露到400℃温度48小时以上。72小时后,在标记处以及涂覆钢板表面中红锈的起始区域清楚形成明显的红锈。图4显示了涂覆有根据实施例7的底层,以及涂覆有根据实施例17的顶层组成t17的钢板,随后根据dineniso9227进行盐雾试验,测试时间230小时以上。同样将涂覆的钢板暴露到400℃温度48小时以上。盐雾测试中超过230小时后,标记处存在明显的起始红锈,而在表面中还并不存在明显的红锈形成。图5显示了涂覆有根据实施例7底层的钢板,随后根据dineniso9227进行盐雾试验,测试时间72小时。钢板暴露到500℃的温度48小时以上。标记处和表面中都明显存在严重的红锈。图6最后显示了涂覆有根据实施例7的底层,以及涂覆有根据实施例17的顶层组合物t17的钢板,随后根据dineniso9227进行盐雾试验,测试时间230小时以上。将涂覆的钢板暴露到500℃温度48小时以上。如图7中所示,即使超过230小时后,盐雾测试中的标记处仅形成极轻微的红锈,而在表面中根本不存在红锈。表17和18中的测量数值以及图中的标示是深刻的证明,一方面,通过使用基于锌-铝-镁合金的锌片涂层,与基于纯锌的锌片涂层相比,获得了高温下显著改善的腐蚀控制,另一方面,通过氧阻隔涂层能够进一步大幅增加高温的腐蚀控制。令人意外的是,这不仅对钢板,而且对螺纹件都是真实的,其由于螺纹不成比例难以获得均匀的涂层并防止腐蚀。附图标记列表1、腐蚀控制涂层;4、氧阻隔层;2、基底;5、附着促进层;3、阴极腐蚀控制层。当前第1页12