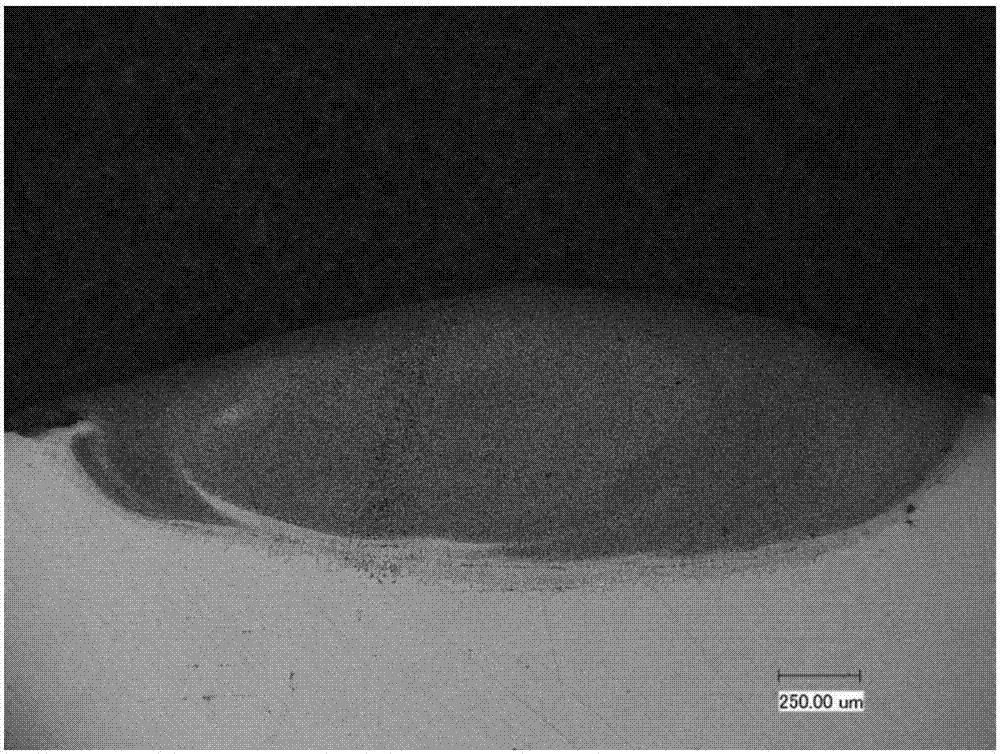
本发明涉及基体表面的激光应用领域,尤其涉及一种用于不锈钢表面铝基合金涂层及其制备方法。
背景技术:
:自304不锈钢可以被大量生产以来,304不锈钢已经大量广泛使用与汽车配件、医疗器具和船舶部件等方面。304不锈钢材具有良好的耐热耐腐蚀性,良好的机械性能,但是其硬度偏低,耐磨损性能较差,在在某些特殊材料的使用中,不锈钢材料表面总会出现凹坑、剥落等现象,严重影响材料的使用寿命,甚至会造成巨大的经济损失。对304不锈钢表面进行改性处理是目前比较理想的处理方法,尤其是激光熔覆技术,可以明显提高基体表面的硬度及磨损性能。在目前的激光熔覆合金粉末研究中,最主要的合金粉末主要有镍基合金粉末,铁基合金粉末以及钴基合金粉等。而对于铝基合金粉末的研究主要集中在铝合金板与镁合金板,中国知识产局公开了104250812铝合金表面的激光熔覆工艺,它的化学组成为60%-70%al,15%-25%ti,6%-8%fe,6%-12%b,上述成分配比为质量百分比。熔覆涂层生成了tib强化相,提高了基体的硬度与耐磨性能。其中铝粉的作用只是为了保证合金粉末与基体的热膨胀系数近似,使涂层与基体有良好的冶金结合性,但是合金粉末中能够生成金属间化和物元素含量较少,因此生成的金属间化和物强化相分布少,对基体的性能改善效果较差,可以考虑在保证熔覆层与基体形成良好冶金结合的同时生成较多的金属间化和物强化相,对于改善集体的各种性能有着巨大的效果。目前对于不锈钢基体采用铝基合金粉末的研究较少,中国知识产局公开了104141084激光熔覆用高熵合金粉末,采用等摩尔的fe,ni,cr,al,si和mn(0-1的摩尔比)在42crmo钢上进行激光熔覆,获得较良好的涂层,平均硬度值最高达到519.5hv,同时耐磨性较基体提高了3倍左右,但是该发明只是针对不锈钢基体的硬度与耐磨损性能,对其他如耐腐蚀性能和抗高温氧化性能等其它没有明显改善。技术实现要素:为了克服现有的技术不足,本发明为了提高熔覆层中生成的强化相的分布率,从而提高熔覆层的特征性能。在304不锈钢板上激光熔覆al-si-ti-ni的合金粉末,在熔覆涂层中形成feal、alti3、feni、tisi2金属间化合物,且分布均匀,提高基体的硬度与摩擦磨损性能,同时改善基体表面抗高温氧化性能与抗硫化性能。对于燃气涡轮发动机热部件表面与其它高温环境下的设备表面和硫化环境下的设备表面修复有着巨大的应用价值。为了实现上述目的,本发明采取的技术方案为:用于不锈钢表面铝基合金涂层的制备方法,包括如下步骤:(1)对不锈钢基材表面进行处理;可以为喷砂预粗化预处理后采用酒精清理干净。可以将不锈钢用al2o3喷砂处理,然后用酒精或其他清洗剂清除残留在变面的杂质与油污。(2)将铝基合金粉末混粉:将铝基合金粉末进行混粉得到混合好的合金粉末;所述合金粉末的成分重量百分比为:30-70%al,10-30%si,10-30%ti,10%ni;根据这四种粉末的比例不同,在熔覆过程中所形成的产物不同,当ti/al≥3时,易形成alti3金属间化合物,当al/ti=1时,易形成alti金属间化合物,当al/ti≥3,易形成al3ti金属间化合物。因此在熔覆涂层中,只要比例合适,可以形成较多的金属间化合物强化相,明显提高熔覆层的硬度和耐磨性能。优选的所述合金粉末的成分重量百分比为:40%-50%al,20%-30%si,10%-30%ti,10%ni,使用本发明的合金粉末在不锈钢合金基体进行激光熔覆会与基体中的铁等元素发生反应,可以生成较多的强化相,能明显改善基体的各项性能。采用10%的ni,含量与不锈钢基体的ni含量百分比相似,既可以使合金粉末的热膨胀系数与基体更相近,提高熔覆层的成型性能,同时提高ni含量可以提高其耐腐蚀性。因为本发明使用的粉末都为纯粉,因此需要将其进行混粉,时期成分均匀,在熔覆涂层中获得均匀的成分分布。(3)预制涂层:将粘结剂与步骤(2)中的混合好的合金粉末混合调和成糊状或膏状,预置在步骤(1)中进行过表面处理的不锈钢表面形成合金涂层,所述合金涂层的厚度为0.8-1.0mm;优选的,粘结剂与合金粉末的配比为3-7ml:9-14g。如果粘结剂量过低,这样不利于粉末均匀铺展在基体表面,如果粘结剂量过高,配成的混合物流动性强,铺展在基体表面的粉末均匀性差,因此要控制好比例,既能使混合物能铺展在基体表面,又能使它的均匀性由保障。(4)合金涂层烘干:将步骤(3)中合金涂层在80℃-100℃烘干形成预置层;(5)激光熔覆:将步骤(4)所得预置层在保护气氛下进行激光熔覆,使所述的预置层与不锈钢基材实现冶金结合,即得到用于不锈钢表面铝基合金涂层。其中,述步骤(2)中的合金粉末为250-350目的,各组分纯度均大于95%。其中,所述步骤(2)中的混粉方式为真空环境下间歇式混粉,每混粉30分钟,暂停10分钟,再进行混粉。可以采用行星式球磨机,采用间歇式混粉,转速250r/min,使用真空球磨罐抽真空,球料比为5:1,混粉时间共计2h。其中,所述步骤(3)中的粘结剂为二丙酮醇和醋酸纤维素反应而成的。其中,所述步骤(5)中保护气氛为氮气、氩气、氦气中的一种或几种,保护气气压是4mpa。其中,所述步骤(5)中激光熔覆中用的激光器采用光纤激光器。该激光器工作模式为多模,连续输出。本发明的激光熔覆工艺采用中高度的激光功率、较快的激光扫描速度,对基体表面进行激光快速熔覆,在基体表面形成的熔池较小并且热影响区较少,在基体表面上获得良好的激光熔覆涂层的同时,减少热影响区对基体的影响。其中,所述步骤(5)中的激光光斑直径为3mm,离焦量35mm。其中,所述步骤(5)中的激光功率分别为1400-1600w,扫描速度分别为550-650mm/min。上述制备方法制备的用于不锈钢表面铝基合金涂层。本发明的有益之处在于:本发明提供的涂层在提高不锈钢基体表面硬度与摩擦磨损性能的同时,改善基体表面抗高温氧化性能与抗硫化性能。本发明提供的制备方法工艺成本较低,易于生产。附图说明图1为实施例1-9中所用带防氧化装置的圆形坩埚。其中,1.保护气、2.进气口、3.坩埚、4.进气口。图2为实施例6的合金涂层的宏观形貌图。图3实施例6的合金涂层微观组织形貌的涂层顶部。图4实施例6的合金涂层微观组织形貌的涂层中部。图5实施例6的合金涂层微观组织形貌的涂层底部。图6为实施例6的xrd分析图。具体实施方式下面结合实施例,对本发明作进一步说明:以下实施例所用的材料参数如下:al(99.5%,300目),si(99.5%,300目),ti(99.5%,300目),ni(99.5%,200目)粘结剂:二丙酮醇和醋酸纤维素反应而成的醋酸纤维。(每200ml二丙酮醇混合8.5g乙酸纤维素,水浴加热温度到90℃进行反应,直到溶液中的乙酸纤维素反应完全为止。)实施例1:(1)将304不锈钢用al2o3喷砂处理,然后用酒精或其他清洗剂清除残留在变面的杂质与油污。(2)将铝基合金粉末混粉:将铝基合金粉末用可变速率行星式高能球磨机混粉,每混粉30分钟,暂停10分钟,再进行混粉,转速250r/min,使用真空球磨罐抽真空,球料比为5:1,混粉时间共计2h。铝基合金粉末各成分重量比为al:si:ti:ni=7:1:1:1,(3)预制涂层:将粘结剂与合金粉末按配比3-7ml:9-14g混合,然后预置在步骤(1)中进行过表面处理的不锈钢表面形成合金涂层,所述合金涂层的厚度为0.9mm;(4)合金涂层烘干:将步骤(3)中合金涂层放入80℃的烘箱4小时后取出,形成预置层。(5)激光熔覆:将有预置层的不锈钢放入自制的圆形坩埚中(如图1),坩埚槽两边通入保护气(ar),保护气气压是4mpa,激光熔覆,激光采用连续式光纤激光器,激光器的输出功率为1500w扫描线速度为600mm/min,激光器离焦量为35mm,激光器的光斑直径为3mm。实施例2:本实施例与实施例1基本相同,只有铝基合金粉末各成分重量比为al:si:ti:ni=6:1:2:1,与实施例1不同,同时其他实验条件不变。实施例3:本实施例与实施例1基本相同,只有铝基合金粉末各成分重量比为al:si:ti:ni=5:1:3:1,与实施例1不同,同时其他实验条件不变。实施例4:本实施例与实施例1基本相同,只有铝基合金粉末各成分重量比为al:si:ti:ni=6:2:1:1,与实施例1不同,同时其他实验条件不变。实施例5:本实施例与实施例1基本相同,只有铝基合金粉末各成分重量比为al:si:ti:ni=5:2:2:1,与实施例1不同,同时其他实验条件不变。实施例6:本实施例与实施例1基本相同,只有铝基合金粉末各成分重量比为al:si:ti:ni=4:2:3:1,与实施例1不同,同时其他实验条件不变。实施例7:本实施例与实施例1基本相同,只有铝基合金粉末各成分重量比为al:si:ti:ni=5:3:1:1,与实施例1不同,同时其他实验条件不变。实施例8:本实施例与实施例1基本相同,只有铝基合金粉末各成分重量比为al:si:ti:ni=4:3:2:1,与实施例1不同,同时其他实验条件不变。实施例9:本实施例与实施例1基本相同,只有铝基合金粉末各成分重量比为al:si:ti:ni=3:3:3:1,与实施例1不同,同时其他实验条件不变。经试验分析发现,实施例5-7的成分比例(40%-50%al,20%-30%si,10%-30%ti,10%ni)得到的熔覆涂层无明显裂纹,硬度值高,其中实施例6(40%al-20%si-30%ti-10%ni)达到的效果最好。对比例1铁基激光熔覆粉末及熔覆层制备方法:(1)将不锈钢喷砂处理,然后用酒精或其他清洗剂清除残留在变面的杂质与油污。(2)将铁基合金粉末混粉:将铁基合金粉末用研钵中机械研磨机混粉,优选组分含量为c为0.5-0.8%,cr为21-22%,ni为10-11%,al为10-10.5%,mo为5-5.5%,ceo2为1-1.2%,其余为fe。(3)在上述铁基激光熔覆粉末中,选用各个组分均为纯度大于等于99%的粉末,粒径为100-500目,优选200-300目,即铁粉、铬粉、镍粉、铝粉、钼粉、石墨粉、二氧化铈。(4)预制涂层:将粘结剂与合金粉末按质量百分比92-95%合金粉末与5-8%乙醇混合,然后预置在步骤(1)中进行过表面处理的不锈钢表面形成合金涂层,所述合金涂层的厚度为1-2mm;(5)激光熔覆:激光功率为1520-1650w,扫描线速度为150-220mm/min,激光器离焦量为0,激光器的光斑直径为0.8-1mm。对比例2激光熔覆用高熵合金粉末及熔覆层制备方法和用途:(1)将不锈钢喷砂处理,然后用酒精或其他清洗剂清除残留在变面的杂质与油污。(2)将高熵合金粉末粉末混粉:将高熵合金粉末用研钵中机械研磨机混粉,组分含量为激光熔覆用高熵合金粉末,由fe、ni、cr、al、si和mn元素粉末组成,即合金粉末组成表示为fenicralsimnx,x为mn的摩尔比且其取值范围为0-1,具体来说,所述fe、ni、cr、al、si之间为等摩尔比,调整金属mn的用量,以使其使用摩尔量与si(或者其余四种元素)的摩尔比为0-1,优选0.3-1,更加优选0.5-0.7。(3)在上述铁基激光熔覆粉末中,选用各个组分均为纯度大于等于99%的粉末,粒径为100-500目,优选200-300目。(4)预制涂层:将粘结剂与合金粉末按质量百分比92-95%合金粉末与5-8%乙醇混合,然后预置在步骤(1)中进行过表面处理的不锈钢表面形成合金涂层,所述合金涂层的厚度为1-2mm;(5)激光熔覆:激光功率为1520-1650w,扫描线速度为150-220mm/min,激光器离焦量为0,激光器的光斑直径为0.8-1mm。下面是对实施例1-9激光熔覆al-si-ti-ni涂层及对比例1、2进行组织结构分析与性能测试。1、组织与结构分析表1宏观形貌分析由图2所示实施例6的熔覆涂层与基体形成冶金结合。由图3-5为实施例6的合金涂层微观组织形貌的涂层顶部、涂层中部、涂层底部。涂层组织结构较为均匀,无明显气孔和裂纹。由图6所示实施例6的xrd分析图,分析发现涂层主要存在feal、alti3、feni、tisi2相,能有效提高集体的硬度与摩擦磨损性能,同时改善基体的抗高温氧化性能与抗硫化性能。2.显微硬度测试实施例1-9及对比例1、2的硬度分析如表2:表2实施例1-9硬度值比较由上表可以看出实施例中实施例6的最高硬度值与平均硬度值达到最高。3.高温抗氧化性能测试为了使抗高温氧化性能测试不受基底材料的影响,氧化试验涂层厚度约为0.6-0.8mm,用线切割方法将涂层与基底分离,氧化试验前涂层试样经超声波丙酮溶液清洗、烘干后用精度0.01mg电光分析天平称重,将试件装入灼烧恒重的氧化铝坩埚中,在800℃条件下利用静态增重法进行氧化试验,时间为80h。每10h称重一次,得出其单位面积氧化增重量,对比试样为无涂层的不锈钢。实施例1-9及对比例1、2的高温抗氧化性能测试分析如表3:表3800℃基体与熔覆涂层随时间变化氧化增重量(mg/cm2)10h20h30h50h80h基体15.1219.2825.3337.5245.19实施例19.2112.2615.3718.6921.33实施例27.6410.1513.5815.3817.58实施例37.1510.0313.4415.0717.44实施例46.289.9912.3514.6516.35实施例55.368.5611.9813.8615.98实施例65.088.0110.2512.93.15.25实施例75.888.6810.6613.3515.66实施例86.359.6211.0913.7916.09实施例97.5510.0312.6214.0116.62对比例111.3613.8817.6919.7322.65对比例27.3810.1613.6316.0117.314.抗硫化性能测试为了使抗高温氧化性能测试不受基底材料的影响,氧化试验涂层厚度约为0.6-0.8mm,用线切割方法将涂层与基底分离,氧化试验前涂层试样经超声波丙酮溶液清洗、烘干后用精度0.01mg电光分析天平称重。将样品放入600℃,0.01mpas(g)+n2的马弗炉中,同时开启硫加热套,对硫坩塥加热,开始反应计时。硫化结束时,取出样品测定样品的硫化增重量。实施例1-9及对比例1、2的抗硫化性能测试分析如表4:表4600℃0.01mpas(g)+n2基体与熔覆涂层随时间变化增重量(mg/cm2)10h20h40h50h基体8.5310.1212.6814.79实施例15.386.217.428.13实施例25.426.167.538.19实施例35.315.947.167.88实施例45.325.867.087.59实施例55.015.366.416.94实施例64.585.015.736.21实施例75.125.796.136.81实施例85.395.756.357.19实施例95.866.356.997.54对比例18.038.759.9910.54对比例27.317.869.2310.06以上所述的实施例对本发明的技术方案和有益效果进行了详细说明,应理解的是以上所述仅为本发明的具体实施例,并不用于限制本发明,凡在本发明的原则范围内所做的任何修改和改进等,均应包含在本发明的保护范围之内。当前第1页12