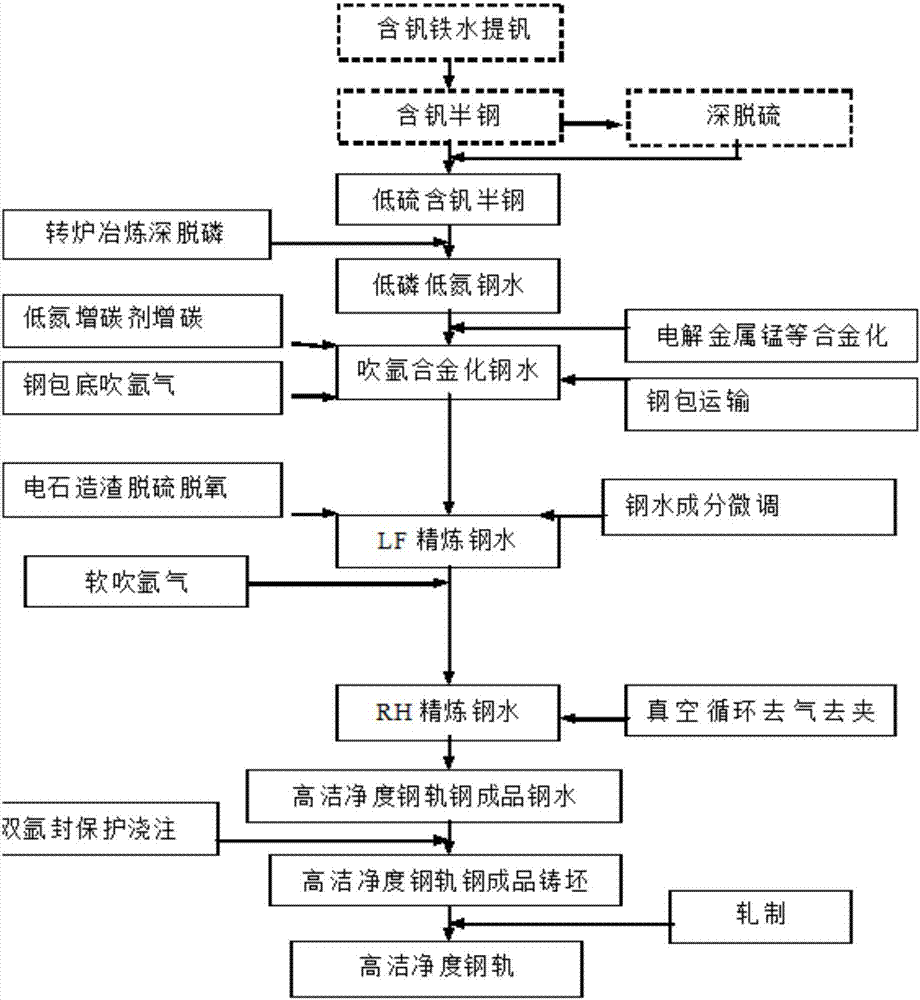
本发明属于冶金
技术领域:
,特别涉及一种以含钒钛铁水为原料生产高洁净度钢轨钢(成品杂质元素含量(P+S+O+N+H)≤0.0180%,非金属夹杂评级(A+B+C+D)总量≤2.5级)的控制方法。
背景技术:
:钢的洁净度是反映钢的总体质量水平的重要标志,是钢的内在质量的保证指标。重轨钢属于高碳钢,重轨钢连铸坯洁净度的要求包括气体含量、夹杂物控制和残留元素含量控制等方面。为了保证钢轨的使用性能,钢轨的标准中都对化学成分、气体含量和残留元素做了严格规定。提高重轨钢的洁净度可以增加重轨的耐磨和耐接触疲劳能力。重轨钢对钢的洁净度有较严格的要求,各种不同的钢轨制造标准也有明确的规定。控制钢中的磷和硫含量可以提高钢轨的强韧性。降低钢中氧含量能够显著改善钢轨的疲劳寿命。过高的氢含量易导致钢轨产生白点缺陷,造成应力集中,是钢轨疲劳断裂的主要因素。钢中存在的非金属夹杂物,尤其是Al2O3类不变形夹杂物,严重破坏钢基体的连续性,是钢轨裂纹源的主要产生因素。近年来,随着炉外精炼装备,技术和连铸工艺技术的不断进步,连铸钢水质量得到大幅度的提高,钢中夹杂总量明显减少,夹杂形态也得到了有效控制,目前国内外少数企业已能够生产出C、S、P、N、H、T[O]质量分数之和≤0.01%的超低碳纯净钢;而在中高碳钢轨钢的生产中,国内外所达到的质量水平:杂质元素含量(P+S+O+H+N)总量在0.022%~0.035%,非金属夹杂A+B+C+D)评级总量在2.5~4.5级。攀钢钢轨钢生产采用含钒钛铁水为主要原料,含钒铁水硫高、温低,同时为了保证钒资源的有效提取,通常进行铁水提钒处理,处理后的脱硫提钒半钢转炉冶炼,严重的热源不足制约转炉终点碳含量的控制(转炉终点钢水碳很难控制在0.15%以上),为满足钢轨钢碳成分要求(0.66%~0.82%),炉后钢水增碳剂用量高(1t左右),致使钢水增氮和空气吸氮情况严重。在已有技术中,脱硫含钒钛铁水或半钢生产钢轨钢的工艺和方法有一定的文献和专利报道,但涉及到一种脱硫含钒钛铁水或半钢为原料生产高洁净度钢轨钢控制方法在转炉炼钢工业生产中尚属先例;此方法不仅简单工艺顺行,同时有效控制钢中的有害杂质元素氮含量,大幅度提高钢的洁净度。为高纯净度高附加值钢轨钢生产提供了重要途径。技术实现要素:本发明要解决的技术问题是提供一种以含钒钛铁水为原料生产高洁净度钢轨钢的方法。以含钒钛铁水为原料生产高洁净度钢轨钢的方法,包括以下步骤:a、含钒钛铁水提钒后得到含钒半钢,再通过复合喷吹脱硫,获得碳含量为3.5%~4.0%,硫含量≤0.003%的低硫含钒半钢;b、将低硫含钒半钢兑入转炉吹炼,进行供氧造渣脱磷脱碳,底吹氩气,拉碳控制吹炼终点钢水[C]质量百分含量在0.06%~0.20%的范围,得到钢渣碱度为4.0~6.0,P含量≤0.006%、N含量≤0.0015%、S含量≤0.008%的低P低N钢水;c、将低P低N钢水出钢,控制出钢速度≤400kg/s,出钢过程中加入合金和增碳剂,钢包底吹氩气,得到吹氩合金化钢水;d、将吹氩合金化钢水通过LF炉进行电加热及成分微调处理,并向钢水内加入电石、活性白灰进行精炼,吹氩气,得到LF精炼钢水;e、获得的LF精炼钢水进入RH真空循环,底吹氩气,得到成品钢水。f、成品钢水通过双氩封保护浇注后,再通过轧制获得成品钢轨。优选的,步骤a中,喷吹的时间为20~35min;脱硫所用脱硫剂为石灰和钝化镁粉,其中石灰加入量为3.5~5.5kg/t铁水,钝化镁粉加入量为0.9~1.2kg/t铁水。优选的,步骤b中,底吹氩气在吹炼开始至拉碳期间氩气流量为7.0NL/(min·t),在拉碳至吹炼终点期间氩气流量为12.0NL/(min·t)。优选的,步骤b中,供氧造渣脱磷脱碳具体方法为,底吹氩气同时开始供氧,加入造渣剂,供氧时间650~720秒时停止供氧进行拉碳,拉碳后,再进行供氧,时间为60~180秒。其中,步骤b中,造渣剂为活性白灰、高镁石灰、硅石,其中活性白灰加入量为35~50Kg/t半钢,高镁石灰加入量为10~25Kg/t半钢,硅石加入量为8~10Kg/t半钢。优选的,步骤c中,增碳剂为高碳石墨增碳剂或石油焦增碳剂,其粒度为5~30mm,N含量<0.10%,P含量<0.10%,S含量<0.30%,固定碳含量>85%;合金为电解金属锰、硅铁,其中,电解金属锰其组分Mn含量>97%,P含量<0.05%,S含量<0.05%,N含量<0.05%,呈颗粒状,粒度为10~60mm;硅铁组分中Al含量72~80%,P≤0.5%,S≤0.04%,C≤0.02%,其粒度为10~60mm;钢包底吹氩气流量为2.0~3.5NL/(min·t)。优选的,步骤d中,加入电石的量为0.2~0.3kg/t钢水,加入活性石灰2~3kg/t钢水,电石和活性石灰分两次加入,第一次加入为总量的2/3,加入时间应间隔4~6min,精炼时间为14min~20min;氩气流量为0.5~1.5NL/(min·t);吹氩气时间>5min。优选的,步骤e中,氩气流量为10~12NL/(min·t),真空循环时间>14min,循环真空度在300Pa以内。优选的,步骤f中,双氩封保护浇注中,氩气流量为1.0~2.0NL/(min·t)。有益效果:本发明的目的克服了含钒铁水硫高、温低和提钒以及脱硫提钒后的半钢炼钢热源严重不足和成渣速度慢等缺陷。本工艺包括了含钒半钢深脱硫、钢水脱硫以及钢水回硫控制,钢水氮含量的控制,转炉深脱磷及合金增磷控制,钢水氧含量及非金属夹杂控制,该工艺不仅保证钒资源的有效利用和提取,同时能有效降低稳定控制钢种杂质元素含量和非金属夹杂,生产成品杂质元素总含量(P+S+O+N+H)≤0.0180%,非金属夹杂评级(A+B+C+D)总量≤2.5级高洁净度钢轨钢。本发明操作方法简单、设备投资小、生产成本低。附图说明图1为以含钒钛铁水为原料生产高洁净度钢轨钢的流程图。具体实施方式本发明要解决的技术问题是提供一种以含钒钛铁水为原料生产高洁净度钢轨钢的方法。以含钒钛铁水为原料生产高洁净度钢轨钢的方法,包括以下步骤:a、含钒钛铁水提钒后得到含钒半钢,再通过复合喷吹脱硫,获得碳含量为3.5%~4.0%,硫含量≤0.003%的低硫含钒半钢。b、将低硫含钒半钢兑入转炉吹炼,进行供氧造渣脱磷脱碳,底吹氩气,拉碳控制吹炼终点钢水[C]质量百分含量在0.06%~0.20%的范围,得到钢渣碱度为4.0~6.0,P含量≤0.006%、N含量≤0.0015%、S含量≤0.008%的低P低N钢水。c、将低P低N钢水出钢,控制出钢速度≤400kg/s,出钢过程中加入合金和增碳剂,钢包底吹氩气,得到吹氩合金化钢水。控制出钢速度以及采用钢包底吹氩气是为了减少空气吸氮,使出钢过程钢水增氮量控制在0.0008%以内。d、将吹氩合金化钢水通过LF炉进行电加热及成分微调处理,并向钢水内加入电石、活性白灰进行精炼,吹氩气,得到LF精炼钢水。LF精炼炉通过电石造渣工艺和软吹氩气,使钢包渣的(FeO+MnO)质量百分含量控制在2.0%以内,钢水中的全氧含量控制在0.0040%以内;通过LF精炼炉电石造渣还原,将钢水中的[S]质量百分含量控制在了0.005%以内。e、获得的LF精炼钢水进入RH真空循环,底吹氩气,得到成品钢水。通过RH精炼真空循环,去氢气并使非金属夹杂(包括硫化物夹杂和氧化物夹杂)聚集充分上浮,使成品钢中全氧含量控制在0.0008%以内,H含量小于0.0002%,非金属夹杂物颗粒小于30μm,非金属夹杂通过标准(GB/T10561)评级(A+B+C+D)总量≤2.5级。f、成品钢水通过双氩封保护浇注后,再通过轧制获得成品钢轨。在上述步骤e、f中,RH真空精炼可以降低氮气,在保护浇注过程采用双氩封控制空气吸氮,使成品氮含量控制在0.0030%以内。优选的,步骤a中,喷吹的时间为20~35min;脱硫所用脱硫剂为石灰和钝化镁粉,其中石灰加入量为3.5~5.5kg/t铁水,钝化镁粉加入量为0.9~1.2kg/t铁水。优选的,步骤b中,底吹氩气在吹炼开始至拉碳期间氩气流量为7.0NL/(min·t),在拉碳至吹炼终点期间氩气流量为12.0NL/(min·t)。优选的,步骤b中,供氧造渣脱磷脱碳具体方法为,底吹氩气同时开始供氧,加入造渣剂,供氧时间650~720秒时停止供氧进行拉碳,拉碳后,再进行供氧,时间为60~180秒。其中,步骤b中,为了使转炉冶炼回硫量控制在0.005%以内,采用大渣量单渣造渣,造渣剂为活性白灰、高镁石灰、硅石,其中活性白灰加入量为35~50Kg/t半钢,高镁石灰加入量为10~25Kg/t半钢,硅石加入量为8~10Kg/t半钢。优选的,步骤c中,为了减少炉后增碳,增碳剂选用低氮含量增碳剂,增碳剂为高碳石墨增碳剂或石油焦增碳剂,其粒度为5~30mm,N含量<0.10%,P含量<0.10%,S含量<0.30%,固定碳含量>85%;为了减少合金增磷,使合金对钢水增P量控制在0.001%以内,钢水合金化采用低P低S含量合金,对于钢水[Mn]采用电解金属锰合金化,钢水[Si]采用硅铁合金化,其中,电解金属锰其组分Mn含量>97%,P含量<0.05%,S含量<0.05%,N含量<0.05%,呈颗粒状,粒度为10~60mm;硅铁(硅铁满足GB2272中的FeSi75Al0.5-B要求)组分Al含量72~80%,P≤0.5%,S≤0.04%,C≤0.02%,其粒度为10~60mm;钢包底吹氩气流量为2.0~3.5NL/(min·t)。优选的,步骤d中,加入电石的量为0.2~0.3kg/t钢水,加入活性石灰2~3kg/t钢水,电石和活性石灰分两次加入,第一次加入为总量的2/3,加入时间应间隔4~6min,精炼时间为14min~20min,使钢包渣中(FeO+MnO)质量百分含量控制在2.0%以内;控制氩气流量为0.5~1.5NL/(min·t);吹氩气时间>5min。优选的,步骤e中,氩气流量为10~12NL/(min·t),真空循环时间>14min,循环真空度在300Pa以内。优选的,步骤f中,双氩封保护浇注中,氩气流量为1.0~2.0NL/(min·t)。下面结合实施例对本发明的具体实施方式做进一步的描述,并不因此将本发明限制在所述的实施例范围之中。实施例1含钒钛铁水以常规技术手段提钒得到含钒半钢,本发明以攀钢含钒半钢为原料,生产U75V钢轨钢,含钒半钢原料主要成分见表1,通过复合喷吹深脱硫,其喷吹时间为28.33min,脱硫剂石灰单耗为4.50kg/t铁水,脱硫剂钝化镁粉单耗为0.9kg/t铁水,脱后获得低硫含钒半钢,其主要成分见表2。将制取的半钢兑入攀钢120t复吹炼钢转炉吹炼,兑入量为138t,并采用535氧枪进行供氧造渣脱磷脱碳,在开始吹氧的同时,转炉底部采用流量为7.0NL/(min·t)的氩气进行底吹,进行炼钢造渣,向炉内加入造渣材料活性石灰、硅石以及高镁石灰,并在开吹供氧至拉碳内将造渣材料全部加完,造渣材料活性石灰、硅石以及高镁石灰以及炼钢污泥球的加入量分别为38Kg/t半钢、8Kg/t半钢、22Kg/t半钢;供氧时间680秒时停止供氧提升氧枪进行拉碳,并将转炉底吹氩气流量切换至12.0NL/(min·t),再进行补吹氧气冶炼,总供氧时间在760s停止供氧提升氧枪,获得温度为1676℃的钢水;转炉终点钢水的主要成分见表3;然后进行当渣出炉,出钢速度为300kg/秒,在出钢过程中加合金和增碳剂进行钢水合金化和增碳,对钢水中[Mn]采用电解金属锰合金化,钢水[Si]采用硅铁合金化;增碳剂成分见表9,电解金属锰合金成分指标见表10;脱氧合金化的钢水进行钢包底吹氩气,吹氩时间5min,氩气流量2.75NL/(min·t),脱氧合金化及吹氩后的钢水成分见表4。将脱氧合金化及吹氩后的钢水通过LF炉电加热及成分微调处理,在处理的同时,向钢包内分两次外加电石和活性石灰,第一次加入电石0.15(kg/t钢水),加入活性石灰2(kg/t钢水),间隔5min后向钢包内外加第二批电石和活性石灰,加入电石0.05(kg/t钢水),加入活性石灰1(kg/t钢水),精炼14.5min后,按流量为1.08NL/(min·t)的氩气进行软吹;软吹时间7min后获得LF精炼钢水和钢包渣;LF精炼钢水见表5,钢包渣的主要成分见表6。获得的LF精炼钢水进入RH真空循环,去气去夹杂,提升气体氩气流量为10.08NL/(min·t);循环真空度280Pa,真空循环时间,16min后获得成品钢水。成品钢水的成分见表7。获得成品钢水通过双氩封保护浇注后(氩气流量为1.67NL/(min·t)),获得浇注钢坯;浇注钢坯通过轧制获得成品钢轨;钢轨的非金属夹杂评级见表8。实施例2含钒钛铁水以常规技术手段提钒得到含钒半钢,本发明以攀钢含钒半钢为原料,生产U75V钢轨钢,含钒半钢原料主要成分见表1,通过复合喷吹深脱硫,其喷吹时间为21.07min,脱硫剂石灰单耗为3.50kg/t铁水,脱硫剂钝化镁粉单耗为0.9kg/t铁水,脱后获得低硫含钒半钢,其主要成分见表2。将制取的半钢兑入攀钢120t复吹炼钢转炉吹炼,兑入量为138t,并采用535氧枪进行供氧造渣脱磷脱碳,在开始吹氧的同时,转炉底部采用流量为7.0NL/(min·t)的氩气进行底吹,进行炼钢造渣,向炉内加入造渣材料活性石灰、硅石以及高镁石灰,并在开吹供氧至拉碳内将造渣材料全部加完,造渣材料活性石灰、硅石以及高镁石灰以及炼钢污泥球的加入量分别为50Kg/t半钢、10Kg/t半钢、10Kg/t半钢;供氧时间660秒时停止供氧提升氧枪进行拉碳,并将转炉底吹氩气流量切换至12NL/(min·t),再进行补吹氧气冶炼,总供氧时间在840s停止供氧提升氧枪,获得温度为1683℃的钢水;转炉终点钢水的主要成分见表3;然后进行当渣出炉,出钢速度为360kg/秒,在出钢过程中加合金和增碳剂进行钢水合金化和增碳,对钢水中[Mn]采用电解金属锰合金化,钢水[Si]采用硅铁合金化;增碳剂成分见表9,电解金属锰合金成分指标见表10;脱氧合金化的钢水进行钢包底吹氩气,吹氩时间8min,氩气流量3.0NL/(min·t),脱氧合金化及吹氩后的钢水成分见表4。将脱氧合金化及吹氩后的钢水通过LF炉电加热及成分微调处理,在处理的同时,向钢包内分两次外加电石和活性石灰,第一次加入电石0.2(kg/t钢水),加入活性石灰1.5(kg/t钢水),间隔4min后向钢包内外加第二批电石和活性石灰,加入电石0.1(kg/t钢水),加入活性石灰0.5(kg/t钢水),精炼20min后,按流量为1.33NL/(min·t)的氩气进行软吹;软吹时间8min后获得LF精炼钢水和钢包渣;LF精炼钢水见表5,钢包渣的主要成分见表6。获得的LF精炼钢水进入RH真空循环,去气去夹杂,提升气体氩气流量为11.7NL/(min·t);循环真空度250Pa,真空循环时间,15min后获得成品钢水。成品钢水的成分见表7。获得成品钢水通过双氩封保护浇注后(氩气流量为2.0NL/(min·t)),获得浇注钢坯;浇注钢坯通过轧制获得成品钢轨;钢轨的非金属夹杂评级见表8。实施例3含钒钛铁水以常规技术手段提钒得到含钒半钢,本发明以攀钢含钒半钢为原料,生产U75V钢轨钢,含钒半钢原料主要成分见表1,通过复合喷吹深脱硫,其喷吹时间为34.6min,脱硫剂石灰单耗为5.50kg/t铁水,脱硫剂钝化镁粉单耗为1.2kg/t铁水,脱后获得低硫含钒半钢,其主要成分见表2。将制取的半钢兑入攀钢120t复吹炼钢转炉吹炼,兑入量为140t,并采用535氧枪进行供氧造渣脱磷脱碳,在开始吹氧的同时,转炉底部采用流量为7.0NL/(min·t)的氩气进行底吹,进行炼钢造渣,向炉内加入造渣材料活性石灰、硅石以及高镁石灰,并在开吹供氧至拉碳内将造渣材料全部加完,造渣材料活性石灰、硅石以及高镁石灰以及炼钢污泥球的加入量分别为35Kg/t半钢、25Kg/t半钢、9Kg/t半钢;供氧时间720秒时停止供氧提升氧枪进行拉碳,并将转炉底吹氩气流量切换至12NL/(min·t),再进行补吹氧气冶炼,总供氧时间在780s停止供氧提升氧枪,获得温度为1680℃的钢水;转炉终点钢水的主要成分见表3;然后进行当渣出炉,出钢速度为340kg/秒,在出钢过程中加合金和增碳剂进行钢水合金化和增碳,对钢水中[Mn]采用电解金属锰合金化,钢水[Si]采用硅铁合金化;增碳剂成分见表9,电解金属锰合金成分指标见表10;脱氧合金化的钢水进行钢包底吹氩气,吹氩时间9min,氩气流量2.08NL/(min·t),脱氧合金化及吹氩后的钢水成分见表4。将脱氧合金化及吹氩后的钢水通过LF炉电加热及成分微调处理,在处理的同时,向钢包内分两次外加电石和活性石灰,第一次加入电石0.1(kg/t钢水),加入活性石灰1.8(kg/t钢水),间隔4min后向钢包内外加第二批电石和活性石灰,加入电石0.05(kg/t钢水),加入活性石灰0.7(kg/t钢水),精炼14min后,按流量为0.75NL/(min·t)的氩气进行软吹;软吹时间6.5min后获得LF精炼钢水和钢包渣;LF精炼钢水见表5,钢包渣的主要成分见表6。获得的LF精炼钢水进入RH真空循环,去气去夹杂,提升气体氩气流量为10.83NL/(min·t);循环真空度200Pa,真空循环时间,16.5min后获得成品钢水。成品钢水的成分见表7。获得成品钢水通过双氩封保护浇注后(氩气流量为1.33NL/(min·t)),获得浇注钢坯;浇注钢坯通过轧制获得成品钢轨;钢轨的非金属夹杂评级见表8。表1含钒半钢成分表2脱硫含钒半钢成分表3转炉终点钢水成分表4脱氧合金化及吹氩后钢水表5LF精炼钢水成分表6钢包渣的主要成分名称CaOFeOMnOSiO2实施例161.690.8360.17121.51实施例253.440.90.14626.22实施例360.671.220.18121.52表7成品钢水成分表8非金属夹杂评级名称ABCDDs实施例11.00.5000实施例21.5000.50实施例31.50000表9低氮增碳剂指标表10电解金属锰指标组元Mn/%P/%S/%Fe/%N/%粒度/mm实际97.1<0.0100.0430.870.0410~60当前第1页1 2 3