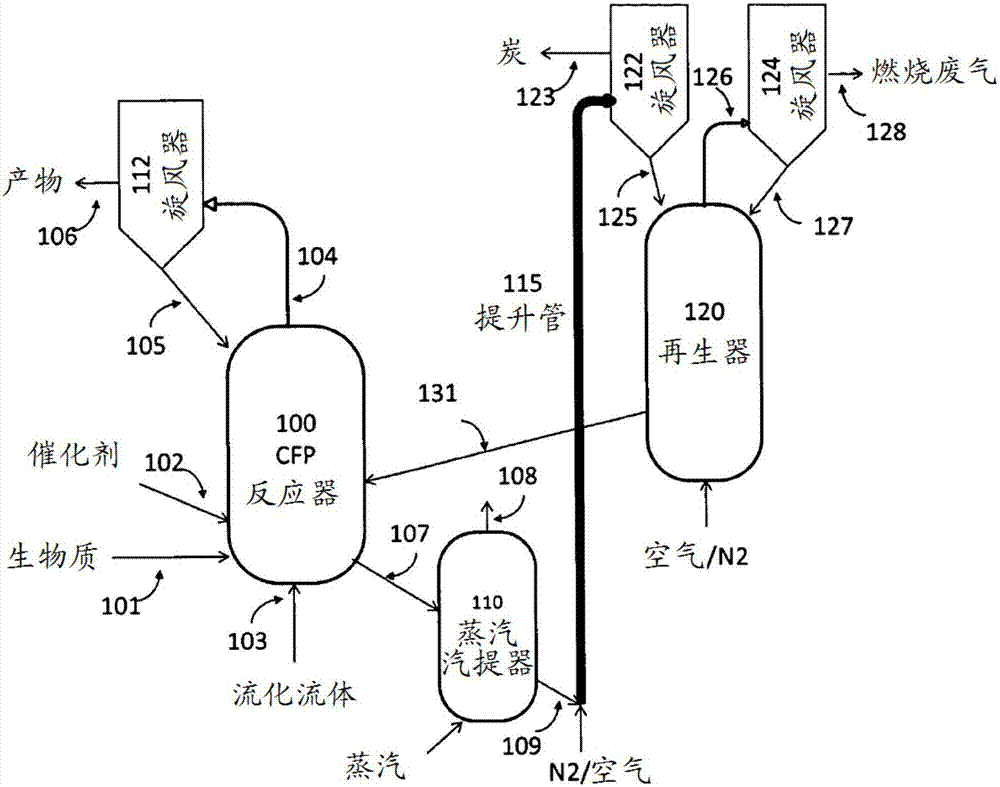
相关申请本申请要求2014年11月17日提交的美国临时专利申请第62/080938号的优先权益。发明背景从可再生生物质获得有用化学品、燃料和能量代表了一个重要挑战,因为这些材料的常规化石来源慢慢地被耗尽。木质纤维素生物质因其低成本和全球可用性而正被广泛研究作为可再生液体生物燃料和化学品的可行原料。生物质衍生的燃料和化学品据计划可同样大体上减少净co2排放(如果产生的话),最少地使用化石燃料。为了迎接这个挑战,进行大量尝试以将生物质转化为燃料和其它有用化学品。归因于原料和产物的性质,从生物质制备燃料和化学品需要不同于常规基于石油的转化过程的专门转化过程。进料的高温、固体进料、高浓度水、高氧气含量、不寻常分离和氧化副产物是生物质转化的不同于石油升级中遇到的那些的一些特征。因此,必须克服许多挑战以便有效地从生物质制备化学品。生物质材料通常包含木质素、纤维素和半纤维素作为主要组分,多种次要有机材料,水,和一些矿物元素。可以使一系列生物质衍生的材料热解以产生芳香族化合物、烯烃、co、co2、水、炭、焦炭和其它产物的混合物。热解的特别合乎需要的形式被称为催化快速热解(cfp),其涉及在催化流化床反应器中转化生物质以产生芳香族化合物、烯烃和多种其它材料的混合物。芳香族化合物包括苯、甲苯、二甲苯(统称为btx)和萘以及其它芳香族化合物。烯烃包括乙烯、丙烯和较少量的更高分子量烯烃。btx芳香族化合物具有高价值并且容易运输。来自cfp过程的原始流出物是包含芳香族化合物、烯烃、含氧化合物、石蜡、h2、ch4、co、co2、水、炭、灰分、焦炭、催化剂细粉和其它材料的复杂混合物。由这种复杂混合物分离、回收和纯化各种组分呈现出未曾令人满意地解决的挑战。一个特别令人烦恼的问题是在固体催化剂存在下产生大量的固体炭。炭是应用于已经在燃烧或热解过程中部分转化的富含碳的固体材料的术语。在用过的cfp催化剂的再生中,炭的存在增加了所需要的再生器的尺寸和所释放的热量的量,增加成本并且可能损害cfp催化剂;因此,分离和去除炭提供了过程和成本优势。此外,炭中存在的碳和其它材料代表了生物质原料的价值的相当大一部分,因此已经对回收所述价值的方法进行了研究。chieky等人在美国专利申请20140073708中描述了一种将生物质转化为产物的方法,其产生挥发性和非挥发性部分,并且非挥发性部分可以包括炭。挥发性部分可以包括烯烃和燃料(如煤油),并且一部分可以经过进一步加工以增加芳香族化合物。stamires和o'connor在美国专利申请20140007499中描述了一种制备生物油的方法,其中从汽提器获得的软焦炭用以预处理进入催化热解反应器的生物质进料。lissianski等人在美国专利申请20120024843中描述了一种方法,其中用微波能量加热碳质材料以产生包含炭、油和气体的混合物。混合物的分离可以在安置在反应器下游的旋风器中进行。所分离的炭然后可以传送到热回收单元。从热回收单元回收的热量然后可以再循环到预加热器。所分离的炭可以部分燃烧并且返回到反应器以供应热量用于处理碳质材料。或者,从热回收单元抽取的炭可以进一步经历如炭气化的处理。还提出了,炭还可以用作肥料—尤其当原料由大量的生物质组成时。raman等人在wo/2009/111345中陈述了,生物质炭可以通过向燃烧和/或气化反应器提供生物质微粒来产生。此类反应器可以集成到一个催化气化过程中。举例来说,在一个集成过程中,生物质微粒可以提供到与水源接触以便产生蒸汽的燃烧反应器;此类蒸汽可以完全或部分提供到催化气化反应器,并且于其中产生的生物质炭可以被提取并且用于制备用于催化气化反应器的微粒组合物。生物质炭的粒度可以通过以下方式减小:用水淬灭热生物质炭,以使得炭中由快速温度变化诱导的应力导致炭粉碎成较小颗粒并且产生浆液。palmas等人在美国专利第8,499,702号中描述了一种热解碳质生物质原料的方法,其产生热解产物和用过的传热介质。用过的传热介质分离成分离的炭和炭耗尽的用过的传热介质。分离的炭用来自密流化床的传热介质在再热器外部在含氧再生气体中燃烧。炭耗尽的用过的传热介质在足以使残余炭燃烧的条件下进入再热器中的含氧再生气流。燃烧使密床材料(即传热介质)的温度升高到热解反应器中所需要的操作条件,即约300℃到约900℃。jadhav在us8,404,909中描述了一种方法,其中包括炭的固体和包括金属氧化物吸附剂的热能载体颗粒从气相分离并且传递到炭燃烧器。炭和还原的热能载体颗粒的物料流供应到炭燃烧器。此外,包括氧化的金属氧化物吸附剂的热能载体颗粒的供料流供应到炭燃烧器。在炭在炭燃烧器中燃烧之后,一部分经加热的还原的金属氧化物吸附剂通过物料流传递到氧化反应器。一部分热能载体颗粒从炭燃烧器接收并且传递到热解反应器,以此方式,热量可以从炭燃烧器传送到热解反应器。炭从催化快速热解过程的分离和其后续加工并非生物质升级工业中的确定方法。尽管有这些和其它现有尝试,但仍需要改进的方法,其用于回收、分离作为催化热解过程的产物流出物的一部分产生的炭和从其获取价值,以便使得所述过程更能量有效、减小催化剂再生器的尺寸和热负荷、去除具有炭的矿物、选择性去除因磨损产生的催化剂细粉和延长催化剂的寿命。发明概要本发明提供了对cfp过程的改进和新颖炭组合物。在第一方面,本发明提供了一种制备芳香族化学品或烯烃的方法,其包括:使固体生物质在反应区中在催化剂存在下反应;产生从所述反应区离开的产物流;从所述反应区取出固体混合物;其中所述移出的固体混合物与所述产物流分开;在催化剂再生步骤之前,从所述固体混合物分离至少一部分炭;任选地将一部分所述分离的炭添加到所述反应区;其中所述炭在所述反应区之前不与生物质混合;和从所述产物混合物回收芳香族化合物或烯烃。在一些优选实施方案中,芳香族化合物被回收,并且所述回收的芳香族化合物以所述生物质中的碳计包含至少10%、优选至少15%产率的量的苯、甲苯和二甲苯,其中所述产率是所述苯、甲苯和二甲苯中的碳的总和除以生物质进料中的碳乘以100%。在这种方法中,原始产物流主要(以质量计)是气态有机化合物、co、co2和水,通常大于90%或至少95%气体具有微量的夹带固体。在一些优选实施方案中,本发明方法可以进一步特征为以下中的一者或任何组合:·其中分离在旋风器或系列旋风器中进行;·其中分离在一系列旋风器中进行,其中进入用以分离炭的每个后续旋风器的材料的线速度不小于进入所述系列旋风器中的前一旋风器的材料的线速度;·其中炭通过淘析与催化剂分离;·其中炭通过固体浮选从催化剂与炭混合物分离,优选包含气体和固体颗粒的鼓泡床;·其中炭通过筛、一组具有各种孔口的筛或另一尺寸排阻装置从催化剂与炭混合物分离,其中固体的分离基于粒度差异进行;·其中至少一部分所述炭在其与其它固体分离之前被粉碎(这个步骤将使得炭颗粒更小并且因此更容易将炭与催化剂分离);·其中至少一部分所述炭在输送管中,任选地通过沿着其长度具有不均匀内部横截面的输送管被粉碎;·其中至少一部分所述炭在包括静态混合器的输送管中被粉碎;至少一部分所述炭通过撞击表面或装置被粉碎,其中颗粒流以与平行成至少45度的攻角冲击所述表面;·其中一部分所述炭通过静电分离从所述固体混合物分离;·用大于使所述炭完全转化为二氧化碳和水所需的最小量的过量氧气燃烧;·其中热量从所述炭的燃烧回收并且转移到催化生物质转化反应器;·其中热量从所述炭的燃烧回收并且用以产生蒸汽;·其中炭燃烧过程在至少700c或至少800c或至少900c或至少1000c或700c到1300c或800到1200c的温度下操作;·其中所述催化剂包含沸石,并且其中所述催化剂再生在低于750c或低于700c或低于650c或低于625c或550c到750c或575c到700c或600c到650c的温度下操作;·其中所述催化剂包含至少10重量%zsm-5;·其中从所述反应区取出的所述固体混合物是催化剂和炭的混合物,并且所述催化剂与炭混合物在蒸汽汽提器中被汽提;·其中所述蒸汽汽提器的温度可以在100到700c或250到650c或400到625c或500到600c范围内,或可以是至少100c或至少250c或至少400c或至少500c或低于700c或低于650c或低于600c;·从所述产物回收烯烃;·利用所述炭发电;·其中至少一部分所述炭进行化学反应并且一部分所述反应的炭返回到所述催化生物质反应器;·其中至少一部分所述炭在其返回到所述催化生物质反应器之前被氧化(这个步骤是有利的,因为氧化的炭与未氧化的炭相比导致btx产率更高),优选地,在炭处理过程中所述添加的氧化剂中的氧原子与所述炭中的碳原子的比率(o/c比率)小于1.5、小于1.0、小于0.8、小于0.5或小于0.25,或是0.01到1.5或0.05到1.0或0.1到0.8或0.15到0.5;·其中所述炭通过与臭氧、氧气、稀空气、过氧化氢、过乙酸(ch3c(o)ooh)、过甲酸(hc(o)ooh)、异丁基过氧化物、no2、no或其它气态或液体氧化剂反应而部分氧化;·其中在炭的氧化中,所述氧化剂中的氧与所述炭中的碳比率(o/c比率)在炭处理过程中小于1.5、小于1.0、小于0.8、小于0.5或小于0.25,或是0.01到1.5或0.05到1.0或0.1到0.8或0.15到0.5;·其中炭处理导致产物与新鲜制得的炭相比具有增加的氧含量或更高o/c比率;·其中如通过对固体产物、液体产物或固体和液体两种产物进行红外光谱法所测量,炭处理的产物展示了碳氧单键和碳氧双键的含量的增加;·其中至少一部分所述炭在蒸汽汽提器中被汽提;·其中所述炭经酸性溶液处理;优选所述酸性溶液包含乙酸、甲酸、硝酸、硫酸、丙酸或碳酸或在cfp过程中产生的一部分水或其组合;·其中所述炭经碱性溶液处理;所述碱性溶液优选包含在所述cfp过程中产生的一部分水或从洗涤在所述cfp过程中所用的催化剂获得的洗涤溶液或使用在cfp过程中产生的灰分制得的溶液或其组合。本发明包括一种基于炭的组合物(炭),其通过本文所述方法中任一项制备。在另一方面,本发明提供了一种基于炭的组合物(炭),其包含至少1重量%沸石或含沸石的催化剂和10到99重量%碳,所述炭优选包含至少1重量%沸石。在一些优选实施方案中,本发明组合物可以进一步特征为以下中的一者或任何组合:·所述炭的酸度使得如果暴露于蒸馏水,那么所述炭产生ph小于7、小于6、小于5或小于4或为2到7或2.5到6或3到5的溶液;·其中所述炭包含1到50重量%或2到40重量%或5到35重量%或10到30重量%或15到25重量%或至少1重量%或至少2重量%或至少5重量%或至少10重量%或至少15重量%或至少20重量%的沸石或含沸石的催化剂(所述含沸石的催化剂包含至少10重量%沸石、优选至少20重量%沸石或20到80重量%沸石或30到70重量%沸石);·其中所述炭的体积平均中值粒度小于200微米或小于150微米或小于125微米或小于100微米或小于75微米(这意指颗粒如通过sem测量的尺寸,在所述粒度下50%所观察体积的炭颗粒小于200μm或150μm或125μm等,并且其中“尺寸”是指每个颗粒如在sem显微照片中观察的最大尺寸);·其中所述炭的质量平均粒度是至少125微米或至少149微米或至少250微米或至少420微米或至少595微米或至少841微米或至少2,000微米,或所述炭包含90%或更多的保留于10目或20目或30目或40目或60目或100目或120目筛上的材料;·其中所述炭中苯、甲苯和二甲苯的总和的量以所述炭的重量计构成少于5%或少于2%或少于1%或少于0.5%或少于0.2%或少于0.1%或少于0.02%;·其中碱金属和碱土金属元素的总和以所述炭的重量计构成至少0.1%或至少0.2%或至少0.5%或至少1.0%或至少2.0%;·其中所述炭包含至少15重量%碳或至少20重量%碳或至少25重量%碳或至少30重量%碳或至少35重量%碳或至少40重量%碳或至少50重量%碳,或15到95重量%碳或20到90重量%碳或25到85重量%碳或30到75重量%碳或40到70重量%碳;·其中所述炭包含至少0.1重量%氢或至少0.5重量%氢或至少1.0重量%氢或至少1.5重量%氢或至少2.0重量%氢或至少2.5重量%氢,或0.1到8.0重量%氢或0.5到6.0重量%氢或1.0到5.0重量%氢或1.5到3.0重量%氢;·其中所述炭可以进一步特征为具有增加的氧含量或已经被处理到氧化处理,其比在环境或接近环境(至多约100c)条件下暴露于空气至多约1天提供更多氧化(增加的氧含量意指含量大于通过在环境或接近环境(至多约100c)条件下暴露于空气至多约1天所获得的含量);·其中所述沸石包含至少40重量%zms-5;·包含至少1重量%(或至少5重量%或2到10重量%)硝酸铵;·其中所述炭包含0.1重量%(优选0.01或0.001重量%)或更少的v、ni和as中的每一者;·包含至少15重量%碳;至少0.1重量%氢;至少0.1重量%的na、k、mg和ca的总和;和至少10重量%的呈沸石形式的si和al的总和;·和/或其氧敏感性使得如果19.5mg所述炭的样品经研磨并且暴露于50ml/min的空气流量,那么至少10%或至少20%或至少30%或至少40%或至少50%或至少60%或10%到99%或20%到90%或30%到80%或40%到75%的所述组合物在以30c/分钟的加热速率在120-800c范围内进行的温度编程氧化(tpo)实验中在300-700c范围内蒸发,并且优选在低于580c或低于550c或低于525c或低于500c或350到580c或375到550c或400到525c的温度下蒸发。所述基于炭的组合物可以特征为一密度,所述炭如通过压汞测孔法所测量,堆积密度小于1.0g/ml或小于0.75g/ml或小于0.5g/ml或小于0.35g/ml或小于0.3g/ml或小于0.2g/ml,或0.05到1.0g/ml或0.1到0.75g/ml或0.18到0.5g/ml,或颗粒密度小于1.5或小于1.1或小于1.0或小于0.9或小于0.8或小于0.7或小于0.6或小于0.5或小于0.4g/ml,或0.1到1.1g/ml或0.2到1.0g/ml或0.3到0.9g/ml或0.5到0.7g/ml,或骨架密度小于2.0g/ml或小于1.9g/ml或小于1.85g/ml或小于1.7g/ml或小于1.55g/ml或小于1.4g/ml,或1.0到2.0g/ml或1.3到1.9g/ml或1.4到1.85g/ml。在另一方面,本发明提供了一种修复土壤的方法,其包括:提供炭(其是如本文所述的含沸石的炭和/或根据所要求的发明的任何方法制得的炭);和将所述炭混合到土壤中。本文所述方法中任一者可以包括进行cfp过程和连续地移出炭和催化剂两种细粉。所得炭与催化剂混合物对于进行土壤修复可以是尤其合乎需要的。本发明还包括一种土壤修复,其包含本文所述的炭中任一者并且包括至少1重量%沸石或至少2重量%沸石或1到15重量%范围内的沸石。本发明还包括通过cfp过程制备炭(优选选自本文所述炭中任一者的炭)的方法。本发明的各个方面的优势可以包括:有用产物的产率增加、能量效率提高、资金成本降低和排放物减少。分离炭和燃烧其以加热cfp反应器使得所述过程更能量有效、减小再生器的尺寸和热负荷、去除具有炭的矿物、选择性去除因磨损产生的催化剂细粉和延长催化剂的寿命。分离炭和使其功能化以使其转化为更高价值材料提高了所述过程的经济和碳效率。图式简要说明图1展示了概念性催化快速热解过程,其展示主要能量(--)和质量(→)流路径。图2说明了用于将生物质转化为芳香族化合物与炭分离的概念性过程。图3说明了用以增强炭颗粒粉碎的静态混合器和转向器。顶图(3a)展示了可以插入到流动管中的混合装置的示意图。中图(3b)展示了通过修改提升管设计增加颗粒-壁接触的若干构件的示意图。底图(3c)展示了另一用于通过管内的物料流划分来混合和增强颗粒-壁和颗粒-颗粒相互作用的方案。图4是炭样品的显微照片。图5展示了从cfp过程分离的两种炭部分的组成。图6展示了炭与催化剂的混合物、炭与二氧化硅的混合物和焦化催化剂的温度编程氧化曲线。图7展示了tpo实验中炭与催化剂的混合物、炭与二氧化硅的混合物和焦化催化剂的累积重量损失相较于温度。图8说明了静电分离设备。术语表如本文所用,术语“芳香族化合物(aromatics/aromaticcompound)”用以指包含一个或多个芳香族基团的烃化合物,如例如单芳香族环系统(例如,苯甲基、苯基等)和稠合多环芳香族环系统(例如萘基、1,2,3,4-四氢萘基等)。芳香族化合物的实例包括(但不限于)苯、甲苯、茚满、茚、2-乙基甲苯、3-乙基甲苯、4-乙基甲苯、三甲基苯(例如,1,3,5-三甲基苯、1,2,4-三甲基苯、1,2,3-三甲基苯等)、乙基苯、苯乙烯、异丙苯、甲基苯、丙基苯、二甲苯(例如,对二甲苯、间二甲苯、邻二甲苯)、萘、甲基-萘(例如,1-甲基萘)、蒽、9.10-二甲基蒽、芘、菲、二甲基-萘(例如,1,5-二甲基萘、1,6-二甲基萘、2,5-二甲基萘等)、乙基-萘、二氢化茚、甲基-二氢化茚和二甲基-二氢化茚。在一些实施方案中,还可以制备单环和/或更多环芳香族化合物。芳香族化合物还包括含有杂原子取代基的单和多环化合物,即苯酚、甲酚、苯并呋喃、苯胺的、吲哚、噻吩等。如本文所用,术语“碱金属和碱土金属”(aaem)包括如国际纯粹与应用化学联合会(iupac)所承认的周期表中的第1族和第2族的金属,包括li、na、k、rb、cs、fr、be、mg、ca、sr、ba和ra。术语碱金属和碱土金属还可以包含在生物质中与第1族和第2族元素一起常见的其它元素,包括si、p、al、fe、cu、zn、mn或其它金属(呈低浓度),或其组合。术语碱金属和碱土金属意图表达在生物质中可见并且不对转化为含烃流体产物敏感的除c、h、o、n和s以外的元素的总和。这些元素通常以盐、氧化物或与各种有机分子的组合形式可见,并且有时被称为矿物。如本文所用,术语“生物质”以本领域中的其常规含义给出并且用以指可再生的任何有机能源或化学品。其主要组分可以是:(1)树木(木材)和所有其它植被;(2)农业产品和废物(玉米、果实、垃圾青贮料等);(3)藻类和其它海洋植物;(4)新陈代谢废物(粪肥、污水);和(5)纤维质城市废物。生物质材料的实例描述于例如huber,g.w.等人,“synthesisoftransportationfuelsfrombiomass:chemistry,catalysts,andengineering”,chem.rev.106,(2006),第4044-4098页中。生物质常规地定义为可以被转化用作燃料或用于工业生产的活的和新死的生物材料。作为生物质的准则在于,材料应在最近参与碳循环,使得燃烧过程中的碳释放在相当短的时期内平均不导致净增加(出于这个原因,如泥煤、褐煤和煤的化石燃料根据这个定义不被视为生物质,因为其含有长时间未曾参与碳循环的碳,使得其燃烧导致大气二氧化碳的净增加)。最常见地,生物质是指生长用作生物燃料的植物体,但其还包括用于产生纤维、化学品或热量的植物或动物体。生物质还可以包括可以作为燃料燃烧或转化为化学品的可生物降解废物或副产物,包括城市废物、绿色废物(可生物降解废物,包含花园或公园废物,如草或花粉屑和篱笆修剪物)、农场副产物(包括动物粪肥)、食品加工废物、污水污泥、来自木浆的黑液或藻类。生物质排除了已经通过地质过程转变为如煤、油页岩或石油的物质的有机材料。生物质广泛并且通常由植物生长,所述植物包括芒属、大戟、向日葵、柳枝稷、大麻、玉米(玉蜀黍)、白杨、柳树、甘蔗和油棕(棕榈油),根、茎、叶、籽壳和果实都可能是有用的。为引入加工单元而对原材料的加工可以根据单元的需要和生物质的形式变化。生物质可以因存在显著高于化石燃料中所见量的量的14c而不同于化石衍生的碳。本文所述产物中任一者优选衍生自生物质。如本文所用,术语“催化快速热解”(cfp)是指通过在催化剂存在下快速加热将含烃材料转化为化学品、燃料或化学品和燃料的过程。适用于cfp的设备和加工条件的实例描述于以引用的方式并入本文中的huber等人的美国专利8,277,643、美国专利申请us2012/0203042a1和huber等人的美国专利申请2013/0060070a1中。用于生物质的cfp的条件可以包括以下特征(其不打算限制本发明的更广泛方面)中的一者或任何组合:沸石催化剂,zsm-5催化剂;包含以下金属中的一者或多者的沸石催化剂:钛、钒、铬、锰、铁、钴、镍、铜、锌、镓、铂、钯、银、磷、钠、钾、镁、钙、钨、锆、铈、镧和其组合;流化床、循环床或提升管反应器;300℃到1000℃范围内的操作温度;和/或0.1与40之间的固体催化剂与生物质质量比。如本文所用,术语“催化剂”具有其常规含义,即添加到过程中以增加化学反应的速率的材料。适用于本发明情形的催化剂组分可以选自本领域中已知或如本领域技术人员所理解的任何催化剂。催化剂促进和/或实现反应。因此,如本文所用,催化剂降低化学过程的活化能(增加速率),和/或改进化学反应中产物或中间物的分布(例如,形状选择性催化剂)。可以被催化的反应的实例包括:脱水、脱氢、异构化、氢转移、芳构化、脱羰、脱羧、醇醛缩合、分子裂化和分解、其组合和其它反应。催化剂组分可以被视为酸性、中性或碱性,如本领域技术人员所理解。对于催化快速热解(cfp),特别有利的催化剂包括含有根据孔隙尺寸选择的内部孔隙率的催化剂(例如,介孔和通常与沸石相关的孔隙尺寸),例如平均孔隙尺寸为小于小于小于小于小于或更小。在一些实施方案中,可以使用平均孔隙尺寸为到的催化剂。在一些实施方案中,可以使用平均孔隙尺寸在与之间或与之间的催化剂。在一些情况下,可以使用平均孔隙尺寸在7埃与之间或与之间的催化剂。在cfp的一些优选实施方案中,催化剂可以选自天然存在的沸石、合成沸石和其组合。在某些实施方案中,催化剂可以是zsm-5沸石催化剂,如本领域技术人员所理解。任选地,这种催化剂可以包含酸性位点。其它类型的沸石催化剂尤其包括:镁碱沸石、y沸石、β沸石、丝光沸石、mcm-22、zsm-23、zsm-57、suz-4、eu-1、zsm-11、zsm-22、sapo-31、ssz-23。本发明的cfp过程流化床反应器中特别有利的催化剂组合物包含特征为大于12的二氧化硅与氧化铝摩尔比(sar)和1到12的约束指数(ci)的结晶分子筛。测定ci的方法更充分描述于关于方法细节以引用的方式并入的美国专利第4,029,716号中。这些结晶分子筛的非限制性实例是具有zsm-5、zsm-11、zsm-12、zsm-22、zsm-23、zsm-35、zsm-48、zsm-50或其组合的结构的分子筛。在其它实施方案中,可以使用非沸石催化剂;例如wox/zro2、磷酸铝等。在一些实施方案中,催化剂可以包含金属和/或金属氧化物。适合金属和/或氧化物尤其包括例如镍、钯、铂、钛、钒、铬、锰、铁、钴、锌、铜、镓和/或其氧化物中任一者。在一些情况下,可以包括选自稀土元素(即元素57-71)、铈、锆之中的促进剂元素或其氧化物用于其组合以改变催化剂的活性或结构。另外,在一些情况下,催化剂的特性(例如,孔隙结构、酸位点的类型和/或数目等)可以经选择以选择性制备所要产物。“炭”是应用于已经在燃烧、热解或催化热解过程中从生物质至少部分转化的富含碳的(至少20质量%c)固体材料的术语。炭通常含有高百分比的碳、一些氢和一定量的氧,并且还可以含有存在于在过程中反应的生物质中的一些其它元素,如ca、k、p、na、mg、mn、si、s、n、fe或其它元素。炭可以呈现得与反应的初始生物质颗粒在形状和整体结构方面类似,或其可以呈现为已经在过程中被研磨成更精细颗粒,或其可以聚结为更大颗粒,或其组合。在一些情况下,炭可以含有实质部分的催化剂已经变得与碳质材料掺杂。炭的其它特征提供于实施方式章节中。炭在比焦炭或焦化催化剂在受控氧化实验中氧化所处的温度低的温度(最大质量损失速率的温度)下氧化。炭具有比焦炭或焦化催化剂低的颗粒密度和低的堆积密度。如本文所用,术语“焦炭”以本领域中的其常规含义给出并且用以指沉积于催化剂或其它材料上的富含碳的固体。焦炭沉积物通常通过在催化剂再生过程中燃烧而去除。焦炭与炭不同之处在于,焦炭通常沉积于催化剂的孔隙中或表面上,与炭相比,芳香性更高并且反应性更小。在许多情况下,焦炭与炭的分离并不便利并且焦炭和炭通常一起视为固体产物。如本文所用,术语“烯烃”或“烯烃化合物”(又名“链烯烃”)以本领域中的其普通含义给出,并且用以指含有一个或多个由双键键联的碳原子对的任何不饱和烃。烯烃包括环状和非环状(脂肪族)烯烃,其中双键位于分别形成环状(闭环)或开链基团的一部分的碳原子之间。另外,烯烃可以包括任何适合数目的双键(例如,单烯烃、二烯烃、三烯烃等)。具有两个双键的烯烃通常被称为二烯。烯烃化合物的实例尤其包括(但不限于)乙烯、丙烯、丙二烯(allene/propadiene)、1-丁烯、2-丁烯、异丁烯(2甲基丙烯)、丁二烯和异戊二烯。环状烯烃的实例尤其包括环戊烯、环己烯、环庚烯。如甲苯的芳香族化合物不被视为烯烃;然而,包括芳香族化合物部分的烯烃被视为烯烃,例如丙烯酸苯甲酯或苯乙烯。“含氧化合物”包括在其结构中含有至少一个氧原子的任何有机化合物,如醇(甲醇、乙醇等)、酸(例如乙酸、丙酸等)、醛(例如甲醛、乙醛等)、酯(例如乙酸甲酯、乙酸乙酯等)、醚(例如二甲醚、二乙醚等)、具有含氧取代基的芳香族化合物(例如苯酚、甲酚、苯甲酸等)、环醚、酸、醛和酯(例如呋喃、糠醛等)等。如本文所用,术语“热解(pyrolysis/pyrolyzing)”以本领域中的其常规含义给出并且用以指通过优选在不添加o2的情况下或在不存在o2下加热将化合物(例如固体含烃材料)转化为一种或多种其它物质(例如挥发性有机化合物、气体、炭和焦炭)。优选地,热解反应室中存在的o2的体积分数是0.5%或更小。热解可以在使用或不使用催化剂的情况下进行。“催化热解”是指在催化剂存在下进行的热解,并且可以涉及如huber等人的美国专利8,277,643、美国专利申请us2012/0203042a1和huber等人的美国专利申请2013/0060070a1和下文中更详细描述的步骤。催化热解过程的实例概述于例如huber,g.w.等人,“synthesisoftransportationfuelsfrombiomass:chemistry,catalysts,andengineering”,chem.rev.106,(2006),第4044-4098页中。组分的“回收率”是存在于所回收产物流中的所述组分与存在于反应器流出物流中的所述组分的量相比的分数(或百分比)。举例来说,如果10克产物a存在于原始流出物中并且8.5克产物a存在于所回收产物流中,那么a的回收率是8.5/10或0.85(85%)。“反应区”是指cfp反应器中的区,其中催化剂和生物质在至少300℃的温度下存在,并且包括催化剂与生物质进料接触的体积,但排除一些催化剂和生物质被输送通过的入口和出口和隔板的体积。如标准专利术语,术语“基本上由……组成”排除了会实质地影响方法的其它步骤或会实质地影响产物的组分的存在。一般来说,使用术语“包含”定义的本发明方法或产物中任一者还可以使用更具限制性的术语“基本上由……组成”或在最狭义情况下“由……组成”表征。另外,本文所述的方法和/或产物步骤中任一者旨在涵盖于本文所述的本发明方法或产物中任一者内。实施方式图1展示了概念cfp过程的一种配置中的质量和能量流的主要路径。生物质在cfp反应器中在催化剂存在下热解。过程的固体产物与蒸气产物分离,蒸气被供应给产物回收和分离系统。一部分固体炭被分离并且任选地燃烧以提供能量以驱动cfp过程。用过的焦化催化剂被分离并且再生以恢复其活性并且向cfp过程提供热量。来自催化剂再生或炭燃烧或两者的过量热量可以被输出并且在别处使用(未展示)。许多热回收和热交换过程和一些质量流在这个概念过程中省去。图2展示了用于将生物质转化为有用产物(包含芳香族化合物(btx)、烯烃和其它组分)和将炭从系统分离的例示性过程。生物质与再循环气体或输送流体一起经由物料流101引入到cfp反应器100中。催化剂可以与输送流体一起经由物料流102引入cfp反应器中。cfp反应器是通过一部分再循环气体或其它流体103流化的流化床催化反应器。来自cfp反应器的产物与连同流体流104一起载运到一个或多个旋风器112中的任何催化剂、灰分或炭分离。固体可以经由物料流105返回到反应器并且产物混合物被传送到产物回收和分离系统(未展示)。任选地,一部分物料流105可以从系统被移出并且被舍弃或传送到催化剂再生器120或传送到蒸汽汽提器110。任选地,一部分物料流105可以传送到炭燃烧单元(未展示)或被舍弃。物料流107中从反应器移出的催化剂通过到蒸汽汽提器110中。在蒸汽汽提器中,催化剂暴露于置换了系统中的气体和挥发物的蒸汽流。这些置换的蒸气和一部分蒸汽可以传送到产物分离和回收部分(未展示)或以其它方式用于过程中。物料流109中被蒸汽汽提的催化剂与包含氮气、空气或氮气和空气的转移流体一起通过到转移线115(任选地提升管)中,并且通过到旋风器或系列旋风器122中以将炭与催化剂分离。富含炭的物料流123可以传送到炭燃烧反应器(未展示)或以其它方式使用或作为产品销售。物料流125的炭耗尽的用过的催化剂通过到再生器120,在其中用空气或含氧物料流使焦炭和任何剩余炭至少部分燃烧。取决于炭颗粒和催化剂颗粒的相对尺寸、密度和性质,富含炭的物料流可以包含物料流123并且物料流125可以包含炭耗尽的用过的催化剂;炭耗尽的用过的催化剂可以在另一或其它旋风器中或通过其它构件从物料流123分离,并且然后传送到再生器120。再生器120任选地被冷却以将温度控制在可接受的极限内;冷却单元未展示于图2中。再生的催化剂可以经由可以任选地包含冷却单元的物料流131返回到反应器。燃烧废气流126通过到旋风器或系列旋风器124中以移出固体并且然后燃烧废气流128被排放或传送到气体清洁系统(未展示)。旋风器124中收集的固体可以返回到再生器或一部分固体可以被去除。在本发明的一个实施方案中,过程中回收的一部分炭被处理并且返回到cfp反应器。cfp过程所制得的炭与生物质进料相比已经至少部分去水并且去氧,但其未曾在cfp过程中氧化。在不希望受理论束缚的情况下,可以预期来自cfp过程的炭比从燃烧或在氧化气氛中进行的其它过程获得或来自煤或石油的炭更易发生氧化。已知炭用空气在比焦炭或焦化催化剂更低的温度下燃烧。因此,cfp炭可以容易在相对温和氧化条件和试剂的作用下氧化或优选部分氧化。在这点上,氧化剂,如臭氧、氧气、稀空气、过氧化氢、过乙酸(ch3c(o)ooh)、过甲酸(hc(o)ooh)、异丁基过氧化物、no2、no或本领域技术人员已知的其它气态或液体氧化剂或其任何组合可以用以使炭部分氧化或官能化。炭处理可以用气态试剂或用溶液进行。炭处理的产物与新鲜制得的炭相比具有增加的o/c比率。如通过对固体产物、液体产物或固体和液体两种产物进行红外光谱法所测量,炭处理的产物具有增加的碳氧单键(c-o)和双键(c=o)的含量。在用气态反应物使炭部分氧化的过程中,温度维持在100c到650c或200c到600c或300c到550c或低于650c或低于600c或低于550c或低于500c或低于450c或低于400c范围内。在用溶液反应物使炭部分氧化的过程中,温度维持在20c到250c或50c到200c或60c到150c或低于250c或低于200c或低于150c或低于100c或低于80c或低于60c范围内。氧化剂(如氧气或过氧化氢)的氧化能力保持在小于实现炭完全燃烧为co2和水所需要的化学计量氧量,以使得所述氧化剂中的氧与所述炭中的碳比率(o/c比率)小于1.5、小于1.0、小于0.8、小于0.5或小于0.25,或是0.01到1.5或0.05到1.0或0.1到0.8或0.15到0.5.炭的溶液处理可以包括去除新鲜制得的炭中的至少一部分矿物。这些过程可以包括用液体溶液(例如水、h2o2水溶液、酸性溶液等)洗涤。任选地,cfp过程中作为副产物产生的一部分含有一些含氧化合物并且ph在约2并且6之间的水溶液可以用以洗涤炭。在本发明的一个实施方案中,炭用以从过程用水提取含氧化合物,作为清洁水的手段和提供这些材料再循环到cfp反应器的手段。在一个实施方案中,炭被部分氧化随后其被洗涤,并且在另一实施方案中,炭被洗涤随后其被部分氧化。至少一部分洗过的炭可以供应给cfp反应器。另一潜在处理是“爆炸性研磨”,其中将炭用溶剂(例如水)或溶液或氨水浸渍,并且快速加热到高于溶剂的沸点,其中其使颗粒膨胀和爆炸。如果气相组分(如co、co2、烯烃或其它轻质烃)是所要的,那么可以使用炭的等离子处理。炭可以经历蒸汽重整条件,例如在蒸汽存在下高于750℃的温度,以使得生物质中碱金属元素的存在催化炭重整为合成气体,即h2、co、co2和蒸汽。这种过程中形成的h2和co可以再循环到cfp反应器或以其它方式用于过程中或用于其它目的。在一个实施方案中,用co2、蒸汽或co2和蒸汽两者使cfp过程中产生的炭经历气化以形成包含co、co2、h2o、h2、甲烷和其它轻质烃的气体混合物。在一些实施方案中,根据本发明的炭的质量平均粒度是至少125微米或至少149微米或至少250微米或至少420微米或至少595微米或至少841微米或至少2,000微米,其中“尺寸”通过人工筛分或光散射使用malvernmastersizer2000激光衍射系统(或其等效物)测量;在未规定时,尺寸欲通过筛分测定。在一些实施方案中,炭包含90%或更多的保留于2000微米(10目)或850微米(20目)或600微米(30目)或425微米(40目)或250微米(60目)或149微米(100目)或125微米(120目)筛上的材料。本发明的炭可以包含至少125微米或至少149微米或至少250微米或至少420微米或至少595微米或至少841微米或至少2,000微米的从固体混合物分离的颗粒。在一些实施方案中,在人工筛分材料2分钟时间之后,根据本发明的炭包含保留于2000微米(10目)或850微米(20目)或600微米(30目)或425微米(40目)或250微米(60目)或149微米(100目)或125微米(120目)筛上的材料。人工筛分根据以下方案进行:在一只手中以稍微倾斜的位置握住具有滑动配合底盘和盖板的个别筛。急剧地并且在抵着另一手跟部的向上动作下以约150次/分钟的速率敲击筛侧,以约25次敲击的间隔转动筛旋转的约六分之一。任选地,至少一部分炭可以在其经历如上所述的处理之前被粉碎。粉碎可以通过碾磨、研磨、捏合、切碎、压碎、磨粉、碎裂或减小炭的平均粒度或增加炭的表面积或两者的任何其它过程实现。如通过光散射所测量,炭的粉碎可以使质量平均粒度减小初始质量平均粒度的至少50%或至少60%或至少70%或至少80%。如通过光散射所测量,炭的粉碎可以使平均直径大于2mm或大于1mm或大于0.5mm或大于0.3mm或大于0.2m或大于0.1mm的颗粒的质量分数减小具有指定平均直径的颗粒的初始质量分数的至少50%或至少60%或至少70%或至少80%。炭的粉碎可以使炭的质量平均粒度减小到小于200微米或小于150微米或小于125微米或小于100微米或小于75微米。在本发明的一个实施方案中,提升管115装有内部器具,如静态混合器、转向器等;或经成形,以这种方式以便增强固体混合物的颗粒-壁、颗粒-颗粒或颗粒-内部器具相互作用并且增强炭颗粒的粉碎。预想了增强炭磨损同时不大体上增强催化剂磨损的任何内部器具或输送形状。炭优先于催化剂的颗粒粉碎(平均粒度减小)可以通过在从蒸汽汽提器到再生器的快速流动管(如提升管或转移线)中磨损来实现。据相信,对于大多数cfp催化剂,炭颗粒比催化剂颗粒更易碎,以使得其通过固体-固体相互作用将被粉碎得更厉害。为了增强炭粉碎,转移线或提升管可以装有多个增加颗粒-颗粒接触、颗粒-器具接触和颗粒-壁接触的静态混合装置或转向器。预想可增强固体-固体接触的内部器具和转移线几何结构的一些非限制性实例展示于图3中,但存在许多其它变动。条件可以经选择以在不显著粉碎催化剂的情况下选择性粉碎炭。因为催化剂是经制造以承受流化床反应器中的操作的流化床催化剂,所以预期其可以具有比炭更大的强度。此外,炭颗粒通常不如催化剂颗粒致密,使其更可能从具有更致密催化剂颗粒的混合物淘析。将炭颗粒粉碎到与催化剂颗粒的尺寸分布相比具有类似或更小平均直径的尺寸分布将允许其更容易如通过图2中的旋风器122分离。在将炭从具有催化剂和灰分的cfp反应器移出之后粉碎其使得淘析过程更有效,向再生器提供更多的缺炭的和缺灰分的催化剂进料。用撞击表面或装置的粉碎是其中至少一些颗粒以从平行到表面或装置为至少45度的攻角冲击表面或装置的过程。在一个实施方案中,少量氧气被引入提升管柱中以在其移动通过提升管时引发炭的燃烧反应。据相信,炭的部分燃烧可以进一步增加炭的易碎性质和减小粒度,致使其更易粉碎和如通过图2中的旋风器122与催化剂颗粒分离。用以输送催化剂和炭与灰分混合物通过提升管115的输送流体的氧气浓度可以是输送流体混合物的体积的小于5%或小于2%或小于1.5%或小于1.0%或小于0.5%或小于0.2%或0.001%到2%或0.01%到1%或0.02%到0.5%或0.02%到0.2%,或其可以大体上不含氧气。在本发明的一个实施方案中,图2中鉴别为112、122和124的旋风器中任一者可以包含多于一个串联的旋风器,或多于一个并联的旋风器或系列旋风器。在使用多个旋风器的情况下,进入每个旋风器的气体/固体混合物的线速度可以通过改变旋风器的几何结构或通过添加输送流体到混合物或两者来调节。优选地,进入一系列旋风器中的个别旋风器的气体/固体混合物的线速度将随每个后续旋风器而增加或至少不降低,即进入第二旋风器的气体/固体混合物的线速度将大于或等于进入第一旋风器的气体/固体混合物的线速度,进入第三旋风器的气体/固体混合物的线速度将大于或等于进入第二旋风器的气体/固体混合物的线速度,等。炭分离可以在蒸汽汽提器用以从焦化催化剂移出烃产物和置换气体之前、同时和/或尤其之后进行。在本发明的一个实施方案中,炭通过在蒸汽汽提器中或后的固体浮选过程与催化剂至少部分分离。一些炭颗粒和一些灰分颗粒不如催化剂颗粒致密,并且因此在适当搅拌条件下倾向于移动到颗粒流化床的上部。浮选过程优选是气体浮选,其中床通过缓慢气体或蒸气流进行搅拌。液体浮选也被预想属于本发明的范围内。用于浮选分离过程的液体可以包括水溶液、酸性溶液、含有如铵盐的盐的水溶液,如水溶液或于有机溶剂或混合溶剂与水中的溶液。浮选液体的ph优选小于7或小于6或小于5或小于4或小于3或1到5或2到4。随着不太致密的颗粒升高到固体混合物的顶部,其可以溢出超过挡板并且被收集,或使用龙头沿着浮选装置在不同点收集具有不同密度的颗粒。在本发明的一些实施方案中,催化剂与炭混合物通过借助于流体对固体颗粒的淘析过程分离。在淘析过程的一个实施方案中,在淘析流体中制备待分离的固体颗粒的悬浮液,所述淘析流体是关于催化剂或炭化学惰性的流体,并且此外在于,所述过程包括以下规定阶段中的一者或多者,其中第一阶段是分离大颗粒的过程,包括将催化剂与炭悬浮液流引入到垂直淘析柱中在柱的中点与底部之间的水平下,将淘析流体流引入到柱中在低于引入催化剂与炭悬浮液的水平的水平下,导致所述流体大体上在层流条件下在上升物料流中流入柱中,从柱的顶部取出大体上不含大炭颗粒或催化剂与炭聚结物的催化剂悬浮液,和从柱的底部取出主要包含大颗粒的悬浮液;并且其中任选的第二阶段是分离细颗粒的过程,包括将从第一淘析柱回收的催化剂悬浮液流引入到垂直淘析柱中高于中点,将淘析流体流引入到柱中在更低水平下,导致所述流体在上升物料流中并且大体上在层流条件下流入柱中,从柱的顶部取出装有细催化剂与炭颗粒的淘析流体,和从柱的底部取出大体上不含细颗粒的催化剂颗粒。在根据本发明的方法的变化形式中,因此,在第一阶段期间制得的于淘析流体中的催化剂悬浮液可以经历淘析操作,使催化剂的大或细颗粒能够被分离。悬浮液还可以经历双淘析操作,使大和细颗粒两者能够同时被分离,大颗粒在第一淘析柱中被分离,优选随后细颗粒在第二淘析柱中被分离。取决于加工条件和炭与催化剂颗粒的相对尺寸,大颗粒或细颗粒或两者可以包含炭或催化剂。优选地,淘析流体是气体或气体的混合物。在本发明的一个实施方案中,炭通过筛、一组具有各种孔洞或开口的筛或另一尺寸排阻装置与催化剂至少部分分离,其中固体的分离基于粒度差异进行。在一些实施方案中,催化剂与炭的混合物通过一筛(优选向上(与重力相反)通过筛),不通过筛的较大颗粒再循环到反应器或通过到催化剂再生器或蒸汽汽提器或炭燃烧器。在一些替代实施方案中,催化剂与炭的混合物通过一筛(优选向上(与重力相反)通过筛),通过筛的较小颗粒再循环到反应器或通过到催化剂再生器或蒸汽汽提器。收集未再循环的炭颗粒作为用于进一步加工的炭。在本发明的一个实施方案中,炭首先通过尺寸排阻从固体混合物分离以产生较大颗粒炭富集的部分和第一较小颗粒炭耗尽的部分。炭富集的部分可以通过淘析分离为第二更富集的炭部分和第二炭耗尽的部分。第二更富集的炭部分可以传送到炭燃烧器或以其它方式处理或舍弃或保留用于其它用途。这些分离过程中任一者可以在固体混合物通过蒸汽汽提器之前或优选在之后进行。在本发明的其中炭被分离和在与催化剂再生分开的容器中燃烧以向cfp反应器提供热量的实施方案中,炭燃烧可以在至少500c或至少600c或至少700c或至少800c或至少900c或至少1000c或700c到1300c或800到1200c的温度下操作。在本发明的其中炭被分离和在与催化剂再生分开的容器中燃烧以向cfp反应器提供热量的实施方案中,催化剂再生可以在低于750c或低于700c或低于650c或低于625c或550c到750c或575c到700c或600c到650c的温度下操作。在适度温度下操作再生器是有利的,因为其将延长zsm-5催化剂和其它沸石催化剂的寿命。在本发明的其中炭被分离和在与催化剂再生分开的容器中燃烧以向过程提供热量的实施方案中,炭燃烧可以在循环流化床反应器、提升管反应器、气化器、逆流气化器、并流气化器、交叉流式气化器、流化床气化器、双燃式气化器、夹带床气化器、熔池气化器、热交换反应器、循环回路反应器、分级燃烧反应器或熟知用以燃烧固体和任选地由其回收热量的任何其它燃烧反应器中进行。炭部分的燃烧在含氧气体(如空气或氧耗尽的空气或氧富集的空气)或含有氧气的烟道气或含有足以支持炭燃烧的氧气的任何气体存在下进行。优选地,炭的燃烧在少量过量的氧气(即比实现碳质材料完全转化为co2和水所需要更多的氧气)存在下进行。在本发明的其中炭被分离和在与催化剂再生分开的容器中燃烧以向过程提供热量的实施方案中,催化剂再生器中的热释放与在炭和催化剂未分离并且一起燃烧时所释放的热量的量相比显著减少。与在炭和焦化催化剂一起在再生器中燃烧而未分离时的热量释放相比,在炭已经被移出时催化剂再生器中的热量释放的减少是至少20%或至少33%或至少50%或至少60%或至少66%或至少75%。从过程分离的炭可以含有炭和来自催化剂(呈如全催化剂颗粒和衍生自cfp过程设备中的催化剂颗粒断裂的催化剂细粉的物理形式)的部分无机沸石和其它无机材料的混合物。在一些情况下,催化剂材料牢固地附着到炭颗粒,或许是通过粘着力。本发明方法中制得的炭可以包含以重量计至少1%或至少10%或至少20%或至少25%或至少30%或10到70%或20到60%或15到50%的呈一种或多种沸石形式的二氧化硅和氧化铝的总和。本发明方法中制得的炭可以包含以重量计至少1%或至少5%或至少10%或至少20%或至少30%的呈一种或多种非晶固体材料(如粘合剂、粘土等)形式的二氧化硅和氧化铝的总和。本发明方法中制得的炭可以包含以重量计至少1%或至少10%或至少20%或至少25%或至少30%或10到95%或20到90%或25到80%的衍生自cfp过程中所用催化剂的固体材料(通常包括粘合剂和沸石)。这种高度多孔的炭与催化剂混合物可以是贵重的土壤修复剂,因为其使碳返回到土壤,提供了提供多孔性以便截留和向土壤释放水的能力,增加了土壤渗透性,疏松了土壤,并且提供了含于无机催化剂材料和cfp过程中制得的多孔炭内的各种金属离子和有机材料的保留和释放。此外,这个过程中制得的cfp炭将在于炭在蒸汽汽提器之内或下游被分离的配置中对催化剂与炭混合物蒸汽汽提期间使已知对植物生长有害的化合物(如挥发性多核芳香族化合物)被大体上去除。已经通过蒸汽汽提加工的炭将包含减少量的芳香族化合物(如btx)和其它挥发性组分。苯加甲苯加二甲苯的量以炭的重量计将是少于5%或少于2%或少于1%或少于0.5%或少于0.2%或少于0.1%或少于0.02%,或浓度低到足以致使炭成为非有害材料。cfp炭优选含有的苯、甲酚、吡啶或金属的浓度使得炭的提取物不展现使用毒性特征浸出程序(toxicitycharacteristicleachingprocedure),测试方法1311于以引用的方式并入本文中的“用于评估固体废物的测试方法,物理/化学方法(testmethodsforevaluatingsolidwaste,physical/chemicalmethods)”,epa出版物sw-846,1992年7月中测量的毒性的特征。在一些实施方案中,致使炭成为非有害的。另外,cfp炭可以包含见于生物质中的一部分金属元素,如ca、k、na、mg、si、p、fe等,其为用于植物生命生长的已知营养素。本发明的cfp炭的ni、cr、v、ag、se、hg、pb、cd、ba、as和氯离子的量优选低于视为将炭归类为有害材料的量。此外,包含cfp过程中所用的一部分酸性沸石催化剂的cfp炭的ph将更接近于促进植物生长的ph;衍生自非催化热解过程的炭通常是碱性极强的,特别是在其含有灰分时,并且因此在其可以用作土壤修复剂之前需要ph调节。用本发明的方法制得的炭在暴露于水后可以产生ph为7或更小、6或更小、5或更小或4或更小或为2到7或2.5到6或3到5的溶液。因此,本发明的优选炭可以特征为具有潜在ph,使得如果10g炭在10分钟搅拌下分散于50g蒸馏水中,那么水将具有上述的特征ph。从cfp过程分离和移出炭还提供了一种从系统去除形成灰分的元素、从过程去除催化剂细粉、延长催化剂寿命、减小催化剂再生器的尺寸和成本、和改进过程的可操作性的手段。含有一部分酸性无机与沸石材料混合物的炭当结合氨肥料施用用作土壤修复材料时将具有关于土壤氮施肥和控制释放的其它益处,因为固体酸位点具有吸附和解吸附碱性分子(如氨和铵离子)的能力。炭分离、处理或燃烧或其任何组合可以是用于调节过程中催化剂藏量的粒度分布的综合控制过程的一部分。与炭分离的细催化剂颗粒可以任选地以适当量和速率返回到cfp反应器以维持催化剂的所要粒度分布。由本发明的cfp过程制得的炭或由其分离的部分包含一部分催化剂,其可以在1到95重量%或2到80重量%或5到70重量%或10到60重量%或15到50重量%或20到40重量%或至少1重量%或至少2重量%或至少5重量%或至少10重量%或至少15重量%或至少20重量%炭范围内。由本发明的cfp过程制得的炭包含碱金属和碱土金属(一起称为aaem),如na、k、mg和ca或其组合。由本发明的cfp过程制得的炭包含至少0.01重量%aaem或至少0.1重量%aaem或至少0.2重量%aaem或至少0.5重量%aaem或至少1.0重量%aaem、至少2.0重量%aaem。由本发明的cfp过程制得的炭或由其分离的部分包含至少15重量%碳或至少20重量%碳或至少25重量%碳或至少30重量%碳或至少35重量%碳或至少40重量%碳或至少50重量%碳,或15到95重量%碳或20到90重量%碳或25到85重量%碳或30到75重量%碳或40到70重量%碳。由本发明的cfp过程制得的炭或由其分离的部分包含至少0.1重量%氢或至少0.5重量%氢或至少1.0重量%氢或至少1.5重量%氢或至少2.0重量%氢或至少2.5重量%氢,或0.1到8.0重量%氢或0.5到6.0重量%氢或1.0到5.0重量%氢或1.5到3.0重量%氢。由本发明方法制得的炭的堆积密度可以小于1.0g/ml或小于0.75g/ml或小于0.5g/ml或小于0.35g/ml或小于0.3g/ml或小于0.2g/ml,或0.05到1.0g/ml或0.1到0.75g/ml或0.18到0.5g/ml。本发明方法的炭的颗粒密度可以小于1.5或小于1.1或小于1.0或小于0.9或小于0.8或小于0.7或小于0.6或小于0.5或小于0.4g/ml,或0.1到1.1g/ml或0.2到1.0g/ml或0.3到0.9g/ml或0.5到0.7g/ml。本发明方法的炭的骨架密度可以小于2.0g/ml或小于1.9g/ml或小于1.85g/ml或小于1.7g/ml或小于1.55g/ml或小于1.4g/ml,或1.0到2.0g/ml或1.3到1.9g/ml或1.4到1.85g/ml。本发明的炭可以包含在cfp过程中产生的固体材料,其中至少10%或至少20%或至少30%或至少40%或至少50%或至少60%或10%到99%或20%到90%或30%到80%或40%到75%的材料以30c/分钟的加热速率在120-800c范围内以小于5,000体积空气/体积样品的比率在气流中进行的温度编程氧化(tpo)实验中在300-700c范围内因燃烧而损失,在低于580c或低于550c或低于525c或低于500c或350到580c或375到550c或400到525c的温度下损失。本发明的炭可以包含在cfp过程中产生的固体材料,其中如以30c/分钟的加热速率在120-800c范围内以小于5,000体积空气/体积样品的比率在气流中进行的温度编程氧化(tpo)实验中所测量的最大重量损失在低于580c或低于550c或低于525c或低于500c或低于490c或低于480c或350到580c或400到550c或425到500c或450到490c下发生。本发明方法的炭的ph可以通过用酸或碱处理以符合特定土壤需求来调节。本发明方法的炭可以用酸处理以用作土壤修复材料。用于炭处理的酸可以包括乙酸、甲酸、硝酸、硫酸、丙酸或碳酸或在cfp过程中产生的一部分水或本领域技术人员已知的其它酸或其组合。本发明方法的炭可以用碱性溶液处理以用作土壤修复材料。碱性材料可以包括在cfp过程中产生的一部分水或从洗涤在cfp过程中所用的催化剂获得的洗涤溶液或使用在cfp过程中通过燃烧炭或生物质产生的灰分制得的溶液或本领域技术人员已知的其它碱性溶液或其组合。在本发明中蒸汽汽提器可以在各种各样的条件下操作。蒸汽汽提器的温度可以在100到700c或250到650c或400到625c或500到600c范围内,或可以是至少100c或至少250c或至少400c或至少500c或低于700c或低于650c或低于600c。蒸汽汽提器中的压力可以是1到20巴(绝对压力)或2到15巴或3到10巴或4到8巴,或至少1巴或至少2巴或至少3巴或至少4巴,或小于20巴或小于10巴或小于8巴。cfp过程可以在400℃或更高的温度下进行,并且来自图2中的100的产物流104通常在300-620℃或400-600℃或500-575℃的温度和100kpa到5000kpa或200kpa到1500kpa或300kpa到700kpa或至少200kpa或至少300kpa或至少400kpa的压力下。(压力以绝对压力表示。)来自cfp反应器的原始产物流包含芳香族化合物、烯烃、含氧化合物、石蜡、h2、ch4、co、co2、水、炭、灰分、焦炭、催化剂细粉和众多其它化合物。基于不含水和不含固体的质量%计算,原始产物流可以包含20到60%或25到55%或30到50%或至少20%或至少25%或至少30%co。基于不含水和不含固体的质量%计算,原始产物流可以包含10到50%或15到40%或20到35%或至少5%或至少10%或至少15%或至少20%co2。基于不含水和不含固体的质量%计算,原始产物流可以包含0.1到2.0或0.2到1.5或0.3到0.75%或至少0.1%或至少0.2%或至少0.3%或少于10%或少于5%或少于1%h2。基于不含水和不含固体的质量%计算,原始产物流可以包含2到15或3到10或4到8%或少于15%或少于10%或少于8%ch4。基于不含水和不含固体的质量%计算,原始产物流可以包含2到40或3到35或4到30%或少于40%或少于35%或少于30%或少于20%btx。基于不含水和不含固体的质量%计算,原始产物流可以包含0.1到10%或0.2到5%或0.3到3%或少于5%或少于3%或少于2%含氧化合物。基于不含水和不含固体的质量%计算,原始产物流可以包含1到15%或2到10%或3到6%c2-c4或至少1%或至少2%或至少3%烯烃。基于不含水和不含固体的质量%计算,原始产物流可以包含蒸气混合物,其中co和co2的总和是30到90%或40到85%或50到80%。实施例1用研钵和研杵将10g获自wastetoenergysolutions,inc.的市售生物炭样品研磨成粉末。将粉末悬浮于烧杯中的50g水中,用磁性搅拌器搅拌。ph在5分钟之后测量为7.64并且在90分钟之后测量为7.65。通过筛分将获自用商业h-zsm-5催化剂使硬木球粒热解的cfp炭从催化剂堆分离。保留于40目筛(0.4mm)上的较大颗粒指定为炭,并且通过40目筛的较小颗粒因主要是催化剂而被舍弃。分析显示,炭样品含有约30重量%碳。将10gcfp炭样品悬浮于50g水中,并且用如上的磁性搅拌器搅拌。ph在5分钟之后测量为6.83、在60分钟之后测量为3.24并且在90分钟之后测量为3.26。实施例2将4英寸直径(10cmod)流化床反应器用于生物质转化和再生持续4个循环,其装有500g已经在空气中在600c下锻烧2小时的平均粒度为约110微米直径并且少于10%大于210微米直径的喷雾干燥的商业h-zsm-5催化剂。用2.3标准升/分钟(slpm)的n2流使得用过的催化剂流化并且将其加热到575c。将含有48.25%c和5.96%h和0.62%灰分的有98%颗粒为0.25到1.4mm(14-60目)的经研磨硬木球粒馈入进料料斗中并且用3.2slpm的n2载体流以4.7g/分钟的速率装入反应器中,持续225分钟以获得1059.8g生物质(6.5g灰分)的总进料,并且以2.9g/分钟的速率添加新鲜催化剂。在反应器的出口处计量稳定固体流以保持总床在恒定体积下。在一系列冷阱中收集蒸气产物,并且收集不可冷凝的气体产物并且取样。使从反应器收集的冷却固体通过60目筛(250微米)以分离282.5g指定为催化炭的大于0.25mm的颗粒部分和指定为焦化催化剂的小于0.25mm的颗粒部分。炭的代表性样品的显微照片呈现于图4中。通过筛分将炭样品分离为如表1中指定的部分。一定的颗粒断裂产生小于0.25mm的材料。将每个部分干燥以提供炭的水分含量(干燥损失,lod)。使经干燥的材料燃烧以提供炭的有机物含量(灼烧损失,loi)。将部分的经干燥的样品送到galbraithlaboratories用于碳和氢分析。氧通过差异计算并且数据收集于表2中。将残余物称重以获得无机物含量。如从显微照片可以看出,炭颗粒相对很大并且不规则地成形,而催化剂颗粒小得多并且大致是球形。因此,未曾经历粉碎的炭/催化剂混合物通常将含有体积平均尺寸比催化剂颗粒的体积平均尺寸大至少10倍的炭颗粒。通过压汞法评估炭的20-40目(850-425微米)和40-60目(425-250微米)颗粒部分的堆积、颗粒和骨架密度。堆积密度定义为材料的质量除以呈松散填充形式的材料所占据的体积;其包括固体颗粒的体积、颗粒之间的空隙和内部孔隙体积。颗粒密度是每个颗粒的密度;其包括内部孔隙体积但排除了颗粒之间的空隙。骨架密度通过用材料的质量除以材料的固体骨架的体积来计算,所述体积通过从堆积体积减去获自压汞测量值的空隙和内部孔隙的体积来测定(质量/(堆积体积-总压hg体积));其仅包括固体材料。数据收集于表3中。通过在马弗炉中在600c下燃烧两小时使20-40目(850-425微米)和40-60目(425-250微米)炭部分的样品再生,以去除所有有机物并且产生包含无机材料的残余物。获得无机残余物的粒度分布(psd)。psd分析存在两个峰。集中于约100微米的大峰分配为催化剂,并且集中于约15微米的较小峰分配为灰分。将每个峰下的区域的积分用以估算催化剂与灰分颗粒之间的体积比率。根据催化剂与炭的堆积密度,计算每一者的炭的重量分数,并且以初始炭部分的质量百分比形式呈现于表3中。图5呈现了从cfp过程分离的炭的两种部分的组成的比较。表1.通过粒度分离的炭部分.表2.通过燃烧各种炭部分产生的燃烧产物的碳、氢和氧组成.筛尺寸碳氢氧(1)碳分布氢分布目重量%重量%重量%%%10-1494.95.11.014-2093.33.03.631.532.720-4090.02.97.054.956.640-6080.53.116.48.810.660-23097.4<12.63.6>23079.8<120.20.2(1)氧通过差异计算。表3.催化剂和两种炭部分的颗粒密度的压汞测定值.实施例3。炭和催化剂的温度编程氧化(tpo)通过将获自实施例2中的流化床反应器中的生物质cfp的催化炭与新鲜商业流化床催化剂样品(在550℃下锻烧2h)混合,制得催化炭与催化剂混合物。在混合之前将催化炭研磨成小粒度。最终混合物含有2重量%催化炭和98重量%催化剂。将19.5mg的一部分混合物放在铂盘中,并且在tga室(tga:shimadzutga-50)中在流动空气(50ml/min)中在120℃下处理20min以去除水分。在预处理之后,在相同气流下使温度以30℃/min的斜变速率升高到900℃。通过tga天平监测并且连续记录样品的重量。数据呈现于图6中。炭和二氧化硅的温度编程氧化(tpo)通过将一部分获自实施例2中的流化床反应器中的生物质cfp的20-40目(850-425微米)催化炭与失活硅胶(在800℃下在空气中失活10h)混合,制备催化炭与二氧化硅混合物。样品含有2重量%催化炭和98重量%硅胶。将18.5mg的一部分混合物放在铂盘中,并且在tga室(tga:shimadzutga-50)中在流动空气(50ml/min)中在120℃下处理20min以去除水分。在预处理之后,在相同气流下使温度以30c/min的斜变速率从120c升高到900c。通过tga天平监测并且连续记录样品的重量。数据呈现于图6中。焦化催化剂的温度编程氧化(tpo)直接从实施例2中的流化床反应器中的生物质cfp获得焦化催化剂样品。将18.5mg的一部分焦化催化剂放在铂盘中,并且在tga室(tga:shimadzutga-50)中在流动空气(50ml/min)中在120℃下处理20min以去除水分。在预处理之后,在相同气流下使温度以30c/min的斜变速率从120c升高到900c。通过tga天平监测并且连续记录样品的重量。数据呈现于图6中。在图6中,已经将三种tpo实验的数据标准化以对于三种样品得到类似峰高度,并且重量变化值绘于y轴上相较于温度绘于x轴上。炭-催化剂和炭-二氧化硅混合物的最大重量变化在470-473c下发生,而焦化催化剂的最大重量变化在584c下发生。炭含有约64%碳和26%催化剂,而焦化催化剂含有约2%碳。20-40目(850-425微米)炭样品的小于1%的重量损失是由于焦化催化剂上的含于其中的碳,如通过集中于470c和584c的tpo峰下的相对面积测定。图7展示了以上tpo实验中炭-催化剂混合物和焦化催化剂样品的累积重量损失作为300-700c范围内的温度的函数。炭-催化剂混合物样品在约350c与650c之间的所有温度下都展示比焦化催化剂样品更大的分数重量损失。在tpo实验中,催化剂炭混合物样品在约426c下展示20%重量损失,而焦化催化剂样品在426c下展示小于4%重量损失,并且焦化催化剂样品在高于炭的温度(约528c)下展示20%重量损失。在tpo实验中,催化剂炭混合物样品在约468c下展示50%重量损失,而焦化催化剂样品在468c下展示仅约7%重量损失,并且焦化催化剂样品在高于炭的温度(约577c)下展示50%重量损失。在tpo实验中,炭-催化剂样品在约528c下展示约90%重量损失,而焦化催化剂样品在528c下展示仅约19%重量损失;并且焦化催化剂样品在远高于炭的温度(约633c)下展示90%重量损失。图7中呈现的实验数据证明,焦炭从焦化催化剂的氧化去除在远高于cfp过程中制得的炭氧化的温度下发生。实施例4.炭从固体混合物的静电分离通过筛分将来自硬木经zsm-5的流化床cfp反应的固体材料样品从固体混合物分离。将类似于图4中展示的材料、包含催化剂颗粒和炭的保留于250微米(60目)尺寸筛上的材料用于这个实验。使用研钵和研杵手工地研磨2.04克这种材料的样品,直到直呈现为细粉并且所有大颗粒都被压碎。样品含有25.06%碳。静电分离设备展示于图8中。在图8中展示的设备中,将压碎的材料样品装载到12.7mm(0.5英寸)od聚碳酸酯管(5)中,并且通过0.5微米玻璃料(6)保持就位。经由橡胶接头(2)和经由连接到地面的不锈钢接头(4)连接18.5mm(0.75英寸)od不锈钢收集管(3)。将铜电极(1)使用穿孔塑料圆盘(未展示)插入到收集管中以保持其居中同时仍考虑到气流。将高电压供应打开并且慢慢地使其达到恰好低于允许电荷从电极跳到收集板所观察到的电压的安全水平,约6.4kv。在电极通电的情况下,将n2流引发通过配件7并且调节到250ml/min。在30分钟之后,使流动停止并且关闭电极。小心地拆下收集管,并且从收集管(3)和从其下方的还原配件(4)收集0.36g分离的炭。收集床中剩余的1.60g材料。对分离的炭的分析表明其含有61.62%碳,并且剩余固体残余物含有14.26%碳。来自类似cfp实验的焦化催化剂的单独样品含有1.6%碳。与样品混合物相比,转移到收集器的材料是碳富集的,而固体残余物是碳耗尽的。对分离的炭样品和残余物进行组成分析,并且结果收集于表4中。表4.静电分离中未分离的炭、分离的炭和残余物的组成分析。值是每种元素的质量百分比.实施例4的结果显示,炭可以通过静电分离从催化剂/炭混合物选择性分离。通过静电分离而分离的炭是钙和碳富集的并且是硅和氧化铝耗尽的,证明至少一部分aaem与炭一起被选择性去除;并且残余物在催化剂中选择性富集,如与未分离的炭相比增加的si和al浓度所示。当前第1页12