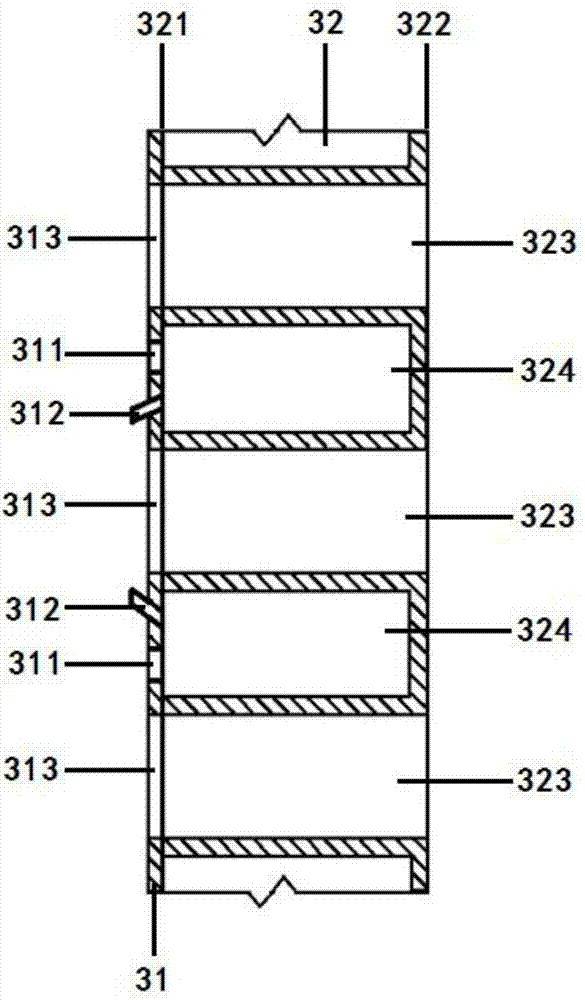
本发明涉及汽车设计和制造的
技术领域:
,更具体地说,本发明涉及一种汽车尾气处理装置。
背景技术:
:随着国内汽车数量的不断增加,尾气造成的环境的污染问题日趋严重。因此,国家对汽车尾气排放的标准也不断更新、日渐严格。据悉,“国六”标准预计将从2020年开始全面实施。“国六”标准基于国际标准制定,是对国五标准的升级,它会成为全球最严格的标准之一。“国六”的排放标准要比“国五”严格30%以上。在排除了工况和测试影响的情况下,汽油车辆关于一氧化碳的排放量降低50%。总碳氢化物和非甲烷总烃的排放量要下降50%。氮氢化合物排放也要下降42%。而汽车尾气处理装置成了车辆排放水平达到“国六”水平的必备装置。在现有技术中,汽车尾气处理装置一般通过触媒催化剂来降低有害废气排放。在触媒催化剂中贵金属原子产生各种不同的过渡反应来提高废气转化成无害气体例如水或二氧化碳的反应机率,而触媒催化剂在化学反应后仍然保持原来的状态,触媒催化剂不仅有良好的使用寿命,也避免了长期使用后被阻塞的可能性,然而由于尾气经过触媒催化剂各部分的流速分布不均匀(例如外缘处流速较慢),而且存在温度波动,导致各不同部位的尾气处理量不均衡,导致转化效率降低,使得实际排放的尾气难以达到“国六”标准。技术实现要素:为了解决现有技术中的上述技术问题,本发明的目的在于提供一种汽车尾气处理装置及其制备方法。一种汽车尾气处理装置,包括进气端、排气端以及设置在所述进气端与所述排气端之间的处理腔室,所述处理腔室内设置有用于处理汽车尾气的三元催化剂;其特征在于:所述进气端与所述处理腔室之间设置有气流分配板,所述气流分配板由导流板和分配板组成,并且所述导流板位于所述进气端一侧,而所述分配板位于所述处理腔室一侧。其中,所述分配板包括与所述导流板内侧接触的第一表面,以及位于所述处理腔室一侧的第二表面;所述分配板上形成有多个自所述第一表面延伸至第二表面的通孔,以及多个从第一表面朝向第二表面部分延伸形成内部空间的不通孔;所述导流板上设置有多个与所述分配板的通孔对齐的通孔,所述导流板上还设置有与所述不通孔的内部空间连通的进气口以及排气管,所述排气管自所述导流板的外侧伸入所述进气端的空腔,并且所述排气管的轴线方向与所述导流板的法线方向倾斜。其中,所述进气口的面积是所述排气管的出口面积的2倍以上。其中,所述导流板和分配板的垂直截面为圆形。其中,所述分配板上的通孔与所述不通孔交替错开分布。其中,所述分配板上的通孔形成多个同心环,而所述不通孔形成多个同心环,并且所述通孔的同心环与所述不通孔的同心环交替分布。其中,所述排气管的轴线方向与所述导流板的法线方向倾斜角度为30°~60°。其中,所述三元催化剂包括位于载体上的镍-钼-钇第一催化剂层,以及铈-锆-铂-钯第二催化剂层。其中,所述载体为由堇青石制成的蜂窝基体,在所述第一催化剂层中,每升载体中镍的负载量为10~20g,钼的负载量为0.5~2.0g,钇的负载量为1.0~5.0。其中,在所述第二催化剂层中,每升载体中氧化铈的负载量为25~30g、氧化锆的负载量为25~30g、铂的负载量为0.30~0.50g、钯的负载量为2.0~2.5g。本发明的汽车尾气处理装置具有以下有益效果:本发明的汽车尾气处理装置能够使尾气进入处理腔室时流动平顺,使得气流在处理腔室截面分布均匀,从而可以避免某些部位的催化剂没有达到正常效能而某些部位的催化剂超负荷,有利于延长催化剂的使用寿命。附图说明图1为本发明的汽车尾气处理装置的结构示意图。图2为汽车尾气处理装置中的气流分配板的部分剖视结构示意图。图3为汽车尾气处理装置中采用的三元催化剂的示意图。具体实施方式以下将结合具体实施例对本发明所述的汽车尾气处理装置做进一步的阐述,以帮助本领域的技术人员对本发明的发明构思、技术方案有更完整、准确和深入的理解。如图1所示,本发明的汽车尾气处理装置,包括进气端10、排气端20以及设置在进气端10与排气端20之间的处理腔室50,处理腔室50内设置有用于处理汽车尾气的三元催化剂51。在本发明中所述的三元催化剂系指汽车中的ch、co以及nox三种主要有害成分均有催化活性的催化剂。所述进气端10与所述处理腔室50之间设置有气流分配板30。如图2所示,所述气流分配板30由导流板31和分配板32组成,并且所述导流板31位于所述进气端10一侧,而所述分配板32位于所述处理腔室50一侧。所述分配板32包括与所述导流板31内侧接触的第一表面321,以及位于所述处理腔室一侧的第二表面322;所述分配板32上形成有多个自所述第一表面延伸至第二表面的通孔323,以及多个从第一表面朝向第二表面部分延伸形成内部空间的不通孔324;所述导流板31上设置有多个与所述分配板的通孔323对齐的通孔313,所述导流板31上还设置有与所述不通孔的内部空间连通的进气口311以及排气管312,所述排气管312自所述导流板31的外侧伸入进气端10的空腔,并且所述排气管312的轴线方向与所述导流板31的法线方向倾斜,所述排气管的轴线方向与所述导流板的法线方向倾斜角度优选为30°~60°,将所述排气管的轴线方向与所述导流板的法线方向倾斜从而能够形成平行于气流板30表面的气流分量,有利于尾气气流从中间向四周分散,从而有利于在截面上获得分布均匀的气流,所述进气口311的面积是所述排气管312的出口面积的2倍以上,通过调节进气口的面积、进气口与排气管的出口的面积比、排气管的倾斜角度,从而可以调节在平行于气流板30表面的气流分量,进而可以在截面上获得分布均匀的气流。具体来说,所述处理腔室的截面为圆形,而相应地,所述导流板和分配板的垂直截面也为圆形,而所述分配板上的通孔与所述不通孔交替错开分布。作为优选地,所述分配板上的通孔323形成多个同心环,而所述不通孔324形成多个同心环,并且所述通孔的同心环与所述不通孔的同心环交替分布。在本发明中所述进口端、出口端以及处理腔室的壳体可为不锈钢材质,厚度为1.0~3.0mm,所述气流分配板30可由陶瓷材料或不锈钢材料制成,当选择不锈钢材料时,优选在所述气流分配板30表面形成高发射率涂层,例如可以形成氧化铝和/或氧化铬的涂层,并且涂层的厚度优选为10~50μm。另外,为了方便进口端、出口端与尾气管路的连接固定,在所述进口端、出口端上还可以设置安装法兰等部件(图中未示出)。本发明的气流分配板结构简单,无需设置复杂的导流结构(例如导流叶片以及肋板等),而且通过设置气流分配板能够使尾气进入处理腔室时流动平顺,使得气流在处理腔室截面分布均匀,能够使得处理腔室的外圆周附近的催化剂充分利用,有利于延长催化剂的使用寿命,提高催化剂的利用效率,并且保证了尾气催化转化的处理效果。在本发明中,如图3所示,本发明的汽车尾气处理装置中采用的三元催化剂51包括由堇青石制成的蜂窝基体52,在堇青石蜂窝载体上的镍-钼-钇第一催化剂层53,以及铈-锆-铂-钯第二催化剂层54。通过包含第一催化剂层组分的溶液涂覆到堇青石蜂窝载体上并加热(焙烧)来形成所述第一催化剂层53,通过包含第二催化剂层组分的浆液涂覆到第一催化剂层53上并加热(焙烧)来形成所述第二催化剂层54,然后在高温下进行热处理得到本发明所采用的三元催化剂。本发明中的堇青石蜂窝基体可以通过市购得到。作为示例性地,上述三元催化剂可通过以下方法制备得到:(1)取适量的镍、钼和钇的可溶性盐,例如硝酸镍、钼酸铵和六水硝酸钇加入水搅拌配置成水溶液(溶解的镍、钼和钇的总离子浓度约为0.1mol/l),并浸渍到500目的堇青石蜂窝基体上,然后在150℃干燥1小时,然后在空气中于500℃焙烧1小时,得到第一催化剂层。(2)取5~10重量份的氧化铈、5~10重量份的氧化锆、硝酸铂、硝酸钯和100重量的水,在空气中用搅拌器搅拌所述混合物30~60分钟得到均匀分散的浆液。将该分散的浆液涂覆到涂覆有所述第一催化剂层的堇青石蜂窝基体上,然后在150℃干燥1小时,然后在空气中于500℃焙烧1小时,得到第二催化剂层。(3)在900~1050℃热处理1~3小时,即可。在所述第一催化剂层中,每升堇青石蜂窝基体中镍的负载量为10~20g,钼的负载量为0.5~2.0g,钇的负载量为1.0~5.0。在所述第二催化剂层中,每升堇青石蜂窝基体中含有:氧化铈的负载量为25~30g、氧化锆的负载量为25~30g、铂的负载量为0.30~0.50g、钯的负载量为2.0~2.5g。实施例1选择500目的堇青石蜂窝基体作为载体,取硝酸镍、钼酸铵和六水硝酸钇加入水搅拌配置成水溶液,并浸渍到载体上,然后在150℃干燥1小时,然后在空气中于500℃焙烧1小时,得到第一催化剂层。取氧化铈、氧化锆、硝酸铂、硝酸钯和水,在空气中用搅拌器搅拌所述混合物30分钟得到均匀分散的浆液。将该分散的浆液涂覆到涂覆有所述第一催化剂层的堇青石蜂窝基体上,然后在150℃干燥1小时,然后在空气中于500℃焙烧1小时,得到第二催化剂层。在第一催化剂层中,每升载体中镍的负载量为18g,钼的负载量为1.2g,钇的负载量为2.0g。在第二催化剂层中,每升载体中氧化铈的负载量为30g、氧化锆的负载量为25g、铂的负载量为0.35g、钯的负载量为2.5g。然后在1000℃下热处理2小时。实施例2选择500目的堇青石蜂窝基体作为载体,取硝酸镍、钼酸铵和六水硝酸钇加入水搅拌配置成水溶液,并浸渍到载体上,然后在150℃干燥1小时,然后在空气中于500℃焙烧1小时,得到第一催化剂层。取氧化铈、氧化锆、硝酸铂、硝酸钯和水,在空气中用搅拌器搅拌所述混合物30分钟得到均匀分散的浆液。将该分散的浆液涂覆到涂覆有所述第一催化剂层的堇青石蜂窝基体上,然后在150℃干燥1小时,然后在空气中于500℃焙烧1小时,得到第二催化剂层。在第一催化剂层中,每升载体中镍的负载量为20g,钼的负载量为1.0g,钇的负载量为3.0g。在第二催化剂层中,每升载体中氧化铈的负载量为30g、氧化锆的负载量为25g、铂的负载量为0.40g、钯的负载量为2.3g。然后在1000℃下热处理2小时。比较例1选择500目的堇青石蜂窝基体作为载体,取氧化铈、氧化锆、硝酸铂、硝酸钯和水,在空气中用搅拌器搅拌所述混合物30分钟得到均匀分散的浆液。将该分散的浆液涂覆到堇青石蜂窝基体上,然后在150℃干燥1小时,然后在空气中于500℃焙烧1小时,然后在1000℃下热处理2小时后,催化剂的比表面积为46m2/g(采用氮气吸附法测量),并且每升载体中氧化铈的负载量为40g、氧化锆的负载量为40g、铂的负载量为0.60g、钯的负载量为2.3g。比较例2选择500目的堇青石蜂窝基体作为载体,取硝酸镍、硝酸铜和六水硝酸钇加入水搅拌配置成水溶液,并浸渍到载体上,然后在150℃干燥1小时,然后在空气中于500℃焙烧1小时,得到第一催化剂层。取氧化铈、氧化锆、硝酸铂、硝酸钯和水,在空气中用搅拌器搅拌所述混合物30分钟得到均匀分散的浆液。将该分散的浆液涂覆到涂覆有所述第一催化剂层的堇青石蜂窝基体上,然后在150℃干燥1小时,然后在空气中于500℃焙烧1小时,得到第二催化剂层。在第一催化剂层中,每升载体中镍的负载量为20g,铜的负载量为0.8g,钇的负载量为3.0g。在第二催化剂层中,每升载体中氧化铈的负载量为30g、氧化锆的负载量为25g、铂的负载量为0.40g、钯的负载量为2.3g。然后在1000℃下热处理2小时。比较例3选择500目的堇青石蜂窝基体作为载体,取硝酸镍和钼酸铵加入水搅拌配置成水溶液,并浸渍到载体上,然后在150℃干燥1小时,然后在空气中于500℃焙烧1小时,得到第一催化剂层。取氧化铈、氧化锆、硝酸铂、硝酸钯和水,在空气中用搅拌器搅拌所述混合物30分钟得到均匀分散的浆液。将该分散的浆液涂覆到涂覆有所述第一催化剂层的堇青石蜂窝基体上,然后在150℃干燥1小时,然后在空气中于500℃焙烧1小时,得到第二催化剂层。在第一催化剂层中,每升载体中镍的负载量为20g,钼的负载量为1.0g。在第二催化剂层中,每升载体中氧化铈的负载量为30g、氧化锆的负载量为25g、铂的负载量为0.40g、钯的负载量为2.3g。然后在1000℃下热处理2小时。将实施例2以及比较例1~3制备得到的催化剂切割成9mm×9mm×48mm的测试样品,沿着平行孔道方向包裹,并将其置于不锈钢反应管中,通入汽油车尾气模拟配气(1.6%的co、12%co2、800ppmc3h8、800ppmnox、1.9%的o2以及余量的n2,空速为60000h-1)进行催化剂起燃特性测试,以10℃/min的速度将不锈钢反应管的温度从室温升至400℃,并记录测量co、c3h8、nox的t50温度,结果显示在表1中。将实施例2以及比较例1~3的催化剂放置在2.8l的燃气发动机的尾气系统中,在950℃的温度下放置150小时,然后进行上述催化剂起燃特性测试,并记录测量co、c3h8、nox的t50温度,结果显示在表2中。表1(t50,℃)c3h8conox实施例2243237233比较例1249243241比较例2241235231比较例3245234237表2(t50,℃)c3h8conox实施例2281278273比较例1289292286比较例2316312309比较例3313307303对于本领域的普通技术人员而言,具体实施例只是对本发明进行了示例性描述,显然本发明具体实现并不受上述方式的限制,只要采用了本发明的方法构思和技术方案进行的各种非实质性的改进,或未经改进将本发明的构思和技术方案直接应用于其它场合的,均在本发明的保护范围之内。当前第1页12