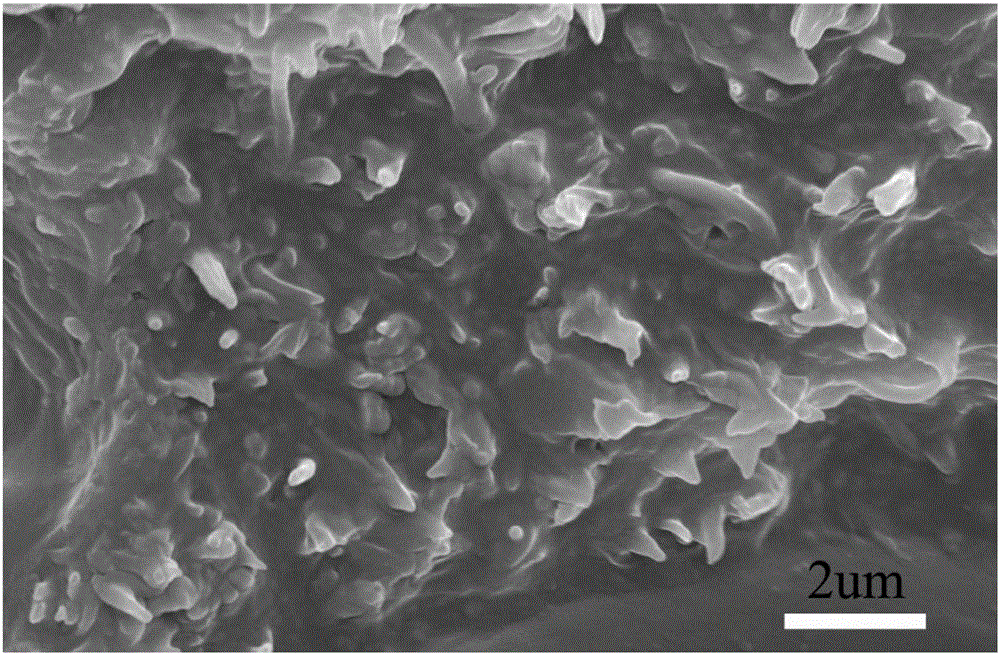
本发明涉及一种质子交换膜的
技术领域:
,特别涉及一种具有跨膜分布纳米纤维结构的质子交换膜及其制备方法。
背景技术:
:燃料电池(Fuelcell)作为一种新型能源转换装置,能够将储存在燃料和氧化剂中的化学能直接转化为电能,能源利用率高,具有广阔的应用前景。在各种不同类型的燃料电池中,直接甲醇燃料电池(DirectMethanolFuelCell,DMFC)使用甲醇水溶液或甲醇蒸汽为燃料供给来源,具有电池结构简单、原料易储存和运输和可低温快速启动等优点,近年来得到的迅猛的发展。质子交换膜(ProtonExchangeMembrane,PEM)是直接甲醇燃料电池的核心部件之一,为质子的传导提供通道,阻止甲醇的渗透扩散,并起到分隔电池阴阳极的作用,它的性能优劣直接影响燃料电池的性能。近年来,以静电纺丝技术为代表的纳米纤维制备技术为质子交换膜的质子传递通道设计提供了新的研究思路。将聚电解质纺制为纳米纤维或在纳米纤维表面固载电解质分子,可实现质子传递基团沿纳米纤维方向的取向富集分布,与成膜物质复合后可在膜内形成质子传递长通道,从而改善膜的质子传导性能。常规静电纺纳米纤维复合膜玻璃板刮涂法和溶液浸渍法制备,由于静电纺纳米纤维间结合紧密,成膜物质在纤维间隙不易填充完全,且复合膜两侧表面容易生成不含纳米纤维的质子传导能力弱的“传递壁垒层”,从而导致复合膜的质子传导能力的下降。技术实现要素:有鉴于此,本发明目的在于提供一种具有跨膜分布纳米纤维结构的质子交换膜及其制备方法,提高质子交换膜的质子传导率、降低甲醇透过率。为了实现上述发明目的,本发明提供以下技术方案:本发明提供了一种具有跨膜分布纳米纤维结构的质子交换膜的制备方法,包括以下步骤:以磺化非氟烃类聚合物为原料,采用溶液喷射纺丝法制备质子传导纳米纤维毡;以热塑性树脂为原料,采用溶液喷射纺丝法制备基质纳米纤维毡;将所述基质纳米纤维毡和质子传导纳米纤维毡间隔叠层铺叠成夹心状纳米纤维毡;所述基质纳米纤维毡为芯层,所述质子传导纳米纤维毡为面层;将所述夹心状纳米纤维毡热压,得到具有跨膜分布纳米纤维结构的质子交换膜。优选的,所述磺化非氟烃类聚合物为磺化聚醚砜、磺化聚醚醚酮、磺化聚苯并咪唑和磺化聚酰亚胺中的一种或几种的混合物。优选的,所述热塑性树脂为聚偏氟乙烯、聚丙烯和聚酯中的一种或几种的混合物。优选的,所述质子传导纳米纤维毡热压前的厚度为50~150μm;所述基质纳米纤维毡热压前的厚度为50~100μm。优选的,所述夹心状纳米纤维毡中基质纳米纤维毡的质量为夹心状纳米纤维毡总质量的10~40%。优选的,所述热压的温度为170~190℃;所述热压的压力为5~15MPa;所述热压的时间为20~60min。优选的,所述热压前还包括预热;所述预热的温度为120~160℃;所述预热的时间为1~8min。本发明提供了一种上述方案所述制备方法制备的具有跨膜分布纳米纤维结构的质子交换膜,包括热塑性树脂基质层和跨膜分布的质子传导纳米纤维。优选的,所述质子交换膜的厚度为40~120μm。本发明提供了一种具有跨膜分布纳米纤维结构的质子交换膜的制备方法,包括以下步骤:以磺化非氟烃类聚合物为原料,采用溶液喷射纺丝法制备质子传导纳米纤维毡;以热塑性树脂为原料,采用溶液喷射纺丝法制备基质纳米纤维毡;将所述基质纳米纤维毡和质子传导纳米纤维毡间隔叠层铺叠成夹心状纳米纤维毡;所述基质纳米纤维毡为芯层,所述质子传导纳米纤维毡为面层;将所述夹心状纳米纤维毡热压,得到具有跨膜分布纳米纤维结构的质子交换膜。本发明利用热压法使基质纳米纤维毡熔融后能在质子传导纤维中均匀分散并充分填充空隙,利用溶液纺丝法制备的纳米纤维具有明显的三维卷曲特性这一特点,使质子传导纳米纤维伸出膜表面,形成明显的跨膜分布结构,避免在膜两侧表面生成不含纳米纤维“传递壁垒层”,有效的扩展了质子传输通道,提高了质子交换膜的质子传输能力;并且本发明利用热塑性的树脂作为内部基质,形成有效的阻醇层,有效降低了质子交换膜的甲醇透过率。本发明提供了一种上述方案所述制备方法制备的具有跨膜分布纳米纤维结构的质子交换膜,具有良好的质子传导能力和阻醇性。实验结果表明,本发明提供的具有跨膜分布纳米纤维结构的质子交换膜的质子传导率可以达到0.178S/cm,甲醇透过率低至0.34×10-8cm2/s。附图说明图1为本发明实施例1所得质子交换膜表面的电子显微镜观测图;图2为本发明实施例1所得质子交换膜断面的电子显微镜观测图;图3为本发明实施例2所得质子交换膜表面的电子显微镜观测图;图4为本发明实施例3所得质子交换膜表面的电子显微镜观测图;图5为本发明实施例的质子交换膜结构示意图。具体实施方式本发明提供了一种具有跨膜分布纳米纤维结构的质子交换膜的制备方法,包括以下步骤:以磺化非氟烃类聚合物为原料,采用溶液喷射纺丝法制备质子传导纳米纤维毡;以热塑性树脂为原料,采用溶液喷射纺丝法制备基质纳米纤维毡;将所述基质纳米纤维毡和质子传导纳米纤维毡间隔叠层铺叠成夹心状纳米纤维毡;所述基质纳米纤维毡为芯层,所述质子传导纳米纤维毡为面层;将所述夹心状纳米纤维毡热压,得到具有跨膜分布纳米纤维结构的质子交换膜。本发明以磺化非氟烃类聚合物为原料,采用溶液喷射纺丝法制备质子传导纳米纤维毡。在本发明中,所述磺化非氟烃类聚合物优选为磺化聚醚砜(SPES)、磺化聚醚醚酮(SPEEK)、磺化聚苯并咪唑(SPBI)和磺化聚酰亚胺(SPI)中的一种或几种的混合物;所述混合物优选为2~3种磺化非氟烃类聚合物的混合物,更优选为磺化聚醚砜(SPES)和磺化聚醚醚酮(SPEEK)的混合物、磺化聚苯并咪唑(SPBI)和磺化聚酰亚胺(SPI)的混合物或磺化聚醚醚酮(SPEEK)和磺化聚苯并咪唑(SPBI)的混合物。在本发明中,所述质子传导纳米纤维毡热压前的厚度优选为50~150μm,更优选为80~120μm;所述质子传导纳米纤维毡的克重优选为15~45g/m2,更优选为25~35g/m2;所述质子传导纳米纤维毡的纤维直径优选为50~800nm,更优选为100~600nm,最优选为200~300nm。本发明优选将磺化非氟烃类聚合物配制成纺丝溶液,再使用溶液喷射纺丝法进行纺丝;所述磺化非氟烃类聚合物用的纺丝溶剂优选为N,N二甲基乙酰胺、丙酮和氯仿中的一种或几种的混合物,所述纺丝溶液中磺化非氟烃类聚合物的质量浓度优选为30~40%,更优选为35~38%。在本发明中,所述溶液喷射纺丝法制备质子传导纳米纤维毡优选包括以下步骤:将磺化非氟烃类聚合物和纺丝溶剂混合,得到纺丝溶液;将所述纺丝溶液进行喷射纺丝,得到质子传导纳米纤维毡。在本发明中,所述喷射纺丝的喂液速度为3~10ml/h,更优选为4~8ml/h,最优选为6ml/h;所述溶液喷射纺丝的牵伸气流压力为0.05~0.5MPa;所述喷射纺丝中纺丝箱体的温度优选为60~95℃,更优选为70~90℃;所述喷射纺丝中接收帘到喷丝孔的接收距离优选为40~80cm,更优选为50~70cm。本发明对溶液喷射纺丝的装置没有特殊要求,使用本领域常规的溶液喷射纺丝装置即可。在本发明的部分具体实施例中,使用溶液喷射纺丝装置进行喷射纺丝优选包括以下步骤:利用注射泵将纺丝溶液经计量泵喂入喷丝头储液池中,纺丝液从喷丝头中挤出形成纺丝液细流,纺丝液细流通过牵伸气流的牵伸细化后进入纺丝箱体,形成纤维,利用风机将纤维收集并凝聚在接收网帘上,得到质子传导纳米纤维毡;在牵伸气流和纺丝箱体加热的共同作用下,纺丝液细流中的溶剂挥发形成纤维。本发明以热塑性树脂为原料,采用溶液喷射纺丝法制备基质纳米纤维毡。在本发明中,所述热塑性树脂的熔点优选为160~200℃,更优选为170~190℃;所述热塑性树脂优选为聚偏氟乙烯、聚丙烯和聚酯中的一种或几种的混合物;所述基质纳米纤维毡热压前的厚度优选为50~100μm,更优选为60~80μm;所述基质纳米纤维毡的克重优选为10~35g/m2,更优选为15~25g/m2;所述基质纳米纤维毡的纤维直径优选为50~800nm,更优选为100~600nm,最优选为200~300nm。在本发明中,所述热塑性树脂具有优异的阻醇性能,形成有效的阻醇层,有效降低了质子交换膜的甲醇透过性。在本发明中,所述采用溶液喷射纺丝法制备基质纳米纤维毡的具体方法包括:将热塑性树脂和纺丝溶剂混合,得到纺丝溶液;将所述纺丝溶液进行喷射纺丝,得到质子传导纳米纤维毡。在本发明中,所述纺丝溶液中热塑性树脂的质量浓度优选为18~25%,更优选为20~22%;所述纺丝溶剂优选独立地选自上述制备质子传导纳米纤维毡中的纺丝溶剂,在此不再赘述;所述喷射纺丝的条件和具体方法和上述制备质子传导纳米纤维毡中一致,在此不再赘述。本发明利用溶液喷射纺丝法制备基质纳米纤维毡和质子传导纳米纤维毡,利用高速气流对纺丝溶液细流进行超细拉伸并使溶剂挥发的得到纳米纤维,在纺丝箱体内部高速气流的紊流剪切作用下得到的纤维具有明显的三维卷曲特性并相互纠缠,利用这种卷曲的结构特性使基质在热压过程中能够在纤维间流动以得到更好的填充效果,并且利用纳米纤维不规则的卷曲结构构造出透膜的纳米纤维结构,避免膜两侧表面“传递壁垒层”的出现。得到基质纳米纤维毡和质子传导纳米纤维毡后,本发明将所述基质纳米纤维毡和质子传导纳米纤维毡间隔叠层铺叠成夹心状纳米纤维毡;所述基质纳米纤维毡为芯层,所述质子传导纳米纤维毡为面层。在本发明中,所述夹心状纳米纤维毡中基质纳米纤维毡的质量优选为夹心状纳米纤维毡总质量的10~40%,更优选为15~35%,最优选为20~30%;在本发明的部分具体实施例中,可以根据纤维毡的克重和厚度控制基质纳米纤维毡和夹心状纳米纤维毡总质量的质量比;在本发明的部分具体实施例中,还可以通过控制基质纳米纤维毡或质子传导纳米纤维毡的层数来达到上述质量比要求。得到夹心状纳米纤维毡后,本发明将所述夹心状纳米纤维毡热压,得到具有跨膜分布纳米纤维结构的质子交换膜。在本发明中,所述热压的温度优选为170~190℃,更优选为175~185℃;所述热压的压力优选为5~15MPa,更优选为8~12MPa;所述热压的时间优选为20~60min,更优选为30~50min;本发明优选使用平板热压机进行热压。在本发明中,所述热压前优选将得到的夹心状纳米纤维毡预热;所述预热的温度优选为120~160℃,更优选为135~155℃;所述预热的时间优选为1~8min,更优选为3~6min。所述热压后,本发明优选将热压所得复合膜热淬火到室温,得到具有跨膜分布纳米纤维结构的质子交换膜。在本发明中,所述热淬火优选为:将热压所得复合膜浸泡入水中,冷却至室温;所述热淬火用水为常温水,无需进行冷却和降温;本发明对热淬火所用水的体积没有特殊要求,能够将热压所得复合膜浸没即可。本发明利用不同聚合物材料熔点的差异,使熔点较低的基质纳米纤维毡(熔点为160~200℃)在热压过程中发生熔融,充分填到高熔点的质子传导纳米纤维毡(熔点大于300℃)的纤维空隙中,得到更加致密的质子交换膜,同时具有三维卷曲特性质子传导纳米纤维伸出膜表面,得到具有跨膜分布纳米纤维结构的质子交换膜。本发明提供了一种上述方案所述制备方法制备的具有跨膜分布纳米纤维结构的质子交换膜,包括热塑性树脂基质层和跨膜分布的质子传导纳米纤维。在本发明中,所述具有跨膜分布纳米纤维结构的质子交换膜的厚度优选为40~120μm,更优选为60~100μm,最优选为70~90μm。下面结合实施例对本发明提供的具有跨膜分布纳米纤维结构的质子交换膜及其制备方法进行详细的说明,但是不能把它们理解为对本发明保护范围的限定。实施例1以N,N-二甲基甲酰胺(DMF)为纺丝溶剂,将磺化聚醚砜(SPES)溶解于纺丝溶剂中,制备成磺化聚醚砜质量浓度为35%的溶液;利用注射泵以6mL/h的速度将纺丝液经计量泵喂入到喷丝头储液池中,纺丝液从喷丝头挤出时形成细流,细流经过高压牵伸气流(压力为0.05MPa)的牵伸细化后进入纺丝箱体(箱体温度为90℃),在高压气流和纺丝箱体的共同作用下,溶剂挥发形成纤维,利用风机将纤维收集在接收网帘(接收距离为80cm)上,得到三维卷曲的磺化聚醚砜纳米纤维毡,控制磺化聚醚砜纳米纤维毡的厚度为130μm,克重为40g/m2;以N,N-二甲基甲酰胺(DMF)为纺丝溶剂,将聚偏氟乙烯(PVDF)溶解于纺丝溶剂中,制备成聚偏氟乙烯质量浓度为20%的溶液;利用步骤1中的方法进行溶液喷射纺丝,得到聚偏氟乙烯纳米纤维毡,厚度为70μm,克重为20g/m2;然后将纤维毡平整地在平板热压机压板中铺叠成“夹心”纤维层结构,其中PVDF纤维毡置于“芯层”,上下两层为SPES纤维毡(控制PVDF纤维毡的质量为夹心状纳米纤维毡总质量的20%),将平板热压机升温到120℃,将压板及纤维毡整体转移到平板热压机,预热复合纤维层1min,预热后升温到170℃进行热压,热压压力5MPa,热压时间为60min,热压完成后将复合膜放入常温水中,热淬火到室温,可得具有跨膜分布纳米纤维结构的质子交换膜,厚度为120μm。使用扫描电子显微镜多所得质子交换膜的表面进行观测,观测结果如图1所示,根据图1可以看出,所得质子交换膜表面有大量的纳米纤维分布,纳米纤维在膜内部呈现跨膜分布状态,形成在膜的一侧表面到另一侧表面的连续质子传输通道。将所得质子交换膜切断,使用扫描电子纤维镜对断面进行观测,观测结果如图2所示;根据图2可以看出,膜内部充分被熔融的基质填充,致密无孔洞,表明本发明得到了致密完整的质子交换膜。实施例2以丙酮为纺丝溶剂,将磺化聚醚砜(SPES)和磺化聚醚醚酮(SPEEK)的混合物(混合摩尔比为1:1)溶解于纺丝溶剂中,制备成SPES和SPEEK总质量浓度为33%的溶液;利用注射泵以3mL/h的速度将纺丝液经计量泵喂入到喷丝头储液池中,纺丝液从喷丝头挤出时形成细流,细流经过高压牵伸气流(压力为0.5MPa)的牵伸细化后进入纺丝箱体(箱体温度为60℃),在高压气流和纺丝箱体的共同作用下,溶剂挥发形成纤维,利用风机将纤维收集在接收网帘(接收距离为60cm)上,得到三维卷曲的SPES/SPEEK纳米纤维毡,控制SPES/SPEEK纳米纤维毡的厚度为110μm,克重为35g/m2;以丙酮(DMF)为纺丝溶剂,将聚丙烯溶解于纺丝溶剂中,制备成聚丙烯质量浓度为20%的溶液;利用步骤1中的方法进行溶液喷射纺丝,得到聚丙烯纳米纤维毡,厚度为85μm,克重为30g/m2;然后将纤维毡平整地在平板热压机压板中铺叠成“夹心”纤维层结构,其中聚丙烯纤维毡置于“芯层”,上下两层为SPES/SPEEK纤维毡(控制聚丙烯纤维毡的质量为夹心状纳米纤维毡总质量的30%),将平板热压机升温到140℃,将压板及纤维毡整体转移到平板热压机,预热复合纤维层8min,预热后升温到180℃进行热压,热压压力8MPa,热压时间为45min,热压完成后将复合膜放入常温水中,热淬火到室温,可得具有跨膜分布纳米纤维结构的质子交换膜,厚度为100μm。使用扫描电子显微镜多所得质子交换膜的表面进行观测,观测结果如图3所示,根据图3可以看出,膜表面的纳米纤维分布情况和实施例1类似;将所得质子交换膜切断,使用扫描电子纤维镜对断面进行观测,观测结果和实施例1类似。实施例3以氯仿为纺丝溶剂,将磺化聚苯并咪唑(SPBI)和磺化聚酰亚胺(SPI)的混合物溶解于纺丝溶剂中,制备成磺化聚苯并咪唑(SPBI)和磺化聚酰亚胺(SPI)总质量浓度为25%的纺丝液;利用注射泵以5mL/h的速度将纺丝液经计量泵喂入到喷丝头储液池中,纺丝液从喷丝头挤出时形成细流,细流经过高压牵伸气流(压力为0.3MPa)的牵伸细化后进入纺丝箱体(箱体温度为75℃),在高压气流和纺丝箱体的共同作用下,溶剂挥发形成纤维,利用风机将纤维收集在接收网帘(接收距离为50cm)上,得到三维卷曲的SPBI/SPI纳米纤维毡,控制SPBI/SPI纳米纤维毡的厚度为80μm,克重为25.5g/m2;以氯仿为纺丝溶剂,将聚酯溶解于纺丝溶剂中,制备成聚酯质量浓度为20%的溶液;利用步骤1中的方法进行溶液喷射纺丝,得到聚丙烯纳米纤维毡,厚度为80μm,克重为17g/m2;然后将纤维毡平整地在平板热压机压板中铺叠成“夹心”纤维层结构,其中聚酯纤维毡置于“芯层”,上下两层为SPBI/SPI纤维毡(控制聚酯纤维毡的质量为夹心状纳米纤维毡总质量的40%),将平板热压机升温到160℃,将压板及纤维毡整体转移到平板热压机,预热复合纤维层6min,预热后升温到190℃进行热压,热压压力10MPa,热压时间为30min,热压完成后将复合膜放入常温水中,热淬火到室温,可得具有跨膜分布纳米纤维结构的质子交换膜,厚度为60μm。使用扫描电子显微镜多所得质子交换膜的表面进行观测,观测结果如图3所示,根据图3可以看出,膜表面的纳米纤维分布情况和实施例1类似。将所得质子交换膜切断,使用扫描电子纤维镜对断面进行观测,观测结果和实施例1类似。对比例1仅在铺叠步骤中将芯层替换为磺化聚醚砜纳米纤维毡,上下两层为聚偏氟乙烯纳米纤维毡,其他条件完全和实施例1相同,得到复合质子交换膜;将磺化聚醚砜纳米纤维毡置于芯层,将聚偏氟乙烯纳米纤维毡置于上下两层,热压熔融之后基质会将起到质子传导作用的磺化聚醚砜纳米纤维完全包裹,在复合膜表面两侧形成“传递壁垒层”。实施例4将实施例1~3得到的具有跨膜纳米纤维结构的质子交换膜、对比例1得到的对比质子交换膜和市场上购买的全氟磺酸膜Nafion117进行性能测试,将所得数据列于表1中;质子传导率:采用CH1660D型电化学工作站测量及其两电极检测样品膜的电阻(检测温度80℃,湿度100%),再通过式1计算质子传导率:式1中,σ:表示质子传导率,单位为(S/cm);l表示两电极之间的距离,单位为cm;t表示样品膜的厚度,单位为cm;w表示样品膜的宽度,单位为cm,R表示样品膜的电阻,单位为Ω。甲醇透过率:利用气相色谱法检测质子交换膜的甲醇透过率。表1实施例1~3、对比例1和全氟磺酸膜Nafion117的性能检测结果样品实施例1实施例2实施例3对比例1全氟磺酸膜Nafion117质子传导率(S/cm)0.1780.1450.120.050.1162甲醇透过率(cm2s-1)1.69×10-81.22×10-80.34×10-80.34×10-814.1×10-7根据表1可以看出,本发明提供的具有跨膜纳米纤维结构的质子交换膜质子传导率高,且甲醇透过率小,说明本发明提供的质子交换膜内部跨膜纳米纤维的存在,可以有效打破膜表面“绝缘层”的影响,从而实现质子的高效传递;根据对比例的检测结果可知膜表面形成传递壁垒层会大大降低膜的质子传导性能;全氟磺酸膜Nafion117质子传导率低于本发明得到的质子交换膜,且其甲醇透过率很高,阻醇性能差,本发明所得的具有跨膜纳米纤维结构的质子交换膜的性能明显优于对比例和全氟磺酸膜Nafion117。由以上实施例可知,本发明提供的制备方法制备的具有跨膜纳米纤维结构的质子交换膜性能优异,可以有效打破膜表面“传递壁垒层”的影响,提高质子传递效率;并且本发明提供的制备方法简单,开发出了利用热压法之额比质子交换膜的新方法,大大降低了质子交换膜的制备成本。以上所述仅是本发明的优选实施方式,应当指出,对于本
技术领域:
的普通技术人员来说,在不脱离本发明原理的前提下,还可以做出若干改进和润饰,这些改进和润饰也应视为本发明的保护范围。当前第1页1 2 3