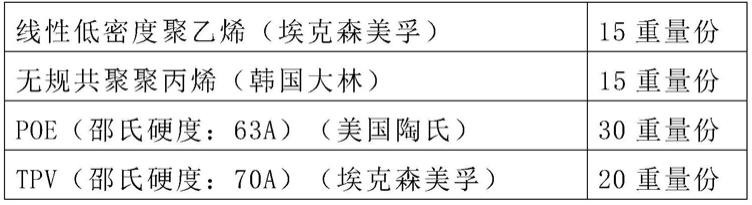
一种无胶水的tpo人造革及其制造方法
技术领域
1.本发明涉及一种无胶水的tpo人造革及其制造方法,其中,该tpo人造革能够缝制并适用于汽车座椅。
背景技术:2.汽车内饰材料广泛使用各种人造革。目前,汽车座椅面料基本采用聚氯乙烯(pvc)人造革或者聚氨酯(pu)人造革。pvc座椅材料的结构一般分为四层,由下至上分别是基布、pvc发泡层、pvc致密层和表面油漆层。由于pvc产品含有增塑剂,增塑剂很容易运动迁移出来,造成材料变硬变脆,在折损疲劳时很容易出现表面龟裂,特别是低温加剧脆化等问题。此外由于高温pvc会降解,所以pvc人造革的耐高温性能不好,容易产生黄变。
3.为了避免pvc人造革的上述缺陷,人们尝试开发其他种类的人造革,例如tpo人造革。对此,现有技术中公开了不同的方法制造各种性能改进的tpo汽车内饰材料。
4.cn107351495a公开了一种多色tpo汽车内饰材料,自下而上包括聚烯烃海绵层、多色tpo表皮层和水性聚氨酯涂层,其中该多色tpo表皮层是由至少两个单色tpo表皮复合拼接而成。通过对各种色彩进行自由组合搭配,能够实现对内饰材料的个性化要求。
5.cn106380772a公开了一种基于sebs的环保型tpo汽车内饰材料,包括tpo表皮层和海绵层,其中的tpo表皮层包含50至80份sebs、10至20份聚丙烯、10至20份增粘树脂、5至20份均聚聚丙烯;海绵层包括35-60份聚丙烯、40至55份增韧材料、15至25份橡胶、20至30份发泡剂。该tpo内饰材料具有低气味和低voc的特性。
6.cn106393890a公开了一种软质环保型tpo汽车内饰材料,包括tpo表皮层和海绵层,其中的tpo表皮层包含10至40份低密度聚乙烯、10至40份聚丙烯、10至40份增粘树脂、30至60份橡胶;海绵层包含35至60份聚丙烯、40至55份增韧材料、15至25份橡胶、20至30份发泡剂。该tpo内饰材料降低了挥发性有机物质(voc)的含量,提高了产品的环保性。
7.然而,现有技术中的这些常规的tpo产品只能用于门板和仪表盘,尚不能满足汽车座椅面料的标准和性能。这是因为,一方面,海绵层导致材料的柔软度不符合座椅面料,并且不易于手工包覆,含海绵层的tpo内饰材料一般用于热塑性加工;另一方面,即使将海绵层简单替换为基布层,从而可缝纫,但是常规的缝纫tpo硬度和刚度都太大,并且韧性以及耐揉皱性能不好,不易手工包覆,容易产生折痕等问题,无法满足座椅性能的测试标准。
8.另外,为了提高tpo表皮层与基布的粘结力,普通的缝纫tpo跟基布之间都需要加上胶水。然而,胶水层的加入一方面会使得材料手感变硬,voc会提升;另一方面在生产线使用胶水增加一道工序,成本增加而且不易操作。
技术实现要素:9.基于上述现有技术,本发明的目的在于提供一种无胶水的tpo人造革。该tpo人造革能够在不需要胶水的情况下提高基布层与tpo表皮层之间的粘结,从而使得tpo表皮层更加容易且可靠地跟基布贴合。本发明的目的还在于提供一种用于制造该无胶水的tpo的方
法。
10.上述目的通过根据本发明的tpo人造革及其制造方法实现。
11.对此,本发明首先提出一种无胶水的tpo人造革,该tpo人造革自下而上至少包含基布层和tpo表皮层,tpo表皮层包含:
12.10至30重量份,例如10重量份、11重量份、12重量份、13重量份、14重量份、15重量份、16重量份、17重量份、18重量份、19重量份、20重量份、21重量份、22重量份、23重量份、24重量份、25重量份、26重量份、27重量份、28重量份、29重量份、30重量份或者这些数值中任两者之间范围内的聚乙烯,
13.10至30重量份,例如10重量份、11重量份、12重量份、13重量份、14重量份、15重量份、16重量份、17重量份、18重量份、19重量份、20重量份、21重量份、22重量份、23重量份、24重量份、25重量份、26重量份、27重量份、28重量份、29重量份、30重量份或者这些数值中任两者之间范围内的聚丙烯,
14.20至70重量份,例如20重量份、21重量份、22重量份、23重量份、24重量份、25重量份、26重量份、27重量份、28重量份、29重量份、30重量份、31重量份、32重量份、33重量份、34重量份、35重量份、36重量份、37重量份、38重量份、39重量份、40重量份、41重量份、42重量份、43重量份、44重量份、45重量份、46重量份、47重量份、48重量份、49重量份、50重量份、51重量份、52重量份、53重量份、54重量份、55重量份、56重量份、57重量份、58重量份、59重量份、60重量份、61重量份、62重量份、63重量份、64重量份、65重量份、66重量份、67重量份、68重量份、69重量份、70重量份或者这些数值中任两者之间范围内的弹性体,
15.5至40重量份,例如5重量份、6重量份、7重量份、8重量份、9重量份、10重量份、11重量份、12重量份、13重量份、14重量份、15重量份、16重量份、17重量份、18重量份、19重量份、20重量份、21重量份、22重量份、23重量份、24重量份、25重量份、26重量份、27重量份、28重量份、29重量份、30重量份、31重量份、32重量份、33重量份、34重量份、35重量份、36重量份、37重量份、38重量份、39重量份、40重量份的烯烃类增粘树脂。
16.在此,提高tpo表皮层与基布之间粘结力的关键在于添加了增粘树脂,尤其是烯烃类增粘树脂。而且,该增粘树脂同时也能够提高柔软度。烯烃类增粘树脂具有特别良好的相容性,获得的tpo人造革具有平滑的表面。如果增粘树脂含量太低,对体系粘度改善不够,无法达到粘结力要求;如果增粘树脂含量太高,则可能导致体系粘度太高,加工性能差,产品耐热等性能变差。
17.根据本发明的一个优选实施方式,烯烃类增粘树脂为乙烯-醋酸乙烯共聚物(eva)或者乙烯-丙烯酸共聚物(eaa)。乙烯-醋酸乙烯共聚物(eva)和乙烯-丙烯酸共聚物(eaa)能够有效地增加体系粘度,增加与基布的粘结力。
18.根据本发明的一个优选实施方式,当所述烯烃类增粘树脂为乙烯-醋酸乙烯共聚物时,所述乙烯-醋酸乙烯共聚物中的醋酸乙烯(va)含量为5至45重量%;当所述烯烃类增粘树脂为乙烯-丙烯酸共聚物时,所述乙烯-丙烯酸共聚物中的丙烯酸(aa)含量为5至45重量%。这里提到的含量基于增粘树脂总量。eva中的va含量以及eaa中的aa含量对于产品的性能有重要影响。如果eva中的va含量或eaa中的aa含量太低,对体系粘度改善不够,无法达到粘结力要求;如果含量太高,则可能导致体系粘度太高,加工性能差,无法挤出成型。
19.本发明中tpo表皮层中的聚乙烯原则上可以使用任何常规的聚乙烯,例如高密度
聚乙烯、低密度聚乙烯等。根据本发明的一个优选实施方式,所述聚乙烯是线性低密度聚乙烯。在tpo表皮层中加入线性低密度聚乙烯(lldpe),其由于相比于非线性ldpe和hdpe具有更小的密度以及更低的硬度,能够实现明显改善的柔软度。
20.本发明中tpo表皮层中的聚丙烯包括均聚聚丙烯和共聚聚丙烯,并且可以涉及等规聚丙烯、无规聚丙烯、间规聚丙烯等。根据本发明的一个优选实施方式,所述聚丙烯是无规共聚聚丙烯,例如乙烯丙烯无规共聚聚丙烯等。相对于其他类型的聚丙烯,无规共聚聚丙烯的硬度更小,能够帮助实现改善的柔软度。
21.本发明中tpo表皮层中的弹性体原则上可以使用任何常规已知的弹性体,例如epdm橡胶、聚氨酯弹性体、sbs弹性体、poe弹性体等。根据本发明的一个优选实施方式,所述弹性体包含热塑性硫化胶(tpv)和乙烯-α烯烃共聚弹性体(poe),优选含有10至30重量份的热塑性硫化胶以及20至50重量份的乙烯-α烯烃共聚弹性体。热塑性硫化胶能够提供人造革光泽和花纹良好的保持性能,并提高耐老化性能。
22.根据本发明的一个优选实施方式,所述热塑性硫化胶的邵氏硬度为45-75a。tpv的邵氏硬度a(按照iso868测定)对产品性能具有重要影响。如果tpv的邵氏硬度a过大,则会造成手感硬且刚度大,因而不能满足汽车座椅面料的性能;如果tpv的邵氏硬度a过小,则会造成产品发粘出油,加工性能劣化。另外,tpv的邵氏硬度对于tpo表皮层与基布之间的粘接性也产生影响,粘接性随着tpv硬度的减小而增大。
23.根据本发明的一个优选实施方式,所述乙烯-α烯烃共聚弹性体的邵氏硬度为45-70a。poe的邵氏硬度a(按照iso868测定)也对产品性能具有重要影响,只有在poe的邵氏硬度a在本发明限定范围内时,才能同时保证良好的柔软度和加工性。另外,poe的邵氏硬度对于tpo表皮层与基布之间的粘接性也产生影响,粘接性随着poe硬度的减小而增大。
24.优选地,同时加入热塑性硫化胶(优选充油胶)以及乙烯-α烯烃共聚弹性体,在该情况下,与传统配方相比,在降低硬度和提高柔软度的同时也提高了产品的韧性,由此使得耐揉皱性和耐弯折性能提高,从常规材料在常温下揉皱1至2万次就破裂显著改进到在常温下揉皱10万次不破裂,完全达到甚至超过对汽车座椅的要求。表皮柔软度通过下垂测试从100-120mm降低到50-80mm,刚度显著减小,手感变软,由此达到座椅面料的性能标准。
25.根据本发明的一个优选实施方式,热塑性硫化胶使用充油胶,特别是低硬度的充油胶,优选使用石蜡油或烷烃油以10-30%的充油量(基于tpv总量)进行充油。如果使用其他非充油胶,或者说采用其他的充油类型或充油量,可能导致voc含量增大,不满足要求,容易析出。
26.根据本发明的一个优选实施方式,乙烯-α烯烃共聚弹性体中的α烯烃单体占poe总重的含量为30-60%,其中,α烯烃单体优选辛烯。α烯烃单体的含量对于poe的硬度具有重要影响。如果α烯烃单体含量过低,则poe中的聚乙烯pe份额增多,其导致结晶度增大,硬度和刚度提高;如果α烯烃单体的含量过高,则poe中的pe被过多打断,增大共聚难度,难以加工。另外,辛烯作为α烯烃单体能够提供特别理想的塑性和柔软度。
27.根据本发明的一个优选实施方式,tpo表皮层包含2至10重量份,例如2重量份、3重量份、4重量份、5重量份、6重量份、7重量份、8重量份、9重量份、10重量份或者这些数值中任两者之间范围内的添加剂。添加剂主要包括耐热稳定剂以及加工助剂、如润滑剂等,可根据需要选择本领域技术人员熟知的常规材料。
28.根据本发明的一个优选实施方式,tpo表皮层包含2至8重量份的色母粒,例如2重量份、3重量份、4重量份、5重量份、6重量份、7重量份、8重量份或者这些数值中任两者之间范围内的色母粒。根据需要,额外选择性地在tpo组合物中添加色母粒,能够帮助满足产品的不同颜色要求。
29.根据本发明的一个优选实施方式,在tpo表皮层上方设有油漆层。可以采用本领域已知的常规油漆进行表面涂覆。本发明中优选采用水性聚氨酯油漆,其包含10至30重量份的水、30至60重量份的聚氨酯、5至10重量份的固化剂以及5至15重量份的助剂。通过在tpo材料表面印刷油漆而进行表面处理,能够有利地改善获得的tpo人造革表面的光泽、手感以及耐光、耐热、耐脏、耐磨、耐刮及其他功能性。
30.根据本发明的一个优选实施方式,基布层为针织布或无纺布,优选是双面针织布。基布层能够提高皮革的柔软度,使得皮革易于在常温下手工包覆。其中,针织布比梭织布等其他的布具有更软的手感。
31.相应地,本发明还提出一种用于制造前述根据本发明的tpo人造革的方法,包含下述步骤:
[0032]-挤出tpo表皮层,所述tpo表皮层中包含
[0033]
10至30重量份的聚乙烯,优选线性低密度聚乙烯,
[0034]
10至30重量份的聚丙烯,优选无规共聚聚丙烯,
[0035]
20至70重量份的弹性体,
[0036]
5至40重量份的烯烃类增粘树脂,
[0037]-复合底部的基布层。
[0038]
tpo表皮层与基布层的复合可以直接通过热压复合实现。
[0039]
前述tpo人造革的各项特征均适用于其制造方法。
[0040]
对于构成本发明的tpo人造革的各层厚度没有特别要求。本领域技术人员可以根据具体要求选择合适的厚度。
[0041]
本发明的tpo人造革能够应用在汽车内饰中,尤其满足汽车座椅面料的性能要求。当然,根据本发明所述的tpo人造革也能够应用于类似汽车内饰的其他领域中。
[0042]
本发明的优点在于:
[0043]
首先,与传统配方相比,体系中添加烯烃类增粘树脂,可以显著提高表皮与基布的粘结力。常规技术中,在不适用额外胶水的情况下,tpo表皮层与基布层之间的粘结力一般为10-20n/5cm左右。经过本发明改善的粘结力则可以达到30n/5cm以上,甚至接近50n/5cm或者撕不开的效果。由此,即使不使用胶水,粘结力也与使用胶水的情况相当。并且,由于舍弃了胶水,使得tpo人造革的手感变好,voc降低,成本降低。
[0044]
其次,根据本发明获得的tpo座椅材料相比于传统pvc座椅,具有以下性能改进:
[0045]-由于tpo产品不含有增塑剂,不会存在增塑剂迁移析出问题;
[0046]-tpo材料的熔点高,使得产品具有良好的高温耐热性能;
[0047]-低温pvc产品容易脆化,产品在低温下容易产生断裂,而tpo产品完美地避免了这一问题;
[0048]-pvc产品具有小分子增塑剂,voc散发性能不好,tpo是根据弹性体调整硬度,其具有良好的气味和散发性能,能够达到国内外在气味散发方面的各种标准。
[0049]
另外,本发明优化的tpo配方使其具有更好的柔韧性、耐揉皱性、耐热性能和柔软性,可以裁切和缝纫,并且在常温下易于手工包覆。根据本发明获得的tpo人造革通过下垂测试具有60-80mm的柔软度;根据bally-flex测试,常温耐揉皱性能够达到10万次,低温(-30℃)耐揉皱性能够达到3万次以上,甚至也能够达到10万次;另外,肉眼几乎看不到折痕。
具体实施方式
[0050]
为使本领域的技术人员更好地理解本发明的技术方案,下面结合实施例和对比例对本发明的技术方案进行清楚、完整的描述,显然,所描述的实施例是本发明的一部分实施例,而不是全部的实施例。基于本发明中的实施例,本领域普通技术人员在没有做出创造性劳动的前提下所获得的所有其他实施例,都属于本发明保护的范围。
[0051]
实施例1:
[0052]
按照下述方法制备tpo人造革:
[0053]
i.根据表1中所示的表皮层配方制备tpo组合物;
[0054]
由获得的tpo组合物通过实验室挤出机(labtech lte20)熔融挤出厚度为0.5mm的薄膜,其中挤出机的温度沿入口到出口方向依次为160℃、180℃、180-190℃,得到tpo表皮层。
[0055]
对薄膜材料表面进行表面电晕处理,以增加表面极性,从而方便下一步的表面处理。
[0056]
ii.涂覆油漆层
[0057]
准备按油漆层重量份数计的如下组分:70份水性聚氨酯分散体,1份聚氨酯增稠剂,0.2份异氰酸酯类固化剂,45份水和1份二氧化硅;
[0058]
将水性聚氨酯分散体、二氧化硅和水混合搅拌均匀,得到混合溶液;
[0059]
加入聚氨酯增稠剂,充分搅拌均匀,得到混合溶液;
[0060]
加入异氰酸酯类固化剂,充分搅拌均匀;
[0061]
在所制备的tpo表皮层表面均匀涂上一层上述获得的水性聚氨酯涂层,然后烘干。
[0062]
iii.制备最终产品
[0063]
将带有油漆的tpo表皮层在复合机器中进行加热,之后与基布进行复合得到最终产品。
[0064]
表1:实施例1的tpo配方
[0065][0066]
[0067]
实施例2:
[0068]
根据表2中所示的表皮层配方,采用与实施例1相同的方法制备tpo人造革。
[0069]
表2:实施例2的tpo配方
[0070]
线性低密度聚乙烯(埃克森美孚)15重量份无规共聚聚丙烯(韩国大林)15重量份poe(邵氏硬度:63a)(美国陶氏)30重量份tpv(邵氏硬度:70a)(埃克森美孚)20重量份增粘树脂eva(va含量35%)(美国杜邦)20重量份添加剂5重量份色母粒4重量份
[0071]
实施例3:
[0072]
根据表3中所示的表皮层配方,采用与实施例1相同的方法制备tpo人造革。
[0073]
表3:实施例3的tpo配方
[0074]
线性低密度聚乙烯(埃克森美孚)15重量份无规共聚聚丙烯(韩国大林)15重量份poe(邵氏硬度:63a)(美国陶氏)30重量份tpv(邵氏硬度:70a)(埃克森美孚)30重量份增粘树脂eaa(aa含量10%)(美国杜邦)10重量份添加剂5重量份色母粒4重量份
[0075]
实施例4:
[0076]
根据表4中所示的表皮层配方,采用与实施例1相同的方法制备tpo人造革。
[0077]
表4:实施例4的tpo配方
[0078][0079][0080]
实施例5:
[0081]
根据表5中所示的表皮层配方,采用与实施例1相同的方法制备tpo人造革。
[0082]
表5:实施例5的tpo配方
[0083]
线性低密度聚乙烯(埃克森美孚)15重量份无规共聚聚丙烯(韩国大林)15重量份
poe(邵氏硬度:50a)(美国陶氏)30重量份tpv(邵氏硬度:50a)(埃克森美孚)20重量份增粘树脂eva(va含量13%)(美国杜邦)20重量份添加剂5重量份色母粒4重量份
[0084]
对比例1:poe硬度过高
[0085]
根据表6中所示的表皮层配方,采用与实施例1相同的方法制备tpo人造革。
[0086]
表6:对比例1的tpo配方
[0087]
线性低密度聚乙烯(埃克森美孚)15重量份无规共聚聚丙烯(韩国大林)15重量份poe(邵氏硬度:80a)(日本三菱)30重量份tpv(邵氏硬度:60a)(埃克森美孚)20重量份增粘树脂eva(va含量35%)(美国杜邦)20重量份添加剂5重量份色母粒4重量份
[0088]
对比例2:tpv硬度过高
[0089]
根据表7中所示的表皮层配方,采用与实施例1相同的方法制备tpo人造革。
[0090]
表7:对比例2的tpo配方
[0091]
线性低密度聚乙烯(埃克森美孚)15重量份无规共聚聚丙烯(韩国大林)15重量份poe(邵氏硬度:60a)(美国陶氏)30重量份tpv(邵氏硬度:80a)(日本三菱)20重量份增粘树脂eva(va含量35%)(美国杜邦)20重量份添加剂5重量份色母粒4重量份
[0092]
对比例3:含胶水
[0093]
根据表8中所示的表皮层配方,采用与实施例1基本相同的方法制备tpo人造革。与实施例1的制备方法不同在于,在对比例3中,在将tpo表皮层和基布复合之前,还在tpo表皮层的背面涂覆溶剂型聚氨酯胶水(溶剂型聚氨酯分散液95重量份,固化剂2重量份)。
[0094]
表8:对比例3的tpo配方
[0095]
线性低密度聚乙烯(埃克森美孚)15重量份无规共聚聚丙烯(韩国大林)15重量份poe(邵氏硬度:60a)(美国陶氏)30重量份tpv(邵氏硬度:70a)(埃克森美孚)20重量份添加剂5重量份色母粒4重量份
[0096]
对比例4:不含增粘树脂
[0097]
根据表9中所示的表皮层配方,采用与实施例1相同的方法制备tpo人造革。
[0098]
表9:对比例4的tpo配方
[0099][0100][0101]
对于由实施例1-5以及对比例1-4获得的tpo人造革进行性能检测。检测结果由表10-11展示出并进行比较。
[0102]
表10:实施例1-5的检测结果
[0103][0104]
表11:对比例1-4的检测结果
[0105][0106][0107]
具体结果描述如下:
[0108]
由实施例1-5获得的tpo人造革的外观均符合美学要求,表面没出现凹坑、亮线、褶皱等不良外观瑕疵。生产过程中均没有出现任何大卷发粘等不良现象。
[0109]
由表10的结果展示可见,不含胶水的、根据本发明的实施例1-5的产品粘结力与含胶水的对比例3的产品粘结力相当,甚至更好。由于不含胶水,使得人造革的voc含量相比于含胶水的对比例3明显降低,对环境影响进一步减小。同时,实施例1-5的邵氏硬度不超过70a,符合座椅面料的硬度要求;柔软下垂度均在60-70mm范围内,具备合适的刚度;常温下能承受达15万次的揉皱,-30℃的低温下能承受达10万次的揉皱。其中,通过实施例1和2说明,随着增粘树脂eva中va含量增大,产品粘结力增高;通过实施例1、4、5说明,随着poe和tpv硬度减小,在产品硬度减小的同时,产品粘结力也增大。
[0110]
与之相对,对比例1和2中使用的poe或tpv的硬度过高。由此导致由对比例1-2获得的tpo人造革具备明显更大的硬度;更大的下垂度说明刚度过小;常温下只能承受5万次的揉皱,不符合汽车座椅对于常温耐揉皱性至少10万次的要求。
[0111]
对比例3中由于在基布层和tpo表皮层之间还有溶剂型胶水,导致刚度相比不含胶水的实施例1-3有所增大,柔软度变差,耐揉皱性也有所降低,同时voc含量明显增大。
[0112]
对比例4由于不含增粘树脂,产品粘结力明显变差。
[0113]
可以理解的是,以上实施方式仅仅是为了说明本发明的原理而采用的示例性实施方式,然而本发明并不局限于此。对于本领域内的普通技术人员而言,在不脱离本发明的精神和实质的情况下,可以做出各种变型和改进,这些变型和改进也视为本发明的保护范围。