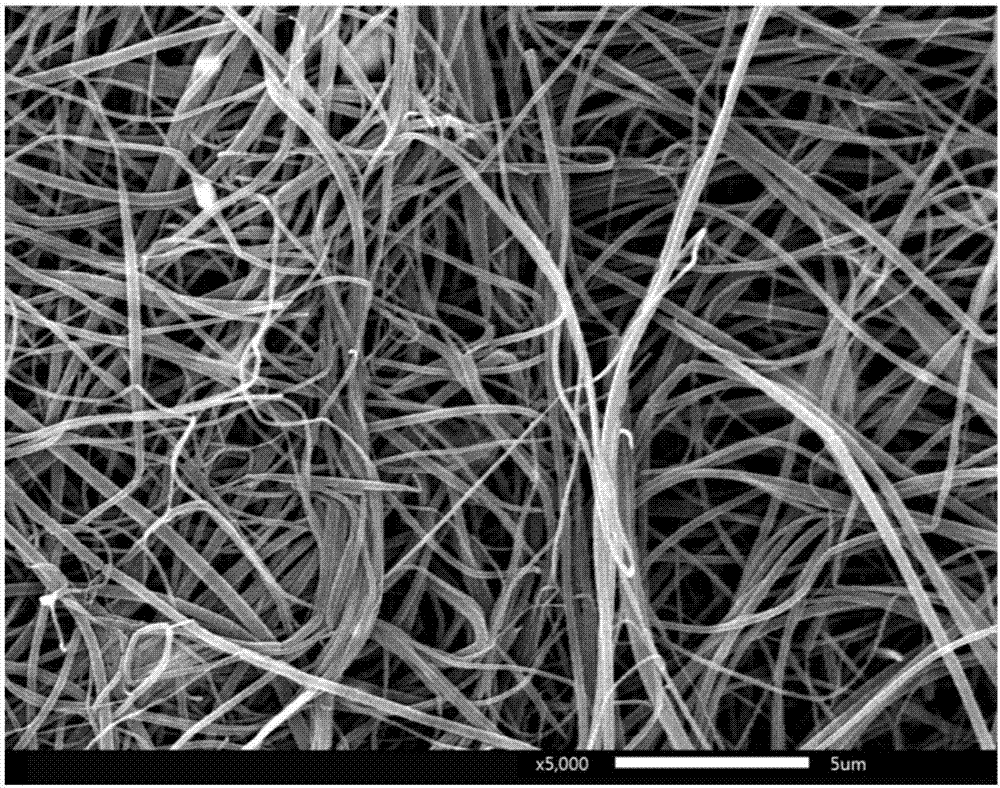
本发明涉及纳米纤维制备
技术领域:
,尤其涉及一种串珠状弹性体/热塑性树脂复合纳米纤维及其制备方法和应用。
背景技术:
:纳米纤维狭义上是指直径为纳米量级的超细纤维,在广义上是指直径为纳米尺度而长度较大的具有一定长径比的线状材料,纳米纤维还包括将纳米颗粒填充到普通纤维中对其进行改性的纤维。纳米纤维因具有高比表面积与高孔隙率等优点在各个领域得到了广泛的应用。目前,纳米纤维的制备方法有很多,包括静电纺丝法、相分离法、模板合成法、自组装法等。近年来,具有串珠状结构的纳米纤维可以制成更加蓬松、孔隙率更大的纳米纤维膜,制备形貌规则、结构可控的高性能珠状纳米纤维成为国内外研究的热点之一。中国发明专利(授权公告号CN103643337B授权公告日2016.04.27)公开了一种串珠状纳米纤维的制备方法,该发明以无机粒子为分散相,高分子聚合物为有机相在有机溶剂中配制了聚合物基质的溶液,采用静电纺丝方法制备了串珠状无机/有机纳米粒子纤维。但是,采用静电纺丝方法制备的珠状纳米纤维具有制备工艺复杂、产率低、无机粒子分散不均匀及无机粒子易脱落的缺点。技术实现要素:为解决以上问题,本发明的目的是提供一种串珠状弹性体/热塑性树脂复合纳米纤维及其制备方法和应用,串珠状弹性体/热塑性树脂复合纳米纤维中珠状物具有分散均匀、结构稳定不易脱落的特点,制备串珠状弹性体/热塑性树脂复合纳米纤维的方法简单、易操作;而且由串珠状弹性体/热塑性树脂复合纳米纤维制成的纳米纤维膜具有空隙率高、孔径小的特点,同时提高了过滤效率和过滤通量。为实现上述目的,本发明所设计的串珠状弹性体/热塑性树脂复合纳米纤维由基体纳米纤维和包埋在基体纳米纤维内的珠状分散相组成,所述基体纳米纤维的原料为热塑性树脂,所述珠状分散相的原料为弹性体;所述基体纳米纤维的平均直径为100~600nm,基体纳米纤维的平均长度为1~1000um,所述珠状分散相的平均直径为850~1250nm。作为优选方案,所述热塑性树脂与弹性体的质量比为19~10:1~10。作为优选方案,所述热塑性树脂为嵌段共聚物、聚酯类高分子树脂、尼龙类高分子树脂、聚烯烃类高分子树脂中的一种。作为优选方案,所述弹性体为聚烯烃类热塑性弹性体、苯乙烯类热塑性弹性体、聚氨酯类热塑性弹性体、聚酰胺类热塑性弹性体中的一种。制备串珠状弹性体/热塑性树脂复合纳米纤维的方法,包括以下步骤:1)复合纳米纤维原丝的制备:采用熔融相分离法将热塑性树脂、弹性体和醋酸丁酸纤维素酯投入双螺杆挤出机中共混挤出,经牵引拉伸制备得到复合纳米纤维原丝;2)串珠状弹性体/热塑性树脂复合纳米纤维的制备:将复合纳米纤维原丝均匀浸泡在丙酮中,利用丙酮萃取复合纳米纤维原丝中的醋酸丁酸纤维素酯后即得串珠状弹性体/热塑性树脂复合纳米纤维。作为优选方案,所述热塑性树脂、弹性体和醋酸丁酸纤维素酯的质量比为19~10:1~10:180。作为优选方案,所述复合纳米纤维原丝的直径为1~2mm。作为优选方案,所述步骤2)中,采用离心技术萃取复合纳米纤维原丝中的醋酸丁酸纤维素酯,具体操作过程为,将浸泡有复合纳米纤维原丝的丙酮投入离心机中,离心转速为1000~6000rpm,每次离心时间为1~5min,共离心3~5次。串珠状弹性体/热塑性树脂复合纳米纤维的应用为,将串珠状弹性体/热塑性树脂复合纳米纤维经流延膜机挤出、单向拉伸和冷却成型工序后得到纳米纤维膜,所述纳米纤维膜用于液体过滤,所述纳米纤维膜的空隙率为0.2~0.4。本发明通过采用熔融相分离法制备串珠状弹性体/热塑性树脂复合纳米纤维的原理为:热塑性树脂、弹性体、CAB不相容三相熔融共混挤出,由于熔融状态的CAB黏度最大,在双螺杆共混挤出的条件下,CAB对热塑性树脂和弹性体发热拉升强度不同,从而形成不同的聚酯形态,然后用丙酮溶剂去除掉CAB,剩下的热塑性树脂形成了基体纳米纤维,弹性体即被包埋在基体纳米纤维内形成珠状结构。本发明的优点在于:1,本发明采用熔融相分离法制备串珠状弹性体/热塑性树脂复合纳米纤维,由于珠状物包埋在基体纳米纤维内,相比于传统珠状物接枝于基体纳米纤维表面的结构,本发明的珠状物更加稳定,不易脱落,而且分散更加均匀。2,本发明串珠状弹性体/热塑性树脂复合纳米纤维与传统采用静电纺丝制备串珠状纳米纤维的方法相比,更加简单,避开复杂的接枝聚合反应,本发明得到的串珠状弹性体/热塑性树脂复合纳米纤维的产率更高。3,由于本发明制得的串珠状弹性体/热塑性树脂复合纳米纤维中的珠状分散相的直径较大,使得由串珠状弹性体/热塑性树脂复合纳米纤维制得的纳米纤维膜具有空隙率高、孔径小的特点,将纳米纤维膜应用于水过滤,解决常规纳米纤维用于水过滤时过滤效率和通量相矛盾的问题。附图说明图1为本发明串珠状弹性体/热塑性树脂复合纳米纤维制备方法的流程示意图;图2为实施例1得到的复合纳米纤维原丝放大5000倍的SEM图;图3为实施例1得到的串珠状弹性体/热塑性树脂复合纳米纤维放大3000倍的SEM图;图中各部件标号如下:双螺杆挤出机1、醋酸丁酸纤维素酯2、热塑性树脂3、弹性体4、复合纤维原丝5、串珠状弹性体/热塑性树脂复合纳米纤维6。具体实施方式为更好地理解本发明,以下将结合附图和具体实例对发明进行详细的说明。为解决现有制备串珠状纳米纤维技术中存在操作复杂,难操作,而且得到的串珠状纳米纤维的珠状物不稳定的问题,本发明提供一种串珠状弹性体/热塑性树脂复合纳米纤维及其制备方法和应用,首先将热塑性树脂、弹性体、CAB不相容的三相熔融共混挤出得到复合纤维原丝,然后用丙酮溶剂去除复合纤维原丝中的CAB得到串珠状弹性体/热塑性树脂复合纳米纤维,串珠状弹性体/热塑性树脂复合纳米纤维由基体纳米纤维和包埋在基体纳米纤维内的珠状分散相组成,基体纳米纤维的原料为热塑性树脂,珠状分散相的原料为弹性体。以下将通过具体的实施例来对本发明的串珠状弹性体/热塑性树脂复合纳米纤维及其制备方法和应用的优选方式进行详细地说明。实施例1制备串珠状弹性体/热塑性树脂复合纳米纤维的方法,包括以下步骤:1)复合纤维原丝的制备:采用熔融相分离法将18gPVA-co-PE(乙烯乙烯醇嵌段共聚物)、2gPU(聚氨酯弹性体)及180gCAB(醋酸纤维素酯)投入双螺杆挤出机中如表1.1的温度共混挤出,经牵引拉伸制备得到复合纤维原丝;复合纤维原丝的直径为1mm。2)串珠状弹性体/热塑性树脂复合纳米纤维的制备:将复合纤维原丝均匀浸泡在丙酮中,采用离心技术萃取复合纤维原丝中的醋酸丁酸纤维素酯,具体操作过程为,将浸泡有复合纤维原丝的丙酮投入离心机中,离心转速为4000rpm,每次离心时间为3min,共离心5次。即得串珠状弹性体/热塑性树脂复合纳米纤维。表1.1双螺杆挤出机各段的温度实施例1得到的复合纤维原丝的SEM图如图1所示,串珠状弹性体/热塑性树脂复合纳米纤维的SEM图如图2所示,根据图1中的尺寸标注功能,对图1片中的复合纤维原丝直径进行直径统计,并且根据图2中的尺寸标注功能,对图2中串珠状弹性体/热塑性树脂复合纳米纤维中基体纳米纤维的平均长度,基体纳米纤维的平均直径以及珠状分散相的平均直径进行统计,实施例1的串珠状弹性体/热塑性树脂复合纳米纤维经流延膜机挤出、单向拉伸和冷却成型工序后得到串珠纳米纤维膜A,采用PMI孔径分析仪对串珠纳米纤维膜A进行孔径分析,其结果见表1.2:表1.2实施例1复合纤维原丝平均直径/mm1基体纳米纤维的平均直径/nm100基体纳米纤维的平均长度/um1珠状分散相的平均直径/nm850串珠纳米纤维膜A的孔隙率分布0.2实施例2制备串珠状弹性体/热塑性树脂复合纳米纤维的方法,包括以下步骤:1)复合纤维原丝的制备:采用熔融相分离法将17g聚对苯二甲酸乙二酯(PET)、3gPU(聚氨酯弹性体)及180gCAB(醋酸纤维素酯)投入双螺杆挤出机中如表2.1的温度共混挤出,经牵引拉伸制备得到复合纤维原丝;复合纤维原丝的直径为2mm。2)串珠状弹性体/热塑性树脂复合纳米纤维的制备:将复合纤维原丝均匀浸泡在丙酮中,采用离心技术萃取复合纤维原丝中的醋酸丁酸纤维素酯,具体操作过程为,将浸泡有复合纤维原丝的丙酮投入离心机中,离心转速为1000rpm,每次离心时间为5min,共离心3次。即得串珠状弹性体/热塑性树脂复合纳米纤维。表2.1双螺杆挤出机各段的温度根据实施例2得到的复合纤维原丝SEM图中的尺寸标注功能,对复合纤维原丝直径进行直径统计,并且计算串珠状弹性体/热塑性树脂复合纳米纤维中基体纳米纤维的平均长度,基体纳米纤维的平均直径以及珠状分散相的平均直径,实施例2的串珠状弹性体/热塑性树脂复合纳米纤维经流延膜机挤出、单向拉伸和冷却成型工序后得到串珠纳米纤维膜B,采用PMI孔径分析仪对串珠纳米纤维膜B进行孔径分析,其结果见表2.2:表2.2实施例2复合纤维原丝平均直径/mm2基体纳米纤维的平均直径/nm600基体纳米纤维的平均长度/um1000珠状分散相的平均直径/nm1250串珠纳米纤维膜B的孔隙率分布0.4实施例3制备串珠状弹性体/热塑性树脂复合纳米纤维的方法,包括以下步骤:1)复合纤维原丝的制备:采用熔融相分离法将15g聚酰胺(PA)、5g聚烯烃弹性体(POE)及180gCAB(醋酸纤维素酯)投入双螺杆挤出机中如表3.1的温度共混挤出,经牵引拉伸制备得到复合纤维原丝;复合纤维原丝的直径为1.5mm。2)串珠状弹性体/热塑性树脂复合纳米纤维的制备:将复合纤维原丝均匀浸泡在丙酮中,采用离心技术萃取复合纤维原丝中的醋酸丁酸纤维素酯,具体操作过程为,将浸泡有复合纤维原丝的丙酮投入离心机中,离心转速为3000rpm,每次离心时间为3min,共离心4次。即得串珠状弹性体/热塑性树脂复合纳米纤维。表3.1双螺杆挤出机各段的温度根据实施例3得到的复合纤维原丝SEM图中的尺寸标注功能,对复合纤维原丝直径进行直径统计,并且计算串珠状弹性体/热塑性树脂复合纳米纤维中基体纳米纤维的平均长度,基体纳米纤维的平均直径以及珠状分散相的平均直径,实施例3的串珠状弹性体/热塑性树脂复合纳米纤维经流延膜机挤出、单向拉伸和冷却成型工序后得到串珠纳米纤维膜C,采用PMI孔径分析仪对串珠纳米纤维膜C进行孔径分析,其结果见表3.2:表3.2实施例3复合纤维原丝平均直径/mm1.5基体纳米纤维的平均直径/nm135基体纳米纤维的平均长度/um542珠状分散相的平均直径/nm867串珠纳米纤维膜C的孔隙率分布0.23实施例4制备串珠状弹性体/热塑性树脂复合纳米纤维的方法,包括以下步骤:1)复合纤维原丝的制备:采用熔融相分离法将10g聚乙烯(PE)、10g苯乙烯热塑性弹性体(TPS)及180gCAB(醋酸纤维素酯)投入双螺杆挤出机中如表4.1的温度共混挤出,经牵引拉伸制备得到复合纤维原丝;复合纤维原丝的直径为1.8mm。2)串珠状弹性体/热塑性树脂复合纳米纤维的制备:将复合纤维原丝均匀浸泡在丙酮中,采用离心技术萃取复合纤维原丝中的醋酸丁酸纤维素酯,具体操作过程为,将浸泡有复合纤维原丝的丙酮投入离心机中,离心转速为5000rpm,每次离心时间为4.5min,共离心3次。即得串珠状弹性体/热塑性树脂复合纳米纤维。表4.1双螺杆挤出机各段的温度根据实施例4得到的复合纤维原丝SEM图中的尺寸标注功能,对复合纤维原丝直径进行直径统计,并且计算串珠状弹性体/热塑性树脂复合纳米纤维中基体纳米纤维的平均长度,基体纳米纤维的平均直径以及珠状分散相的平均直径,实施例4的串珠状弹性体/热塑性树脂复合纳米纤维经流延膜机挤出、单向拉伸和冷却成型工序后得到串珠纳米纤维膜D,采用PMI孔径分析仪对串珠纳米纤维膜D进行孔径分析,其结果见表4.2:表4.2实施例5制备串珠状弹性体/热塑性树脂复合纳米纤维的方法,包括以下步骤:1)复合纤维原丝的制备:采用熔融相分离法将18gPVA-co-PE(乙烯乙烯醇嵌段共聚物)、2g聚酰胺类热塑性弹性体(TPEA)及180gCAB(醋酸纤维素酯)投入双螺杆挤出机中如表5.1的温度共混挤出,经牵引拉伸制备得到复合纤维原丝;复合纤维原丝的直径为1.6mm。2)串珠状弹性体/热塑性树脂复合纳米纤维的制备:将复合纤维原丝均匀浸泡在丙酮中,采用离心技术萃取复合纤维原丝中的醋酸丁酸纤维素酯,具体操作过程为,将浸泡有复合纤维原丝的丙酮投入离心机中,离心转速为3000rpm,每次离心时间为4.5min,共离心4次。即得串珠状弹性体/热塑性树脂复合纳米纤维。表5.1双螺杆挤出机各段的温度根据实施例5得到的复合纤维原丝SEM图中的尺寸标注功能,对复合纤维原丝直径进行直径统计,并且计算串珠状弹性体/热塑性树脂复合纳米纤维中基体纳米纤维的平均长度,基体纳米纤维的平均直径以及珠状分散相的平均直径,实施例5的串珠状弹性体/热塑性树脂复合纳米纤维经流延膜机挤出、单向拉伸和冷却成型工序后得到串珠纳米纤维膜E,采用PMI孔径分析仪对串珠纳米纤维膜E进行孔径分析,其结果见表5.2:表5.2实施例6制备串珠状弹性体/热塑性树脂复合纳米纤维的方法,包括以下步骤:1)复合纤维原丝的制备:采用熔融相分离法将19gPVA-co-PE(乙烯乙烯醇嵌段共聚物)、1gPU(聚氨酯弹性体)及180gCAB(醋酸纤维素酯)投入双螺杆挤出机中如表6.1的温度共混挤出,经牵引拉伸制备得到复合纤维原丝;复合纤维原丝的直径为1.1mm。2)串珠状弹性体/热塑性树脂复合纳米纤维的制备:将复合纤维原丝均匀浸泡在丙酮中,采用离心技术萃取复合纤维原丝中的醋酸丁酸纤维素酯,具体操作过程为,将浸泡有复合纤维原丝的丙酮投入离心机中,离心转速为6000rpm,每次离心时间为5min,共离心2次。即得串珠状弹性体/热塑性树脂复合纳米纤维。表6.1双螺杆挤出机各段的温度根据实施例6得到的复合纤维原丝SEM图中的尺寸标注功能,对复合纤维原丝直径进行直径统计,并且计算串珠状弹性体/热塑性树脂复合纳米纤维中基体纳米纤维的平均长度,基体纳米纤维的平均直径以及珠状分散相的平均直径,实施例6的串珠状弹性体/热塑性树脂复合纳米纤维经流延膜机挤出、单向拉伸和冷却成型工序后得到串珠纳米纤维膜F,采用PMI孔径分析仪对串珠纳米纤维膜F进行孔径分析,其结果见表6.2:表6.2实施例6复合纤维原丝平均直径/mm1.1基体纳米纤维的平均直径/nm215基体纳米纤维的平均长度/um45珠状分散相的平均直径/nm1206串珠纳米纤维膜F的孔隙率分布0.37将实施例1~6制备得到的纳米纤维膜进行了纤维膜的反冲洗测试,与具体的操作如下:称取面积为10cm2的实施例1~6的串珠纳米纤维膜和采用静电纺丝制备得到的对比例纳米纤维膜(制备工艺为参见中国发明专利(授权公告号CN103643337B授权公告日2016.04.27)中的实施例1,然后经流延膜机挤出、单向拉伸和冷却成型工序后得到对比例纳米纤维膜),采用压力为0.2MPa,大小为10cm2的水流持续随机冲击上述的纳米纤维膜的不同位置,冲击时间为120min,最后将水流冲击后的纳米纤维膜进行烘干、称量,并计算出测试前后的质量损失,所得到实验结果如下:测试前质量/g测试后质量/g损失率%对比例纳米纤维膜0.05580.05452.33串珠纳米纤维膜A0.06230.06220.16串珠纳米纤维膜B0.05890.05850.68串珠纳米纤维膜C0.06680.06650.45串珠纳米纤维膜D0.07150.07120.42串珠纳米纤维膜E0.06940.06890.72串珠纳米纤维膜F0.05960.05910.84将对比例纳米纤维膜水洗液中检测到二氧化硅的含量为0.85%,说明在水洗过程中该二氧化硅存在一定的脱落现象,这是由于采用表面接枝聚合的方法存在结合力不够的缺点,无机离子容易脱落。将实施例1得到的串珠纳米纤维膜水洗液中无法检测到聚氨酯弹性体的含量,说明本发明制备得到的串珠状弹性体/热塑性树脂复合纳米纤维的珠状物具有结构稳定,不易脱落的特点。以上所述实施例仅表达了本发明的几种实施方式,其描述较为具体和详细,但并不能因此而理解为对本发明专利范围的限制。应当指出的是,对于本领域的普通技术人员来说,在不脱离本发明构思的前提下,还可以做出若干变形和改进,这些都属于本发明的保护范围。因此,本发明专利的保护范围应以所附权利要求为准。当前第1页1 2 3