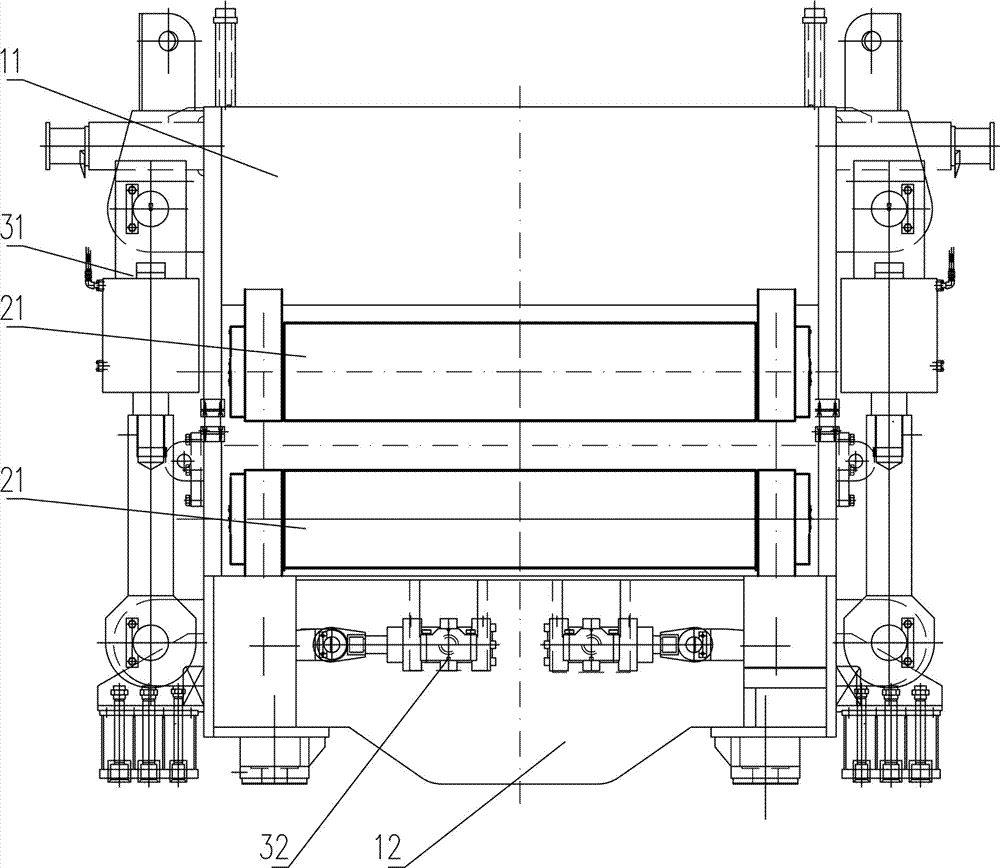
本发明涉及用于金属连续铸造时在现场对铸造坯料进行后处理或后加工的附属设备领域,具体为一种用于改善板坯疏松缩孔缺陷的重压下扇形段及其使用方法。
背景技术:宽厚连铸板坯普遍存在内部中心偏析、中心疏松与缩孔的问题,造成铸坯的质量缺陷,严重影响钢材的机械性能。实践证明动态轻压下技术可以有效地解决铸坯内部中心偏析问题,但对于铸坯内部疏松与缩孔的问题则收效甚微。为了解决铸坯内部疏松与缩孔的问题,目前普遍的做法是加大铸坯轧制过程中的压缩比,但这又限制了厚板轧材的厚度。研究发现,铸坯的内部疏松与缩孔主要形成于铸坯液芯凝固的末端处,因此,在铸坯液芯凝固末端处对铸坯施加10mm以上的厚度缩减的压下量,通过对铸坯此处的挤压,可使中心疏松与缩孔在其形成阶段就被压合,从而消除这一铸坯缺陷。通过这一技术,不仅可以消除铸坯的内部疏松与缩孔,提高铸坯的内部质量,确保钢材的机械性能,还可以有效地降低铸坯轧制过程的压缩比,提高厚钢板的成材厚度。但是,由于受结构型式所限,目前板坯连铸机的各种扇形段都不能够满足单个扇形段对铸坯实施10mm以上的压下量。
技术实现要素:为了克服现有技术的缺陷,提供一种铸坯质量高,疏松和缩孔缺陷少的铸造辅助设备,本发明公开了一种用于改善板坯疏松缩孔缺陷的重压下扇形段及其使用方法。本发明通过如下技术方案达到发明目的:一种用于改善板坯疏松缩孔缺陷的重压下扇形段,包括上框架和下框架,上框架设于下框架的正上方,两对夹紧液压缸通过连接轴和关节轴承分别把上框架和下框架铰接在一起,其特征是:还包括一对大自由辊、一对驱动辊、至少三对小自由辊、大自由辊压下油缸、水平油缸、驱动辊压下油缸和水管,上框架的底部通过轴承可转动地依次设有一根大自由辊、一根驱动辊和至少三根小自由辊,下框架的顶部通过轴承可转动地依次设有一根大自由辊、一根驱动辊和至少三根小自由辊,大自由辊、驱动辊和小自由辊的中心轴线都互相平行,一对大自由辊、一对驱动辊和各对小自由辊的辊面互相正对;大自由辊压下油缸的缸体固定在上框架上,大自由辊压下油缸活塞杆的移动端垂直朝下设置并和设于上框架底部的大自由辊连接,水平油缸的缸体固定在下框架上,水平油缸活塞杆的移动端水平设置并和一对以斜面互相贴合的斜楔滑块中之一连接,另一块斜楔滑块和设于下框架顶部的大自由辊连接;驱动辊压下油缸的缸体固定在上框架上,驱动辊压下油缸活塞杆的移动端垂直朝下设置并和设于上框架底部的驱动辊连接;小自由辊压下油缸的缸体固定在上框架上,小自由辊压下油缸活塞杆的移动端垂直朝下设置并和设于上框架底部的各个小自由辊连接;水管的一端连接水箱,水管的另一端分别贯通连接大自由辊压下油缸、水平油缸、驱动辊压下油缸和小自由辊压下油缸的内腔。所述的用于改善板坯疏松缩孔缺陷的重压下扇形段,其特征是:大自由辊和小自由辊都采用芯轴式三分节辊的结构,驱动辊都采用芯轴式四分节辊的结构,设于大自由辊、小自由辊和驱动辊两端的边部轴承都采用一端为调心辊子轴承、另一端为三圈轴承,设于大自由辊、小自由辊和驱动辊中部的中间轴承都采用两个三圈轴承;大自由辊、小自由辊和驱动辊以及设于大自由辊、小自由辊和驱动辊上轴承的轴承座都采用内部通水冷却,大自由辊、小自由辊和驱动辊的内腔都通过外置式旋转接头连接水管;大自由辊和小自由辊安装好后,冷却水通过水管自动接通注入,减少了扇形段机上配管,扇形段的结构简洁;驱动辊的一端固定法兰,通过法兰可以和扇形段驱动装置的万向联轴器直接相接,两流扇形段可以完全互换,减少了扇形段的备件量。所述的用于改善板坯疏松缩孔缺陷的重压下扇形段,其特征是:大自由辊横截面的直径为R,驱动辊和小自由辊横截面的直径都为r,r≥200mm,R的取值为[2r,2.5r]。所述的用于改善板坯疏松缩孔缺陷的重压下扇形段的使用方法,其特征是:按如下步骤实施:一对大自由辊之间的辊缝作为扇形段的入口侧,最外侧的一对小自由辊作为扇形段的出口侧,铸坯从入口侧进入扇形端;调整连铸机对铸坯的牵引速度,使铸坯的液芯凝固末端处于一对大自由辊之间的辊缝时,启动大自由辊压下油缸,使大自由辊压下油缸的活塞杆向下推动设于上框架底部的大自由辊;同时启动水平油缸,使水平油缸的活塞杆推动水平方向的斜楔滑块,通过斜楔滑块斜面之间的作用力,把水平推动力转化成施加在设于下框架顶部的大自由辊的垂直向上的驱动力,使一对大自由辊共同挤压铸坯,通过一对大自由辊对铸坯的共同挤压,对铸坯施加不小于10mm的压下量;挤压完毕后,铸坯在连铸机的牵引下从扇形段的出口侧输出。本发明提供了一种全新的重压下扇形段,实现了消除铸坯内部的缩孔与疏松,提高连铸坯的内部质量,确保轧制钢板的机械性能,同时降低其轧制压缩比的目的,可用于生产厚度更高的轧制厚钢板。本发明的有益效果是:铸坯质量高,疏松和缩孔缺陷少。附图说明图1是本发明的主视图;图2是图1的K向视图;图3是水平油缸、斜楔滑块和大自由辊的连接示意图。具体实施方式以下通过具体实施例进一步说明本发明。实施例1一种用于改善板坯疏松缩孔缺陷的重压下扇形段,包括上框架11、下框架12、一对大自由辊21、一对驱动辊22、三对小自由辊23、大自由辊压下油缸31、水平油缸32、驱动辊压下油缸33和水管4,如图1和图2所示,具体结构是:上框架11设于下框架12的正上方,两对夹紧液压缸通过连接轴和关节轴承分别把上框架11和下框架12铰接在一起;上框架11和下框架12都采用立板式结构,具有高强度和刚度,满足实施重压下的辊缝控制调节要求,立板式结构通透性好,抗热变形能力强,有利于二冷喷嘴的安装,同时避免下框架氧化铁皮及二冷水的堆积,不会产生辊子堵转的现象;上框架11的底部通过轴承可转动地依次设有一根大自由辊21、一根驱动辊22和至少三根小自由辊23,下框架12的顶部通过轴承可转动地依次设有一根大自由辊21、一根驱动辊22和三根小自由辊23,轴承的轴承座安装面堆焊不锈钢,扇形段上的配管和喷嘴支架均为不锈钢,减少整个扇形段的维护量,大自由辊21、驱动辊22和小自由辊23的中心轴线都互相平行,一对大自由辊21、一对驱动辊22和各对小自由辊23的辊面互相正对;大自由辊压下油缸31的缸体固定在上框架11上,大自由辊压下油缸31活塞杆的移动端垂直朝下设置并和设于上框架11底部的大自由辊21连接,水平油缸32的缸体固定在下框架12上,如图3所示,水平油缸32活塞杆的移动端水平设置并和一对以斜面互相贴合的斜楔滑块321中之一连接,另一块斜楔滑块321和设于下框架12顶部的大自由辊21连接;驱动辊压下油缸33的缸体固定在上框架11上,驱动辊压下油缸33活塞杆的移动端垂直朝下设置并和设于上框架11底部的驱动辊22连接;小自由辊压下油缸34的缸体固定在上框架11上,小自由辊压下油缸34活塞杆的移动端垂直朝下设置并和设于上框架11底部的各个小自由辊23连接;水管4的一端连接水箱,水管4的另一端分别贯通连接大自由辊压下油缸31、水平油缸32、驱动辊压下油缸33和小自由辊压下油缸34的内腔。本实施例中,大自由辊21和小自由辊23都采用芯轴式三分节辊的结构,驱动辊22都采用芯轴式四分节辊的结构,设于大自由辊21、小自由辊23和驱动辊22两端的边部轴承都采用一端为调心辊子轴承、另一端为三圈轴承,设于大自由辊21、小自由辊23和驱动辊22中部的中间轴承都采用两个三圈轴承;大自由辊21、小自由辊23和驱动辊22以及设于大自由辊21、小自由辊23和驱动辊22上轴承的轴承座都采用内部通水冷却,大自由辊21、小自由辊23和驱动辊22的内腔都通过外置式旋转接头连接水管4;大自由辊21和小自由辊23安装好后,冷却水通过水管4自动接通注入,减少了扇形段机上配管,扇形段的结构简洁;驱动辊22的一端固定法兰,通过法兰可以和扇形段驱动装置的万向联轴器直接相接,两流扇形段可以完全互换,减少了扇形段的备件量。设大自由辊21横截面的直径为R,驱动辊22和小自由辊23横截面的直径都为r,则r≥200mm,R的取值为[2r,2.5r],本实施例中,R=500mm,r=230mm。本实施例使用时,按如下步骤实施:一对大自由辊21之间的辊缝作为扇形段的入口侧,最外侧的一对小自由辊23作为扇形段的出口侧,铸坯从入口侧进入扇形端,铸件的输送方向如图1中的空心箭头所示;调整连铸机对铸坯的牵引速度,使铸坯的液芯凝固末端处于一对大自由辊21之间的辊缝时,启动大自由辊压下油缸31,使大自由辊压下油缸31的活塞杆向下推动设于上框架11底部的大自由辊21;同时启动水平油缸32,使水平油缸32的活塞杆推动水平方向的斜楔滑块321,通过斜楔滑块321斜面之间的作用力,把水平推动力转化成施加在设于下框架12顶部的大自由辊21的垂直向上的驱动力,使一对大自由辊21共同挤压铸坯,通过一对大自由辊21对铸坯的共同挤压,对铸坯施加不小于10mm的压下量;重压下扇形段采用远程辊缝调节的控制方式,两对夹紧液压缸布置在扇形段的两个侧边,并带位移传感器,由伺服阀控制,实现重压下工艺操作;在液压阀台上设有压力传感器,进行压力显示;挤压完毕后,铸坯在连铸机的牵引下从扇形段的出口侧输出。