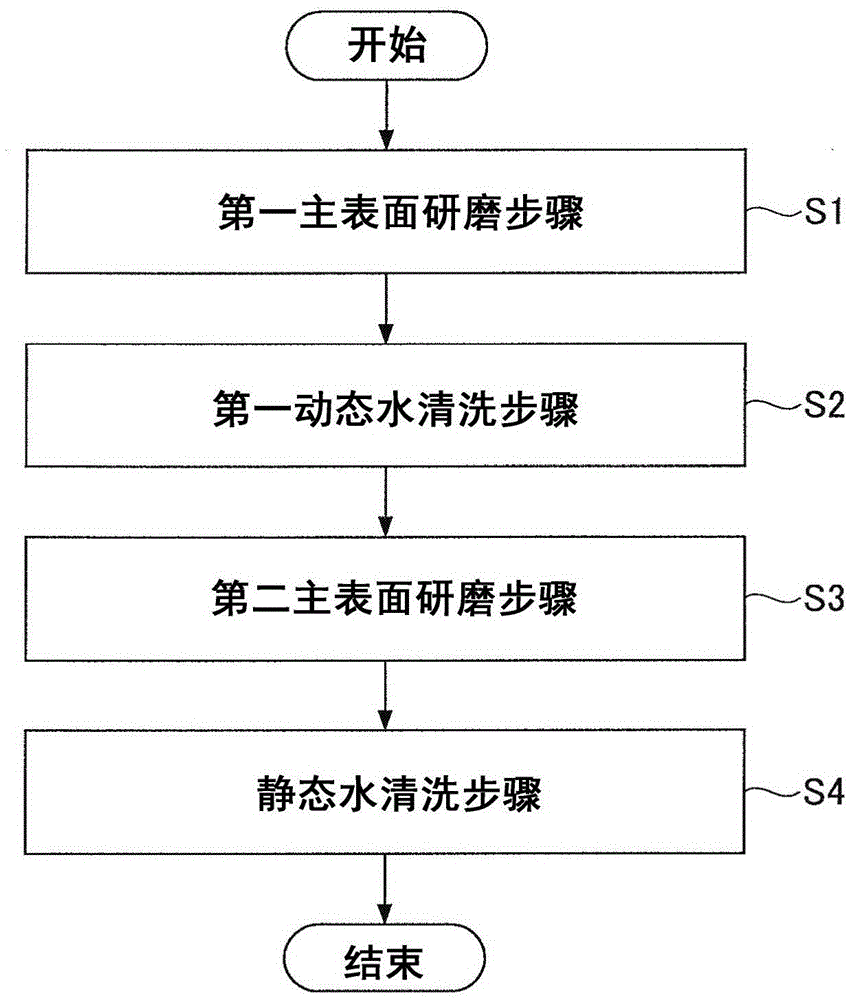
本发明涉及磁记录介质用玻璃基板的制造方法。
背景技术:
:作为在磁盘记录装置等中使用的磁记录介质用基板,目前使用铝合金基板。然而,近年来,伴随着高记录密度化的要求,与铝合金基板相比,较硬、且平坦性、平滑性优异的玻璃基板成为了主流。磁记录介质用玻璃基板呈在中央部具有同心圆状的开口部的圆板形状,其通过进行加工成上述形状的工序、研磨主表面的工序、研磨端面的工序等而制造出。磁记录介质用基板的主表面是记录面,因此,一直以来对研磨主表面的工序进行了各种研究,以能获得期望的特性的主表面。关于研磨磁记录介质用玻璃基板的主表面的方法,在例如专利文献1中公开了一种磁记录介质用基板的制造方法,该制造方法具有一边供给包含磨粒的浆料一边研磨基板的表面的基板研磨工序。具体而言,公开了一种磁记录介质用玻璃基板的制造方法,基板研磨工序包括:在对基板的表面施加了与磨粒的电动电位相同符号的电位的状态下,供给浆料并研磨基板的表面的浆料研磨工序;以及在对基板的表面施加了电位的状态下供给清洗液以代替浆料,以对基板的表面进行清洗研磨的清洗研磨工序。根据专利文献1公开的磁记录介质用玻璃基板的制造方法,能降低研磨后的磨粒残渣。但是,在专利文献1记载的磁记录介质用玻璃基板的制造方法中,作为研磨对象的基板限于至少在表面具有导电性的基板,作为磁记录介质用玻璃基板,无法适用于成为近年主流的磁记录介质用玻璃基板。例如使用双面研磨装置,将研磨片压紧于磁记录介质用玻璃基板的主表 面,一边供给研磨液,一边使磁记录介质用玻璃基板及研磨片旋转,从而能实施研磨磁记录介质用玻璃基板的主表面的工序。通过如上所述对磁记录介质用玻璃基板的主表面进行研磨,能将磁记录介质用玻璃基板的主表面的平坦度、起伏、表面粗糙度设为期望的范围,此外,还能将磁记录介质用玻璃基板设为期望的板厚。现有技术文献专利文献专利文献1:日本专利特开2006-53965号公报然而,在研磨磁记录介质用玻璃基板的主表面的工序中,可能会在主表面产生线状损伤。近年来,要求磁记录介质的高记录密度化,尤其对作为记录面的主表面要求降低损伤。因此,在研磨主表面的工序中,要求抑制磁记录介质用玻璃基板的主表面产生线状损伤。技术实现要素:因此,本发明鉴于上述现有技术所具有的问题而作,其目的在于提供一种能在对主表面进行研磨的工序中抑制在主表面产生线状损伤的磁记录介质用玻璃基板的制造方法。为了解决上述技术问题,本发明的磁记录介质用玻璃基板的制造方法具有对磁记录介质用玻璃基板的主表面进行研磨的主表面研磨工序,所述主表面研磨工序依次包括:第一主表面研磨步骤,在该第一主表面研磨步骤中,将研磨片压紧于磁记录介质用玻璃基板的主表面,一边供给研磨液,一边使所述磁记录介质用玻璃基板及所述研磨片旋转,以对所述主表面进行研磨;第一动态水清洗步骤,在该第一动态水清洗步骤中,供给水以代替研磨液,并使所述磁记录介质用玻璃基板及所述研磨片旋转以进行清洗;以及第二主表面研磨步骤,在该第二主表面研磨步骤中,供给研磨液以代替水,并使所述磁记录介质用玻璃基板及所述研磨片旋转,以对所述主表面进行研磨。根据本发明的磁记录介质用玻璃基板的制造方法,能提供一种在对主表面 进行研磨的工序中能抑制在主表面产生线状损伤的磁记录介质用玻璃基板的制造方法。附图说明图1是双面研磨装置的结构例的说明图。图2是本发明实施方式的主表面研磨工序的流程图。图3是本发明实施方式的主表面研磨工序的研磨压力、定盘的转速的历时变化的示意图。图4是本发明实施方式的主表面研磨工序的流程图。图5是本发明实施方式的主表面研磨工序的研磨压力、定盘的转速的历时变化的示意图。图6是比较例1的主表面研磨工序的研磨压力、定盘的转速的历时变化的示意图。图7是表示实施例、比较例中的具有线状损伤的磁记录介质用玻璃基板的比例的图。(符号说明)16、18研磨片具体实施方式以下,参照附图说明用于实施本发明的方式,但本发明并不限于下述实施方式,只要不脱离本发明的范围,也能在下述实施方式中加入各种变形及置换。对本实施方式的磁记录介质用玻璃基板的制造方法的一结构例进行说明。本实施方式的磁记录介质用玻璃基板的制造方法具有对磁记录介质用玻璃基板的主表面进行研磨的主表面研磨工序。然后,主表面研磨工序能依次具有以下步骤。第一主表面研磨步骤:将研磨片压紧于磁记录介质用玻璃基板的主表面,一边供给研磨液,一边使磁记录介质用玻璃基板及研磨片旋转,以进行主表面的研磨。第一动态水清洗步骤:供给水以替换研磨液,并使磁记录介质用玻璃基板及研磨片旋转以进行清洗。第二主表面研磨步骤:供给研磨液以替换水,并使磁记录介质用玻璃基板及研磨片旋转以进行主表面的研磨。本发明的发明人对在主表面研磨工序中产生线状损伤的原因进行了深刻研究。其结果是,发现因在开始主表面研磨工序之前混入双面研磨装置内的异物、在研磨主表面的过程中产生的研磨残渣、研磨液的浆料的凝聚体、研磨中保持磁记录介质用玻璃基板(以下也记载为“玻璃基板”)的支座产生的扬尘等异物,产生了上述损伤。因此,本实施方式的磁记录介质用玻璃基板的制造方法能在主表面研磨工序中设置动态水清洗步骤,该动态水清洗步骤在利用研磨液研磨主表面的两个步骤之间供给水以替换研磨液,并使研磨片及玻璃基板旋转。根据上述主表面研磨工序,在使用研磨液研磨主表面的第一主表面研磨步骤之后,能通过第一动态水清洗步骤降低、去除双面研磨装置内含有的异物等。然后,通过在降低、去除了双面研磨装置内的异物的环境下,实施第二主表面研磨步骤,能防止产生新的损伤,且即便在第一主表面研磨工序中产生了线状损伤,也能降低、去除上述损伤。因此,在主表面研磨工序中,能抑制在主表面产生线状损伤。以下,对各步骤进行说明。(第一主表面研磨步骤)在第一主表面研磨步骤中,将进行主表面研磨的磁记录介质用玻璃基板固定于双面研磨装置,一边供给研磨液,一边使玻璃基板及研磨片旋转,以研磨磁记录介质用玻璃基板的主表面。此处,使用图1对双面研磨装置的结构例进行说明。图1(A)示出了在进行主表面研磨步骤时使用的支座的结构例,图1(B)示出了双面研磨装置的示意图。当研磨玻璃基板的主表面时,在图1(A)所示的具有能保持玻璃基板的玻璃基板保持孔11的支座(主表面研磨用夹具)10上设置多个玻璃基板。另 外,在图中,例示出了设有圆形的玻璃基板保持孔11的支座10,但并不限定于上述实施方式,还能形成与研磨的玻璃基板的形状相配合的玻璃基板保持孔11。例如,在对形状成形前的玻璃基板进行研磨的情况下,能使用具有四边形的玻璃基板保持孔11的支座10。将设置有玻璃基板的支座10固定于图1(B)所示的双面研磨装置12,并驱动太阳齿轮13、小齿轮14以规定的旋转比率旋转。藉此,使支座10自转,并使支座10以绕着太阳齿轮13公转的方式移动。另外,能使上定盘15及下定盘17旋转,藉此,固定于上定盘15、下定盘17的研磨片16、18也旋转。此时,保持于支座10的玻璃基板的两主表面夹持、按压于在与玻璃基板相对的面分别安装有研磨片16、18的上定盘15与下定盘17之间,因此,玻璃基板的两主表面被同时研磨。另外,当进行研磨时,能朝研磨面与玻璃基板之间供给研磨液。本实施方式的磁记录介质用玻璃基板的制造方法中使用的玻璃基板只要是磁记录介质用的玻璃基板即可,并未被特别限定。例如,玻璃的种类也可以是非晶玻璃、结晶化玻璃,还可以是在玻璃基板的表层具有强化层的强化玻璃。另外,用于主表面研磨工序的玻璃基板也可以是在中央具有圆形的开口部的圆板形状的玻璃基板,还可以是加工成该圆板形状之前的、即进行形状成形工序之前的四边形的玻璃基板。玻璃基板例如能使用通过浮法、熔融法、下拉法、或者冲压成形法等成形的玻璃基板。第一主表面研磨步骤中的具体的研磨条件并未被特别限定,能根据研磨的玻璃基板所要求的研磨量等任意地选择研磨时间、双面研磨装置的上定盘及下定盘的转速等。根据定盘的大小等不同研磨条件也是不同的,但例如能将研磨时间设为10分钟以上60分钟以下,另外,还能将上定盘及下定盘的转速设为0.1rpm以上100rpm以下。也能任意地选择研磨压力,但为了生产率较高地实施主表面的研磨,因此,研磨压力处于80g/cm2以上是较为理想的。但是,当研磨压力过高时,玻璃基板可能会破损等,因此,研磨压力处于140g/cm2以下是较为理想的。另外,研磨压力是指在图1(B)所示的双面研磨装置中利用上定盘15和下定盘17按压 玻璃基板的压力,其是换算为工件上的单位面积的压力后的值。以下说明也相同。另外,在第一主表面研磨步骤中使用的研磨液也未被特别限定,能根据研磨的玻璃基板所要求的研磨量等进行选择。例如,能使用作为研磨液含有氧化铈磨粒的研磨液、胶体二氧化硅等。但是,根据本文说明的主表面研磨工序,其能抑制线状损伤的产生,因此,在具有多个研磨主表面的工序的情况下,较为理想的是,主表面研磨工序是研磨主表面的工序中的最后的工序。因此,作为研磨液,特别优选使用胶体二氧化硅。(第一动态水清洗步骤)在第一动态水清洗步骤中,供给水以替换研磨液,并使玻璃基板及研磨片旋转以进行清洗。如上所述,通过实施第一动态水清洗步骤,能降低、去除双面研磨装置内的在第一主表面研磨步骤中产生的异物、在第一主表面研磨步骤之前混入的异物等。然后,通过在异物被降低、去除了的环境下实施后述的第二主表面研磨步骤,即便通过第一主表面研磨步骤在玻璃基板的主表面上产生了线状损伤,也能降低、去除上述损伤。作为第一动态水清洗步骤中使用的水并未被特别限定,但如上所述,是为了去除双面研磨装置内的异物而供给的水,所以,使用含有异物较少的水是较为理想的,这样不会混入新的异物。能优选使用例如经由逆渗透膜过滤后的初级纯净水,尤其更优选使用经由过滤器降低、去除了异物后的初级纯净水。在第一动态水清洗步骤中,水的流量(供给速度)并未被特别限定,但第一动态水清洗步骤是使水流遍双面研磨装置内来降低、去除双面研磨装置内的异物的步骤,因此,以足够的流量供给水,这是较为理想的。因此,关于水的流量,工件单位面积的流量例如为1.5ml/cm2·min以上是较为理想的,为2.0ml/cm2·min以上是更为理想的。但是,即便过度增大水的流量,也几乎无法看到去除异物的效果提高,因此,工件单位面积的流量为5.0ml/cm2·min以下是较为理想的,为4.0ml/cm2·min以下是更为理想的。第一动态水清洗步骤中的研磨压力并未被特别限定,但通过导入水能使摩 擦力提高得比研磨时高,因此,当研磨压力过高时,双面研磨装置的负荷可能会升高。但是,当研磨压力过低时,双面研磨装置的定盘的旋转可能会不稳定。因此,研磨压力例如为20g/cm2以上80g/cm2以下是较为理想的,为30g/cm2以上50g/cm2以下是更为理想的。另外,尽管在第一动态水清洗步骤中并不进行研磨,但由于一般将利用上定盘和下定盘按压玻璃基板的压力称为研磨压力,因此,作为研磨压力进行了说明。另外,第一动态水清洗步骤中的定盘的转速并未被特别限定,但由于通过导入水会使摩擦力提高得比研磨时高,因此,最好使转速比第一主表面研磨步骤时的转速小。但是,由于第一动态水清洗步骤是使水流遍双面研磨装置内来降低、去除双面研磨装置内的异物的步骤,因此,当转速过小时,为了使水流遍双面研磨装置内而需要时间,这不是理想的。因此,第一动态水清洗步骤中的定盘的转速为第一主表面研磨步骤时的定盘的转速的20%以上60%以下是较为理想的,为30%以上50%以下是更为理想的。另外,在第一主表面研磨步骤中,在上定盘的转速与下定盘的转速不同的情况下,对应的各定盘的转速在上述范围内是较为理想的。实施第一动态水清洗步骤的时间未被特别限定,选择实施第一动态水清洗步骤的时间,以能使水流遍双面研磨装置内来去除异物,是较为理想的。例如选择实施第一动态水清洗步骤的时间,以在第一动态水清洗步骤期间至少使上定盘旋转0.5周以上,是较为理想的。特别地,选择实施第一动态水清洗步骤的时间,以在第一动态水清洗步骤期间至少使上定盘旋转一周以上,是更为理想的。另外,此处,对以上定盘的转速为基准实施第一动态水清洗步骤的时间进行了说明,但其原因是:通常从设于上定盘的供给口朝双面研磨装置内供给水。(第二主表面研磨步骤)在第二主表面研磨步骤中,能供给研磨液以替换水,并使玻璃基板及研磨片旋转以对玻璃基板的主表面进行研磨。第二主表面研磨步骤中的具体的研磨条件并未被特别限定,能根据研磨的 玻璃基板所要求的研磨量等任意地选择研磨时间、双面研磨装置的转速等。但是,第二主表面研磨步骤在通过第一动态水清洗步骤降低、去除了双面研磨装置内的异物的环境下进行主表面的研磨,即便在通过第一主表面研磨步骤在玻璃基板的主表面产生了线状损伤的情况下,也能降低、去除上述损伤。因此,将研磨时间确保为能降低、去除第一主表面研磨步骤中产生的线状损伤的程度是较为理想的,例如第二主表面研磨步骤的时间、即研磨时间为30秒以上是较为理想的,为60秒以上是更为理想的。另一方面,当第二主表面研磨步骤的时间(研磨时间)过长时,可能会重新产生异物,重新产生线状损伤。因此,研磨时间为八分钟以下是较为理想的,为五分钟以下是更为理想的,为三分钟以下是进一步理想的。也能任意地选择研磨压力,但为了生产率较高地实施主表面的研磨,因此,研磨压力处于80g/cm2以上是较为理想的。但是,当研磨压力过高时,玻璃基板可能会破损等,因此,研磨压力处于140g/cm2以上是较为理想的。另外,在第二主表面研磨步骤中使用的研磨液也未被特别限定,能根据研磨的玻璃基板所要求的研磨量等进行选择。例如,能使用作为研磨液含有氧化铈磨粒的研磨液、胶体二氧化硅等。但是,根据本文说明的主表面研磨工序,能抑制线状损伤的产生,因此,在具有多个研磨主表面的工序的情况下,较为理想的是,主表面研磨工序是研磨主表面的工序中的最后的工序。因此,作为研磨液,特别优选使用胶体二氧化硅。以上说明的主表面研磨工序如图2的流程图所示的那样,能依次实施上述第一主表面研磨步骤S1、第一动态水清洗步骤S2、第二主表面研磨步骤S3。另外,较为理想的是,为了防止步骤间的异物混入,连续地、即以不打开双面研磨装置的方式实施上述三个步骤。此外,在第二主表面研磨步骤结束之后,进行在使玻璃基板及研磨片的旋转停止的状态下朝双面研磨装置内供给水的静态水清洗步骤S4,以降低、去除双面研磨装置内的研磨液。在静态水清洗步骤S4之后,能从双面研磨装置中取出研磨后的玻璃基板。能在静态水清洗步骤中优选使用的水、其流量的优选范围与第一动态水清 洗步骤的情况相同,因此,此处省略说明。实施静态水清洗步骤的时间未被特别限定,但例如为10秒以上120秒以下是较为理想的。在图3中示意地示出了至此说明的主表面研磨工序中的研磨压力、定盘的转速及研磨液、水的供给的变化。在图3中,直线表示研磨压力,虚线表示定盘的转速。另外,图表中下部所示的带斜线的块箭头是指供给研磨液的期间,空心的块箭头是指供给水的期间。如图3所示,在主表面研磨工序刚开始之后,供给研磨液,并提高研磨压力、定盘的转速,从而能实施第一主表面研磨步骤(S1)。然后,在第一主表面研磨步骤(S1)结束之后,供给水以替代研磨液,或者降低研磨压力及定盘的转速,从而能实施第一动态水清洗步骤(S2)。接着,供给研磨液以代替水,并提高研磨压力、定盘的转速,从而能实施第二主表面研磨步骤(S3)。在第二主表面研磨步骤结束之后,供给水以代替研磨液,并停止定盘的旋转,从而能实施静态水清洗步骤(S4)。另外,还可以与第一动态水清洗步骤相同地,供给水并使玻璃基板及研磨片旋转而进行清洗,以替换在停止玻璃基板及研磨片的旋转的状态下朝双面研磨装置内供给水的静态水清洗步骤S4。即,主表面研磨工序还可以具有第二动态水清洗步骤,以代替静态水清洗步骤S4,该第二动态水清洗步骤在第二主表面研磨步骤结束之后,供给水以代替研磨液,并使磁记录介质用玻璃基板及研磨片旋转以进行清洗。在该情况下,如图4所示,在第二主表面研磨步骤S3之后,能实施第二动态水清洗步骤S5。这样,通过供给水,并使玻璃基板及研磨片旋转,能将冲洗水流遍双面研磨装置内。因此,尤其能降低、去除附着于双面研磨装置内的研磨液的磨粒等,另外,尤其能抑制接着利用相同的装置研磨玻璃基板的主表面时在主表面产生的损伤。能在第二动态水清洗步骤中优选使用的水、其流量、研磨压力、转速的优选范围与第一动态水清洗步骤的情况相同,因此,此处省略说明。实施第二动态水清洗步骤的时间未被特别限定,选择实施第二动态水清洗 步骤的时间,以能使水流遍双面研磨装置内来去除异物,是较为理想的。例如选择实施第二动态水清洗步骤的时间,以在第二动态水清洗步骤期间至少使上定盘旋转0.2周以上,是较为理想的。特别更为理想的是,选择实施第二动态水清洗步骤的时间,以在第二动态水清洗步骤期间至少使上定盘旋转0.5周以上。实施第二动态水清洗步骤的时间的上限并未被特别限定,但从不重新产生异物的观点出发,选择实施第二动态水清洗步骤的时间,以使第二动态水清洗步骤期间的上定盘的转速为三周以下,是较为理想的。也可在第二动态水清洗步骤结束之后,打开双面研磨装置以取出玻璃基板,但还能如图4所示进一步实施上述静态水清洗步骤S4,在该静态水清洗步骤S4中,在停止玻璃基板及研磨片的旋转的状态下继续供给水。在第二动态水清洗步骤结束之后,还实施静态水清洗步骤,从而能进一步降低残留于双面研磨装置内的磨粒,因此,是较为理想的。如上所述,通过实施第二动态水清洗步骤,能降低、去除双面研磨装置内的研磨磨粒,但仅通过第二动态水清洗步骤可能无法充分地进行去除。另外,若长时间地进行第二动态水清洗步骤,还存在产生新的异物的危险性,因此,实施在停止玻璃基板及研磨片的旋转的状态下继续供给水的静态水清洗步骤是较为理想的。对于能在静态水清洗步骤中优选使用的水、其供给量等已经进行了说明,因此,此处省略说明。图5中示意地示出了在第二主表面研磨步骤之后实施第二动态水清洗步骤及静态水清洗步骤的情况下的、主表面研磨工序中的研磨压力、定盘的转速及研磨液、水的供给变化。与图3相同,直线表示研磨压力,虚线表示定盘的转速。另外,图表中下部所示的带斜线的块箭头是指供给研磨液的期间,空心的块箭头是指供给水的期间。直至第二主表面研磨步骤(S3)为止,与图3的情况相同。然后,在第二主表面研磨步骤结束之后,供给水以替代研磨液,降低研磨压力及定盘的转速,从而能实施第二动态水清洗步骤(S5)。接着,停止定盘的旋转,以实施静态 水清洗步骤(S4)。至此,对主表面研磨工序进行了说明,但实施上述主表面研磨工序的时间点并未被特别限定,能在任意的时间点进行实施。在磁记录介质用玻璃基板的制造方法中,能具有多个对磁记录介质用玻璃基板的主表面进行研磨的工序。在具有多个对磁记录介质用玻璃基板的主表面进行研磨的工序的情况下,在研磨磁记录介质用玻璃基板的主表面的工序中的最后的工序中,实施至此为止说明了的主表面研磨工序是较为理想的。在具有多个研磨玻璃基板的主表面的工序的情况下,通常为了在初始的工序中确保足够的研磨量,利用含有较大粒径的研磨磨粒的研磨液进行研磨。然后,在后期的工序中,进行精密研磨,以使玻璃基板的主表面变为期望的形状。因此,在后期的工序中,特别要求从玻璃基板的主表面去除损伤。此外,根据至此为止说明了的主表面研磨工序,能降低、去除因异物等而产生的线状损伤,因此,优选适用于特别要求去除损伤的后期的工序,尤其适用于最终的工序。特别地,近年来,伴随着提高磁记录介质的记录密度的要求,对于作为记录面的主表面,即使是深度1nm左右较浅的损伤,也要求降低、去除该损伤。此外,在至此为止说明了的主表面研磨工序中,能降低、去除上述较浅的损伤,因此,优选适用于研磨玻璃基板的主表面的多个工序中的最后的工序,对于上述细微的损伤,也能去除。至此,对本实施方式的磁记录介质用玻璃基板所具有的主表面研磨工序进行了说明,但本实施方式的磁记录介质用玻璃基板除了主表面研磨工序之外还能具有各种工序。本实施方式的磁记录介质用玻璃基板的制造方法例如能包括以下的工序1~5。(工序1)从玻璃类基板加工成在中央部具有圆孔的圆板形状的玻璃基板的形状成形工序。(工序2)对玻璃基板的内周和外周的端面部分进行倒角的倒角工序。(工序3)对玻璃基板的端面(内周端面及外周端面)进行研磨的端面研 磨工序。(工序4)对玻璃基板的主表面进行研磨的工序。(工序5)将玻璃基板清洗并加以干燥的清洗、干燥工序。上述工序无需按上述记载的顺序进行,例如,也可在形状成形工序之前进行研磨主表面的工序。另外,各工序未被限定为一次,能根据所要求的玻璃基板的规格等实施任意次数。例如,能在形状成形工序之后进行研磨主表面的工序,然后,还能在进行完倒角工序和端面研磨工序之后,再次实施研磨主表面的工序。此处,(工序1)的形状成形工序将通过浮法、熔融法、冲压成形法、下拉法或者再曳引法成形的玻璃类基板加工成在中央部具有圆孔的圆板形状的玻璃基板。另外,所使用的玻璃类基板也可以是非晶玻璃、结晶化玻璃,还可以是在玻璃基板的表层具有强化层的强化玻璃。在(工序2)的倒角工序中,能对玻璃基板的内周、外周的端面部分进行倒角。(工序3)的端面研磨工序能对玻璃基板的端面(侧面部和倒角部)进行研磨。在(工序4)的研磨主表面的工序中,能使用例如图1(B)所示的双面研磨装置对玻璃基板的主表面进行研磨。另外,当研磨玻璃基板的主表面时,并不限定于如至此说明的那样使用研磨液等的游离磨粒进行研磨的方法,也能使用固定磨粒进行研磨。在使用固定磨粒进行研磨的情况下,在图1(B)所示的双面研磨装置12中,能将研磨片16、18替换成固定磨粒工序进行实施。在实施多次研磨主表面的工序的情况下,实施至少一次已述的主表面研磨工序是较为理想的,在最后的研磨主表面的工序中,实施已述的主表面研磨工序是更为理想的。(工序5)的清洗、干燥工序是对研磨后的玻璃基板进行清洗并进行干燥的工序。具体的清洗方法并未被特别限定。例如,能通过使用清洗剂的擦洗清洗、浸渍在清洗剂溶液中的状态下的超声波清洗、浸渍在纯净水中的状态下的 超声波清洗等进行清洗。另外,干燥方法也未被特别限定,例如能利用异丙醇蒸气进行干燥。此外,也可在上述各工序间进行玻璃基板的清洗(工序间清洗)、玻璃基板表面的蚀刻(工序间蚀刻)。另外,在对玻璃基板要求较高的机械强度的情况下,也可在工序3、4中例举出的研磨工序前、或研磨工序后、或研磨工序间,实施在玻璃基板的表层形成强化层的强化工序(例如化学强化工序)。此外,对通过包括上述各工序的制造方法获得的玻璃基板还进行在主表面上形成磁性层等的薄膜的工序,从而成为磁记录介质。以上说明的本实施方式的磁记录介质用玻璃基板的制造方法在主表面研磨工序中,较为理想的是在最后的主表面研磨工序中,在第一主表面研磨步骤与第二主表面研磨步骤之间具有第一动态水清洗步骤。此外,能通过第一动态水清洗步骤降低、去除在第一主表面研磨步骤中在双面研磨装置内产生的异物等,并能通过第二主表面研磨步骤在降低、去除了异物的环境下实施主表面的研磨。因此,在主表面研磨工序中,能抑制在磁记录介质用玻璃基板的主表面产生线状损伤。[实施例]以下举例说明具体的实施例,但本发明并不限定于上述实施例。(实施例1)通过以下步骤制造出磁记录介质用玻璃基板。首先,由通过浮法成形的以SiO2为主要成分的铝硅酸盐玻璃基板,加工成圆板形状玻璃基板,以获得呈同心圆状地具有直径为20mm的圆孔的、直径65mm的磁记录介质用玻璃基板(形状成形工序)。然后,对玻璃基板的内周、外周的端面部分进行倒角(倒角工序)。接着,使用氧化铝磨粒,对玻璃基板的上下的主表面进行磨削(一次磨削工序)。在一次磨削工序中,作为研磨工具使用铸铁定盘和含有氧化铝磨粒的磨削液,利用双面研磨装置(创技电子机械(公司名:speedfam)制、产品名:DSM-16B-5PV-4MH)对玻璃基板的上下的主表面进行磨削(一次切削)。一次 磨削工序结束后,清洗玻璃基板,以去除研磨液及其它污垢。接着,使用研磨刷和氧化铈磨粒对外周侧面和外周倒角部进行研磨,去除外周侧面及外周倒角部的伤痕,以形成镜面的方式对外周端面进行研磨加工。然后,对外周端面研磨后的玻璃基板的磨粒进行清洗去除(外周端面研磨工序)。接着,使用研磨刷和氧化铈磨粒对玻璃基板的内周侧面和内周倒角部进行研磨,去除内周侧面及内周倒角部的伤痕,以形成镜面的方式对内周端面进行研磨加工,清洗去除磨粒(内周端面研磨工序)。接着,作为研磨工具使用含有平均粒径为4μm的金刚石粒子的固定磨粒工具和含有表面活性剂的磨削液,利用双面研磨装置(创技电子机械(公司名:speedfam)制、产品名:DSM-16B-5PV-4MH)对上下的主表面进行了磨削(二次切削)(二次磨削工序)。在二次磨削工序结束后,清洗玻璃基板,以去除研磨液及其它污垢。然后,通过研磨该玻璃基板的主表面,制作出外径为65m、内径为20mm、板厚为0.8mm的磁盘用玻璃基板。在主表面研磨工序中,最初进行了一次研磨。具体而言,作为研磨工具使用软质聚氨酯制的研磨片(皮革类研磨片)和含有氧化铈磨粒的磨削液,利用16B型的双面研磨装置(创技电子机械(公司名:speedfam)制、产品名:DSM-16B-5PV-4MH)对玻璃基板的上下的主表面进行一次研磨。另外,作为含有氧化铝磨粒的研磨液,使用了以平均粒子直径(以下简称为平均粒径)为约1.0μm的氧化铝为主成分的研磨液组成物。另外,一次研磨的主要的研磨加工压力为120g/cm2,下定盘转速为30rpm,上定盘转速为与下定盘相反方向的10rpm,研磨支座公转速为10rpm,自转速为3rpm,在板厚方向上对上下两主平面研磨了合计30μm。在一次研磨结束后,清洗玻璃基板以去除氧化铈。(一次研磨工序)接着,通过以下步骤对玻璃基板的上下的主表面进行二次研磨(二次研磨工序)。根据图2所示的流程图实施二次研磨工序。另外,使双面研磨装置的研磨 压力、定盘的转速及研磨液、水的供给如图3所示地变化来进行实施。利用图1所示的16B型的双面研磨装置12(创技电子机械(公司名:speedfam)制、产品名:DSM-16B-5PV-4MH)进行了主表面的二次研磨。双面研磨装置12包括:在与玻璃基板相对的面上安装有研磨片16、18的上定盘15;以及下定盘17。接着,将结束了一次研磨工序后的圆板形状玻璃基板固定于支座10,并按每批100块的量将玻璃基板固定于双面研磨装置以进行研磨。在主表面的二次研磨工序中,首先,实施第一主表面研磨步骤S1。在第一主表面研磨步骤中,利用上定盘15和下定盘17以研磨压力达到100g/cm2的方式按压玻璃基板,并以上定盘15的转速为7rpm、下定盘的转速为21rpm的方式进行驱动,研磨了三十分钟。另外,此时,驱动太阳齿轮13、小齿轮14旋转,使支座10一边自转一边以绕着太阳齿轮13公转的方式移动,从而也使玻璃基板旋转。另外,在研磨的期间,朝研磨片的研磨面和玻璃基板的主表面之间供给平均粒径为大约20nm的胶体二氧化硅研磨液以作为研磨液。在第一主表面研磨步骤结束之后,实施第一动态水清洗步骤S2。第一动态水清洗步骤在第一主表面研磨步骤结束后,在不打开双面研磨装置的情况下连续地实施了30秒钟。在第一动态水清洗步骤中,将研磨机的研磨压力改变为40g/cm2,将上定盘的转速改变为3rpm,将下定盘的转速改变为9rpm。另外,供给经由过滤器过滤后的初级纯净水,以代替研磨液。以单位工件面积的流量为2.4ml/cm2·min的方式供给上述初级纯净水。在第一动态水清洗步骤结束之后,实施第二主表面研磨步骤S3。第二主表面研磨步骤在第一动态水清洗步骤结束后,在不打开双面研磨装置的情况下连续地实施了5分钟。除了研磨时间之外,与第一主表面研磨步骤相同地实施了第二主表面研磨步骤。在第二主表面研磨步骤结束之后,停止玻璃基板及定盘的旋转,也停止研 磨液的供给。接着,朝双面研磨装置内供给经由过滤器过滤之后的初级纯净水,在不打开双面研磨装置的情况下连续地实施了40秒钟静态水清洗步骤S4。在静态水清洗步骤中,以单位工件面积的流量为2.4ml/cm2·min的方式供给上述初级纯净水。在静态水清洗步骤之后,打开双面研磨装置,并取出磁记录介质用玻璃基板。以上说明的二次研磨工序之后,进行擦洗清洗、浸渍在纯净水中的状态下的超声波清洗的清洗,并利用异丙醇蒸气干燥(清洗、干燥工序)之后,用于评价。下面说明评价方法及评价结果。使用光散射方式表面观察机(公司名:KLATencor公司制,OSACandela7100)对在磁记录介质用玻璃基板的表面是否形成有线状损伤进行评价。此外,算出具有线状损伤的磁记录介质用玻璃基板的比例,结果确认为2.1%。另外,使用光散射方式表面观察机对附着于所获得的磁记录介质用玻璃基板的表面的颗粒的数量进行了评价,结果确认OSA计数的中位数为19。另外,OSA计数的数值越小,则意味着附着的颗粒的数量越少。(实施例2)在实施例2中,根据图4所示的流程图实施主表面的二次研磨工序。另外,使双面研磨装置的研磨压力、定盘的转速及研磨液、水的供给如图5所示地变化来进行实施。即,在第二主表面研磨步骤S3结束后、静态水清洗步骤S4之前,除了实施第二动态水清洗步骤S5这点以及将静态水清洗步骤的时间设为30秒钟这点之外,均与实施例1相同地制造出磁记录介质用玻璃基板。第二动态水清洗步骤S5在第二主表面研磨步骤结束后,在不打开双面研磨装置的情况下,连续地实施了10秒钟。在第二动态水清洗步骤中,在第二主表面研磨步骤结束后,将研磨机的压力改变为40g/cm2,另外,还将上定盘的转速改变为3rpm,将下定盘的转速改 变为9rpm。另外,供给经由过滤器过滤后的初级纯净水,以代替研磨液。在第二动态水清洗步骤S5中,以工件单位面积的流量为2.4ml/cm2·min的方式供给上述初级纯净水。静态水清洗步骤S4在第二动态水清洗步骤结束后,在不打开双面研磨装置的情况下,连续地实施了30秒钟。在静态水清洗步骤中,停止玻璃基板及定盘的旋转。然后,朝双面研磨装置内供给经由过滤器过滤后的初级纯净水。在静态水清洗步骤中,以工件单位面积的流量为2.4ml/cm2·min的方式供给上述初级纯净水。在静态水清洗步骤结束之后,打开双面研磨装置,取出磁记录介质用玻璃基板,与实施例1同样地,在进行完清洗、干燥之后,用于评价。与实施例1相同地,算出具有线状损伤的磁记录介质用玻璃基板的比例,结果确认为0.9%。另外,与实施例1同样地,对附着于获得的磁记录介质用玻璃基板的表面的颗粒的数量进行了评价,结果确认OSA计数的中位数为14。(比较例1)除了不实施第一动态水清洗步骤,将第一主表面研磨步骤的研磨时间设为35分钟,不实施第二主表面研磨步骤这些点之外,与实施例1相同地制造出磁记录介质用玻璃基板。即,将第一主表面研磨步骤和第二主表面研磨步骤作为一个研磨步骤连续地进行实施。此处,在图6中示意地示出了比较例1中的主表面研磨工序中的研磨压力、定盘的转速及研磨液、水的供给的变化。与图3相同,直线表示研磨压力,虚线表示定盘的转速。另外,图表中下部所示的带斜线的块箭头是指供给研磨液的期间,空心的块箭头是指供给水的期间。在主表面的二次研磨工序刚开始之后,一边供给研磨液,一边提高研磨压力、定盘的转速,从而实施第一主表面研磨步骤(S1')。此外,在第一主表面研磨步骤(S1’)结束之后,供给水以代替研磨液,并停止定盘的旋转,从而实施静态水清洗步骤(S4)。在静态水清洗步骤结束之后,打开双面研磨装置,取出磁记录介质用玻璃 基板,与实施例1同样地,在进行完清洗、干燥之后,用于评价。与实施例1相同地,算出具有线状损伤的磁记录介质用玻璃基板的比例,结果确认为7.3%。另外,与实施例1相同地,对附着于获得的磁记录介质用玻璃基板的表面的颗粒的数量进行了评价,结果确认OSA计数的中位数为20。图7中示出了将具有线状损伤的磁记录介质用玻璃基板的比例的评价结果图表化后的图。此外,在表1中总结示出了对附着于上述实施例、比较例所获得的磁记录介质用玻璃基板的表面的颗粒的数量进行评价后的OSA计数的中位数的值。(表1)实施例1实施例2比较例1OSA计数的中位数191420根据图7所示的具有线状损伤的磁记录介质用玻璃基板的比例,能确认出实施了第一动态水清洗步骤之后的实施例1、2与比较例1相比较,具有线状损伤的磁记录介质用玻璃基板的比例大幅降低。这可以认为是以下原因:在实施例1、2中,与比较例1不同,能通过第一动态水清洗步骤降低、去除双面研磨装置内的异物,并能在降低、去除了异物的环境下实施第二主表面研磨步骤。另外,关于表1所示的附着于磁记录介质用玻璃基板的表面的颗粒的数量,能确认出实施例2与实施例1、比较例1相比大幅降低了。在实施例1、比较例1中,重复相同条件制造出磁记录介质用玻璃基板,因此,可能在双面研磨装置内残留有研磨磨粒等。但是,在实施例2中,考虑由于实施了第二动态水清洗步骤,因此,尤其能降低残留于双面研磨装置内的研磨磨粒,并能降低附着于磁记录介质用玻璃基板的颗粒。当前第1页1 2 3