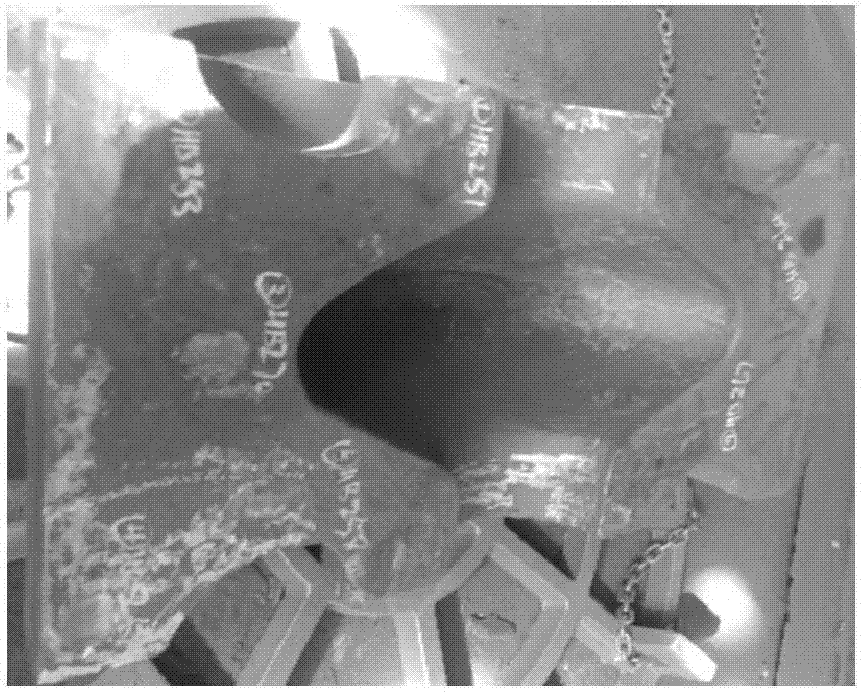
本发明涉及球墨铸铁领域,具体地说是一种合金球墨铸铁轧辊及其制备工艺。
背景技术:
:球墨铸铁轧辊可以用在各种型钢和板钢的开坯轧机、粗轧机和精轧前的轧机上。其服役特点是轧制温度高、钢锭变形量大,与板坯分离后,轧辊随又要在连续喷水下急速冷却,从而使轧辊表面承受交变的热应力的作用,容易造成辊身表面产生大量的热裂纹。因此,轧辊需要兼有高的强度与韧性,良好的耐磨性以提高其轧制量,较好的抗热疲劳性能以提高其耐热性。现有技术中,当球墨铸铁厚度较小时,其硬度可以超过300HBW,但是当球墨铸铁的厚度大于200mm,特别是壁厚达到500mm时,硬度就很难超过300HBW,并且硬度不均很难达到使用要求。技术实现要素:本发明的目的在于提供一种合金球墨铸铁轧辊及其制备工艺,该合金球墨铸铁轧辊硬度HBW300以上,轧辊表面硬度任意点间的硬度值相差不大于20HBW。本发明的具体的技术方案为:一种合金球墨铸铁轧辊,由以下组分组成:C:3.50~3.60wt%;Si:2.1~2.3wt%;Mn:0.5~0.8wt%;Cr:0.2~0.3wt%;Mo:0.4~0.6wt%;Cu:0.7~0.8wt%;Sb:0.006~0.009wt%;P:≤0.030wt%;S:≤0.010wt%;Re:≤0.010wt%;Mg:0.035~0.045wt%,余量铁以及不可除杂质。在上述的合金球墨铸铁轧辊中,由以下组分组成:C:3.55%;Si:2.23wt%;Mn:0.74wt%;Cr:0.20wt%;Mo:0.44wt%;Cu:0.78wt%;Sb:0.0075wt%;P:0.021wt%;S:0.008wt%;Re:0.0057wt%;Mg:0.045wt%,余量铁以及不可除杂质。在上述的合金球墨铸铁轧辊中,所述的合金球墨铸铁轧辊的直径厚度为205-500mm,合金球墨铸铁轧辊硬度HBW300以上,表面硬度任意点间的硬度值相差不得大于20HBW。同时,本发明还公开了上述的合金球墨铸铁轧辊的制备工艺,包括以下步骤:步骤1:熔炼,将原料在电炉中熔炼;步骤2:球化,将熔炼后的金属液温度达到1440~1450℃时出炉进行球化处理;步骤3:浇注,将球化处理后的金属液温度达到1350℃~1360℃时浇注得到轧辊;步骤4:热处理,将轧辊装炉在升温阶段控制升温速率60℃/h,在650℃时保温2.5h,最后升温880℃~920℃,保温4小时,然后喷雾冷却20分钟,吹风冷却2~4小时,580℃~600℃回火,保温5小时,炉冷即得合金球墨铸铁轧辊。在上述的合金球墨铸铁轧辊的制备工艺中,步骤1中,熔炼时控制原料中Ti≤0.020wt%。在上述的合金球墨铸铁轧辊的制备工艺中,步骤1中,熔炼温度小于1540℃~1550℃,原料融化完成后,在1500℃时静置一段时间后除去上浮的杂质。在上述的合金球墨铸铁轧辊的制备工艺中,所述的球化处理步骤中的球化剂为重稀球化剂土和轻稀土球化剂,重稀球化剂土和轻稀土球化剂的重量比为7~6:3~4,球化剂的用量为步骤1中的原料总量的1.2wt%。优选地,重稀球化剂土的组份为Mg:5.67wt%;Si:46.67wt%;Ca:1.08wt%;Y:1.02wt%;Al:0.35wt%;轻稀土球化剂的组份为Mg:5.88wt%;Si:45.43wt%;Ca:1.02wt%;Ce:0.42wt%;Al:0.42wt%。在上述的合金球墨铸铁轧辊的制备工艺中,所述的球化处理的工艺为堤坝式球化包冲入法球化工艺。在上述的合金球墨铸铁轧辊的制备工艺中,在浇注时,加入0.12%粒度为0.2~0.7mm的硫氧孕育剂进行随流孕育处理。优选地,硫氧孕育剂组分为Si:74.2wt%;Ca:0.77wt%;Ce:1.71wt%;Al:0.93wt%;S,O适量。与现有技术相比,本发明的有益效果在于:本合金球墨铸铁轧辊断面厚度大,表面硬度高,硬度均匀。对于合金球墨铸铁轧辊来说,由于化学成分的不同,铸造工艺的不同,其铸态组织是完全不同的,可以呈现出不同的性能指标。C和Si两元素直接影响铸铁轧辊的综合性能。C和Si应统一考虑,碳当量上限以不发生石墨漂浮为原则,下限应满足轧辊性能要求,保证有合适含量的碳化物。所以碳当量取4.2%~4.40%为宜。结合实际,C取3.50%~3.60%,Si取2.1%~2.30%。Mn元素降低共析转变温度,起稳定并细化珠光体的作用。可提高轧辊的强度、硬度,但含量过高时偏析严重,沿晶界析出网状碳化物,使白口化倾向加大,降低其韧性,综合考虑应控制在0.5%~0.8为宜。P在大直径轧辊的生产中,是要严格控制的元素。过高的磷含量会生成二元磷共晶或三元磷共晶。磷共晶分布在共晶团晶界上,呈多角形,质硬而脆,容易造成应力集中,降低球铁的强度、塑性和韧性。所以对于直径较大的轧辊来说,P含量应控制在0.030%以下。S含量应尽可能地低,应控制在0.010%以下。Cr元素它能显著抵消硅的不利影响,有利于硬度和耐磨性的提高。对大直径的轧辊生产中,Cr含量超过0.3%,稍有控制不当很容易出现游离碳化物,降低强度和韧性。所以Cr含量控制在0.2%~0.3%为宜。Mo作为稳定珠光体元素,可促进珠光体组织的形成,细化晶粒增加珠光体的弥散度。钼抑制奥氏体分解,有利于贝氏体组织的形成。但钼易于偏析,故其含量不宜过高,控制在0.4%~0.6%为宜。Cu可提高淬透性,改善铸件断面组织与性能的均匀,对基体有固溶强化和沉淀硬化作用,控制在0.7%~0.8%为宜。Sb含量选择在0.006%~0.009%,不仅会使轧辊的石墨圆整度提高,使石墨球数增加,而且增加基体组织中的珠光体数量。通过合理选取化学成分,严格控制熔炼球化处理工艺,结合一些大断面球铁件的生产经验,合适的球化和孕育处理以及适当添加一些合金元素,在铸态硬度达不到技术要求时,通过部分奥氏体化正火+回火工艺热处理等工艺措施,轧辊的硬度HBW300以上,轧辊表面硬度任意点间的硬度值相差不大于20HBW。附图说明图1是本发明实施例1的浇注后的铸试块的金相组织图;图2是本发明实施例1的浇注后的轧辊的表面硬度取样点示意图;图3是本发明实施例1的热处理后的轧辊的取样示意图;图4是本发明实施例1的热处理后的轧辊的取样示意图;图5是本发明实施例1的热处理后的轧辊的取样点从外圆到内圆硬度变化情况示意图;图6是本发明实施例1的热处理后的轧辊金相组织图。具体实施方式下面结合具体实施方式,对本发明的技术方案作进一步的详细说明,但不构成对本发明的任何限制。实施例1合金球墨铸铁轧辊的制备工艺如下:1、原材料中生铁选用优质的Q10生铁;废钢选用五金冲压后的边角料,在微量元素中,应特别注意控制Ti≤0.020%;合金为锰铁、铬铁、钼铁、电解铜、锑锭等。2、熔炼设备为5T中频感应电炉,熔炼时要控制温度不超过1550℃,熔化完后铁液不要急于除渣,应在1500℃左右静止片刻,让铁液中未及时上浮的杂质有时间上浮到铁液表面,随表面浮渣一起扒除,从而得到纯净的铁液。3、球化孕育处理当铁液温度到达1440~1450℃时出炉进行球化处理。球化剂选用60%重稀球化剂土+40%轻稀土球化剂,孕育剂用高钡钙孕育剂。采用堤坝式球化包冲入法球化,球化剂加入量1.20%。为加强孕育效果,在铁液浇注时用0.12%粒度为0.2~0.7mm的硫氧孕育剂进行随流孕育处理。浇注前控制好铁液温度在1350℃时才进行浇注。浇注后取样,化学成分见表1,力学性能见表2。表1化学成分表2附铸试块力学性能抗拉强度Rm/MPa屈服强度Rp0.2/MPa伸长率A/MPa布氏硬度HBW7294292.4268浇注后的铸试块的金相组织图见图1;金相评定见表3。表3试块金相评定球化级别(级)石墨大小(级)珠光体(%)碳化物(%)2695<0.5浇注后的铸试块的表面硬度如表4,各取样点见图2(图2上看不到有16个点,要不你通过文字大体描述一下各个点的位置。)。表4铸态本体表面硬度1#2#3#4#5#6#7#8#2512532702552582772272579#10#11#12#13#14#15#16#267264289256268277259266从表1化学成分检验结果可知,试制件的化学成分基本控制在设计的范围内。表2的力学性能显示,抗拉强度、伸长率均达到了QT700-2技术要求。表3的金相组织对照球铁金相评定图谱,球化级别、石墨大小达到了较高水平。95%的珠光体保证了足够的力学性能。表4的铸态本体的硬度显示,铸态下未能达到交货条件要求。需要通过热处理提高硬度才能满足要求。4、热处理热处理的目的,就是在于根据轧辊的技术要求和使用条件及原始铸态组织情况,用合适的热处理方法来调整基体组织和内应力状态,以使轧辊达到最佳的技术性能指标和使用效果。根据轧辊的技术要求,结合铸态下检查的本体硬度综合考虑,采用部分奥氏体化正火+回火工艺热处理。参考《热处理手册》的热处理工艺,通过机理分析和球墨铸铁的热处理工艺证实,880℃以上奥氏体加热,铁素体已全部溶解,920℃或大于920℃加热,奥氏体晶粒粗大,稳定性增加,导致冷却后残余奥氏体增多,轧辊硬度下降。为此,把奥氏体化温度确定为880~900℃是比较合适的。回火温度,580℃回火贝氏体量减少,600℃回火硬度下降。考虑到轧辊在实际加热炉中回火时间较长和温度控制精度的实际情况,将轧辊的回火温度确定为580℃~600℃。确定的热处理工艺如下:从轧辊装炉在升温阶段升温速率60℃/h,在650℃时保温2.5h,最后升温880℃~920℃,保温4小时,然后喷雾冷却20分钟,吹风冷却2~4小时,580℃~600℃回火,保温5小时,炉冷。热处理后的轧辊从正中间取样,如图3中以斜线标示的位置,图3中的轧辊的厚度为500mm。对取得的样品分为A、B、C样品进行检测,A、C样品做力学性能检验,B号样从外圆到内圆硬度变化情况进行检验,如图4。图5示出了取样点从外圆到内圆硬度变化情况示意图。力学强度如表5。表5本体力学性能编号抗拉强度Rm/MPa屈服强度Rp0.2/MPa伸长率A/%布氏硬度HBA6634111.4329C6714101.4311平均值6674111.4320各取样点的硬度如表6。表6从外圆到内圆硬度变化情况表图6示出了热处理后的轧辊金相组织图。表7为热处理后的轧辊金相组织评定数据表7金相组织评定球化级别(级)石墨大小(级)珠光体(%)碳化物(%)2698<0.5从表6的热处理后试制件本体表面硬度可知,最高值337,最低值317的硬度基本达到了硬度均匀性的要求。表5的本体力学性能抗拉强度667MPa,伸长率1.4%达到了技术要求。表6的从外圆到内圆硬度变化情况,反映该试制件的内外硬度基本一致。表7的金相组织的球化级别,石墨大小达到了良好水平,无明显碳化物。从以上检验结果看出,选取的化学成分,熔炼球化处理工艺及拟定的热处理工艺,基本可满足轧辊的技术要求。实施例2合金球墨铸铁轧辊的制备工艺如下:1、原材料中生铁选用优质的Q10生铁;废钢选用五金冲压后的边角料,在微量元素中,应特别注意控制Ti≤0.020%;合金为锰铁、铬铁、钼铁、电解铜、锑锭等。2、熔炼设备为5T中频感应电炉,熔炼时要控制温度不超过1540℃,熔化完后铁液不要急于除渣,应在1500℃左右静止片刻,让铁液中未及时上浮的杂质有时间上浮到铁液表面,随表面浮渣一起扒除,从而得到纯净的铁液。3、球化孕育处理当铁液温度到达1440~1450℃时出炉进行球化处理。球化剂选用70%重稀球化剂土+30%轻稀土球化剂,孕育剂用高钡钙孕育剂。采用堤坝式球化包冲入法球化,球化剂加入量1.20%。为加强孕育效果,在铁液浇注时用0.12%粒度为0.2~0.7mm的硫氧孕育剂进行随流孕育处理。浇注前控制好铁液温度在1355℃时才进行浇注。浇注后的化学成分取样测试结果如表8。表8化学成分元素CSiMnPSCrMoCuSbREMg含量3.52.30.50.0220.0090.250.40.80.0060.0100.0354、热处理确定的热处理工艺如下:从轧辊装炉在升温阶段升温速率60℃/h,在650℃时保温2.5h,最后升温880℃~920℃,保温4小时,然后喷雾冷却20分钟,吹风冷却2~4小时,580℃~600℃回火,保温5小时,炉冷。实施例3合金球墨铸铁轧辊的制备工艺如下:1、原材料中生铁选用优质的Q10生铁;废钢选用五金冲压后的边角料,在微量元素中,应特别注意控制Ti≤0.020%;合金为锰铁、铬铁、钼铁、电解铜、锑锭等。2、熔炼设备为5T中频感应电炉,熔炼时要控制温度不超过1545℃,熔化完后铁液不要急于除渣,应在1500℃左右静止片刻,让铁液中未及时上浮的杂质有时间上浮到铁液表面,随表面浮渣一起扒除,从而得到纯净的铁液。3、球化孕育处理当铁液温度到达1440~1450℃时出炉进行球化处理。球化剂选用65%重稀球化剂土+35%轻稀土球化剂,孕育剂用高钡钙孕育剂。采用堤坝式球化包冲入法球化,球化剂加入量1.20%。为加强孕育效果,在铁液浇注时用0.12%粒度为0.2~0.7mm的硫氧孕育剂进行随流孕育处理。浇注前控制好铁液温度在1360℃时才进行浇注。浇注后的化学成分取样测试结果如表9。表9化学成分4、热处理确定的热处理工艺如下:从轧辊装炉在升温阶段升温速率60℃/h,在650℃时保温2.5h,最后升温880℃~920℃,保温4小时,然后喷雾冷却20分钟,吹风冷却2~4小时,580℃~600℃回火,保温5小时,炉冷。以上所述的仅为本发明的较佳实施例,凡在本发明的精神和原则范围内所作的任何修改、等同替换和改进等,均应包含在本发明的保护范围之内。当前第1页1 2 3