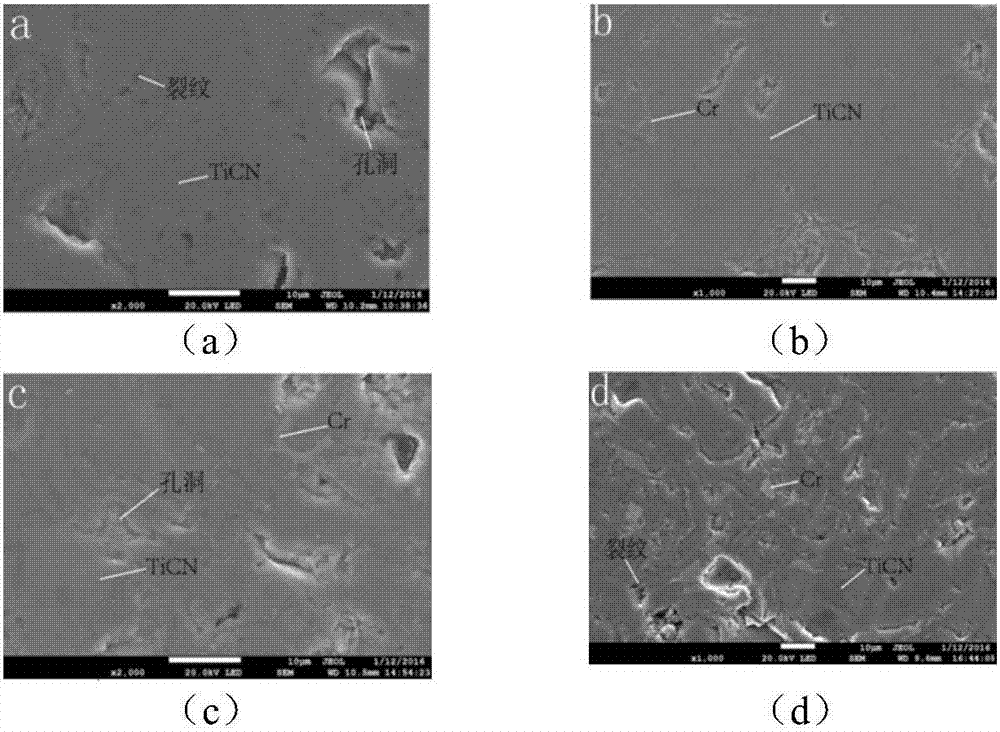
本发明属于油田采油领域,涉及抽油机光杆防腐涂层,特别涉及一种防腐耐磨ticn复合涂层及其喷涂方法及防腐耐磨抽油机光杆。
背景技术:
:随着油田二次采油开采的不断深入,大多油井进入高含水期,抽油机井普遍出现了光杆的腐蚀磨损问题,造成光杆偏磨、盘根密封不严、井口盘根渗漏及胶皮盘根磨损等一系列问题,影响了油井正常的清洁生产。为了确保油区生产不污染周边环境以及不增加工人的工作量,因此急需解决抽油机光杆的腐蚀磨损问题,提出并采取相应有效的防治和减缓腐蚀磨损速度的措施。当前,抽油机光杆表面普遍采用电镀铬技术来处理,电镀铬是一种传统的表面电镀技术,已经应用近百年。然而,抽油机光杆长期在腐蚀、磨损的工况下工作,由于采油工艺和油质的变化,与光杆接触的油液、水液中含有h2s、o2等强腐蚀性介质,传统镀铬层无法满足光杆表面的防腐要求,同时由于光杆长期与密封井口的盘根接触摩擦,腐蚀产生的麻点和油液和水液中的沙粒将会加速盘根和光杆的磨损,最终光杆因腐蚀和磨损而失效。电镀硬铬过程中产生的cr6+会导致严重的环境污染问题。镀铬使用铬酸溶液,在镀铬过程中会产生大量的氢气,氢气泡破裂产生的酸雾中含有致癌的cr6+;另外镀铬会产生大量的有毒废物和含有cr6+的废水。因此,各国对镀铬工艺的管制越来越严格。为了避免cr6+对环境的污染,人们一直努力寻找能替代电镀硬铬的涂层工艺。已开发出多种涂层技术,包括物理气相沉积、化学气相沉积、激光涂层技术、热喷涂技术等。然而,由于pvd、cvd等膜技术在真空中实现,部分形状复杂和较大的零件,加上成本高,限制了这些技术的应用。而热喷涂技术灵活、方便、零件无需重新设计,是替代镀铬层最有竞争力的技术。但目前开发的替代涂层多以超音速火焰喷涂wc-co或wc-co-cr为主,在国内推广应用遇到了较大的阻碍,其主要原因仍是成本问题。因此,亟需一种环保、成本低、喷涂技术便捷且具有强韧性及强度的喷涂涂层及其喷涂方法,延长抽油机光杆和盘根的整体寿命,降低抽油机的能耗,替代传统的代镀铬层来防止抽油机光杆表面的腐蚀及磨损问题。技术实现要素:本发明的目的在于克服现有技术的不足,提供一种不仅能够延长抽油机光杆使用寿命,且能够降低抽油机能耗,有效解决抽油机光杆表面的腐蚀及磨损问题的抽油机光杆防腐耐磨ticn复合涂层。本发明的目的还在于提供一种喷涂过程中工艺参数可控、有效防止氧化物的干扰,确保喷涂效果的抽油机光杆防腐耐磨ticn复合涂层喷涂方法。本发明的目的还在于提供一种耐磨性能、耐腐蚀性能高,能够延长抽油机光杆使用寿命的防腐耐磨抽油机光杆。本发明解决其技术问题是通过以下技术方案实现的:一种抽油机光杆防腐耐磨ticn复合涂层,其特征在于:所述ticn复合涂层由crmo基层、nial粘结层及ticn涂覆层组成,所述crmo基层的组成及其重量百分比为:cr40~45%mo55~60%所述nial粘结层的组成及其重量百分比为:ni粉90-95wt%al粉5-10wt%所述ticn涂覆层的组成及其重量百分比为:c粉20-25wt%ti粉75-80wt%。而且,所述ni粉及al粉的粒度为-140~+325目。而且,所述ti粉为timp-1钛粉,粒度为-300目。而且,所述nial粘结层的喷涂厚度为30~50μm。而且,所述ticn涂覆层的喷涂厚度为20~30μm。抽油机光杆防腐耐磨ticn复合涂层的喷涂方法,其特征在于:所述喷涂方法的步骤为:(1)抽油机光杆表层处理:将抽油机光杆表层用喷砂或砂纸打磨,除去铁锈、油污,获得洁净、高粗糙度的抽油机光杆表层;(2)crmo基层喷涂:在预处理后的抽油机光杆表层喷涂cr、mo粉末,并加热固化制备crmo基层;(3)nial粘结层喷涂:在crmo基层上采用反应等离子喷枪喷涂al/ni粉末,制备nial粘结层,所述nial粘结层的制备参数为:ar离子气体流量70~90l/min,n2离子气体流量20~60l/min,送粉气体流量0.5m3/h,电弧功率25~30kw,电流350~500a,喷涂距离100~150mm;(4)制备ticn涂覆层复合粉:将ti粉与c粉按所述重量百分比混合后经过300~350℃加热后得到ticn涂覆层复合粉;(5)ticn涂覆层喷涂:采用反应等离子喷枪喷涂ticn涂覆层复合粉制备ticn涂覆层,所述ticn涂覆层的制备参数为:ar离子气体流量50~70l/h,n2离子气体流量50~70l/h,送粉气体流量3~5m3/h,电弧功率25~30kw,电流350~500a,喷涂距离80~120mm。而且,所述步骤(3)(5)中的送粉气体均为n2。一种防腐耐磨抽油机光杆,其特征在于:包括杆体及依次喷涂于杆体表面的crmo基层、nial粘结层及ticn涂覆层。而且,所述nial粘结层的喷涂厚度为30~50μm。而且,所述ticn涂覆层的喷涂厚度为20~30μm。本发明的优点和有益效果为:1、本发明的抽油机光杆防腐耐磨ticn复合涂层,crmo基层、nial粘结层及ticn涂覆层,crmo基层能够保证ticn复合涂层主相单一,无氧化物的干扰,nial粘结层能够有效加强ticn涂覆层与抽油机光杆的结合强度,保证ticn复合涂层的强度,且相比现有的tic或者tin复合涂层,ticn中c原子取代n原子,一方面形成高键能的ti-c键,另一方面造成了ticn的晶格畸变,这两者共同作用使得ticn复合涂层的硬度提高,且具有较高的耐磨、耐腐蚀性能,能够有效解决抽油机光杆的腐蚀及磨损问题,增强抽油机光杆的使用寿命。2、本发明的抽油机光杆防腐耐磨ticn复合涂层的喷涂方法,采用反应等离子喷枪进行喷涂,等离子喷枪内为n2,同时作为反应气体及送粉气体,且喷涂过程中各工艺参数可控,能够调整获得主相单一的ticn复合涂层,防止氧化物的干扰而影响ticn复合涂层的纯度,确保喷涂效果。3、本发明的防腐耐磨抽油机光杆,nial粘结层能够有效加强ticn涂覆层与抽油机光杆杆体的结合强度,提高抽油机光杆的硬度,且具有较高的耐磨、耐腐蚀性能,能够有效解决抽油机光杆的腐蚀及磨损问题,增强抽油机光杆的使用寿命。4、本发明的ticn复合涂层致密均匀,具有较高的硬度及强度,且耐磨性能、耐腐蚀性能高,不仅能够延长抽油机光杆使用寿命,且能够降低抽油机能耗,有效解决抽油机光杆表面的腐蚀及磨损问题;本ticn复合涂层采用反应等离子喷枪进行喷涂,喷涂过程中的工艺参数可控,能够得到主相单一的ticn复合涂层,有效防止氧化物的干扰,确保喷涂效果,具有很好的工业应用前景。附图说明图1a为反应等离子喷涂的ticn复合涂层表面sem图,图1b为机械振动喷涂的ticn复合涂层表面sem图;图2a中cr含量为0的ticn复合涂层表面sem图,图2b中cr含量为10%的ticn复合涂层表面sem图,图2c中cr含量为20%的ticn复合涂层表面sem图,图2d中cr含量为30%的ticn复合涂层表面sem图;图3a中mo含量为10%的ticn复合涂层表面sem图,图3b中mo含量为20%的ticn复合涂层表面sem图,图3c中mo含量为30%的ticn复合涂层表面sem图;图4a为ticn复合涂层截面形貌图,图4b为图4a的放大图,图4c为ticn复合涂层的截面能谱分析图;图5为ticn复合涂层的xrd衍射分析;图6a、图6c为ticn复合涂层背面的腐蚀形貌图,图6b、图6d为ticn复合涂层正面的腐蚀形貌图;图7为ticn复合涂层的xps谱图;图8为ticn复合涂层ti2p的xps谱图;图9a为ticn复合涂层c1s的能谱图,图9b为ticn复合涂层n1s的能谱图;图10a为ticn复合涂层的tem相图,图10b为图10a的局部放大图;图11为ticn复合涂层的显微硬度-载荷关系曲线图;图12a中载荷为100g的ticn复合涂层截面显微压痕形貌图,图12b中载荷为200g的ticn复合涂层截面显微压痕形貌图,图12c中载荷为300g的ticn复合涂层截面显微压痕形貌图,图12d中载荷为500g的ticn复合涂层截面显微压痕形貌图;图13为ticn复合涂层断裂截面图;图14为不同载荷下tin及ticn复合涂层的摩擦系数曲线图;图15为不同载荷下tin及ticn复合涂层摩擦磨损失重曲线图;图16为防腐耐磨抽油机光杆的结构示意图。1-抽油机光杆、2-ticn涂覆层、3-nial粘结层、4-crmo基层、5-杆体。具体实施方式下面通过具体实施例对本发明作进一步详述,以下实施例只是描述性的,不是限定性的,不能以此限定本发明的保护范围。实施例一一种抽油机光杆防腐耐磨ticn复合涂层,其创新之处在于:ticn复合涂层由crmo基层、nial粘结层及ticn涂覆层组成,crmo基层的组成及其重量百分比为:cr40gmo60gnial粘结层的组成及其重量百分比为:ni粉90gal粉10gticn涂覆层的组成及其重量百分比为:c粉20gti粉80g。ni粉及al粉的粒度为-140目。ti粉为timp-1钛粉,粒度为-300目。nial粘结层的喷涂厚度为30μm。ticn涂覆层的喷涂厚度为20μm。抽油机光杆防腐耐磨ticn复合涂层的喷涂方法,其创新之处在于:喷涂方法的步骤为:(1)抽油机光杆表层处理:将抽油机光杆用喷砂或砂纸打磨,除去铁锈、油污,获得洁净、高粗糙度的抽油机光杆表层;(2)crmo基层喷涂:在预处理后的抽油机光杆表层喷涂cr、mo粉末,并加热固化制备crmo基层;(3)nial粘结层喷涂:在crmo基层上采用反应等离子喷枪喷涂al/ni粉末,制备nial粘结层,所述nial粘结层的制备参数为:ar离子气体流量70l/min,n2离子气体流量20l/min,送粉气体为n2,其流量为0.5m3/h,电弧功率25kw,电流350a,喷涂距离100mm;(4)制备ticn涂覆层复合粉:将ti粉与c粉按所述重量百分比混合后经过300℃加热后得到ticn涂覆层复合粉;(5)ticn涂覆层喷涂:采用反应等离子喷枪喷涂ticn涂覆层复合粉制备ticn涂覆层,所述ticn涂覆层的制备参数为:ar离子气体流量50l/h,n2离子气体流量50l/h,送粉气体为n2,其流量为3m3/h,电弧功率25kw,电流350a,喷涂距离80mm。一种防腐耐磨抽油机光杆,其创新之处在于:包括杆体及依次喷涂于杆体表面的crmo基层、nial粘结层及ticn涂覆层,其中nial粘结层的喷涂厚度为30μm,ticn涂覆层的喷涂厚度为20μm。实施例二一种抽油机光杆防腐耐磨ticn复合涂层,其创新之处在于:ticn复合涂层由crmo基层、nial粘结层及ticn涂覆层组成,crmo基层的组成及其重量百分比为:cr45gmo55gnial粘结层的组成及其重量百分比为:ni粉95gal粉5g所述ticn涂覆层的组成及其重量百分比为:c粉25gti粉75g。ni粉及al粉的粒度为325目。ti粉为timp-1钛粉,粒度为-300目。nial粘结层的喷涂厚度为50μm。ticn涂覆层的喷涂厚度为30μm。抽油机光杆防腐耐磨ticn复合涂层的喷涂方法,其创新之处在于:喷涂方法的步骤为:(1)抽油机光杆表层处理:将抽油机光杆用喷砂或砂纸打磨,除去铁锈、油污,获得洁净、高粗糙度的抽油机光杆表层;(2)crmo基层喷涂:在预处理后的抽油机光杆表层喷涂cr、mo粉末,并加热固化制备crmo基层;(3)nial粘结层喷涂:在crmo基层上采用反应等离子喷枪喷涂al/ni粉末,制备nial粘结层,所述nial粘结层的制备参数为:ar离子气体流量90l/min,n2离子气体流量60l/min,送粉气体为n2,其流量为0.5m3/h,电弧功率30kw,电流500a,喷涂距离150mm;(4)制备ticn涂覆层复合粉:将ti粉与c粉按所述重量百分比混合后经过300~350℃加热后得到ticn涂覆层复合粉;(5)ticn涂覆层喷涂:采用反应等离子喷枪喷涂ticn涂覆层复合粉制备ticn涂覆层,所述ticn涂覆层的制备参数为:ar离子气体流量70l/h,n2离子气体流量70l/h,送粉气体为n2,其流量为5m3/h,电弧功率30kw,电流500a,喷涂距离120mm。一种防腐耐磨抽油机光杆,其创新之处在于:包括杆体及依次喷涂于杆体表面的crmo基层、nial粘结层及ticn涂覆层,其中nial粘结层的喷涂厚度为50μm,ticn涂覆层的喷涂厚度为30μm。实施例三一种抽油机光杆防腐耐磨ticn复合涂层,其创新之处在于:所述ticn复合涂层由crmo基层、nial粘结层及ticn涂覆层组成,crmo基层的组成及其重量百分比为:cr42gmo58gnial粘结层的组成及其重量百分比为:ni粉92gal粉8gticn涂覆层的组成及其重量百分比为:c粉22gti粉78g。ni粉及al粉的粒度为200目。ti粉为timp-1钛粉,粒度为-300目。nial粘结层的喷涂厚度为40μm。ticn涂覆层的喷涂厚度为25μm。抽油机光杆防腐耐磨ticn复合涂层的喷涂方法,其特征在于:所述喷涂方法的步骤为:(1)抽油机光杆表层处理:将抽油机光杆表层用喷砂或砂纸打磨,除去铁锈、油污,获得洁净、高粗糙度的抽油机光杆表层;(2)crmo基层喷涂:在预处理后的抽油机光杆表层喷涂cr、mo粉末,并加热固化制备crmo基层;(3)nial粘结层喷涂:在crmo基层上采用反应等离子喷枪喷涂al/ni粉末,制备nial粘结层,所述nial粘结层的制备参数为:ar离子气体流量80l/min,n2离子气体流量40l/min,送粉气体流量0.5m3/h,电弧功率27kw,电流400a,喷涂距离120mm;(4)制备ticn涂覆层复合粉:将ti粉与c粉按所述重量百分比混合后经过300~350℃加热后得到ticn涂覆层复合粉;(5)ticn涂覆层喷涂:采用反应等离子喷枪喷涂ticn涂覆层复合粉制备ticn涂覆层,所述ticn涂覆层的制备参数为:ar离子气体流量60l/h,n2离子气体流量60l/h,送粉气体流量4m3/h,电弧功率27kw,电流400a,喷涂距离100mm。步骤(3)(5)中的送粉气体均为n2。一种防腐耐磨抽油机光杆,其特征在于:包括杆体及依次喷涂于杆体表面的crmo基层、nial粘结层及ticn涂覆层。nial粘结层的喷涂厚度为40μm。ticn涂覆层的喷涂厚度为25μm。ticn复合涂层的组织结构观察图1(a)为反应等离子喷涂ticn复合涂层液滴表面铺展图,将喂料送入反应等离子流中,经过高温离子流加热和加速后熔融液滴以极高的速度到达基体表面,发生铺展和凝固冷却。在整个喷涂的过程中,各个熔融液滴扁平化并且不断的堆叠最终形成涂层,从图中可以看出,液滴融化完全并且铺展良好。图1(b)为机械振动喷涂的ticn复合涂层表面图。可以看到涂层表面分布着形状不规则的黑色物质,由于涂层是经微波震荡处理过的,表面的铺展情况不如等离子喷涂的效果好。图2(a)为不含cr的ticn复合涂层sem图,图2(b)为cr含量为10%的ticn复合涂层sem图,图2(c)为cr含量为20%的ticn复合涂层sem图,图2(d)为cr含量为30%的ticn复合涂层sem图。从图2(a)中可以看出涂层表面存在孔洞和少量裂纹,图2(b)中白色区域为cr相,灰色区域为ticn相,孔洞处氧含量较高,说明孔洞处主要为氧化。随着cr含量的增多,图层中白色区域面积越来越大。对比得知,四个不同cr含量的涂层均存在裂纹和孔隙,因为涂层在熔化凝固过程中体积收缩,层与层之间存在较大的应力,而ticn本身硬度很高,脆性大,在制备过程中部分剥落形成孔洞。图3为不同mo含量ticn基复合涂层sem图。从图3可以看出,实际喷涂得到的涂层在厚度方向上有明显的微观组织和成分不均匀现象,从3组不同的mo含量的sem图片对比可以发现,随着mo含量的增多,白色区域面积逐渐增加,而这些白色区域主要是mo的碳化物和mo单质,同时也伴随着涂层孔隙率的有所增加。图4为涂层的截面sem形貌图及能谱分析图。从图中可以明显观察到,采用反应等离子喷涂所制得的ticn复合涂层的组织致密,喷涂各层之间结合较为紧密,没有明显的分层,涂层为典型的波浪状多层组织。从图4(a)中可以明显分辨出基体相、nial粘结层和涂层相。nial粘结层的厚度约为0.1mm左右,涂层的厚度在0.4-0.5mm之间。从图4(b)中可以看出,涂层和nial粘结层之间结合良好,涂层的截面致密,在其表面分布着黑色颗粒,该黑色颗粒为c。图4(c)为截面能谱分析图,由此可知,涂层中的c/n比值约为2.45,与tic0.7n0.3中的c/n原子比基本相同。另外,涂层中分布着o元素,由于制备的喂料ti颗粒被紧密包覆在核心,很少一部分ti在反应过程中被喷涂产生余热而被氧化。ticn复合涂层的相组成分析(xrd)对ticn复合涂层进行xrd分析。图5是ticn复合涂层的xrd图谱。从图中可以看出,涂层的主相为tic0.7n0.3,分别对应(111)、(200)、(220)、(311)和(222)五个晶体学方向,而且在(111)、(200)两个晶面呈现出强烈的取向,并且xrd衍射峰都有展宽的趋势,说明其中可能存在纳米晶粒。涂层中有少量氧化物存在,氧化物相为ti3o,并没有发现ti的存在,说明制备的喂料反应完全,氧化物的存在可能是因为在喷涂过程中涂层被氧化所致。另外由于制备的喂料石墨层将ti颗粒紧紧包覆,基本隔绝了ti与空气中氧气的反应。所以涂层中的氧化物含量低。ticn复合涂层的晶粒形貌分析在喷涂过程中,由于首先接触到基体的液滴处于快冷状态,在涂层厚度达到0.4mm左右时基体温度已经升高,液滴接触到基体时冷却速度要小于一开始的冷却速度,对ticn复合涂层的表面和背面进行了腐蚀以研究晶粒的生长,如图6所示。图6(a)和图6(b)分别为涂层背面和表面的腐蚀形貌图,从图6中可以明显观察到背面的晶粒为等轴晶,表面的晶粒已经长成树枝晶。图6(c)、图6(d)分别为图6(a)和图6(b)的放大图。背面的等轴晶颗粒细小,表层的等轴晶之间相互连接长大,刚开始喷涂时液滴接触到冷的基体冷却速度快,晶粒来不及长大,因此形成的是等轴晶。在后续的喷涂过程中,基体的温度升高,液滴的冷却速度降低,晶粒和晶粒之间相互相互连接长大,因此长成树枝晶。树枝晶之间相互交错,在磨损过程中可以形成阻力,防止晶粒被拽出。ticn复合涂层的xps分析ticn、tin、tic都为面心立方结构,因此在xrd谱上存在相似的结果,只通过xrd分析并不能完全确定ticn的存在,所以需要通过x射线光电子谱(xps)对涂层进行更深一步的分析,以通过测得涂层中各元素的结合能来准确地确定涂层的成分。图7为制备涂层表面全扫描xps谱图,从xps结合能谱线中可以看出,涂层表面元素为ti、c、n、o,ar为经ar+离子刻蚀后残留的元素。为了进一步确定涂层成分,对各元素进行窄扫描。图8为ti2p的光电子谱图,从图中可以看出ti2p的光电子峰由一对自旋轨道ti2p3/2和ti2p1/2峰组成,两个峰的结合能分别为454.82ev和460.84ev,峰间距为6.02ev;图中ti-n2p3/2与ti-n2p1/2的结合能分别为455.04ev与460.64ev;而454.65ev和460.48ev则分别对应着ti-c2p3/2与ti-c2p1/2结合能。tic与tin的结合能在ti2p谱图上非常接近,为了明确物质的组成,需要进一步分析ticn复合涂层的c1s与n1s谱。如图9所示,分别对c1s、n1s光电子谱分峰拟和。从图9(a)可以看出,c1s拟合出三个光电子峰位,其轨道电子结合能分别对应于281.32ev(p1)、284.38ev(p2)、285.16ev(p3);图9(b)n1s拟和谱中出2个峰位,其结合能分别为397.3ev(p1)、399.3ev(p2)。c1s(p1)峰和n1s(p1)峰相对其他峰较高,两个峰的结合能分别对应着ti-c、ti-n的结合能,两个峰值最高,峰面积最大,峰面积的大小代表了元素处于该化合价下的含量,因此涂层中ti-c、ti-n的含量较高。ticn复合涂层的tem分析图10所示为ticn复合涂层的透射分析图。从图10(a)明显观察到ticn主要以等轴晶的形式存在并且涂层的为纳米晶,晶粒直径在60~100nm之间,从图中还可以明显观察到ticn晶粒分布在大块的白色区域上,另外取图10(a)中的a区域进行高分辨分析,见图10(b)。经高分辨分析可以看出白色区域为杂乱无序的排列,呈现典型的非晶形貌特征,黑色斑点呈现微晶条纹,经过分析可知微晶的晶面间距为0.21nm,与tic0.7n0.3的(200)面基本相符(d(200)=0.214nm)。在喷涂的过程中,喂料等离子焰流内融化、反应,到达基体上迅速冷却凝固,导致了部分晶粒来不及形核因此形成了纳米晶。另外从图10(b)图中还可以观察到微晶相与非晶没有明显的边界,推断ticn晶粒是从非晶中形核长大的。ticn复合涂层的力学性能分析一般喷涂的陶瓷涂层只有几百微米的厚度,而且存在一定量的孔隙,所以它不可能像整体材料那样承受较大的载荷,它的力学性能要比实体材料低的多。显然,涂层的主要作用是赋予结构材料以某种附加功能,而不能替代结构材料。涂层的力学性能,对于涂层的某些应用领域,如摩擦磨损,抗冲蚀等,则是十分重要的。1)涂层显微硬度分析实验测量了不同载荷下(100g、200g、300g、500g、1000g)涂层的硬度,具体数据见表1。从表中数据可以看出,涂层具有高的硬度1674hv0.1,在载荷为1000g时仍能保持较高硬度1284hv1,相对于同属于面心立方结构的tin涂层1311hv0.1其硬度显著提高,这是因为ticn中c原子取代n原子,一方面形成高键能的ti-c键,另一方面造成了ticn的晶格畸变,这两者共同作用使得涂层的显微硬度提高。表1不同载荷下ticn复合涂层截面显微硬度载荷100g200g300g500g1000g硬度(hv0.2)16741520141713641284根据实验结果绘制如图11所示的显微硬度与载荷关系曲线图。从图中可以明显看出ticn复合涂层截面硬度随着载荷的增大呈下降趋势,即呈现明显的压痕尺寸效应。并且折线的斜率随着载荷的增大逐渐减小,并趋于稳定,压痕尺寸效应减弱,涂层的硬度值越趋近与真实硬度。产生压痕尺寸效应的主要原因是载荷功的额外消耗,从能量平衡的角度对压痕尺寸效应做出了新解释,在压痕过程中,由于材料内部裂纹的萌生和扩展、晶界的迁移以及试件表面和压头之间的摩擦等因素造成了能量的额外消耗。压痕的内部出现了微裂纹,压痕的尖角部位与涂层之间也发生了微开裂的现象,这些因素都导致了能量的消耗。2)显微压痕形貌的分析显微压痕的的形貌可以在一定程度上反映出材料的韧性。图12分别是不同载荷(100g,200g,300g,500g)下ticn复合涂层截面显微压痕的扫描图。由图12(a)可以看出100g时候的显微压痕较小,且规则平整,没有显微裂纹的出现,随着载荷进一步的增大,图12(b)(200g)、图12(c)(300g)的显微压痕相应的增大,几乎没有出现显微裂纹,只是涂层发生了一定程度的塑性变形,即ticn复合涂层可以承受一定的载荷而不发生脆性断裂。图12(d)中当载荷增大至500g时,d压痕尖角及其边缘出现了开裂及压碎的现象,并且压痕内部也出现了一定数量的显微裂纹,涂层被破坏,发生了脆性断裂。根据hall-petch模型总结出的经验公式:σy=σ0+kd-1/2可以知道晶粒越细小,即d值越小,材料的屈服强度σy越高。这是因为晶粒细小导致晶界面积增大,从而裂纹要扩展所需要的能量也就增高。因此与粗晶相比,ticn复合涂层晶粒为纳米晶,其韧性和强度在一定程度上得到改善与提高,脆断倾向小。3)结合强度实验采用拉伸实验的方法测量ticn复合涂层与基体的结合强度。其拉伸结果如图13所示。在影响ticn复合涂层结合强度的众多因素中,残余应力是最主要原因之一。残余应力的存在削弱了涂层与基体之间的结合强度,在使用过程中容易开裂脱落,降低涂层的使用寿命。一般认为,在喷涂过程中由于被高温等离子焰流加热融化的喂料熔滴到达基体时与基体的温差过大,造成涂层中残余应力的形成;另外熔滴在冷却过程中各层之间的温差不同以及涂层与基体的热膨胀系数有所差异所产生的,这也是涂层中残余应力的来源之一。影响涂层结合强度的另一个因素是由于涂层内部的位错、空位以及杂质等非热力因产生的内应力,又称为本征应力。从图13中可以明显看出,涂层断裂方式为ticn涂覆层和nial粘结层之间断裂,断裂过程中残余应力和本征应力同时涂层的断裂起到了作用。经过测量可知:ticn涂覆层和杆体之间有较高的结合强度,为26.7mpa.4)摩擦磨损性能分析①磨损载荷与摩擦系数关系润滑的目的是为了减小磨损量以及降低摩擦系数固体自润滑涂层往往具有较低的摩擦系数,在工程应用中显示出了巨大的优越性。tin具有优异的耐磨性能,为了研究ticn的耐磨性,实验以相同喷涂工艺下的tin涂层做对比。图14为两种涂层在不同承重载荷下摩擦系数曲线图。从图中可以明显观察到,随着载荷的增加,涂层的摩擦系数呈下降趋势,ticn复合涂层的摩擦系数由0.4233(100n)降低到0.2767(1000n),tin涂层的摩擦系数由0.6791(100n)降低到0.3509(1000n)。在干摩擦磨损过程中,摩擦系数随加载载荷的增加而降低负,这是因为负载增加导致了磨损表面的温度升高,摩擦副表面的硬度降低;另外由于载荷增加,摩擦副表面的塑性变形加剧,这些因素共同导致了摩擦副表面粗糙度降低,从而导致摩擦系数下降;另外从图中可以看出ticn复合涂层的摩擦系数始终都比较低并且明显低于tin涂层摩擦系数。这是因为等离子方法制备的ticn复合涂层中存在较多的游离石墨相,石墨具有非常低的剪切强度,在摩擦过程中受到摩擦副的正压力和剪切力的作用,极易形成转移膜,转移到对磨环上形成润滑膜,从而降低了摩擦系数;较低的摩擦系数可以使涂层在使用过程中的具有较小的启动力矩以及良好的减磨性能。②磨损载荷与失重量关系磨损是指物体工作表面的物质由于表面相对运动而不断损失的现象。任何光滑的表面从微观来看都是凹凸不平的,由许多波峰和波谷组成。在摩擦磨损过程中,在微观上摩擦副与涂层的波峰接触,接触点由弹性变形到塑性变形,另外摩擦过程中产生的大量的热,致使波峰与对磨环之间发生焊连,随着对磨环的转动,接触点脱离涂层面,造成了涂层的磨损。图15为ticn复合涂层和tin涂层在不同载荷下失重曲线图,从图中可以明显看出,随着施加载荷的增加,磨损量增大;另外ticn复合涂层的磨损量要明显低于tin的磨损量,这是因为tin的硬度低于ticn,在磨损过程中发生粘着磨损严重,施加载荷的增加增大了粘着磨损的发生,使得涂层破坏严重;ticn复合涂层本身硬度高,耐磨性好,而且在涂层中存在着润滑相—石墨,ticn在磨损过程中还可能发生分解,析出新的石墨相,这都大大提高了涂层的耐磨性。由图中可知,施加载荷小于500n时,ticn复合涂层的磨损量很小,并且随着载荷的增加磨损量增加趋势不明显,小于0.001g,然而tin涂层在100n的载荷下磨损量为0.0025g,大大高于ticn复合涂层的磨损量,并且随着载荷的增加,涂层磨损量增加的趋势要比ticn的高出很多;施加载荷大于500n时,两种涂层失重曲线的斜率大幅增高,出现这种现象的原因为磨损机制发生了变化,载荷小于500n时,为涂层的轻微磨损区,载荷大于500n时涂层发生严重磨损。在轻微磨损区时,涂层的磨损机理主要为塑性变形、犁耕、微切削和微断裂磨损,随着载荷的增大ticn复合涂层塑性变形能力差,涂层表面变形加剧,涂层内部微裂纹形成并扩展,当载荷大于500n时,微裂纹的密度达到足够高并结合在一起形成大裂纹,导致涂层发生断裂;另外由于载荷的不断增加,造成ticn摩擦表面积聚了大量的热,陶瓷本身韧性低、导热性差,因此在热作用下产生裂纹,造成涂层的破坏。当载荷大于700n时,失重量减缓,这可能是因为在摩擦磨损过程中,磨屑由于热作用在摩擦表面形成了ticn磨屑吸附层,使摩擦发生在磨屑吸附层和ticn之间,因此摩擦系数降低。另外在高载荷下涂层表面积聚了高的热量,涂层形成的氧化膜也会降低摩擦系数。由上述分析得:①涂层为纳米晶涂层,因此具有优异的力学性能。ticn复合涂层表现出高的硬度,为1674hv0.1。②采用拉伸的方法测定了涂层的结合强度,涂层断裂方式为ticn复合涂层和nial粘结层之间断裂,涂层具有和基体之间有较高的结合强度,为26.7mpa。③在相同的磨损条件下,ticn复合涂层的耐磨性明显高于tin涂层,耐磨性能优异,分析失效机理认为:在低载荷(<500n)的情况下涂层的磨损机理主要为微切削,犁耕和微断裂,当载荷较高时磨损机理变为断裂磨损,通过线扫描分析可以看出在磨损过程中同时发生着粘着磨损。6)腐蚀试验结果用模拟海水溶液浸泡表面积相同的镀铬层试样和ticn复合涂层试样,10天之后称重,采用失重法计算腐蚀速度。表2为腐蚀性试验原始数据,从表中可以看出镀铬层试样腐蚀速度约为ticn复合涂层腐蚀速度的3倍,说明,ticn复合涂层的试样比镀铬层试样具有更强的耐腐蚀性能。表2腐蚀性试验失重量对比数据尽管为说明目的公开了本发明的实施例和附图,但是本领域的技术人员可以理解:在不脱离本发明及所附权利要求的精神和范围内,各种替换、变化和修改都是可能的,因此,本发明的范围不局限于实施例和附图所公开的内容。当前第1页12