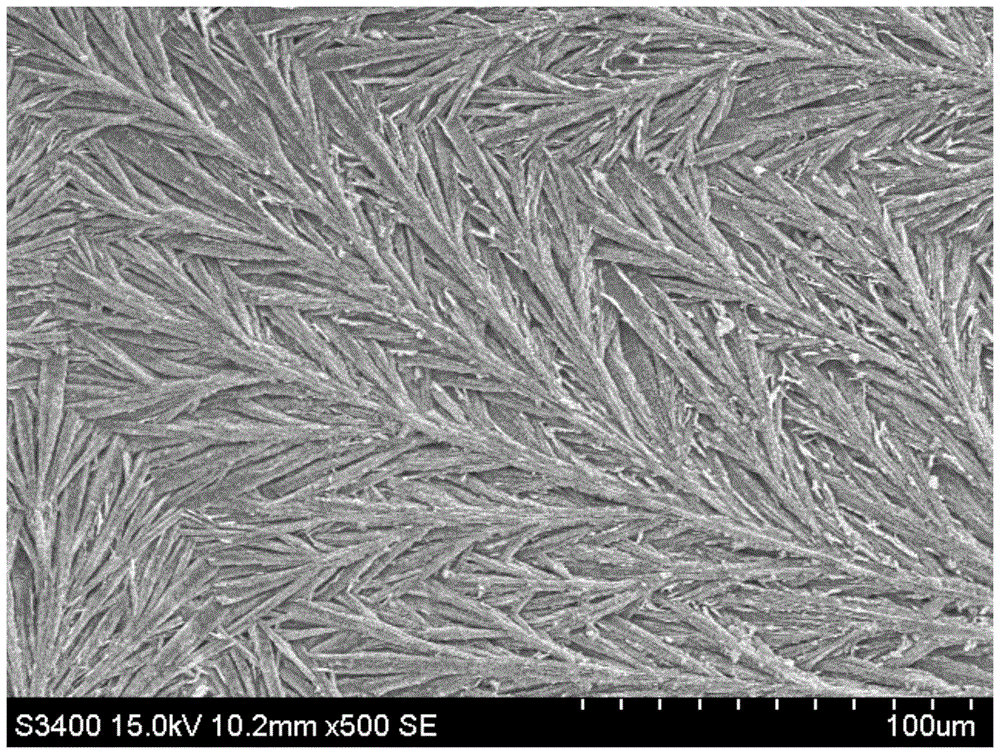
本发明属于钢铁表面处理
技术领域:
,具体涉及一种钢铁中温磷化液及其制备方法和使用方法。
背景技术:
:钢铁磷化是指钢铁与磷酸或其酸性盐溶液之间发生一系列化学或电化学反应,并在钢铁表面生成磷酸盐膜即磷化膜的过程。钢铁磷化的主要作用有:增强涂装膜层(如涂料涂层)与钢铁件间结合力,提高涂装后钢铁件表面涂层的耐蚀性;提高钢铁件装饰性;提高钢铁件的耐磨性;使钢铁件在机械加工过程中具有润滑性等。钢铁磷化工艺按操作温度可以分为低温、中温和高温磷化。中温磷化一般温度范围在50~75℃之间,高温磷化一般温度范围在90℃以上。由于传统的高温磷化能量消耗过大,并且因操作温度过高,磷化液中某些成分挥发损失增大,导致磷化液成分变化快,磷化膜层结晶颗粒不均,因此钢铁磷化逐步向中低温方向发展。中温磷化工艺膜层耐蚀性跟高温磷化膜差不多,且能耗较低,溶液浓度稳定,磷化速率快,磷化膜质量好,耐蚀性强,具有十分广泛的应用价值。目前用于钢铁的中温磷化液仍存在一定的缺陷,有待进一步改进。中国发明专利申请cn108085667a中公开一种适用于铸铁、碳钢工件的中温耐腐蚀黑色磷化处理剂及制备方法,该磷化液的组成如下:磷酸10~20%、氧化锌6~8%、质量浓度69%的硝酸15~20%、硝酸锰1~12%、碳酸锰1~10%、硝酸镍0.1~2%、edta-4钠0.1~2%、氟化钠0.1~2%、氟硅酸0.1~2%、柠檬酸铵0.1~2%、五水硫酸铜0.1~1%、钼酸钠0.1~1%、钼酸铵0.1~1%、过硫酸钠0.1~2%、亚硒酸0.1~2%及水余量。该磷化配方组分复杂,且亚硒酸有毒,价格昂贵,增加了原料成本,因此其应用和进一步发展受到限制。中国发明专利申请cn102605364a中公开了一种中温低沉渣低排放厚膜磷化液及其磷化方法,该专利在工件磷化前需用钛盐表调,使磷化操作程序繁杂。技术实现要素:本发明主要提供了一种钢铁中温磷化液及其制备方法和使用方法,采用中温磷化,既节约能源,又使形成的磷化膜层均匀致密,具有良好的耐腐蚀性。其技术方案如下:一种钢铁中温磷化液,每1l磷化液中含有马日夫盐20-55g、硝酸锌25-35g、硝酸镍1-9g、氯酸钠2-8g、络合促进剂0.5-4.0g,余量为水。优选的,每1l磷化液中含有马日夫盐45-55g、硝酸锌25-30g、硝酸镍2-7g、氯酸钠4-6g、络合促进剂0.5-2.0g,余量为水。优选的,所述络合促进剂为酒石酸、edta、柠檬酸中的一种或几种的混合。优选的,所述络合促进剂为柠檬酸。优选的,所述水为去离子水。优选的,所述磷化液的ph为2.2-2.8。上述钢铁中温磷化液的制备方法具体的为,取配方量的马日夫盐、硝酸锌、硝酸镍、氯酸钠、络合促进剂溶于水中,配制成混合溶液,调节混合溶液的ph至2.2-2.8,得磷化液。上述钢铁中温磷化液的使用方法具体的为,所述磷化液使用时对钢铁的磷化处理温度为60-70℃,磷化处理时间为15-30min。优选的,所述磷化液使用时对钢铁的磷化处理温度为65℃,磷化处理时间为20min。采用上述方案,本发明具有以下优点:本发明磷化液适用的磷化温度低,中温下即可实现磷化处理,节省能源,且磷化液组分简单,原料成本低,使用时无需表调,简化了磷化操作步骤,节能了处理成本。形成的磷化膜均匀致密,膜层与钢铁基体的粘接性强,最终所得磷化膜的硫酸铜点滴时间可达420s,3%nacl溶液浸泡时间超过6h,膜重可达12g/m2,说明磷化效果良好,具有良好的耐腐蚀性。附图说明图1为经本发明磷化液磷化所得磷化膜的电镜扫描图。具体实施方式以下实施例中的实验方法如无特殊规定,均为常规方法,所涉及的实验试剂及材料如无特殊规定均为常规生化试剂和材料。以下各实施例采用的组分原料为:马日夫盐:mnh4p2o8.2h2o,含量99%,上海麦克林生化科技有限公司;硝酸锌:zn(no3)2·6h2o,含量99%,江苏强盛化工有限公司;硝酸镍:ni(no3)2·6h2o,含量99%,国药集团化学试剂有限公司;氯酸钠:(nh2oh)·h2so4,含量99%,江苏强盛化工有限公司;柠檬酸:c6h8o7·h2o,含量99.5%,江苏永丰化学试剂厂。实施例1-6采用不同用量马日夫盐的磷化液(见表1)及其磷化效果实验。表1组分实施例1实施例2实施例3实施例4实施例5实施例6马日夫盐(g)102030505560硝酸锌(g)353535353535硝酸镍(g)777777氯酸钠(g)666666柠檬酸(g)333333水至1l至1l至1l至1l至1l至1l将实施例1~6中的6种磷化液用于钢铁件的磷化处理,ph值调节到2.3。磷化温度为60℃,磷化时间为30min。依照gb6807-86《钢铁件涂漆前磷化处理技术条件》,对制得的磷化膜采用硫酸铜点滴实验及3%氯化钠溶液浸泡实验来判断磷化液对钢铁件的磷化性能,其结果如表2所示。表2项目实施例1实施例2实施例3实施例4实施例5实施例6硫酸铜点滴时间71秒154秒213秒305秒384秒373秒氯化钠溶液浸泡时间0.5小时1小时2小时4小时6小时6小时由表2可知,当马日夫盐浓度由10g/l增加到55g/l时,磷化膜耐腐蚀性逐渐增强;在马日夫盐浓度为55g/l的情况下,耐蚀时间达到最高;继续增加马日夫盐浓度,所得磷化膜耐蚀时间不再有明显增加。在磷化液中,马日天盐主要提供mn2+和h2po4-离子,它是磷化膜形成的主要物质,且能很好的维持和稳定磷化液的游离酸和总酸度。控制好磷化液中马日天盐的含量,可以有效的提高磷化膜的抗腐蚀性能。马日夫盐浓度为55g/l时,磷化膜的耐蚀性最好。实施例7-11采用不同用量硝酸锌的磷化液(见表3)及其磷化效果实验。表3组分实施例7实施例8实施例9实施例10实施例11硝酸锌(g)2025303540马日夫盐(g)5555555555硝酸镍(g)66666氯酸钠(g)88888柠檬酸(g)22222水至1l至1l至1l至1l至1l将实施例7~11中的5种磷化液用于钢铁件的磷化处理,ph值调节到2.5。磷化温度为65℃,磷化时间为25min。依照gb6807-86《钢铁件涂漆前磷化处理技术条件》,对制得的磷化膜采用硫酸铜点滴实验及3%氯化钠溶液浸泡实验来判断磷化液对钢铁件的磷化性能,其结果如表4所示。表4项目实施例7实施例8实施例9实施例10实施例11硫酸铜点滴时间50秒277秒345秒269秒249秒氯化钠溶液浸泡时间1小时5.5小时6小时5小时4小时由表4可知,在硝酸锌浓度由20g/l增加到25g/l时,磷化膜耐蚀时间显著增大;硝酸锌浓度由25g/l增加到30g/l时,磷化膜耐蚀时间缓慢增加;继续增大硝酸锌浓度,磷化膜耐蚀时间随硝酸锌浓度的增加开始逐渐下降。因此,硝酸锌浓度为30g/l时,磷化膜耐蚀性达到最佳。实施例12-17采用不同用量硝酸镍的磷化液(见表5)及其磷化效果实验。表5组分实施例12实施例13实施例14实施例15实施例16实施例17硝酸镍(g)013579马日夫盐(g)505050505050硝酸锌(g)303030303030氯酸钠(g)666666柠檬酸(g)111111水至1l至1l至1l至1l至1l至1l将实施例12~17中的6种磷化液用于钢铁件的磷化处理,ph值调节到2.5。磷化温度为70℃,磷化时间为15min。依照gb6807-86《钢铁件涂漆前磷化处理技术条件》,对制得的磷化膜采用硫酸铜点滴实验及3%氯化钠溶液浸泡实验来判断磷化液对钢铁件的磷化性能,其结果如表6所示。表6由表6可知,磷化液中未引入硝酸镍时,磷化膜耐蚀性较差;引入硝酸镍的浓度为1g/l时,磷化膜耐蚀时间显著增大;继续增大硝酸镍浓度到7g/l,随着硝酸镍浓度的提高,磷化膜的耐蚀时间逐渐增加;再继续增加镍离子的浓度到9g/l,磷化膜的耐蚀时间出现下降趋势。由此可知,硝酸镍的最佳浓度为7g/时耐蚀性最好。对比实验本发明磷化液与现有磷化液的成膜耐蚀性对比实验。磷化温度均为65℃,磷化时间均为20min。表7为了比较本发明的磷化液与现有磷化液的成膜耐蚀性,选用表7中列出的两种磷化液进行对比实验,采用硫酸铜点滴实验法测定耐蚀时间。从表7中的数据结果可知,使用本发明的磷化液能够获得耐蚀性较高的磷化膜,本发明的磷化液制得的磷化膜点滴时间远大于现有磷化液所得磷化膜的点滴时间。本发明磷化液所得磷化膜呈灰黑色,硫酸铜点滴时间可达420s,3%nacl溶液浸泡时间超过6h,膜重可达12g/m2,属重量级。扫描电镜图如图1所示,磷化膜呈松针状,表面覆盖完整,未见基底裸露。膜层晶粒尺寸均匀,排列整齐、致密,有一定趋向性,这对磷化膜的耐蚀性具有很强的促进作用。对本领域的技术人员来说,可根据以上描述的技术方案以及构思,做出其它各种相应的改变以及形变,而所有的这些改变以及形变都应该属于本发明权利要求的保护范围之内。当前第1页12