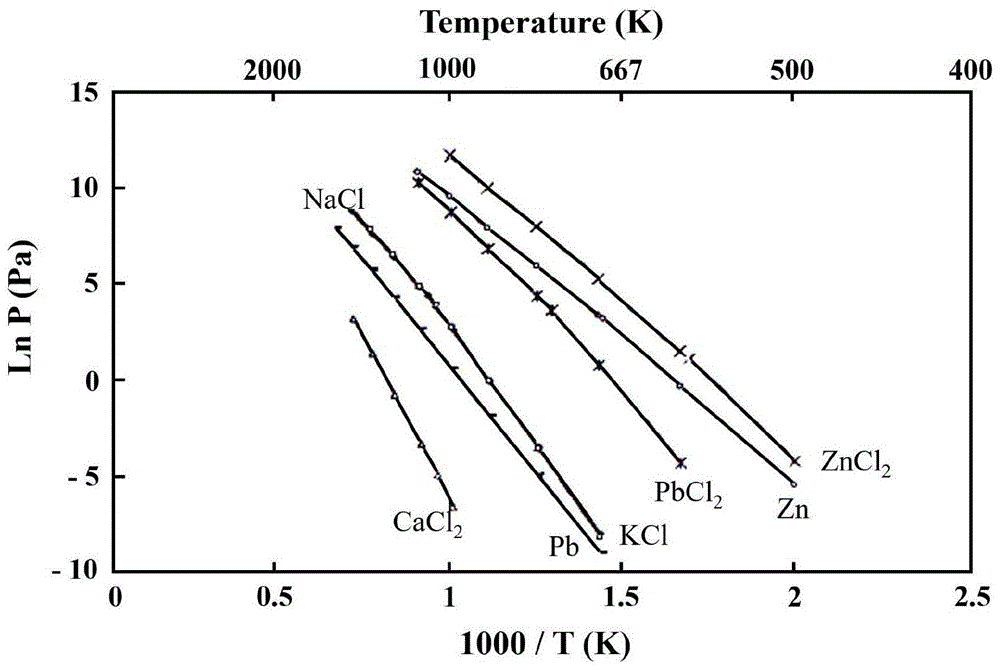
本发明属于固废处理
技术领域:
,尤其涉及一种有色金属冶炼渣的处理方法。
背景技术:
:有色金属冶炼渣是有色金属冶炼生产过程中产生的一类具有超稳定结构的化合物,我国的有色金属冶炼渣产生量大,每年以千万吨的速度递增。如铜浮选尾渣、氰化尾渣、铅冶炼渣、锌浸出渣等。有色金属冶炼渣中富含铜、铅、锌、铁、金、银等金属元素,是具有重要经济价值的二次资源,但其具有非常复杂的多组分体系,常规方法难以解离,其中的有价金属分离和富集异常困难。目前,有色金属冶炼渣的处理方法主要以露天堆放为主,该法未实现有色金属冶炼渣资源化利用,且渣中的重金属严重污染环境。现有技术中也有一些研究针对有色金属冶炼渣资源化利用,主要集中在火法贫化、湿法提取、选矿处理以及氯化焙烧等方面。cn109261347a公开了“一种铅锌有色金属冶炼渣资源化利用的方法”,该方法首先将铅锌有色金属冶炼渣磁选,将得到的磁选尾矿进行混合浮选,得到混合精矿和浮选尾矿,然后将混合精矿微波活化后进行高温处理,收集有价金属烟尘,该方法主要侧重于混合精矿微波活化后的高温处理,处理温度高达1300℃,处理时间高达10h。cn108273830a公开了“一种铜冶炼典型废渣协同同化/稳定化处理方法”,该方法通过对浮选渣改性预处理、破碎、球磨、配料、注模、成型、养护等工艺制备得到成品,该方法可实现废渣再利用,但流程较为繁复。cn101225468a公开了“磁化氯化法从酸化焙烧烧渣中回收金、银、铁和铅的方法”,该方法通过高温氯化焙烧回收渣中金银铜铅,同时使渣中铁元素磁化为四氧化三铁,该方法氯化焙烧温度高达1250℃,焙烧时间高达3h,且排放大量温室气体。另外,采用传统方法,金属回收率低、处理耗时长、能耗高、流程复杂,一直以来是限制有色金属冶炼渣资源化利用工业化应用的主要因素。由上可知,传统的有色金属冶炼渣利用方法技术手段落后,流程长,无害化、资源化水平较低,金属回收率低。因此,亟待开发一种经济、高效、环保的有色金属冶炼渣资源化利用方法。技术实现要素:本发明所要解决的技术问题是克服以上
背景技术:
中提到的不足和缺陷,提供一种有色金属冶炼渣回收有价金属的方法,该方法以卤化剂为焙烧主要添加剂,硫化物为焙烧辅助添加剂,在负压环境下进行焙烧,能够在低温环境下,节能高效地回收有色金属冶炼渣中的有价金属。为解决上述技术问题,本发明提出的技术方案为:一种负压卤化焙烧有色金属冶炼渣回收有价金属的方法,包括以下步骤:(1)将有色金属冶炼废渣、卤化剂、硫化物混合研磨(研磨至200目)、干燥得到预处理矿料;(2)将步骤(1)中得到的预处理矿料放入加热炉(如管式炉)内,控制加热炉内压力为负压,升温进行焙烧处理,焙烧处理过程中分区收集产生的金属卤化物烟气得到金属卤化物,焙烧结束后,产物快速冷却(30℃以下),得到焙烧渣。上述不同金属卤化物烟气在焙烧过程中,通过炉内不同温段实现分区收集。通过对收集到的混合金属卤化物进行水浸分离处理,可以实现各金属卤化物的分离。上述焙烧方法工业化应用时,可以在物料连续焙烧状态下实现金属卤化物烟气分区收集,同时可根据生产需要,定向分离回收目标金属卤化物,实现固废资源高值化综合利用。上述有色金属冶炼渣回收有价金属的方法中,优选的,所述有色金属冶炼废渣为铜浮选尾渣、氰化尾渣、铅冶炼渣或锌浸出渣中的一种或多种,所述有色金属冶炼废渣中含有铜、铅和锌。以zn和pb及其氯化物为例,其饱和蒸气压与温度的关系如图1所示。由图可知,在较低温度时,zn、pb氯化物已经具有较高的饱和蒸气压,如zncl2在550℃时饱和蒸气压高达1.01×106pa,说明在500-800℃的焙烧温度下,可以实现渣中金属的回收。上述有色金属冶炼渣回收有价金属的方法中,优选的,所述卤化剂为cacl2和/或ki,所述卤化剂的加入量为有色金属冶炼废渣质量的1-20%。更优选的,所述有色金属冶炼废渣为铜浮选尾渣,所述卤化剂为cacl2和ki,所述cacl2与ki的质量比为3:2,所述卤化剂的加入量为有色金属冶炼废渣质量的5-20%。本发明中,适当增加卤化剂的含量可以提升卤元素供体与pb、zn、cu相之间的接触率,促进卤化反应,但是考虑到有色金属冶炼渣中pb、zn、cu金属元素有限,过多含量的卤化剂对金属回收率的提升效果不显著。本发明的焙烧体系为固-固体系,选用cacl2和ki作为焙烧过程中的卤化剂,焙烧过程中cacl2和ki在高温作用下,与有色金属冶炼渣中的sio2形成稳定的硅酸盐和卤化气体(如cl2和i2),卤化气体再与有色金属冶炼渣中的含铜、铅、锌物相发生反应,生成低沸点的金属盐(如zncl2、pbcl2、cucl2、zni2、pbi2、cui)。上述氯化物体系,较nacl、fecl3、mgcl2、alcl3等氯化剂相比,cacl2的氯化效果更佳,成本更低廉。上述碘化物体系,ki较nai相比,经济适用性更高。我们研究发现,通过对有色金属冶炼渣的碘化焙烧和氯化焙烧实验效果对比可知,在负压焙烧的条件下,氯化焙烧过程pb、zn元素回收率更高,碘化焙烧过程cu元素回收率更高,同时采用cacl2和ki作为焙烧过程中的卤化剂,其二者协同作用,可以明显提升有色金属冶炼废渣中铜、铅、锌的回收率。以处理铜浮选尾渣为例,我们研究表明,cacl2与ki的质量比为3:2时,卤化挥发焙烧效果相对更优,pb、zn、cu金属元素综合收得率更高。上述有色金属冶炼渣回收有价金属的方法中,优选的,所述硫化物为含s元素35-45%的黄铁矿、辉铜矿或其他冶炼废渣,所述硫化物的加入量为有色金属冶炼废渣质量的2-5%。更优选的,所述卤化剂与硫化物的质量比为4:1。本发明中,我们研究表明,卤化焙烧过程中添加硫化物可以促进卤化剂的分解生成卤族气体(如cl2、i2)。从热力学上分析,这是因为硫化物在参与有色金属冶炼渣(如铜浮选尾渣)卤化焙烧过程中,可以降低卤化剂(如cacl2、ki)与有色金属冶炼渣之间反应生成硅酸盐(如casio4、k2sio4)和卤族气体(如cl2、i2)的吉布斯自由能,进而促进卤族气体与有色金属冶炼渣中pb、zn、cu元素的卤化反应过程。在硫化物参与的焙烧过程中,硫化物中的s元素以caso4的形式得到富集,不产生其他废气,实现了从有色金属冶炼渣中高效、环保地回收有价金属的目的。硫化物含量过低,反应过程促进效果不明显,硫化物含量过高,会导致金属回收率下降,这是因为硫化物具有还原性,过量的硫化物会降低卤化气体对pb、zn、cu金属元素的卤化效率。综合考虑,硫化物的加入量为有色金属冶炼废渣质量的2.5-5%。以处理铜浮选尾渣为例,硫化物的加入量为有色金属冶炼渣的5%更优。更优选的,考虑到硫化物作用发挥与卤化剂具有不可分割的联系,我们研究表明,卤化剂(cacl2或ki)与硫化物的质量比为4:1时,卤化挥发焙烧效果相对更优,pb、zn、cu金属综合元素收得率更高。上述有色金属冶炼渣回收有价金属的方法中,优选的,所述预处理矿料中还加入有二氧化硅,所述二氧化硅的加入量为有色金属冶炼废渣质量的5-10%。本发明中,有色金属冶炼渣中的pb、zn、cu主要以zn2sio4、znfe2o4、pbo、cuo形式赋存,根据反应的热力学计算表明,在这些物质的卤化反应过程中,加入酸性氧化物sio2会显著降低反应的吉布斯自由能,促进反应进行,提升金属回收率。有色金属冶炼渣中只含有少量sio2,为提升金属回收率,需结合不同有色金属冶炼渣的成分及物相组成,适当添加sio2促进卤化挥发焙烧过程,提升工艺的经济价值。以处理铅冶炼渣为例,我们研究表明,添加铅冶炼渣渣质量5%的sio2更有利于提升金属回收率。以采用氯化钙处理冶炼废渣中的znfe2o4、pbo和cuo回收zn、pb、cu为例,无活化剂与添加sio2作为活化剂时,氯化焙烧过程中涉及的主要反应分别为:①znfe2o4+cacl2=zncl2(g)+cao+fe2o3;②pbo+cacl2=pbcl2(g)+cao;③cuo+cacl2=cucl2(g)+cao;④znfe2o4+cacl2+sio2=zncl2(g)+fe2o3+casio3;⑤pbo+cacl2+sio2=pbcl2(g)+casio3;⑥cuo+cacl2+sio2=cucl2(g)+casio3;通过热力学数据及hsc软件计算做出如图2所示的各反应吉布斯自由能变化与温度的关系图。由图2可知,采用sio2作为活化剂时,其氯化反应的自由能小于无活化剂作用的氯化反应吉布斯自由能。即在焙烧过程中添加sio2提高了氯化反应趋势。上述有色金属冶炼渣回收有价金属的方法中,优选的,所述升温进行焙烧处理时,控制升温的速率为5-10℃/min,升温至500-800℃,控制焙烧处理的时间为10-60min,并对焙烧体系抽真空,控制焙烧体系压力为0.05-0.1atm。本发明中,采用负压条件进行卤化挥发焙烧,负压条件下能够改变物质挥发饱和蒸汽压,有利于金属卤化物的挥发。同时,根据卤化原理可知,焙烧过程中卤化反应分为两步进行,首先是卤化剂反应分解出气态cl2或i2,然后在cl2或i2的作用下,对有色金属冶炼渣中pb、zn、cu金属元素进行卤化反应。以反应cuo+cacl2+sio2=cucl2(g)+casio3为例,根据公式及相关热力学文献中的数据,可以计算出不同系统压力下反应的吉布斯自由能,式中10mpa为假设系统压力。当m分别为5、4.7、3、3.7、2、2.7和1时,所对应的系统压力分别为100000pa(1atm)、50000pa、10000pa、5000pa、1000pa、500pa和100pa。图3为该反应在不同系统压力下的吉布斯自由能变化。由此可以看出,负压条件下,更容易发生卤化剂的反应分解,系统压力越低,卤化剂分解反应越容易。但系统压力过低,会导致加热炉炉膛变形,对加热炉的耐压要求更高,同时增加能耗。综合考虑,焙烧体系的系统压力为0.05-0.1atm最佳。另外,我们研究表明,在负压条件下进行卤化焙烧,有利于促进cacl2或ki的协同作用,以更好发挥卤化作用,提高铜、铅、锌的回收率。本发明中,若焙烧温度过低,会使得渣中金属元素卤化效果差,金属回收率低。若焙烧温度过高,会使得渣熔化,不利于卤化反应的进行。根据上述卤化原理可知,卤化剂高温下所释放的气态cl2或i2与渣中pb、zn、cu金属相进行卤化反应,气体与固态颗粒之间的卤化效率远高于在熔体中的卤化效率,且焙烧温度过高将影响有色金属冶炼渣处理成本。综合考虑,卤化挥发焙烧温度为500-800℃。本发明中,焙烧时间对pb、zn、cu金属卤化挥发效果影响较大,若焙烧时间过短,会使得渣中金属元素无法充分卤化,金属回收率低。若焙烧时间过长,会影响有色金属冶炼渣处理成本。综合考虑,卤化挥发焙烧处理时间为10-60min。上述有色金属冶炼渣回收有价金属的方法中,优选的,所述有色金属冶炼废渣中同时含有铜、锌和铅,所述卤化剂为cacl2和ki,所述加热炉为多温区加热炉,包括焙烧段和四段金属卤化物收集段,所述焙烧段产生的金属卤化物烟气依次经过第一金属卤化物收集段、第二金属卤化物收集段、第三金属卤化物收集段和第四金属卤化物收集段收集。更优选的,所述第一金属卤化物收集段的温度控制为550-600℃,所述第二金属卤化物收集段的温度控制为450-500℃,所述第三金属卤化物收集段的温度控制为300-400℃,所述第四金属卤化物收集段的温度控制为150-250℃。进一步优选的,所述第一金属卤化物收集段的温度控制为550℃,所述第二金属卤化物收集段的温度控制为475℃,所述第三金属卤化物收集段的温度控制为350℃,所述第四金属卤化物收集段的温度控制为200℃。上述加热炉炉腔内具有可控多温段,升温过程可保持炉腔内压力不变,焙烧段主要负责卤化挥发,金属卤化物收集段主要用于分段进行烟气的收集,根据氯化铜、碘化亚铜、氯化锌、碘化锌、氯化铅和碘化铅的不同熔点及不同挥发性能和凝固特性确定温度,其中,第一金属卤化物收集段,温度约控制为550℃,冷凝回收cucl2(熔点620℃)、cui(熔点605℃)烟气,第二金属卤化物收集段温度约控制为475℃,冷凝回收pbcl2(熔点501℃),第三金属卤化物收集段温度约控制为350℃,冷凝回收zni2(熔点446℃)烟气、pbi2(熔点402℃),第四金属卤化物收集段温度约控制为200℃,冷凝回收zncl2(熔点283℃)烟气。上述有色金属冶炼渣回收有价金属的方法中,优选的,所述第一金属卤化物收集段与第三金属卤化物收集段收集的金属卤化物烟尘经水浸处理以分离不同种类的金属卤化物,所述水浸处理时,控制浸出温度为60-80℃,固液比为1:(5-10)(质量:体积),浸出时间为30-60min。本发明中,针对同时含有铜、锌和铅的有色金属冶炼废渣,我们优选采用cacl2和ki的共同卤化剂,虽然可以提高铜、锌、铅整体的回收率,但最终得到的烟气难以较纯净的分离,即便我们采用多温区加热炉,通过不同的金属卤化物收集段处理,也难以得到单一的金属卤化物。我们进一步研究表明,采用水浸处理方法对第一金属卤化物收集段与第三金属卤化物收集段收集的金属卤化物进行进一步分离,可以得到单一、纯净的金属卤化物。其中,第一金属卤化物收集段收集物为cucl2和cui,第三金属卤化物收集段收集物为zni2和pbi2。由于cui和pbcl2不溶于水,对以上两段收集物分别进行水浸处理,可以分离cucl2、cui、zni2和pbi2。卤化挥发焙烧法属于火法冶金范畴,主要利用金属卤化物普遍具有熔沸点较低、挥发性高、易溶于水等特点,使金属元素以卤化物(如氯化物、碘化物等)形式从伴生体系中挥发出来。同时,根据金属卤化物生成的难易不同和性质差异,通过控制反应温度和产物蒸汽压等条件,将金属元素选择性卤化挥发,达到金属元素分离的目的。本发明利用卤化挥发焙烧法,优化焙烧为负压环境,优化焙烧过程中的辅助添加剂,各因素相互配合,协同作用,可以大大降低焙烧温度,缩短焙烧时间,提高金属元素的回收率,充分利用有色金属冶炼废渣,创造可观的经济效益。与现有技术相比,本发明的优点在于:1、本发明采用硫化物作为焙烧添加剂,硫化物中的s具有活化、降低卤化反应吉布斯自由能的作用。使用本发明所提供的硫化物作为焙烧添加剂对有色金属冶炼渣进行卤化挥发焙烧,可促进有色金属冶炼渣中pb、zn、cu元素的卤化挥发,同时可降低卤化挥发pb、zn、cu元素的焙烧温度,缩短焙烧时间,提高金属回收率,降低工艺成本。2、本发明采用负压条件进行有色金属冶炼渣卤化焙烧,负压条件下可以使得物质挥发饱和蒸汽压发生改变,有利于金属卤化物的挥发。负压条件降低了卤化挥发pb、zn、cu元素的焙烧温度,缩短了焙烧时间。3、本发明完成达产时,以处理铜浮选尾渣为例,我国每年铜尾渣产生量为1986.6万吨,通过本发明方法,每年可回收39.73万吨zn、7.95万吨pb等金属,创造百亿级的经济效益。此外,通过本发明方法处理过的有色金属冶炼渣,重金属含量远低于国家《危险废物填埋污染控制标准(gb18598-2019)》,实现了有色金属冶炼渣清洁化高效处理。附图说明为了更清楚地说明本发明实施例或现有技术中的技术方案,下面将对实施例或现有技术描述中所需要使用的附图作简单地介绍,显而易见地,下面描述中的附图是本发明的一些实施例,对于本领域普通技术人员来讲,在不付出创造性劳动的前提下,还可以根据这些附图获得其他的附图。图1为本发明负压卤化焙烧法所回收典型金属及其氯化物的饱和蒸气压与温度的关系。图2为本发明负压卤化焙烧有色金属冶炼渣典型反应的自由能变化与温度关系图。图3为本发明负压卤化焙烧有色金属冶炼渣典型反应在不同系统压力下自由能变化图。图4为本发明负压卤化焙烧有色金属冶炼渣回收有价金属的方法的工艺流程图。具体实施方式为了便于理解本发明,下文将结合说明书附图和较佳的实施例对本发明作更全面、细致地描述,但本发明的保护范围并不限于以下具体的实施例。除非另有定义,下文中所使用的所有专业术语与本领域技术人员通常理解的含义相同。本文中所使用的专业术语只是为了描述具体实施例的目的,并不是旨在限制本发明的保护范围。除非另有特别说明,本发明中用到的各种原材料、试剂、仪器和设备等均可通过市场购买得到或者可通过现有方法制备得到。下述实施例、对比例中所用铜浮选尾渣、氰化尾渣、铅冶炼渣、锌浸出渣和硫化物(以黄铁矿为例)的重要化学组成分别为表1、表2、表3、表4和表5所示。表1:铜浮选尾渣化学组成(%,ω)名称pbzncusio2质量分数(%)0.4512.8030.55111.75表2:氰化尾渣化学组成(%,ω)名称pbzncusio2质量分数(%)0.320.570.3318.98表3:铅冶炼渣化学组成(%,ω)名称pbznsio2质量分数(%)3.357.759.83表4:锌浸出渣化学组成(%,ω)名称pbzncusio2质量分数(%)5.064.950.2613.67表5:黄铁矿化学组成(%,ω)名称fessio2质量分数(%)42.7840.6111.71实施例1:如图4所示,一种有色金属冶炼渣回收有价金属的方法,包括以下步骤:(1)将20g铜浮选尾渣(成分如表1所示,下同)、4gcacl2和1gfes2(黄铁矿,成分如表5所示,下同)混匀后研磨至200目后,放入刚玉舟(长度为120mm,宽度为60mm,高度为20mm)中,干燥60min后得到预处理矿料;(2)将预处理矿料放入管式炉中,将炉内压力控制为0.05atm,以5-10℃/min的升温速度升温至800℃,随后进行卤化挥发焙烧,焙烧时间为60min,焙烧处理过程中分区收集产生的烟气,焙烧结束后得到pbcl2、zncl2、cucl2与焙烧渣。上述分区收集采用三温区加热炉,分别回收pbcl2、zncl2、cucl2。经测定,本实施例中,pb金属回收率为97.45%,zn金属回收率为85.32%,cu金属回收率为70.96%。对比例1:如图4所示,一种有色金属冶炼渣回收有价金属的方法,包括以下步骤:(1)将20g铜浮选尾渣(成分如表1所示,下同)、8gcacl2和1gfes2(黄铁矿,成分如表5所示,下同)混匀后研磨至200目后,放入刚玉舟(长度为120mm,宽度为60mm,高度为20mm)中,干燥60min后得到预处理矿料;(2)将预处理矿料放入管式炉中,将炉内压力控制为0.05atm,以5-10℃/min的升温速度升温至800℃,随后进行卤化挥发焙烧,焙烧时间为60min,焙烧处理过程中收集产生的烟气,焙烧结束后得到pbcl2、zncl2、cucl2与焙烧渣。上述分区收集采用三温区加热炉,分别回收pbcl2、zncl2、cucl2。经测定,本对比例中,pb金属回收率为97.53%,zn金属回收率为86.11%,cu金属回收率为70.17%。实施例2:如图4所示,一种有色金属冶炼渣回收有价金属的方法,包括以下步骤:(1)将20g铜浮选尾渣、1gcacl2和1gfes2混匀后研磨至200目后,放入刚玉舟(长度为120mm,宽度为60mm,高度为20mm)中,干燥60min后得到预处理矿料;(2)将预处理矿料放入管式炉中,将炉内压力控制为0.05atm,以5-10℃/min的升温速度升温至800℃,随后进行卤化挥发焙烧,焙烧时间为60min,焙烧处理过程中收集产生的烟气,焙烧结束后得到pbcl2、zncl2、cucl2与焙烧渣。上述分区收集采用三温区加热炉,分别回收pbcl2、zncl2、cucl2。经测定,本实施例中,pb金属回收率为75.23%,zn金属回收率为42.12%,cu金属回收率为30.41%。实施例3:如图4所示,一种有色金属冶炼渣回收有价金属的方法,包括以下步骤:(1)将20g铜浮选尾渣、4gki和1gfes2混匀后研磨至200目后,放入刚玉舟(长度为120mm,宽度为60mm,高度为20mm)中,干燥60min后得到预处理矿料;(2)将预处理矿料放入管式炉中,将炉内压力控制为0.05atm,以5-10℃/min的升温速度升温至800℃,随后进行卤化挥发焙烧,焙烧时间为60min,焙烧处理过程中分段收集产生的烟气,焙烧结束后得到zni2、pbi2、cui与焙烧渣。上述分区收集采用三温区加热炉,分别回收zni2、pbi2、cui。经测定,本实施例中,pb金属回收率为84.12%,zn金属回收率为64.71%,cu金属回收率为86.83%。实施例4:如图4所示,一种有色金属冶炼渣回收有价金属的方法,包括以下步骤:(1)将20g铜浮选尾渣、2.4gcacl2、1.6gki和1gfes2混匀后研磨至200目后,放入刚玉舟(长度为120mm,宽度为60mm,高度为20mm)中,干燥60min后得到预处理矿料;(2)将预处理矿料放入管式炉中,将炉内压力控制为0.05atm,以5-10℃/min的升温速度升温至800℃,随后进行卤化挥发焙烧,焙烧时间为60min,焙烧处理过程中分段收集产生的烟气。焙烧段产生的金属卤化物烟气依次经过第一金属卤化物收集段、第二金属卤化物收集段、第三金属卤化物收集段和第四金属卤化物收集段收集。第一金属卤化物收集段的温度控制为550℃,第二金属卤化物收集段的温度控制为475℃,第三金属卤化物收集段的温度控制为350℃,第四金属卤化物收集段的温度控制为200℃。其中,第一金属卤化物收集段冷凝回收cucl2、cui烟气,第二金属卤化物收集段温度冷凝回收pbcl2,第三金属卤化物收集段约冷凝回收zni2、pbi2,第四金属卤化物收集段冷凝回收zncl2烟气。上述第一金属卤化物收集段与第三金属卤化物收集段收集的混合金属卤化物烟尘经水浸处理以分离不同种类的金属卤化物。水浸温度为70℃、固液比为1:5、浸出时间为60min。经水浸分离处理后,得到zncl2、pbcl2、cucl2、zni2、pbi2、cui与焙烧渣。经测定,本实施例中,pb金属回收率为97.40%,zn金属回收率为85.29%,cu金属回收率为85.17%。实施例5:如图4所示,一种有色金属冶炼渣回收有价金属的方法,包括以下步骤:(1)将20g铜浮选尾渣、2.4gcacl2、1.6gki和0.5gfes2混匀后研磨至200目后,放入刚玉舟(长度为120mm,宽度为60mm,高度为20mm)中,干燥60min后得到预处理矿料;(2)将预处理矿料放入管式炉中,将炉内压力控制为0.05atm,以5-10℃/min的升温速度升温至800℃,随后进行卤化挥发焙烧,焙烧时间为60min,焙烧处理过程中分段收集产生的烟气。经过水浸温度为70℃、固液比为1:5、浸出时间为60min的水浸分离处理后,得到zncl2、pbcl2、cucl2、zni2、pbi2、cui与焙烧渣(具体分区收集方式、水浸处理方式同实施例4)。经测定,本实施例中,pb金属回收率为89.71%,zn金属回收率为76.12%,cu金属回收率为78.11%。对比例2:如图4所示,一种有色金属冶炼渣回收有价金属的方法,包括以下步骤:(1)将20g铜浮选尾渣、2.4gcacl2、1.6gki和2gfes2混匀后研磨至200目后,放入刚玉舟(长度为120mm,宽度为60mm,高度为20mm)中,干燥60min后得到预处理矿料;(2)将预处理矿料放入管式炉中,将炉内压力控制为0.05atm,以5-10℃/min的升温速度升温至800℃,随后进行卤化挥发焙烧,焙烧时间为60min,焙烧处理过程中分段收集产生的烟气。经过水浸温度为70℃、固液比为1:5、浸出时间为60min的水浸分离处理后,得到zncl2、pbcl2、cucl2、zni2、pbi2、cui与焙烧渣(具体分区收集方式、水浸处理方式同实施例4)。经测定,本对比例中,pb金属回收率为83.13%,zn金属回收率为72.64%,cu金属回收率为72.72%。实施例6:如图4所示,一种有色金属冶炼渣回收有价金属的方法,包括以下步骤:(1)将20g铜浮选尾渣、2.4gcacl2、1.6gki和1gfes2混匀后研磨至200目后,放入刚玉舟(长度为120mm,宽度为60mm,高度为20mm)中,干燥60min后得到预处理矿料;(2)将预处理矿料放入管式炉中,将炉内压力控制为0.05atm,以5-10℃/min的升温速度升温至500℃,随后进行卤化挥发焙烧,焙烧时间为60min,焙烧处理过程中分段收集产生的烟气。经过水浸温度为70℃、固液比为1:5、浸出时间为60min的水浸分离处理后,得到zncl2、pbcl2、cucl2、zni2、pbi2、cui与焙烧渣(具体分区收集方式、水浸处理方式同实施例4)。经测定,本实施例中,pb金属回收率为65.13%,zn金属回收率为26.12%,cu金属回收率为10.27%。对比例3:如图4所示,一种有色金属冶炼渣回收有价金属的方法,包括以下步骤:(1)将20g铜浮选尾渣、2.4gcacl2、1.6gki和1gfes2混匀后研磨至200目后,放入刚玉舟(长度为120mm,宽度为60mm,高度为20mm)中,干燥60min后得到预处理矿料;(2)将预处理矿料放入管式炉中,将炉内压力控制为0.05atm,以5-10℃/min的升温速度升温至1200℃,随后进行卤化挥发焙烧,焙烧时间为60min,焙烧处理过程中分段收集产生的烟气。经过水浸温度为70℃、固液比为1:5、浸出时间为60min的水浸分离处理后,得到zncl2、pbcl2、cucl2、zni2、pbi2、cui与焙烧渣(具体分区收集方式、水浸处理方式同实施例4)。经测定,本对比例中,pb金属回收率为63.62%,zn金属回收率为47.42%,cu金属回收率为67.92%。实施例7:如图4所示,一种有色金属冶炼渣回收有价金属的方法,包括以下步骤:(1)将20g铜浮选尾渣、2.4gcacl2、1.6gki和1gfes2混匀后研磨至200目后,放入刚玉舟(长度为120mm,宽度为60mm,高度为20mm)中,干燥60min后得到预处理矿料;(2)将预处理矿料放入管式炉中,将炉内压力控制为0.05atm,以5-10℃/min的升温速度升温至800℃,随后进行卤化挥发焙烧,焙烧时间为10min,焙烧处理过程中分段收集产生的烟气。经过水浸温度为70℃、固液比为1:5、浸出时间为60min的水浸分离处理后,得到zncl2、pbcl2、cucl2、zni2、pbi2、cui与焙烧渣(具体分区收集方式、水浸处理方式同实施例4)。经测定,本实施例中,pb金属回收率为69.12%,zn金属回收率为40.64%,cu金属回收率为20.12%。实施例8:如图4所示,一种有色金属冶炼渣回收有价金属的方法,包括以下步骤:(1)将20g铜浮选尾渣、2.4gcacl2、1.6gki和1gfes2混匀后研磨至200目后,放入刚玉舟(长度为120mm,宽度为60mm,高度为20mm)中,干燥60min后得到预处理矿料;(2)将预处理矿料放入管式炉中,将炉内压力控制为0.1atm,以5-10℃/min的升温速度升温至800℃,随后进行卤化挥发焙烧,焙烧时间为60min,焙烧处理过程中分段收集产生的烟气。经过水浸温度为70℃、固液比为1:5、浸出时间为60min的水浸分离处理后,得到zncl2、pbcl2、cucl2、zni2、pbi2、cui与焙烧渣(具体分区收集方式、水浸处理方式同实施例4)。经测定,本实施例中,pb金属回收率为91.22%,zn金属回收率为75.65%,cu金属回收率为78.28%。实施例9:如图4所示,一种有色金属冶炼渣回收有价金属的方法,包括以下步骤:(1)将20g氰化尾渣(成分如表2所示)、2.4gcacl2、1.6gki和1gfes2混匀后研磨至200目后,放入刚玉舟(长度为120mm,宽度为60mm,高度为20mm)中,干燥60min后得到预处理矿料;(2)将预处理矿料放入管式炉中,将炉内压力控制为0.05atm,以5-10℃/min的升温速度升温至800℃,随后进行卤化挥发焙烧,焙烧时间为60min,焙烧处理过程中分段收集产生的烟气。经过水浸温度为70℃、固液比为1:5、浸出时间为60min的水浸分离处理后,得到zncl2、pbcl2、cucl2、zni2、pbi2、cui与焙烧渣(具体分区收集方式、水浸处理方式同实施例4)。经测定,本实施例中,pb金属回收率为95.60%,zn金属回收率为91.73%,cu金属回收率为88.11%。实施例10:如图4所示,一种有色金属冶炼渣回收有价金属的方法,包括以下步骤:(1)将20g铅冶炼渣(成分如表3所示)、2.4gcacl2、1.6gki和1gfes2混匀后研磨至200目后,放入刚玉舟(长度为120mm,宽度为60mm,高度为20mm)中,干燥60min后得到预处理矿料;(2)将预处理矿料放入管式炉中,将炉内压力控制为0.05atm,以5-10℃/min的升温速度升温至800℃,随后进行卤化挥发焙烧,焙烧时间为60min,焙烧处理过程中分段收集产生的烟气。经过水浸温度为70℃、固液比为1:5、浸出时间为60min的水浸分离处理后,得到zncl2、pbcl2、zni2、pbi2与焙烧渣(zncl2、pbi2经水浸分离处理)。经测定,本实施例中,pb金属回收率为90.12%,zn金属回收率为87.81%。实施例11:如图4所示,一种有色金属冶炼渣回收有价金属的方法,包括以下步骤:(1)将20g铜浮选尾渣、2.4gcacl2、1.6gki、1gfes2和1gsio2混匀后研磨至200目后,放入刚玉舟(长度为120mm,宽度为60mm,高度为20mm)中,干燥60min后得到预处理矿料;(2)将预处理矿料放入管式炉中,将炉内压力控制为0.05atm,以5-10℃/min的升温速度升温至800℃,随后进行卤化挥发焙烧,焙烧时间为60min,焙烧处理过程中分段收集产生的烟气。经过水浸温度为70℃、固液比为1:5、浸出时间为60min的水浸分离处理后,得到zncl2、pbcl2、cucl2、zni2、pbi2、cui与焙烧渣(具体分区收集方式、水浸处理方式同实施例4)。经测定,本实施例中,pb金属回收率为98.12%,zn金属回收率为87.21%,cu金属回收率为86.69%。实施例12:如图4所示,一种有色金属冶炼渣回收有价金属的方法,包括以下步骤:(1)将20g锌浸出渣(成分如表4所示)、2.4gcacl2、1.6gki和1gfes2混匀后研磨至200目后,放入刚玉舟(长度为120mm,宽度为60mm,高度为20mm)中,干燥60min后得到预处理矿料;(2)将预处理矿料放入管式炉中,将炉内压力控制为0.05atm,以5-10℃/min的升温速度升温至800℃,随后进行卤化挥发焙烧,焙烧时间为60min,焙烧处理过程中分段收集产生的烟气。经过水浸温度为70℃、固液比为1:5、浸出时间为60min的水浸分离处理后,得到zncl2、pbcl2、cucl2、zni2、pbi2、cui与焙烧渣(具体分区收集方式、水浸处理方式同实施例4)。经测定,本实施例中,pb金属回收率为87.63%,zn金属回收率为91.21%,cu金属回收率为72.94%。当前第1页12