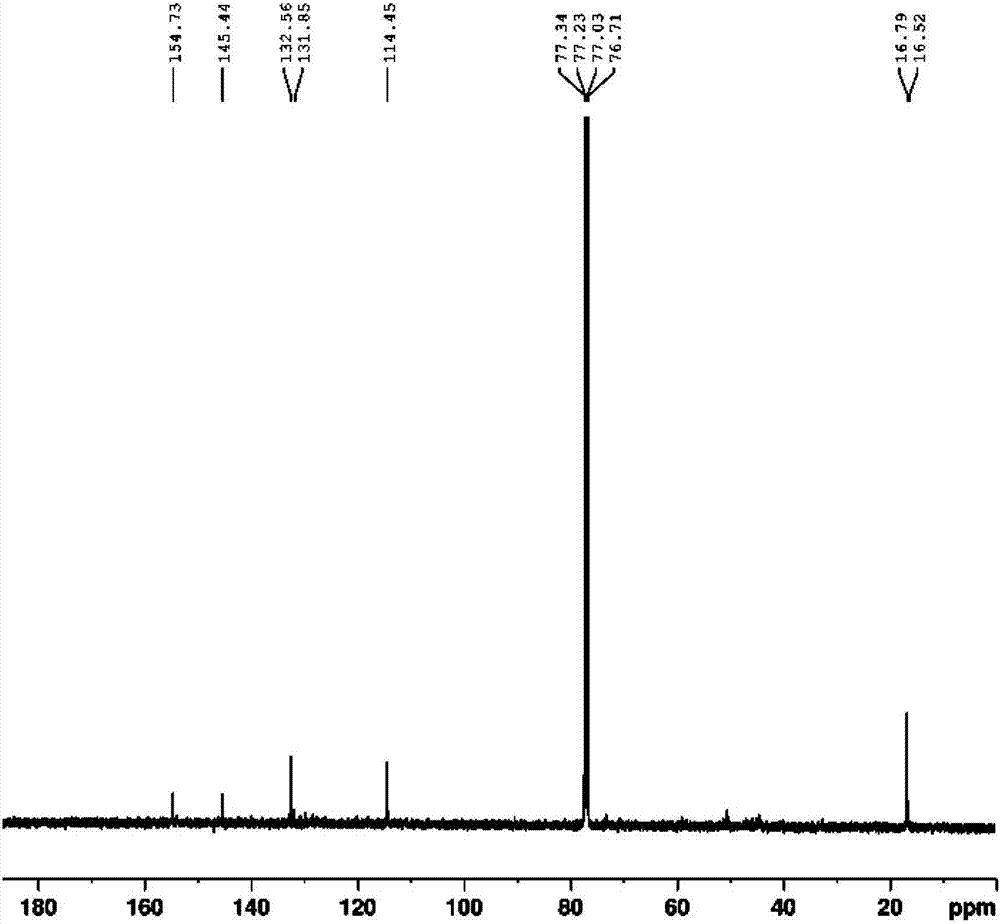
本发明涉及一种聚苯醚树脂、包括本发明的聚苯醚树脂的半固化胶片及其在覆铜板领域中的应用。
背景技术:
:覆铜板(ccl)是印刷电路板(pcb)的重要板材,随着pcb行业逐渐向传输高速、体型轻薄方向发展,对覆铜板的需求越来越高,高频覆铜板需求十分旺盛。聚苯醚(ppe)是一种性能优异的热塑性工程塑料,具有如下优点:(1)优良的物理、力学性能。密度小、无毒,较高的力学强度,成型收缩率低;(2)优良的耐热性能。玻璃化转变温度(tg)在热塑性塑料中最高,约210℃,结晶度约50%,熔点约260℃,它可在160~190℃范围内连续工作,高温下的耐蠕变性是热塑性工程塑料中较为优异的;(3)优良的电性能。ppe分子结构中无强极性基团,电性能稳定,可在广泛的温度及频率范围内保持良好的电性能。其介电常数和介电损耗角正切是工程塑料中最小的,几乎不受温度、湿度及频率的影响;(4)难燃,有自熄性。其氧指数为29%,阻燃性良好;(5)优良的耐酸碱性、耐应力松弛和耐疲劳性能以及良好的尺寸稳定性。尽管具有上面一系列的优点,但ppe作为热塑性工程材料存在耐溶剂性和流动性的缺点,从而限制了ppe在覆铜板领域的推广应用。虽然物理共混可以很大程度上改善产品的特性,但物理共混的前提,是需要有性能足够优秀的树脂可供选择。这里所说的足够优秀,不仅仅是指电性能和热性能,也包括树脂在覆铜板用溶剂中的溶解性和树脂之间的相容性。因此,开发和生产性能可靠的树脂,是重中之重。为充分发挥ppe优异的介电性能和耐热性,日本旭化成工业首先推出了热固性ppe(jp11012456,1999-01-19)。该热固性ppe是在ppe的分子主链上引入可进行交联反应的烯丙基。该固化物的tg可提高至240℃以上,并且不溶于卤代烃和芳烃溶剂中。但是,丁基锂的制备方法比较苛刻,危险系数高。将烯丙基与末端羟基反应,形成末端烯丙基封端的改性聚苯醚,但是由于烯丙基活性的原因,硬化温度偏高、收缩率大。引入双马来酰亚胺改性烯丙基封端的聚苯醚,虽然解决了硬化温度偏高和收缩率偏大的缺点,但增加了反应步骤,增加了产品工艺的复杂性, 进而影响了产品的稳定性。用丙烯酸酯基团封端的聚苯醚的固化温度较为适合,但丙烯酸酯改性聚苯醚对基底的粘附力不够。因此,特别需要一种聚苯醚树脂,兼顾低介电常数和介电损耗,低吸水率,低收缩率,以及对基底具有足够粘附力的性能。技术实现要素:本发明的目的是提供一种具有低介电常数和介电损耗,低吸水率,低收缩率,对基底粘附力足够的环氧封端的改性聚苯醚树脂。本发明的另一目的是提供一种具有低介电常数和介电损耗,低吸水率,低收缩率的苯并环丁烯封端的改性聚苯醚树脂。本发明的另一目的是提供包含所述环氧封端的改性聚苯醚树脂的组合物。本发明的另一目的是提供包含所述苯并环丁烯封端的改性聚苯醚树脂的组合物。本发明的另一目的是提供同时包含所述苯并环丁烯封端和环氧封端的改性聚苯醚树脂的组合物。本发明的另一目的是提供所述苯并环丁烯封端、环氧封端的改性聚苯醚树脂及其组合物的应用。为了完成上述发明目的,本发明提供一种具有通式ⅰ结构的环氧封端的改性聚苯醚树脂:其中,所述z表示选自由以下结构组成的组的芳香二酚结构:所述r31和r32相同或不同,各自独立的表示表示氢或甲基;所述me表示甲基,et表示乙基;所述p、q、r、s、t、u和v相同或不同,各自独立的表示0、1或2;所述a和b相同或不同,各自独立的表示0-100的整数,其中,m+n表示1-100的正整数。在一些实施方案中,优选地,z表示选自由以下结构组成的组的芳香二酚结构:在一些实施方案中,优选地,z表示选自由以下结构组成的组的芳香二酚结构:在本发明的一些实施方式中,所述通式ⅰ选自如下结构:以及在一些实施方案中,所述通式ⅰ选自如下结构:以及在一些实施方案中,所述通式ⅰ选自如下结构:发明人发现,由于覆铜板领域环氧树脂的大量使用,关于环氧封端的聚苯醚树脂化合物被相对广泛的报道。通式ⅰ中,以被公开的取代基团z至少有:双酚a、四甲基双酚a、六氟双酚a、联苯二酚、对苯二酚。但现有的文献和专利都只是罗列了一些双酚原料进行合成制备,仅仅停留在不同的双酚原料会有不同性能的初浅认识,并未对不同的双酚原料为何有不同做深入的理解。实际上,在高分子聚苯醚的合成制备历史中,早期的研究集中在如何将小分子的苯酚 聚合得到无甲基的聚苯醚结构,后来人们发现,无论如何努力,通过小分子的苯酚氧化聚合,总是无法得到线性的有一定规整性的无甲基的聚苯醚结构。而通过小分子的2,6-二甲基酚,在合适的催化体系下,就可以氧化得到线性的有一定规整性的聚苯醚结构。分子侧链的两个甲基保护了聚苯醚体系中相对脆弱的碳氧键,同时也钝化了苯环体系的反应活性,使得合成得以进行,得到的有甲基的聚苯醚相比其他材料具有相对高的耐热耐化学稳定性。因此,在聚苯醚体系中,分子侧链是否含有甲基,对材料的制备以及加工性能,都起着及其重要的作用。基于以上的认识,由于甲基对高分子聚苯醚的合成具有举足轻重的影响,可以合理推断在本发明提供的降解方法,将已有的高分子聚苯醚降解成相对小分子量的寡聚的聚苯醚时,降解采用的双酚是否具有甲基将对得到的产物同样产生显著的影响。毕竟,本发明提供的降解方法,原本是小分子合成大分子聚苯醚的一个副反应。双酚单体的甲基是一个重要的影响反应和性能的因素,而在聚苯醚改性的研究过程中并未被显著性的谈到,缺失这部分信息的原因,还在于不同双酚单体的分子结构本身差别相当大,转移了研究人员的注意力。事实上,有些特定的双酚单体没有甲基,制备得到的改性聚苯醚同样具有良好的效果,出现这样看上去矛盾的原因,是因为双酚单体的整体骨架结构的影响大于有无甲基的影响,同时在覆铜板行业中,不同的实验配方,其他组分会影响测试的结果。因此,在相同的骨架结构下,在相同的配方下、比较甲基对性能的差异才具有显著的意义。从实验上,我们也同样验证了以上的推断,当分别采用双酚a和四甲基双酚a降解高分子量的聚苯醚,采用相同的试剂和合成方法,制备双酚a和四甲基双酚a改性的聚苯醚,在相同条件下测试板材的特性,四甲基双酚a改性的聚苯醚的综合性能明显优于双酚a改性的聚苯醚体系。因此,本发明的环氧封端的聚苯醚树脂,更优选含甲基双酚单体的改性聚苯醚。可采用如下方法制备通式ⅰ所述改性聚苯醚树脂:步骤1,将高分子量的聚苯醚溶解到良溶剂中,再加入引发剂和相应的双酚单体,一定温度下搅拌反应若干小时,再加入不良溶剂析出固体。良溶剂可选择甲苯、丁酮、环己酮。优选甲苯。引发剂可选择常规的引发剂,如aibn(偶氮二异丁腈)和bpo(过氧化苯甲酰)。优选bpo。温度范围是40-160℃。优选110℃反应时间为0.5-24小时。优选6小时。步骤2,将析出的固体、环氧氯丙烷、相转移催化剂依次溶解到溶剂中,升温反应若干小时,滴加碱溶液后再反应若干小时,降温后除去有机溶剂,固体用丙酮溶解,滤去不 溶物,向滤液加入甲醇析出目标产物。溶剂可选择任何常规溶剂,只要可以溶解产物即可。优选异丙醇、乙醇。相转移催化剂选择季铵盐类催化剂,优选苄基三乙基氯化铵、四丁基氯化铵。温度范围为40-80℃,优选60℃。碱溶液为naoh或koh的水溶液,浓度5%-15%,优选naoh的10%水溶液。温度范围是80-160℃。优选110℃。反应时间为2-24小时。优选2小时。本发明提供了一种具有通式ⅱ结构的苯并环丁烯封端的改性聚苯醚树脂:其中,所述x表示芳香二酚结构;所述m和n相同或不同,各自独立的表示0-100的整数,其中,m+n表示0或者1-100的正整数。在本发明的一些实施方式中,所述x选自如下结构:其中,r1-r12相同或不同,各自独立的表示氢、甲基、乙基和卤素原子;z表示-s-、-so2-、-so-、羰基、酯基;r21、r22、r23和r24相同或不同,各自独立的表示氢、甲基、乙基和卤素原子。在本发明的一些实施方式中,所述x选自如下结构:其中,r1-r12相同或不同,各自独立的表示氢、甲基、乙基和卤素原子;z表示-s-、-so2-、-so-、羰基、酯基;r21、r22、r23和r24相同或不同,各自独立的表示氢、甲基、乙基和卤素原子。在本发明的一些实施方式中,所述x选自如下结构:其中,r1-r6和r11-r12相同或不同,各自独立的表示氢、甲基、乙基和卤素原子;z表示-s-、-so2-、-so-、羰基、酯基;r22表示氢、甲基、乙基和卤素原子。在本发明的一些实施方式中,优选地,所述通式ⅱ选自如下结构:以及其中,m和n相同或不同,各自独立的表示0-100的整数,其中,m+n表示0或者1-100的正整数。在本发明的一些实施方式中,优选地,所述通式ⅱ选自如下结构:以及其中,m和n相同或不同,各自独立的表示0-100的整数,其中,m+n表示0或者1-100的正整数。在本发明的一些实施方式中,优选地,所述通式ⅱ选自如下结构:在本发明的一些实施方式中,优选地,所述通式ⅱ选自如下结构:以及本发明中,对单独的m和n数值没有具体的要求。本发明中,当m+n数值不为零时,分子量范围在1000-10000为适合范围,优选的,分子量范围在1500-7500。本发明所述的分子量范围,是指采用凝胶色谱仪,采用凝胶色谱的方法得到的数均分子量。可采用如下方法制备通式ⅱ的聚苯醚树脂:步骤1,将高分子量的聚苯醚溶解到良溶剂中,再加入引发剂和相应的双酚单体,一 定温度下搅拌反应若干小时,再加入不良溶剂析出固体。良溶剂可选择甲苯、丁酮、环己酮。优选甲苯。引发剂可选择常规的引发剂,如aibn(偶氮二异丁腈)和bpo(过氧化苯甲酰)。优选bpo。温度范围是40-160℃。优选110℃反应时间为0.5-24小时。优选6小时。步骤2,将析出的固体再溶解到良溶剂中,加入甲醇钠,4-溴苯并环丁烯和催化剂,加热回流,反应若干小时,经提纯可得到通式ⅱ所述改性聚苯醚树脂。良溶剂可选择甲苯、丁酮、环己酮。优选甲苯。催化剂为一价铜盐,如氯化亚铜,溴化亚铜,碘化亚铜。优选氯化亚铜。温度范围是80-160℃。优选110℃。反应时间为2-24小时。优选10小时。本发明还提供了一种包含通式ⅰ所示的聚苯醚树脂化合物的组合物。本发明还提供了一种包含通式ⅱ所示的聚苯醚树脂化合物的组合物。本发明还提供了一种同时包含通式ⅰ和通式ⅱ所示的聚苯醚树脂化合物的组合物。本发明还提供了一种包含通式ⅰ或通式ⅱ所示改性聚苯醚树脂及其组合物在半固化片中的应用。本发明还提供了一种所述半固化片在覆铜板中的应用。本发明通式ⅰ或通式ⅱ所示的聚苯醚树脂及其组合物,可经过如下方式,得到半固化片:将通式ⅰ或通式ⅱ所示改性聚苯醚树脂及其组合物,溶解到合适的溶剂中,一般为甲苯或丁酮溶液,得到20-60%的甲苯或丁酮溶液,再加入重量为树脂比例10%的taic(三烯丙基异氰脲酸酯),充分搅拌,形成胶液;将增强材料,一般为玻纤布,纸基,复合材料等几种类型,浸没到胶液中,保持数分钟,取出浸渍胶液的增强材料,除掉溶剂,即为半固化片。与现有技术相比,本发明所述的苯并环丁烯封端和环氧封端的改性聚苯醚树脂,既保留了聚苯醚树脂原有的低介电常数和介电损耗性能,低的收缩率和吸水率,提高了对基底粘附力。附图说明图1是化合物ⅰ-1的碳谱。图2是化合物ⅰ-5的碳谱。具体实施方式以下将结合具体实施方案来说明本发明。需要说明的是,下面的实施例为本发明的示例,仅用来说明本发明,而不用来限制本发明。在不偏离本发明主旨或范围的情况下,可进行本发明构思内的其它组合和各种改良。实施例1化合物ⅱ-a-1的制备将1kg高分子聚苯醚,溶解到10l甲苯溶液中,加热搅拌使其溶解充分。加入重量百分比为10%的bpo和双酚a。保持110℃反应6小时。停止反应后,减压除去大部分甲苯溶液后,再加入5l甲醇,析出930g白色固体,记为树脂a。将树脂a溶解到甲苯中,再一次加入10g甲醇钠,10克4-溴苯并环丁烯,10克氯化亚铜,110℃反应10小时。冷却后,溶液经过滤,蒸出溶剂,加入甲醇析出固体,即为所需化合物ⅱ-a-1。实施例2化合物ⅱ-a-2的制备将1kg高分子聚苯醚,溶解到10l甲苯溶液中,加热搅拌使其溶解充分。加入重量百分比为10%的bpo和四甲基双酚a。保持110℃反应6小时。停止反应后,减压除去大部分甲苯溶液后,再加入5l甲醇,析出960g白色固体,记为树脂b。将树脂b溶解到甲苯中,再一次加入10g甲醇钠,10克4-溴苯并环丁烯,10克氯化亚铜,110℃反应10小时。冷却后,溶液经过滤,蒸出溶剂,加入甲醇析出固体,即为所需化合物ⅱ-a-2。实施例3化合物ⅱ-f-1的制备将1kg高分子聚苯醚,溶解到10l甲苯溶液中,加热搅拌使其溶解充分。加入重量百分比为10%的bpo和六氟双酚a。保持110℃反应6小时。停止反应后,减压除去大部分甲苯溶液后,再加入5l甲醇,析出910g白色固体,记为树脂c。将树脂c溶解到甲苯中,再一次加入10g甲醇钠,10克4-溴苯并环丁烯,10克氯化亚铜,110℃反应10小时。冷却后,溶液经过滤,蒸出溶剂,加入甲醇析出固体,即为所需化合物ⅱ-f-1。实施例4化合物ⅱ-e-3的制备将1kg高分子聚苯醚,溶解到10l甲苯溶液中,加热搅拌使其溶解充分。加入重量百分比为10%的bpo和双酚s。保持110℃反应6小时。停止反应后,减压除去大部分甲苯溶液后,再加入5l甲醇,析出850g白色固体,记为树脂d。将树脂d溶解到甲苯中,再一次加入10g甲醇钠,10克4-溴苯并环丁烯,10克氯化亚铜,110℃反应10小时。冷却后,溶液经过滤,蒸出溶剂,加入甲醇析出固体,即为所需化合物ⅱ-e-3。实施例5化合物ⅱ-b-2的制备将1kg高分子聚苯醚,溶解到10l甲苯溶液中,加热搅拌使其溶解充分。加入重量百分比为10%的bpo和四甲基联苯双酚。保持110℃反应6小时。停止反应后,减压除去大部分甲苯溶液后,再加入5l甲醇,析出960g白色固体,记为树脂e。将树脂e溶解到甲苯中,再一次加入10g甲醇钠,10克4-溴苯并环丁烯,10克氯化亚铜,110℃反应10小时。冷却后,溶液经过滤,蒸出溶剂,加入甲醇析出固体,即为所需化合物ⅱ-b-2。实施例6化合物ⅱ-3-2的制备将1kg高分子聚苯醚,溶解到10l甲苯溶液中,加热搅拌使其溶解充分。加入重量百分比为10%的bpo和甲基双酚芴。保持110℃反应6小时。停止反应后,减压除去大部分甲苯溶液后,再加入5l甲醇,析出980g白色固体,记为树脂f。将树脂f溶解到甲苯中,再一次加入10g甲醇钠,10克4-溴苯并环丁烯,10克氯化亚铜,110℃反应10小时。冷却后,溶液经过滤,蒸出溶剂,加入甲醇析出固体,即为所需化合物ⅱ-3-2。实施例7化合物ⅱ-6-1的制备将1kg高分子聚苯醚,溶解到10l甲苯溶液中,加热搅拌使其溶解充分。加入重量百分比为10%的bpo和双酚x。保持110℃反应6小时。停止反应后,减压除去大部分甲苯溶液后,再加入5l甲醇,析出960g白色固体,记为树脂g。将树脂g溶解到甲苯中,再一次加入10g甲醇钠,10克4-溴苯并环丁烯,10克氯化亚铜,110℃反应10小时。冷却后,溶液经过滤,蒸出溶剂,加入甲醇析出固体,即为所需化合物ⅱ-6-1。实施例8将10g化合物(12f)溶解到甲苯中,再一次加入10g甲醇钠,10克4-溴苯并环丁烯,10克氯化亚铜,110℃反应10小时。冷却后,溶液经过滤,蒸出溶剂,加入甲醇析出固体,即为所需化合物ⅱ-10-1-1。化合物(12f)如下所示:实施例9化合物ⅱ-8-1-1的制备将10g化合物(phdcpd)溶解到甲苯中,再一次加入10g甲醇钠,10克4-溴苯并环丁烯,10克氯化亚铜,110℃反应10小时。冷却后,溶液经过滤,蒸出溶剂,加入甲醇析出固体,即为所需化合物ⅱ-8-1-1。化合物(phdcpd)如下所示:实施例10化合物ⅰ-1的制备将1kg高分子聚苯醚,溶解到10l甲苯溶液中,加热搅拌使其溶解充分。加入重量百分比为10%的bpo和四甲基联苯二酚。保持110℃反应6小时。停止反应后,减压除去大部分甲苯溶液后,再加入5l甲醇,析出930g白色固体,记为树脂e1。将树脂e1溶解到异丙醇中,依次加入环氧氯丙烷、四丁基氯化铵,60℃反应2小时后,滴加10%的naoh水溶液,滴加完成后再反应2小时。降温后旋蒸除去有机相,将固体用丙酮溶解,滤去不溶物,向滤液加入甲醇析出固体。得到的固体,即为符合式ⅰ-1所示的化合物。碳谱测试溶剂:氘代氯仿,如图1所示。实施例11化合物ⅰ-3的制备将1kg高分子聚苯醚,溶解到10l甲苯溶液中,加热搅拌使其溶解充分。加入重量百 分比为10%的bpo和双酚opa。保持110℃反应6小时。停止反应后,减压除去大部分甲苯溶液后,再加入5l甲醇,析出930g白色固体,记为树脂e2。双酚opa如下式所示:将树脂e2溶解到异丙醇中,依次加入环氧氯丙烷、四丁基氯化铵,60℃反应2小时后,滴加10%的naoh水溶液,滴加完成后再反应2小时。降温后旋蒸除去有机相,将固体用丙酮溶解,滤去不溶物,向滤液加入甲醇析出固体。得到的固体,即为符合式ⅰ-3所示的化合物。实施例12化合物ⅰ-5的制备将1kg高分子聚苯醚,溶解到10l甲苯溶液中,加热搅拌使其溶解充分。加入重量百分比为10%的bpo和甲基双酚芴。保持110℃反应6小时。停止反应后,减压除去大部分甲苯溶液后,再加入5l甲醇,析出930g白色固体,记为树脂e3。将树脂e3溶解到异丙醇中,依次加入环氧氯丙烷、四丁基氯化铵,60℃反应2小时后,滴加10%的naoh水溶液,滴加完成后再反应2小时。降温后旋蒸除去有机相,将固体用丙酮溶解,滤去不溶物,向滤液加入甲醇析出固体。得到的固体,即为符合式ⅰ-5所示的化合物。碳谱测试溶剂:氘代氯仿,如图2所示。实施例13化合物ⅰ-9的制备将1kg高分子聚苯醚,溶解到10l甲苯溶液中,加热搅拌使其溶解充分。加入重量百分比为10%的bpo和9,10-二羟基蒽。保持110℃反应6小时。停止反应后,减压除去大部分甲苯溶液后,再加入5l甲醇,析出930g白色固体,记为树脂e4。将树脂e4溶解到异丙醇中,依次加入环氧氯丙烷、四丁基氯化铵,60℃反应2小时后,滴加10%的naoh水溶液,滴加完成后再反应2小时。降温后旋蒸除去有机相,将固体用丙酮溶解,滤去不溶物,向滤液加入甲醇析出固体。得到的固体,即为符合式ⅰ-9所示的化合物。按照上述的半固化片制作方式,制作相应的半固化片(以下记为pp),根据ipc-tm-650进行性能测试。对比实施例采用的聚苯醚树脂如式ss所示。其中,环氧树脂的收缩率的测试,采用将2份环氧和1份二胺(nn),在180℃固化2小时,分别测试固化前的体积和固化后的体积进行。表1:半固化片的性能数据pp实施例1pp实施例2pp实施例3对比实施例组成ⅰ-1ⅰ-5ⅰ-1和ⅰ-5ss比例100%100%50%和50%100%dk4.214.194.164.43df0.00990.00880.00850.0125收缩率1%1.5%1.3%1.3%吸水率0.510.550.510.53粘附力好好好好表2:半固化片的性能数据pp实施例5pp实施例6pp实施例7pp实施例8组成ⅱ-a-2ⅱ-b-2ⅱ-3-2ⅰ-1和ⅱ-b-2比例100%100%100%50%和50%dk3.213.163.063.83df0.00490.00380.00350.0065收缩率2%2.5%2.3%1.8%吸水率0.610.650.660.58粘附力好好好好从以上实施例可以看出,采用本发明的聚苯醚树脂,收缩率低,吸水率低,粘附力好,制备的板材具有优良的dkdf性能。当前第1页12