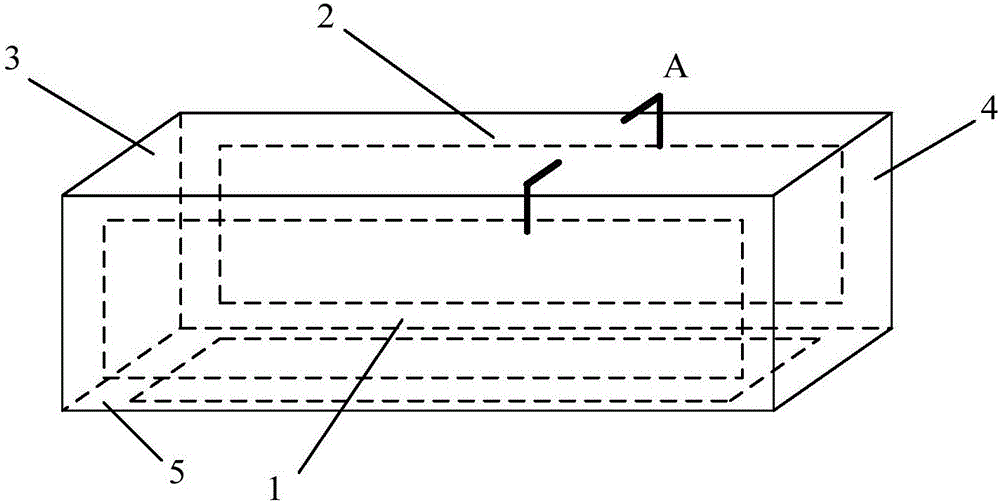
本发明属于多晶硅加工
技术领域:
,尤其涉及一种金刚线切割的多晶硅的清洗方法。
背景技术:
:金刚石线锯切割技术是目前最有潜力的硅片切割技术。与砂浆线锯切割技术相比,具有切割速率高;环境污染小;锯缝窄、硅损耗少;切割所得硅片表面损伤层薄、金属污染小、厚度分布均匀等优点;尤其是硅损耗方面可以使金刚石线锯切割技术比砂浆线锯切割技术获得更大的成本优势。金刚线切割的过程是:将硅铸定通过粘胶剂粘结在基板上,形成工件,之后采用固定有金刚石线的线锯切割所述工件,得到多晶硅片。所述工件具有图1所示的结构,具有基板100,粘结层200,通过粘结层200粘结于基板100上的晶体硅片300,每一个晶体硅片300之间具有锯缝400,锯缝400内部充满切割后的细小硅粉颗粒。脱胶工艺就是要将所述工件上的粘结剂脱除,将晶体硅片从基板上剥落。金刚线切割的晶体硅片锯缝400狭窄,对于切割后硅片的脱胶非常不利。脱胶剂难以快速进入充满硅粉的锯缝中与胶层接触达到脱胶的目的。脱胶耗时是同等片厚规格砂线片的2倍以上,与上游金刚线切割工序速率高,产能大难以匹配;本领域需要开发一种与金刚线切割多晶硅片工艺相匹配的脱胶方法,提高金刚线切割多晶硅的生产效率。技术实现要素:针对现有技术的不足,本发明的目的之一在于提供一种金刚线切割的晶体硅片的脱胶方法,所述方法包括如下步骤:(1)预清洗:将所述晶体硅片进行预清洗,除去切割过程中形成的松散硅粉;(2)一次超声清洗:将晶体硅片置于第一超声水槽中,进行超声清洗;(3)超声脱胶:将晶体硅片置于含有脱胶剂的第二超声水槽中,进行超声脱胶;(4)超声漂洗:将晶体硅片置于第三超声水槽中,进行超声漂洗;所述第一超声水槽、第二超声水槽、第三超声水槽中形成的超声波分别独立地至少具有第一超声传播方向,与第一超声传播方向相反的第二超声传播方向,以及与第一超声传播方向和第二超声传播方向均垂直的第三超声传播方向。本发明通过设计超声水槽中超声传播的方向,提高了超声波在超声水槽中的分布均匀性,增加了硅粉的去除效率,提高了脱胶剂向狭缝的分布速率,提高了晶体硅片的脱胶速率。优选地,所述第一超声水槽、第二超声水槽、第三超声水槽均具有垂直于第一超声传播方向的第一震板,具有垂直于第二超声传播方向的第二震板,以及垂直于第三超声传播方向的第三震板。优选地,所述第一超声水槽、第二超声水槽、第三超声水槽为长方体水槽,所述第一震板和第二震板分别固定于所述长方体水槽长度较长的两个侧面上,第三震板固定于所述长方体水槽的底面上。所述震板的大小不做限定,示例性的所述震板占所述面面积的0.5~0.9,例如0.6、0.7、0.8等。本发明所述超声水槽(包括第一超声水槽、第二超声水槽、第三超声水槽)具有底面,相对的第一侧面、第二侧面,与第一侧面、第二侧面和底面均垂直的第三侧面和第四侧面;第一侧面和第二侧面均比第三侧面和第四侧面大,所述第一侧面和第二侧面即为长度较长的侧面,第三侧面和第四侧面即为长度较短的侧面。优选地,所述第一震板固定于第一侧面上,第二震板固定于第二侧面上,第三震板固定于底面上。优选地,所述第一超声水槽、第二超声水槽、第三超声水槽中,每个超声传播方向的超声源的超声功率均各自独立地选自800~1500W,例如820W、840W、850W、870W、890W、920W、940W、950W、970W、990W、1020W、1040W、1050W、1070W、1090W、1120W、1140W、1150W、1170W、1190W、1220W、1240W、1250W、1270W、1290W、1320W、1340W、1350W、1370W、1390W、1420W、1440W、1450W、1470W、1490W等。优选地,所述脱胶剂包括乳酸和/或柠檬酸。优选地,所述第二超声水槽中,脱胶剂的浓度为60~80wt%,例如62wt%、65wt%、68wt%、72wt%、75wt%、78wt%等。优选地,所述第二超声水槽的水温为60~75℃,例如62℃、65℃、67℃、70℃、72℃、73℃等。作为优选具体实施方式,所述第二超声水槽为长方体水槽,其中第一震板、第二震板和第三震板的超声功率均为1000W。优选地,所述晶体硅片在第二超声水槽中的超声时间为500~700s,例如520s、550s、600s、650s、670s、680s等。作为优选具体实施方式,所述第一超声水槽为长方体水槽,其中第一震板、第二震板和第三震板的超声功率均为1000W。优选地,所述晶体硅片在第一超声水槽中的超声时间为300~500s,例如320s、350s、400s、450s、470s、480s等。优选地,所述第一超声水槽的水温为35~45℃,例如37℃、39℃、42℃、43℃等。作为优选具体实施方式,所述第三超声水槽为长方体水槽,其中第一震板、第二震板和第三震板的超声功率均为1000W。优选地,所述晶体硅片在第三超声水槽中的超声时间为100-300s,例如220s、230s、240s、250s、270s、280s等。优选地,所述第三超声水槽的水温为35~45℃,例如37℃、39℃、42℃、43℃等。作为优选具体实施方式,所述预清洗包括至少一次喷淋预清洗和至少一次超声预清洗,优选包括依次进行的第一次喷淋预清洗、第一次超声预清洗和第二次喷淋预清洗。优选地,所述第一次喷淋预清洗、第一次超声预清洗和第二次喷淋预清洗的温度为20~30℃,例如23℃、26℃、27℃等,优选25℃;优选地,所述第一次喷淋预清洗时间为100~300s,例如120s、130s、140s、150s、170s、180s、220s、230s、240s、250s、270s、280s等。优选地,所述第一次超声预清洗时间为100~300s,例如120s、130s、140s、150s、170s、180s、220s、230s、240s、250s、270s、280s等。优选地,所述第二次喷淋预清洗时间为100~300s,例如120s、130s、140s、150s、170s、180s、220s、230s、240s、250s、270s、280s等。优选地,所述脱胶方法中,相邻的水槽间的温差在25℃以下。相邻的水槽间的温差在25℃以下,能够减少硅片制程损耗。作为优选具体实施方式,本发明所述金刚线切割的晶体硅片的脱胶方法包括如下步骤:(1)预清洗:将所述晶体硅片依次进行25℃下的第一次喷淋预清洗100~300s,25℃下的第一次超声预清洗100~300s和25℃下的第二次喷淋预清洗100~300s;(2)一次超声清洗:将晶体硅片置于35~45℃的第一超声水槽中,进行超声清洗300~500s,所述第一超声水槽具有分别在第一超声传播方向、第二超声传播方向和第三超声传播方向上1000W的超声功率;(3)超声脱胶:将晶体硅片置于含有脱胶剂的60~75℃的第二超声水槽中,进行超声脱胶500~700s,所述第二超声水槽具有分别在第一超声传播方向、第二超声传播方向和第三超声传播方向上1000W的超声功率;(4)超声漂洗:将晶体硅片置于35~50℃的第三超声水槽中,进行超声漂洗200~300s,所述第二超声水槽具有分别在第一超声传播方向、第二超声传播方向和第三超声传播方向上1000W的超声功率。本发明目的之二是提供一种用于金刚线切割的晶体硅片脱胶方法的超声水槽,所述超声水槽形成的超声波至少具有第一超声传播方向,与第一超声传播方向相反的第二超声传播方向,以及与第一超声传播方向和第二超声传播方向均垂直的第三超声传播方向。优选地,所述超声水槽具有垂直于第一超声传播方向的第一震板,具有垂直于第二超声传播方向的第二震板,以及垂直于第三超声传播方向的第三震板。优选地,所述超声水槽为长方体水槽,所述第一震板和第二震板分别固定于所述长方体水槽长度较长的两个侧面上,第三震板固定于所述长方体水槽的底面上。优选地,所述超声水槽中,每个超声传播方向的超声源的超声功率均各自独立地选自800~1500W。优选地,所述超声水槽用于如权利要求1所述的金刚线切割的晶体硅片脱胶方法。与现有技术相比,本发明具有如下有益效果:本发明通过将超声水槽中的超声波设计成三个具有特定方向的传播方向,实现了超声波在超声水槽中的均匀分布,提高了晶体硅片狭缝中水的润湿度,提高了脱胶剂在狭缝中的分散速率,提高了狭缝中硅粉的脱落速率,缩短了金刚线切割的晶体硅片的脱胶时间,提高了生产效率。附图说明图1金刚线切割后工件的结构示意图;图2超声水槽S1的结构示意图;图3超声水槽S1沿A面的剖面结构示意图。具体实施方式为便于理解本发明,本发明列举实施例如下。本领域技术人员应该明了,所述实施例仅仅是帮助理解本发明,不应视为对本发明的具体限制。图2~图3给出了一种超声水槽S1,具有长方体结构,具有底面5,相对的第一侧面1、第二侧面2,与第一侧面1、第二侧面2和底面均垂直的第三侧面3和第四侧面4;第一侧面1和第二侧2面均比第三侧面3和第四侧面4大,所述第一侧面1和第二侧面2为长度较长的侧面,第三侧面3和第四侧面4即为长度较短的侧面;所述第一震板11固定于第一侧面1上,第二震板21固定于第二侧面2上,且第一震板11和第二震板21相对;所述第三震板31固定于底面5上,且第一震板11、第二震板21和第三震板31均向水槽内部发射超声波。图2超声水槽S1的结构示意图;图3超声水槽S1沿A面的剖面结构示意图。所述震板的大小不做限定,示例性的所述震板占所述面面积的0.5~0.9,例如0.6、0.7、0.8等。实施例1~3提供了一种金刚线切割的晶体硅片的脱胶方法,处理硅片数量为2500片,所述方法包括如下步骤:(1)预清洗:将所述晶体硅片依次进行25℃下的第一次喷淋预清洗100~300s,25℃下的第一次超声预清洗100~300s和25℃下的第二次喷淋预清洗100~300s;(2)一次超声清洗:将晶体硅片置于35~45℃的第一超声水槽中,进行超声清洗300~500s,所述第一超声水槽具有分别在第一超声传播方向、第二超声传播方向和第三超声传播方向上1000W的超声功率;(3)超声脱胶:将晶体硅片置于含有脱胶剂的60~75℃的第二超声水槽中,进行超声脱胶500~700s,所述第二超声水槽具有分别在第一超声传播方向、第二超声传播方向和第三超声传播方向上1000W的超声功率;(4)超声漂洗:将晶体硅片置于35~50℃的第三超声水槽中,进行超声漂洗200~300s,所述第二超声水槽具有分别在第一超声传播方向、第二超声传播方向和第三超声传播方向上1000W的超声功率。实施例1的具体工艺条件如表1:表1其中,4#槽和6#槽采用图2~3提供的超声水槽,5#槽中添加有70wt%的乳酸。实施例2的具体工艺条件如表2:表2其中,4#槽和6#槽采用图2~3提供的超声水槽,5#槽中添加有60wt%的乳酸。实施例3的具体工艺条件如表3:表3其中,2#槽、4#槽和6#槽采用图2~3提供的超声水槽,5#槽中添加有80wt%的乳酸。对比例1与实施例1的区别在于,4#槽和5#槽不使用图2~3提供的超声水槽,只使用超声水槽A1,所述超声水槽A1不具有第一震板和第二震板,只在底面具有第三震板。脱胶5#槽耗时为2000s。对比例2与实施例1的区别在于,4#槽和5#槽不使用图2~3提供的超声水槽,只使用超声水槽A2,所述超声水槽A2不具有第三震板,只在第一侧面具有第一震板,在第二侧面具有第二震板。脱胶5#槽耗时为1800s。对比例3与对比例2的区别在于,具体工艺条件如表4:槽编号1#槽2#槽3#槽4#槽5#槽6#槽功能喷淋超声喷淋超声超声脱胶超声清洗温度/℃252525307550时间/s40040040040012002405#槽中添加有80wt%的乳酸。对比例4与实施例1的区别在于,脱胶剂为50wt%的乳酸。脱胶耗时为1200s。脱胶耗时:硅片完全剥离时脱胶5#槽的实际运行时间。性能测试:将实施例和对比例脱胶完毕的工件进行硅片的剥落,统计硅片完全剥离时脱胶第五槽的运行时间统计如下表所示。脱胶耗时,s实施例1550实施例2500实施例3600对比例12000对比例21800对比例31200对比例41200申请人声明,本发明通过上述实施例来说明本发明的详细工艺设备和工艺流程,但本发明并不局限于上述详细工艺设备和工艺流程,即不意味着本发明必须依赖上述详细工艺设备和工艺流程才能实施。所属
技术领域:
的技术人员应该明了,对本发明的任何改进,对本发明产品各原料的等效替换及辅助成分的添加、具体方式的选择等,均落在本发明的保护范围和公开范围之内。当前第1页1 2 3